Top Casting Defects and How to Avoid Them
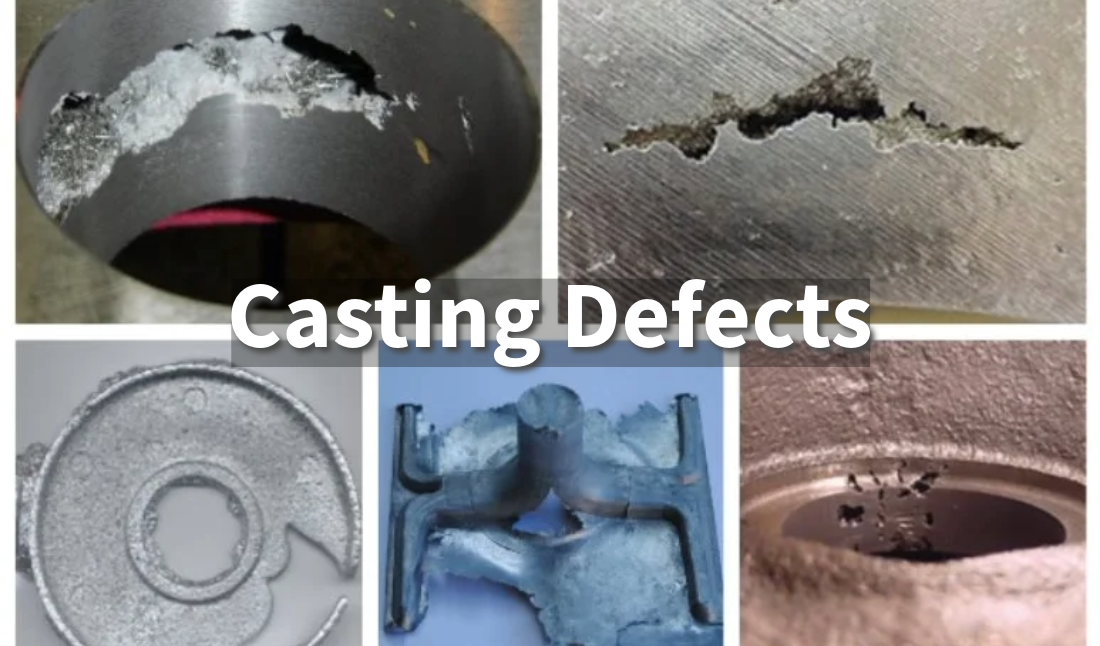
Learn about the common problems that can happen in metal casting, what causes them, and how to prevent them to make sure your metal products are high quality.
Introduction
Casting defects are problems that happen during the casting process. These defects can affect the quality, strength, and cost of the finished product. Understanding and preventing these defects is important to make sure the parts work well and meet quality standards.
What Are Casting Defects?
Casting defects are imperfections that occur during the casting process, potentially affecting the appearance, strength, or functionality of the final product. While some defects are purely cosmetic, others can compromise the safety and reliability of the part, making early detection and prevention essential.
Uncontrolled defects lead to higher costs, waste, and customer dissatisfaction due to reduced product performance and lifespan. By minimizing defects, manufacturers can enhance quality, improve efficiency, and deliver durable, reliable products while reducing production costs.
Overview of Metal Casting Defects
What Is Metal Casting?
