Guide to Brushed Finish [+Maintenance Tips]
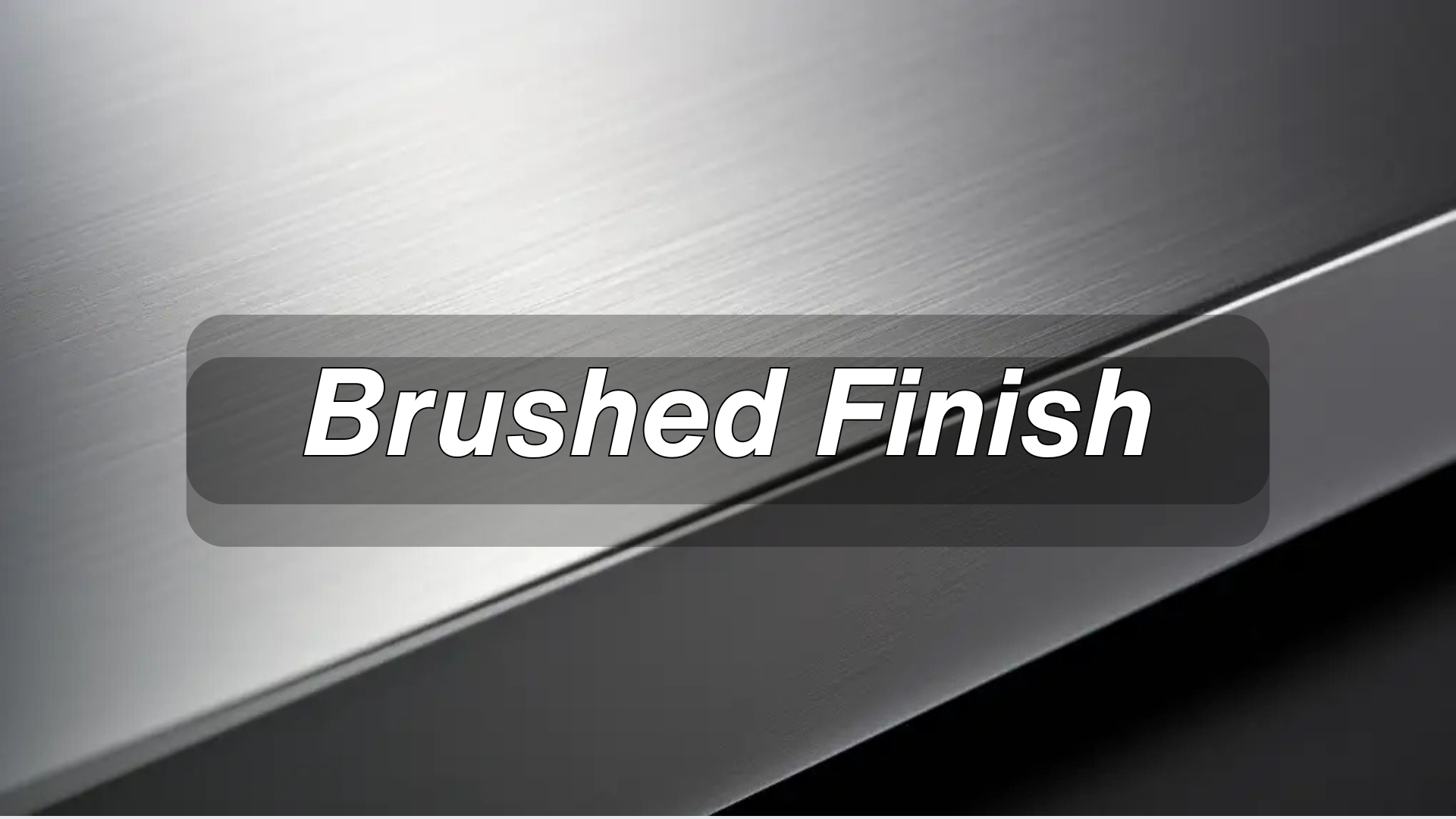
Discover the basics of brushed finish, tell its differences with polished and painted finishes and get maintenance tips to keep your surface durable.
