Galvanized Steel vs. Aluminum: A Comparative Analysis
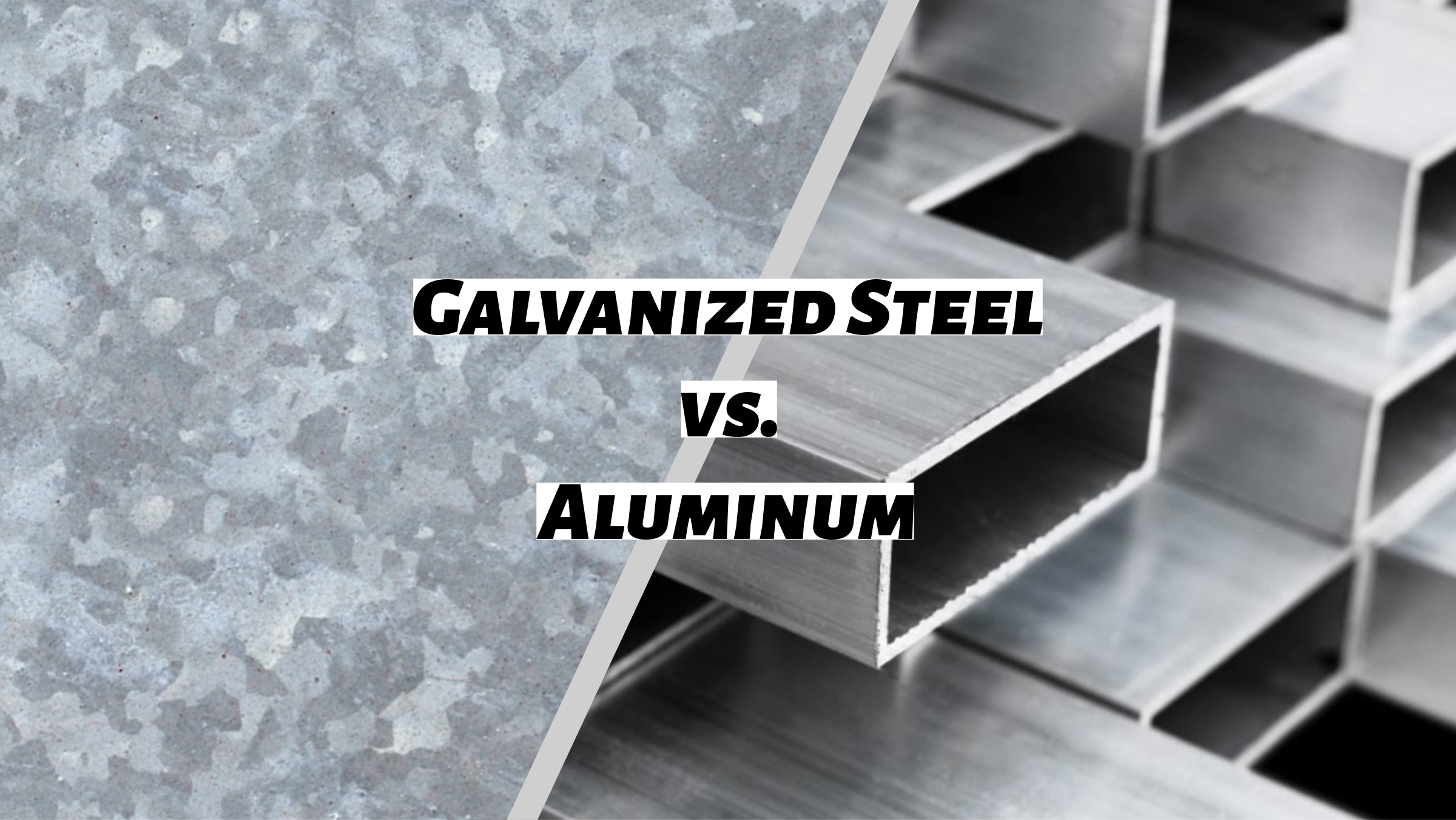
This article compares galvanized steel and aluminum, highlighting their unique properties, advantages, and drawbacks.
