Understanding Titanium Anodizing
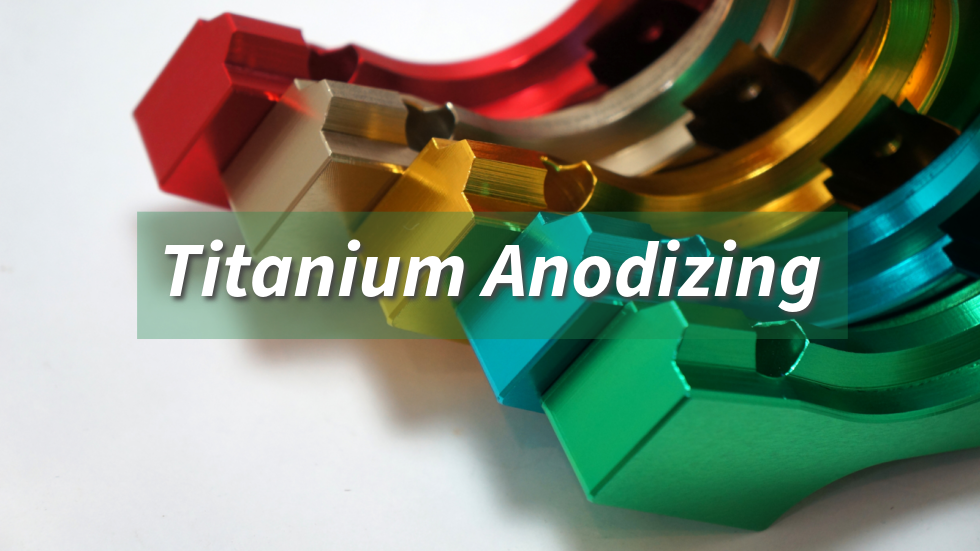
Explore titanium anodizing techniques, benefits, and a comprehensive color chart for anodizing.
Introduction
This guide will explain the main points of titanium anodizing, including its uses, types, benefits, limitations, and the materials required for the process.
By learning about titanium anodizing, you can make better choices to enhance the strength and appearance of your products.
What is Titanium Anodizing?
Titanium anodizing is an electrochemical process that changes the surface of titanium and its alloys.
In this process, titanium is placed in an electrolyte solution and connected to a power source. The electric current causes oxidation, creating a protective oxide layer on the surface.
This layer improves the material's resistance to wear and corrosion, and it can be colored by adjusting the voltage during anodizing.
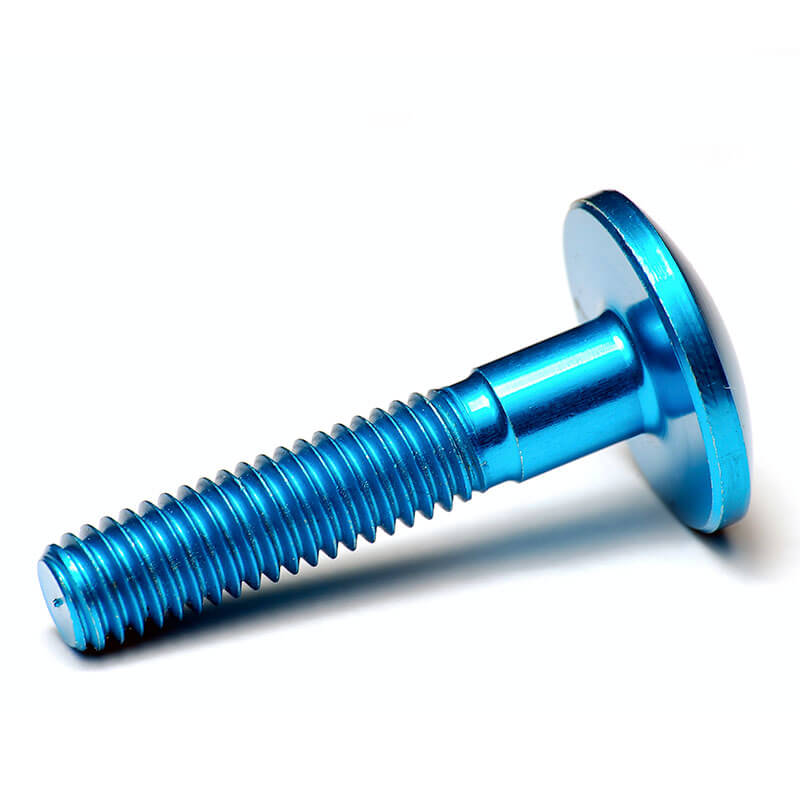
Source: titaniumfinishing.com
Applications of Titanium Anodizing
Titanium anodizing is used in various industries due to its unique properties. Key applications include:
Aerospace: Anodized titanium is used in aircraft components where lightweight and corrosion resistance are critical.
