Guide to SLM 3D Printing/Metal LPBF [+Cost Calculator]
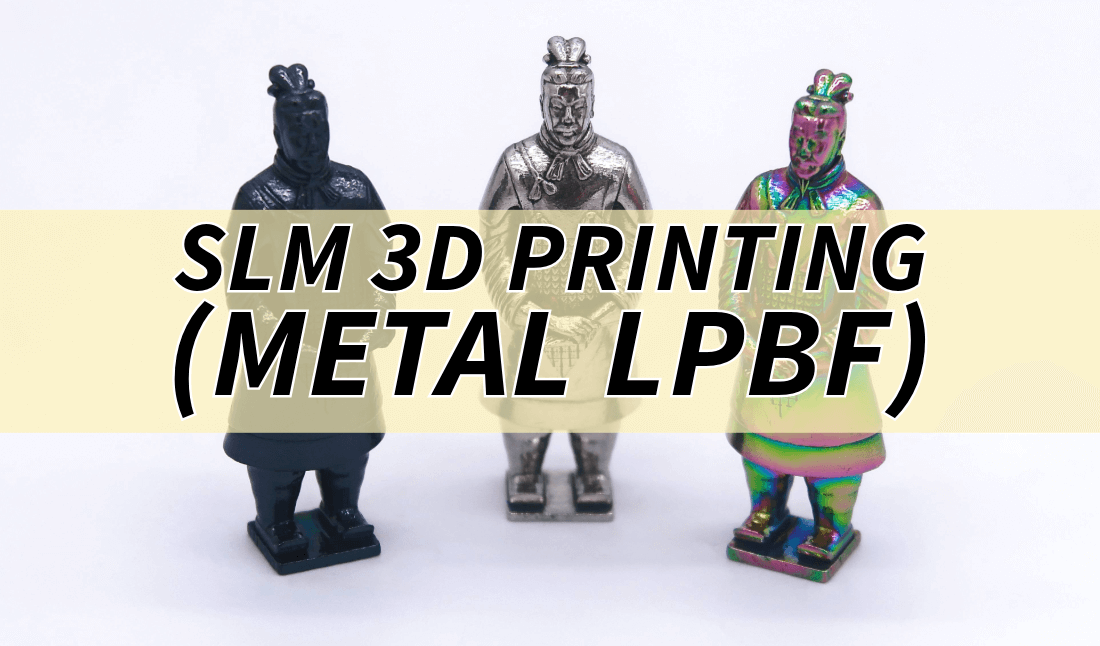
Figure out what is SLM 3D Printing / Metal LPBF and choose the most suitable service provider in one guide.
Introduction
When producing metal parts, especially complex and custom designs, with traditional manufacturing methods, we may often face these challenges:
Significant time and money on mold creation upfront;
Low material efficiency, leading to considerable waste;
Inadequate precision, causing rework and delayed deliveries.
All of them will greatly impact production timelines, costs, and overall efficiency. And this is where metal 3d printing, especially SLM 3d printing, comes in as a game-changer, providing solutions with better value for money.
What Is SLM 3D Printing?
SLM stands for Selective Laser Melting. It uses a high-powered laser to fully melt metal powder layer by layer. Based on different material states, energy sources, and forming methods uses, the Standard ISO/ASTM 52900:2021 has divided 3d printing technologies into 7 categories, among which, SLM can be categorized as Powder Bed Fusion (PBF).
More precisely, SLM, along with Selective Laser Sintering (SLS), belongs to Laser Powder Bed Fusion (LPBF) because they use laser. Since SLM only processes metal, it’s also called metal LPBF.
Beyond lasers, the PBF category also includes EPBF (Electron Powder Bed Fusion), which utilizes an electron beam as its energy source.
