Copper CNC Machining [+ Free Cost Calculator]
![Copper CNC Machining [+ Free Cost Calculator]](https://ufc-dtc-cms.oss-accelerate.aliyuncs.com/blog/20250319/150610_j1vyuoodq.png)
Discover how to optimize copper CNC machining with expert tool selection, cutting parameters, and cooling strategies. Get free access to Unionfab’s cost calculator and material selection guide to enhance efficiency and reduce costs.
Introduction
Copper is a highly conductive and corrosion-resistant metal widely used in industries like electronics, aerospace, and automotive manufacturing.
However, machining copper presents unique challenges due to its softness, work hardening tendencies, and chip formation issues. In this guide, we will explore the best techniques, tooling strategies, and optimization methods for achieving precision in copper CNC machining.
Understanding Copper CNC Machining
What is Copper CNC Machining?
Copper CNC machining refers to the process of using computer-controlled tools to cut, shape, and finish copper components with high precision. This method is commonly used in applications requiring excellent electrical and thermal conductivity, such as circuit boards, heat exchangers, and electrical connectors.
Why Choose Copper for CNC Machining?
High electrical and thermal conductivity – Ideal for electronic components and heat dissipation applications.
Corrosion resistance – Suitable for aerospace, marine, and medical applications.
Good machinability – Copper alloys improve workability compared to pure copper.
Aesthetic appeal – Commonly used for decorative and architectural applications.
Antimicrobial properties – Beneficial for medical and food-processing applications.
Learn more about Unionfab’s CNC copper machining services: Unionfab CNC Copper Machining
Properties of Copper That Affect Machining
Copper is a highly versatile metal widely used in electrical, automotive, and aerospace industries due to its excellent conductivity, corrosion resistance, and ductility. However, these same properties present unique challenges when machining copper. Understanding these factors is crucial for optimizing tool selection, cutting parameters, and finishing techniques.
Softness & Ductility
Copper is an inherently soft and ductile metal, which means it deforms easily under cutting forces. While this makes it less prone to breaking, it also leads to:
Burr formation – Small metal fragments remain on the edges of the machined surface, requiring additional deburring steps.
Poor surface finish – The material tends to tear rather than shear cleanly, reducing dimensional accuracy.
Solution: Use sharp carbide tools with a high rake angle to ensure clean cutting and minimize burrs. Adjusting cutting speeds and feeds also helps achieve a smoother finish.
High Thermal Conductivity
Copper has a thermal conductivity of approximately 401 W/m·K (compared to aluminum at ~237 W/m·K), making it one of the most heat-conductive metals used in manufacturing. While this is beneficial for heat dissipation in applications like heat sinks, it poses machining challenges:
Heat is rapidly transferred to the cutting tool, leading to tool wear and reduced lifespan.
Excessive heat buildup can soften copper further, worsening workpiece deformation.
Solution:
Use carbide or coated tools (TiAlN, TiCN) to withstand high temperatures.
Apply coolants and lubricants, such as water-soluble or synthetic cutting fluids, to control heat and prevent tool adhesion.
Optimize cutting speeds—too high can cause overheating, while too low may lead to built-up edges.
Work Hardening
Unlike aluminum or brass, pure copper hardens significantly when subjected to mechanical stress, making it difficult to machine consistently. This phenomenon, known as work hardening, leads to:
Increased cutting forces, which can shorten tool life.
Higher risk of chatter, causing surface imperfections and inaccuracy.
Solution:
Use higher feed rates to minimize material strain.
Select tellurium copper (C145) or beryllium copper (C172), which are less prone to work hardening than pure copper.
Avoid unnecessary re-cutting or excessive tool passes.
⠀
Adhesion to Cutting Tools
Due to its high ductility and low melting point (1,085°C), copper tends to stick to cutting tools, leading to:
Built-up edge (BUE) formation, where chips adhere to the tool, causing inconsistent cutting.
Reduced tool efficiency, requiring frequent tool changes.