Medical Devices: Implants and surgical tools made from anodized titanium are popular due to their biocompatibility and durability.
Automotive: Anodized titanium parts are used in high-performance vehicles for both functional and aesthetic purposes.
Consumer Products: Items such as jewelry and watches benefit from anodizing, offering enhanced appearance and scratch resistance.
Types of Titanium Anodizing
There are generally types of titanium anodizing, which can include:
Type | Electrolyte | Thickness | Color Range | Applications |
---|---|---|---|---|
Type I | Chromic Acid | 0.1 to 2 microns | Usually dull gray | Aerospace, bonding with paints and coatings |
Type II | Sulfuric Acid | Up to 25 microns | Various | Aerospace, medical devices, consumer products |
Type III | Hard Anodizing (Sulfuric) | Up to 100 microns | Limited | Military, aerospace, heavy-duty industrial |
Type IV | Various | Similar to Type II | Wide array | Consumer goods, jewelry, decorative items |
Type I: Chromic Acid Anodizing
Type I anodizing uses a chromic acid solution. The titanium part is placed in the solution, and an electric current is applied, which creates a protective oxide layer on the surface.
Thickness: Typically creates a thin oxide layer (0.1 to 2 microns).
Color: Usually results in a dull gray finish, with limited color options.
Applications: Commonly used in aerospace due to its excellent corrosion resistance and good bonding with paints and coatings.
Type II: Sulfuric Acid Anodizing
Type II anodizing uses sulfuric acid as the electrolyte. This method is popular for anodizing titanium and involves applying an electric current to form an oxide layer.
Thickness: Produces a thicker oxide layer (up to 25 microns).
