Galvannealed vs. Galvanized [+Free Coating Comparison Chart & CNC Material Tips]
![Galvannealed vs Galvanized [+Free Coating Comparison Chart & CNC Material Tips]](https://ufc-dtc-cms.oss-accelerate.aliyuncs.com/blog/20250327/123656_xitcm89zd.png)
Compare Galvannealed vs Galvanized steel in this expert guide. Learn which surface coating suits your CNC project best. Includes free coating chart, material selection tips, and instant quoting tool from Unionfab.
Introduction: Choosing the Right Coating Matters
When it comes to metal fabrication and CNC machining, surface treatment is just as important as the base material. Surface coatings impact corrosion resistance, appearance, weldability, and paintability. Engineers and procurement professionals often need to decide between different surface finishes to meet performance and cost requirements.
This guide explains and compares Galvannealed vs Galvanized steel, the two most common zinc-based coatings used in manufacturing. Whether you're designing automotive parts, electrical enclosures, or industrial components, Unionfab is here to support your decision-making and manufacturing needs.
Galvannealed vs Galvanized Steel
Let’s start with the basics. Both coatings aim to protect steel from corrosion, but they’re made differently and offer unique properties.
What is Galvanized Steel?
Galvanized steel is created by dipping the base steel into a bath of molten zinc. This process forms a physical zinc coating that shields the steel from moisture and corrosion. The result is a shiny, silver finish often seen on fencing, outdoor signage, or HVAC components.
Advantages:
Strong barrier against moisture and atmospheric corrosion
Cost-effective
Long-lasting in outdoor environments
Limitations:
Surface may flake during welding or painting
Less suitable for secondary coatings without surface prep
What is Galvannealed Steel?
Galvannealed steel undergoes the same hot-dip process but is then annealed at a high temperature. This allows iron from the steel to mix with zinc, creating a zinc-iron alloy layer.
Advantages:
Excellent paint adhesion without additional surface treatment
Superior weldability
Uniform matte surface ideal for aesthetic finishes
Limitations:
More brittle coating than galvanized
Slightly higher cost
Slightly less corrosion resistance in bare environments
Common Applications by Industry
Different industries have varying demands for surface performance, appearance, weldability, and cost. Choosing between Galvannealed and Galvanized steel depends heavily on the specific environment and end-use of the product.
Here’s a breakdown of recommended usage by industry:
Construction Industry
Galvanized Steel is ideal for roofing sheets, exterior railings, gutters, and HVAC ducting, where corrosion resistance and affordability are critical.
Galvannealed Steel is suitable for door frames, window casings, or any components requiring post-painting. Its superior paint adhesion ensures long-lasting finishes.
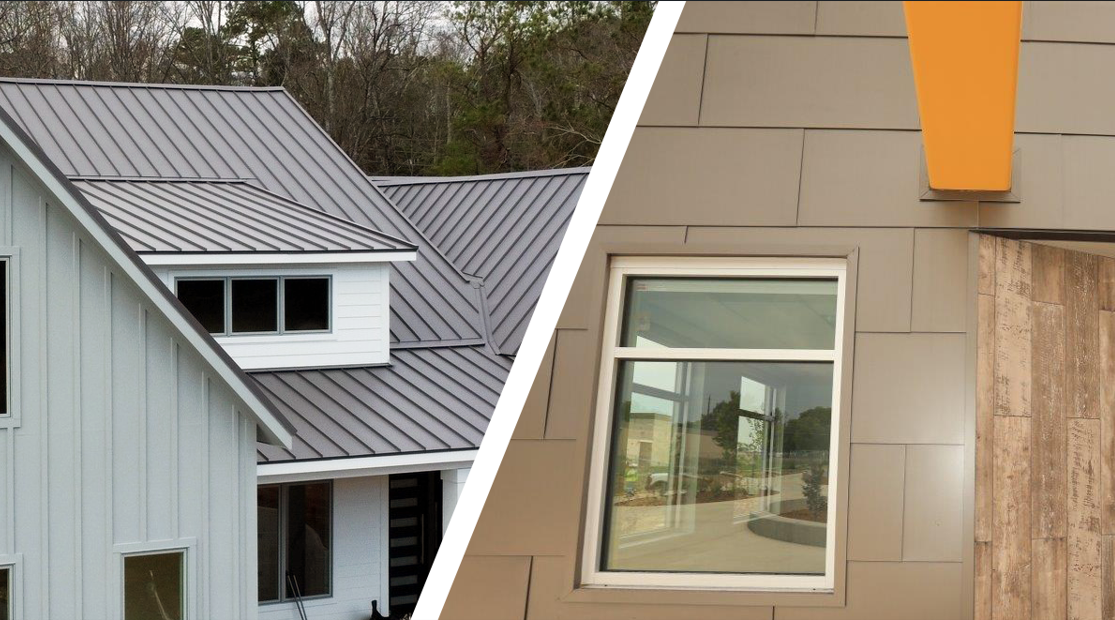
Left: Galvanized steel roofing panels & Right: Galvannealed steel
Source: sheffieldmetals.com
Automotive Industry
Galvannealed Steel is the standard for car body panels, especially for doors, hoods, and structural parts. It supports high weldability and seamless painting in mass production.(e.g., Widely used by brands like Toyota, Honda, and Ford.)
