Guide to SLS 3D Printing [+Free Cost Calculator]
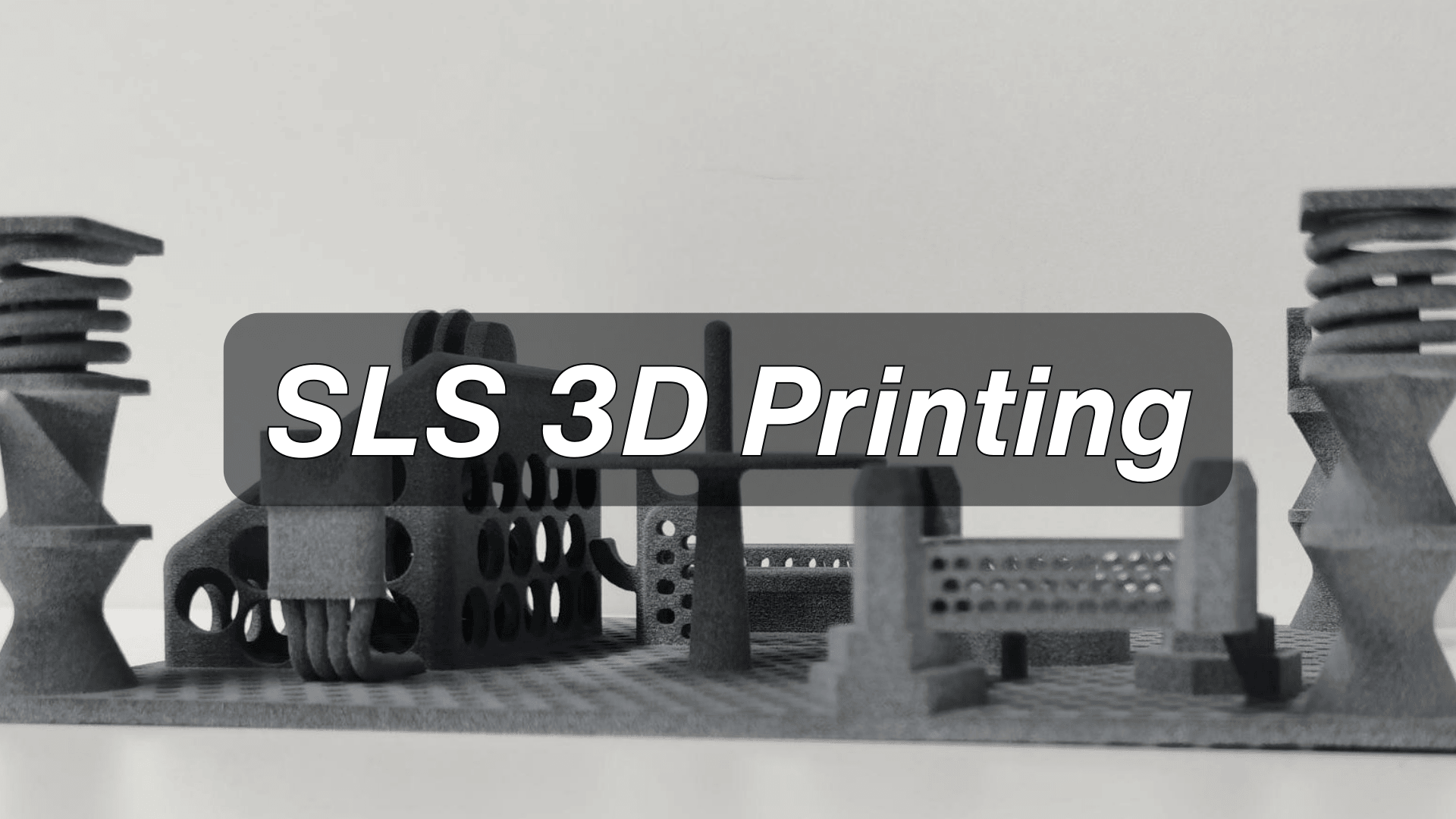
Explore the working principles, materials and applications of SLS 3d printing, and get an instant quote using Unionfab’s free cost calculator!
What is SLS 3D Printing?
