Maximizing Efficiency in Machining
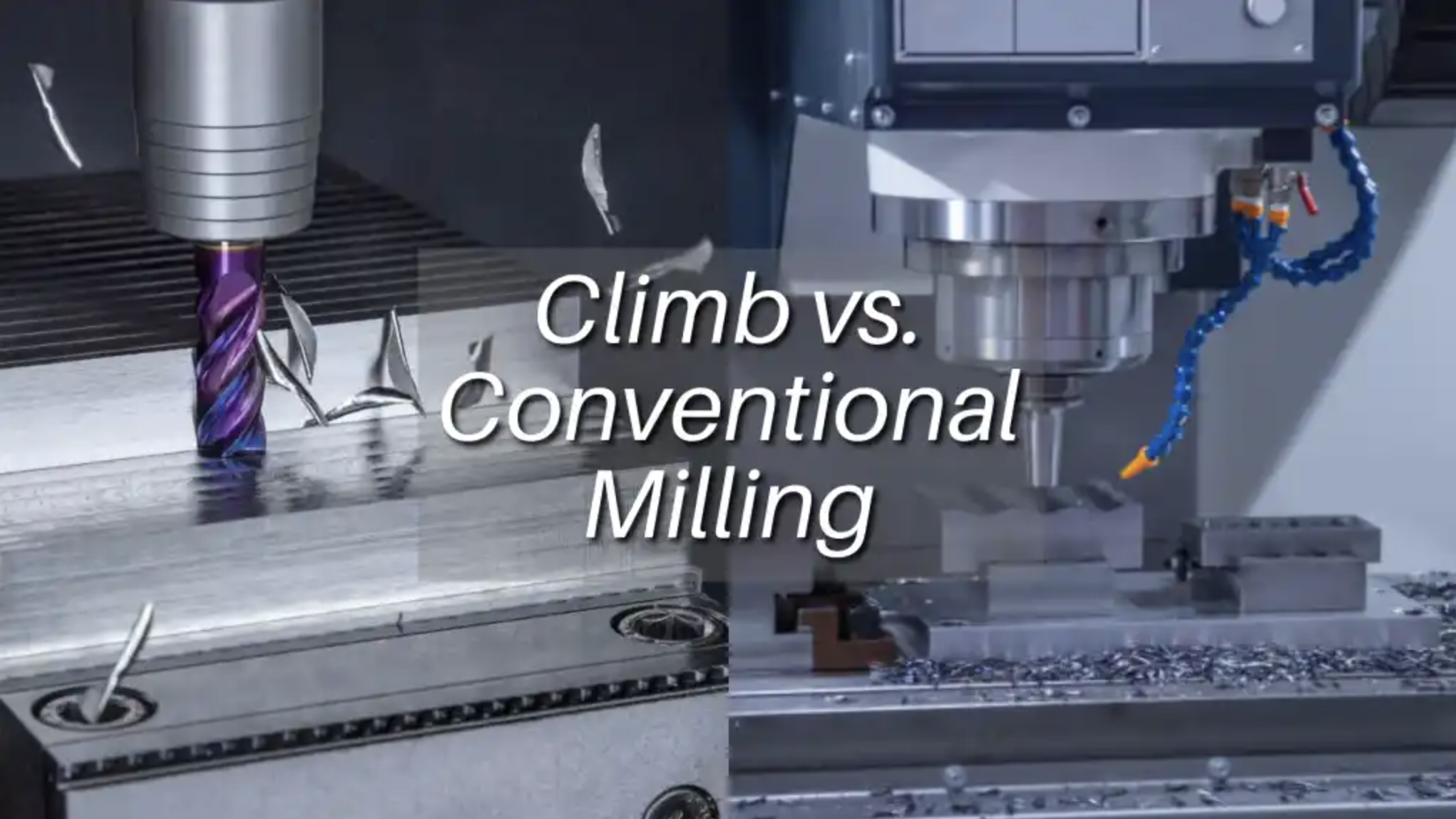
Discover the differences between climb milling and conventional milling techniques and learn how to optimize your machining processes.
Introduction
Climb (Down) milling and conventional (up) milling, the two main approches of metal removal with rotating tools. While both achieve precise cuts, the direction of the feed (movement of the workpiece) relative to the tool's rotation creates distinct advantages and disadvantages.
Climb vs. Conventional Milling: Definition
What is Climb Milling
In climb milling, the tool rotation and the feed direction are in the same direction. This creates a shearing action where the chips are pushed away from the cutting zone, minimizing recutting and potentially leading to a better surface finish.
However, climb milling can put a greater strain on the tool due to the pulling force exerted by the rotating tool. This can lead to tool deflection and affect dimensional accuracy.