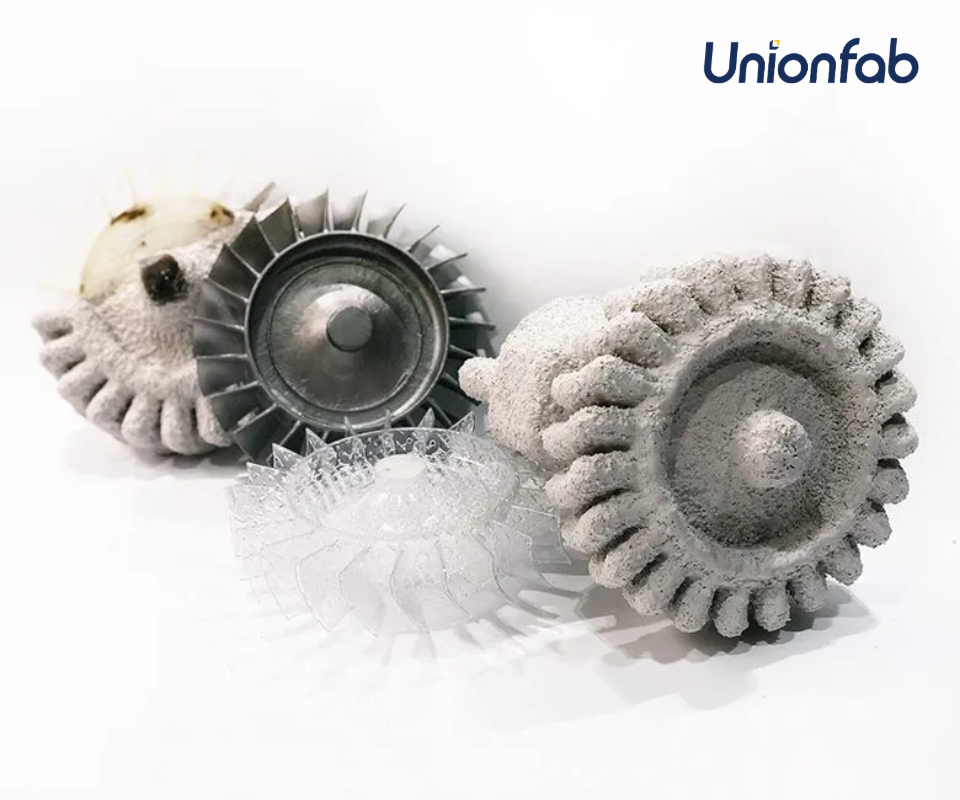
Source: Unionfab
Metal casting is a process where molten metal is poured into a mold to create parts with a specific shape. Once the metal cools and hardens, it takes the form of the mold. This versatile method is commonly used to produce parts like engine components and tools, offering the ability to create complex designs at a lower cost. Metal casting is suitable for both small and large parts, making it essential across various industries.
Types of Defects by Cause
Casting defects can be grouped based on what causes them. Mold-related defects come from problems with the mold, while metal-related defects happen because of impurities in the metal. Process-related issues happen because of poor handling, incorrect temperatures, or improper pouring techniques.
Common Types of Defects in Metal Casting
Porosity
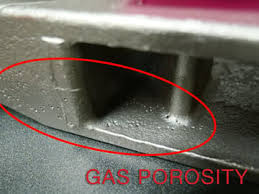
Source: eaglegroupmanufacturers.com
What It Is: Porosity means there are small holes or air pockets in the metal. These holes can make the metal weaker.
Causes: Porosity happens because of trapped gases, poor venting, or contamination. It can occur if the mold doesn't let gases escape properly.
How to Prevent It: To prevent porosity, make sure there is good venting, control the pouring speed, and remove gases from the molten metal. Keeping the mold and environment clean also helps.
Shrinkage
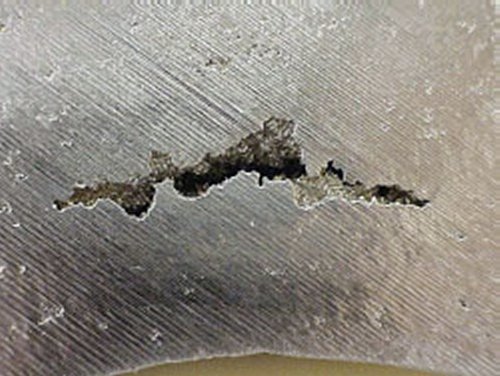
Source: steeldata.info
What It Is: Shrinkage occurs when the metal volume decreases as it cools, causing empty spaces inside the casting.
Where It Happens: Shrinkage often happens in thick areas or places that cool unevenly.