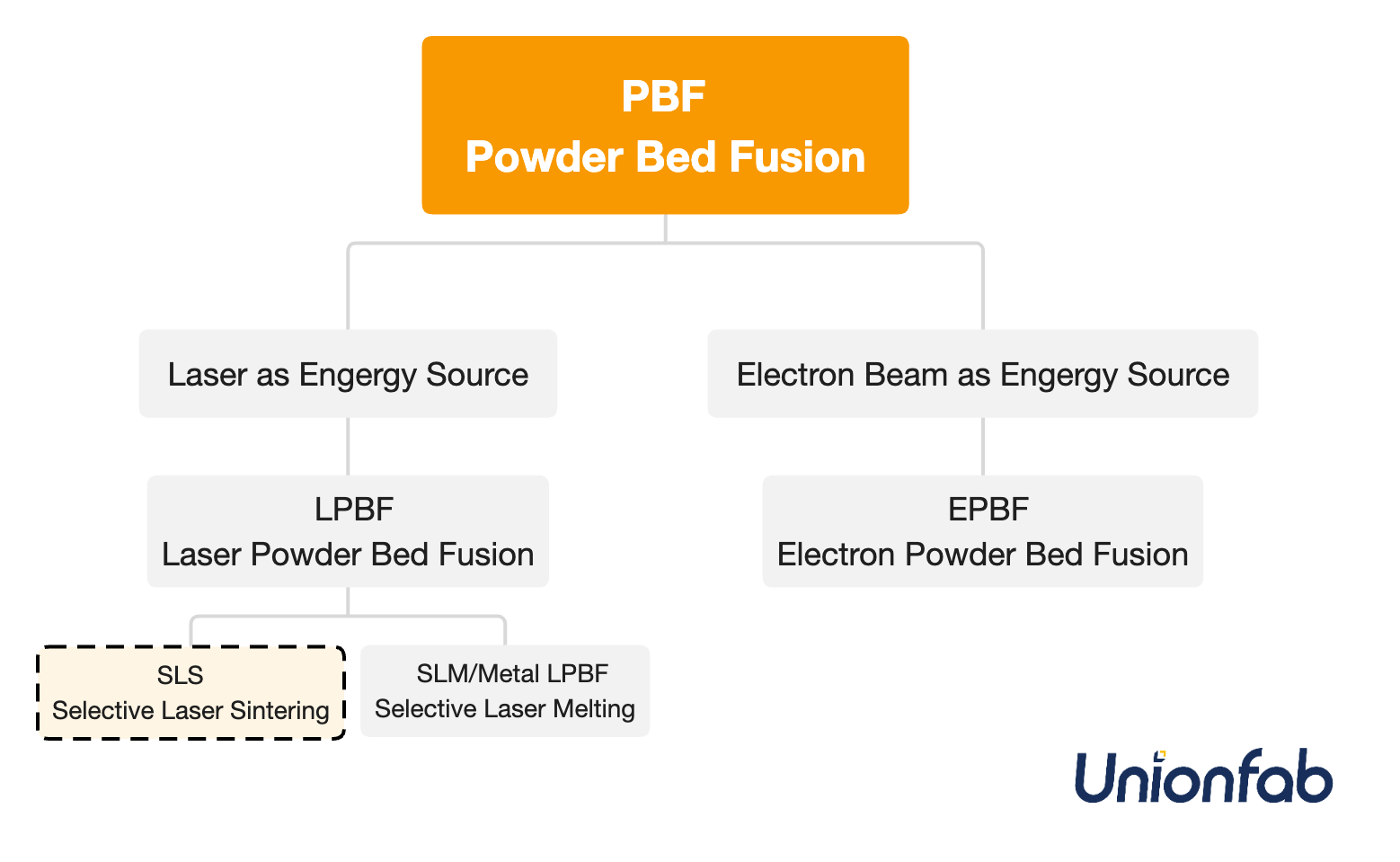
SLS stands for selective laser sintering in 3d printing. It belongs to laser powder bed fusion, using a high-powered laser to fuse small particles of plastic, metal, or ceramic powder into solid structures.
Applications of SLS 3D Printing
SLS is a reliable solution for industries demanding high-strength, lightweight, and intricately designed parts without the constraints of traditional manufacturing. Its strength and versatility make it ideal for:
1. Concept Models
Functional Proof of Concept Models | Design Evaluation Models (Form & Fit) |
---|---|
|
|
2. Rapid Prototyping
Engineering Design Verification | Product Performance & Testing | Tooling and Patterns |
---|---|---|
|
|
|
3. Direct Digital Manufacturing
Rapid Manufacturing | Production Applications | On-Demand Tooling |
---|---|---|
|
|
|
How SLS 3D Printing Works?
