MJF 3D Printing: The Ultimate Guide [+ 2025 Service Providers]
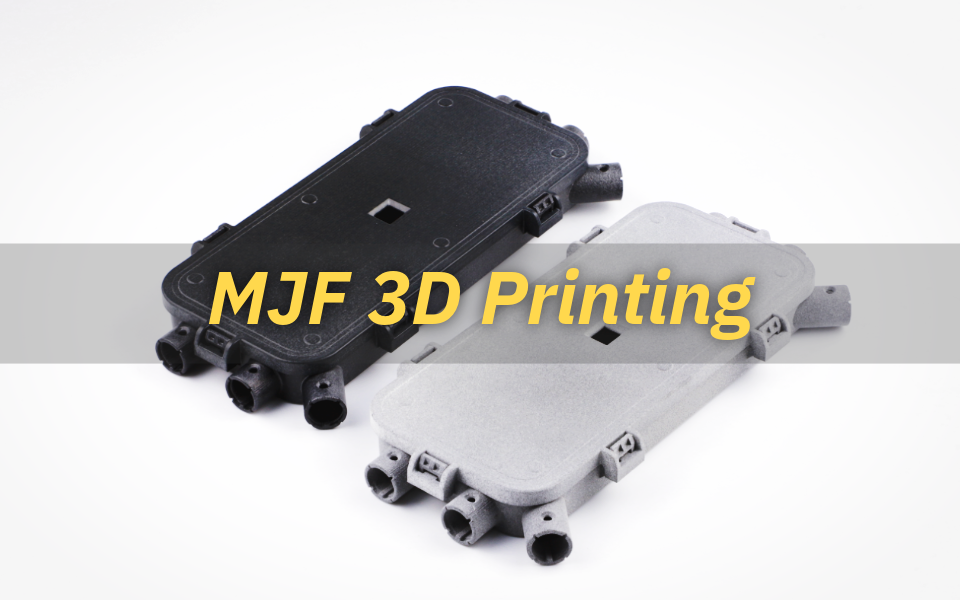
Explore Multi Jet Fusion — the fastest & most functional polymer 3D printing technology — with Unionfab’s ultimate guide.
Introduction
Need rapid production of durable, high-precision plastic parts? Multi Jet Fusion (MJF) is one of the most advanced 3D printing technologies available today—up to 10× faster than SLS, with excellent strength, fine detail, and smooth finishes straight off the printer.
In this guide, we’ll break down how MJF works, the best materials to use, cost factors, real-world applications, and best MJF service providers 2025—so you can decide if it’s right for your project!
What is MJF 3D Printing?
Developed by HP, Multi Jet Fusion (MJF) is a powder bed fusion 3D printing process designed to produce functional, end-use plastic parts with industrial-grade performance. It primarily uses nylon-based materials like PA12 and PA11.
How It Works
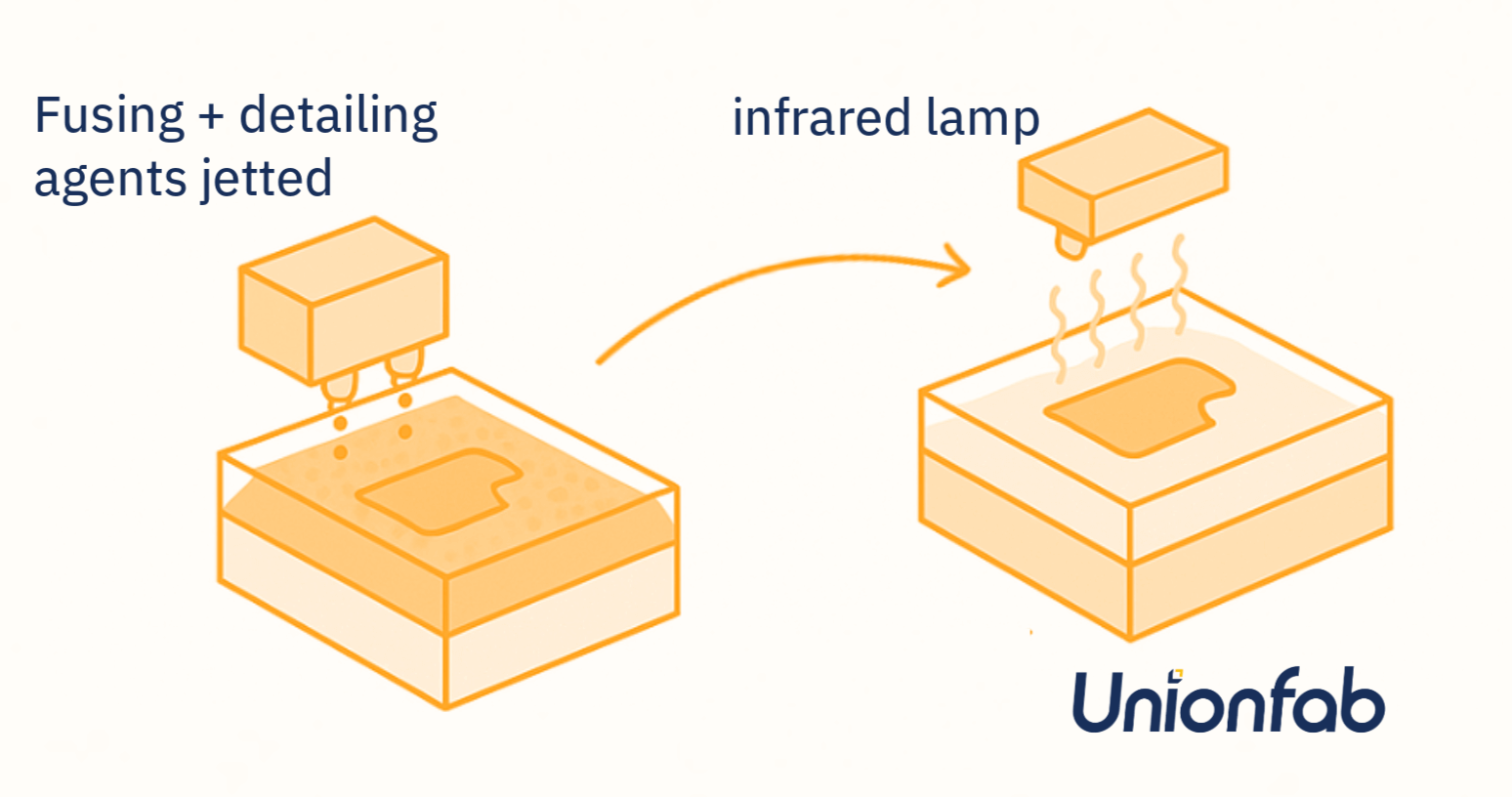
Instead of using lasers like SLS, MJF jets a fusing agent and detailing agent onto a powder bed, then fuses the material using infrared light. This speeds up the process and ensures consistent quality across builds.