How to Prevent It: Use risers to feed extra molten metal, control the cooling rate, and add insulation to help cool the part evenly.
Cold Shuts
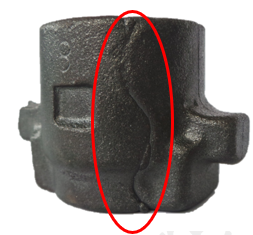
Source: castingsimulation.in
What It Is: Cold shuts happen when two streams of molten metal do not fuse properly, leaving a weak seam.
Causes: Cold shuts can be caused by pouring the metal too slowly or at too low a temperature.
How to Prevent It: Make sure the pouring temperature is high enough and that the mold design allows smooth metal flow. Preheating the mold and adjusting the gating system can also help.
Misruns
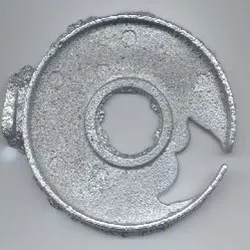
Source: cmtimports.com
What It Is: Misruns are incomplete castings where the metal didn't fill the mold completely.
Causes: Misruns can happen if the pouring temperature or speed is too low.
How to Prevent Them: Increase the pouring temperature, use a more fluid metal alloy, and preheat the mold to prevent the metal from cooling too quickly.
Inclusions
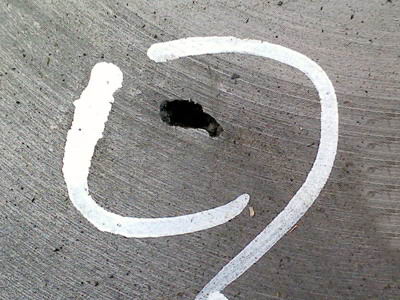
Source: iron-foundry.com
What It Is: Inclusions are impurities or particles trapped inside the casting.
Causes: Inclusions come from contamination or not filtering the metal properly.
How to Prevent Them: Clean the mold and metal, filter the molten metal, and avoid contamination during pouring.
Hot Tears
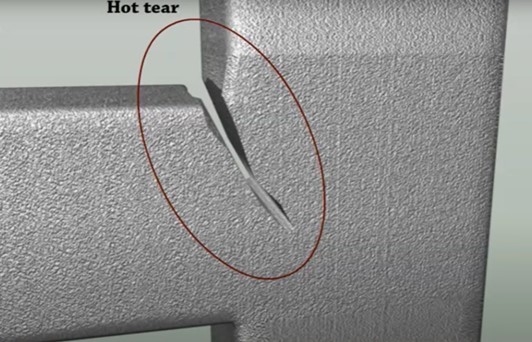
Source: .sunrise-metal.com
What It Is: Hot tears are cracks that form when the metal cools and can't shrink freely.
Causes: Uneven cooling creates stress, which causes the metal to crack.
How to Prevent Them: Use mold materials that allow for some flexibility, control the cooling rate, and design molds that cool evenly.
Identifying Casting Defects
Ways to Detect Defects
There are different ways to find casting defects, like visual inspection, X-ray inspection, ultrasonic testing, and dye penetrant testing.
Visual inspection can find surface defects, while X-ray and ultrasonic testing can find problems inside the part. Dye penetrant testing is useful for finding small cracks. By using these methods, manufacturers can find and fix defects before the product goes to the customer.
How to Improve Metal Casting Quality
Rigorous Quality Control Checks
Regularly inspect castings at every production stage to identify defects early.
Use non-destructive testing (NDT) methods like X-ray inspection, ultrasonic testing, or magnetic particle inspection to ensure defect-free components.
Optimal Casting Temperatures
Monitor and control the pouring and mold temperatures carefully to avoid issues like shrinkage, porosity, or cracking.
Use temperature sensors or thermal cameras for precise monitoring.
High-Quality Raw Materials
Source pure, defect-free alloys and ensure consistency in material composition.
Conduct metallurgical tests to avoid impurities or unwanted inclusions.
Optimize Mold Designs
Design molds that allow for proper filling, solidification, and cooling of the metal.
