Low Alloy Steel: A Comprehensive Overview
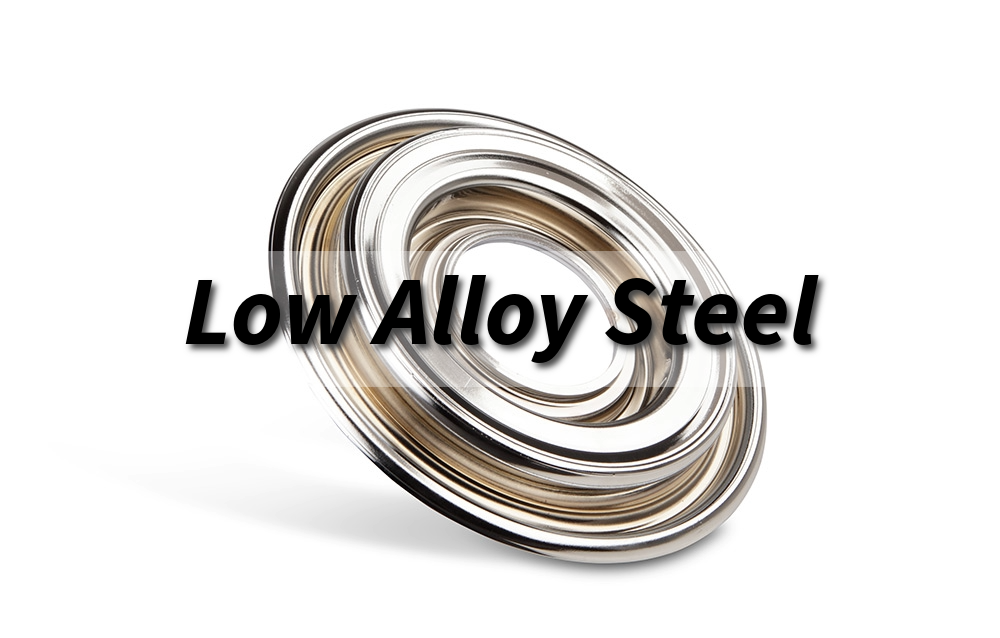
Learn about the different grades and types of low alloy steel, and how they are tailored to specific requirements.
Introduction
Low alloy steels are steels where the total amount of alloying elements, excluding carbon, does not exceed 8%. These steels offer a balance of mechanical strength and corrosion resistance.
This article will delve into what low alloy steel is, its types, grades, and practical applications, as well as how it compares to other steel types.
What is Low Alloy Steel?
Low alloy steel refers to a group of steels that contain small percentages of alloying elements, usually between 1% and 8% by weight.
These elements, such as chromium, molybdenum, vanadium, and nickel, are added to improve specific properties like strength, toughness, corrosion resistance, and weldability.
Key Properties
Increased Strength: Low alloy steels are stronger than carbon steels, particularly in high-stress environments.
Enhanced Toughness: These steels can withstand impacts and resist fracturing under load.
Better Corrosion Resistance: Alloying elements like chromium and molybdenum provide increased resistance to corrosion and oxidation.
Improved Weldability: The controlled composition allows for better weldability compared to high alloy steels.
Low Alloy Steel Grades
Low alloy steels are classified into various grades based on their specific chemical compositions and intended use. Common low alloy steel grades include:
AISI 4140: Known for its toughness and good fatigue strength.
AISI 4340: Contains nickel for increased hardness and strength.
AISI 6150: A chromium-vanadium steel known for excellent wear resistance.
AISI 8620: A case-hardening steel used in gears and heavy-duty applications.
Types of Low Alloy Steel
Low alloy steels can be further categorized into different types based on their composition and treatment processes. Each type offers distinct properties tailored for specific industrial needs.
High Strength Low Alloy (HSLA) Steel
HSLA steels are designed to provide better mechanical properties and greater resistance to atmospheric corrosion compared to carbon steel.
They are ideal for structural applications like bridges, towers, and buildings, offering excellent strength-to-weight ratios.
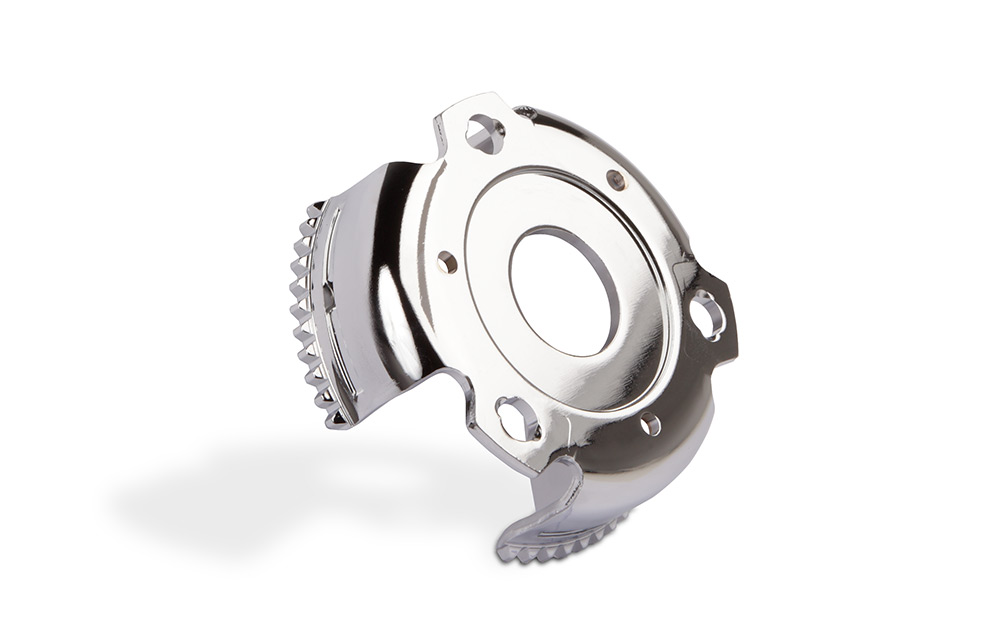
Source: bilsteincrs.com
Quenched and Tempered (Q&T) Low Alloy Steel
Q&T steels are subjected to heat treatment processes to increase strength and toughness.
