Aluminum 6061 vs 6063: Properties & Applications
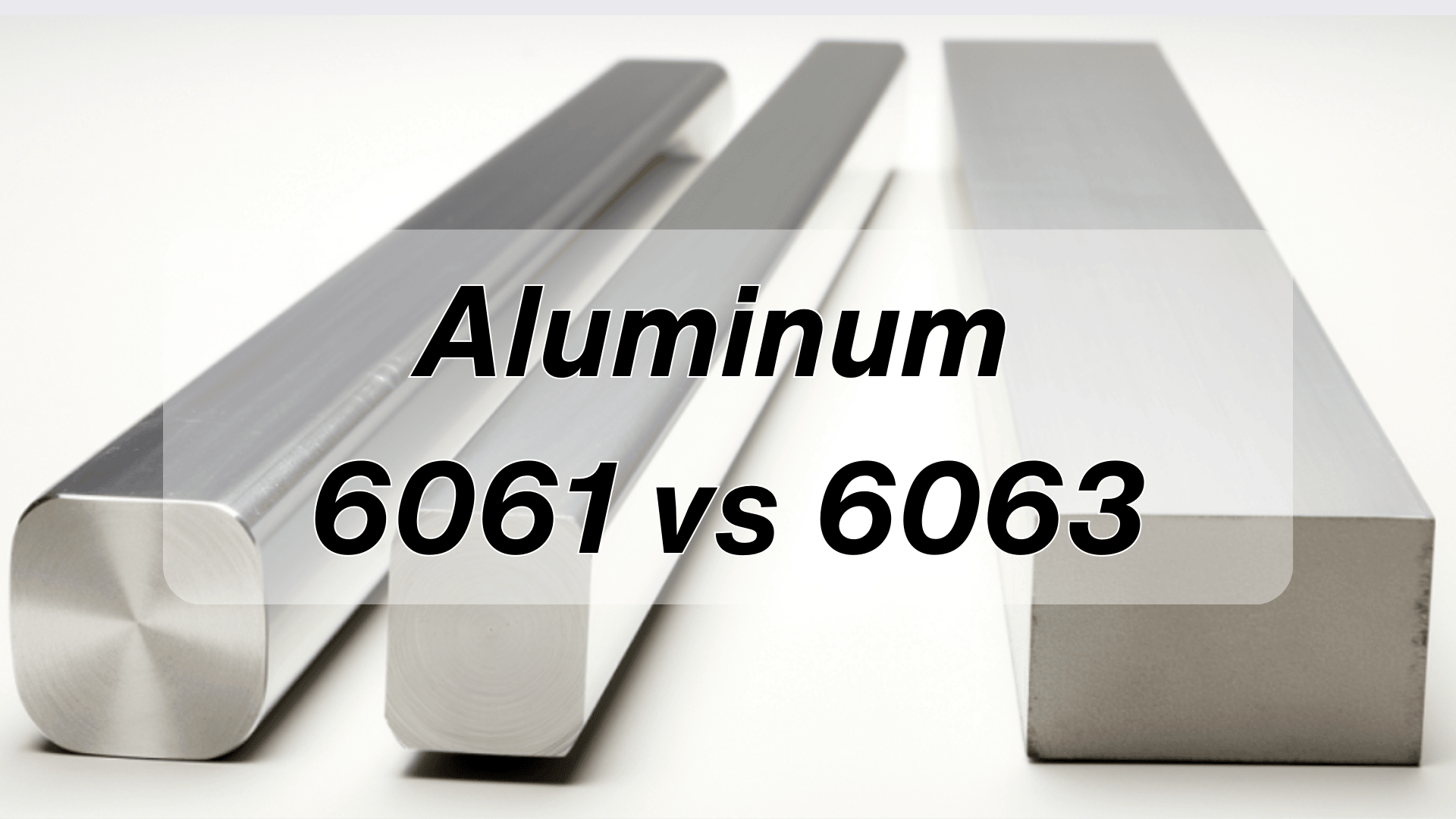
This article compares the chemical composition, physical & mechanical properties and applications of Aluminum 6061 vs 6063 to help you to make a choice.
Introduction
In the aerospace industry, 6061 aluminum is used in over 70% of structural components requiring high strength-to-weight ratios. Meanwhile, 6063 dominates 85% of architectural extrusion applications. But what makes them so popular in these distinct fields? Let's break it down.