Key Advantages of MJF
Feature | Benefit |
---|---|
Ultra-fast Production | Up to 10× faster than SLS—ideal for prototyping & low-volume runs |
Functional Strength | Comparable to injection molding—great for parts under stress |
High Precision | Supports complex geometries & fine details |
Smooth Surface Finish | Parts come out with uniform texture, ready for coloring & post-processing |
Why Choose MJF for Your Project?
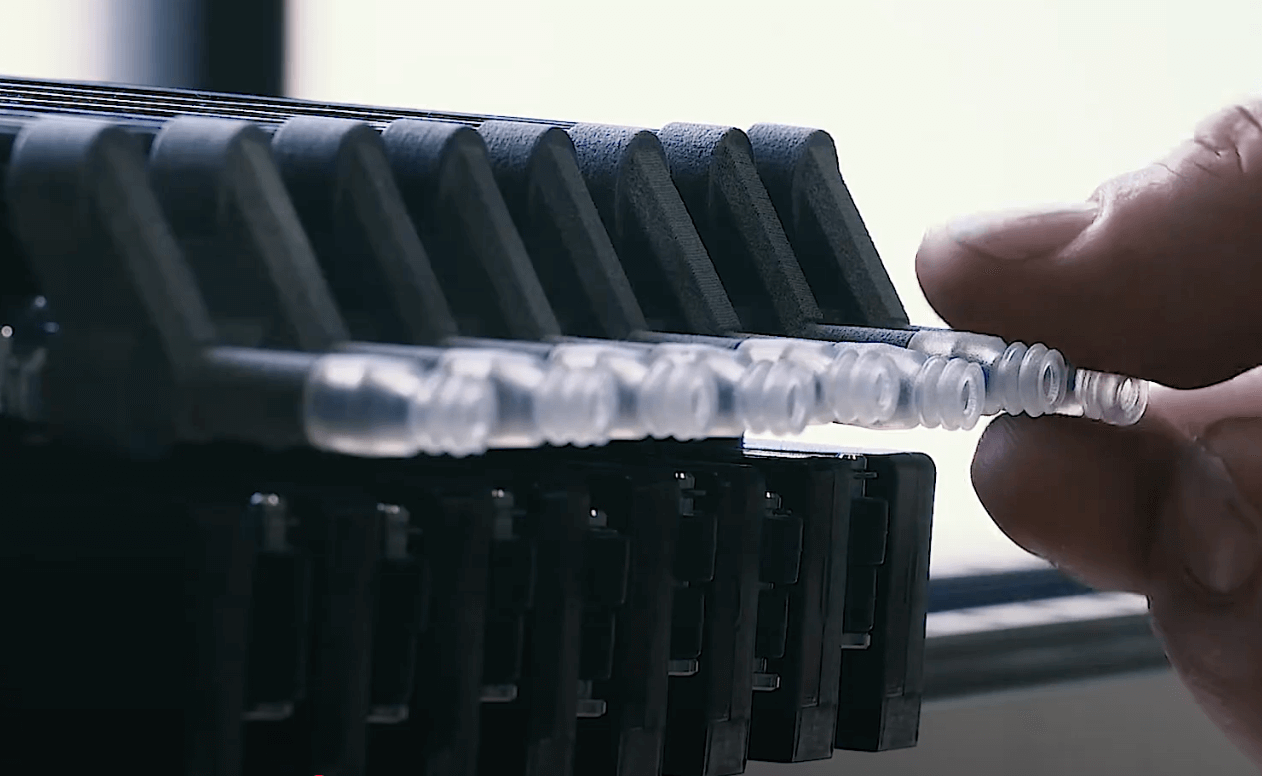
leak-resistant parts for machinery, optimizing design and reducing costs.
MJF combines speed, strength, and design freedom. Whether you're creating one prototype or 10,000 end-use parts, MJF delivers reliable results for:
Short lead times
Functional testing
Production-grade durability
Perfect for industries like:
Industry | Applications | Parts Made by Unionfab | Key Benefits |
---|---|---|---|
Automotive | Functional parts, in-car brackets | ![]() | Heat-resistant, lightweight |
Medical | Prosthetics, orthopedic braces, medical instruments | ![]() | Custom-fit, biocompatible materials |
Consumer Electronics | Complex components, impact-resistant parts | ![]() | High detail, durable |
Industrial Manufacturing | Jigs, custom tools, device casings | ![]() | Strong, precise, customizable |
Ready to get started? Request a Free Quote or Talk to an Expert to see how MJF fits your next project.
How Does Multi Jet Fusion Work?