To understand the fundamentals of SLS 3D printing, it is essential to examine the core components of an SLS 3D printer and their roles in the sintering process.
Components of a SLS 3D Printer
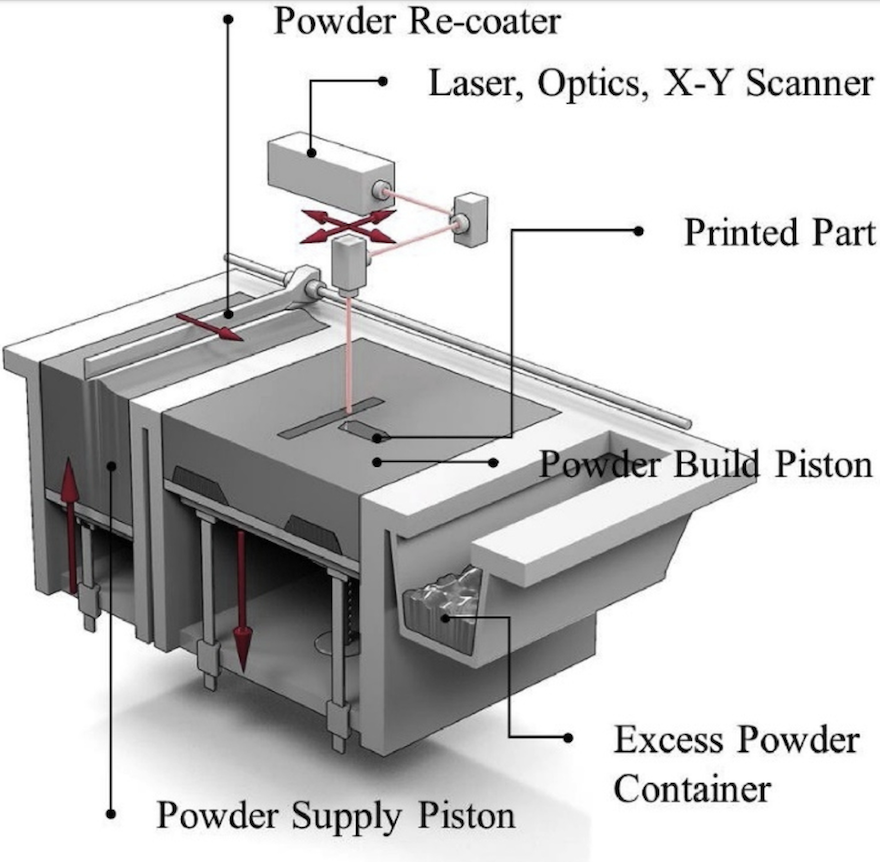
Source: https://doi.org/10.1002/app.53476
A SLS 3d printer is made up of 4 components: Laser System, Powder Handling System, Heating System, Control System. Each components with its core parts, plays its due role in the printing process.
Apart from them, the building chamber is filled with inert gas, usually nitrogen or argon to prevent powder oxidation during sintering.
Component | Core Parts | Function |
---|---|---|
Laser System | CO₂ laser | Melts and fuses powder particles selectively using focused laser energy. |
Powder Handling System | - Powder supply chamber | Stores, distributes, and layers powder material for sintering. |
Heating System | Preheating modules | Heats the powder bed to near-melting temperature to minimize thermal stress. |
Inert Gas Environment | Nitrogen/argon gas supply | Prevents powder oxidation during sintering. |
Control System | - Motion controllers | Coordinates laser scanning, powder spreading, and layer-by-layer building. |
Step-by-Step SLS 3D Printing Process
Model Preparation: Prepare and slice a 3D model into layers for printing.
Printer Setup: Load polymer powder and preheat the build chamber
Layer Building: Spread powder and sinter each layer with a laser.
Cooling: Allow the part to cool gradually within the powder bed.
Post-Processing: Extract the part, clean excess powder, and apply finishing.
Additional Notes:
Unsintered powder is recycled for future use.
Parts exhibit high strength across all axes.
Complex geometries are achievable without support structures.
The entire process typically completes in 12–48 hours, depending on part size and complexity.