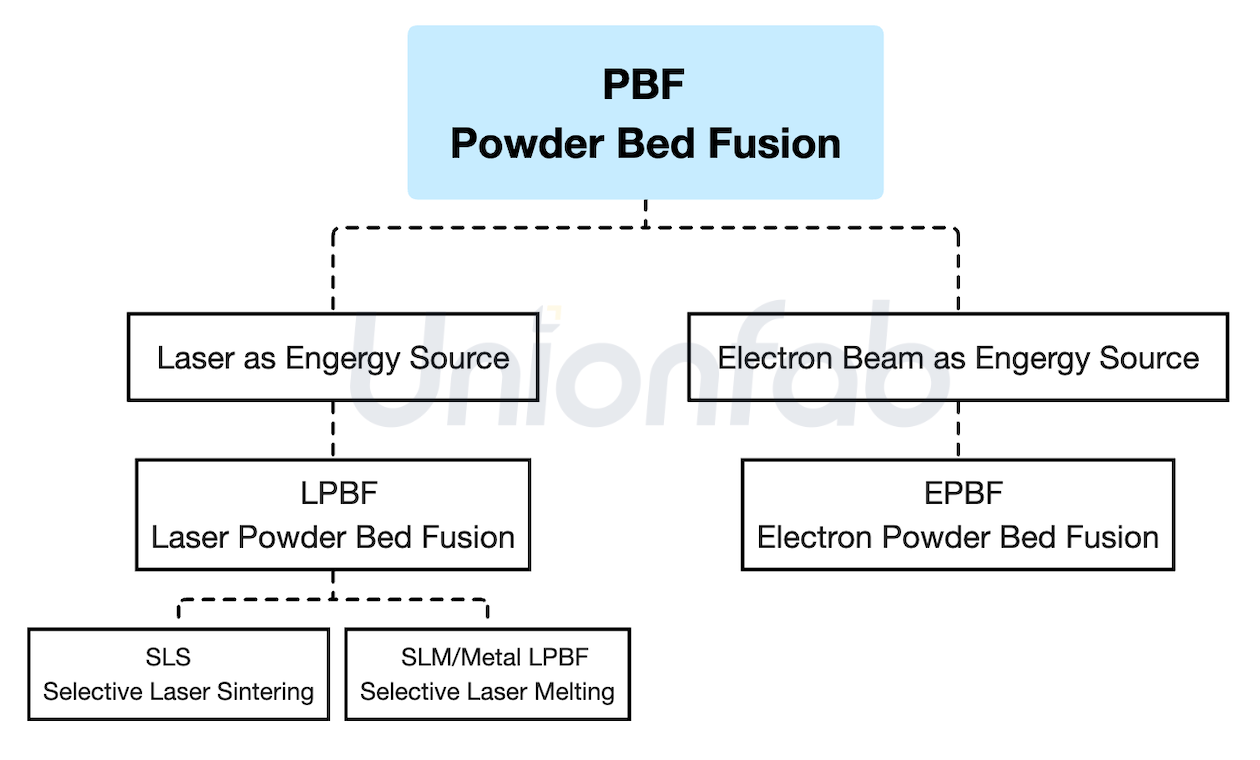
How Does SLM 3D Printing Work?
Components of a SLM 3D Printer
To understand how SLM 3d printing works, it is necessary to figure out what a SLM 3d printer is composed of and how each part functions. An SLM 3d printer usually consists of the following critical components.
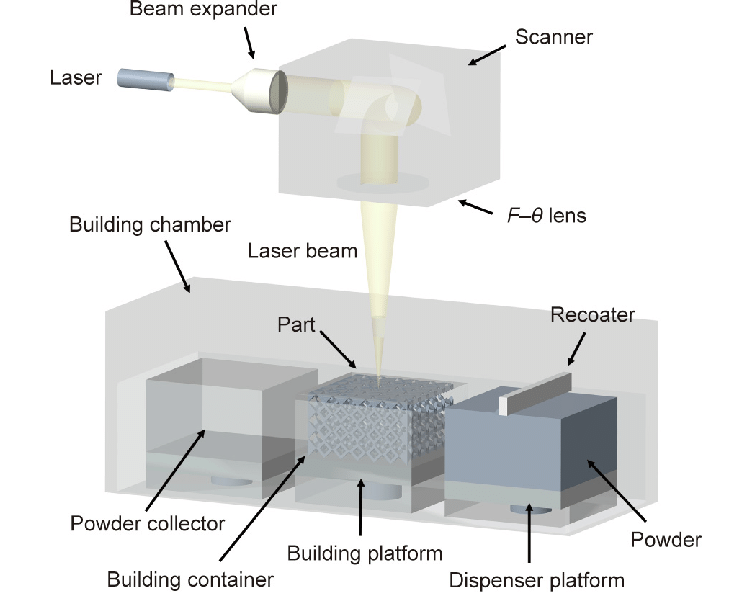
Part | Component | Description |
---|---|---|
Scanning System | Laser | Commonly fiber lasers; |
Lens | Focuses the laser for precise work. | |
Scanner | Directs the laser to the desired locations | |
Building Chamber | Building Space | The enclosed area where printing happens. |
Building Platform | Also called substrate or printing bed; | |
Powder Collector | Gathers leftover powder for reuse. | |
Powder Supplier | Feeds new powder for printing. | |
Recoater | Spreads a thin layer of powder evenly. | |
Inert Gas | Commonly argon or nitrogen; | |
Control System | Computer | Oversees and controls the entire printing. |
SLM 3D Printing Process
After knowing what is a SLM 3d printer, it will be easier for us to understand the process. The SLM 3D printing process usually involves the following steps:
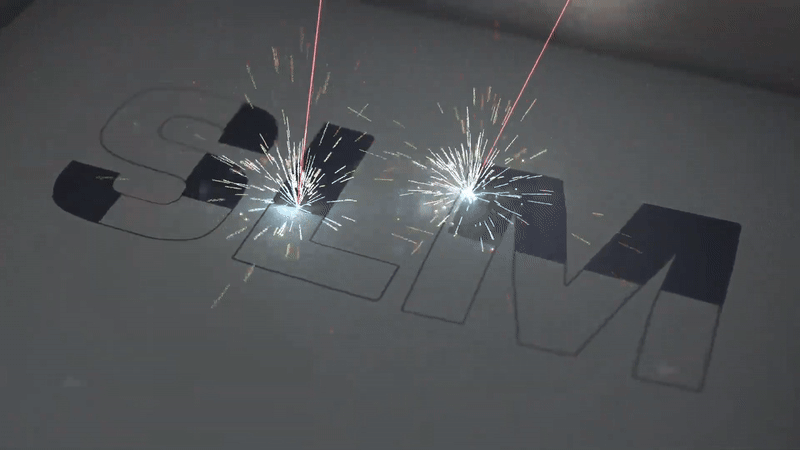
3D Model Preparation and Slicing: A digital 3D model of the object is created using CAD software and then sliced into thin layers.
Powder Spreading: A thin layer of metal powder (usually 20 to 50 μm) is spread evenly across the build platform using the recoater.
Laser Melting: The laser selectively melts the powder according to the cross-sectional pattern of the first layer, fusing the particles together.
Layer Completion: Once a layer is complete, the build platform lowers by one layer thickness, and a new layer of powder is spread.
Repetition: Steps 2-4 are repeated until the entire object is built.
