3D Printed Gears: A Complete Guide [+Free Gear Generators]
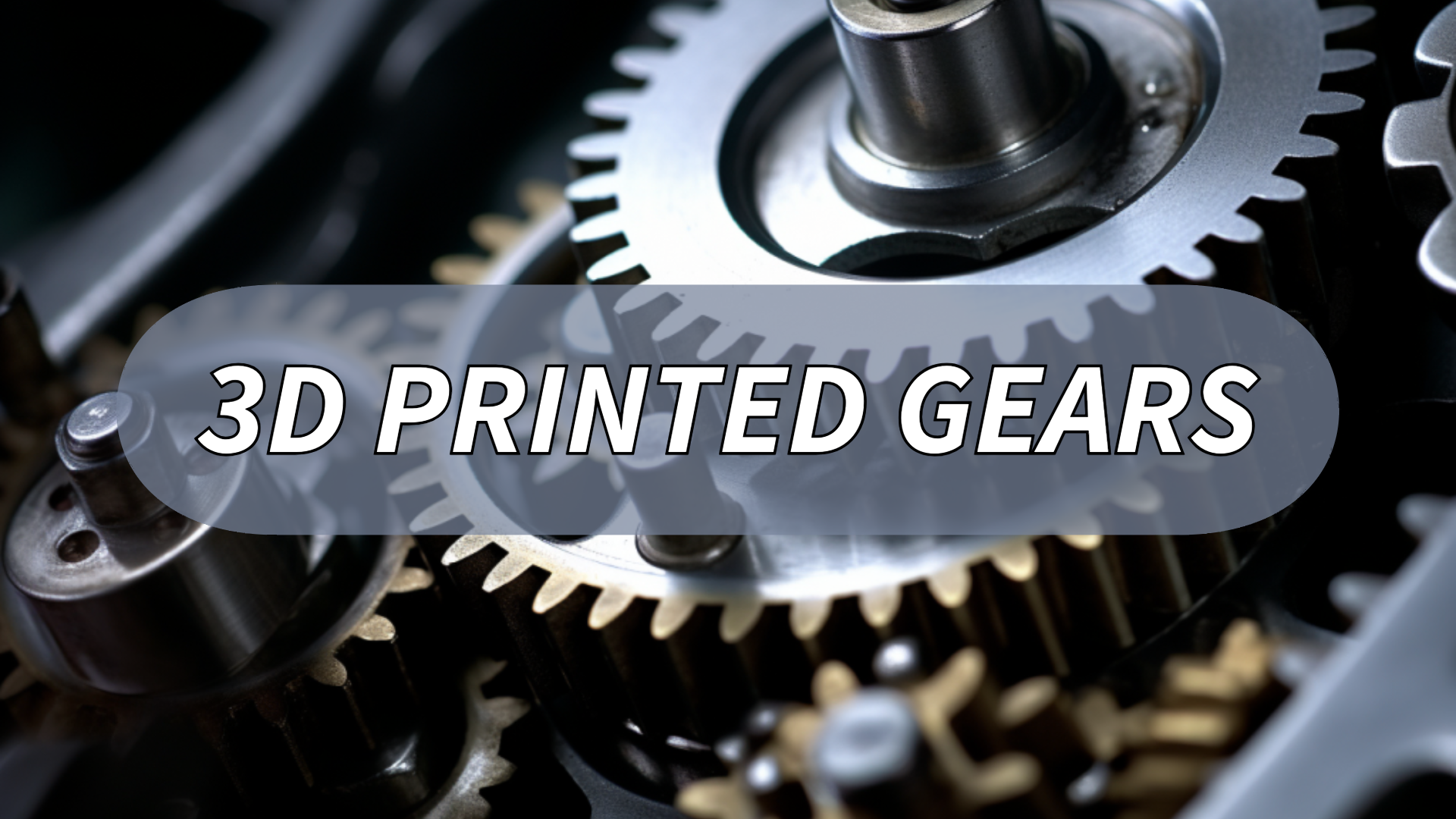
Get your gear models with free gear generators and 3d print them to gear up your machines.
Introduction
Gears are crucial for efficient movement and power transfer in machines. While traditional methods like machining and casting are time-consuming, 3D printing allows for the creation of custom, precise gears quickly and cost-effectively.