Let’s explore how this technology works under the hood:
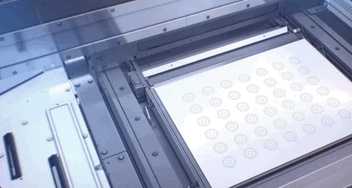
Multi Jet Fusion builds parts layer by layer using a precise combination of fusing agents, detailing agents, and infrared energy.
Unlike SLS, which sinters powder point-by-point using a laser, MJF fuses entire cross-sections of a layer in a single pass, significantly boosting efficiency.
At the heart of this speed is HP’s dual-carriage system:
One carriage selectively jets fusing and detailing agents onto the powder bed.
The second carriage immediately follows with infrared energy, fusing the powdered areas marked by the agents.
This unique system enables simultaneous recoating and fusing, eliminating downtime between layers and making MJF up to 10x faster than selective laser sintering (SLS).
The result? High-quality, functional parts with excellent mechanical properties, minimal visible layer lines, and smoother surfaces—perfect for industries like automotive, medical, and aerospace.
Material Options for MJF 3D Printing
MJF supports a range of engineering-grade, powder-based thermoplastics—each tailored for different functional needs. Here’s a comparison of the top materials:
Material | Key Properties | Best For | Notable Features |
---|---|---|---|
✔ High strength & stiffness | Functional prototypes; | ✅ Strong & durable | |
✔ More flexible than PA12 | Medical devices; | ✅ Greater ductility | |
PP (Polypropylene) | ✔ Lightweight & flexible | Automotive reservoirs; | ✅ Watertight capabilities |
✔ Rubber-like flexibility | Footwear; | ✅ Impact absorbing | |
✔ High stiffness | Jigs & fixtures; | ✅ 30–40% glass bead filling |
Want to Explore Nylon/TPU 3D Printing in Detail?
Key Material Comparison Chart
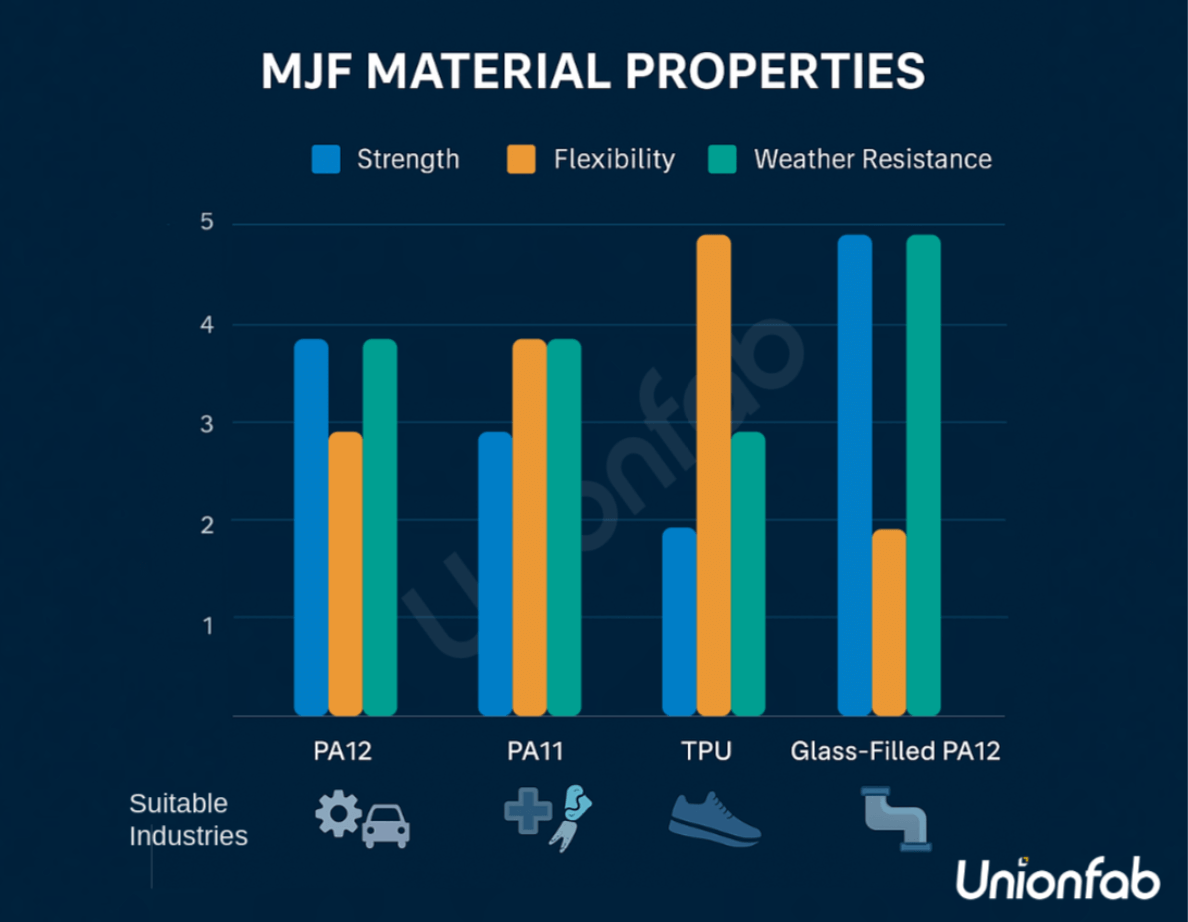
Need help choosing the right material? Speak with an MJF specialist now →

MJF vs SLS vs SLA vs FDM: Which 3D Printing Technology Is Right for You?