Post-Processing: After printing, the object is removed from the build platform, and excess powder is removed. Additional post-processing, such as heat treatment or surface finishing, may be required.
Materials Used in SLM 3D Printing
The common metals used in SLM 3d printing are Aluminum Alloy, Steel, Titanium and Copper Alloy. Here we have compared their performances in different properties.
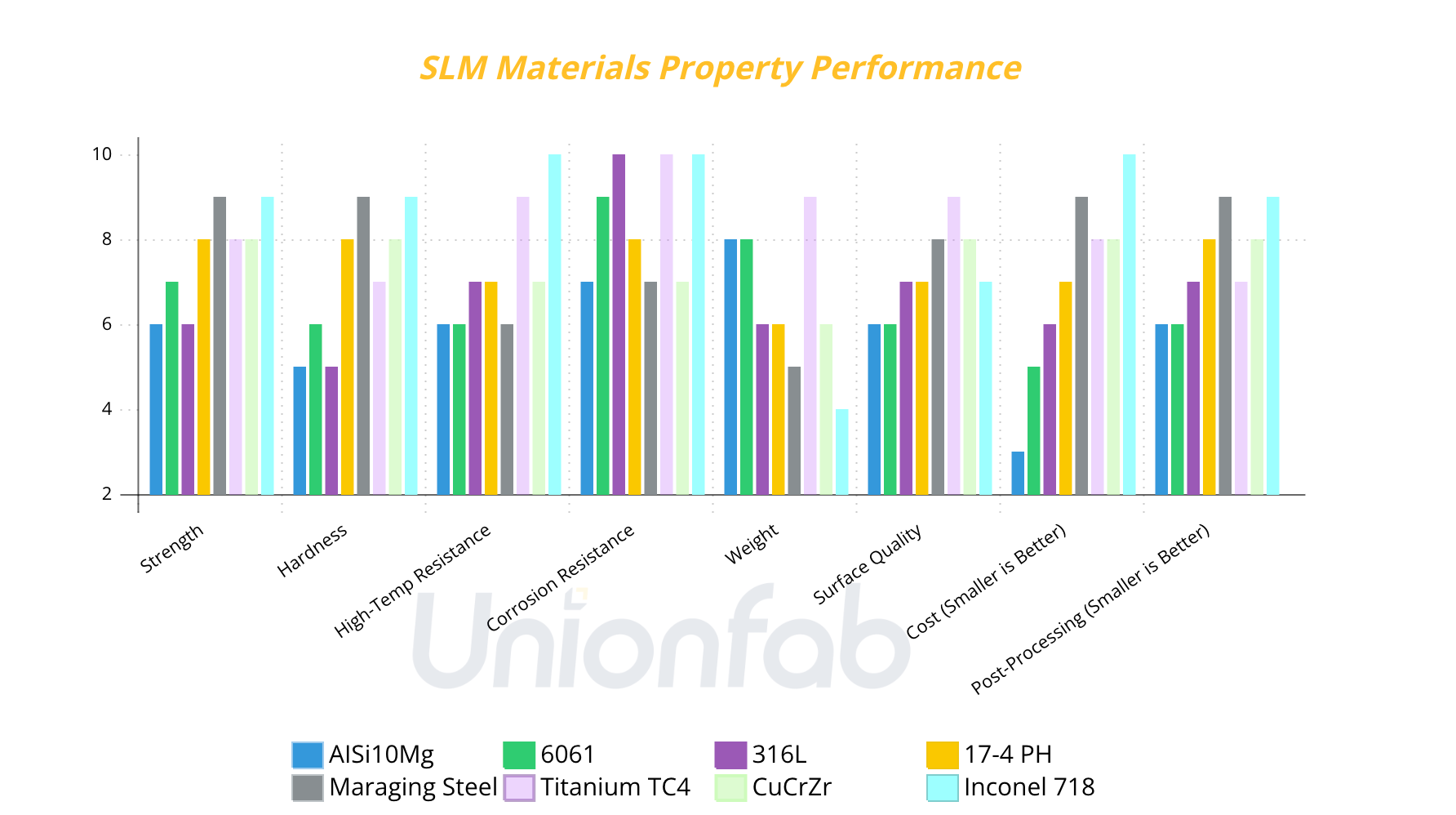
Note: The values in the chart are only used for comparing materials’ performance in different aspects above and have no other meaning.
As we can see from the bar chart,
AlSi10Mg and 6061: Suitable for lightweight, low-cost applications, but have poor high-temperature resistance.
316L: Excellent corrosion resistance, ideal for medical and chemical industries.
17-4PH and Maraging Steel: High strength, suitable for high-strength structural components and molds, but come with higher costs.
TC4: Excellent overall performance, ideal for aerospace and medical fields, but expensive.
CuCrZr: Outstanding thermal performance, suitable for thermal management and electronics, but relatively heavy.
Inconel 718: Exceptional strength, high-temperature resistance, corrosion resistance, and durability, making it ideal for extreme environments like aerospace and power generation.
For more details of the properties of the materials above, you can download their data sheets from our material page.
Design Guideline for SLM 3D Printing
After gaining a basic understanding of SLM technology and materials, it is also essential to strictly follow certain guidelines in model design to prevent potential issues and ensure smooth printing.
Layer Thickness | 0.035 mm |
---|---|
Min. Wall Thickness | 0.5 mm |
Tolerances | ±0.2 mm |
Min. Hole Diameter | 1 mm |
Min. Internal Channel Diameter | 2 mm |
Beyond following the design guideline above, some other key considerations should be taken into account as well before you print the model.