In this guide, we’ll explore 3D printed gears—covering their definition, advantages, design considerations, materials, and production processes. Whether you’re a DIY enthusiast, engineer, or manufacturer, you'll learn how 3D printing can transform gear design and production.
What Are Gears?
Definition
A gear is a mechanical component with teeth that interlock with another gear to transfer rotational motion and torque. Gears are used to change the direction, speed, and force in mechanical systems, making them essential in devices ranging from clocks to cars.
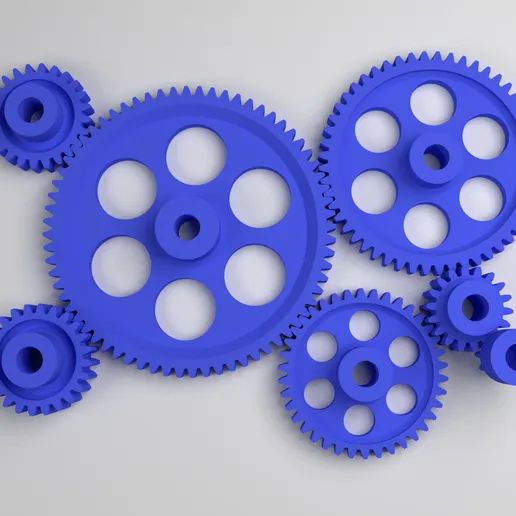
Types of Gears and Their Uses
Gears come in various shapes, sizes, and configurations, each suited to specific tasks. Below are the most common types:
Gear Type | Characteristics | Application |
---|---|---|
Spur Gears | - Simple, straight teeth | - Conveyor belts |
Helical Gears | - Angled teeth for smoother meshing | - Automotive transmissions |
Bevel Gears | - Straight or spiral teeth (spiral provides smoother operation) | - Power tools |
Worm Gears | - Worm (screw) meshing with a gear (wheel) | - Elevators |
Hypoid Gears | - Similar to bevel gears but with non-intersecting axes | - Automotive differentials |
Internal Gears | - Teeth on the inside of a cylindrical surface meshing with an external gear | - Planetary gear systems |
Get to know more types of gear, you can refer to the article: Types of Gears: Understanding Gear Types
Advantages of 3D Printing in Gear Production
1. Precision in Complex Gear Geometries
Custom tooth profiles: 3D printing enables the creation of unique, complex gear teeth that are difficult to achieve with traditional methods.
Integrated features: Gears can include internal structures such as lubrication channels or cooling fins, which improve functionality and performance. ⠀
2. Rapid Prototyping and Design Iteration
Fast prototyping: New gear designs can be printed and tested in just hours or days, speeding up the development cycle.
Cost-effective iteration: Multiple design versions can be tested at a low cost, enabling continuous improvement for custom or low-volume gears. ⠀
3. Tailored Material Properties for Gears
Specialized materials: 3D printing supports high-performance materials like nylon, carbon fiber composites, and even metals, which can be chosen based on the specific demands of the gear.
Functionally graded materials: Different materials can be combined in a single gear, optimizing strength, durability, and weight where needed. ⠀
4. Reducing Gear Manufacturing Complexity
No tooling costs: Unlike traditional methods, 3D printing eliminates the need for expensive molds or specialized tooling, making it ideal for low-volume or custom gears.
One-step manufacturing: The entire gear can be printed in one process, reducing the time and cost involved in multiple stages of traditional gear production. ⠀
5. Lightweight and Optimized Gear Design
Topology optimization: 3D printing allows for the use of algorithms to reduce weight while maintaining gear strength, making them ideal for applications where weight is critical.
Conformal designs: Gears can be designed to fit precisely within specific assemblies, optimizing space and ensuring a better fit compared to traditional manufacturing methods. ⠀
6. On-Demand Production and Supply Chain Flexibility
Localized production: Gears can be produced on-site or in local facilities, reducing lead times and the need for large inventories or long supply chains.
On-site customization: 3D printing allows for quick customization of gears for unique applications, reducing the need for outsourcing or additional manufacturing steps.
Design Considerations for 3D Printing Gears
Tips for Better 3D Gear Designs
1. Gear Shape, Tooth Design, and Load Distribution
Optimize Tooth Size:
For small gears, use larger teeth to avoid weak or incomplete parts.
