Blow Molding vs Injection Molding: Key Differences
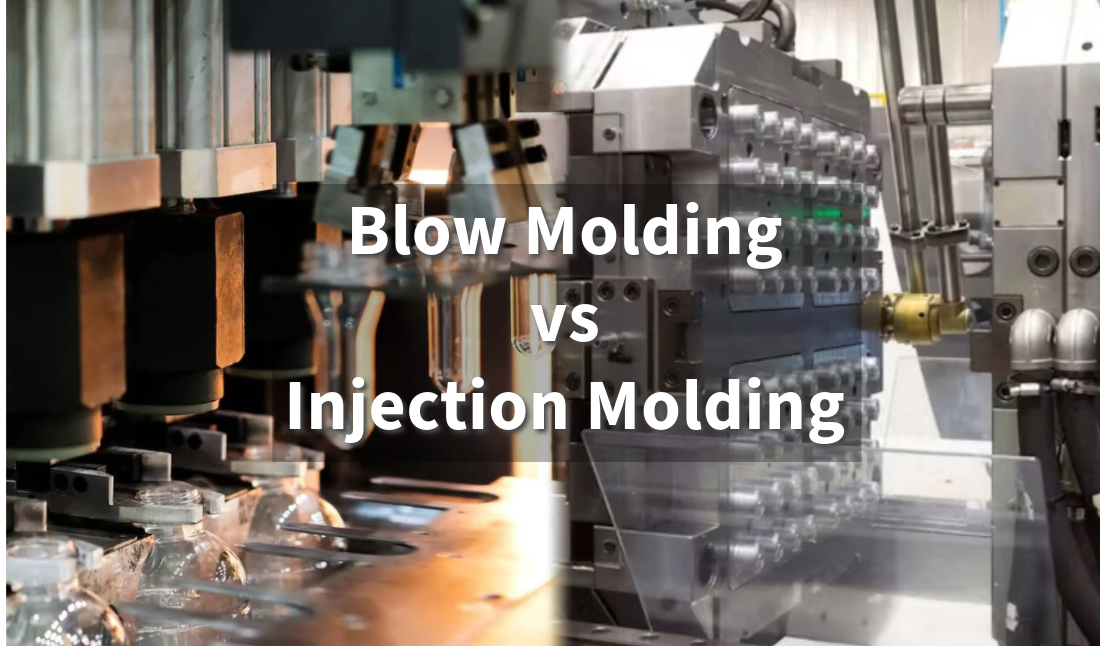
Learn the differences between blow molding and injection molding, their unique advantages, and which process suits your manufacturing needs.
Introduction
Blow molding and injection molding are two common ways to shape plastic into different products. Both use molds to make objects, but they work differently and are used for different types of items. Knowing these differences can help you pick the right method, whether you are making or buying products.
Blow molding is used to make hollow plastic items, like bottles and containers. Injection molding, on the other hand, is used to make solid items, such as toy parts, household products, and machinery components. Understanding how these methods work can help you decide which is better for what you need—whether it's lightweight containers or strong, durable parts.
What is Blow Molding?
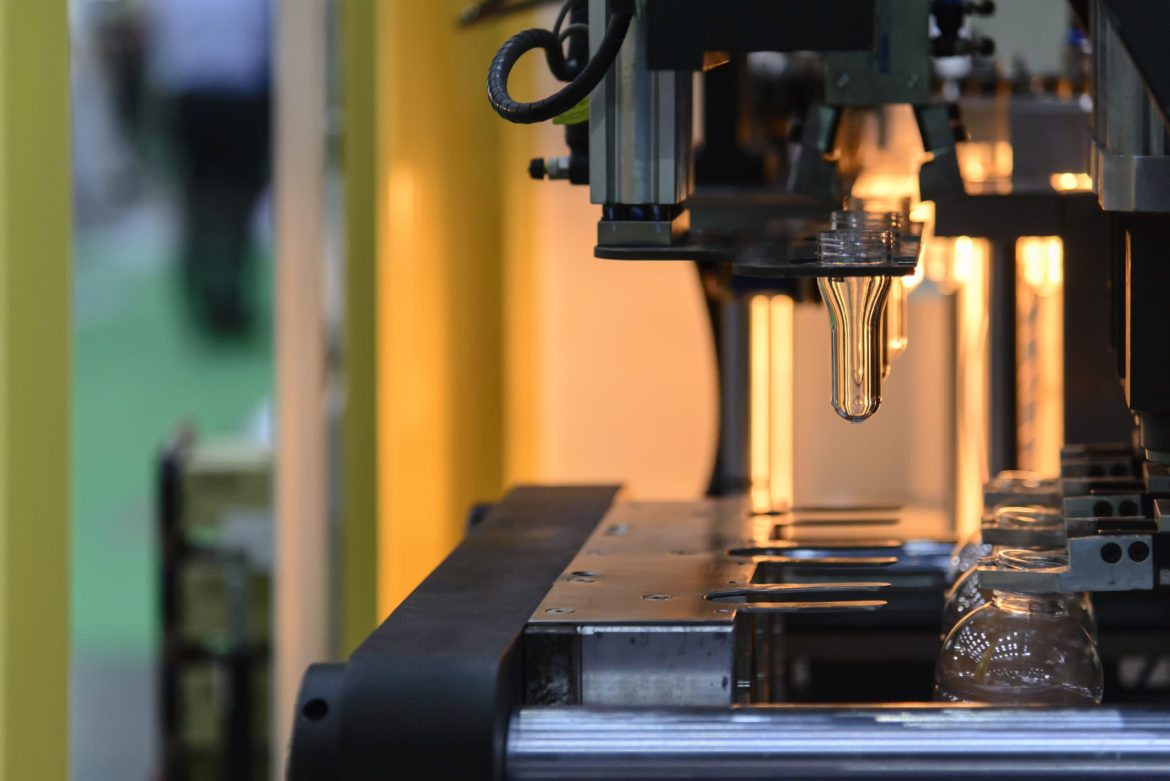
Source: valenciaplastics.com
Overview of the Blow Molding Process
Blow molding is a way to make hollow plastic products by blowing air into a heated plastic tube inside a mold until it takes the shape of the mold. It starts by melting plastic and forming it into a parison, which is a tube-like piece of plastic with a hole at one end. Air is then blown into the parison, pushing the plastic against the mold to create the final shape.
Types of Blow Molding
Extrusion Blow Molding: In this type, plastic is melted and shaped into a parison, which is then inflated to make the product. This method is used for making bottles and large containers.