Home Appliance Industry
For washing machines, refrigerators, microwaves, and other large appliances, Galvannealed is preferred. Its surface bonds well with coatings, maintaining both function and appearance through the product's lifespan.
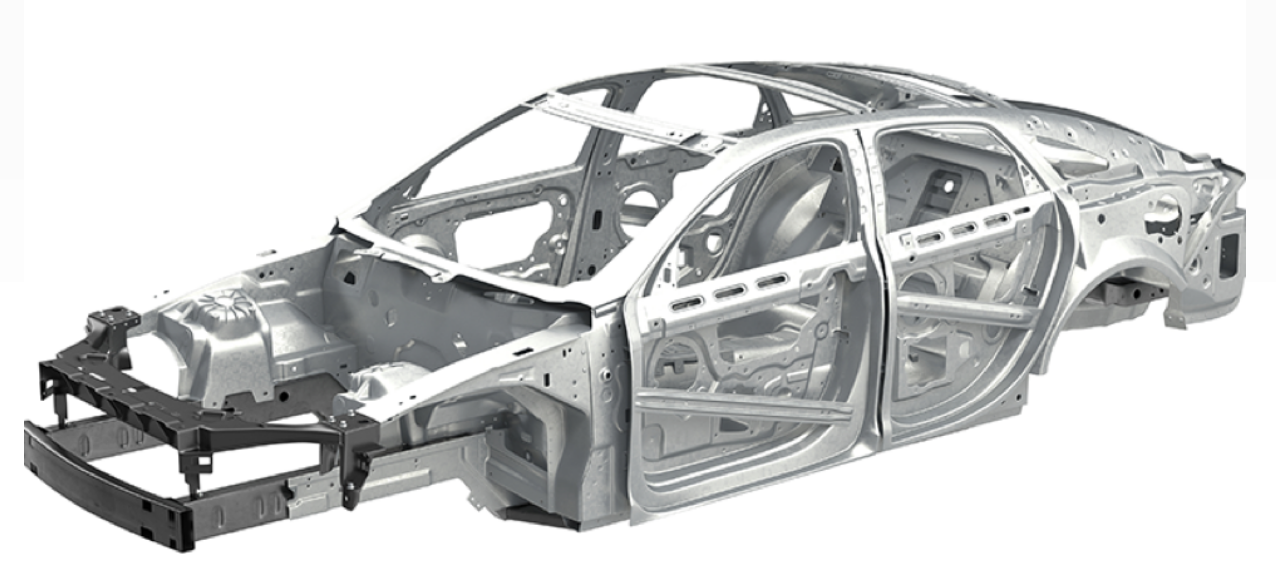
Source: nationalmaterial.com
Electrical & Enclosures
Galvannealed Steel is used in electrical cabinets, switch boxes, and distribution panels where both rust resistance and paintability are required for long-term indoor or sheltered use.