Different 3D printing technologies bring unique advantages depending on your project goals. Here's how Multi Jet Fusion (MJF) compares to other major processes:
Feature | ||||
---|---|---|---|---|
Technology | Inkjet + infrared fusion of powder | Laser sintering of powder | UV curing of liquid resin | Extrusion of melted filament |
Speed | 🚀 Fastest (10× faster than SLS) | Slower due to laser scanning | Moderate (depends on resin curing) | Slow, layer-by-layer extrusion |
Material | Nylon (PA 12, PA 11), TPU | Nylon, TPU, composites | Photopolymer resin | PLA, ABS, PETG |
Part Strength | High (close to injection molding) | Strong and durable | Brittle, best for aesthetics | Moderate strength |
Surface Finish | Smooth, uniform, suitable for dyeing | Slightly rough, requires post-processing | Best detail & smoothest finish | Layer lines visible |
Best For | Functional prototypes, low-volume production | Industrial parts, functional prototypes | High-detail prototypes, casting patterns | Hobby projects, low-cost prototyping |
Cost | $$ – Efficient powder reuse reduces cost | $$ – $$$: Diverse material options with a wide price range | $ -$$$ – Diverse resin options with a wide price range | $ – Most affordable |
Key Takeaways:
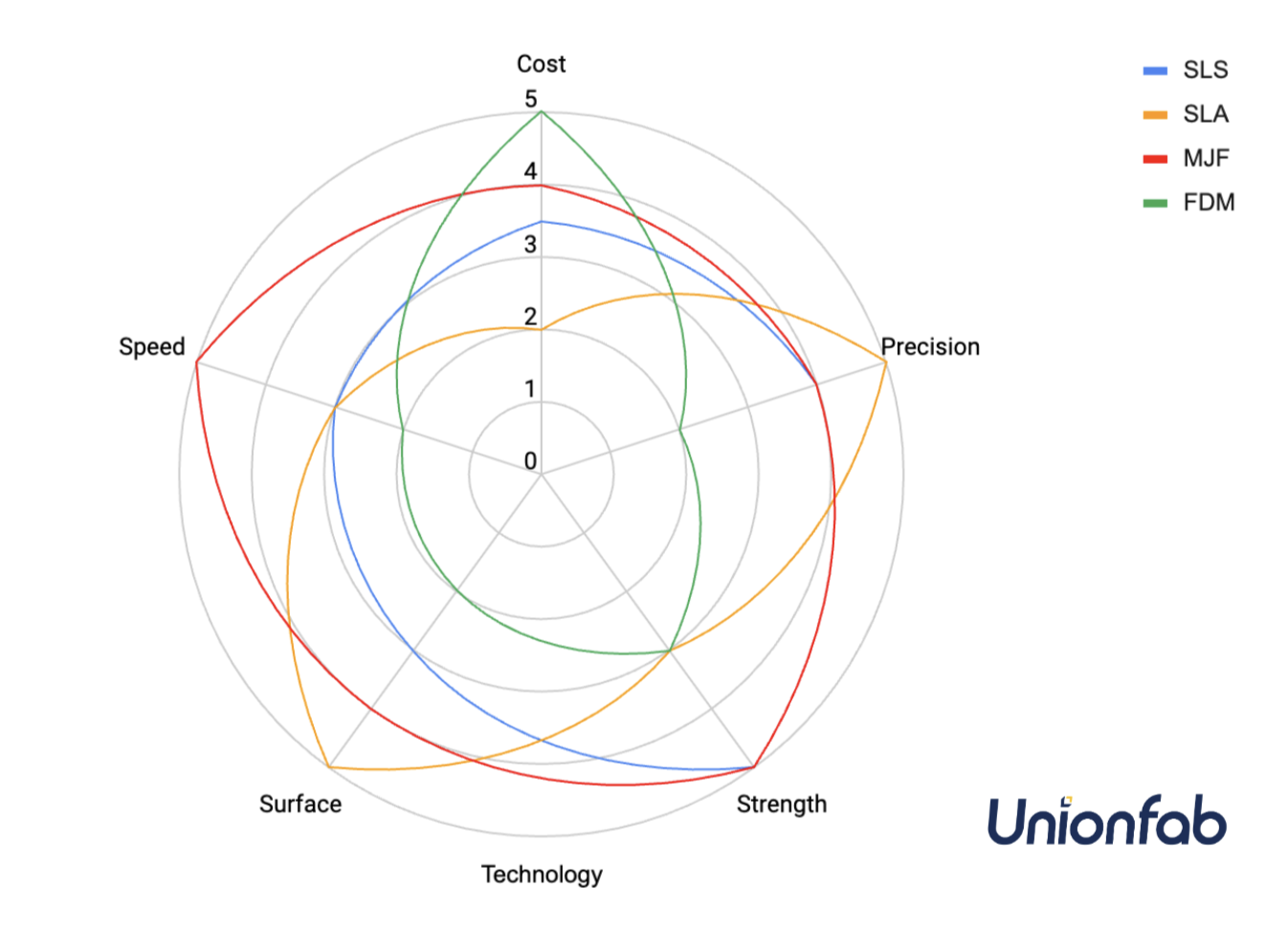
MJF strikes the best balance of speed, performance, and scalability. It’s ideal for producing industrial-grade polymer parts with high strength, fine detail, and consistent quality—without breaking the bank.
While SLS is ideal for industrial applications, and SLA excels in high-detail prototypes, FDM remains the most affordable option for basic prototyping.