Avoid making teeth too fine (e.g., smaller than 0.4mm for a 0.4mm nozzle).
Increase the number of teeth in contact to better spread the load and reduce wear.
Chamfer and Fillet Edges:
Chamfer tooth edges to reduce stress and improve durability.
Fillets at the tooth root prevent cracks under pressure. ⠀
2. Material Choice and Printing Settings
Choose the Right Material:
Use strong materials like nylon or carbon fiber-reinforced nylon for high-wear applications.
Avoid PLA for gears under heavy stress. Use ABS or PETG instead.
Adjust Printing Settings:
Print gears with teeth flat on the bed for better strength.
Use smaller layer heights (0.1mm or less) for better detail.
Add support for steep overhangs to ensure accuracy.
Account for Shrinkage:
Materials like ABS shrink while printing, so slight tolerances can be added to compensate for this. ⠀
3. Tolerance, Fit, and Assembly
Leave Space Between Gears:
Add 0.2-0.5mm clearance between meshing gears to prevent them from getting stuck.
Make axle holes a bit bigger (around +0.1mm) to ensure they fit well after printing.
Use Inserts for Strength:
For gears under heavy load, consider using metal inserts to reinforce weak points. ⠀
4. Multi-Gear System Compatibility and Testing
Keep Tooth Pitch Consistent:
Make sure all gears in your system have the same tooth pitch to mesh smoothly.
Use simulation software to check how gears fit together before printing.
Test the Design:
Print test gears to check fit and performance before finalizing the design.
Free Gear Generators
If you find designing gears from scratch too complicated, we've gathered some free gear generators that can help you out.
Gear Generator | Export Filetype |
---|---|
STL and DXF | |
DXF | |
DXF and SVG | |
STL and DXF | |
DXF, SVG and CSV |
No filetypes you need? Download the model from the websites above and convert it using cloud convert.
If you do not own a 3d printer but long for 3d-printing your gear model, why not choosing a 3d printing service provider like Unionfab? We are China’s largest 3d printing manufacturer, specializing in rapid prototyping and on-demand production. Work with Unionfab, Gear Your Machines Up!
