Types of Gears: Understanding Gear Types
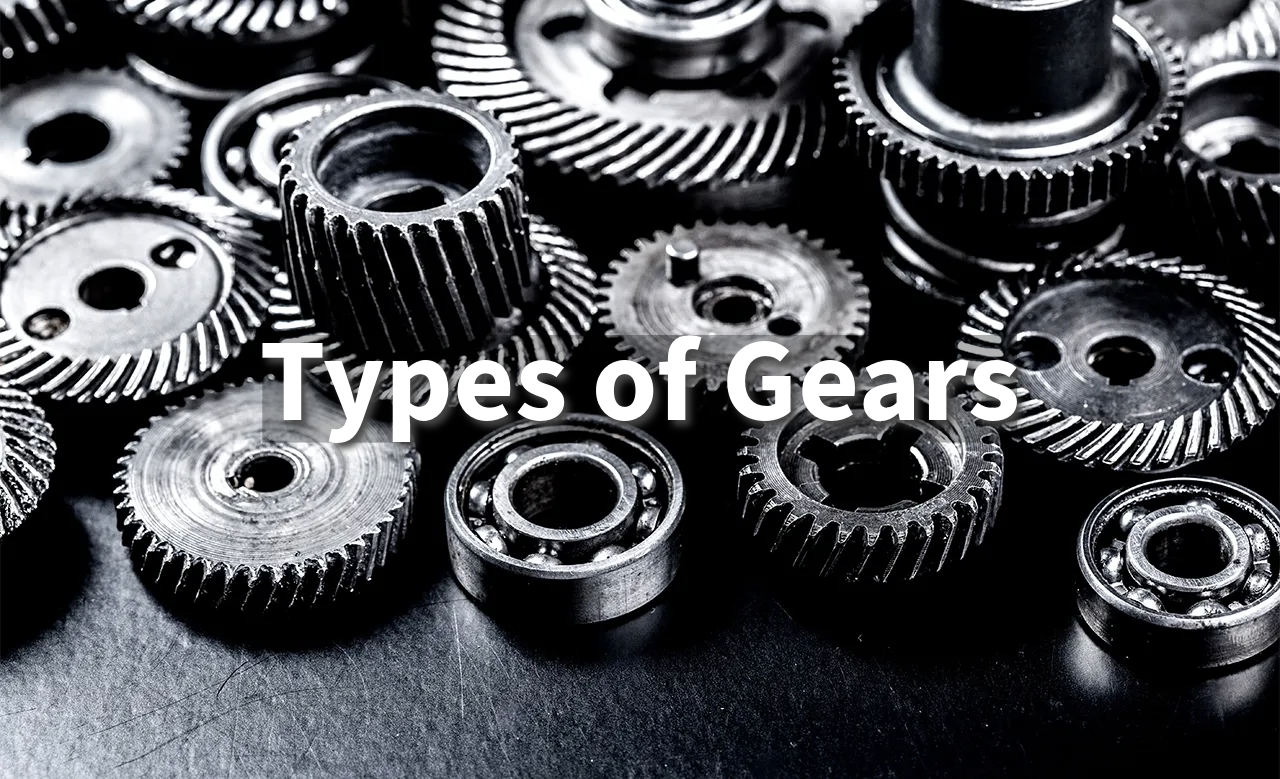
Learn about the different types of gears and their unique functions with this comprehensive guide.
Introduction
Gears come in many forms, each suited for specific uses. But which type is best for your project?
In our guide, we break down the characteristics of common gear types like spur, bevel, worm and more.
What Are Gears?
Gears are toothed wheels that mesh together to transfer rotational motion from one shaft to another. When one gear turns, its teeth engage with the teeth of the second gear, causing it to rotate as well.
Gears help control power by changing speed, torque (twisting force), or direction of motion, depending on their size and number of teeth. This makes them essential for ensuring smooth and synchronized movement in machines and mechanical systems, like engines and motors.
Types of Gears and Their Applications
1. Spur Gears
Spur gears are the simplest type of gears, featuring straight teeth mounted on parallel shafts. They are easy to manufacture, highly efficient, and well-suited for low-speed, high-torque applications.
Commonly used in gearboxes, conveyor systems, and simple mechanical devices, spur gears excel in environments where noise is not a concern.
2. Helical Gears
Helical gears have angled teeth that engage gradually, making them quieter than spur gears. This suits high speeds like automotive transmissions, where their efficiency improves fuel economy.Angled teeth absorb higher loads too due to more contact area.
3. Bevel Gears
Bevel gears are cut at an angle to transmit torque between non-parallel shafts. This direction change finds use in drills, machines and differentials, which employ bevel gears to redirect drive from the transmission to rear wheels. Varieties like spiral bevel gears operate even more smoothly.
4. Worm Gears
Worm gears offer large speed reductions within a small footprint as their worm tightly meshes with the worm gear. This compact design fits steering columns and conveyors well, though efficiency is lower than other gear types.
Reliable torque transmission suits applications with space constraints like elevators.
5. Rack and Pinion Gears
Rack and pinion gears convert rotation to linear motion - the pinion's teeth engage the rack's to enable straight line movement.
