TPE vs TPU [+ Comparison Table, Unionfab Case Studies, and Selection Guide]
![TPE vs TPU [+ Comparison Table, Unionfab Case Studies, and Selection Guide]](https://ufc-dtc-cms.oss-accelerate.aliyuncs.com/blog/20250327/151400_yqstwe4wh.png)
Discover the key differences between TPE and TPU for 3D printing. This guide includes a free performance comparison chart, practical use cases, and expert tips from Unionfab to help you choose the best flexible material for your project.
Introduction
When it comes to 3D printing flexible materials, TPE (Thermoplastic Elastomer) and TPU (Thermoplastic Polyurethane) are the top contenders. Both are elastomers—offering stretchability, flexibility, and shock absorption—but they differ significantly in structure, print behavior, and performance.
This blog provides a complete comparison of TPE vs TPU, tailored for engineers, designers, and manufacturers working with 3D printing. From core material properties to real-world Unionfab use cases and printability insights, you'll find everything you need to choose the right material for your next project.
What Are TPE and TPU?
Material Definitions and Characteristics
TPE (Thermoplastic Elastomer) is a blend of polymers that behaves like rubber but processes like plastic. It’s soft, flexible, and commonly used in products that require comfort, grip, or cushioning.
TPU (Thermoplastic Polyurethane) is a subtype of TPE known for its excellent toughness, abrasion resistance, and elasticity. TPU can be either soft or semi-rigid, depending on its formulation, and is favored for its durability.
Structural Differences
TPE and TPU differ significantly in their molecular structure, which directly affects their physical behavior and suitability for 3D printing.
TPE is typically a polymer blend, made from soft rubber phases like SBS, SEBS, or TPV combined with rigid plastic phases such as PP or PS. The combination influences material properties: for example, SEBS-based TPEs offer better UV resistance, while TPVs deliver enhanced heat resistance.
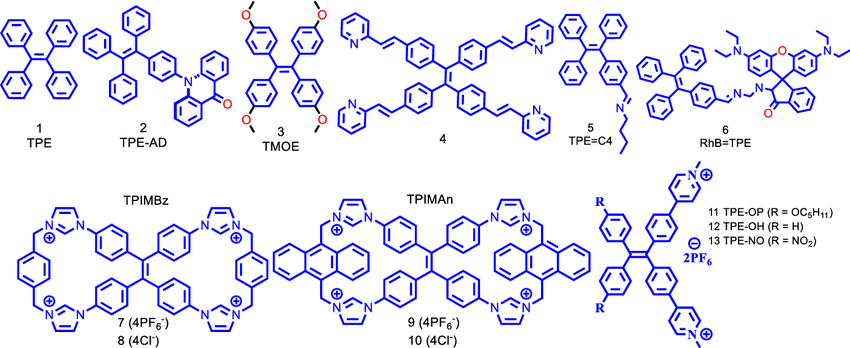
Source: researchgate.net
TPU, on the other hand, is a block copolymer, made from alternating hard segments (diisocyanate + chain extenders) and soft segments (polyether or polyester). Polyether-based TPUs are more hydrolysis-resistant and flexible, whereas polyester-based TPUs offer better abrasion resistance but are more prone to hydrolysis.