Introduction
Galvanized Steel vs. Aluminum
Galvanized metal is regular steel (or iron) that has been coated with a thin layer of zinc. This zinc coating protects the steel underneath from rust and corrosion. Galvanized metal is a strong and affordable material that is widely used in construction, manufacturing, and infrastructure.
Aluminum is a naturally corrosion-resistant and lightweight metal. It is a good conductor of heat and electricity and is easily recyclable. Aluminum is used in a wide variety of applications, including transportation, construction, and packaging.
Why Material Selection Matters
Choosing the right material is crucial for the success of a product or project across many industries. Here's why:
Performance: Different materials have different properties, such as strength, weight, corrosion resistance, and heat conductivity. The chosen material needs to meet the specific demands of the application. For instance, a car frame needs to be strong and lightweight, while a cooking pot needs to conduct heat well.
Cost: Material costs can significantly impact the overall project budget. While aluminum might be ideal for a product due to its lightweight properties, steel might be a more budget-friendly option if weight isn't a major concern.
Durability: The material needs to be able to withstand the expected wear and tear over the product's lifespan. For example, pipes used for plumbing should be durable and resistant to corrosion.
Sustainability: Some materials are more eco-friendly than others in terms of their extraction, processing, and recyclability. Manufacturers are increasingly considering the environmental impact of their material choices.
For more information, please view Unionfab’s metal post-process options.
Galvanized Steel: Properties and Applications
Galvanized metal is a versatile and popular material thanks to the zinc coating, which offers superior protection for the underlying metal, mainly steel. Here's a closer look at the process, properties, and applications of galvanized metal, using :
The Galvanization Process
There are a few different methods for galvanizing steel, but the most common is hot-dip galvanizing. In this process:
Steel is cleaned and prepared to ensure a good bond with the zinc coating.
The steel is then submerged in a bath of molten zinc at around 840°F (450°C).
The zinc reacts with the steel to form a zinc-iron alloy layer that bonds metallurgically to the steel surface.
As the steel cools, a layer of pure zinc crystallizes on top of the alloy layer.
This zinc coating acts as a sacrificial barrier, protecting the steel from corrosion. If the galvanized surface is scratched, the zinc corrodes first, protecting the steel beneath it. This is called galvanic cathodic protection.
Properties of Galvanized Steel
Durability: Galvanized metal is known for its long lifespan, especially in outdoor environments. The zinc coating provides excellent protection against rust and corrosion, extending the life of the steel underneath.
Corrosion Resistance: As mentioned earlier, zinc acts as a sacrificial barrier, significantly improving the corrosion resistance of steel. This makes galvanized metal ideal for use in harsh environments like near saltwater or where moisture is present.
Strength: Galvanized metal retains the inherent strength of steel, making it suitable for structural applications. The zinc coating adds minimal weight while providing significant corrosion protection.
Workability: Galvanized steel can be formed, bent, and cut using traditional metalworking techniques. This allows for its use in various applications requiring different shapes and configurations.
Cost-effective: Galvanized metal offers a good balance between cost and performance. The zinc coating adds a layer of protection at a relatively lower cost compared to other corrosion-resistant materials.
Applications of Galvanized Steel
Due to its beneficial properties, galvanized metal finds application in a wide range of industries, including:
Construction: Galvanized steel is widely used in roofing (sheets, flashing), framing (studs, joists), gutters, downspouts, and door frames due to its strength, durability, and weather resistance.
Automotive: Galvanized steel is used in car bodies (especially underbody panels), bumpers, and other automotive parts exposed to the elements for its corrosion resistance.
Agricultural Equipment: Due to its strength and ability to withstand harsh weather conditions, galvanized metal is used in farm buildings, fences, grain silos, and agricultural equipment frames.
Appliance Industry: Washing machines, dryers, and other appliances often utilize galvanized steel components due to its affordability, durability, and rust resistance in humid environments.
Utilities: Galvanized steel is used in utility poles, traffic signal poles, street signs, and chain-link fencing because of its strength, weather resistance, and longevity.
