Alloy Steel vs Stainless Steel vs Steel: A Comprehensive Comparison
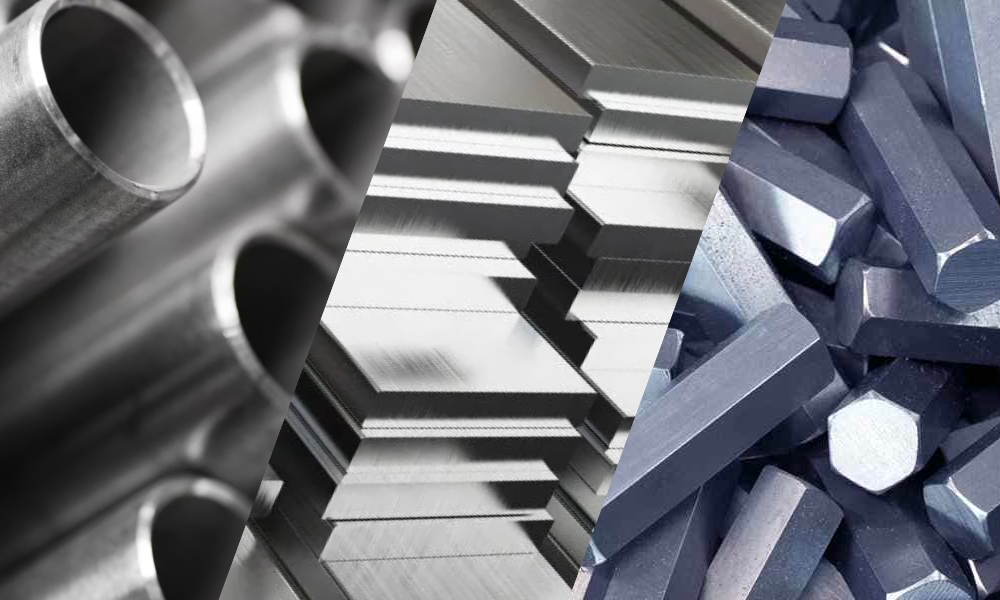
This article compares alloy steel, stainless steel, and carbon steel, highlighting key differences in composition, properties, performance, and applications.
Introduction
Steel is the backbone of modern infrastructure and manufacturing, serving as a vital component in various industries worldwide. Its versatility and durability make it indispensable in applications ranging from construction and automotive to aerospace and metal parts.
In this comprehensive comparison, we delve into three common types of steel—alloy steel, stainless steel, and carbon steel — to understand their unique characteristics, applications, and advantages.
Introduction to Steel and Steel Alloys
Defining Steel and its Variants
Steel: Basic Composition and Properties
Steel is an alloy made of iron and carbon. In plain carbon steel, the carbon content typically ranges between 0.2-2.1% by weight. This small percentage of carbon makes steel significantly stronger and harder than pure iron because carbon atoms fit neatly between the crystals of iron without substantially changing its body-centered cubic structure.
The yield strength and tensile strength of steel increase with higher carbon content, maximizing around 0.7-1.0% carbon depending on other alloying elements present. Beyond 1.0% carbon, steel becomes too brittle for practical structural applications.
