Nylon 6 vs Nylon 66 [+ Free Material Tools]
![Nylon 6 vs Nylon 66 [+ Free Material Tools]](https://ufc-dtc-cms.oss-accelerate.aliyuncs.com/blog/20250401/214555_52nqdv7id.png)
Compare Nylon 6 and Nylon 66 for 3D printing applications with this complete guide. Discover key material differences, use cases, and access free tools from Unionfab including printability tips, comparison tables, and instant quoting.
Introduction
Nylon is a widely utilized engineering thermoplastic, renowned for its strength, durability, and versatility across various industries.
Among its variants, Nylon 6 and Nylon 66 are the most prevalent, each offering distinct properties that cater to specific applications. This comprehensive guide explores their differences, manufacturing processes, performance in 3D printing, CNC machining, and practical considerations.
Chemical Composition and Synthesis
Nylon 6 is produced through the ring-opening polymerization of caprolactam, forming long molecular chains with six carbon atoms in each repeating unit. This results in a material that is more flexible and easier to process.
In contrast, Nylon 66 is synthesized by condensing hexamethylenediamine with adipic acid. Each of these monomers contains six carbon atoms, giving Nylon 66 its name. Its tightly packed molecular structure enhances stiffness and thermal resistance.
Physical and Mechanical Properties
Property | Nylon 66 | |
---|---|---|
Melting Point | ~220°C | ~260°C |
Tensile Strength | Moderate | High |
Flexibility | Higher | Lower |
Impact Resistance | Excellent at low temperatures | Moderate |
Abrasion Resistance | Moderate | High |
Moisture Absorption | Higher | Lower |
Heat Deflection Temp | Lower | Higher |
Chemical Resistance | Good | Excellent |
Printability | Easier | Requires advanced control |
Tip from Unionfab: You can access our full engineering materials library, including Nylon 6 and 66 data sheets and printability ratings, via our Materials Page to compare properties across plastics.
Thermal and Chemical Resistance
Thanks to its higher crystallinity, Nylon 66 maintains its mechanical properties better at elevated temperatures and offers excellent resistance to a wide range of chemicals, particularly acids and solvents.
Nylon 6, while still chemically resilient, performs best in less aggressive environments. Its lower melting point makes it less suitable for parts exposed to prolonged heat.
Nylon 6 and Nylon 66 Processing Methods
Both Nylon 6 and Nylon 66 can be processed using various manufacturing methods, including 3D printing, CNC machining, and injection molding, depending on the application and desired material characteristics.
Nylon 6 is particularly well-suited for Selective Laser Sintering (SLS) 3D printing, where it offers a balance of flexibility, mechanical strength, and printability.
In contrast, Nylon 66 is more commonly used in CNC machining due to its higher melting point and structural stiffness, which require precise thermal control.
In 3D printing, Nylon 6 is favored for producing functional prototypes and load-bearing components with good surface finish. Its low shrinkage rate makes it suitable for large prints, and it performs well in most open or closed 3D printers. Nylon 66, while stronger, is less frequently printed due to warping and printability challenges.
In CNC machining, however, Nylon 66 excels in delivering highly accurate, durable parts for mechanical and industrial uses.
Injection molding is also a common processing method for both materials in large-scale manufacturing, offering excellent surface finish and repeatability, though it requires significant tooling investment.
👉 At Unionfab, we offer full-service processing for these two key materials:
Nylon 6 for SLS 3D Printing: View Nylon 6 Glass-Filled SLS Details
Nylon 6 and 66 are also available as engineering plastics for CNC Machining: Click to Download Datasheet
With in-house capabilities and material expertise, Unionfab helps you choose the best method and material for your specific application.