Aluminum: Properties and Applications
Aluminum is a highly versatile metal prized for its unique combination of properties. Let's delve into its key characteristics, different alloy types, and the vast array of applications it finds itself in.
Properties of Aluminum
Lightweight: Aluminum is one of the lightest engineering metals, boasting a density about three times lower than steel. This makes it ideal for applications where weight reduction is crucial, such as in aircraft construction and fuel efficiency in vehicles.
Corrosion Resistance: Aluminum naturally forms a thin oxide layer on its surface when exposed to air. This invisible layer acts as a passive barrier, protecting the metal from further corrosion. This makes it suitable for use in marine environments and for products exposed to moisture.
Good Conductor: Aluminum is a good conductor of both heat and electricity. This property makes it valuable for heat sinks in electronics, electrical wiring, and cookware.
Malleable and Ductile: Aluminum is highly malleable, meaning it can be easily shaped into sheets or foils. It's also ductile, allowing it to be drawn into thin wires. This formability allows for a wide range of product designs.
Recyclable: Aluminum is one of the most recyclable metals, with a very high recycling rate. Recycled aluminum requires significantly less energy to produce compared to virgin aluminum, making it an environmentally friendly choice.
Types of Aluminum Alloys
While pure aluminum has many desirable properties, its strength can be limited for certain applications. To address this, aluminum is often alloyed with other elements like copper, magnesium, silicon, and manganese. These alloying elements alter the properties of the base aluminum, creating a vast array of aluminum alloys with specific strengths, formability, and heat treatment characteristics. Here are some common aluminium alloy types:
1xxx Series (Pure Aluminum): Highly formable and conductive but not very strong. Used for foil, beverage cans, and electrical applications.
2xxx Series (Copper): High strength and good machinability. Used for aerospace components, bicycle frames, and fasteners.
5xxx Series (Magnesium): Lightweight with good weldability and corrosion resistance. Used for marine applications, storage tanks, and building panels.
6xxx Series (Magnesium and Silicon): Good combination of strength, formability, and corrosion resistance. Used for building materials, automotive parts, and extruded products.
7xxx Series (Zinc): High strength and good fatigue resistance. Used for aircraft parts, sporting goods, and high-performance components.
Applications of Aluminum
Aluminum's unique properties have led to its widespread use across various industries. Here are some prominent applications:
Aerospace: The lightweight nature and strength of aluminum alloys make them ideal for aircraft construction, contributing to fuel efficiency and performance.
Transportation: Aluminum is extensively used in car bodies, wheels, and other automotive parts due to its weight-saving properties and corrosion resistance. It's also used in trains, ships, and bicycles.
Packaging: Aluminum foil and cans are widely used in food and beverage packaging due to their lightweight nature, formability, and excellent barrier properties that protect contents from spoilage.
Construction: Aluminum is used in building facades, window frames, roofing sheets, and other architectural applications because of its lightweight strength, corrosion resistance, and aesthetics.
Consumer Goods: Aluminum is found in a variety of everyday items, including cookware, appliances, beverage cans, electronics enclosures, and sporting goods due to its versatility and formability.
Electrical Applications: Aluminum's good electrical conductivity makes it a viable alternative to copper in power transmission lines and electrical wiring, especially for applications where weight is a concern.