Overview of Aluminum 6061 vs 6063
Here’s a concise overview of Aluminum 6061 vs 6063, highlighted in a comparison:
● Aluminum 6061: A versatile aluminum alloy engineered for structural integrity, featuring Mg and Si alloying elements. Ideal for load-bearing applications in aerospace, automotive, and industrial machinery, where durability and high tensile strength are critical.
● Aluminum 6063: A low-alloy aluminum variant optimized for aesthetic and architectural use, with lower Mg/Si content. Renowned for its ability to achieve intricate extrusions and accept flawless anodized finishes, prioritizing visual appeal and malleability.
In general, 6061 prioritizes strength for heavy-duty uses, while 6063 emphasizes surface quality and malleability for decorative/architectural needs.
Differences of Aluminum 6061 vs. 6063
Chemical Composition
Aluminum 6061:
Primary alloying elements: Mg (1.0–1.4%), Si (0.4–0.8%), with Cu (0.15–0.4%) and Cr (0.04–0.35%) for strength and corrosion resistance.
Aluminum 6063:
Lower alloy content: Mg (0.45–0.9%), Si (0.2–0.6%), optimized for formability and surface finish, with minimal impurities.
Physical Properties
Property | Aluminum 6061 | Aluminum 6063 |
---|---|---|
Density | ~2.7 g/cm³ (similar for both) | ~2.7 g/cm³ |
Melting Point | 582–652°C (wider range due to Cu) | 615–652°C (cleaner alloy, higher purity) |
Thermal Conductivity | ~180–210 W/(m·K) | ~205–220 W/(m·K) (slightly higher due to lower alloy content) |
Mechanical Properties
Property | Aluminum 6061 (T6 temper) | Aluminum 6063 (T5 temper) |
---|---|---|
Tensile Strength | 310–350 MPa | 190–240 MPa |
Yield Strength | 276–310 MPa | 150–210 MPa |
Hardness (Brinell) | 95–100 HB | 50–80 HB |
Fatigue Strength | Higher (suited for cyclic loads) | Lower (better for static, non-stress applications) |
Elastic Modulus | ~69 GPa (same for both) | ~69 GPa |
Forming and Working
Formability & Workability:
Aluminum 6061: Moderate formability; best for simple shapes; requires higher force for bending due to higher strength.
Aluminum 6063: Excellent formability; ideal for complex extrusions (e.g., window frames, decorative profiles).
Machinability:
Aluminum 6063: Superior machinability; produces smooth surfaces with minimal tool wear.
Aluminum 6061: Good but slightly harder to machine; benefits from lubrication in high-precision tasks.
Weldability:
Both are weldable, but Aluminum 6061 retains better post-weld strength (common in structural welding), while Aluminum 6063 is preferred for aesthetic welds due to cleaner appearance.
Heat Treatment & Hardening:
Aluminum 6061: Strongly responsive to heat treatment (T6 temper boosts strength significantly).
Aluminum 6063: Typically uses T5 temper (air-cooled) for moderate hardness, prioritizing surface quality over extreme strength.
Machining Methods
Aluminum 6061 and 6063, with their distinct properties, suit different processes. Here's a concise comparison of their machining methods:
Machining Methods for Aluminum 6063
Extrusion:6063 is the preferred material for extruded aluminum profiles. The material flows well during extrusion, allowing for flexible die design and high production efficiency.
Cutting and Punching:6063 is easy to cut and punch, making it suitable for producing parts for lightweight frames and decorative components.
Bending:6063 has good ductility and is suitable for bending processes.
Joining:6063 profiles are commonly assembled using methods like riveting and bolting.
Machining Methods for Aluminum 6061
Machining:6061 has excellent machinability for CNC machining, milling, drilling, and turning.
Welding:6061 can be welded using methods like MIG and TIG. Post-weld heat treatment (e.g., T6) is often needed to restore strength.
Forging:6061 is suitable for forging and is often used to produce high-strength parts like automotive suspension components.
Forming:6061 can be bent or stretched under appropriate conditions, though it is less formable than 6063.
Summary of Machining Method Comparison
6061 is suitable for machining (CNC, milling), welding, forging, and heat treatment, making it ideal for high-strength, precision, and structural machining needs.
6063 is suitable for extrusion, surface treatment (anodizing), bending, and cutting, making it ideal for complex shapes and aesthetic requirements in profile machining.
Notably, aluminum 6061 can be processed through innovative methods like 3D printing, yet there are a few tips to keep in mind.
Traditional processing usually requires aluminum 6061 to be in block or plate form, demanding robust mechanical properties to endure cutting and forming.