Color Range: Offers various colors based on the applied voltage, including blue, purple, and gold.
Applications: Frequently used in aerospace, medical devices, and consumer products, where both protection and aesthetics are important.
Type III: Hard Anodizing
Type III anodizing, or hard anodizing, uses higher voltages and specific sulfuric acid solutions to create a very thick and durable oxide layer.
Thickness: Results in a significantly thicker oxide layer (up to 100 microns).
Durability: Produces a tough surface that enhances wear and corrosion resistance.
Applications: Ideal for military, aerospace, and heavy-duty industrial applications, where extreme durability is essential.
Type IV: Color Anodizing
Type IV anodizing can use various electrolyte solutions, mainly sulfuric acid. This method focuses on achieving vibrant colors through careful control of the anodizing process.
Thickness: Generally produces a thinner oxide layer, similar to Type II.
Color Range: Offers a wide array of colors for custom finishes.
Applications: Often used in consumer goods, such as jewelry and decorative items, where aesthetic appeal is important along with functionality.
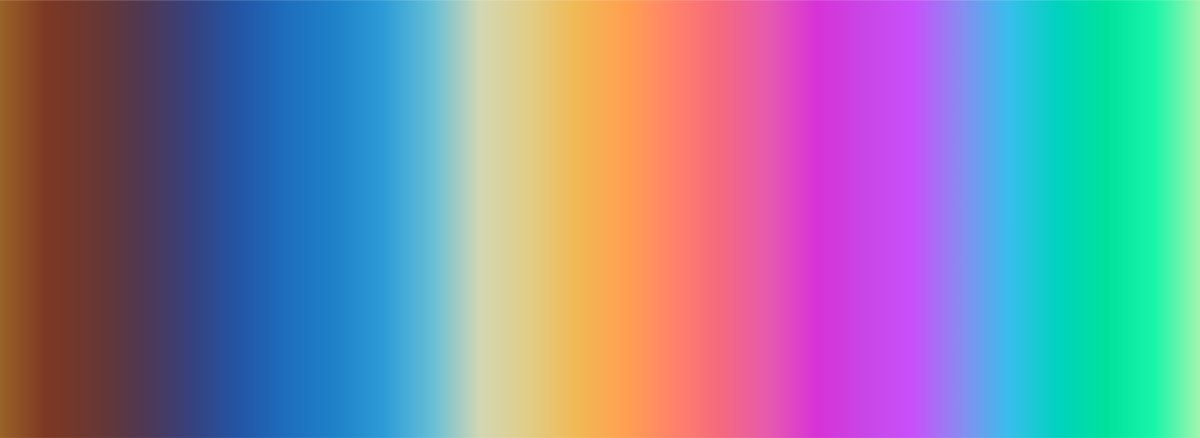
Source: wisconsinmetaltech.com
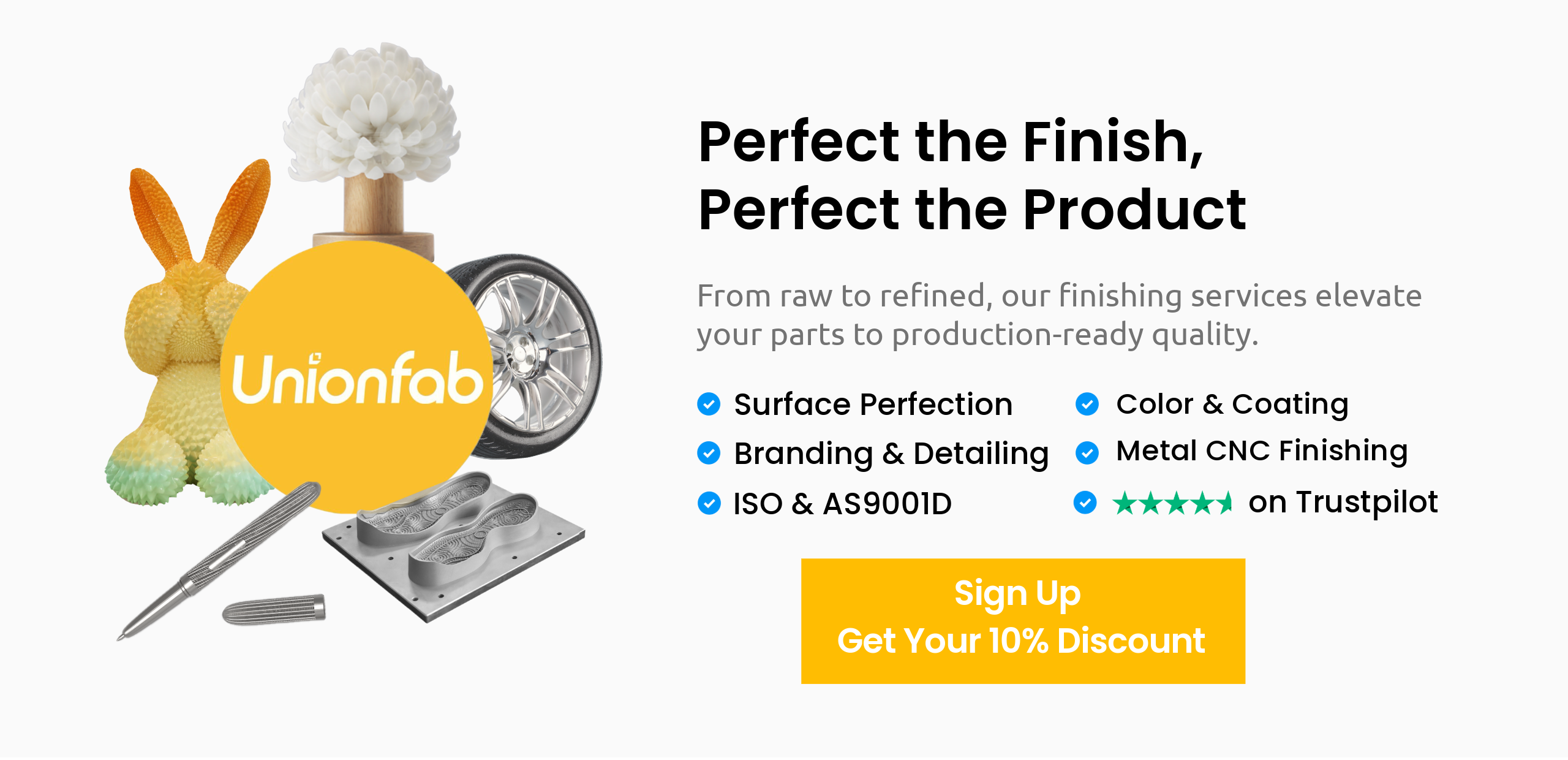
Titanium Anodizing Chart
Here's a simple titanium anodizing color chart, showing the typical colors produced through different anodizing voltages:
Voltage (V) | Color |
---|---|
10 V | Light Gold |
15 V | Blue |
20 V | Purple |
25 V | Bronze |
30 V | Dark Blue |
35 V | Light Green |
40 V | Yellow |
45 V | Pink |
50 V | Black |
Benefits of Titanium Anodizing
Titanium anodizing offers several advantages, including:
Enhanced Corrosion Resistance: The anodized layer protects titanium from environmental factors, extending its lifespan.