Introduction
A brushed finish is a versatile and widely adopted surface treatment that enhances both the aesthetics and functionality of metal materials.
By imparting a uniform, textured appearance characterized by fine parallel lines, this finish offers a modern, sophisticated look while also providing practical benefits.
In this guide, we’ll break down everything you need to know about brushed finishes—from what they are to how to choose the right one for your project.
What Is Brushed Finish?
A brushed finish creates a smooth, matte surface with subtle, parallel texture lines (brush strokes) using abrasive materials like sandpaper, wire brushes, or abrasive pads.
Unlike polished finishes, it’s non-reflective and hides fingerprints, smudges, and minor imperfections, making it popular for both decorative and high-use items.
How to Do a Brushed Metal Finish
Achieving a perfect brushed metal finish involves selecting the right tools and carefully following each process step. Here’s a simplified guide:
Tools You Will Need
Cleaning Supplies:
Soap and water or a specialized degreaser to remove grease, rust, or debris from the metal surface.
Abrasive Tools:
Abrasive pads or sanding discs in various grits. Start with a medium grit (around 240–400) for rough work, then use higher grits (800–1200) for a smoother, refined finish.
A wire brush or an abrasive brush can also be used, depending on the metal and the desired effect.
Type | Applications |
---|---|
Wire Brush | Heavy-duty cleaning, removing rust/paint, creating coarse brush strokes on steel. |
Sandpaper (Various Grits) | Initial shaping (low grit, e.g., 80–240); refining texture (high grit, e.g., 800–1200). |
Abrasive Pads | Curved/smooth surfaces (e.g., aluminum rims, stainless steel appliances). |
Buffing Wheels | Final polishing to enhance smoothness and subtle sheen on brass/nickel. |
Nylon Brushes | Gentle cleaning/polishing on soft metals (copper, aluminum) without scratching. |
Cloths and Solvents:
A soft cloth for cleaning and wiping down the surface.
A suitable solvent to remove any leftover abrasive residue after the brushing process.
Step-by-Step Process
Prepare the Surface:
Begin by thoroughly cleaning the metal to remove any grease, rust, or debris. Using soap and water or a degreaser ensures that the surface is spotless and ready for finishing.
Select the Right Abrasive Grit:
For the initial stage, use a medium grit (240–400) abrasive pad to create a rough texture on the metal surface. This step is key for establishing the fundamental brushed pattern.
Once the heavy texture is created, move on to finer grits (800–1200) to smooth out the lines and enhance the finish.
Apply Uniform Pressure:
Using the chosen abrasive tool, work the surface with a consistent, back-and-forth motion. Whether you prefer straight, circular, or random strokes, the key is to maintain uniform pressure throughout. This consistency ensures an even, professional-looking brushed texture.
Final Cleanup:
Once the brushing is complete, clean off any abrasive residue by wiping the surface with a soft cloth or the recommended solvent. This final step not only removes debris but also reveals the true, refined look of your brushed finish.
Following these simple tools and steps will help you achieve a sleek brushed metal finish that enhances both the aesthetic and durability of your product.
Types of Brushed Metal Finish (By Pattern and Texture)
Brushed finishes are a popular metal surface treatment that enhances both the aesthetic appeal and tactile quality of metal products. Characterized by fine linear or patterned textures, these finishes not only improve appearance but also help conceal minor scratches.