Injection Blow Molding: This method involves injecting molten plastic into a preform, which is then moved to a blow mold and inflated. It is used for smaller containers, like medicine bottles.
Stretch Blow Molding: In this process, the plastic preform is stretched and blown into shape. This method is used to make strong, lightweight bottles, like those for soft drinks.
Typical Materials Used
Common materials used in blow molding include polyethylene (PE), polypropylene (PP), and polyethylene terephthalate (PET). These materials are flexible, strong, and good for making hollow shapes.
Applications and Common Products
Blow molding is used to make items like plastic bottles, containers, fuel tanks, and other hollow products. It is great for making lightweight, durable products used in packaging, cars, and household goods.
What is Injection Molding?
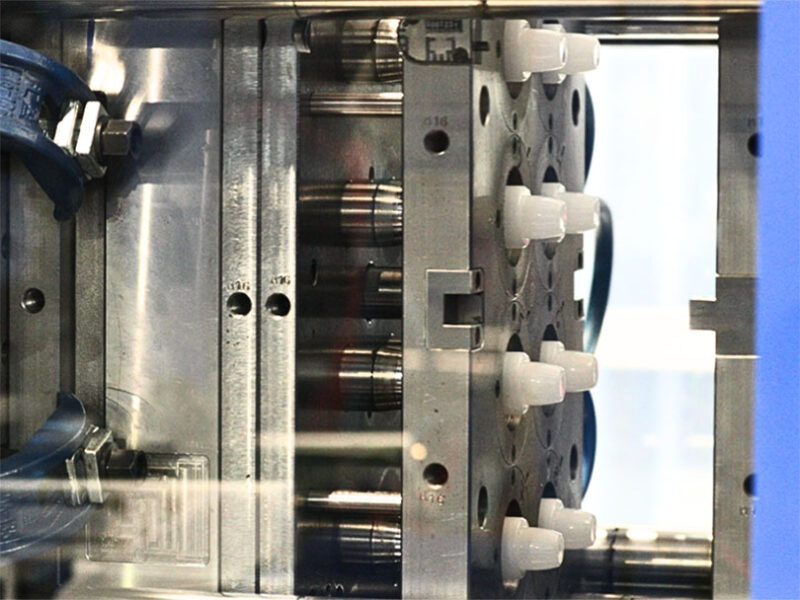
Source: sybridge.com
Overview of the Injection Molding Process
Injection molding is used to make solid plastic parts by injecting melted plastic into a mold. The process starts by heating plastic pellets until they melt. The molten plastic is then injected into a mold, where it cools and hardens into the final shape. Injection molding is great for making large numbers of identical parts with a lot of detail.
Materials Used in Injection Molding
Materials used in injection molding include polystyrene (PS), polypropylene (PP), polyethylene (PE), acrylonitrile butadiene styrene (ABS), and nylon. These materials are strong, durable, and good for making complex shapes.
Examples of Products Made with Injection Molding
Injection molding is used to make products like plastic housings, car parts, household goods, toys, and medical devices. It is ideal for making detailed parts that need to be consistent.