1. Optimize Geometric Design
Avoid Overhangs: Minimize overhang angles (typically >45° requires supports) to reduce support needs and simplify post-processing.
Add Fillets: Use fillets on sharp corners to reduce stress and prevent cracks or deformation during printing.
2. Reduce Support Needs
Self-Supporting Designs:
Use arch or triangular structures for natural support.
Design overhangs in stepped shapes to keep angles below 45°.
Shorten Overhangs: If overhangs are unavoidable, reduce their length to minimize supports.
3. Choose the Best Print Orientation
Surface Quality: Orient critical surfaces (e.g., exteriors) toward the top or sides to reduce support marks.
Thermal Stress: Ensure even mass distribution to avoid overheating or warping.
Function First: Prioritize functional needs (e.g., load direction) when selecting orientation.
4. Check 3D Files
Ensure the model is watertight (no holes or gaps).
Fix non-manifold edges (misconnected faces).
Verify normals are correct (all faces outward).
Use 10-20 triangles per mm for balanced file size and accuracy.
5. Design Proper Part Clearance
When designing parts that need to fit together or move relative to each other, ensure sufficient clearance for smooth assembly or motion.
Assembly Clearance: At least 0.3mm to avoid fitting issues.
Motion Clearance: At least 0.5mm for smooth movement, and 1mm or more for parts requiring frequent motion
6. Simulate and Validate
Simulation Tools: Use software (e.g., ANSYS, SimScale) to predict thermal stress and deformation, optimizing the design.
Prototype Testing: Print a small prototype to test design feasibility and print quality.
DMLS vs. SLM vs. EBM Vs. Binder Jetting
In addition to SLM, there are several other metal 3D printing technologies: DMLS, EBM, and Binder Jetting. The table below distinguishes these technologies to help you choose the most suitable one.