What is Conventional Milling
In conventional milling, the tool rotation and the feed direction are in opposite directions. This pushing action helps to clamp the workpiece down, reducing chatter and improving stability.
However, conventional milling can lead to chip re-cutting, which can cause a rougher surface finish and potentially accelerate tool wear.
Climb milling vs. Conventional milling
Source: sandvik.coromant.com
Climb vs. Conventional Milling: Properties
Here are differences in properties of climb milling and conventional milling.
Property | Climb Milling | Conventional Milling |
---|---|---|
Cutting Direction | Same as feed direction (shearing) | Opposite of feed direction (pushing) |
Chip Formation | Thinner, more manageable chips | Thicker, more difficult to control chips |
Tool Engagement | Pulling force, can cause deflection | Wedging action, better stability |
Surface Finish | Generally better (reduced re-cutting) | May be rougher (chip re-cutting) |
Climb vs. Conventional Milling: Properties
Climb vs. Conventional Milling: Process
Machining Process of Climb Milling
Setup: The workpiece is secured on the milling table, and the desired cutting tool is mounted on the spindle.
Feed Direction: The workpiece is programmed to move in the same direction as the tool's rotation.
Cutting Action: As the tool rotates and the workpiece feeds, the cutting edges engage the material with a shearing action.
Force: The cutting force acts in the same direction as the feed, potentially putting a greater strain on the tool shank due to the pulling effect. This can lead to tool deflection in certain situations.
Machining Process of Conventional Milling
Setup: Similar to climb milling, the workpiece is secured, and the cutting tool is mounted.
Feed Direction: The workpiece is programmed to move in the opposite direction of the tool's rotation.
Cutting Action: With the opposing feed direction, the cutting edges engage the material with a pushing action.
Force: The cutting force opposes the feed, helping to clamp the workpiece down and reduce chatter.
Climb vs. Conventional Milling: Pros and Cons
To choose the right milling technique for your project, it's necessary to learn about pros and cons of climb and conventional milling.
Property | Climb Milling | Conventional Milling |
---|---|---|
Surface Finish | Superior (minimized chip re-cutting) | Rougher (chip re-cutting) |
Cutting Forces | Reduced | Higher |
Chip Evacuation | Improved | Increased re-cutting |
Tool Deflection | Increased risk | Less prone |
Material Suitability | Not ideal for chipping materials | Wider range of materials |
Setup Requirements | Rigid setup and strong tools | More forgiving setup |
Stability | May be less stable | Improved stability |
Dimensional Accuracy | Potential for inaccuracies due to deflection | Less prone to deflection |
Climb vs. Conventional Milling: Pros and Cons
Climb vs. Conventional Milling: Choosing the Right Milling
Material Type and Hardness
Climb Milling: Ideal for softer, ductile materials where a smooth finish is crucial. It's less suitable for brittle materials prone to chipping due to the pulling force.
Conventional Milling: More versatile for various materials, including harder materials and those prone to chipping. The pushing action helps clamp the workpiece and reduces chipping.
Machine Rigidity
Climb Milling: Requires a rigid machine setup to minimize tool deflection. This is especially important for deep cuts or weak tools.
Conventional Milling: Less susceptible to tool deflection due to the pushing action. This makes it a good choice for machines with less rigidity.
Tool Condition and Wear
Climb Milling: Puts greater strain on the tool due to the pulling force. Sharper and stronger tools are recommended to minimize deflection.
Conventional Milling: Less demanding on the tool. However, tool wear can still lead to increased chip re-cutting and a rougher surface finish.
Machining Purpose
Climb Milling: Excellent for finishing cuts where a superior surface finish is important. It can also be used for roughing cuts on softer materials with proper considerations for machine rigidity and tool selection.
Conventional Milling: Ideal for roughing cuts where a smooth finish is less critical and chip evacuation is important. It's also preferred for workpieces prone to vibration or chatter due to its improved stability.
Conclusion
Climb milling and conventional milling offer distinct advantages and disadvantages. Climb milling excels in achieving a superior surface finish and requires less cutting force, but demands a rigid setup and stronger tools.
Conventional milling, on the other hand, provides better stability, handles a wider range of materials, and is less prone to deflection, but may result in a rougher surface.
By understanding these factors and carefully considering your project's needs, you can select the right milling technique for optimal results.
Unionfab Provides Professional CNC Machining Services
Unionfab provides a comprehensive range of CNC machining services, including CNC Turning, CNC Milling and CNC Routing.
With multi-axis milling and turning expertise, our services cater to diverse client applications, ensuring accurate, efficient, and cost-effective production of your finished components.