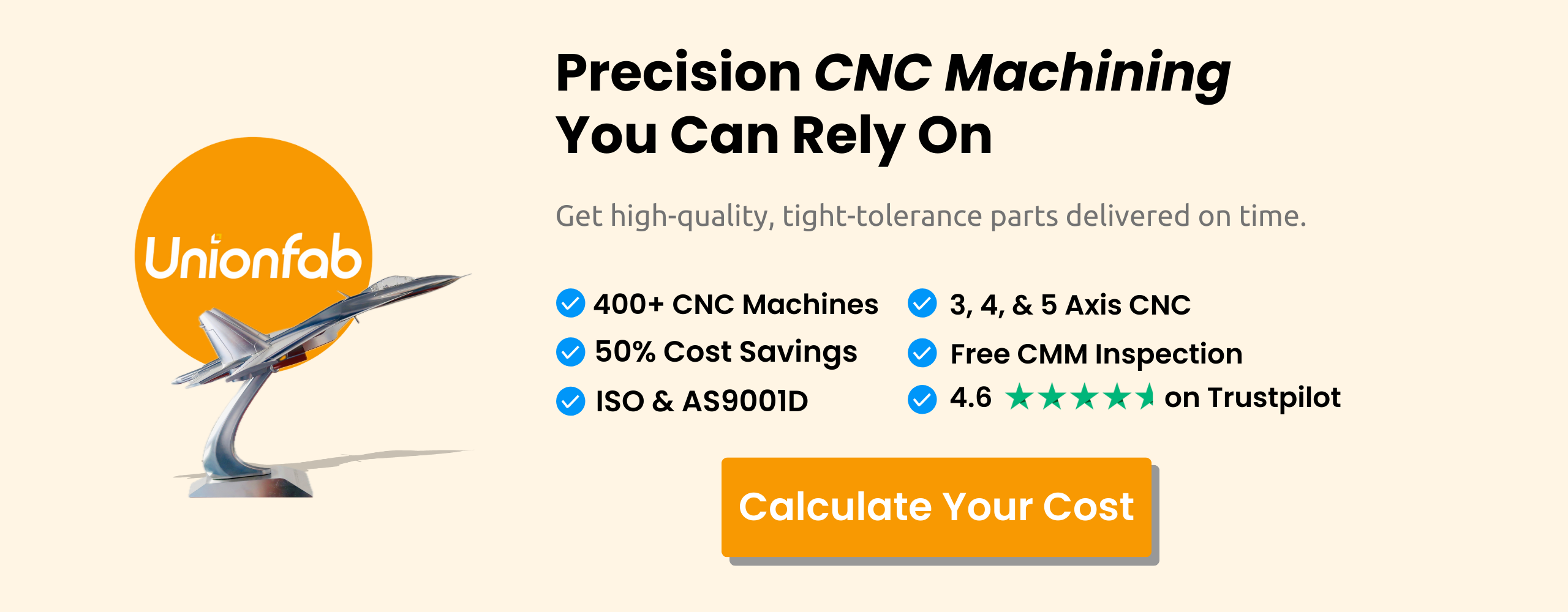
Applications Across Industries
Both nylon variants are used in diverse industries, but their applications vary based on performance needs.
Nylon 6 is widely employed in the textile industry for apparel and industrial fibers. In 3D printing, it is commonly used for brackets, housings, jigs, and other parts where flexibility and ease of printing are important.

Structural Support Bracket with Nylon 6
Source: Unionfab

The bracket shown below was 3D printed using Unionfab’s Nylon 6 Glass-Filled material via SLS technology. It highlights the material’s balance of rigidity and lightweight structure, ideal for load-bearing mechanical components. With excellent print definition and dimensional accuracy, it’s a strong example of Nylon 6 in action for real-world structural parts.
Nylon 66, due to its strength and heat resistance, finds use in demanding environments such as under-the-hood automotive components, electrical enclosures, and custom mechanical parts made through additive manufacturing. Its ability to maintain structural integrity under load makes it suitable for high-performance tools and mechanical end-use parts.
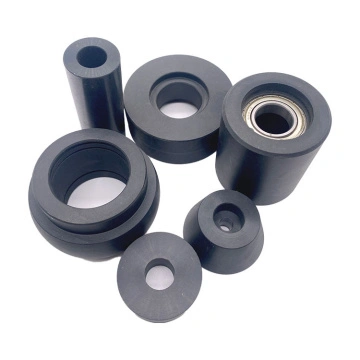
CNC-Machined Nylon 66 Components
Source: honyplastic.com

The image above features a series of precision CNC-machined parts made from Nylon 66. These components demonstrate the material’s excellent dimensional stability, wear resistance, and suitability for mechanical loads and friction-intensive environments.
Nylon 66 is a top choice for structural, insulating, and load-bearing components in the automotive, industrial, and electronics sectors.