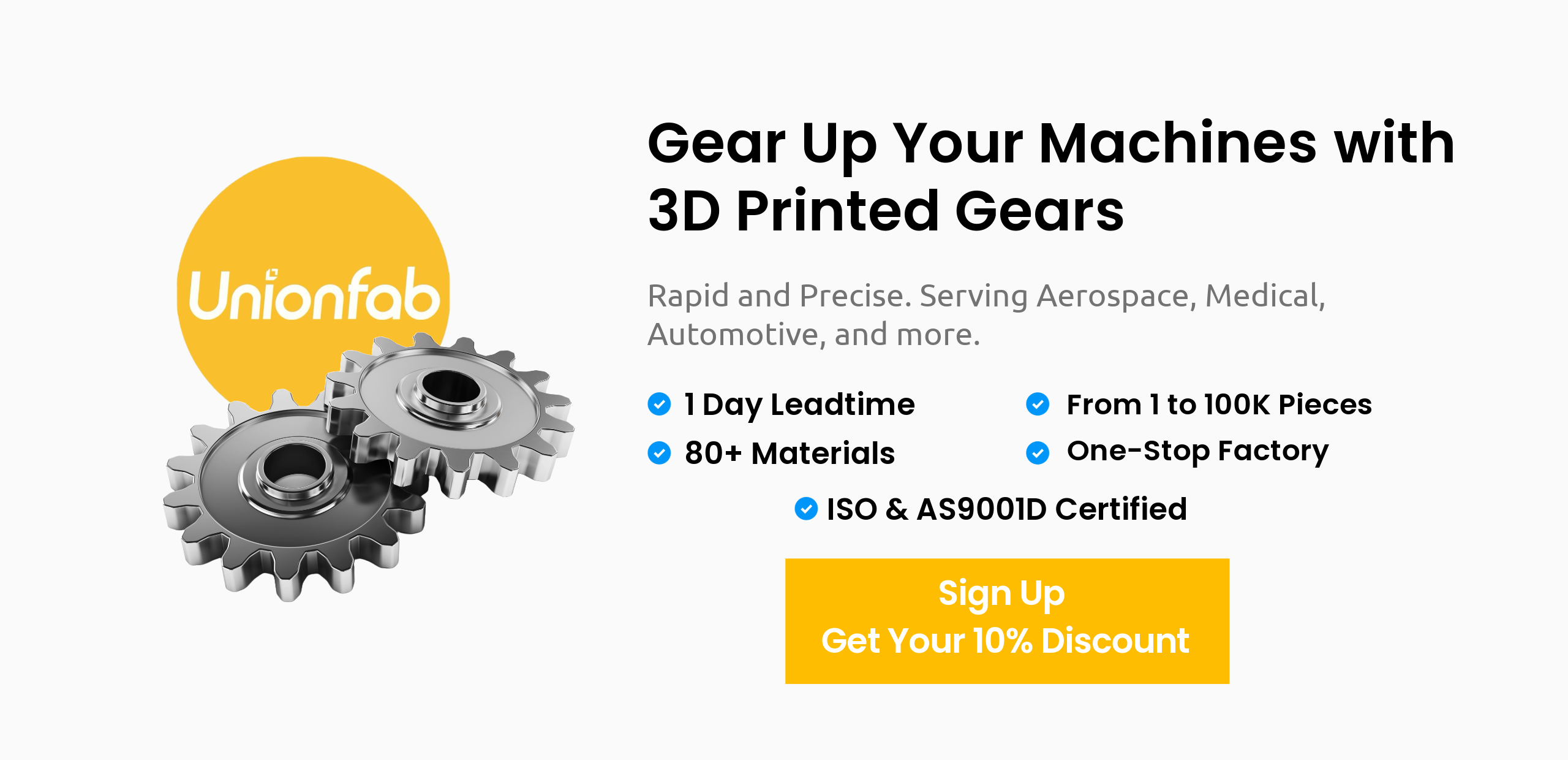
Best Filament for Gear 3D Printing
Here's a comparison of the most commonly used materials for 3D printing gears based on strength, wear resistance, ease of printing, and cost:
Material | Strength | Wear Resistance | Ease of Printing | Cost |
---|---|---|---|---|
PLA | ⭐⭐ Not ideal for high-load gears. | ⭐ Degrades quickly under friction. | ⭐⭐⭐⭐⭐ Very easy to print, ideal for prototyping. | $: Very affordable |
ABS | ⭐⭐⭐ Suitable for medium-load applications. | ⭐⭐⭐ Performs okay in non-heavy-duty uses. | ⭐⭐⭐ Needs a heated bed and careful setup. | $$: Affordable but slightly higher than PLA |
PETG | ⭐⭐⭐ Good for most general uses. | ⭐⭐⭐⭐ Better wear resistance than PLA and ABS. | ⭐⭐⭐⭐⭐ Easy to print, minimal warping. | $$: Slightly higher than ABS, but still budget-friendly |
Nylon | ⭐⭐⭐⭐⭐ Excellent for high-load, durable gears. | ⭐⭐⭐⭐⭐ Very good for high-stress, high-wear applications. | ⭐⭐⭐ Needs drying before printing due to moisture. | $$$: More expensive, but ideal for heavy-duty applications. |
Carbon Fiber Reinforced Nylon | ⭐⭐⭐⭐⭐ Stronger than standard nylon. | ⭐⭐⭐⭐⭐ Ideal for heavy-duty, high-wear use. | ⭐⭐⭐ Requires a hardened nozzle due to abrasiveness. | $$$$: Expensive due to carbon fiber content. |
TPU | ⭐⭐⭐ Flexible, not ideal for heavy-duty. | ⭐⭐⭐⭐⭐ Great in shock-absorbing applications. | ⭐⭐⭐⭐ Easy to print but requires slower speeds. | $$$$: More expensive due to flexibility and specialized use. |
PEEK | ⭐⭐⭐⭐⭐⭐⭐ One of the strongest materials available. | ⭐⭐⭐⭐⭐⭐⭐ Perfect for aerospace and extreme conditions. | ⭐⭐ Requires high-temp printer and expertise. | $$$$$$$: One of the most expensive 3D printing materials. |
Metal-Infused Filaments (e.g., Copper, Stainless Steel) | ⭐⭐⭐⭐⭐ Strong due to metal content. | ⭐⭐⭐⭐ Durable, but not as high as full metal gears. | ⭐⭐⭐ Requires special care due to abrasiveness. | $$$$: Expensive due to metal content. |
Key Takeaways:
Strength: For high-load gears, Nylon, Carbon Fiber Reinforced Nylon, Metals and PEEK stand out.