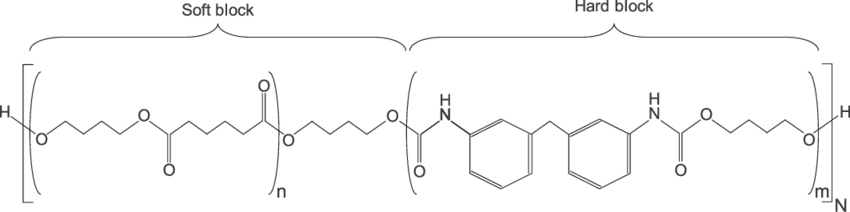
Source: researchgate.net
Types of TPE and TPU
Type | Key Characteristics | Typical Applications |
---|---|---|
TPE-S (SBS, SEBS) | Soft touch, excellent feel | Grips, toys, medical products |
TPE-O (Olefin-based) | Good weather resistance | Automotive seals, outdoor items |
TPE-V (Vulcanized rubber) | High heat resistance, tear strength | Automotive parts, piping systems |
TPU – Polyether | Flexible, hydrolysis-resistant | Wearables, cables |
TPU – Polyester | Tough, abrasion-resistant | Wheels, industrial components |
TPU: Tightly packed polyurethane chains → tougher, more resilient, and chemically resistant
Common Usage Scenarios
TPE: Overmolded grips, ergonomic handles, vibration dampers, soft wearables
TPU: Wear-resistant components, protective casings, mechanical connectors, flexible hinges
TPE vs TPU Performance Comparison
The following table highlights key mechanical and thermal properties that influence printability and end-use performance:
Property | TPE | TPU |
---|---|---|
Elasticity | Good | Excellent |
Hardness (Shore A) | 20A–80A | 60A–95A |
Abrasion Resistance | Moderate | High |
Chemical Resistance | Moderate | High |
Heat Resistance | Up to 80°C | Up to 120°C |
UV Resistance | Moderate | Good |
Surface Finish | Matte, rubber-like feel | Smooth, slightly glossy |
Recyclability | Yes | Yes |
Printability (FDM) | Technically challenging | Good |
Cost | Lower | Slightly higher |
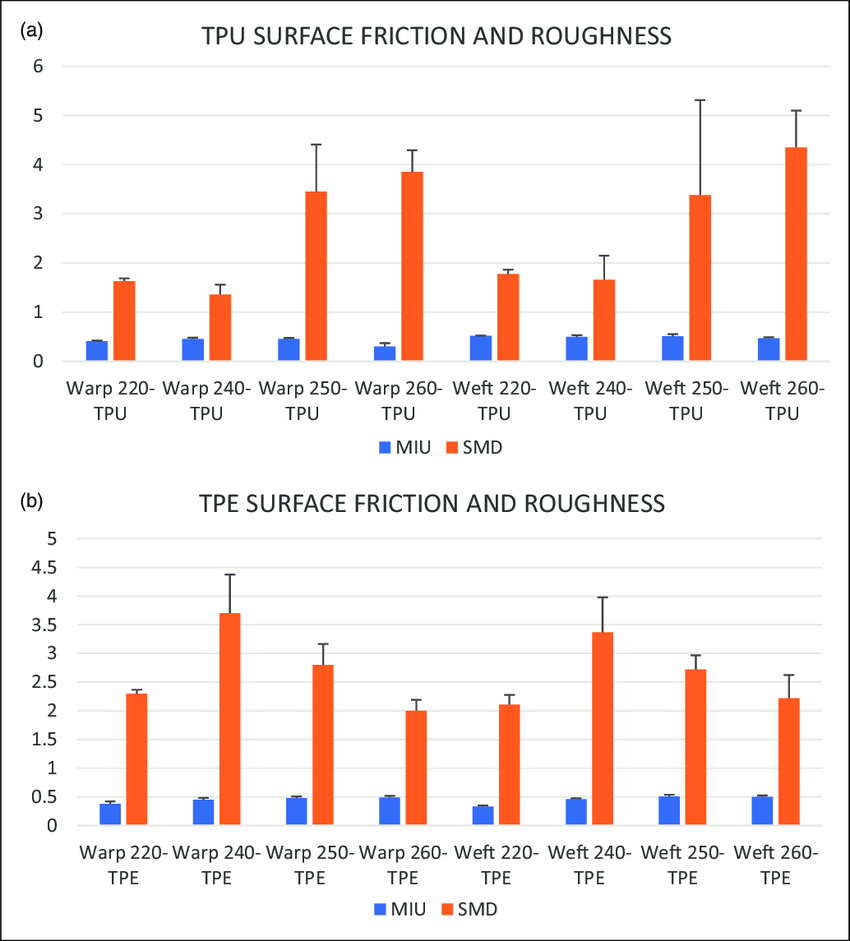
Source: RearchGate
Real-World Applications
Medical and Healthcare
TPE in Medical Devices: TPE is highly valued in the medical industry for its chemical inertness and biocompatibility. It is commonly used in the manufacturing of medical components such as tourniquets, breathing masks, medical tubing, and infusion sets.