Depending on the brushing technique and texture direction, brushed finishes can be categorized into several common types:
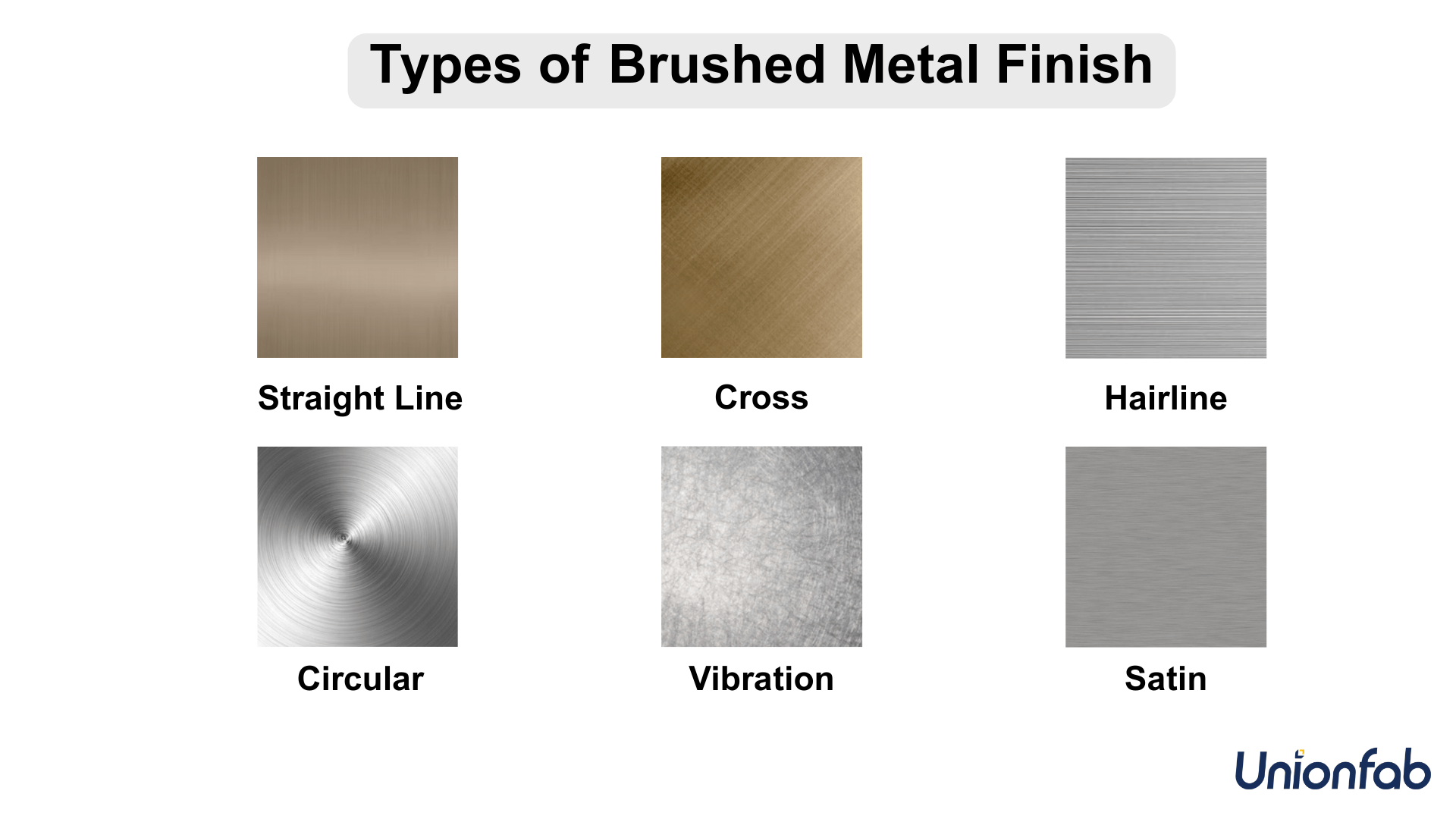
1. Straight Line Brushed Finish (Standard Brushed)
Look: Uniform, parallel lines across the surface.
Method: Created using abrasive belts or brushes moving in one direction.
Common Metals: Stainless steel, aluminum.
Applications: Kitchen appliances, architectural panels, elevator interiors, wall claddings.
2. Cross Brushed Finish (Cross Hairline / Multi-Directional)
Look: Intersecting lines, often in a grid-like or random crosshatch pattern.
Method: Brushing in multiple directions, sometimes by rotating the piece during brushing.