In contrast, 3D printing necessitates high-purity, low-impurity aluminum 6061 powder to enhance the precision and surface quality of printed parts.
Curious about the cost to print your model? Feel free to use Unionfab’s free online 3D printing cost calculator below:

Applications(By Industry)
Here’s a comparison of Aluminum 6061 and 6063 applications, structured for clear cross-industry contrast:
1. Marine Industry
6061: Prioritizes durability for load-bearing roles like boat frames, engine mounts, and hull supports for its heat-treatable strength and moderate corrosion resistance.
6063: Focuses on aesthetics and formability for non-critical elements or anodized extrusions, where surface finish outweighs extreme structural needs.
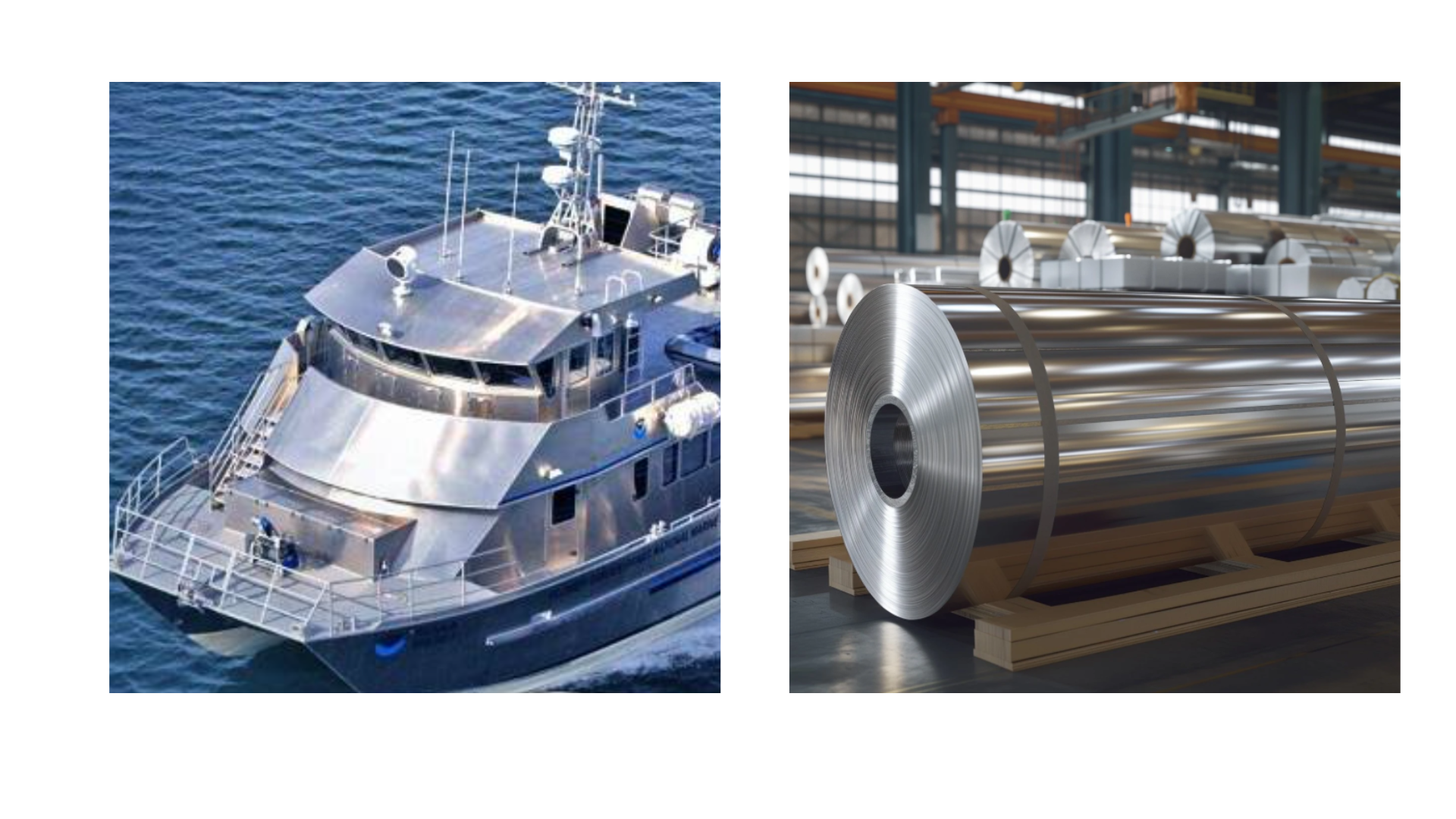
2. Automotive Components
6061: Used in high-stress parts (suspension arms, brake calipers, chassis components) requiring a strong strength-to-weight ratio for performance and safety.