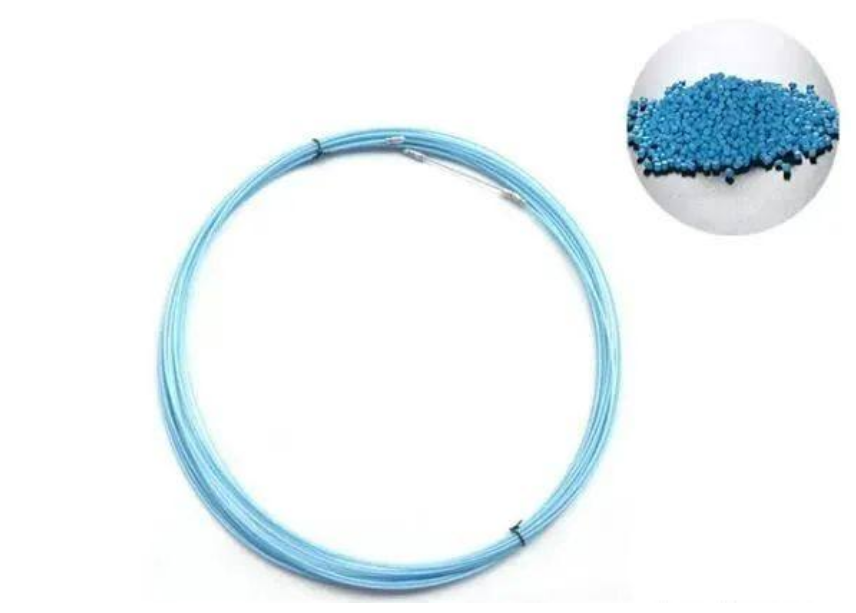
Source: abmed360.com
TPU in Wearable Medical Devices: TPU is used to manufacture wristbands and straps for wearable medical devices. It is hypoallergenic, comfortable for skin contact, and offers excellent flexibility for long-term use.
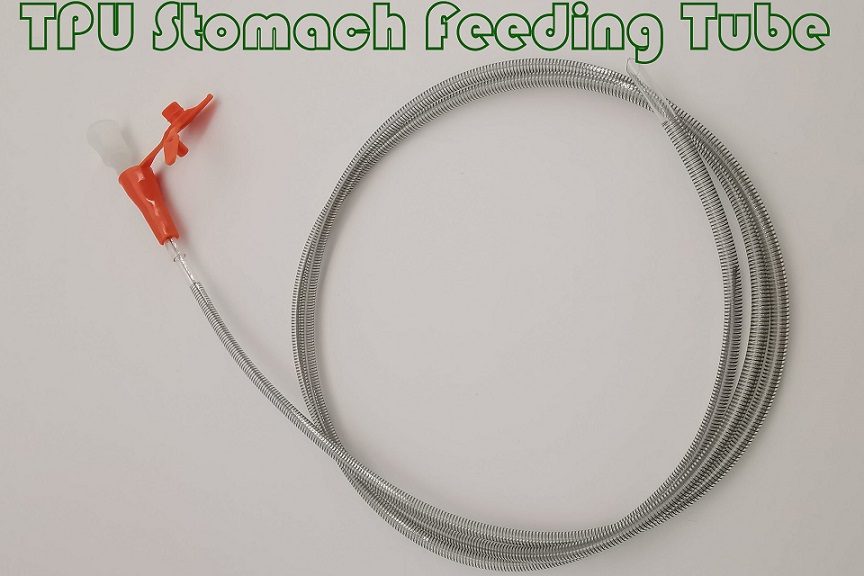
Source: tpupolymer.com
Electronics
TPE in Cable & Audio Lines: With its excellent flexibility and surface finish, TPE is a go-to material for USB cables, headphone wires, and jack housings where flexibility and aesthetics are key.
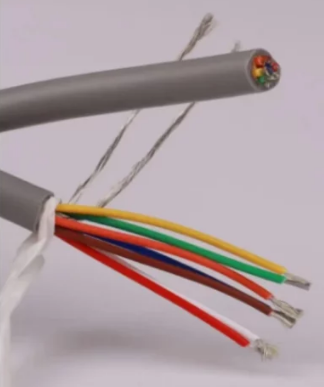
Source: centralwires.com
TPU in Rollable Electronics: TPU’s elasticity makes it ideal for rollable and foldable electronics. It has been used as the outer shell and internal structure for devices like rollable OLED TVs.
