Metal Binder Jetting: Your Complete Guide [+ Key Comparisons]
![Metal Binder Jetting: Your Complete Guide [+ Key Comparisons]](https://ufc-dtc-cms.oss-accelerate.aliyuncs.com/blog/20241226/153758_acu5b2dh0.png)
Learn how Metal Binder Jetting offers cost-effective, scalable metal 3D printing with design freedom that surpasses DMLS/SLM.
Introduction
Metal Binder Jetting is an innovative and cost-effective metal 3D printing technology that is reshaping the manufacturing landscape. In this guide, we’ll explore the details of the Metal Binder Jetting process, highlighting its diverse applications across industries.
Additionally, we’ll compare it with other widely used manufacturing methods, such as CNC machining, casting, and DMLS/SLM 3D printing, providing you with the insights needed to choose the most suitable approach for your specific production needs.
Learn more about this unique metal 3D printing solution here.
What is Metal Binder Jetting?
Metal Binder Jetting is an additive manufacturing process where a liquid binder selectively bonds layers of powdered metal to create a green part. This part undergoes post-processing, such as sintering or infiltration, to achieve final strength and durability.
Binder Jetting Process
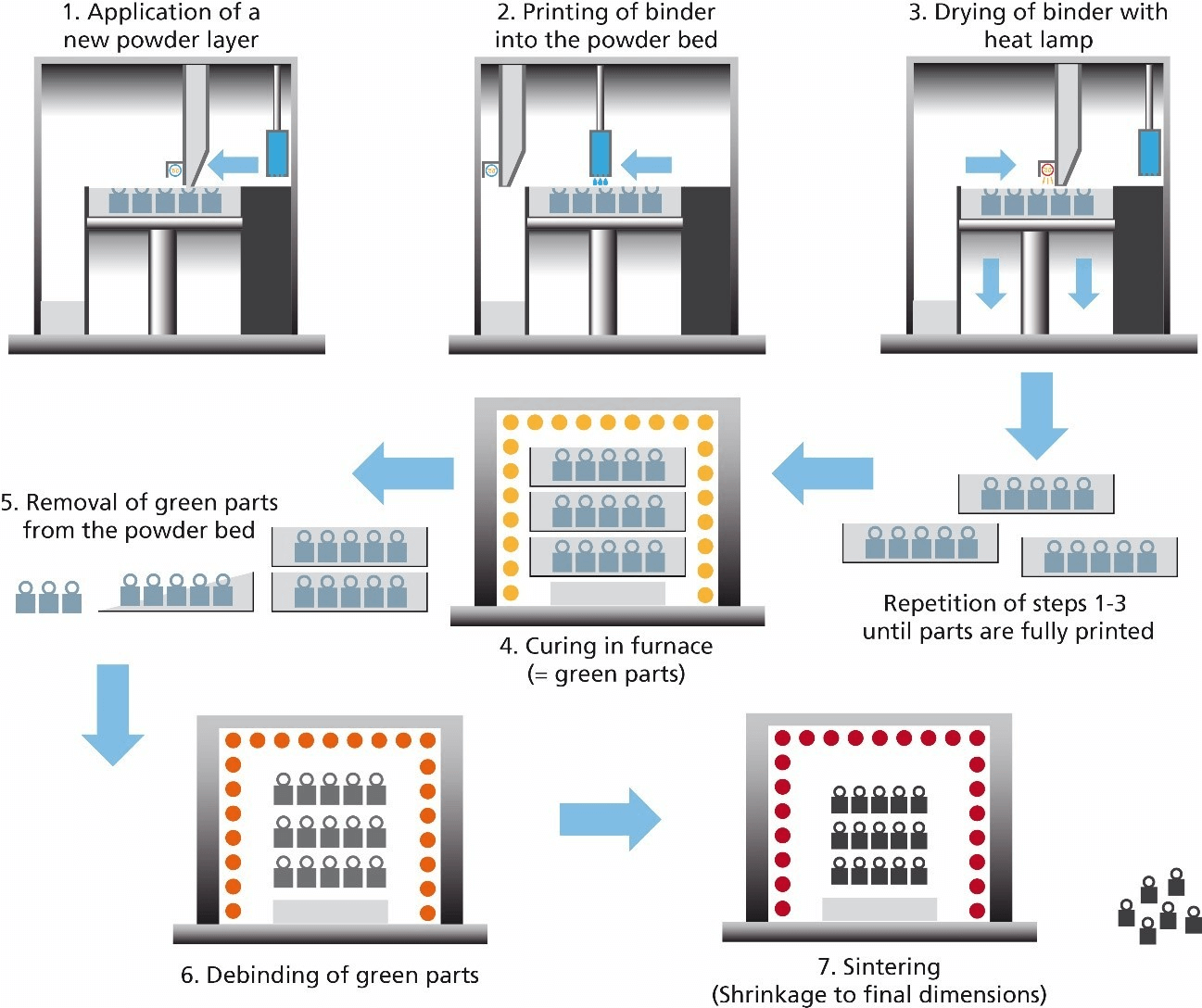
The Binder Jetting process involves several steps:
Layer-by-Layer Printing: A printhead deposits liquid binder onto a bed of metal powder, binding the powder layer by layer.