Before comparing, we need to clarify that DMLS and SLM are two different names for the same technology, MLPBF. Therefore, in the table below, we will list them under the same column. For more information on the naming of DMLS and SLM, we recommend reading the article by All3dp.
Aspect | SLM/DMLS | EBM | |
---|---|---|---|
Energy Source | Laser | Electron Beam | Liquid Binder |
Environment | Inert Gas (e.g., argon, nitrogen) | Vacuum | Ambient Air |
Build Speed | Moderate | High | Very High |
Material Options | Wide range (aluminum, titanium, stainless steel, nickel alloys, etc.) | Limited | Moderate range (stainless steel, tool steel, titanium, etc.) |
Support Structures | Required | Minimal | Not required (binder holds powder in place) |
Part Size Limitations | Limited by build chamber size | Limited by vacuum chamber size | Larger build volumes possible |
Post-Processing | Required | Minimal | Required (sintering, infiltration, surface finishing) |
Part Density | Fully dense | Fully dense | Porous |
Mechanical Strength | High | High | Lower |
Surface Finish | Excellent | Rough | Moderate (typically requires post-processing) |
Material Waste | Moderate | Moderate | Low |
Real-World Usability | Best for high-performance, complex parts | Best for high-strength, high-temperature applications | Best for prototyping, tooling, and low-to-medium stress components |
Scalability | Moderate (limited by build chamber size and speed) | Moderate (limited by vacuum chamber size) | High (large build volumes, batch processing) |
Cost | High | High | Lower (scalable) |
Operator Skill Level | High | High | Low to Moderate (easier to operate) |
Ease of Use | Moderate | Moderate | Easy |
Environmental Impact | Moderate (inert gas usage, energy-intensive) | Moderate (vacuum system energy consumption) | Lower (no heat source, less energy-intensive) |
Multi-Material Capability | Limited (typically single-material) | Limited (typically single-material) | Possible (supports multi-material printing, though not common) |
Conclusion
SLM is ideal for high-precision, complex parts with excellent mechanical properties but comes at a higher cost.
EBM is suited for high-strength applications, especially in aerospace and medical fields, with faster build speeds but limited material options.