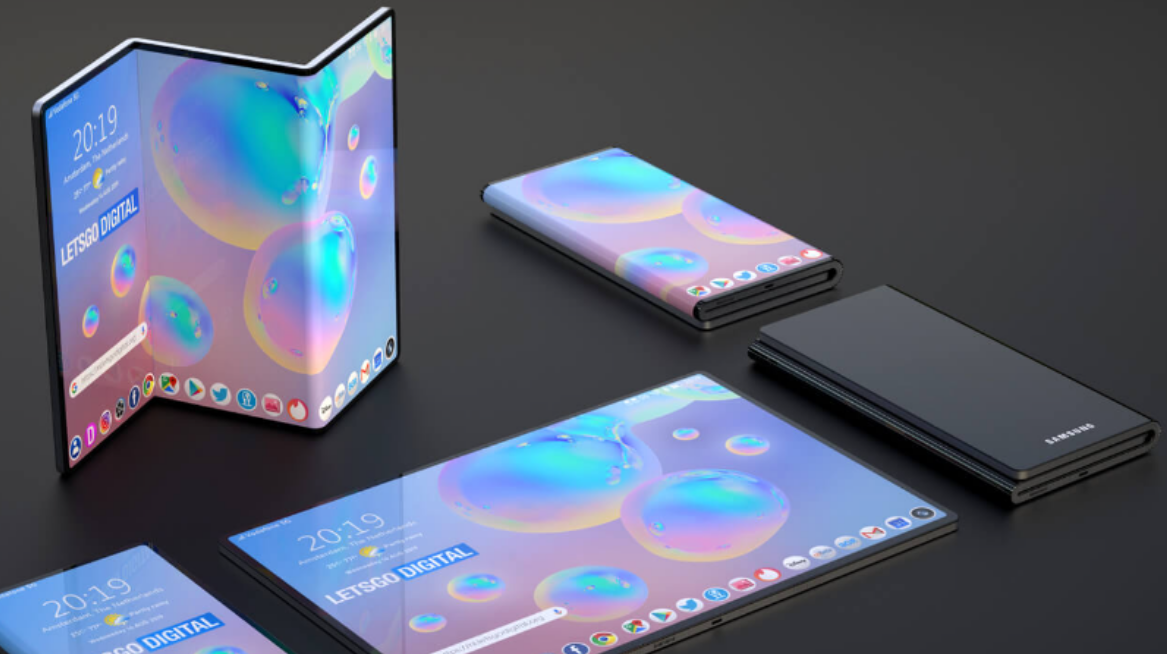
Source: aibang.com
Unionfab TPU/TPE Case Study
One of Unionfab’s most popular applications of TPU is in the production of flexible shoe soles, combining abrasion resistance and elasticity. Using SLS technology, we helped a footwear brand develop a lightweight, shock-absorbing sole that maintains flexibility under repeated compression—ideal for performance and casual wear alike.
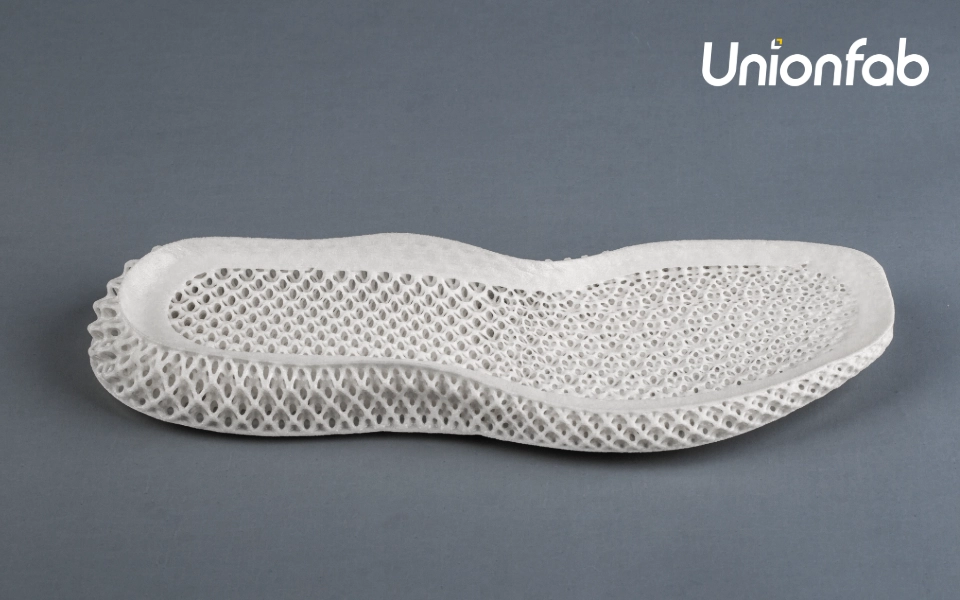
Source: Unionfab
In another creative example, we 3D printed a squishy puffer fish toy using ultra-soft TPE. The model demonstrates how TPE can be used not only for function but also for tactile user experience. The material offered just the right rebound and softness for an engaging prototype that mimicked real-life squish behavior.