Curing: The printed part is gently cured to solidify the binder.
Depowdering: Excess powder is removed, leaving a fragile green part.
Post-Processing: The green part undergoes sintering, where high temperatures fuse the metal particles, or infiltration to achieve final density.
Binder Jetting Materials
Metal Binder Jetting supports a range of materials, including:
Stainless Steel: Ideal for functional prototypes and industrial parts.
Titanium: Lightweight and strong, suitable for aerospace and medical applications.
Copper: Excellent for heat and electrical conductivity applications.
Ceramics: Used for specialized applications in industries like electronics.
This technology is recognized as a key player in low-cost metal 3D printing due to its efficient use of materials and batch production capabilities.
Top Applications of Metal Binder Jetting
Metal Binder Jetting is widely used across industries for:
Production of Complex Parts
Metal Binder Jetting (MBJ) excels at producing small-to-medium batches of intricate parts, thanks to its unique ability to build without support structures.
This capability enables the creation of complex geometries, such as lightweight brackets with internal cavities or heat exchangers with intricate lattice designs, which are challenging or impossible to achieve with traditional methods.

Source: Unionfab
Robust Prototypes for Testing
MBJ can produce strong prototypes suitable for functional testing, provided the post-sintering process is done correctly. It's frequently used in product development for early validation.
Lightweight Structures
Ideal for drone frames, medical implants, and other applications requiring reduced weight and structural integrity.
Artistic and Consumer Products
Perfect for producing intricate designs in jewelry, art, and custom consumer goods.
Problems with Traditional Metal Manufacturing
Traditional manufacturing methods like CNC machining and casting have long been used for metal part production. However, these approaches often face significant limitations:
High Costs: Customization or low-volume production incurs significant expenses due to setup and tooling.
Long Lead Times: Casting molds require extensive development time, delaying production schedules.
Complex Geometry Restrictions: CNC machining struggles with intricate designs, while casting cannot easily produce fine details or internal structures.
Why Choose Metal Binder Jetting?
Emerging technologies like Metal Binder Jetting offer an innovative alternative for industries seeking cost-effective, fast, and flexible production solutions.
Cost Efficiency
Metal Binder Jetting provides a significant cost advantage, especially for small-to-medium batch production.
By minimizing material waste and enabling batch processing, it lowers overall production costs compared to traditional methods.
Rapid Production
The Binder Jetting process reduces time from design to final product. Its digital workflow eliminates tooling and mold preparation, making it faster than CNC machining and casting for many applications.
Complex, Lightweight Parts
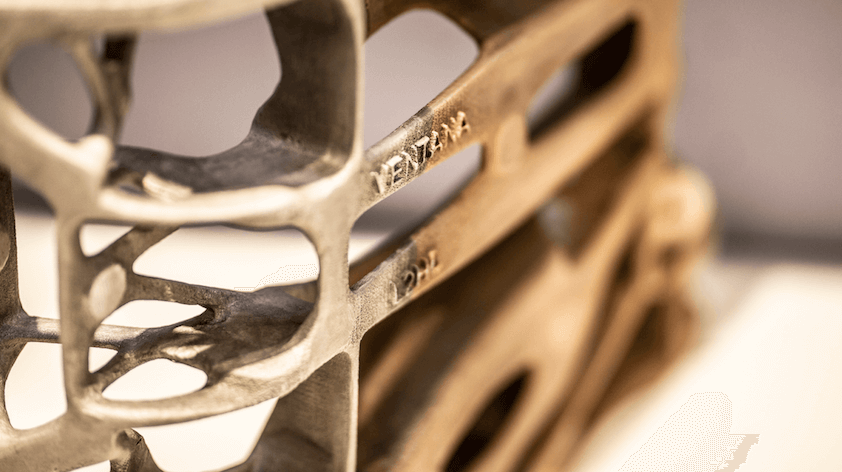
Source: exone.com
Unlike many traditional manufacturing methods, Metal Binder Jetting (MBJ) can produce intricate and complex structures without additional cost.