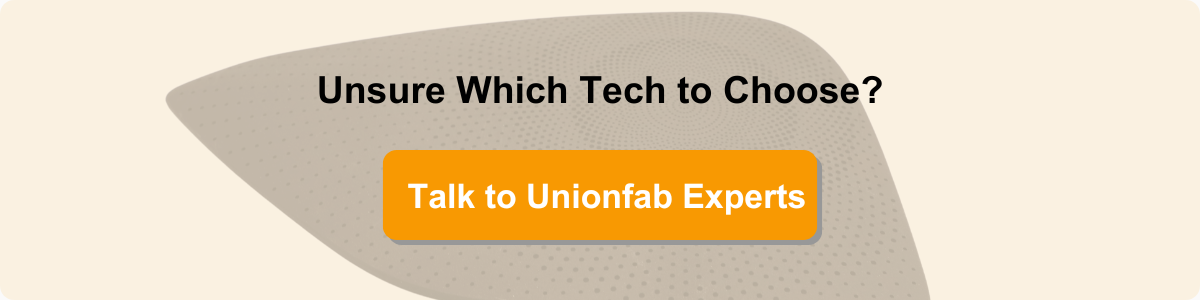
MJF (Multi Jet Fusion) 3D Printing Cost Breakdown
Wondering how much MJF really costs? Here's a full look at the key cost drivers—whether you're producing in-house or outsourcing to a service provider.
In-House Production Cost
Key cost factors in MJF printing include:
Machine Cost
Drawback: Industrial MJF systems like the HP Jet Fusion 5200 range from $200,000 to $400,000, depending on build size and automation features.
Advantage: Despite the high upfront investment, high throughput and material reuse help significantly reduce the long-term cost per part—especially at scale.
Material Cost
Drawback: MJF uses nylon-based powders like PA12, typically priced at $50–$80 per kilogram, which can add up quickly.
Advantage: However, the ability to reuse 70–80% of unused powder keeps material waste and ongoing costs low, particularly in batch production environments.
Post-Processing Cost
Drawback: While some cleanup is still needed, basic post-processing like bead blasting can cost $3–$10 per part, depending on geometry and surface requirements.
Advantage: MJF parts don’t require support structures, resulting in less manual labor, shorter lead times, and smoother workflows.
ROI Analysis: Is MJF Worth the Investment?
While MJF machines come with a high upfront cost, their superior production speed, minimal post-processing, and efficient powder reuse can deliver a strong return on investment (ROI), depending on production volume.
You’ll benefit most if:
You're producing 10,000+ parts per year
You need rapid iteration without supplier delays
You want tight control over design and production workflows
When to Use a 3D Printing Service Instead?
Outsourcing to a service provider like Unionfab can be smarter in many scenarios:
In-House (DIY) | Outsourcing (Via Service Provider) |
---|---|
✔ High print volume (>10,000 parts/year) | ✔ Low to mid volume (<5,000 parts/year) |
✔ Need for fast internal turnaround | ✔ Occasional or on-demand printing |
✔ Full control over design iterations | ✔ Access to wide material/finish options |
❌ High initial capex & maintenance | ✔ Zero upfront investment |
❌ Limited material inventory | ✔ One-stop access to latest technologies |
Get real-time pricing for your MJF parts—just Upload Your 3D File and get a quote within a minute.
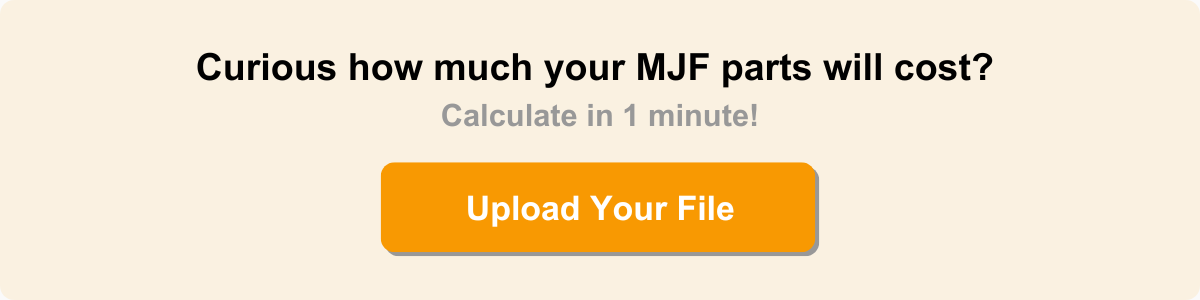
How to Choose the Right MJF 3D Printing Service in 2025?
With so many MJF 3D printing providers on the market, it’s easy to feel overwhelmed. Pricing, lead times, materials, and reliability all vary widely.
To help you choose wisely, we’ve created a detailed side-by-side comparison of the top MJF 3D printing services in 2025.
Compare Top MJF 3D Printing Service Providers in 2025
We evaluated the top service providers based on materials offered, build capacity, lead times, sample costs, and Trustpilot reviews.
Service Provider | Profile | Material | Lead Time | *Sample Cost | Trustpilot |
---|---|---|---|---|---|
PCBWay | Leading PCB Manufacturer and Prototyping Services | PA 12 | 3-4 Days | $61.84 | |
Unionfab | China-based Global 3D Printing Service Provider; Six In-house Factories | •Nylon 12 (PA 12) | 3 Days | PA 12: $51.9 | |
Xometry | Global Factory-less 3D Printing Supply Chain Platform | •Nylon 11 | •Expedite: 1- 4 Days | Nylon | |
Protolabs Network | A US-based Global 3D Printing Service Provider | •PA 12 | 3-5 Days | PA 12: $84.28 | |
Stratasys | A US-based Global 3D Printing Service Provider | Nylon 12 | 3 | $75.91 | Not listed |
RapidDirect | China-Based Manufacturing services | Nylon 12 | 5 | $78.35 |
Key Takeaways: Who Comes Out on Top?
Best Value: Unionfab – starting from $51.90; reliable in-house production.
Fastest Turnaround: Unionfab and Stratasys offer 3-day lead times. Xometry provides 1–4 days with expedited service.