Wear Resistance: Nylon and Carbon Fiber Reinforced Nylon lead the way, with PEEK close behind.
Ease of Printing: PLA and PETG are the easiest materials to print with, while PEEK and Carbon Fiber Reinforced Nylon require special equipment and care.
Cost: PLA is the most budget-friendly, while PEEK and Carbon Fiber Reinforced Nylon are the most expensive due to their superior properties.
Best Material for Specific Needs:
For Prototyping: PLA is great due to its low cost and ease of use.
For General Use and Medium Loads: PETG and ABS are solid, cost-effective options.
For Heavy-Duty or High-Wear Gears: Nylon and Carbon Fiber Reinforced Nylon are the top choices.
For Extreme Conditions (e.g., aerospace, automotive): PEEK and Metal-Infused Filaments are ideal.
If you'd like a clearer, more visual comparison of these materials, check out the video below.
Tips for 3D Printing Gears
When 3D printing gears, there are several key factors to consider in order to achieve high-quality, durable parts. Here are some essential tips to help you get the best results from your 3D-printed gears:
1. Ensure Proper Gear Alignment
Tip: Align the gear’s axis and teeth orientation correctly when setting up your print.
Why: Incorrect alignment can lead to weak points, improper tooth meshing, or even gear failure when in use. Make sure the gear's teeth are printed in a way that ensures optimal strength and performance. ⠀
2. Use Higher Infill Densities for Stronger Gears
Tip: Increase the infill percentage to enhance gear strength.
Why: For gears that will bear heavy loads or high friction, a higher infill density (around 60%–100%) will provide additional strength. This is especially important for materials like PLA or ABS, which tend to be brittle at lower infill densities. ⠀
3. Opt for Fine Layer Resolution for Precision
Tip: Use a higher layer resolution (e.g., 0.1–0.2 mm) for better precision on small gears.
Why: Fine layers reduce the roughness of the gear teeth, leading to smoother meshing and less wear. This is particularly important for high-precision gears that need to mesh with other parts seamlessly. ⠀
4. Choose the Right Print Orientation
Tip: Position your gear horizontally (flat) to ensure better strength and surface quality.
Why: Printing gears vertically can lead to weak points along the layer lines. Horizontal orientation provides better bonding between layers, resulting in a stronger, more durable part. ⠀
5. Test Gear Fitment Before Full Production
Tip: Print a small-scale test gear first to check tooth fit and alignment.
Why: Testing with a smaller prototype allows you to check if the gear meshes correctly and rotates smoothly. It also gives you a chance to make adjustments to the design or print settings before committing to a full-size print. ⠀
6. Minimize Overhangs with Proper Support
Tip: Use adequate support structures for gears with complex features.
Why: Overhangs can lead to poor quality in the printed teeth. Support structures ensure that the gear prints correctly, especially for gears with intricate tooth designs or angled components. ⠀
7. Control Temperature Settings
Tip: Set the correct printing temperature based on the material you're using.
Why: Each material has an ideal printing temperature, which influences the bonding of the layers. Too high or too low a temperature can cause warping or poor adhesion between layers. For instance, PLA prints best at around 190°C, while Nylon requires a higher temperature of around 250°C. ⠀
By following these tips, you'll be able to optimize your 3D printing process for gears, ensuring that they are strong, durable, and functional for your specific applications.
Common Issues and Solutions in 3D Printing Gears
During the 3D printing of gears, several common issues can arise that may affect the quality and functionality of the printed parts. Below are the most frequent problems along with potential solutions:
1. Warping or Deformation of Gears
Cause: During 3D printing, rapid cooling, especially at the bottom layers, can cause warping or deformation. Larger gears with thicker bottoms are more prone to this.
Solution:
Use a heated bed to ensure uniform temperature distribution during printing.