Its ability to build without support structures, unlike Selective Laser Melting (SLM), makes it particularly well-suited for creating designs with internal cavities, lattice structures, and lightweight components.
This capability is essential for industries like aerospace and automotive, where reducing weight while maintaining structural integrity is a critical design requirement.
MBJ vs. DMLS: A Comparison
Both Metal Binder Jetting and Direct Metal Laser Sintering (DMLS) are leading technologies in metal 3D printing, each excelling in distinct areas.
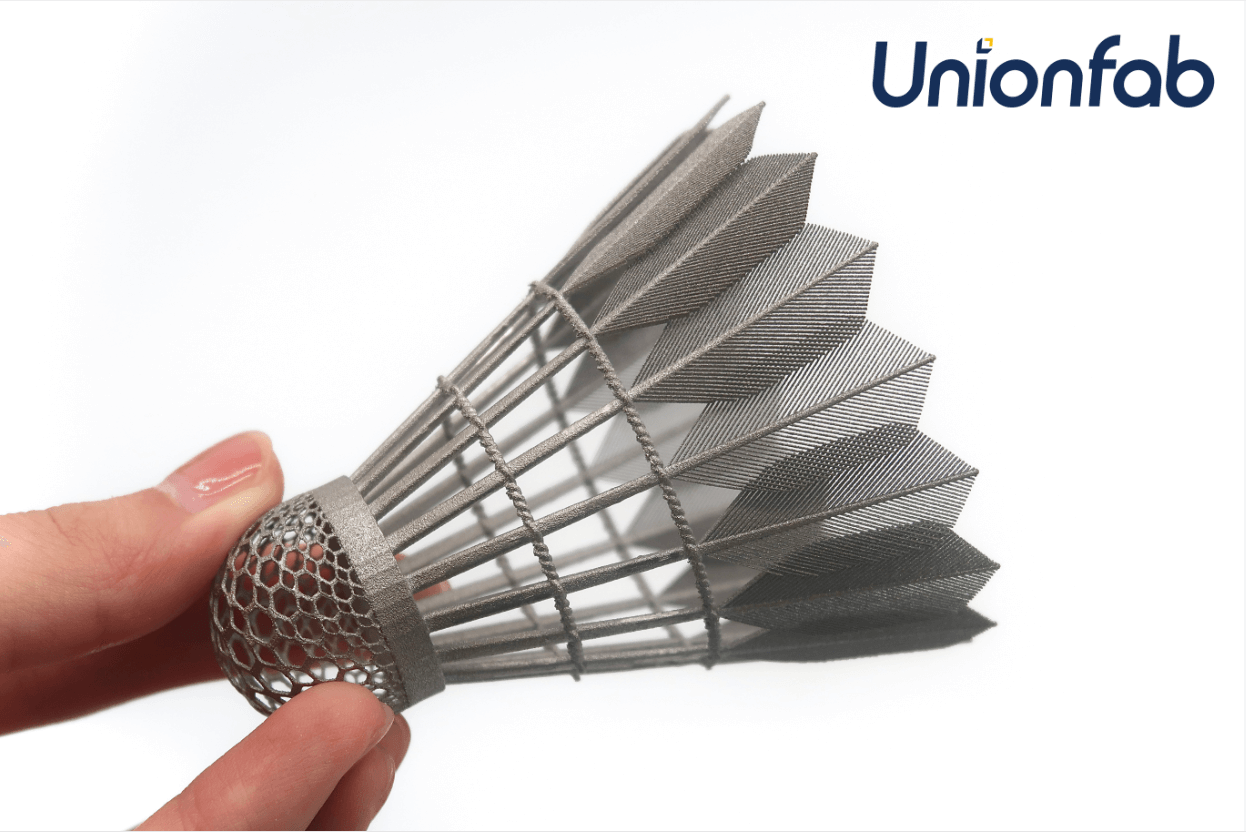
Source: Unionfab
To help you choose the right solution for your needs, here’s a detailed comparison of their key features and applications.