Flexible Options: Xometry – Offer TPU and PP, Flexible Delivery Speeds.
Highest Trustpilot Rating: Tie between Xometry and RapidDirect (4.7), Unionfab follows closely at 4.6.
What to Look for in an MJF Printing Service
Beyond cost and speed, consider these key criteria:
Industrial-Grade Equipment Ensure the provider uses professional HP MJF 4200 or 5200 printers for consistent quality.
Finishing Capabilities Look for post-processing options like dyeing, polishing, sealing, or coating—essential for end-use parts.
Transparent Pricing Choose services offering instant quotes, volume discounts, and no hidden fees.
Quality Assurance Need tight tolerances? Look for providers that offer CMM inspection or dimensional reports.
Logistics & Support Global shipping, real-time support, and fast communication are vital for meeting deadlines and reducing risk.
Why Unionfab Is the Smart Choice for MJF Printing
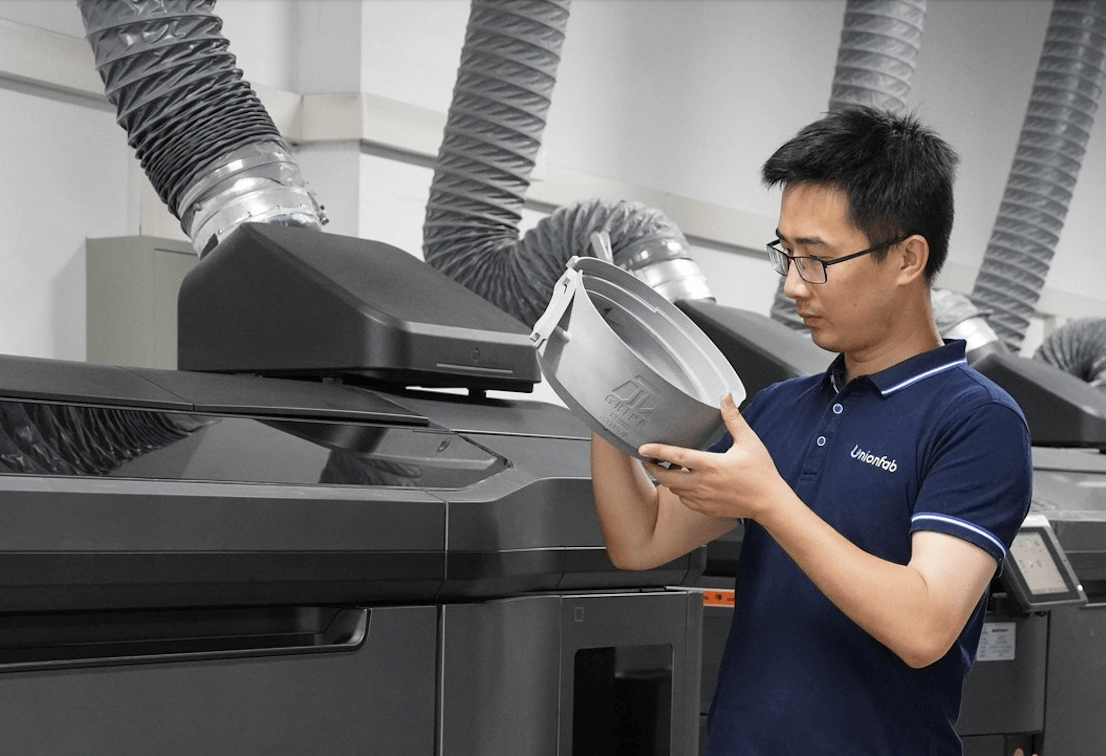
With 20+ years of manufacturing experience, Unionfab is one of the few providers offering full-spectrum industrial MJF 3D printing with unmatched value, speed, and service:
In-House Production Scale
10× HP MJF 4200 printers
8× HP MJF 5200 printers
6 dedicated production facilities across China
⠀Fast, Accurate, and Reliable
3-Day standard lead time
CMM inspection for critical tolerances
Full batch traceability and documentation
⠀Hassle-Free Ordering, Support & After-Sales
Real-time quoting & order tracking
24/7 online support, global shipping & after-sales policy
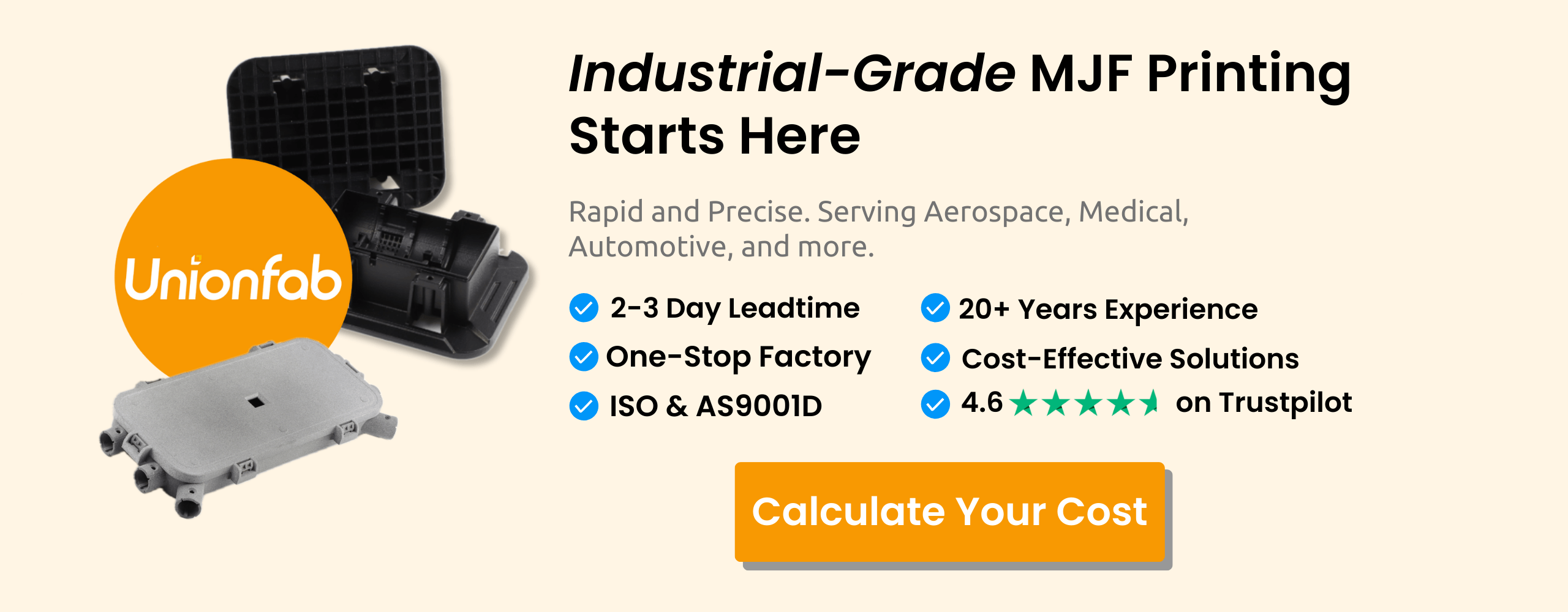
Post-Processing Techniques for MJF 3D Printing
Post-processing is essential to improve aesthetics, surface quality, and environmental performance—especially for end-use or customer-facing products.