6063: Ideal for exterior/interior trim (window frames, door handles, dashboard panels), leveraging its smooth surface and ability to form intricate shapes for visual appeal.
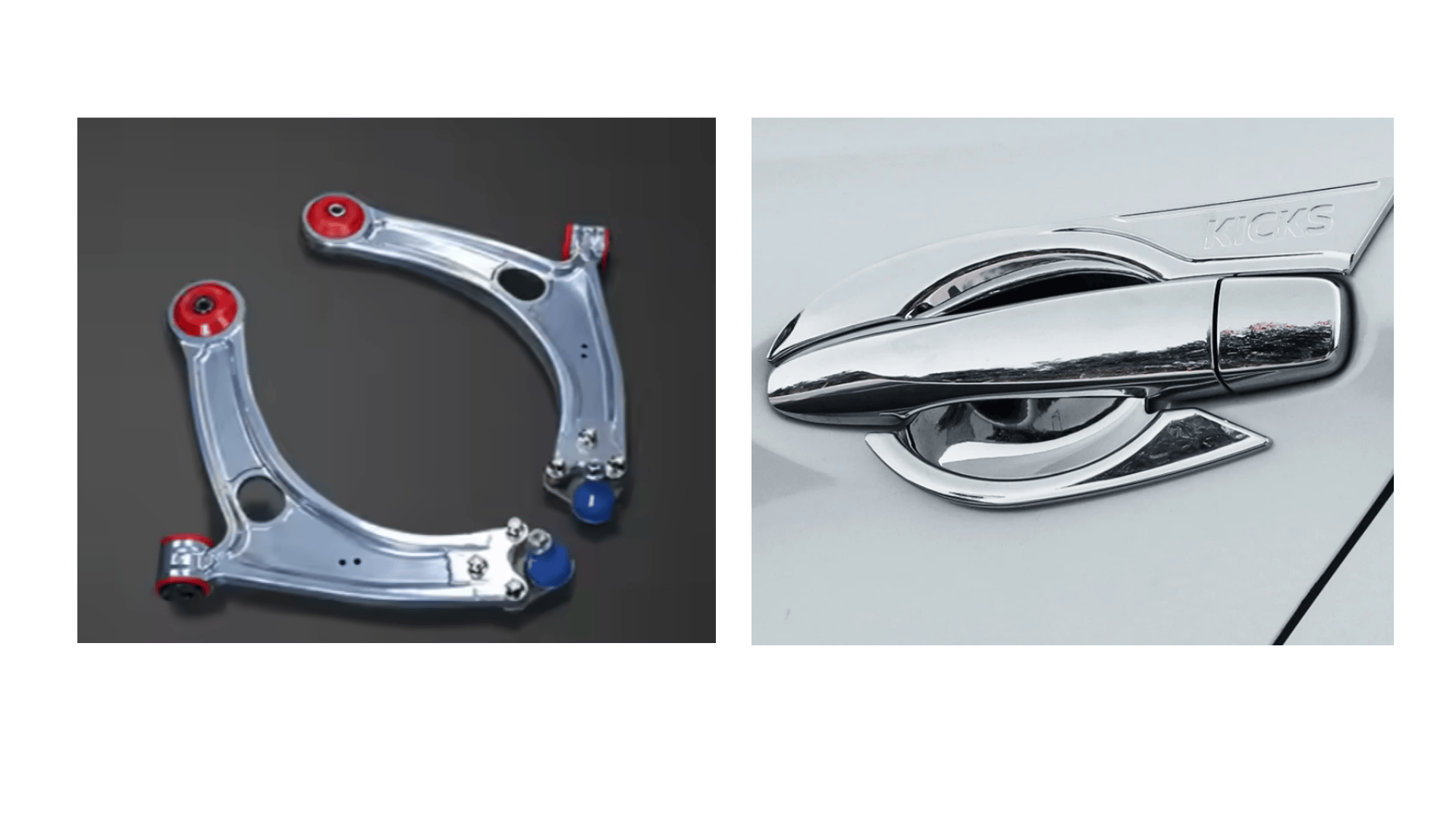
3. Consumer Goods
6061: Found in rugged tools (bicycle frames, ladders) and industrial equipment, prioritizing structural integrity over aesthetics.