Solution:
Use lubricants like oil-based coolants to reduce friction and prevent chip adhesion.
Choose high-polish tool coatings to improve chip evacuation.
Employ proper chip-breaking geometries to enhance chip flow.
⠀
Machinability Comparison: Pure Copper vs. Copper Alloys
Property | Pure Copper (C101, C110) | Tellurium Copper (C145) | Brass/Bronze |
---|---|---|---|
Machinability Rating | 20% (Difficult) | 85% (Easier) | 80-90% (Easy) |
Work Hardening | High | Low | Low |
Chip Control | Poor | Good | Excellent |
Tool Wear | High | Moderate | Low |
Key Takeaways:
For high-precision CNC machining, use Tellurium Copper (C145) for its improved machinability.
Brass and bronze alloys are excellent alternatives where high conductivity is not required.
Design Considerations for Copper Machining
When designing parts for copper CNC machining, it’s essential to account for its unique properties:
Wall Thickness: Maintain uniform wall thickness to prevent uneven cooling and potential warping.
Corner Radii: Incorporate appropriate corner radii to reduce stress concentrations and facilitate smoother machining.
Hole Sizes: Design hole diameters that accommodate standard drill sizes to enhance precision and reduce machining time.
Threading: When designing threaded features, consider using inserts to improve durability, especially in applications requiring frequent assembly and disassembly.
Standard Machining Tolerances
Linear Dimensions: Typically, a tolerance of ±0.1 mm is achievable for most copper parts.
Hole Diameters: Standard tolerances range from H7 to H9, depending on the hole’s function and size.
Surface Finish: Achieving a surface roughness (Ra) of 0.8 to 1.6 micrometers is standard for machined copper surfaces.
Best Copper Grades for Machining
Grade | Properties | Machinability |
---|---|---|
C101 (Oxygen-Free Copper) | High electrical conductivity, difficult to machine | Low |
C110 (Electrolytic Tough Pitch Copper) | Common for electrical applications, challenging to machine | Low |
C145 (Tellurium Copper) | Best machinability, used in precision and electrical parts | High |
C182 (Chromium Copper) | High strength, used in welding electrodes | Medium |
CNC Machining Techniques for Copper
CNC Milling for Copper
CNC milling is one of the most effective methods for machining copper.
Climb milling is recommended over conventional milling because it reduces tool wear and enhances surface finish. Using high-speed spindles and polished carbide end mills helps prevent material adhesion. Additionally, light passes with a high feed rate improve machining efficiency while minimizing heat buildup.
CNC Turning for Copper
CNC turning is widely used for cylindrical copper parts. Sharp carbide inserts with a positive rake angle reduce cutting forces and prevent built-up edge formation.
Using a moderate cutting speed and a generous application of coolant minimizes heat generation and improves dimensional accuracy. Employing low depths of cut and higher feed rates helps manage chip formation efficiently.
CNC Drilling for Copper
Drilling copper requires special attention to chip formation and tool wear. Carbide or cobalt drill bits with a polished surface improve drilling efficiency. The peck drilling technique is highly recommended to break up long chips and improve coolant penetration.
Using split-point drills enhances accuracy, reduces wandering, and minimizes burr formation, resulting in cleaner holes.
Electrical Discharge Machining (EDM) for Copper
EDM is an excellent alternative for machining intricate copper parts. Since EDM does not involve direct contact with the material, it eliminates challenges related to chip formation and tool wear.
Wire EDM is used for high-precision contouring, while sinker EDM is ideal for creating cavities and complex geometries. This technique is particularly useful for copper alloys that are difficult to machine using conventional methods.
Cost Optimization Strategies
How to Reduce Machining Costs?
Optimize CNC Toolpaths: Reduce unnecessary tool movements to minimize material waste.
Batch Production Efficiency: Large quantity orders lower unit costs by reducing machine setup time.
Use Durable Tooling: High-performance tools extend tool life and reduce replacement costs.