Common Post-Processing Methods for MJF
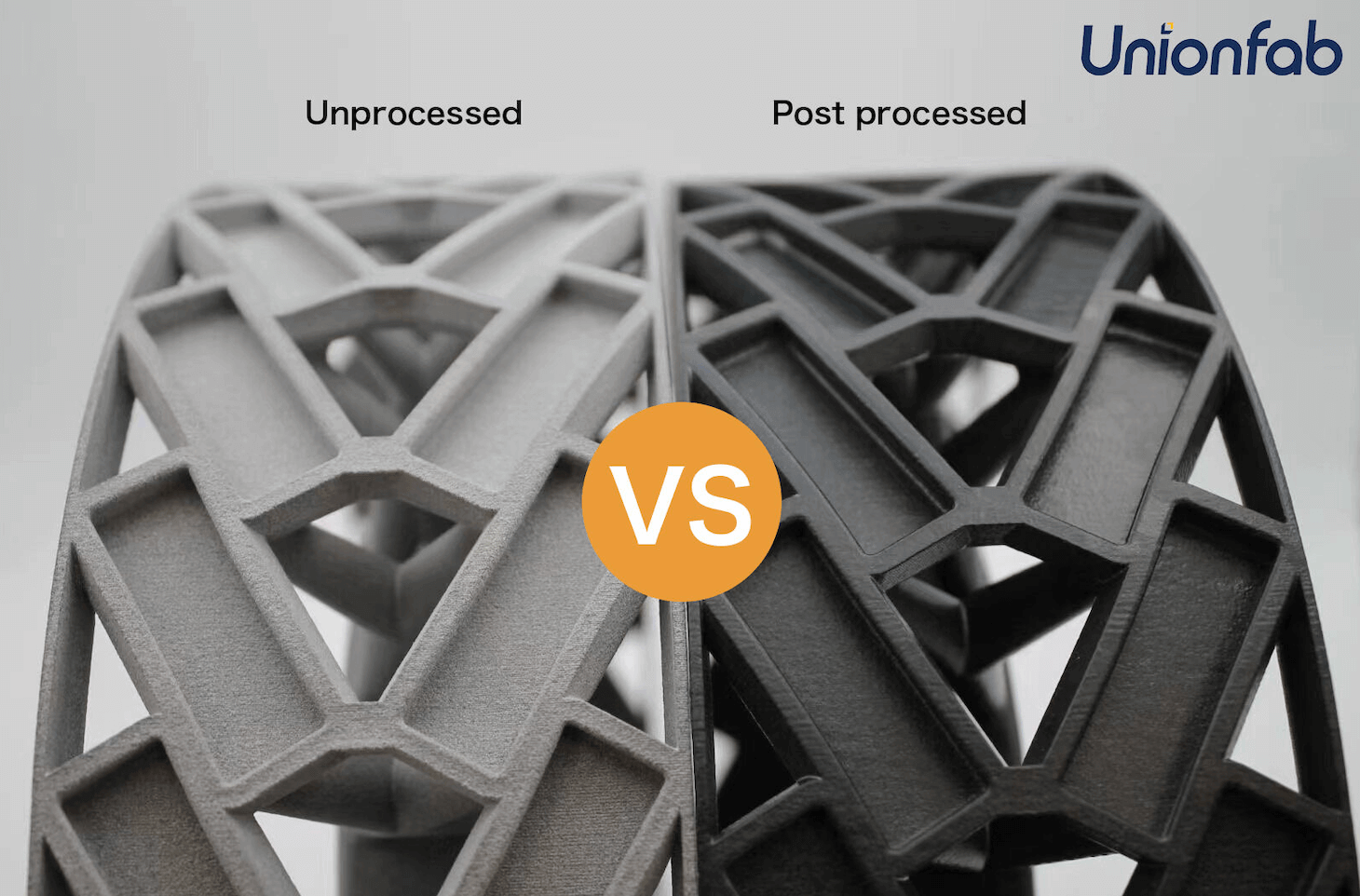
Cleaning & Surface Smoothing Bead blasting or media tumbling removes residual powder and provides a uniform matte finish.