6063: Dominates sleek, high-design products (smartphone cases, laptop shells, decorative hardware), valued for its anodizing quality and malleability for precise finishes.
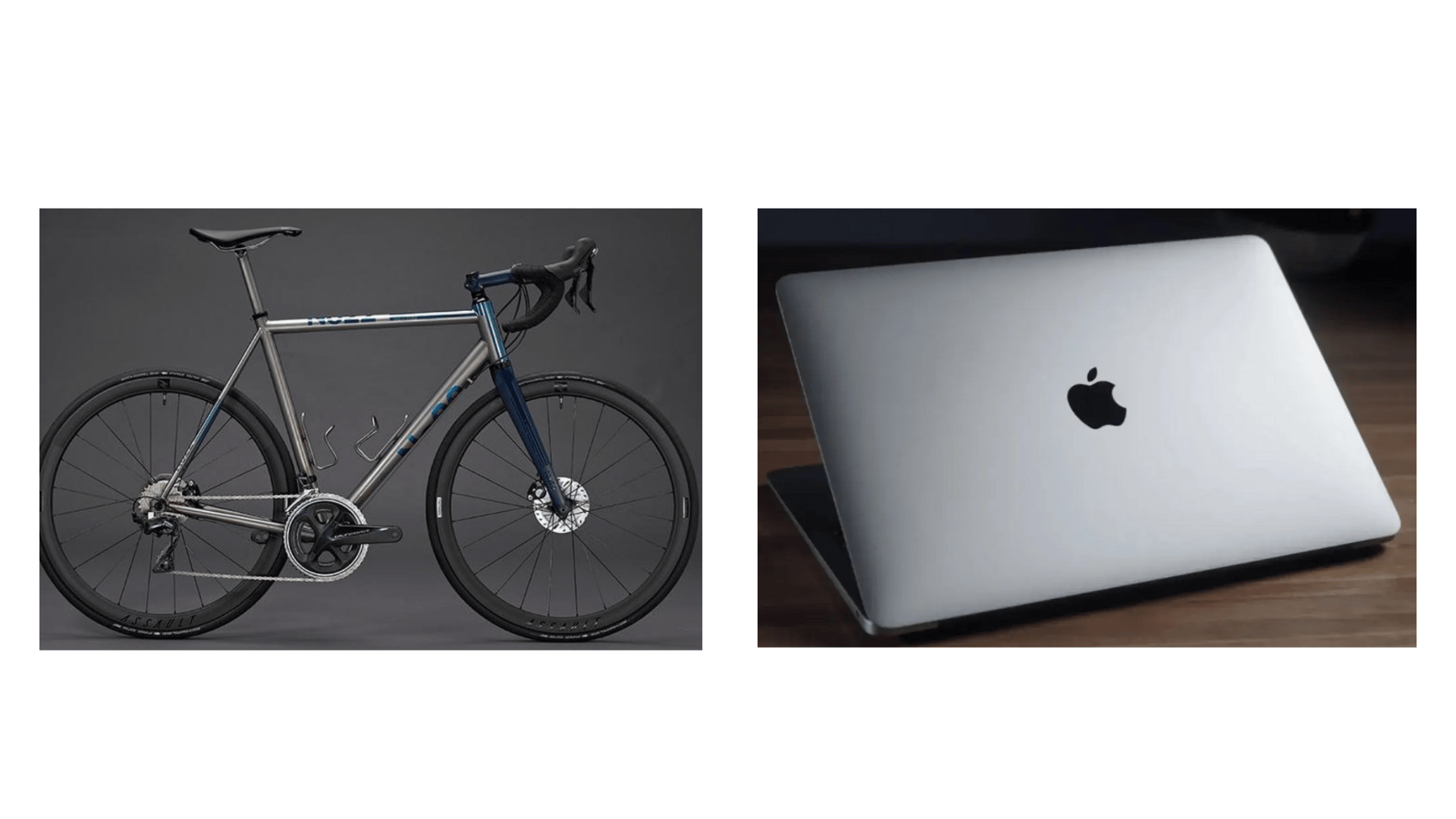
4. Aerospace Applications
6061: Supports mid-weight structural roles (wing ribs, fuselage brackets) where strength, fatigue resistance, and cost-effectiveness are critical (e.g., general aviation, non-critical aircraft components).
6063: Limited to non-load-bearing parts (cabin fixtures, interior panels) requiring light weight and corrosion resistance without heavy stress.