Stainless Steel: Corrosion-Resistant Alloy
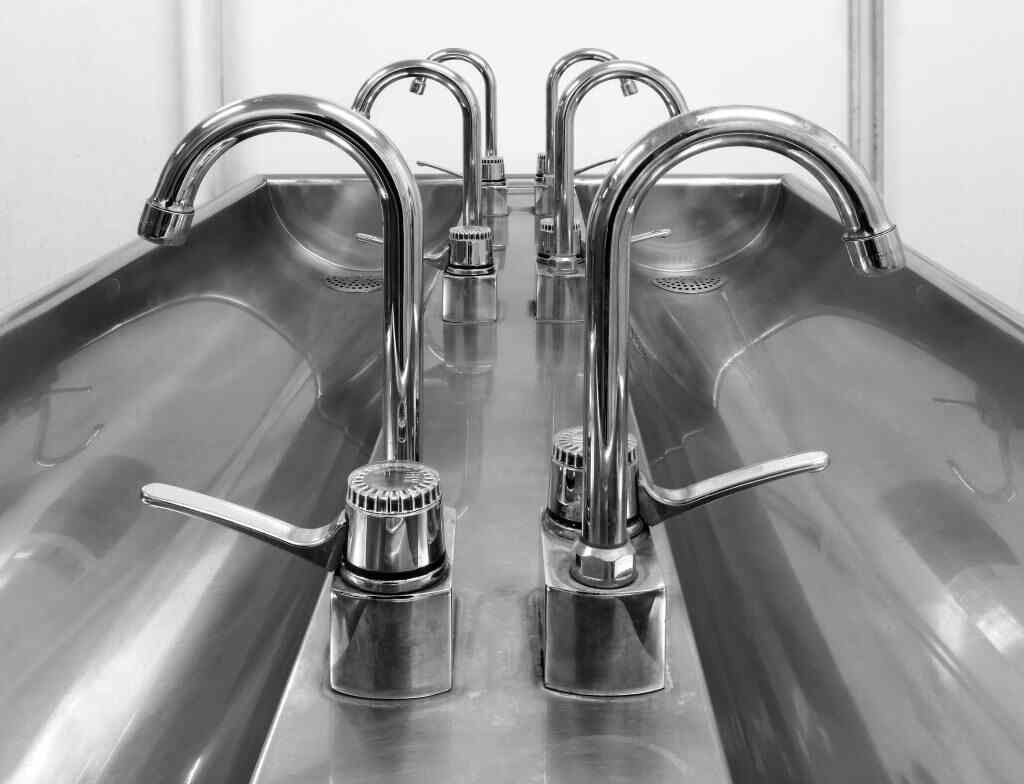
Source: https://commons.wikimedia.org/w/index.php?curid=57016790
Stainless steel contains a minimum of approximately 11% chromium by weight. The presence of chromium allows a passive chromium oxide layer to form spontaneously on the steel surface when exposed to oxygen. This invisible oxide layer protects the base metal from further corrosion, even under harsh and damp environmental conditions.
In addition to chromium, stainless steels also typically contain nickel and molybdenum which enhance the protective properties of the passive film.
Alloy Steel and Low Alloy Steel: Enhanced Strength and Durability
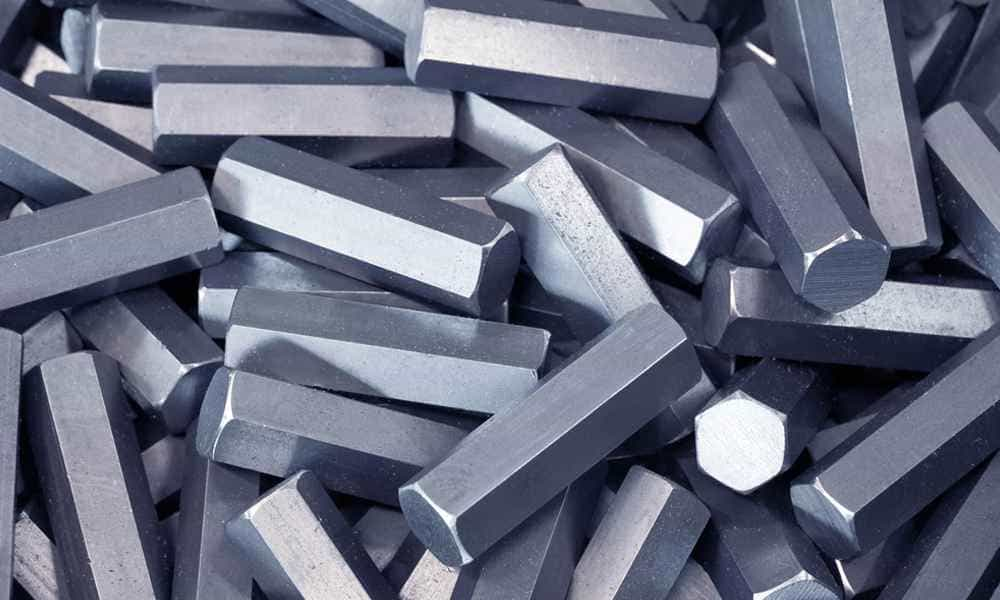
Alloy steels contain precise additions of other elements beyond iron and carbon. Common alloying elements include chromium, nickel, molybdenum, manganese and vanadium. These improve mechanical properties such as strength, toughness, hardenability, and wear resistance compared to plain carbon steel.