Dyeing Since MJF parts are naturally gray, dyeing is used to achieve deep black or custom colors (e.g., red, blue) for branding or cosmetic appeal.
Polishing Mechanical polishing or chemical smoothing enhances surface smoothness for a semi-gloss, consumer-ready finish.
Coating & Sealing Various coatings improve wear resistance, waterproofing, or chemical durability, making MJF parts suitable for demanding environments.
Advanced Finishing Options at Unionfab
In addition to standard post-processing, Unionfab offers a wide variety of professional-grade plastic finishing techniques to meet specialized requirements:
Laser Engraving | Regular Spray Paint | Nickel Plating | Tin Plating | Zinc Plating |
---|---|---|---|---|
Crackle Paint | Matte Finish | Glossy Finish | Sandblasting | Texture Etching |
Mold Etching | Electroplating | Electrolytic Plating | Vacuum Plating | Silk Screen Printing |
Pad Printing | Water Transfer Printing | Heat Transfer Printing | Hot Stamping | UV Printing |
Whether you want your part to look premium, resist harsh conditions, or meet specific regulatory standards, Unionfab’s finishing capabilities have you covered!
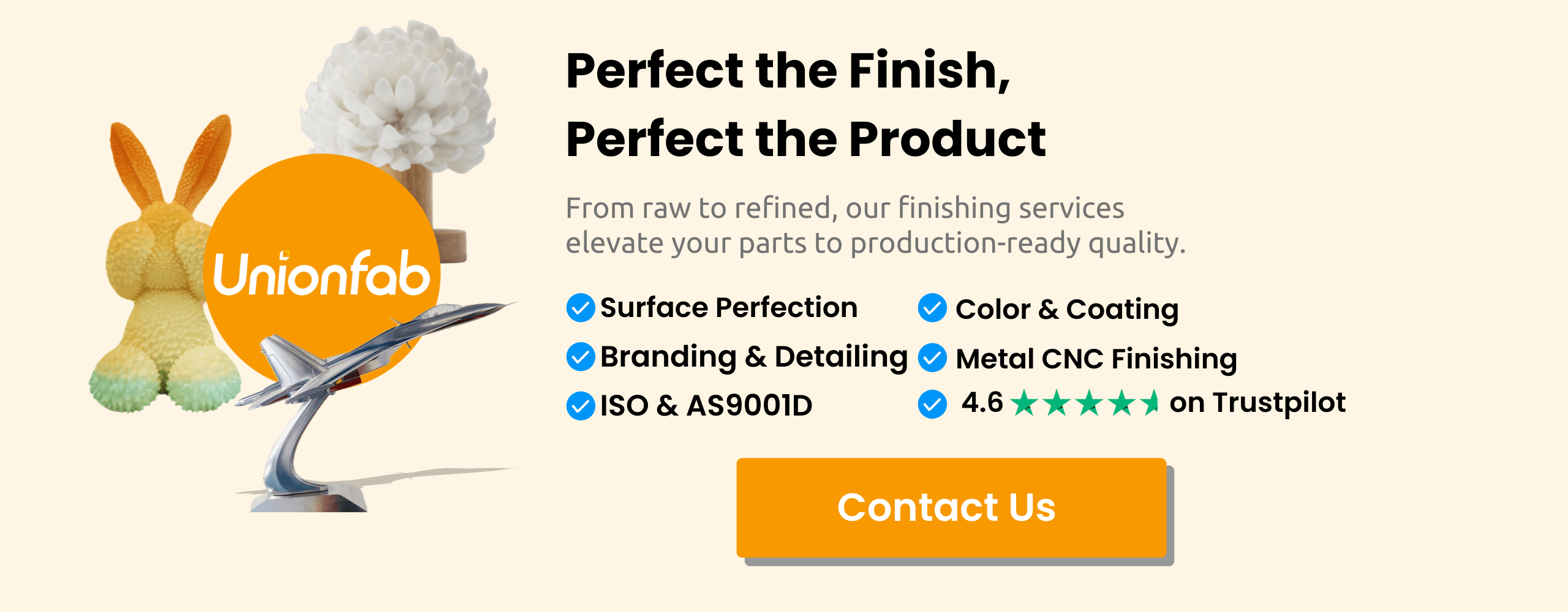
FAQs About MJF 3D Printing
Can MJF parts be used outdoors?
Yes! PA12 parts offer solid moisture and abrasion resistance. For long-term outdoor use, adding UV-resistant coatings is recommended to prevent fading or brittleness.
What’s the minimum order volume for MJF parts?
At Unionfab, there is no MOQ. Whether you need one prototype or 10,000+ parts, we scale to your needs.
Is MJF waterproof?
Right out of the printer, MJF parts are not fully waterproof due to the porous nature of nylon powder. That said, with post-processing techniques like sealing, vapor smoothing, or coating, you can significantly improve water resistance.
So yes, waterproofing is possible—just not entirely "as-printed."
Does MJF printing need supports?
One of the major advantages of MJF is that it doesn’t require support structures. The surrounding powder provides all the support your part needs, which means more design freedom, less material waste, and faster turnaround times.
What are the advantages of MJF?
MJF is known for its:
High detail and dimensional accuracy
Smooth, consistent surface finish
Excellent mechanical strength (especially with PA12)
No support structures needed
Great for both prototyping and functional end-use parts
Cost-effective for low to mid-volume production
What are the disadvantages of MJF?
Like any process, MJF isn’t perfect for everything. Here’s where it has some limitations:
Limited material selection compared to other 3D printing methods
Surface finish is matte and slightly grainy without post-processing
Parts may require sealing for water- or air-tightness
Initial equipment cost (for in-house use) is relatively high