Select the Right Material: Choosing the best copper alloy for the application reduces machining difficulty and cost.
Use Unionfab’s Free Cost Calculator to Estimate Pricing: Unionfab CNC Cost Estimator
Key Supplier Selection Criteria
Choosing the right supplier ensures efficiency and quality. Key factors to consider:
Machining Precision: Can they meet ±0.01 mm tolerances?
Delivery Time: Fast turnaround and reliable lead times.
Quality Assurance: Stringent quality control to ensure accuracy.
Scalability: Ability to handle both small and large production runs.
Cost Transparency: Clear pricing with no hidden fees.
Find out why Unionfab is the right supplier: Unionfab CNC Services
Industry Applications
Electronics
Used in EV electrical systems and high-efficiency heat sinks.
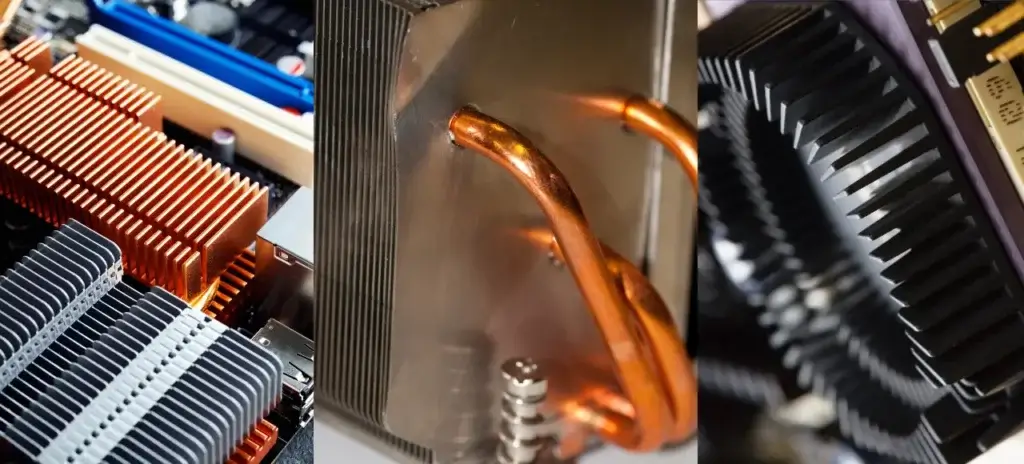
Source: zetwerk.com
Aerospace
Copper’s excellent thermal conductivity is crucial for thermal control components and precision connectors.
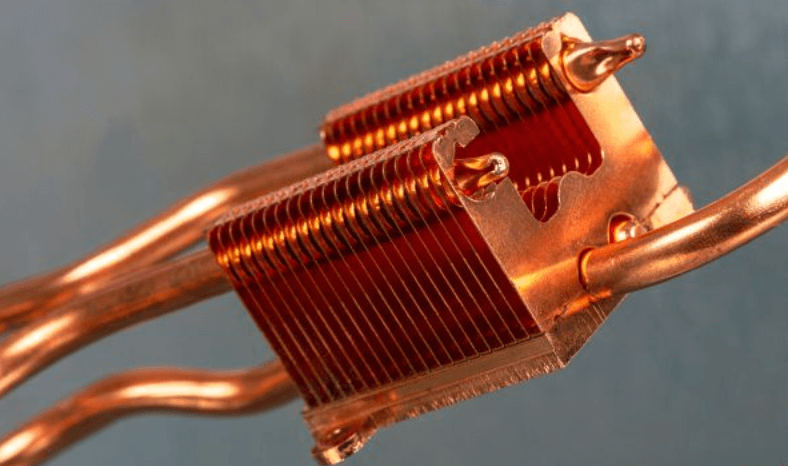
Source: termopasty.com
Medical Devices
Antimicrobial surgical tools and FDA-compliant implant parts.