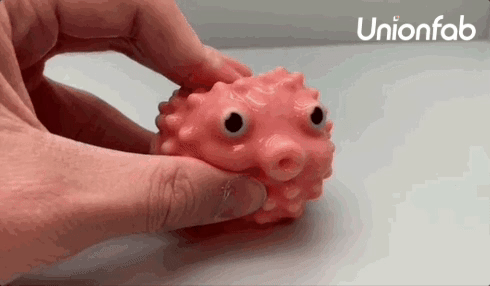
Source: Unionfab
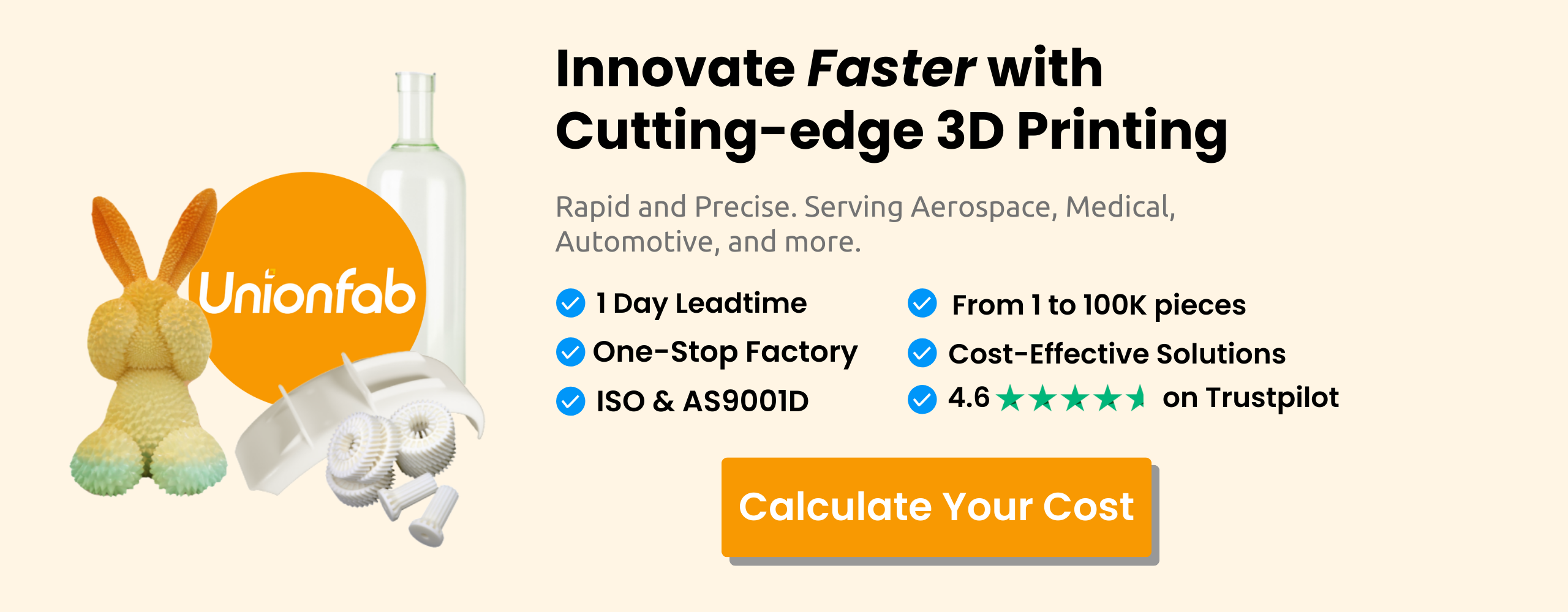
TPE vs TPU in 3D Printing
Both materials are printable, but their behavior differs significantly depending on printer setup and print parameters.