SLS 3D Printing Materials
Theoretically, materials that can be used in SLS 3d printing include thermoplastics, metals and ceramics.
However, metals and ceramics are less prevalent in SLS due to their higher processing temperatures, inferior flow characteristics, and better compatibility with other 3d printing technologies.
Therefore, we will focus on thermoplastics next.
Materials for SLS Nylon 3D Printing
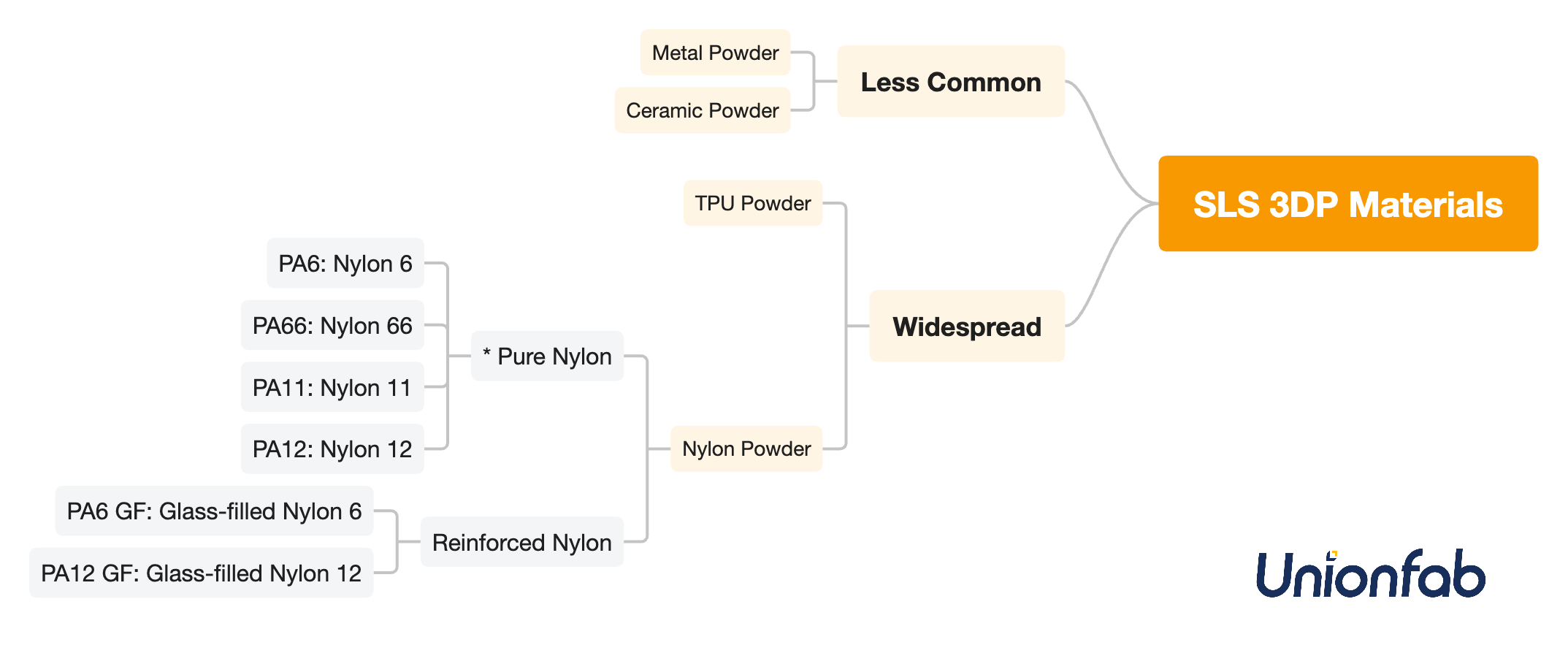
Unlike FDM using filament, and SLA using liquid resin, SLS sinters materials in powder form. SLS powders mainly fall into two categories: TPU and Nylon.
TPU (Thermoplastic Polyurethane) is a flexible, rubber-like material used in SLS printing to create elastic, durable parts.
Known for its stretchability (up to 500% elongation) and tear resistance, it’s perfect for shock-absorbing parts, wearable devices, and snap-fit designs. Its balance of softness and strength makes it ideal for products needing both comfort and performance.