Low alloy steels contain minimal alloy additions, usually less than 5%, to provide enhanced characteristics without significant increases in production costs.
Mechanisms of Alloy Formation
Alloys: Combination of Base Metals and Other Elements
An alloy is formed by combining a base metal such as iron with precise amounts of other elements. These alloying elements dissolve into the base metal's crystalline structure when melted together. Their atoms populate interstitial spaces between the iron atoms or replace iron atoms entirely within the lattice.
For steels, the most common alloying elements are carbon, chromium, nickel, manganese, molybdenum, silicon, and vanadium. By altering the crystal structure, these alloy additions positively change the resulting material properties compared to pure iron alone.
Alloy Formation Processes
Steel alloys are primarily produced through one of two industrial processes - melting and casting. In melting, the ingredients are heated to their liquid states, allowing thorough mixing at a molecular level. Once cast into ingots or continuous cast shapes, controlled heat treatments are used to refine microstructures for optimum characteristics.
Annealing relieves stress from shaping, while processes like quenching and tempering introduce controlled levels of hardness. These precisely controlled solidification and post-processing steps allow tailoring the final steel's crystal structure and internal defects like dislocations and precipitates for enhanced performance.
Significance of Alloying Elements
Role of Alloying Elements in Modifying Properties
Alloying elements introduce distinct changes to the structure and properties of steel, enabling engineers to fine-tune its behavior for various applications.
Strengthening: Certain alloying elements, such as chromium, nickel, and molybdenum, serve to strengthen the steel matrix by promoting the formation of secondary phases or solid solution strengthening mechanisms. These elements effectively hinder dislocation movement within the crystal lattice, enhancing the material's resistance to deformation and improving its mechanical strength.
Enhanced Hardenability: Alloying elements like manganese, silicon, and vanadium can enhance the hardenability of steel, influencing the depth and uniformity of hardness achieved during heat treatment processes such as quenching. This property is crucial for achieving desired material properties in components subjected to varying levels of mechanical stress.
Corrosion Resistance: Elements such as chromium, nickel, and copper are commonly added to steel to impart corrosion resistance. These elements form protective oxide layers on the surface of the steel, inhibiting corrosion and extending the material's service life in aggressive environments.
Improvement of Toughness and Ductility: Alloying elements can also influence the toughness and ductility of steel, impacting its ability to withstand impact loading and deformation without fracture. Elements like nickel and manganese promote the formation of tough, ductile microstructures, enhancing the material's resilience to mechanical stresses.
Control of Thermal Expansion: Certain alloying elements, such as silicon and aluminum, can help control the thermal expansion coefficient of steel, making it suitable for applications requiring dimensional stability over a wide temperature range.
Overall, the presence of alloying elements profoundly influences the mechanical, thermal, and chemical properties of steel alloys.
Alloy Steel vs Stainless Steel
Characteristics and Composition
Stainless Steel: Corrosion Resistance
Stainless steel is prized for its exceptional corrosion resistance, owing to its composition of iron, chromium, nickel, and other elements. The passive oxide layer formed by chromium protects the steel from corrosion, making it ideal for harsh environments.
Alloy Steel: Enhanced Strength and Durability
Alloy steel boasts superior mechanical properties, including strength, hardness, and toughness, thanks to the addition of alloying elements like manganese, chromium, and molybdenum. Corrosion resistance is not as high as stainless.
Applications and Industries
Stainless Steel Applications
Stainless steel finds widespread use in industries requiring corrosion-resistant materials, including:
Architecture and Construction: Stainless steel is favored for building facades, roofing, structural components, and decorative elements due to its durability, aesthetic appeal, and resistance to atmospheric corrosion.
Food Processing and Hygiene: Stainless steel is the material of choice for food processing equipment, kitchen appliances, and sanitary fittings due to its hygienic properties, ease of cleaning, and resistance to corrosion from food acids and chemicals.