Advantages and Disadvantages of Nylon 6 vs. Nylon 66
The following table summarizes the key advantages and disadvantages of Nylon 6 and Nylon 66, helping you quickly identify the best fit for your application:
Feature | Nylon 6 Advantages | Nylon 6 Disadvantages | Nylon 66 Advantages | Nylon 66 Disadvantages |
---|---|---|---|---|
Printability | Easy to print; low shrinkage; forgiving setup | Sensitive to moisture; requires drying | Stronger parts; good layer bonding when tuned | High shrinkage; difficult to print; moisture sensitive |
Mechanical Performance | Flexible; impact-resistant | Lower tensile strength | High tensile strength and stiffness | More brittle; less flexible |
Thermal Resistance | Suitable for general applications | Not ideal for high heat | Excellent heat resistance (~260°C) | Requires high-temp equipment |
Cost Efficiency | Lower cost; good for prototypes | Less suitable for extreme demands | Better long-term performance | Higher material and processing cost |
Dimensional Stability | Acceptable for most prints | Affected by high moisture absorption | Excellent stability; low moisture uptake | Requires precise control during post-processing |
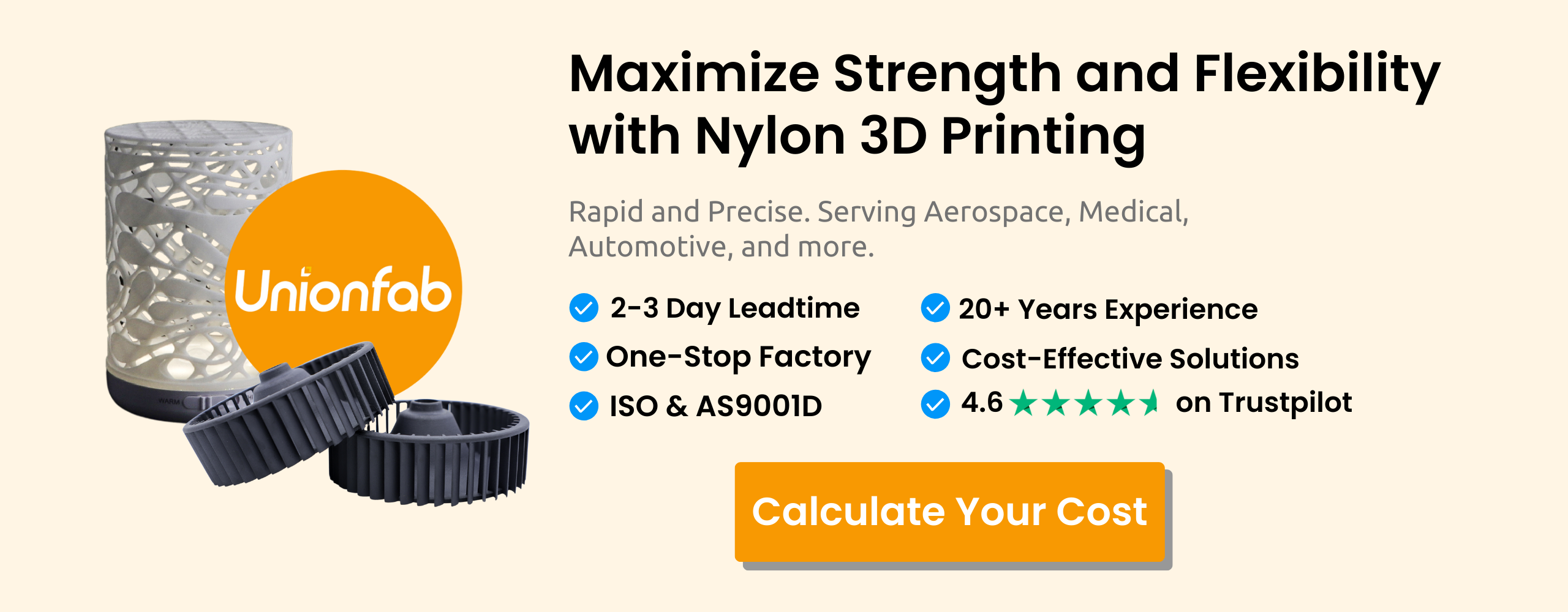
Considerations for Material Selection in 3D Printing
The table below outlines the key considerations when choosing between Nylon 6 and Nylon 66 for 3D printing, helping engineers and designers align material properties with project requirements:
Consideration | Nylon 6 | Nylon 66 |
---|---|---|
Ease of Printing | High – forgiving setup and low shrinkage | Low – requires heated chamber and tuning |
Part Complexity | Suitable for large, complex geometries | Best for simpler geometries with fewer warping risks |
Mechanical Load | Moderate strength, high flexibility | High strength and rigidity under load |
Temperature Resistance | Moderate (not for high-heat environments) | Excellent – up to ~260°C |
Dimensional Accuracy | Good with minimal warping | Excellent but needs controlled environment |
Cost Sensitivity | Lower cost, good for prototyping | Higher cost, suitable for critical parts |
Moisture Sensitivity | High – needs careful drying | Lower – more stable in humid conditions |
Use these criteria to determine which nylon type best suits your production needs, whether it’s for prototyping, functional parts, or industrial applications.