Effect: Gives a more dynamic, high-end industrial look.
Applications: Decorative panels, luxury retail displays, signage.
3. Hairline Brushed Finish
Look: Very fine, continuous lines, longer than standard brushed finish.
Method: Fine abrasives with consistent directional movement.
Effect: Sleek and elegant, often used in premium products.
Applications: Electronics (laptops, phones), high-end kitchenware, elevators.
4. Circular Brushed Finish (Orbital / Swirl Finish)
Look: Circular or spiral pattern resembling swirls or concentric arcs.
Method: A rotating abrasive pad is applied to the surface.
Effect: Artistic, more decorative and eye-catching.
Applications: Jewelry, metal art, architectural features, knobs, small components.
5. Vibration Brushed Finish (Non-Directional Brushed)
Look: Random, non-directional patterns that shimmer under light.
Method: Created using vibrating or oscillating abrasive pads.
Effect: Hides fingerprints and scratches very well.
Applications: Decorative metals in architecture, luxury interiors, countertops.
6. Satin Brushed Finish
Look: Smooth, low-gloss, fine-textured appearance.
Method: Often achieved with finer abrasives or soft polishing tools.
Note: Sometimes used interchangeably with “brushed,” but usually refers to an even softer and more subtle surface.
Applications: Faucets, door handles, kitchen hardware.
Each brushed finish type offers unique aesthetic and functional benefits, allowing designers and manufacturers to select the most appropriate texture for their specific application.
Brushed vs. Polished vs. Painted Finishes
When selecting a surface finish for your project, understanding the distinctions between brushed, polished, and painted finishes is essential. Each finish offers unique aesthetic and functional benefits, making them suitable for different applications.
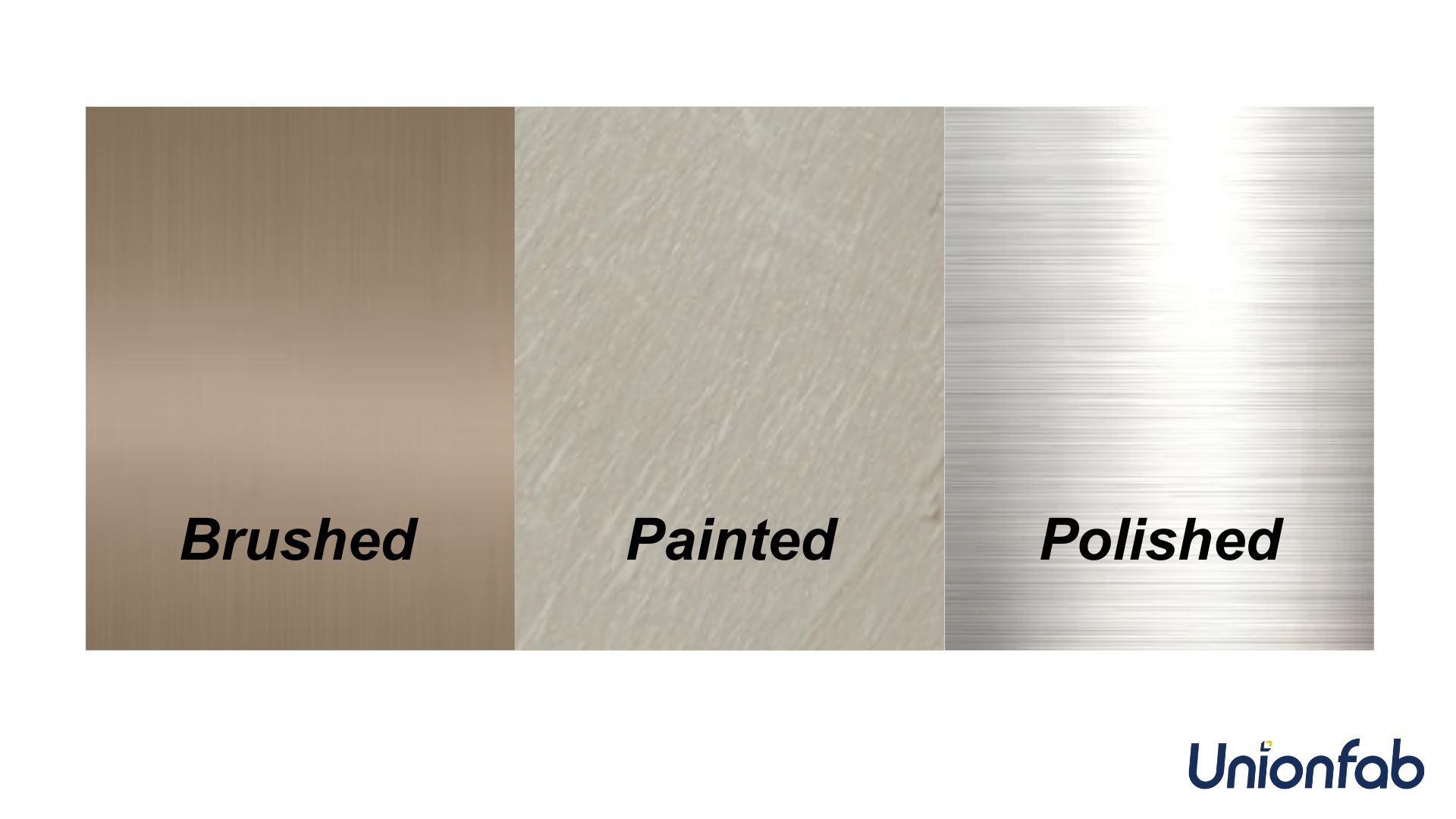
Below is a comparative overview to help you make an informed decision:
Feature | Brushed | Polished | Painted |
---|---|---|---|
Appearance | Matte, textured, low-gloss | Shiny, reflective, smooth | Solid color, smooth or textured |