Binder Jetting is cost-effective and scalable for prototyping and less demanding applications but requires post-processing to achieve desired properties.
Comparison of SLM 3D Printing Service Providers
To help you choose the most suitable 3d printing service provider, we have listed a table to compare the key metal 3d printing service providers around the world in terms of the following aspects.
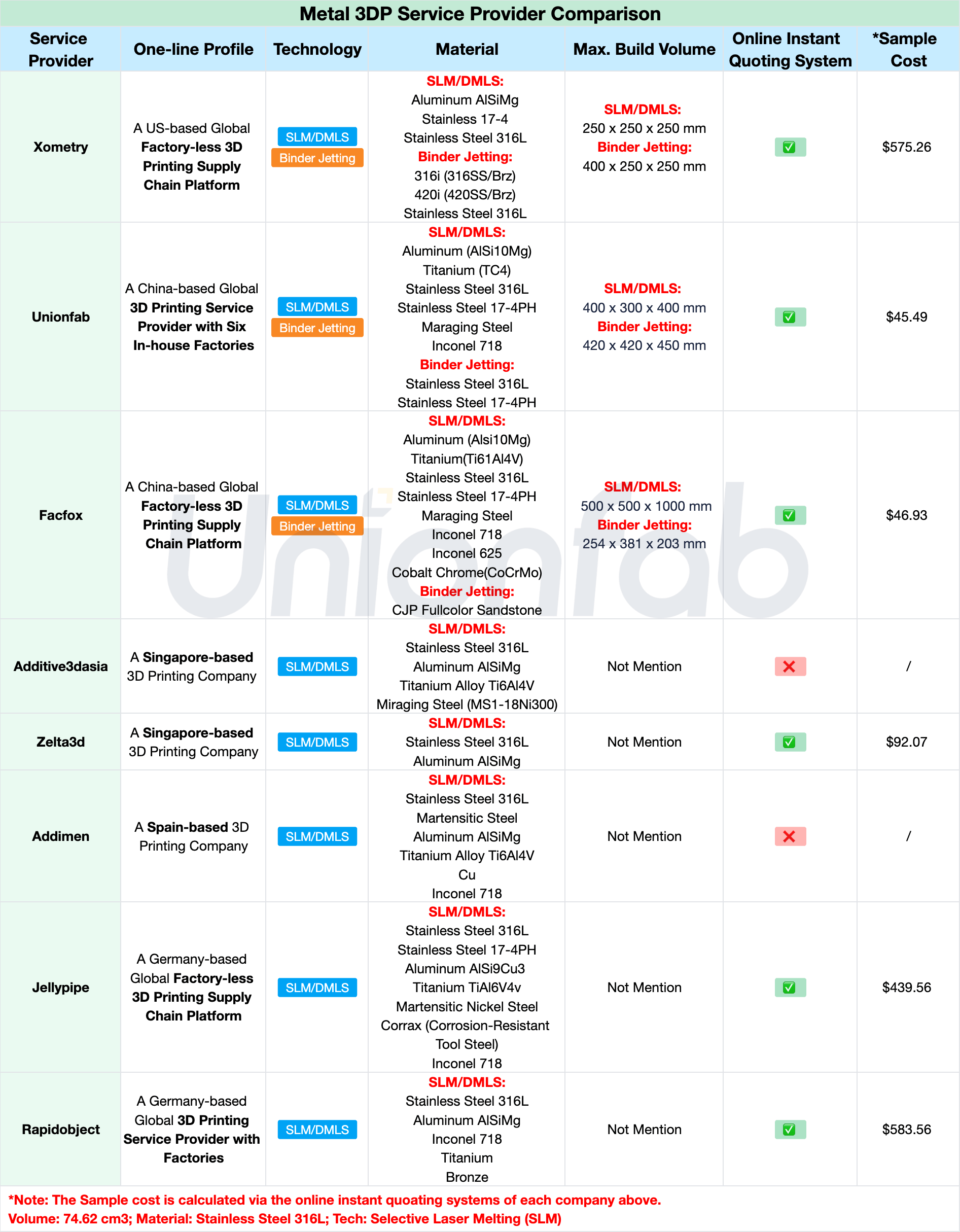
In summary,
Xometry, Unionfab, and Facfox offer both SLM/DMLS and Binder Jetting Technologies.
Xometry, Unionfab, and Facfox provide relatively rich metal materials.
Facfox has the largest build volume for SLM/DMLS: 500 x 500 x 1000 mm.
Unionfab has the largest build volume for Binder Jetting: 420 x 420 x 450 mm.
Xometry, Facfox, and Jellypipe are factory-less supply chain platforms, while Unionfab and Rapidobject have self-owned factories.
Below is the score of some companies above on Trustpilot. You can click the score to see feedback from real customers.
How to Reduce SLM 3D Printing Cost?
Below are some specific strategies from the design perspective that can help minimize printing costs.
Simplify Design
Minimize complex details and overhangs to reduce print time and material usage.
Avoid excessive supports by using self-supporting angles or simpler shapes.
Optimize Wall Thickness & Structure
Use minimal wall thickness for strength.
Design parts as hollow or with lattice structures to save material and weight.
Optimize Print Orientation
Adjust part orientation to reduce supports and print time.
Choose the most efficient orientation (horizontal/vertical) to reduce waste.
Choose Cost-Effective Materials
Select cheaper materials when performance isn’t critical.
Use lightweight designs like lattices to reduce material use.
Consolidate Parts
Combine multiple parts into one to reduce print count and cost.
Design for modularity to simplify assembly after printing.
Minimize Post-Processing
Design parts to need less post-processing, reducing labor and time.
Ensure supports are easy to remove and parts are close to the final shape.
Optimize Powder Usage
Design to minimize metal powder waste and increase powder reuse.
Collaborate with Service Providers
Work with your printer to follow their best practices for cost-effective printing
To predict the cost of your 3d model, you can upload your model to Unionfab’s free online cost calculator to check it out.