Improved Aesthetic Appeal: Available in various colors and finishes, anodized titanium can be visually striking.
Increased Durability: The anodized layer adds hardness, making titanium components more resilient to wear and tear.
Biocompatibility: Anodized titanium is safe for use in medical applications, reducing the risk of rejection in the body.
limitations of Titanium Anodizing
Despite its benefits, titanium anodizing has some limitations:
Cost: The anodizing process can be expensive due to the materials and equipment required.
Limited Thickness: The anodized layer has a maximum thickness, which may not be suitable for all applications.
Color Consistency: Achieving uniform color can be challenging, as variations in the anodizing process can lead to different shades.
Not Suitable for All Titanium Alloys: Some titanium alloys may not anodize well, limiting their use in certain applications.
How to Anodize Titanium?
The anodizing process involves several steps:
Surface Preparation: Clean the titanium surface to remove oils and contaminants.
Setup: Place the titanium in an electrolyte solution, typically sulfuric acid.
Connect Power Supply: Attach the titanium to the positive terminal (anode) and a cathode to the negative terminal.
Apply Voltage: Adjust the voltage to achieve the desired thickness and color of the oxide layer.
Rinse and Dry: After anodizing, rinse the titanium in distilled water and dry it thoroughly.
Seal the Anodized Layer: Optionally, seal the surface to improve durability.
Which Materials Are Needed to Anodize Titanium?
To anodize titanium, the following materials are typically required:
Titanium Workpiece: The item to be anodized.
Electrolyte Solution: Commonly, sulfuric acid or phosphoric acid is used.
Power Supply: A direct current (DC) power source to provide the necessary voltage.
Durometer: For measuring the hardness of the anodized layer.
Distilled Water: For rinsing after the anodizing process.
Safety Equipment: Gloves, goggles, and protective clothing to ensure safety during the process.
Conclusion
Titanium anodizing is a valuable process that enhances the properties of titanium, making it a versatile and desirable material for a wide range of applications.
By understanding the techniques, benefits, and limitations of anodizing, industries can make informed decisions when selecting materials and optimize the performance of their products.
High-Quality Titanium Anodizing Services
Looking to enhance your titanium parts with a durable, corrosion-resistant finish?
At Unionfab, we specialize in premium titanium anodizing services designed to meet your specific project needs. Our anodizing process not only improves appearance but also adds strength and longevity to your parts.
Contact us to learn how our titanium anodizing can elevate your project!
Ready to get started? Use our instant quoting system to customize your project. Select from various finishing options like anodizing, polishing, and more.
Learn how to quote your finishing here.
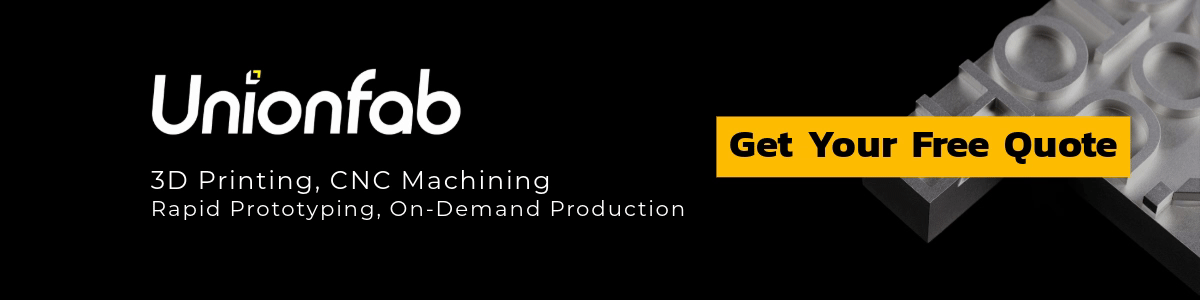
FAQs
What is the difference between anodized and un-anodized titanium?
Anodized titanium has a protective oxide layer that enhances corrosion resistance and allows for various color finishes, while unanodized titanium lacks this layer, making it more vulnerable to scratches and environmental damage.
Can titanium anodizing be done at home?
While it is possible to anodize titanium at home using a DIY setup, it requires specific equipment, safety precautions, and a good understanding of the process to achieve desired results safely and effectively.
How does anodizing affect the mechanical properties of titanium?
Anodizing can improve the wear resistance and surface hardness of titanium. Still, it may also affect certain mechanical properties, such as flexibility and toughness, depending on the thickness of the anodized layer.