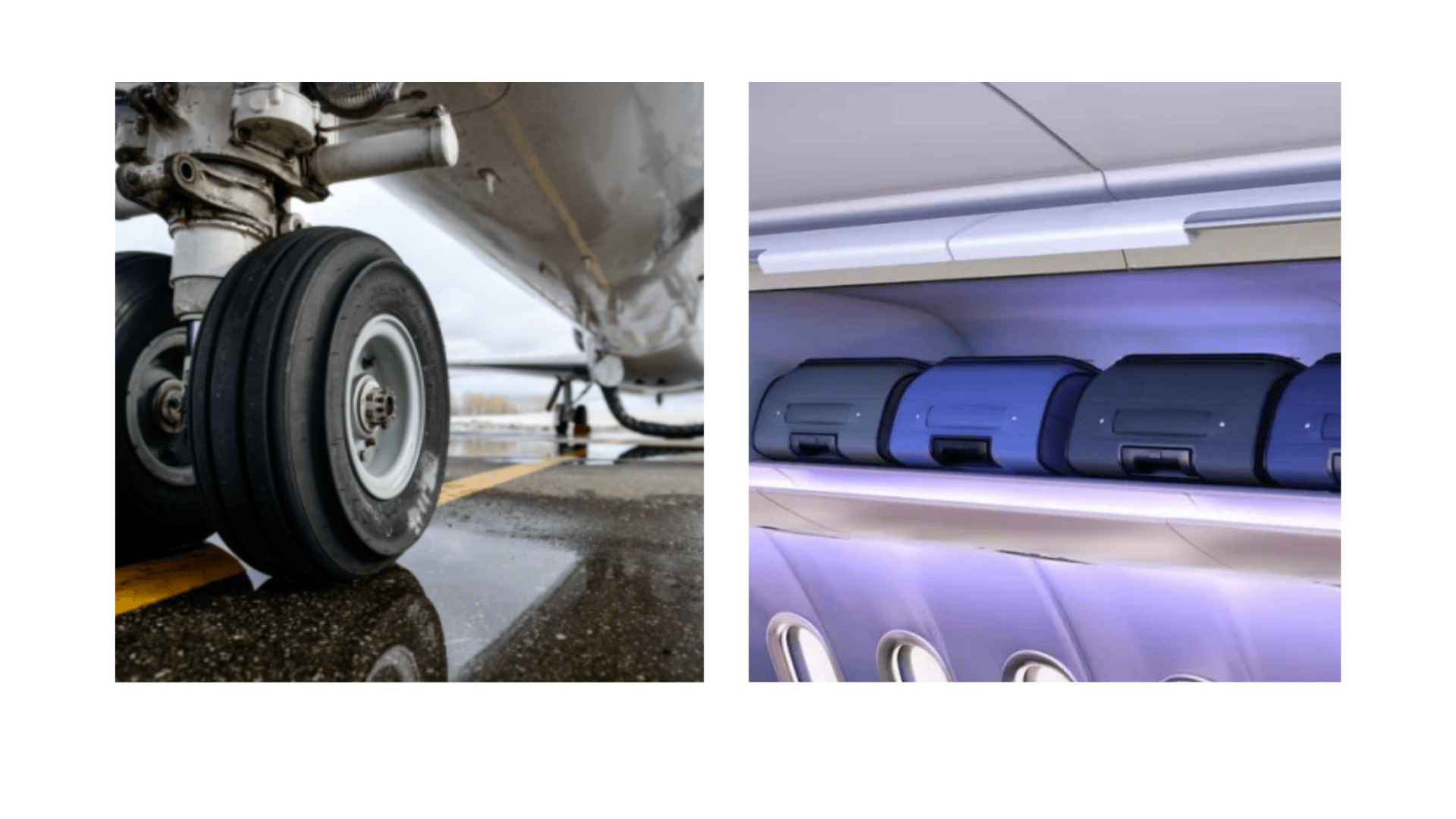
5. Architectural & Construction
6061: Rarely used in architecture; better suited for industrial structures needing high strength (e.g., bridges, heavy machinery supports).
6063: Primary choice for windows/door frames, curtain walls, and decorative panels, excelling in complex extrusions, urban corrosion resistance, and flawless anodized finishes.