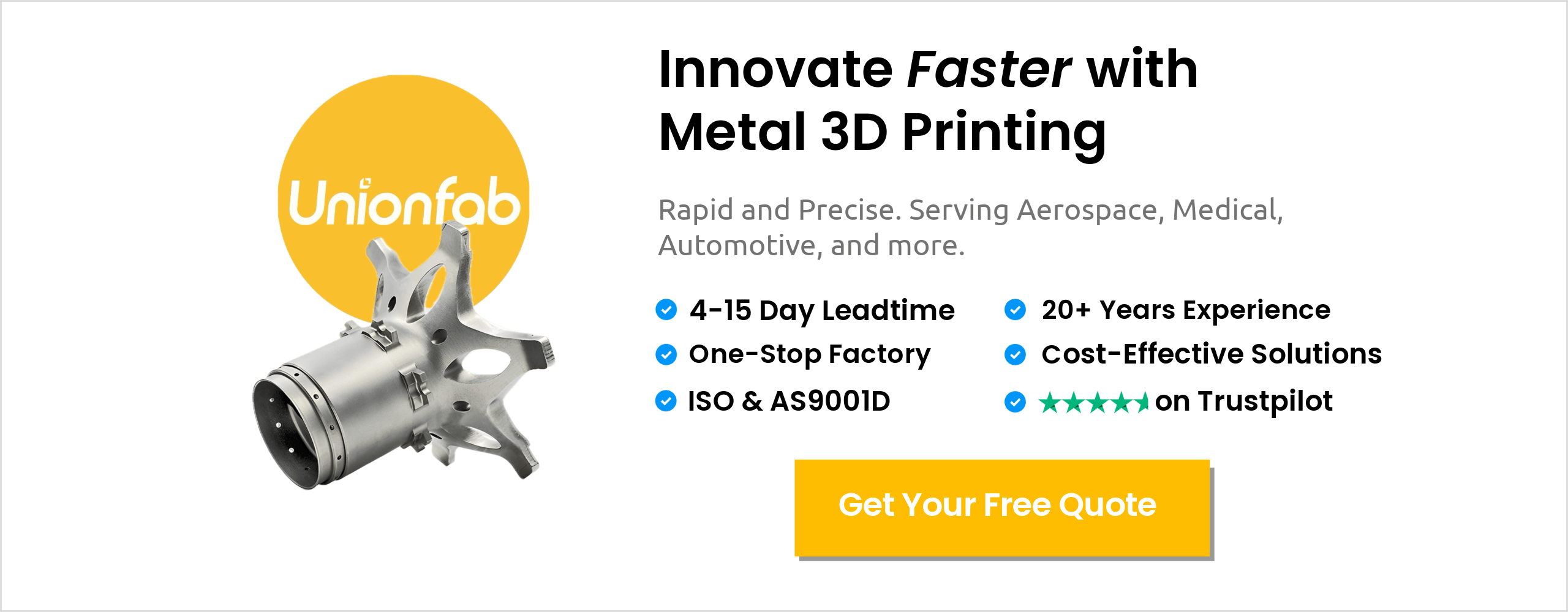
Unionfab’s Metal 3D Printing Service
With 20+ years of expertise, 1,000+ industrial 3D printers, and 6 cutting-edge factories, Unionfab, certified with ISO 9001, ISO 13485, and AS 9001D, is committed to delivering high-quality, cost-effective 3D printing services.
The followings are the details of our SLM printing service.
SLM/DMLS | Binder Jetting | |
---|---|---|
Equipment | BLT; SLM; EOS; EXONE | HP S100 |
Materials | Aluminum (Alsi10Mg) |
|
Max Part Size | 400 x 300 x 400mm | 420 x 420 x 450mm |
Layer Thickness | 0.035 mm | 0.035 mm |
Tolerance | ±0.2 mm | ±0.2 mm |
Min. Wall Thickness | 0.5 mm | 0.5 mm |
*Min. Reference Unit Price of Materials | Aluminum (Alsi10Mg): $0.6/g | Aluminum (Alsi10Mg) $0.6/g |
Pass Rate | 99.5% | 99.5% |
Lead Time | As fast as 4-5 days | As fast as 4-5 days |
On-time Delivery Rate | 98% | 98% |
Certification | ISO 9001, ISO 13485, and AS 9001D | ISO 9001, ISO 13485, and AS 9001D |
*The actual unit price is subject to real-time inquiry.
Post Processing
We not only provide high-precision printing but also a range of post-processing options below, including sandblasting, electroplating, and polishing etc., to improve surface quality, durability, and aesthetics of the prints, ensuring the perfect fit for various applications.
![]() | ![]() | ![]() | ![]() | ![]() |
---|---|---|---|---|
![]() | ![]() | ![]() | ![]() | ![]() |
![]() | ![]() | ![]() | ![]() | ![]() |
QA Report
In addition to delivering cost-effective prints, we also offer quality assurance services and can send the QA report with the shipment.
Btw, if you haven’t used Unionfab’s 3d printing service yet, sign up now to get a 10% discount on your first order!