Maintenance | Low (hides smudges) | High (shows fingerprints) | Medium (risk of chipping/peeling) |
Durability | Good (resists minor scratches) | Moderate (prone to scratches) | Varies (depends on paint quality) |
Cost | Moderate | High (complex process) | Low to high (depends on paint type) |
Takeaways:
Brushed Finish: high-use, low-maintenance areas (e.g., kitchens, automotive, architecture). Hides fingerprints/scratches; ideal for durability-focused designs.
Polished Finish: decorative, high-gloss applications (e.g., luxury hardware, premium products). Requires regular cleaning to maintain shine.
Painted Finish: customizable aesthetics (color/texture). Suits projects prioritizing design variety, though durability depends on paint quality/application.
Key Elements Influencing Brushed Finish Quality
Abrasive Grit Selection:
Use lower grit (80–240) for bold, rugged textures (e.g., industrial tools).
Opt for higher grit (800–1200) for fine, smooth finishes (e.g., decorative hardware).
Uniform Stroke Direction:
Maintain consistent horizontal, vertical, or circular strokes for a cohesive, professional look.
Avoid mixing directions to prevent a messy, unbalanced appearance.
Surface Preparation:
Thoroughly clean the base material to remove grease, rust, or debris.
Sand uneven surfaces first to create a smooth foundation for uniform results.
Tool Pressure Control:
Apply moderate, steady pressure to avoid deep grooves (from excessive pressure) or incomplete texture (from light pressure).
Use even strokes to ensure consistent material removal and texture depth.
Tips for Brushed Finishes
1. Processing Tips
Use a guide or template for straight strokes to avoid wobbling.
For curved surfaces (e.g., rims), use flexible abrasive pads to follow contours.
Test on a scrap piece first to dial in the desired texture.
2. Maintenance Tips (Material-Specific)
Brushed Nickel & Chrome
Cleaning: Wipe with a soft, damp cloth and mild dish soap; dry immediately to prevent water spots.
Avoid: Acidic cleaners (e.g., vinegar, lemon juice) or abrasive pads—they can dull the finish or cause pitting.