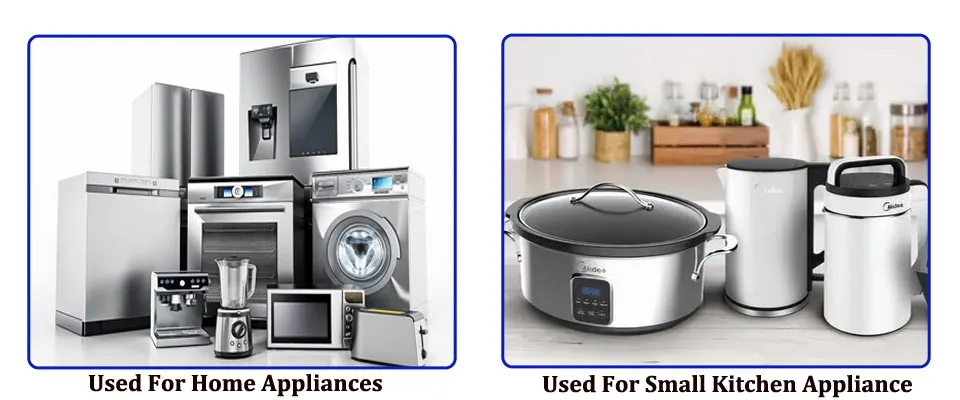
Source: jinbosteel.com

Agriculture & Outdoor Equipment
Galvanized Steel is commonly applied in grain silos, irrigation structures, greenhouse supports, and farm equipment, thanks to its strong protection against rain, humidity, and chemicals.
Recommended Material by Industry
Industry | Application Examples | Recommended Material |
---|---|---|
Construction | Roofs, fences, ductwork | Galvanized |
Construction | Doors, window frames (to be painted) | Galvannealed |
Automotive | Body panels (doors, hoods), undercarriage parts | Galvannealed |
Home Appliances | Refrigerator shells, washing machines, ovens | Galvannealed |
Electrical Equipment | Enclosures, cabinets, switch panels | Galvannealed |
Agriculture / Outdoors | Silos, fencing, irrigation structures | Galvanized |
Tip: For parts requiring both corrosion resistance and painting, Galvannealed offers the best performance-to-cost ratio.
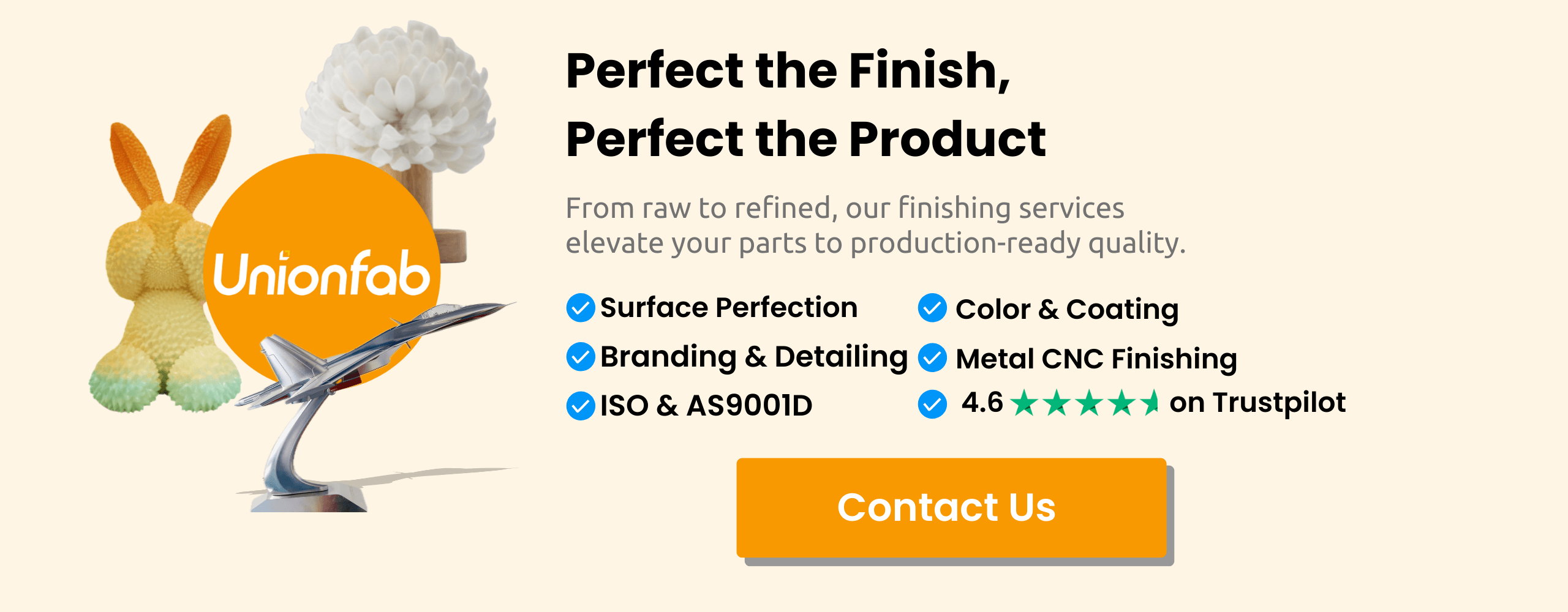
Key Differences: Galvannealed vs Galvanized Steel
Feature | Galvannealed | Galvanized |
---|---|---|
Surface Hardness | High | Moderate |
Weldability | Excellent | Fair |
Paintability | Very good (ideal for powder coat) | Limited (paint may peel) |
Corrosion Resistance | Moderate | High (especially outdoors) |
Appearance | Dull grey, matte finish | Shiny, spangled surface |
Surface Adhesion | Excellent for coatings | Less ideal for post-processing |
Cost | Slightly higher | Lower |
Understanding Corrosion Resistance: Mechanism & Coating Thickness
While Galvanized steel is known for its superior corrosion resistance compared to Galvannealed, it's important to understand why — and how the protection works at the chemical and structural level.
Corrosion Protection Mechanism
Type | Mechanism Explained |
---|---|
Galvanized | The coating is made of pure zinc, which offers sacrificial anodic protection. When the coating is scratched or damaged, the surrounding zinc corrodes first, shielding the steel underneath. This is known as the “sacrificial anode effect.” |
Galvannealed | The zinc-iron alloy coating contains less free zinc. While harder and more abrasion-resistant, it provides less sacrificial protection, making it more suitable for indoor or painted applications. |
Coating Thickness Comparison: Durability Matters
The thickness of the protective coating directly impacts how well the material performs in different environments:
Property | Galvanized Steel | Galvannealed Steel |
---|---|---|
Coating Thickness | 50–100 µm | 5–15 µm |
