Why Nylon 6/6 is Dominating Industries Worldwide?
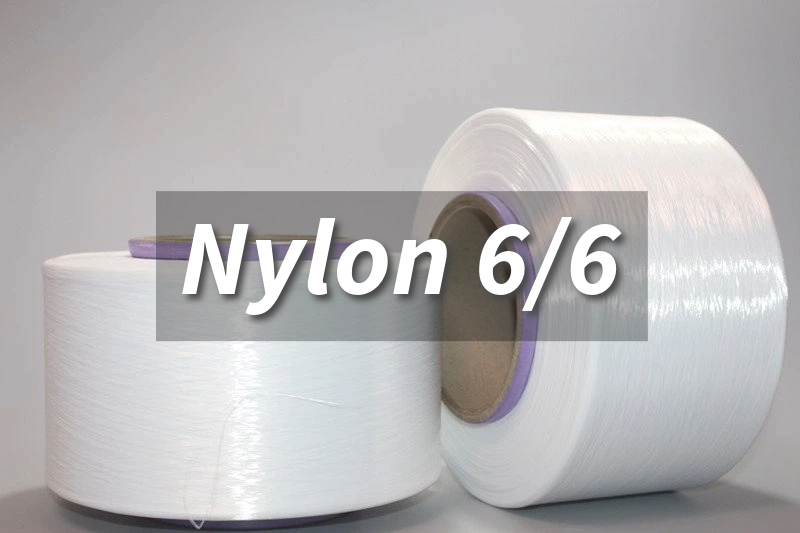
Nylon 6/6 is known for its strength, toughness, and chemical resistance. Learn about its properties, applications, and manufacturing processes.
Introduction
As one of the most widely used nylon polymers, Nylon 6/6 offers a unique blend of strength, durability, and resistance to chemical/heat. Its broad set of properties make it well-suited for numerous industrial and consumer applications.
This guide provides an overview of the versatile engineering plastic Nylon 6/6. You will learn about its key properties, common applications, and how it is manufactured.
What is Nylon 6/6?
Nylon 6/6 (also written nylon 6-6, nylon 66, nylon 6,6, or nylon 6:6), a type of polyamide, is a synthetic polymer known for its exceptional strength, durability, and resistance to abrasion. It is widely used in various applications, from automotive parts to textiles.
Made from two monomers—hexamethylenediamine and adipic acid—Nylon 6/6 features a high melting point and good chemical resistance, making it suitable for demanding environments.
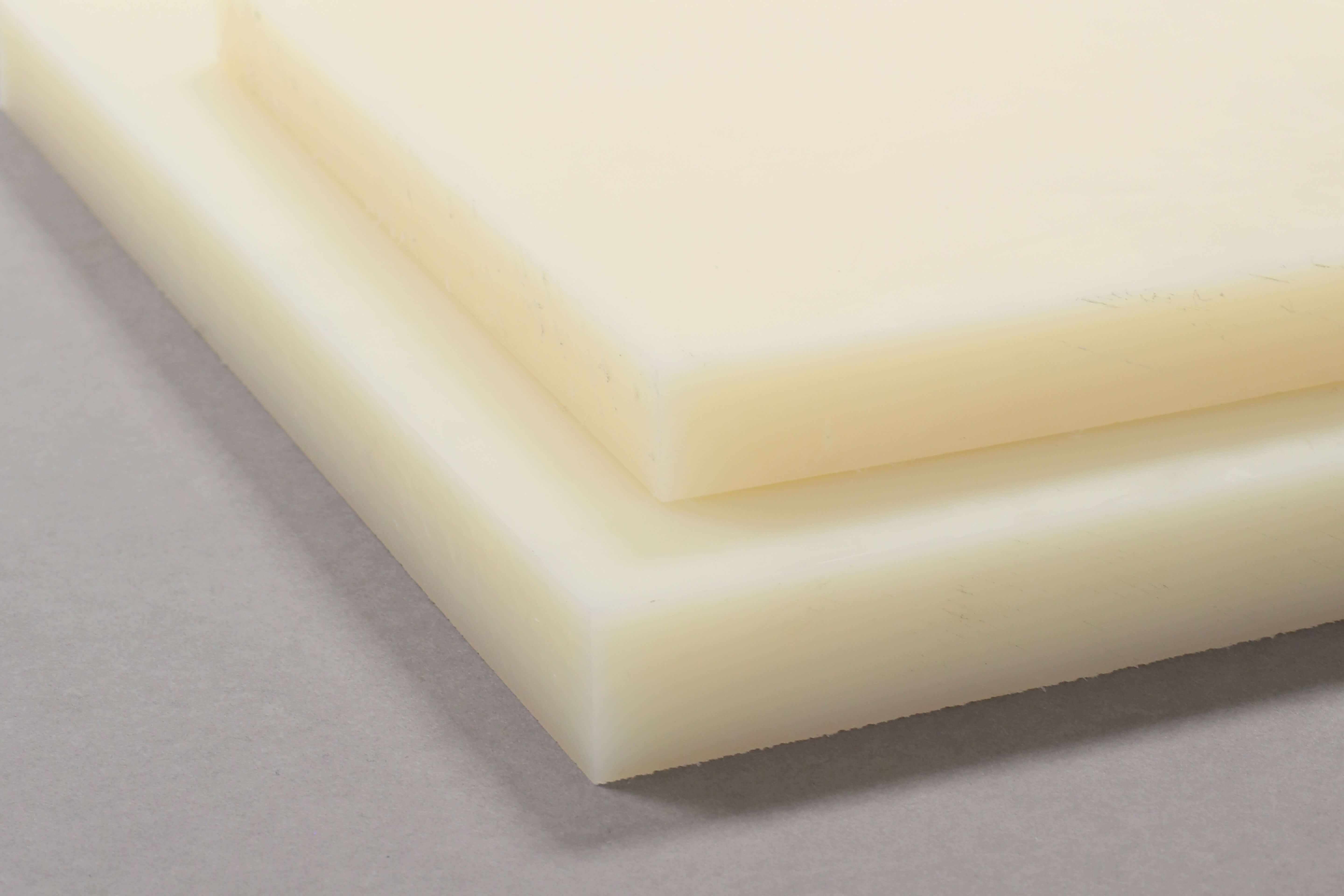
Source: aiplastics.com
Nylon 6 vs. Nylon 6/6
Nylon 6 and Nylon 6/6 are two of the most common types of nylon.
The table below highlights the key differences between Nylon 6 and Nylon 6/6:
Property | Nylon 6 | Nylon 6/6 |
---|---|---|
Chemical Structure | Single monomer | Two monomers |
Tensile Strength | Lower tensile strength | Higher tensile strength |
Elasticity | More elastic and flexible | More rigid and stiff |
Moisture Absorption | Higher moisture absorption | Lower moisture absorption |
Dimensional Stability | Less stable due to moisture absorption | More stable under varying humidity |
Melting Point | ~220°C (428°F) | ~260°C (500°F) |