Brushed Stainless Steel & SS
Daily Care: Use a non-abrasive cloth and neutral pH cleaner (e.g., mild soap diluted in water).
Stain Removal: For stubborn marks, mix baking soda with water to form a paste, gently rub in the direction of the brush strokes, then rinse.
Brushed Aluminum
Gentle Cleaning: Wipe with a soft cloth and lukewarm water; avoid alkaline-based cleaners (e.g., ammonia) that may damage the anodized layer.
Oxidation Prevention: Apply a thin layer of aluminum-specific protectant (if uncoated) to shield against moisture.
Brushed Brass & Gold
Tarnish Control: Clean with a soft cloth and a brass/gold polish (non-abrasive formula) to remove patina; rinse and dry thoroughly.
Protection: Apply a clear wax or sealant every 3–6 months to slow natural tarnishing (especially for brass).
Brushed Steel
Rust Prevention: Wipe with an oiled cloth (e.g., mineral oil) in humid environments; for outdoor items, consider a matte clear coat.
Debris Removal: Use a soft brush to clean grooves, then wipe with a dry cloth to prevent dirt buildup.
Applications of Brushed Finish
Architecture: Railings, elevator panels, and building facades for a modern, low-maintenance look.
Source: glmetalfab.com Home Design: Cabinet hardware, kitchen sinks, and furniture legs for subtle elegance.
Source: probrico.com Automotive: Interior trim, wheel rims, and engine components for a sporty or industrial vibe.
Source: www.streetmusclemag.com Electronics: Phone cases, laptop bodies, and appliance exteriors for a premium feel.
Source: hlhrapid.com
How to Choose the Right Brushed Finish
Material Compatibility:
Match the finish to your base material (e.g., stainless steel for kitchens, aluminum for lightweight projects).
Environment:
Prioritize corrosion-resistant finishes (nickel, aluminum) for humid or outdoor use.
Aesthetic Goals:
Decide between warm tones (brass, gold) or cool tones (steel, stainless steel) to match your design theme.
Functionality:
Choose a coarser finish for heavy-use items (tools) and finer finishes for decorative pieces.
With the right finish, you can transform ordinary materials into eye-catching, durable pieces. Explore Unionfab's top solutions for professional finishing services:
Advanced Finishing Solutions at Unionfab
In addition to brushed finish service, Unionfab provides a broad range of professional-grade metal finishing options to cater to specialized needs:
Finishing Service | Key Features | Suitable Metals | Common Applications |
---|---|---|---|
Brushed Finish | Textured, non-reflective surface with uniform strokes. | Stainless steel, aluminum, brass, nickel | Architectural trim, automotive parts, kitchen appliances. |
Polished Finish | High-gloss, mirror-like surface for premium shine. | Stainless steel, brass, copper | Luxury hardware, decorative elements, automotive trim. |
Anodizing | Corrosion-resistant, colorable oxide layer on aluminum. | Aluminum, aluminum alloys | Electronics (cases/frames), bicycle components, signage. |
Powder Coating | Durable, scratch-resistant finish with matte/satin/gloss textures. | Steel, aluminum, galvanized metal | Outdoor furniture, industrial equipment, automotive parts. |
Electroplating | Thin metal layer (chrome, nickel, gold) for corrosion resistance and aesthetics. | Steel, copper, zinc, aluminum | Jewelry, automotive trim, electrical connectors. |
Sandblasting | Matte, textured surface via abrasive particle blasting. | Stainless steel, aluminum, steel | Tool surfaces, architectural panels, artistic engravings. |
Passivation | Removes free iron from stainless steel to enhance corrosion resistance. | Stainless steel | Medical devices, food processing equipment, marine components. |
Electrophoretic Coating | Smooth, even film with excellent edge coverage and rust resistance. | Steel, aluminum | Automotive parts, metal frames, hardware. |
Painted Finish | Protective and decorative coatings in endless colors. | All metals | Machinery, consumer goods, furniture, signage. |
Whether you're looking to enhance your part’s appearance, ensure it stands up to tough conditions, or meet specific regulatory requirements, Unionfab's finishing options have you covered!