Feature | Metal Binder Jetting (MBJ) | DMLS/SLM |
---|---|---|
Support Requirements | No supports needed; ideal for complex geometries. | Requires supports; limits design flexibility. |
Production Speed | Faster printing, but debinding and sintering extend total time (7–15 days). | Direct process; faster overall for small batches (4–5 days). |
Cost | Cost-effective in large batches in regions like Europe/North America. Higher cost for small batches. | Lower cost for small, high-precision batches. |
Material Flexibility | Limited but expanding. | Extensive, includes specialty alloys. |
Part Strength | Medium-to-high strength after sintering. | High strength directly from printing. |
Applications | Complex geometries, medium batches, no-support parts. | High-precision, small-batch parts (e.g., aerospace). |
Want to learn more about metal 3D printing? Visit Unionfab Metal 3D Printing Services.
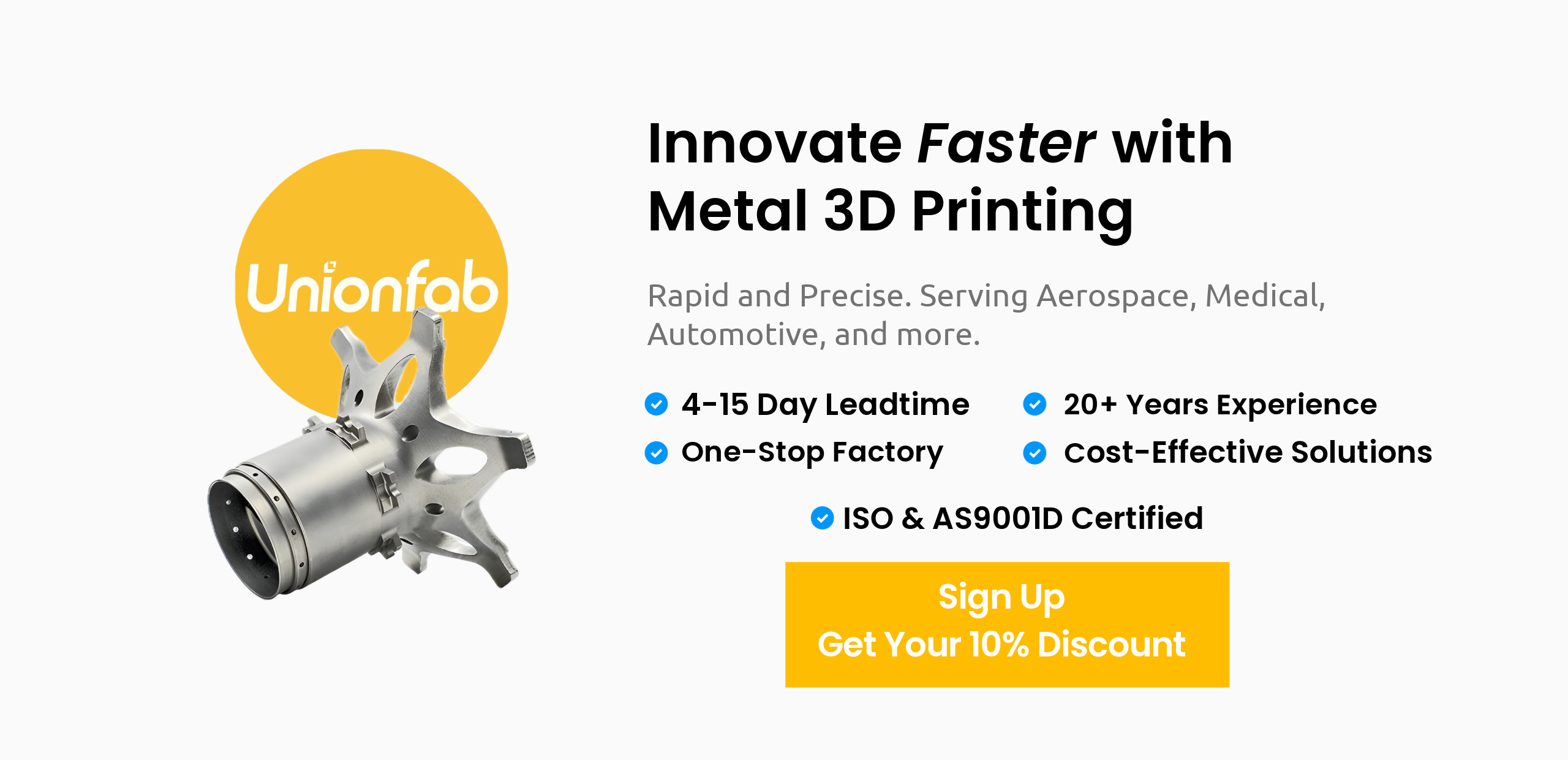
When to Choose Metal Binder Jetting
Metal Binder Jetting is ideal for various scenarios where cost, speed, and design complexity are priorities. Key use cases include:
Parts Without Support Structures
MBJ doesn’t need support structures, making it ideal for creating complex shapes like internal cavities or lattice designs that would be hard to produce with SLM.
Cost-Sensitive Projects
If your application can tolerate slightly lower density or strength, this process offers significant cost savings compared to other methods. Its batch production capabilities make it a cost-effective solution.
Low-to-Medium Volume Production
MBJ is especially cost-effective for producing dozens or hundreds of parts since the cost of debinding and sintering is spread across more units.