Include features like risers and vents to prevent common issues like air entrapment or incomplete fills.
Keep Equipment in Good Condition
Regularly maintain and calibrate tools, furnaces, and molding equipment to avoid malfunctions or inconsistencies.
Train and Upskill Workers
Provide regular training for workers on advanced casting techniques and safety protocols.
Encourage a culture of continuous learning to adapt to modern practices.
3D Printed Molds: Revolutionizing Mold Design
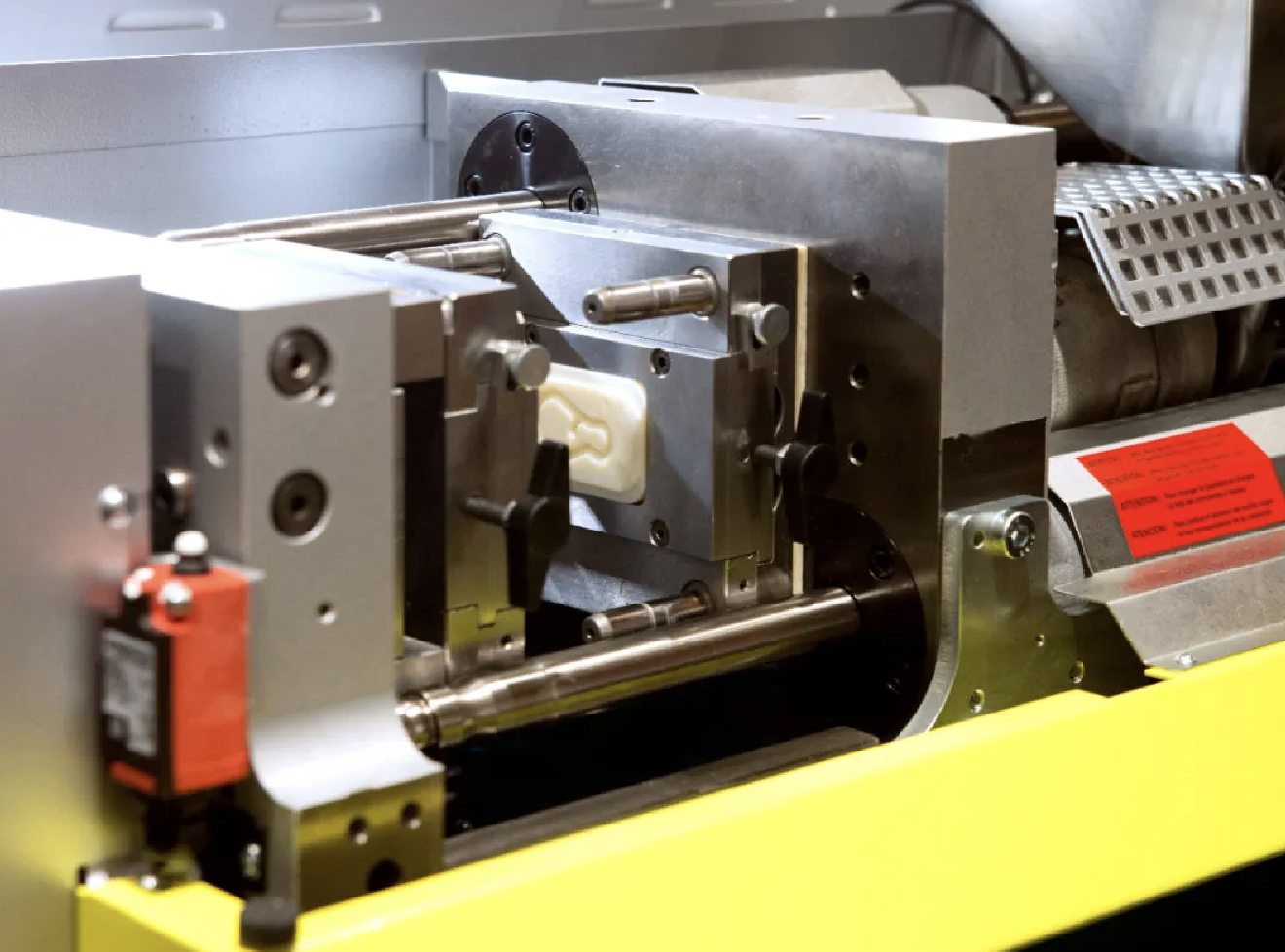
Source: Unionfab
3D printing, or additive manufacturing, is transforming how molds and patterns are designed and produced. See this article on 3D printed molds for more information.