Applications | Textiles, ropes, consumer goods | Automotive parts, electrical housings, mechanical components |
Properties of Nylon 6/6
Nylon 6/6 is known for its impressive physical and chemical properties, which contribute to its widespread use across various industries. Key properties include:
High Strength: Nylon 6/6 exhibits superior tensile strength, making it highly resistant to deformation and capable of withstanding heavy loads.
Durability: It is highly resistant to wear and abrasion, ensuring longevity even in demanding environments.
Heat Resistance: With a melting point of around 260°C, Nylon 6/6 can maintain its mechanical properties under elevated temperatures.
Chemical Resistance: This polymer is resistant to many chemicals, oils, and greases, making it suitable for use in harsh conditions.
Low Moisture Absorption: Compared to other nylon types, Nylon 6/6 has lower moisture absorption, which helps maintain its dimensional stability and mechanical properties in humid conditions.
Applications of Nylon 6/6
Nylon 6/6 is utilized in a wide range of applications due to its excellent properties. Common applications include:
Automotive Parts: Used for manufacturing components such as gears, bearings, and fuel lines due to its strength and heat resistance.
Electrical Components: Employed in electrical insulators and connectors because of its good dielectric properties.
Industrial Equipment: Used in conveyor belts, rollers, and machinery parts, benefiting from its durability and resistance to wear.
Consumer Goods: Found in items like sporting goods, luggage, and textiles, where strength and flexibility are essential.
Medical Devices: Used in certain medical applications, including surgical instruments and components, due to its sterility and chemical resistance.