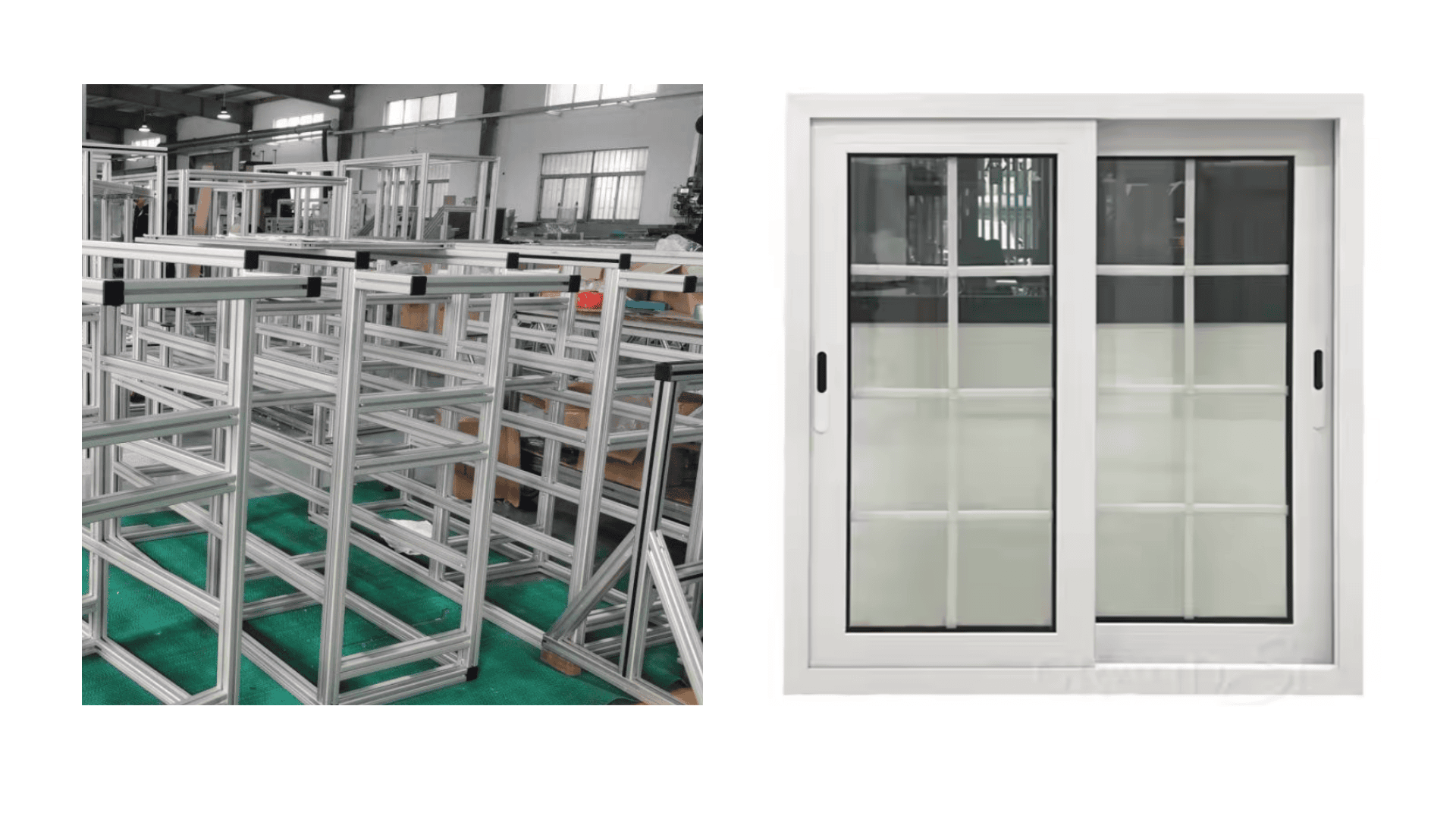
Core Takeaway
6061: Thrives in industries demanding structural robustness (marine, automotive powertrains, aerospace frameworks).
6063: Leads in sectors prioritizing aesthetics and formability (consumer electronics, architectural design, automotive styling).
Factors to Consider When Choosing Aluminum 6061 vs Aluminum 6063
When deciding between Aluminum 6061 and Aluminum 6063, several key factors should be evaluated to ensure the material aligns with your project requirements and constraints. Here’s a concise guide to help make an informed choice:
1. Project Requirements
Strength:
Aluminum 6061 is preferred for high-strength applications, such as aerospace, automotive, and industrial machinery, due to its superior tensile and yield strength. Aluminum 6063, while less strong, offers excellent formability and is ideal for decorative or architectural uses where aesthetics and surface finish are prioritized.