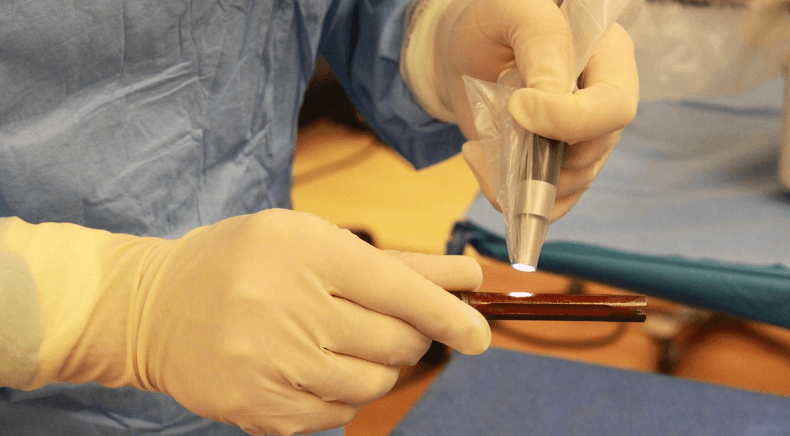
Source: pratt.duke.edu
Automotive
Fuel delivery systems and electrical components for hybrid and electric vehicles.
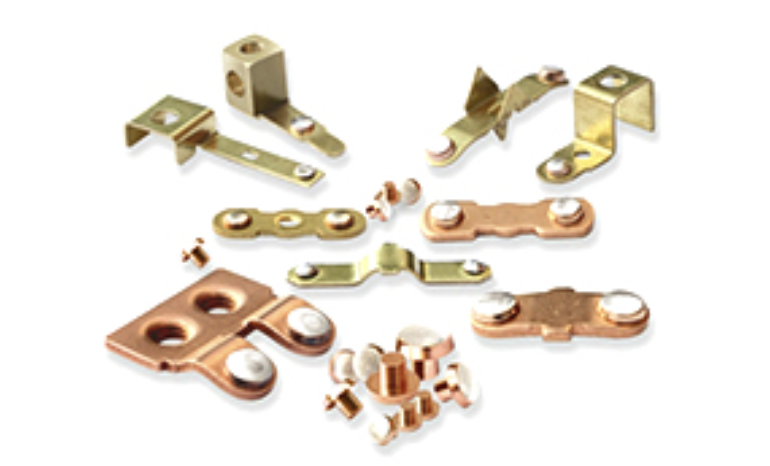
Source: conexcopper.com
Why Choose Unionfab for Copper CNC Machining?