Precision Geometries — Less Dimensional Errors
3D printing allows for the creation of intricate mold designs that are difficult or impossible to achieve with traditional methods. This precision helps ensure the mold shapes are exact, reducing the risk of dimensional errors in the final casting.
Conformal Cooling Channels — Prevents Warping
3D printing enables the integration of conformal cooling channels directly into the mold design. These channels follow the contours of the casting, ensuring more even cooling and minimizing thermal gradients that could lead to defects like warping, cracking, or shrinkage.
Faster Prototyping — Reduces Trial and Error
3D printed molds can be quickly produced and tested, allowing for rapid iteration of design changes. This speed helps identify potential issues early in the process, reducing trial-and-error costs and leading to more reliable castings.
Optimized Mold Venting — Avoids Gas Porosity
3D printing allows for highly accurate venting systems within the mold, ensuring gases escape during the pouring process. Proper venting reduces the risk of air pockets or gas porosity, resulting in cleaner, more reliable castings.
Conclusion
Casting defects can weaken parts, increase costs, and impact reliability. By understanding their causes and prevention, manufacturers can create safer, more durable products while reducing waste and keeping customers satisfied.
Get Expert Casting Solutions from Unionfab
At Unionfab, we go beyond 3D printing and CNC machining to deliver exceptional metal casting services. Using advanced techniques and materials, our team ensures reliable, cost-effective solutions tailored to your specific needs.
Contact us today for expert support and take your project to the next level with confidence and precision!
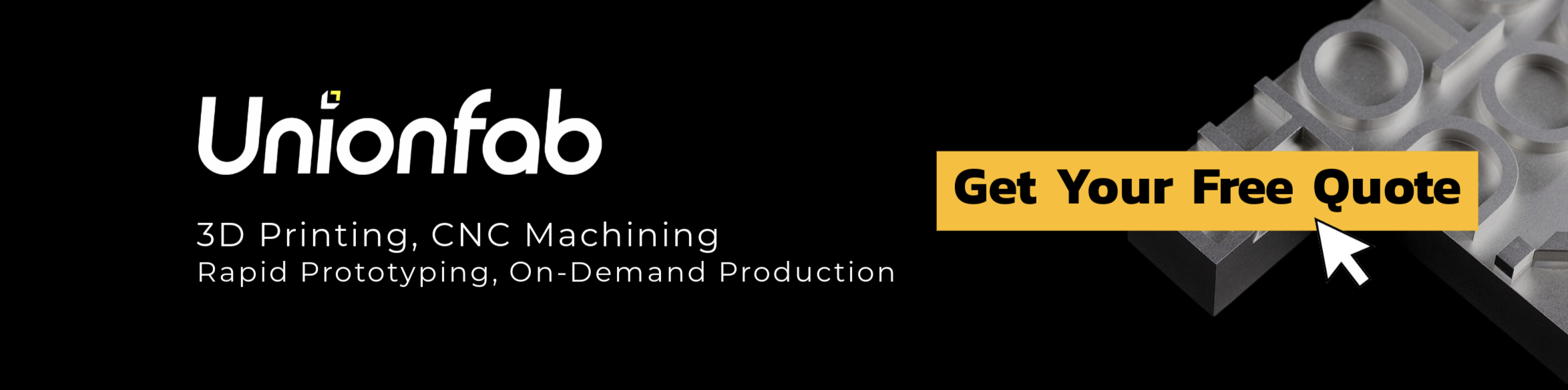