Corrosion Resistance:
Both alloys provide good corrosion resistance, but 6061 is more suitable for harsh environments like marine or industrial settings. 6063 is better for urban or architectural applications where surface appearance is critical.
Formability:
6063 excels in forming complex shapes and profiles, making it ideal for extruded parts like window frames or decorative trim. 6061 is less ductile but still formable enough for structural components.
2. Budget Constraints
Aluminum 6063 is generally more cost-effective for decorative or low-stress applications due to its simpler processing requirements. Aluminum 6061, with its higher strength and heat-treatable properties, may incur higher costs, especially for specialized applications like aerospace or heavy machinery.
3. Environmental Conditions
For high-stress, corrosive environments (e.g., marine or industrial), Aluminum 6061 is the better choice.
For urban or architectural settings where aesthetics matter more than extreme durability, Aluminum 6063 is preferable.
4. Required Mechanical Properties
Tensile Strength: Aluminum 6061 offers higher tensile strength (up to 45,000 psi vs. 6063’s 31,000 psi).
Yield Strength: Aluminum 6061’s yield strength (40,000 psi) surpasses 6063’s (20,000 psi), making it better for load-bearing applications.
Hardness: Aluminum 6061 is harder (Brinell hardness ~95 vs. 6063’s ~60), enhancing its durability in high-wear scenarios.
Final Considerations
Choose Aluminum 6061 for projects requiring high strength, durability, and performance in demanding environments.
Opt for Aluminum 6063 when prioritizing aesthetics, surface finish, and cost-effectiveness for decorative or lightweight applications. Balancing these factors will ensure the best material choice for your specific needs.
Conclusion
Aluminum 6061 and 6063 each excel in distinct applications. Aluminum 6061 is ideal for high-strength, load-bearing projects requiring durability and performance, such as aerospace, automotive, and industrial machinery.
In contrast, aluminum 6063 shines in formability and aesthetics, making it perfect for architectural extrusions, consumer goods, and decorative components.
Understanding these differences helps you choose the right alloy for your needs, ensuring optimal performance and extended product lifespan.
Achieve Perfect Products with Unionfab
Unionfab, the overseas branch of Uniontech, which holds 60% of China's 3d printing market share, is the
largest 3D printing manufacturer in China, specializing in rapid prototyping and on-demand production.
In addition, we offer CNC machining, vacuum casting, injection molding and finishing services, providing a
comprehensive, one-stop solution for all your manufacturing needs.
If you're interested in manufacturing with Aluminum or other materials, feel free to contact us.
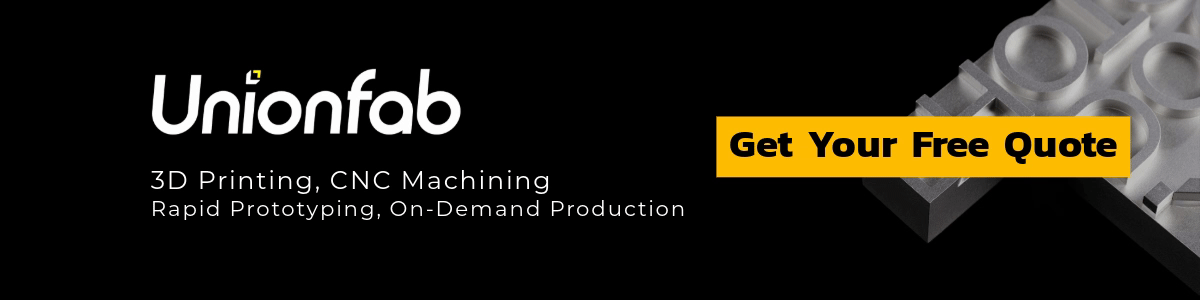
FAQs
Is 6061 aluminum strong?
Yes, 6061 aluminum is a high-strength alloy, especially in its heat-treated (T6) state, with tensile strength up to 350 MPa. It’s widely used for load-bearing applications like aerospace parts and machinery.
How much weight can 6061 aluminum hold?
Weight capacity depends on shape, thickness, and load type (e.g., tension, compression). As a reference, its tensile strength is 310–350 MPa, but specific calculations require engineering analysis for your design.
Can you bend 6061 aluminum?
Yes, but it has moderate formability. Bending works best with larger radii and in the annealed (O-temper) state for higher ductility. In T6 temper (hardened), it’s stiffer and may require more force or risk cracking in sharp bends.