Medical and Pharmaceutical: Stainless steel is used in medical devices, surgical instruments, and pharmaceutical equipment due to its biocompatibility, sterilizability, and resistance to bodily fluids and harsh cleaning agents.
Alloy Steel Applications
Alloy steel's enhanced mechanical properties make it suitable for a wide range of demanding applications across industries such as:
Automotive and Transportation: Alloy steel is used in automotive components, including engine parts, transmission gears, axles, and chassis components, where high strength, durability, and wear resistance are critical for performance and safety.
Aerospace and Defense: Alloy steel is employed in aircraft components, missile systems, and military vehicles, where lightweight yet high-strength materials are essential for structural integrity, reliability, and mission success.
Oil and Gas: Alloy steel is utilized in drilling equipment, pipelines, valves, and fittings for the oil and gas industry, where resistance to high-pressure, corrosive environments, and abrasive wear is paramount for operational efficiency and safety.
Low Alloy Steel vs Stainless Steel
Low Alloy Steel: A Balance of Properties
Low alloy steel represents a compromise between plain carbon steel and high alloy steels, offering a balance of properties suitable for various applications.
Low alloy steels contain minimal alloy additions (typically <5%) of elements like chromium, molybdenum, nickel to enhance carbon steel. This provides better strength, toughness and weldability than carbon steel, at a lower cost than stainless or higher-alloy steels.
Comparisons with Stainless Steel
While not as corrosion resistant as stainless, low alloy steels exhibit higher strength and are more formable and weldable. Several key differences:
Mechanical Properties: Low alloy steel generally offers superior mechanical properties, including strength, toughness, and hardness, compared to stainless steel.
Corrosion Resistance: Stainless steel outperforms low alloy steel in resisting corrosion, thanks to its high chromium content. Low alloy steel may require additional coatings or protection in corrosive environments.
Cost-effectiveness: Low alloy steel often presents a more cost-effective alternative to stainless steel, particularly in applications prioritizing enhanced mechanical properties over corrosion resistance.
Versatility through Heat Treatment: Low alloy steel can be effectively heat-treated to further enhance its properties, offering versatility in engineering applications where specific mechanical characteristics are required.
Low Alloy Steel Applications
Low alloy steel finds applications in a wide range of industries where a balance of properties is required, including:
Automotive: Low alloy steel is commonly used in automotive components such as chassis, suspension systems, and engine parts, where high strength, toughness, and weldability are essential for safety and performance.
Construction: Low alloy steel is utilized in structural components, bridges, and buildings where enhanced strength and durability are required, particularly in high-stress environments or harsh weather conditions.
Machinery and Equipment: Low alloy steel is employed in the manufacturing of machinery, tools, and equipment, where wear resistance, toughness, and cost-effectiveness are critical for performance and longevity.
Alloy Steel vs Steel
Plain Carbon Steel: Basic Composition and Properties
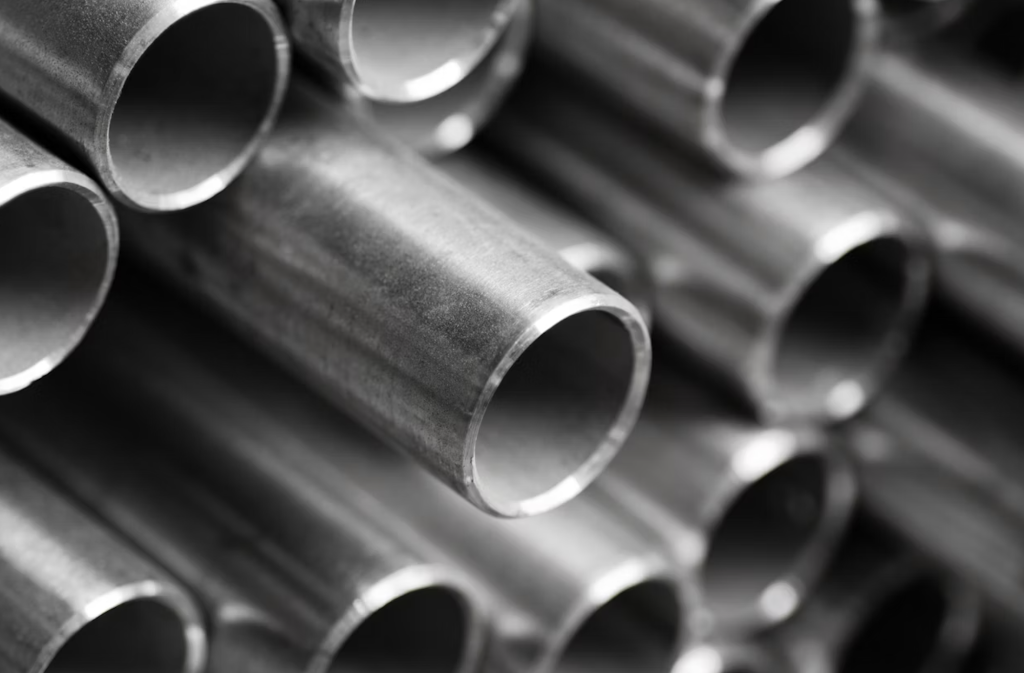
The properties of plain carbon steel largely depend on its carbon content:
Low Carbon Steel: Contains less than 0.3% carbon and is characterized by its ductility, formability, and weldability. It is commonly used in construction, automotive manufacturing, and machinery components.
Medium Carbon Steel: Contains 0.3% to 0.6% carbon and offers improved strength and hardness compared to low carbon steel. It finds applications in gears, shafts, and structural components requiring higher mechanical properties.
High Carbon Steel: Contains more than 0.6% carbon and exhibits high hardness and wear resistance. It is utilized in tools, knives, and springs where hardness and edge retention are critical.
Comparisons with Alloy Steel
Alloy steel differs from plain carbon steel by the addition of alloying elements such as manganese, chromium, nickel, molybdenum, and vanadium. These alloying elements enhance the properties of steel, offering advantages such as:
Improved Strength: Alloying elements contribute to the formation of secondary phases or solid solutions, increasing the strength and toughness of the material compared to plain carbon steel.
Enhanced Hardenability: Alloy steel can be heat-treated to achieve desired mechanical properties, such as hardness and toughness.
Better Wear Resistance: Certain alloying elements, such as chromium and molybdenum, improve the material's resistance to wear and abrasion, prolonging its service life in demanding applications.
Limitations and Applications
Despite its versatility, plain carbon steel has limitations compared to alloy steel:
Limited Strength: Plain carbon steel generally exhibits lower strength and hardness compared to alloy steel, limiting its suitability for high-stress applications.
Reduced Corrosion Resistance: Plain carbon steel is susceptible to corrosion in aggressive environments, necessitating protective coatings or treatments to mitigate degradation.
Plain carbon steel finds applications where cost-effectiveness and ease of fabrication are prioritized, such as:Construction: Structural beams, plates, and bars in buildings and bridges.
Automotive: Chassis components, body panels, and suspension parts.
Machinery: Shafts, gears, and fasteners.
Conclusion
In summary, the comparison of alloy steel, stainless steel, low alloy steel, and plain carbon steel reveals the diverse range of options available for meeting specific performance needs in various applications.
Alloy Steel: Offers enhanced mechanical properties and versatility through alloying elements, making it ideal for demanding industries like automotive and aerospace.
Stainless Steel: Renowned for its corrosion resistance and hygienic properties, it is indispensable in food processing, medical devices, and marine engineering.
Low Alloy Steel: Strikes a balance between cost-effectiveness and performance, serving a wide range of industries such as automotive, construction, and machinery.
Plain Carbon Steel: Cost-effective and versatile, it remains a preferred choice in construction, automotive, and machinery applications.
By carefully considering factors such as mechanical requirements, environmental conditions, and cost constraints, engineers can make informed decisions to optimize performance and cost-effectiveness across industries.
Unionfab’s Diverse Material Options
Unionfab leads the way in precision manufacturing with an extensive materials database covering mechanical, physical and corrosion properties. This includes metals, polymers, composites, coatings and more.
Trusted for quality and expertise, we offer tailored solutions to meet your needs.