For more details about TPU 3d printing, you can read our previous article: TPU 3D Printing: Tips, Tricks & Best Solutions
Nylon used in SLS 3d printing can be further divided into pure nylon (Nylon 6, Nylon 66, Nylon 11 & Nylon 12) and reinforced Nylon materials (Glass-filled & Carbon-filled).
For pure nylon powders, additives are often blended to enhance flowability, thermal stability, anti-static properties, and sintering performance—ensuring higher-quality prints.
Glass fibers or beads are added to nylon to increase its strength, rigidity, and dimensional stability. Glass fibers are inexpensive and provide a good balance between performance and cost.
Carbon fibers are added to nylon to improve strength, stiffness, and thermal conductivity. Carbon fibers offer even higher performance than glass fibers, but at a higher cost.
For more details about the comparison between different nylon powders, you can read our previous article: Guide to Nylon 3D Printing.
SLA vs. SLS vs. MJF vs. FDM
Criteria | SLS | |||
---|---|---|---|---|
Best For | Designers, dental/jewelry fields | Engineers, medical/auto industries | Manufacturers, batch production | Makers, education/hobby use |
Common Uses | High-detail models, molds | Functional parts, hinges | Durable end-use parts | Rapid prototypes, low-cost tests |
Cost | High ($100–300/kg resin) | High ($80–200/kg nylon powder) | Medium ($60–150/kg nylon powder) | Low ($20–50/kg filament) |
Print Speed | Medium (volume-dependent) | Slow (12–48 hrs with cooling) | Fast (<24 hrs for batches) | Slow-moderate (layer bonding) |
Post-Processing | High (washing, curing, supports) | Medium (powder removal, polishing) | Low (direct use/sandblasting) | Low (support removal, sanding) |
Design Freedom | High detail, limited by supports | Excellent (no supports, nesting) | High (complex structures) | Low (supports needed for overhangs) |
Strength | Brittle (low impact resistance) | High (near-injection molding) | High (uniform, wear-resistant) | Moderate (layer adhesion limits) |
Surface Quality | Smooth (polishable to clear) | Gritty (sandpaper-like) | Matte, uniform | Visible layer lines |
Environmental Impact | Toxic resin handling required | High powder reuse (>95%) | Energy-efficient, recyclable | PLA biodegradable, ABS fumes |
Quick Use Case Matching
✅ Choose SLA:
Ultra-detailed/transparent parts (e.g., jewelry molds).
Tolerate post-processing effort.
✅ Choose SLS:
Functional moving parts (hinges, snap-fits).
Industrial lightweight components.
✅ Choose MJF:
Small-batch end-use production (50–1k units).
Speed + durability balance (e.g., custom housings).
✅ Choose FDM:
Budget-friendly prototyping/education.
Simple home/hobby projects.
Decision Checklist
Quantity: 1–10 units → SLA/FDM; 10–500 units → SLS/MJF
Load-bearing Needs: High stress → SLS/MJF; Cosmetic → SLA/FDM
Surface Finish Priority: Critical → SLA; Acceptable texture → SLS/MJF
Why Outsourcing? The Hidden Costs of Self-printing
Once you’ve selected the ideal 3D printing technology and materials, the next question arises: “Buy a machine or outsource?”
Though the answer varies by project, outsourcing typically offers lower risks and greater convenience than managing in-house SLS printing.
High Initial Investment: Equipment and facility costs are significant. Outsourcing eliminates capital investment.
Material and Waste: Wastes of expensive materials are inevitable. Service providers minimize costs via bulk purchasing and recycling.
Operating and Maintenance: Maintenance and high energy costs are ongoing and high. Outsourcing shifts these responsibilities.
Labor and Training: Skilled operators hiring and training add costs. Outsourcing simplifies the process.
Opportunity Costs: Low equipment utilization and slow response to urgent orders. Outsourcing improves efficiency and flexibility.
Quality Control and Risk: High failure rates and compliance risks. Service providers manage these costs and certifications.
With the information above, it's clear that outsourcing 3D printing services offers significant advantages. The next step is to choose a reliable service provider.