Corrosion Protection | Strong – ideal for outdoor & humid conditions | Moderate – best when painted |
Surface Hardness | Softer, more prone to scratching | Harder, more wear-resistant |
Which One Should You Choose?
The ideal choice depends on your product’s function, environment, and downstream processing needs.
If your product needs painting or powder coating → Choose Galvannealed. The rough surface promotes paint adhesion without pre-treatment.
If it will be used in outdoor or humid environments → Go with Galvanized for its superior corrosion resistance.
If welding is involved → Galvannealed performs better and produces less hazardous fumes.
If you're working within budget constraints → Galvanized is often the more cost-effective choice.
Short-Term vs Long-Term Cost Considerations
While Galvanized steel is typically cheaper upfront, Galvannealed steel may offer better long-term value depending on the application. It’s important to consider the total cost of ownership, not just the initial material price.
Cost Factor | Galvanized Steel | Galvannealed Steel |
---|---|---|
Initial Cost | Lower – economical choice for high-volume, general-purpose parts | Slightly higher due to the additional annealing process |
Processing Cost | May require surface prep before painting; zinc layer may flake when welding | Easier to weld and paint; better suited for automation |
Maintenance | May develop corrosion spots over time; requires periodic touch-ups | Strong paint adhesion leads to lower maintenance costs |
Aesthetic & Finish | Good corrosion resistance without paint, but limited finish options | Excellent for painted applications with enhanced durability |
Best For | Short-term use, outdoor structures, cost-sensitive projects | Long-term use, high-performance components, premium product lines |
Other Common Surface Coatings in CNC Fabrication
While Galvanized and Galvannealed coatings are widely used, there are other surface finishes worth considering depending on your application:
1. Electroplating (Zinc, Nickel)
A thinner and more uniform coating applied using electrical current. Often used for small, precision parts in electronics or medical devices.
2. Powder Coating
An additional layer applied after machining, offering strong adhesion and color flexibility. Used for consumer goods, enclosures, and outdoor parts.
3. Anodizing (for Aluminum)
An electrochemical process that increases surface hardness and corrosion resistance in aluminum components. Common in aerospace, electronics, and automotive.