At Unionfab, we specialize in high-precision CNC machining for copper and other metals.
Get expert CNC machining with Unionfab!
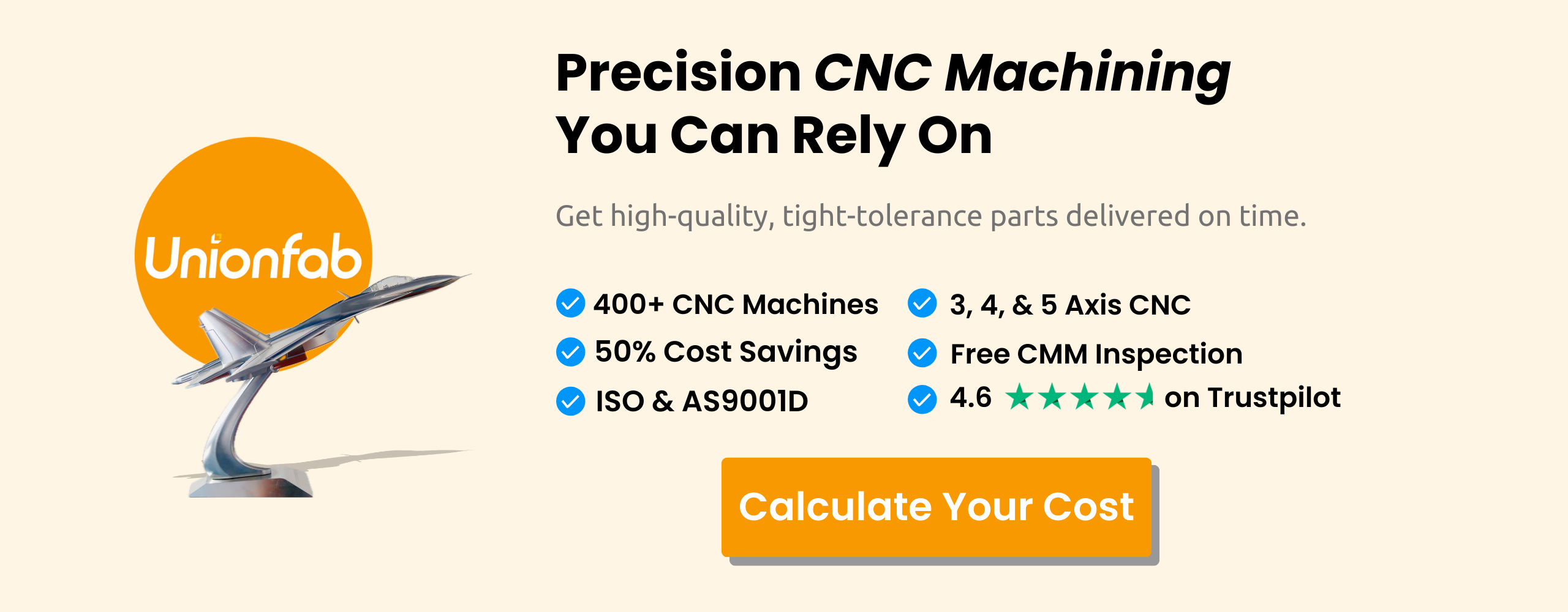
Looking for a trusted CNC machining partner for copper components? Unionfab provides precision, efficiency, and expert craftsmanship.
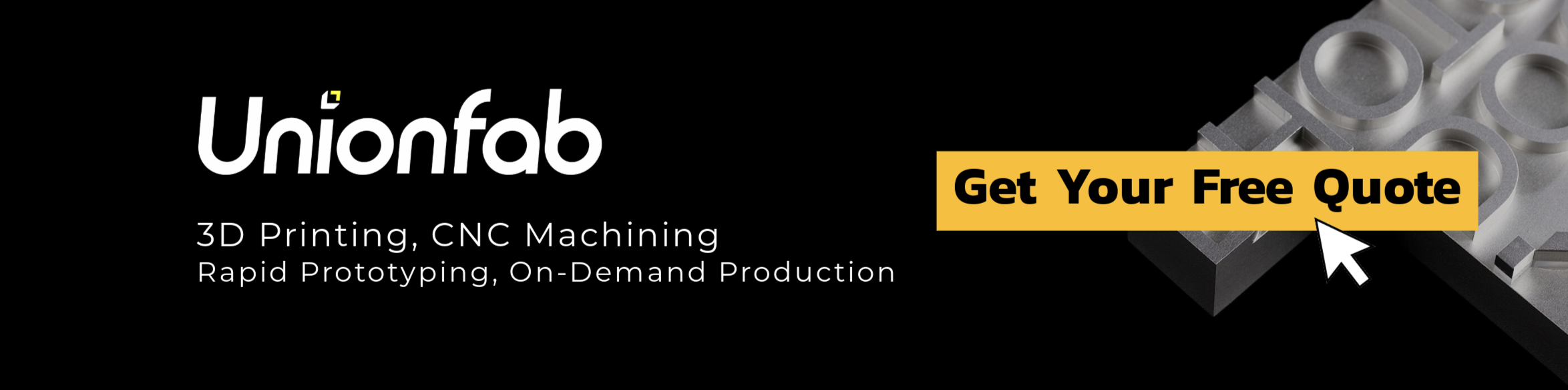