Recommended 3D Printing Technologies
Technology | TPE | TPU |
---|---|---|
FDM | Yes (difficult) | Yes (most common) |
SLS | Limited | Excellent |
MJF | Not available | Excellent |
SLA/DLP | Not suitable | Not suitable |
TPU Hardness Levels and Printing Behavior
TPU is available in different Shore A hardness levels, and this greatly affects printability and performance:
60A TPU: Extremely soft and elastic; difficult to extrude consistently. Not recommended for FDM.
85A TPU: Balanced flexibility and printability; suitable for insoles, soft enclosures, protective pads.
95A TPU: Near-rigid behavior; excellent for industrial-grade parts requiring abrasion resistance and structural shape.
Printing Methods in Detail
When it comes to flexible materials like TPU, the choice of 3D printing method significantly affects print quality, production speed, and application suitability. Three of the most commonly used methods for TPU are SLS, FDM, and MJF.
Selective Laser Sintering (SLS)
TPU is ideal for producing parts with complex geometries because it doesn’t require support structures during printing. This makes it especially suited for applications like wearables, sports gear, and medical devices where organic shapes and fine detailing are essential.
SLS TPU parts also tend to have excellent surface finish and mechanical performance right out of the printer.
Fused Deposition Modeling (FDM)
TPU is widely used in FDM printing due to its availability in filament form. However, print results vary depending on printer configuration. Direct-drive extruders are highly recommended, especially when working with softer TPU grades, since Bowden extruders may struggle to maintain filament control.
When configured correctly, FDM offers a cost-effective and accessible way to produce flexible components for functional prototyping or small-batch runs.
Multi Jet Fusion (MJF)
Multi Jet Fusion (MJF) by HP is a more recent method used for producing TPU parts in large volumes. MJF excels in speed and scalability, making it ideal for mass-customized products such as shoe soles, soft robotics, and industrial damping pads. It also offers good dimensional accuracy and repeatability with minimal post-processing.
To learn more about each method’s tradeoffs and real-world examples, check out our deep dive on TPU printing: TPU 3D Printing: Tips, Tricks & Best Solutions (2025).
For material safety considerations, refer to: Is TPU Toxic? What You Need to Know.
Printability Tips
TPE (FDM):
Requires direct-drive extruder
Very soft = risk of jamming
Print slowly (20–30 mm/s)
Difficult with retraction → oozing possible
Best for experienced users
TPU (FDM/SLS):
Easier to feed due to slightly higher rigidity
Compatible with both direct and Bowden setups
Great for functional parts with excellent layer adhesion
Ideal for both prototypes and production
Post-Processing & Surface Finishing
TPE and TPU also differ in how they respond to surface treatment:
TPU is more receptive to coatings such as paints and adhesives, making it suitable for colored finishes or custom texturing.
TPE has a more rubbery surface, which can be difficult for paint or adhesives to bond with, requiring specialized primers or surface treatments.
Common Finishing Options:
Spray painting (TPU recommended)
Tumble polishing (for MJF/SLS parts)
Color dyeing (especially effective for SLS TPU)
Surface sealing/coating for improved wear or waterproofing
Unionfab offers a wide range of professional finishing services for flexible materials, including coloring, polishing, and advanced coating solutions for industrial use.
Learn more about available finishes in our Post-Processing Capabilities.
Both materials exhibit high shrinkage, so accurate dimensional compensation is essential.
Supports may not always be required due to flexibility, but part orientation matters greatly.
Explore our 3D Printing Materials Guide for more technical insights.