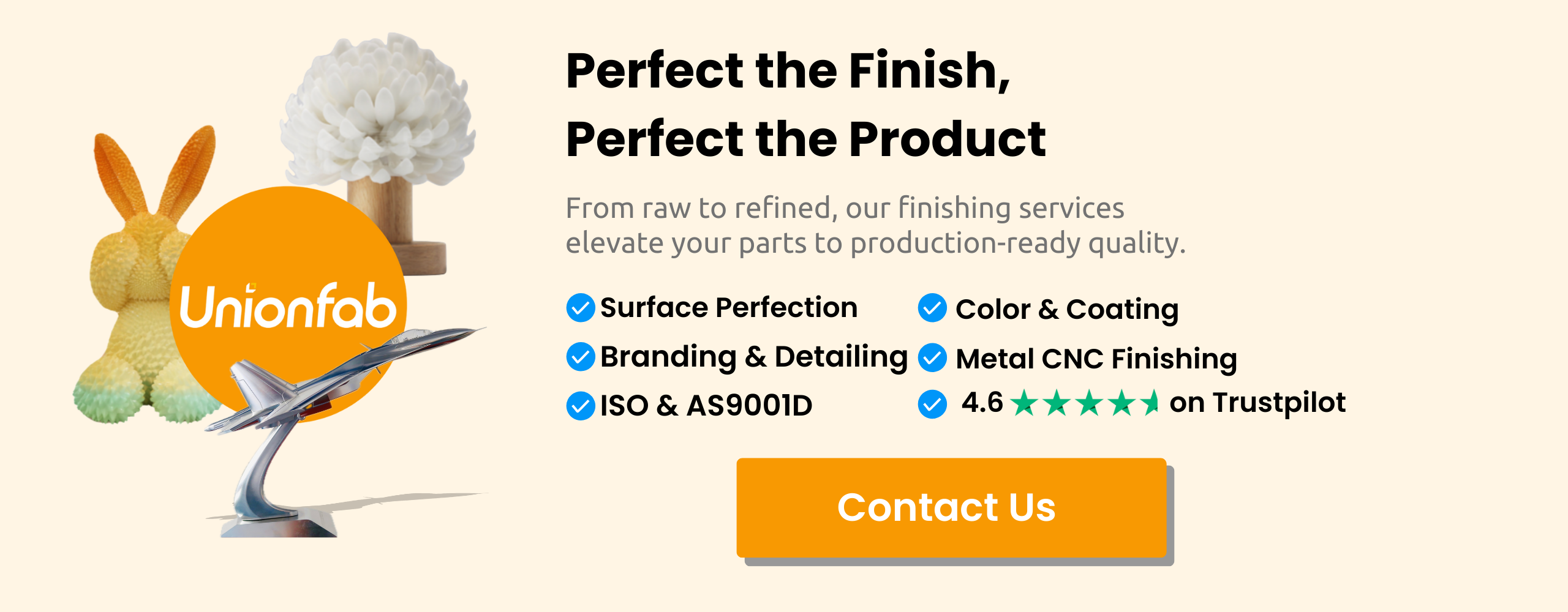
FAQs
Q: Is a brushed finish more durable than a polished finish?
Yes! It’s more resistant to scratches and fingerprints due to its textured surface.
Q: Can I apply a brushed finish to non-metal materials?
Yes! It works on wood, plastic, and even some ceramics with the right abrasive tools.
Q: What the advantages of a brushed finish?
Aesthetic Appeal: It has a sleek, modern appearance and can hide fingerprints, scratches, and dirt better than polished finishes.
Durability: The texture can make it less prone to visible scratches over time.
Low Maintenance: It’s easier to maintain than shiny finishes because it doesn’t show smudges as easily.
Non-reflective: The matte look reduces glare, making it ideal for environments with bright lighting.
Q: Does a brushed finish require sealing?
It depends on the material. Metals like brass or steel may benefit from a protective coating to prevent tarnish.