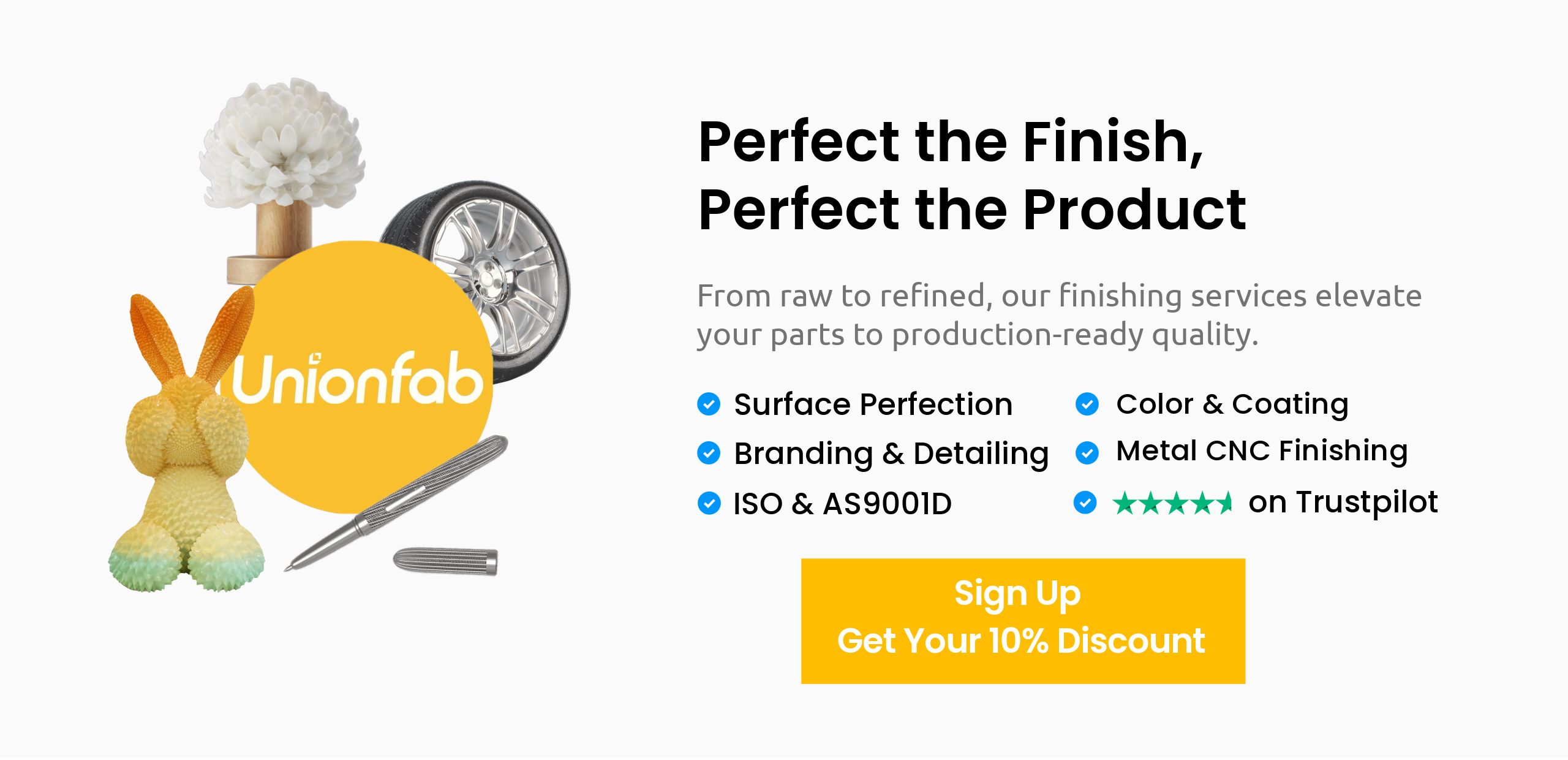
At Unionfab, we specialize in providing one-stop manufacturing and value-added finishing services to help you get the most out of your chosen material. Whether you need galvanizing, polishing, or other post-processing solutions, our team is here to assist you.
Contact us today to discuss your project and discover how our finishing services can elevate your designs!
Galvanized Steel vs. Aluminum: Properties
A closer look at how galvanized steel and aluminum compare in terms of key properties for material selection, using galvanized steel as the example:
Corrosion Resistance
Galvanized Steel: Offers good corrosion resistance due to the zinc coating. The zinc acts as a sacrificial barrier, corroding first to protect the underlying steel. However, in highly acidic or alkaline environments, the zinc layer can deteriorate faster.
Aluminum: Naturally forms a protective oxide layer that resists corrosion well, particularly in saltwater environments. However, this layer can be compromised by strong alkalis or specific chemicals.