Choosing the Right Material: Simple Decision Guide
Not sure which material fits your needs? Start with these key questions:
Question | Best Material |
---|---|
Do you need soft, skin-contact comfort? | TPE |
Will the product be bent or flexed frequently? | TPU |
Is abrasion or impact resistance important? | TPU |
Is ease of 3D printing a major factor? | TPU |
Is cost a primary concern? | TPE |
Do you need excellent chemical or UV resistance? | TPU |
Final Thoughts: Summary of Key Differences
Both TPE and TPU are excellent flexible materials, but their differences matter—especially in 3D printing.
Choose TPE if you need a soft-touch, ergonomic product and are working with a direct-drive printer.
Choose TPU if your part needs to withstand wear, chemicals, or repeated mechanical stress, or if you want an easier print experience.
The right choice will reduce trial-and-error and improve both print quality and end-use performance.
Start Printing Flexible Parts with Unionfab
At Unionfab, we help you go from design to production with precision 3D printing of TPU and TPE materials. Whether you're testing a prototype or manufacturing complex flexible components, our team ensures the right material, technology, and support.
Work with Unionfab:
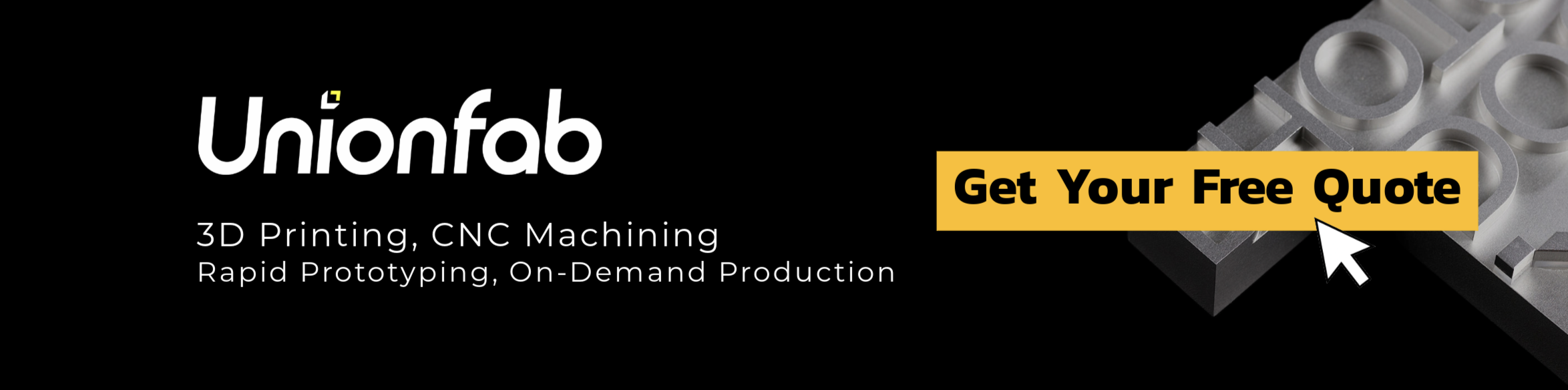
People Also Ask (FAQ)
What is the main difference between TPE and TPU?
TPE is a polymer blend that is softer and easier to stretch, while TPU is a type of block copolymer with superior durability, abrasion resistance, and better printability in most 3D printing technologies.
Can TPE and TPU be used in 3D printing?
Yes, both TPE and TPU are 3D printable, but TPU is more stable and easier to use—especially with FDM and SLS printers. TPE requires more careful handling and often a direct-drive extruder.
Which is more flexible, TPE or TPU?
TPE is generally softer and more elastic. However, TPU offers a better balance of flexibility and toughness, making it suitable for functional applications.
Is TPU more expensive than TPE?
Yes, TPU typically costs more than TPE due to its enhanced mechanical properties and broader industrial applications.
Which material is better for functional parts?
TPU is preferred for functional 3D-printed parts because of its superior wear resistance, elasticity, and chemical durability.
Can I color or paint TPE and TPU parts?
Yes. TPU is easier to post-process and coat, while TPE may need special surface treatment to hold paint or adhesives effectively.
Still have questions? Explore our 3D Printing Knowledge Base or contact Unionfab's material experts.