SLS Printing Service Providers Comparison
To help you choose the most suitable service provider, we have made a comparison table as below:
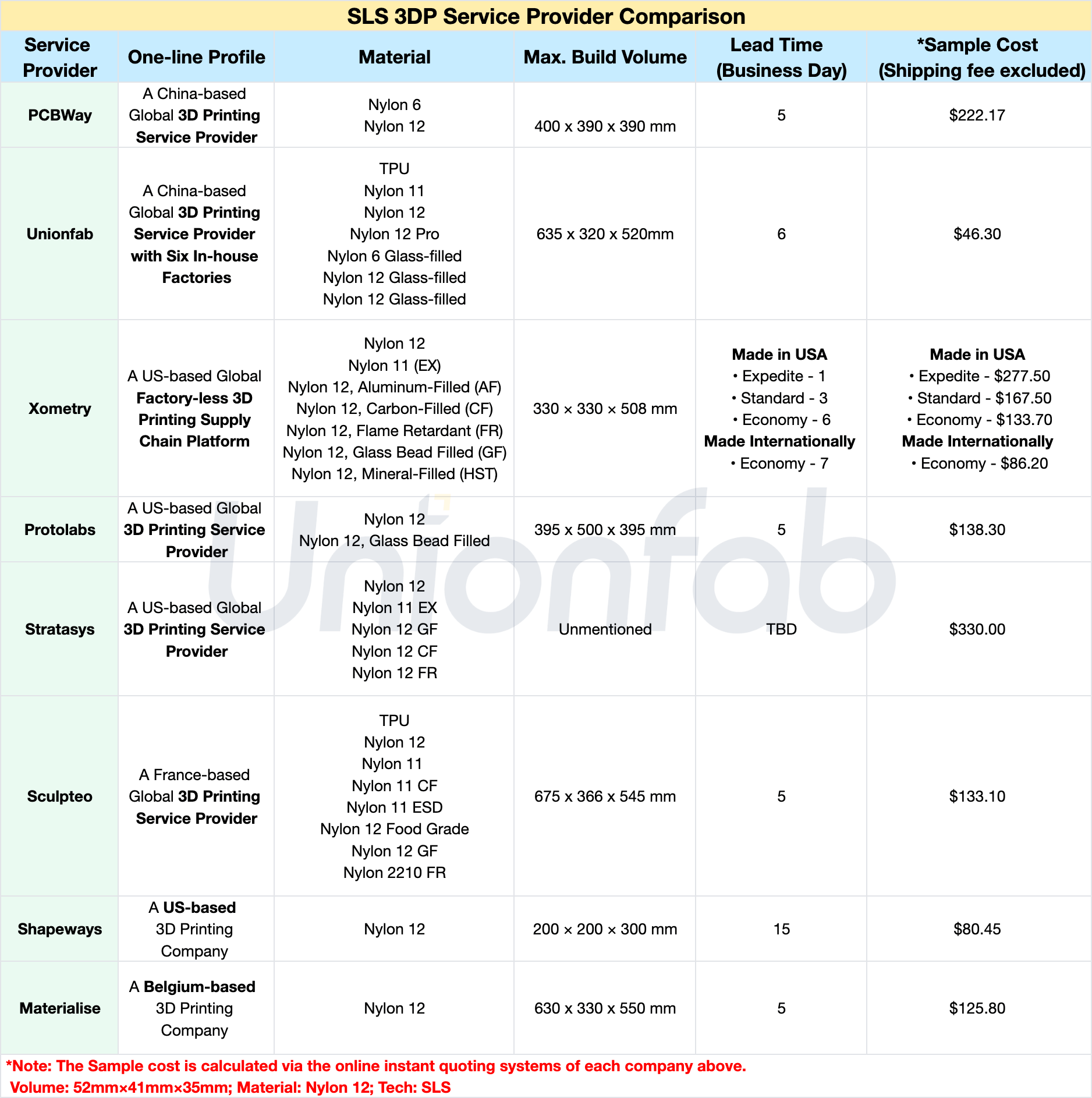
Recommendation:
If cost is a key factor, Unionfab provides the most affordable service.
If you need larger parts, Unionfab, Sculpteo and Materialise are all good options.
If specialized materials are required, Xometry and may be worth considering despite the higher cost.
If you're looking for SLS 3d printing service and want to know exactly how much your 3d model will cost, feel free to try Unionfab's free online cost calculator below. Simply upload your model and get an instant SLS 3d printing quote.