4. Black Oxide (for Steel)
A chemical conversion coating that adds mild corrosion resistance and a sleek black appearance. Typically used in tooling and fasteners.
Understanding the performance, cost, and compatibility of each option helps ensure the right match between function and finish.
Can Galvannealed and Galvanized Steel Be Used in CNC Machining?
Yes—and Unionfab supports CNC machining for both materials.
👉 Free Tool: Use our Instant Quoting Engine to compare prices, lead times, and materials instantly.
👉 Materials Resource: Access our Online Material Library for datasheets, performance specs, and surface finish guides.
👉 Tips: Need help choosing a surface treatment? See our CNC Machining finishing options or contact our experts.
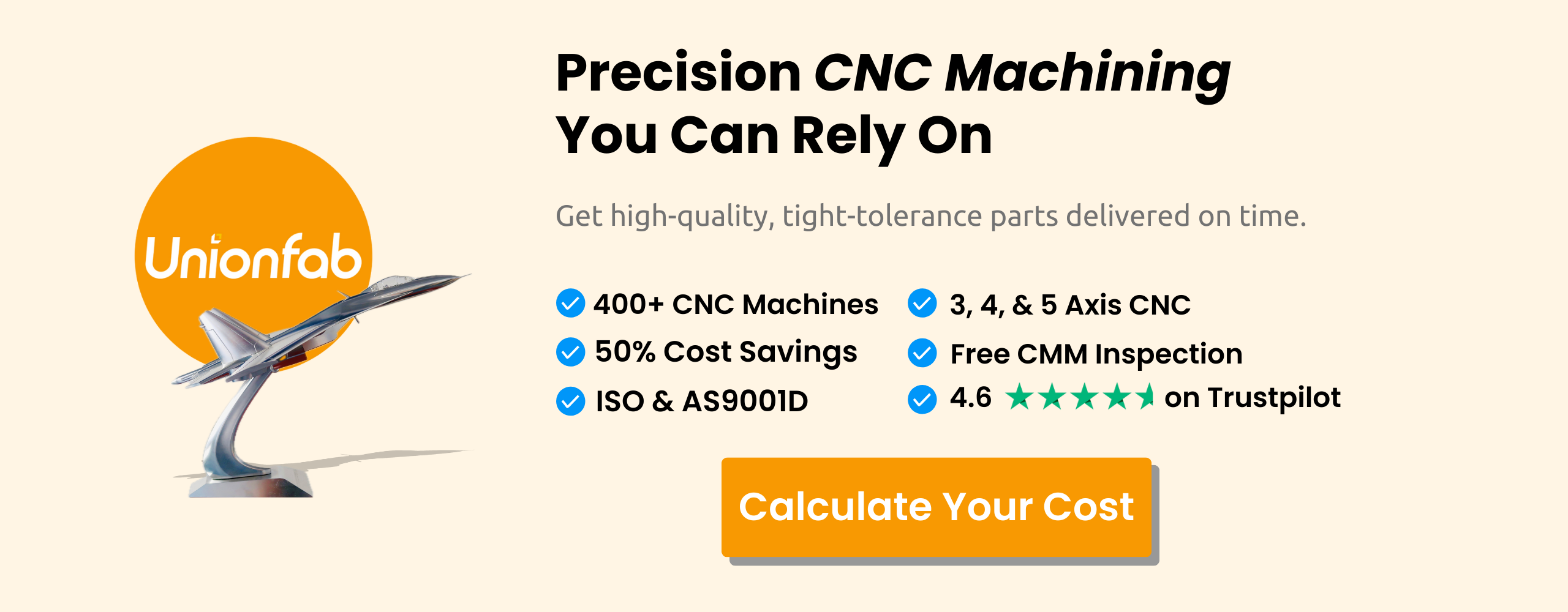
Processing Considerations:
Galvannealed Steel: Suitable for laser cutting, milling, and forming. The alloyed zinc surface holds up well during machining and doesn't flake.
Galvanized Steel: Also machinable but requires extra caution. Cutting exposes bare steel at edges, which may rust if not re-coated. This is critical in structural or visible components.
Unionfab Services Include:
CNC milling, turning, laser cutting for coated steel
Surface finish preservation during fabrication
Optional post-processing: deburring, coating, assembly
Quality assurance for mechanical and aesthetic results
👉 Need help choosing the right material? Talk to our experts
Why Work with Unionfab?