Choose the right print speed and temperature to avoid fast cooling.
Use a brim or support structures to stabilize the gears and reduce warping.
2. Rough Gear Surface
Cause: Poor layer adhesion or insufficient printer precision can lead to rough surfaces.
Solution:
Adjust printer resolution (e.g., increase XY axis precision) for finer surface reproduction.
Use proper print settings (such as reducing layer height) to achieve a smoother surface.
Clean the print bed before starting to ensure good adhesion.
3. Poor Gear Mesh (Misalignment)
Cause: Gear teeth may not match properly or the gap between them may be too large, leading to poor meshing.
Solution:
Ensure accurate design of the gear teeth and tooth pitch, possibly using a gear generator tool for precision.
Test the gear mesh to ensure smooth engagement.
Adjust the gap between the gears to ensure proper meshing.
4. Cracks or Breakage in Gear Teeth
Cause: Inadequate material selection or rapid cooling during printing can weaken the teeth, making them prone to cracks or breakage.
Solution:
Use stronger materials such as Nylon or carbon fiber-reinforced materials instead of weaker ones like PLA.
Reduce print speed and increase temperature for better layer adhesion.
Consider using a higher infill density (e.g., 50%-100%) to increase overall strength.
5. Material Adhesion Issues
Cause: The bottom of the gear may not stick well to the print bed, causing it to shift or become misaligned during printing.
Solution:
Apply a dedicated adhesive or coating to the print bed, such as blue painter's tape or glue.
Adjust the bed temperature to improve adhesion during the printing process.
Use heated bed functionality to prevent material warping as it cools.
6. Excessive Wear or Gear Failure
Cause: 3D printed materials may not be durable enough, or poor design could lead to gears wearing out quickly.
Solution:
Use durable, wear-resistant materials like Nylon or carbon fiber-reinforced Nylon for heavy-duty applications.
Optimize the gear design to increase the contact area of the teeth, reducing localized wear.
Regularly check and replace worn-out gears to prevent failure.
Conclusion
3D printing has transformed gear manufacturing by offering unmatched customization, speed, and precision. With a wide range of materials and design flexibility, it's easier than ever to create high-quality, functional gears that meet specific needs.
Embrace the future of gear production with 3D printing to optimize performance and reduce costs in your mechanical systems.
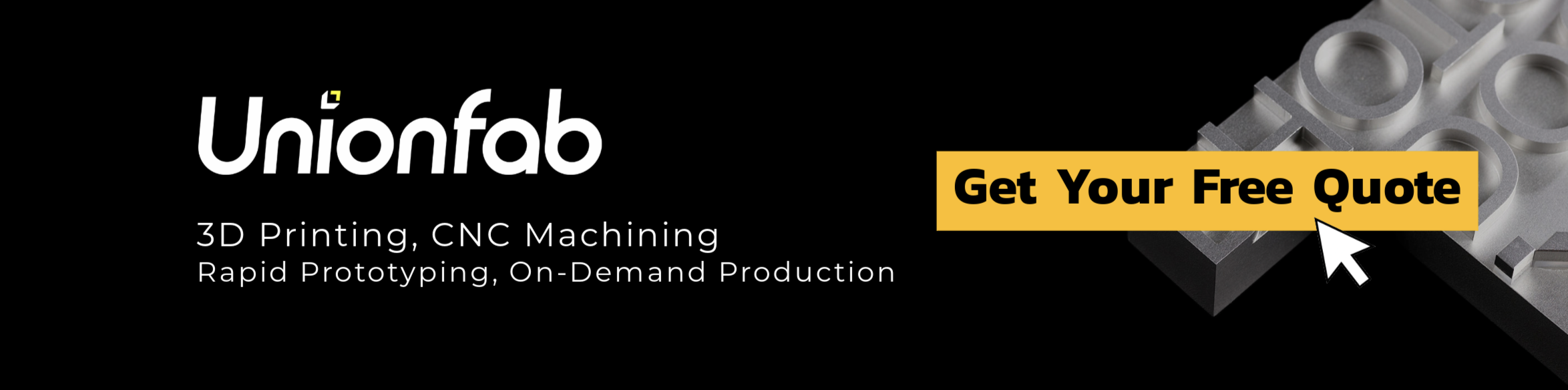