Both materials offer good corrosion resistance, but galvanized steel might perform better in some acidic environments, while aluminum excels in saltwater settings. For environments with mixed factors, consider additional coatings for either material.
Strength-to-Weight Ratio
Galvanized Steel: Steel itself is a strong material, and the zinc coating adds minimal weight. However, aluminum offers a significantly better strength-to-weight ratio. This means for the same weight, an aluminum component will be stronger than its galvanized steel counterpart.
Aluminum: Lightweight yet possesses good strength, making it ideal for applications where weight reduction is crucial.
Aluminum is the clear winner in terms of strength-to-weight ratio, making it a preferred choice when weight is a major concern.
Durability
Galvanized Steel: Highly durable, especially in outdoor environments. The zinc coating provides a long lifespan, but scratches can expose the steel underneath, leading to eventual rusting. Proper maintenance (like repainting) can extend its life.
Aluminum: Durable and naturally corrosion-resistant. However, it can be susceptible to mechanical damage like dents or scratches, which can compromise its strength and aesthetics. Unlike steel, it won't rust, but significant dents can affect its functionality.
Both materials offer good durability, with galvanized steel potentially lasting longer, especially with maintenance. However, aluminum requires less maintenance due to its inherent corrosion resistance.
Cost-effectiveness
Galvanized Steel: Generally less expensive than aluminum upfront due to the lower material cost of steel. However, it might require additional maintenance like repainting over time, adding to the long-term cost.
Aluminum: Can be more expensive than galvanized steel initially. However, due to its low maintenance requirements and longer lifespan in some applications, the overall cost might be lower.
Galvanized steel has a lower initial cost, while aluminum offers potentially lower long-term expenses due to its lower maintenance needs. The most cost-effective choice depends on the specific application and its lifespan requirements.
Galvanized Steel vs. Aluminum: Pros and Cons
Galvanized Steel
Pros of Galvanized Steel:
Strength: Steel is a strong material, and galvanized steel retains this strength with the added benefit of corrosion resistance. This makes it suitable for structural applications, load-bearing components, and situations requiring high impact resistance.
Affordability: Galvanized steel is generally less expensive than aluminum upfront due to the lower cost of steel. This makes it a budget-friendly choice for many applications.
Durability: With proper maintenance (like occasional repainting), galvanized steel offers excellent long-term durability, especially in outdoor environments. The zinc coating provides a good barrier against corrosion.
Availability: Galvanized steel is a widely available material, making it easy to source and use in various projects.
⠀Cons of Galvanized Steel:
Weight: Galvanized steel is significantly heavier than aluminum. This can be a disadvantage in applications where weight reduction is crucial, such as transportation or aerospace.
Susceptibility to Corrosion: While the zinc coating protects the steel, it can eventually wear down, especially in highly acidic or alkaline environments. Without maintenance, the exposed steel can rust.
Maintenance: Galvanized steel might require occasional maintenance like repainting to extend its lifespan and maintain its appearance. Scratches can expose the underlying steel and accelerate corrosion.
Formability: Galvanized steel is less malleable and ductile than aluminum, making it more challenging to shape into complex forms.
Aluminum
Pros of Galvanized Steel:
Lightweight: Aluminum is a major advantage, particularly in applications where weight reduction is critical. This is why it's widely used in aircraft, transportation, and consumer goods.
Corrosion Resistance: Aluminum naturally forms a protective oxide layer that makes it highly corrosion-resistant, especially in saltwater environments. This eliminates the need for additional coatings in many cases.
Recyclability: Aluminum is one of the most recyclable metals, with a very high recycling rate. This makes it an environmentally friendly choice and reduces dependence on virgin material extraction.
Formability: Aluminum is highly malleable and ductile, allowing it to be easily shaped into sheets, foils, or drawn into thin wires. This versatility is valuable for creating complex shapes and intricate designs.
⠀Cons of Galvanized Steel:
Strength: While aluminum offers good strength, it's generally not as strong as steel for the same weight. This might limit its use in high-stress applications.
Cost: Aluminum can be more expensive than galvanized steel upfront due to the higher material cost. However, the lower maintenance requirements might offset the initial cost in some cases.