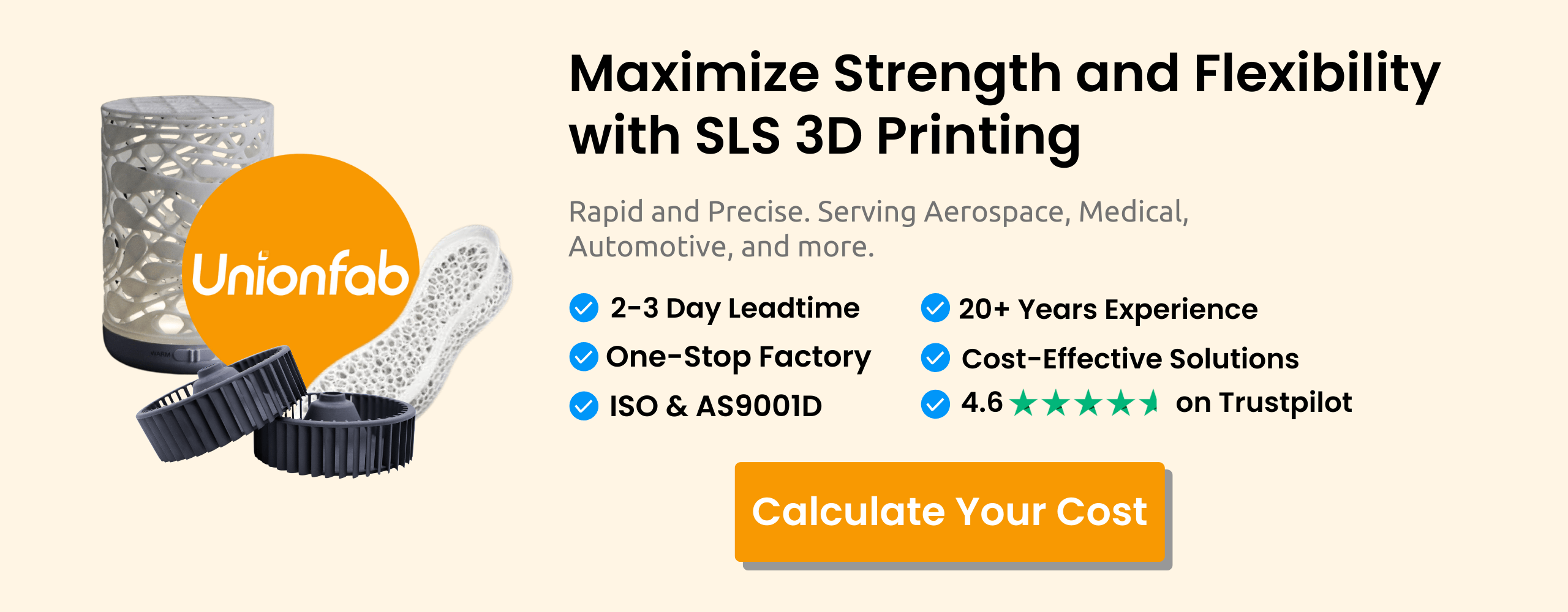
Unlock Unmatched Precision & Durability with Unionfab
With 20+ years of expertise, 1,000+ industrial 3D printers, and 6 cutting-edge factories, Unionfab, certified with ISO 9001, ISO 13485, and AS 9001D, is dedicated to providing high-quality, cost-effective 3D printing services.
To give you a better understanding of our SLS 3D printing capabilities, we’ve prepared a VR video for a virtual factory tour. Click the GIF below to start now!
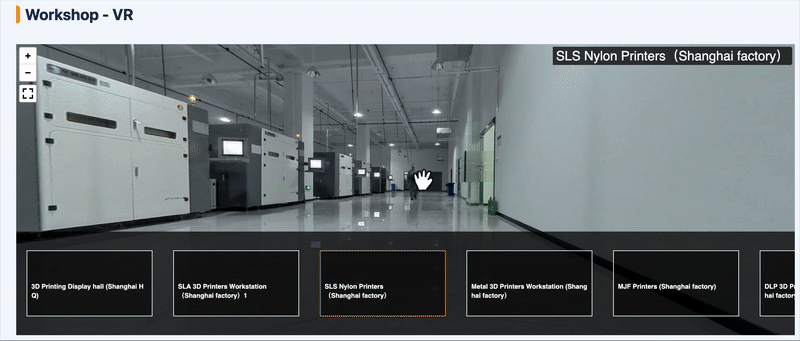
Unionfab’s SLS 3D Printing Service
Here are the details of Unionfab’s SLS 3d printing service.