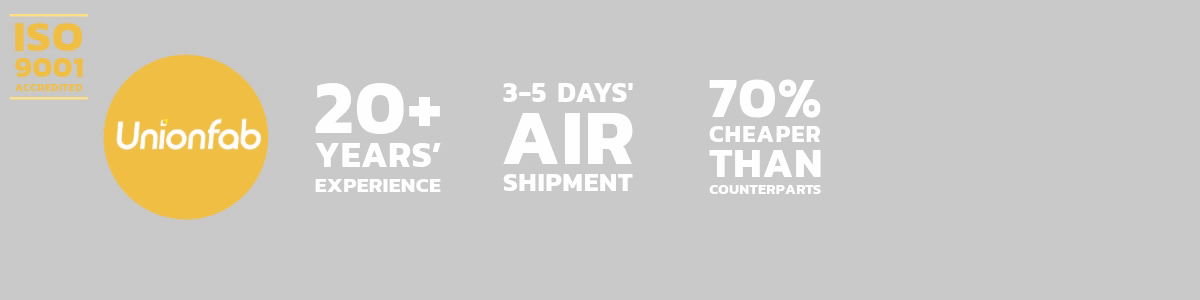
Customer Review
See Unionfab’s customer review from Trustpilot:
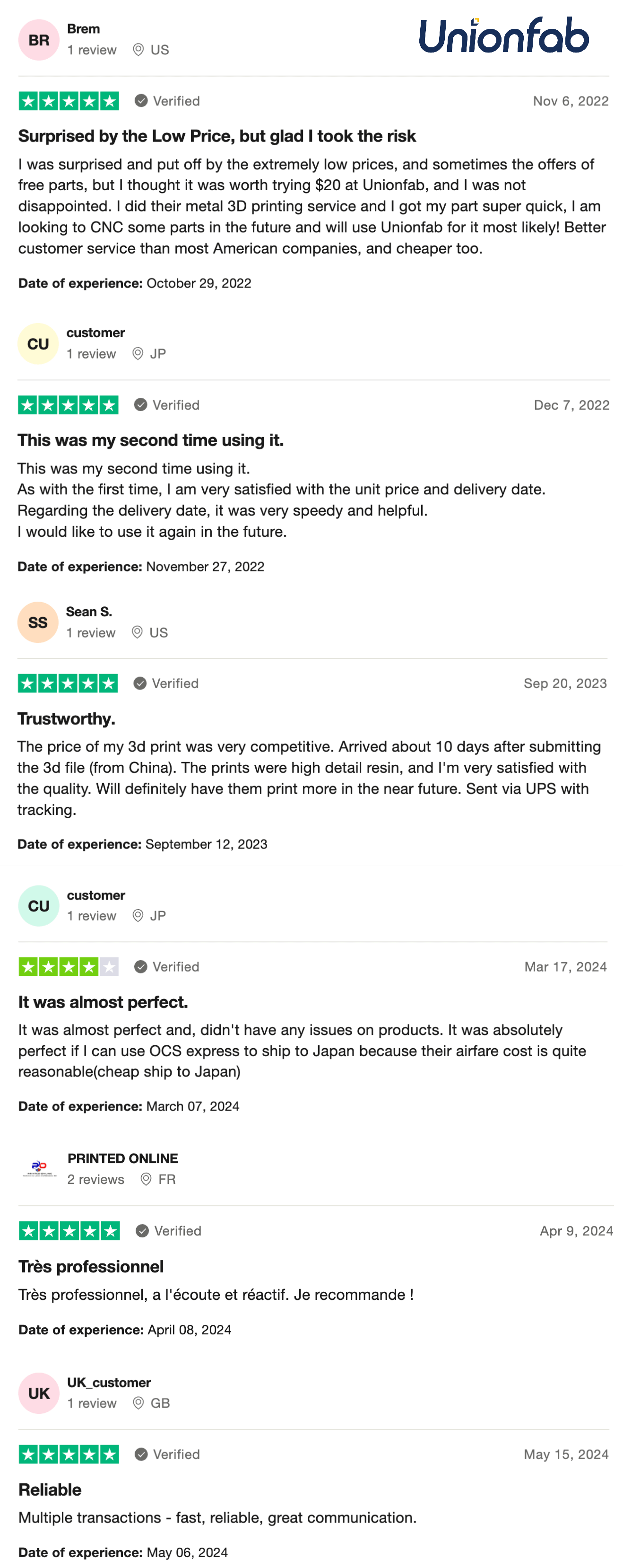
FAQs
How much does it cost to 3d print something using SLM?
The cost varies depending on the material, part size, complexity, and print time. To get more details, you can read the article: How much does it cost to 3d print something?
What is the difference between SLS and SLM?
SLS (Selective Laser Sintering) uses a laser to fuse powdered material (often plastic, whereas SLM (Selective Laser Melting) melts the metal powder completely to form a solid structure. To get detailed comparison, you can read the article: SLA vs SLS vs SLM.
What is the most expensive metal for 3D printing?
Titanium (especially Ti-6Al-4V) is one of the most expensive metals for 3D printing due to its high performance and strength-to-weight ratio.
What is the cheapest metal for 3D printing?
Aluminum is typically the cheapest metal used in 3D printing due to its relatively low cost and wide availability.
What is the toughest metal for 3D printing?
Inconel (especially Inconel 718) is known for its toughness, especially at high temperatures, making it ideal for aerospace and high-performance applications.