Susceptibility to Mechanical Damage: Aluminum can be susceptible to dents or scratches, which can compromise its strength and aesthetics. It's not ideal for applications requiring high impact resistance.
Limited Heat Resistance: Aluminum melts at a lower temperature compared to steel. This might limit its use in high-heat environments.
In conclusion, the best material choice between galvanized steel and aluminum depends on your specific project requirements. Consider factors like:
Strength requirements
Weight limitations
Corrosion environment
Budget constraints
Formability needs
Maintenance considerations
Galvanized Steel vs. Aluminum: Environmental Impact
When selecting a material, environmental impact is a growing concern. Here's a comparison of galvanized steel and aluminum regarding their sustainability and ecological impact, using galvanized steel as an example:
Recyclability
Galvanized Steel: Both steel and zinc in galvanized steel are highly recyclable. Steel boasts one of the highest recycling rates of any material. However, the recycling process for galvanized steel can be slightly more complex due to the need to separate the zinc coating from the steel during processing.
Aluminum: Aluminum is one of the most recyclable metals globally, with a very high recycling rate (over 70%). Recycled aluminum requires significantly less energy to produce compared to virgin aluminum, making it an environmentally friendly choice. The recycling process for aluminum is simpler than that of galvanized steel.
Energy Consumption in Production
Galvanized Steel: Steel production is an energy-intensive process, requiring high temperatures to extract iron ore and convert it to steel. The galvanization process also adds some energy consumption.
Aluminum: Aluminum production also requires significant energy, but generally less compared to steel. However, this can vary depending on the specific production methods used. There's ongoing research and development to reduce the energy footprint of aluminum production.
Aluminum has a clear advantage in terms of recyclability. While both materials require substantial energy for production, aluminum production might have a slightly lower footprint.
Ecological Impact of Galvanized Steel
Zinc Concerns: While zinc in the coating protects the steel and prevents rust, large-scale use of galvanized steel can contribute to zinc pollution if not properly managed during its lifecycle. Runoff from galvanized structures or improper disposal at the end of life can release zinc into the environment.
Longevity and Maintenance: Galvanized steel offers good longevity, but it might require maintenance like repainting over time. The production of paint and the repainting process itself add to the environmental impact.
Additional Considerations
Transportation: The environmental impact of transporting the materials to the final use location needs to be factored in. The lighter weight of aluminum can be an advantage here.
Application Specifics: The environmental impact of each material can vary depending on the specific application and its lifespan. For instance, if a galvanized steel structure lasts for decades with minimal maintenance, its overall impact might be lower than frequently replaced aluminum components.
Conclusion
Choosing between galvanized steel and aluminum depends on your specific needs and applications. Here are some guiding principles:
Strength is critical: Opt for galvanized steel for structural applications, load-bearing components, or situations requiring high impact resistance.
Weight reduction is crucial: Choose aluminum for applications where weight is a major concern, such as transportation, aerospace, or consumer goods.
Corrosion environment: Consider the specific environment. Galvanized steel might be better for some acidic environments, while aluminum excels in saltwater settings.
Budget constraints: If upfront cost is a major concern, galvanized steel might be a good choice. However, factor in potential maintenance costs over time.
Formability needs: If your project requires complex shapes, aluminum's superior formability makes it a better option.
Sustainability is a priority: If environmental impact is a major concern, aluminum's high recyclability and potentially lower production footprint make it a more sustainable choice.
Overall, both galvanized steel and aluminum will likely remain important materials in various industries.
Why Choose Unionfab for Your Material Needs?

Comprehensive Expertise: With over 20 years of experience, we provide end-to-end manufacturing solutions, including material selection, prototyping, and finishing.
High-Quality Finishing: From coating to galvanizing, our finishing services enhance both the performance and appearance of your parts.
Custom Solutions: Every project is unique, and we’re here to provide customized recommendations based on your requirements.
While these services aren’t included in our instant quoting system, you can easily reach out to our experts for tailored solutions.
Contact us today to discover how our finishing solutions can elevate your stainless steel creations!