SLS | |
---|---|
Equipment | EOS; Farsoon |
Materials | TPU |
Max Part Size | 635 x 320 x 520mm |
Layer Thickness | 0.1016 mm |
Tolerance | ±0.3% |
Min. Feature Size | / |
Min. Wall Thickness | 0.762 mm |
Min. Reference Unit Price of Materials | Nylon 12(White): |
Pass Rate | 99.5% |
On-time Delivery Rate |
|
*The actual unit price is subject to real-time inquiry.
If you haven’t used Unionfab’s 3d printing service before, sign up to get 10% discount for your first order.
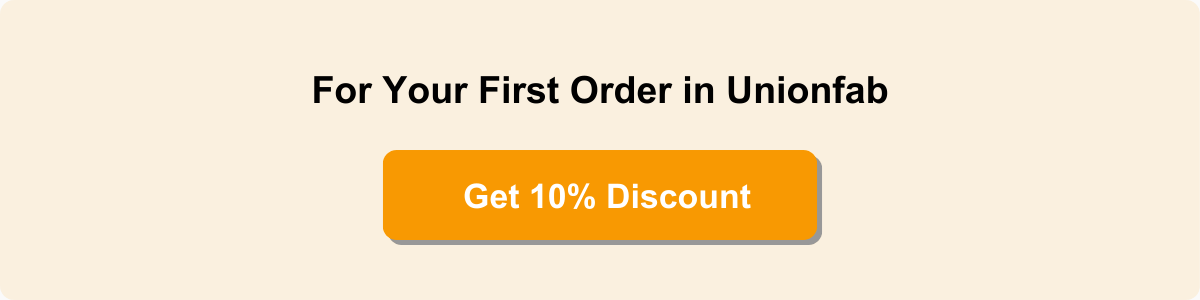
Post-processings for SLS 3D Printing
Except for sls 3d printing, we also offer finishing services. The followings are some of our finished prints.
![]() | ![]() | ![]() |
---|---|---|
![]() | ![]() | ![]() |
SLS 3D Printing Case Displays
The followings are some sls-printed products made by Unionfab.
![]() | ![]() | ![]() |
---|---|---|
![]() | ![]() | ![]() |
![]() | ![]() | ![]() |
FAQs
What does SLS stand for in 3D printing?
SLS stands for Selective Laser Sintering. It is a 3D printing technology that uses a high-powered laser to fuse powdered material (typically nylon) layer by layer, creating durable and complex parts without the need for support structures.
Advantages and Limitations of SLS 3D Printing
Advantages:
No support structures needed – The surrounding powder supports the part during printing, allowing for complex geometries.
Strong and durable parts – Produces high-strength functional prototypes and end-use parts.
Wide material options – Compatible with various nylon-based and composite materials.
High accuracy and detail – Ideal for intricate designs and fine details.
Batch production – Multiple parts can be printed in a single build, optimizing efficiency.
Limitations:
Higher cost – More expensive than FDM and SLA due to the specialized equipment and materials.
Rough surface finish – Printed parts may require post-processing for a smoother finish.
Powder handling – Requires careful material management and post-processing to remove excess powder.
Is SLS printing expensive?
Yes, SLS printing is more expensive than FDM and SLA due to the cost of materials, specialized equipment, and post-processing requirements.
However, it is cost-effective for small to medium batch production and functional prototypes because multiple parts can be printed in one build.
Is SLS printing strong? And what is the strongest material for SLS?
Yes, SLS-printed parts are strong and durable, often comparable to injection-molded plastic. The strength depends on the material used. The strongest materials for SLS include:
Nylon 12 CF (Carbon-Filled) – High strength, stiffness, and lightweight properties.
Nylon 6 – Excellent mechanical strength and heat resistance.
Glass-Filled Nylon – Increased rigidity and heat resistance for industrial applications.
Which is better, SLS, SLA, or FDM?
It depends on the application:
SLS – Best for functional parts, complex geometries, and small-batch production. Strong and durable but more expensive.
SLA – Best for high-detail prototypes and smooth surface finishes. Good for aesthetics but weaker than SLS.
FDM – Best for low-cost prototyping and large parts. Less detailed and weaker than SLS or SLA.
If you need strong, functional parts, go for SLS. If you need high-detail prototypes, choose SLA.
If budget is a priority, FDM is the best choice.