Their precise linear motion proves useful in vehicles' steering systems and CNC machines.
6. Planetary Gears
Planetary gears involve planet gears revolving around a central sun gear, housed in a ring gear, creating a compact, high-torque system. This arrangement suits precision requirements like automatic transmissions, aerospace equipment and robotics.
7. Hypoid Gears
Hypoid gears resemble spiral bevel gears but their shafts are offset rather than intersecting, providing smoother, quieter operation at higher torque than bevel gears alone. This characteristic makes hypoid gears well-suited to differentials in rear-wheel drive vehicles.
8. Herringbone Gears
Herringbone gears contain two opposing helical gears to cancel axial thrust for very smooth, low-vibration power transmission. Heavy machinery and high-load industrial equipment applications benefit from their durability.
9. Internal Gears
Internal gears have teeth cut into the inside of a cylinder or cone to mesh with planetary or spur gears rotating within. Planetary gearboxes, hydraulic motors and some vehicle components exploit their compact, efficient yet smooth-operating nature.
10. Spiral Gears
Spiral gears utilize curved teeth for bevel gears, engaging gradually to operate quietly at higher speeds. This feature suits automotive differentials where noise-free performance is important.
11. Face Gears
Face gears cut teeth into the face rather than edge to mesh with spur or bevel pinions, changing motion direction by 90°. Aircraft transmissions, helicopter rotors and other space-limited applications use them for specific angled drives.
12. Sprockets
Sprockets resemble gears but transmit rotation over distance by engaging a chain or track. Their toothed wheels efficiently convey power on long paths as used on bicycles, conveyor systems and factory machinery.
13. Miter Gears
Miter gears transmit motion between perpendicular shafts at a 1:1 ratio, simply changing the rotational direction. Conveyors, drills and machinery requiring 90° angle changes employ their efficient design.
14. Differential Gears
Differential gears allow drive shafts to spin at different speeds while transmitting torque, key to letting vehicle wheels rotate independently. They enable four-wheel drive vehicles to navigate uneven terrain.
15. Cycloidal Gears
Cycloidal gears utilize a cycloid tooth shape rather than involute for compact designs with smooth operation and high load capacity. Their precision movement proves advantages in robotics, machinery and small mechanisms like clocks.
16. Magnetic Gears
Magnetic gears transmit torque without physical contact using magnetic fields only. Their wear-free, efficient transmission at high speeds suits clean energy applications and anywhere low noise and minimal maintenance are important.
17. Zerol Bevel Gears
Zerol bevel gears have curved, untipped teeth that transmit torque smoothly between shafts without axial thrust, suiting applications requiring efficient yet quiet power transmission such as aircraft parts and vehicle differentials.
18. Hypocycloidal Gears
Hypocycloidal gears employ rolling contact for a smaller gear inside a larger one, providing very high torque and efficiency within a small footprint. Medical devices, precision gearboxes and robotics utilize their space-saving capability.
19. Epicyclic Gears
Epicyclic or planetary systems arrange planet gears to revolve around a central sun gear inside a ring, achieving compact transmission of high torque. Automatic transmissions, tools and wind turbines take advantage of their precision and forces.
20. Hirth Gears
Hirth gears mesh radially to achieve precise axial alignment and transfer high torque capacity, well-suited to aerospace components, precision saws and other demands of repeatable positioning.
Factors to Consider When Choosing a Gear Type
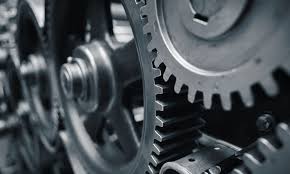
Source: ptggear.com
Here are some key factors to consider when selecting the appropriate gear type for an application:
Load capacity - The expected operating loads and torque requirements dictate if a gear can withstand mechanical stresses. High-torque applications require robust gear designs.
Speed requirements - The necessary input and output rotational speeds determine if speed-increasing or reducing gears are needed. Smaller diameters provide higher speed ratios.
Efficiency and noise levels - Gear design, teeth shape, and finish affect friction levels and noise. Helical and bevel gears tend to operate more quietly than spur gears.
Physical dimensions - Space constraints within a device may necessitate more compact gear types. Spur gears take up less space than helical or worm gears, for example.
Manufacturing feasibility - Some gear types require specialized machining and may not be suitable for low-volume production or prototyping. Cost and lead time also factor in.
Operating conditions - Environmental settings like temperature, vibration, and ingress protection influence suitable materials and seals.
Conclusion
Gears are parts that transfer motion and power between moving machine parts. They can change how fast or how strong the motion is, and which direction it moves.
By considering these details and comparing the pros and cons of each gear, you can find the best one. This makes sure the gears provide strong and long-lasting power transfer for what the machine needs to do.
Gear Production Made Easy with Unionfab
Let Unionfab be your one-stop-shop for rapid prototyping and manufacturing of all your gear parts. From iteration to fast shipping, we'll ensure your projects stay on the critical path.
Contact us today to discuss how we can assist with your 3D printed gearing needs.