Key Differences Between Blow Molding and Injection Molding
Process Differences
Blow molding involves blowing air into heated plastic to form hollow items, while injection molding involves injecting molten plastic into a mold to make solid parts. Blow molding is used for hollow items, while injection molding is used for solid, detailed parts.
Material Considerations
Both methods use materials like polyethylene (PE) and polypropylene (PP). Injection molding also uses materials like ABS and nylon, which add strength and complexity. Blow molding materials are good for making flexible, hollow shapes.
Design Flexibility
Injection molding is more flexible for making complex, detailed parts. Blow molding is better for simpler designs but works well for lightweight, hollow products.
Production Volume and Cost
Injection molding is cost-effective for making a lot of identical parts due to its precision and efficiency. Blow molding is more affordable for large, hollow items, especially when they don’t need to be very complex.
Product Characteristics
Blow molding is best for lightweight, hollow products like bottles and containers. Injection molding is great for making solid, durable parts with lots of details, like car components and household goods.
Pros and Cons of Each Method
Advantages and Disadvantages of Blow Molding
Advantages:
Cost-effective for making hollow products.
Great for lightweight containers.
Good for high-volume production of simple, uniform items.
Disadvantages:
Limited design options.
Not suitable for very detailed parts.
Hollow products are usually not as strong as solid parts.
Advantages and Disadvantages of Injection Molding
Advantages:
High precision, good for making detailed parts.
Works well for high-volume production with consistent quality.
Can use a wide range of materials for added strength.
Disadvantages:
Higher initial cost for molds.
Not ideal for hollow items.
More expensive for small production runs.
Choosing the Right Molding Technique for Your Project
Factors to Consider When Deciding Between Blow Molding and Injection Molding
When deciding between blow molding and injection molding, think about the type of product, design complexity, production volume, materials, and budget. Blow molding is better for hollow, lightweight products, while injection molding is ideal for solid, detailed parts. The cost of the mold, materials, and how many items you need are important factors in making the choice.
Which Molding Type is Best for Specific Types of Projects and Industries
Blow molding is used in industries that need lightweight, hollow products, like packaging, automotive, and consumer goods. Products like plastic bottles, fuel tanks, and containers are made using blow molding. Injection molding is used in industries that need solid, precise parts, like automotive, medical, and electronics. Products like plastic housings, toys, and medical devices are best made with injection molding due to the need for detail and strength.
Conclusion
In summary, blow molding and injection molding are two different methods, each with their own benefits and best uses. Blow molding is great for making lightweight, hollow products like bottles and containers. Injection molding is better for creating solid, detailed parts like car parts and medical devices. When choosing between these methods, it’s important to think about product design, materials, production volume, and budget.
Contact Unionfab for Expert Guidance
Need help deciding the best molding process for your project? At Unionfab, our experienced team is ready to assist you. Whether you're looking to produce lightweight, hollow products or solid, intricate components, we have the expertise to guide you to the perfect solution.
Contact us today to get started!
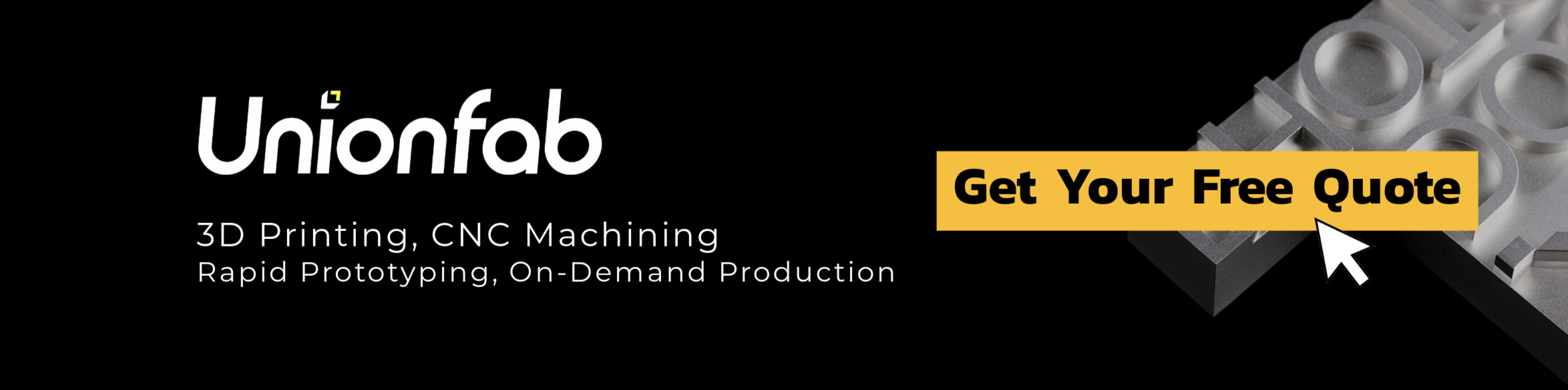