Rapid Prototyping
This technology enables faster prototyping cycles, allowing designers to test and iterate on new ideas more quickly, reducing overall development time. But for small and high-precision batches, DMLS/SLM excels in cost and efficiency.
Sustainability Goals
With reduced material usage and lower energy consumption, Metal Binder Jetting is a sustainable option for companies aiming to minimize their environmental impact.
Unionfab’s Binder Jetting: Your Reliable Solution
Unionfab offers industry-leading Binder Jetting services with unique advantages:
High-Efficiency Production: Fast and cost-effective solutions for batch manufacturing.
Industry Experience: 20+ years of industry experience. Comprehensive support from prototyping to production.
Comprehensive Post-Processing Options: Explore detailed finishes at Metal 3D Printing Finishes.
Quick Delivery: Receive your parts within 7-15 days.
Diverse Material Selection: Learn more about available materials at Binder Jetting Materials.
Design Guidelines for Optimal Results: Check our Metal 3D Printing Design Guidelines to ensure the best outcomes.
Conclusion
Metal Binder Jetting offers a balance of affordability, scalability, and design flexibility, making it a standout option in metal 3D printing. While DMLS/SLM provides exceptional precision and material options, Metal Binder Jetting excels in medium-volume production and cost efficiency.
Want to experience the high-efficiency and low-cost production of Binder Jetting? Contact us today.
Ready to try metal 3D printing? Get your instant quote now!
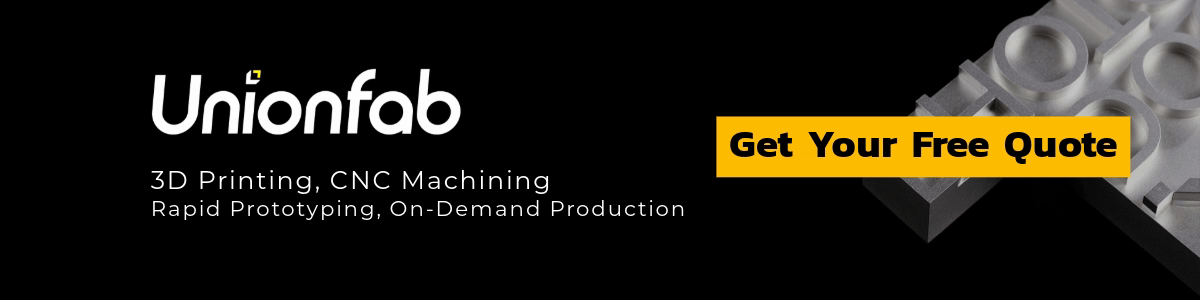