Choosing the right coating material is a critical step in cost control, performance, and long-term durability.
Unionfab supports engineers and procurement teams with:
Expert guidance on material selection
Experience across industries (automotive, electrical, industrial equipment)
Precision machining for both galvanized and galvannealed steel
Integrated services from prototyping to production
Conclusion
In the debate between Galvannealed vs Galvanized, there is no one-size-fits-all answer. Each coating serves specific purposes based on its composition and performance characteristics.
For projects requiring superior corrosion resistance and cost-efficiency, galvanized steel is a solid choice. For applications demanding paintability, weldability, and a smooth finish, galvannealed steel excels.
By understanding these distinctions, manufacturers and engineers can make smarter material decisions that improve product durability, quality, and appearance.
Get a Fast Quote with Unionfab Today
Unionfab provides professional CNC machining services with support for Galvannealed and Galvanized steel.
Upload your drawing now and get a free quote. Let Unionfab help you choose smarter and build faster.
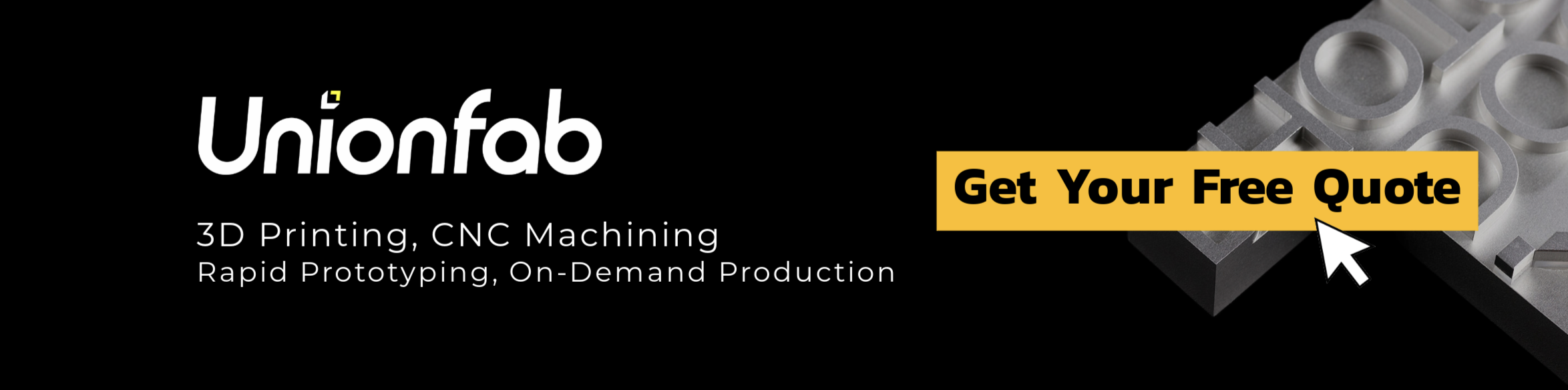
Frequently Asked Questions (FAQ)
1. What is the difference between Galvannealed and Galvanized steel?
Galvanized steel is coated with pure zinc for strong corrosion resistance, ideal for outdoor use. Galvannealed steel goes through an additional annealing process that creates a zinc-iron alloy, which offers better paint adhesion and weldability but slightly less corrosion resistance.
2. Is Galvannealed steel more expensive than Galvanized?
Yes, Galvannealed steel is slightly more expensive due to the added heat treatment step. However, it can reduce costs in the long term through easier processing, better finish quality, and lower maintenance needs.
3. Can you paint Galvanized steel?
It’s possible, but not ideal. Galvanized steel requires surface preparation before painting (like etching or priming), otherwise paint may not adhere well. Galvannealed steel is the better choice for painted applications.
4. Which is better for welding: Galvannealed or Galvanized?
Galvannealed steel is much better suited for welding. Its zinc-iron alloy layer reduces toxic fumes and provides more consistent welds. Galvanized coatings tend to burn off and release zinc oxide fumes when welded.
5. What is the typical coating thickness for Galvanized and Galvannealed steel?
Galvanized steel: 50–100 µm
Galvannealed steel: 5–15 µmThicker coatings on Galvanized steel mean stronger corrosion resistance, but Galvannealed’s thinner layer is better for painting and forming.