Advantages and Disadvantages of Nylon 6/6
Nylon 6/6 offers several advantages that make it a preferred choice for many applications:
Exceptional Mechanical Properties: Its high tensile strength and toughness allow it to perform well in demanding situations.
Thermal Stability: The ability to withstand high temperatures without losing structural integrity is crucial for many industrial applications.
Chemical Resistance: It can resist a wide variety of chemicals, which is vital for applications in harsh environments.
Versatility: Its adaptability allows for use in numerous industries, from automotive to consumer products.
Despite its many benefits, Nylon 6/6 also has some disadvantages:
Higher Cost: It can be more expensive compared to other polymers, which may limit its use in budget-sensitive applications.
Limited UV Resistance: Prolonged exposure to UV light can degrade Nylon 6/6, making it less suitable for outdoor applications unless treated.
Hygroscopic Nature: Although it has lower moisture absorption than Nylon 6, it can still absorb moisture, potentially affecting its mechanical properties over time.
Manufacturing Processes of Nylon 6/6
Injection Molding
Injection molding is a widely used process for producing Nylon 6/6 parts with complex shapes and intricate details.
This process is highly efficient for mass production and can produce parts with high precision and consistency.
Process: It involves heating Nylon 6/6 resin to a molten state and injecting it into a mold cavity. Once the resin cools and solidifies, the part is ejected from the mold.
Extrusion
Extrusion is a continuous process used to produce Nylon 6/6 in various shapes, including sheets, filaments, and tubes.
It is a versatile process suitable for a wide range of applications, such as automotive parts, industrial components, and consumer goods.
Process: The resin is heated and forced through a die with the desired shape. The extruded material is then cooled and solidified.
Blow Molding
Blow molding is a process used to create hollow Nylon 6/6 parts, such as containers and bottles. It is an efficient process for producing large quantities of hollow parts with consistent quality.
Process: A parison, which is a preheated tube of Nylon 6/6, is placed into a mold cavity. Air is then blown into the parison, causing it to expand and conform to the shape of the mold. Once the part is cooled and solidified, it is removed from the mold.
CNC Machining
CNC machining is a subtractive manufacturing process that involves using computer-controlled machines to remove material from a block of Nylon 6/6 to create complex components. It is suitable for producing custom parts with high precision and tolerance requirements.
Process: Various machining operations, such as milling, turning, drilling, and cutting, can be performed to achieve the desired shape and features.
Comparison to Other Common Polymers
When comparing Nylon 6/6 to other common polymers, several key properties are considered. Below is a comparison with some widely used polymers:
Property | Nylon 6/6 | Polypropylene (PP) | Polyethylene (PE) | ||
---|---|---|---|---|---|
Tensile Strength | High | Moderate | Moderate | Moderate | High |
Heat Resistance | High (260°C) | Moderate (100-150°C) | Low (80-120°C) | Low (80-100°C) | High (120-130°C) |
Moisture Absorption | Low | Very Low | Very Low | Low | Low |
Chemical Resistance | High | Moderate | High | Moderate | Moderate |
Durability | Excellent | Good | Moderate | Good | Excellent |
Polypropylene
Offers lower tensile strength and heat resistance than Nylon 6/6, but has very low moisture absorption and is cost-effective for various applications, particularly in packaging and containers.
Polyethylene
Similar to polypropylene, it exhibits low moisture absorption and good chemical resistance but lacks the strength and heat resistance found in Nylon 6/6. It's widely used in bags, bottles, and other consumer products.
Acrylic
Provides good clarity and moderate strength but has lower heat resistance and durability compared to Nylon 6/6. It’s often used in applications requiring transparency, such as lenses and displays.
Polycarbonate
Known for its high impact resistance and clarity, polycarbonate has comparable heat resistance to Nylon 6/6. However, it is not as strong and durable, making it suitable for applications like eyewear and safety gear.
Conclusion
Nylon 6/6 is a versatile and durable polymer that excels in a variety of applications, thanks to its impressive mechanical properties and chemical resistance.
While it has some disadvantages, such as cost and UV sensitivity, its advantages often outweigh these drawbacks in critical applications.
Understanding its properties, applications, and manufacturing processes can help in selecting the right material for specific needs, making Nylon 6/6 a valuable option in engineering and manufacturing.
Discover Unionfab for Premium Nylon Solutions!
Our versatile, durable nylon materials excels in engineering applications, offering exceptional strength and chemical resistance.
Choose quality materials for your next project!