Conclusion
Both Nylon 6 and Nylon 66 are valuable materials in the world of 3D printing, each offering unique benefits depending on your project’s requirements. Nylon 6 is well-suited for users prioritizing ease of printing and flexibility, while Nylon 66 is the better choice for high-performance, load-bearing applications.
Understanding their properties and trade-offs allows you to make an informed decision—and with support from Unionfab, you can ensure optimal results for your next nylon 3D printing project.
Unionfab: Your Partner in Nylon 3D Printing
At Unionfab, we provide expert 3D printing solutions tailored to Nylon 6 and Nylon 66 materials.
Our professional team can guide you through the material selection process and ensure your parts meet the highest standards of strength, accuracy, and reliability.
Whether you're developing functional prototypes or production-grade components, Unionfab is your trusted partner.
Need help selecting the right material? Contact Unionfab for expert guidance and a custom quote.
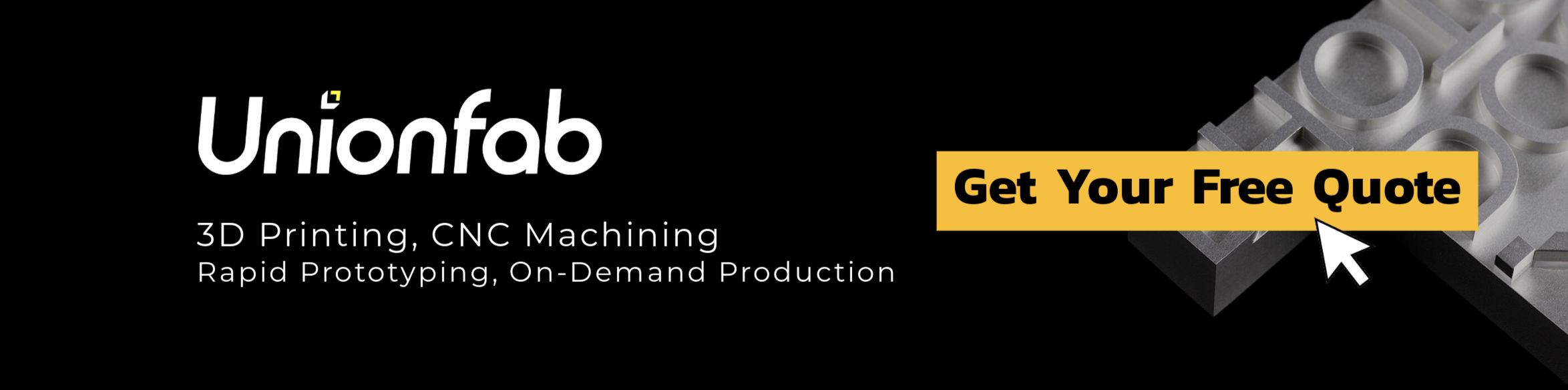
FAQs: Nylon 6 vs Nylon 66 in 3D Printing
Which is easier to 3D print, Nylon 6 or Nylon 66?
Nylon 6 is generally easier to print. It offers better layer adhesion and lower shrinkage, which helps reduce warping and increases printing consistency across a variety of printers.
Can Nylon 66 be printed on a desktop FDM printer?
It is possible, but Nylon 66 performs best with an enclosed or heated build chamber. The higher processing temperature and shrinkage require strict environmental control for optimal results.
Is Nylon 66 stronger than Nylon 6 after printing?
Yes. Nylon 66 provides greater tensile strength, stiffness, and thermal resistance, making it ideal for high-performance applications where mechanical stress is a concern.
Which nylon is better for prototyping?
Nylon 6 is preferred for prototyping due to its forgiving print behavior, lower cost, and good balance of strength and flexibility.
Should nylon filament be dried before printing?
Absolutely. Both Nylon 6 and Nylon 66 are hygroscopic, meaning they absorb moisture from the air. Filament should be thoroughly dried before printing to avoid defects like bubbling, stringing, and weak layer adhesion.