These steels are commonly used in heavy-duty industrial applications like construction machinery, pressure vessels, and military equipment.
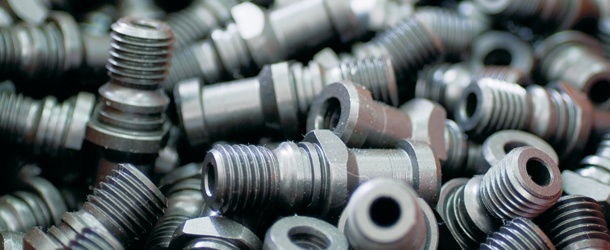
Source: rodacciai.com
Chromium-Molybdenum (Cr-Mo) Low Alloy Steel
Cr-Mo steels are known for their high temperature resistance and strength.
These steels are often used in high-stress applications such as boiler and pressure vessels, pipelines, and power plants.
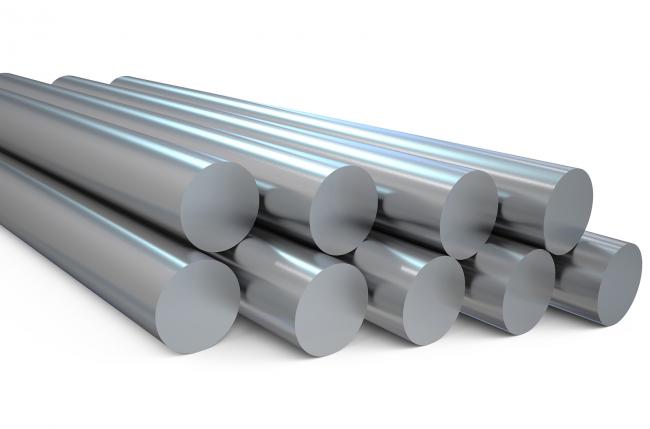
Source: upmet.com
Nickel-Chromium-Molybdenum (Ni-Cr-Mo) Low Alloy Steel
Adding nickel to the Cr-Mo alloy further improves the steel’s strength and toughness, especially at low temperatures.
Ni-Cr-Mo steels are commonly used in aerospace components, high-strength fasteners, and other critical applications.
Vanadium and Titanium Low Alloy Steel
Vanadium and titanium are added to enhance strength and toughness without compromising ductility.
These steels are used in high-performance applications such as automotive components, oil and gas pipelines, and industrial equipment.
Weathering Steel (Cor-Ten Steel)
Weathering steels, also known by the trade name Cor-Ten, are designed to resist atmospheric corrosion by forming a stable rust-like appearance over time.
These steels are commonly used in outdoor structures, such as bridges and sculptures, where long-term durability and minimal maintenance are essential.
Applications of Low Alloy Steel
Low alloy steels have found widespread application in various industries due to their excellent combination of strength, toughness, and weldability. Here are some examples of their use:
Transportation
Railways: Tracks, locomotives, and railway cars.
Shipping: Hulls, decks, and machinery of ships.
Off-road vehicles: Frames, axles, and suspension components.
Consumer Goods
Appliances: Washing machines, dryers, refrigerators, and stoves.
Tools: Hammers, wrenches, and saws.
Sporting goods: Bicycles, golf clubs, and fishing equipment.
Other Industries
Manufacturing: Machine tools, industrial machinery, and molds.
Agriculture: Tractors, combines, and other farm equipment.
Defense: Tanks, armored vehicles, and weapons.
Mining: Mining equipment and infrastructure.
Low alloy steels continue to be a crucial material in modern society, providing essential components for numerous applications. Their versatility and durability make them a preferred choice for engineers and manufacturers worldwide.
Low Alloy Steel vs. High Alloy Steel
The primary distinction between low alloy steel and high alloy steel lies in the percentage of alloying elements, which significantly influences their properties, applications, and cost.
Here's a comparative table:
Property | Low Alloy Steel | High Alloy Steel |
---|---|---|
Alloying Content | 1% - 8% alloying elements | > 8% alloying elements |
Strength | High, with good balance of toughness | Very high |
Corrosion Resistance | Moderate to high | Excellent |
Toughness | High, good resistance to impact | Generally more brittle |
Weldability | Good, particularly in HSLA steels | More difficult |
Heat Resistance | Moderate to high | Excellent |
Ductility | Good | Generally lower |
Cost | Lower | Higher |
Common Uses | Structural applications, pipelines, machinery | Aerospace, chemical processing, power generation |
Examples | HSLA, Cr-Mo steels | Stainless steel, superalloys (e.g., Inconel) |
Low Alloy Steel vs. Stainless Steel
Low alloy steel and stainless steel differ significantly in terms of alloy composition, corrosion resistance, mechanical properties, and typical applications.
The table below compares key aspects of the two materials:
Property | Low Alloy Steel | |
---|---|---|
Alloying Content | 1% - 8% of alloying elements (e.g., Cr, Mo, Ni, V) | Minimum 10.5% chromium, often with nickel, molybdenum, and others |
Corrosion Resistance | Moderate to high | Very high |
Strength | High, especially in heat-treated forms | Moderate to high |
Toughness | High, good impact resistance | Good |
Weldability | Good, especially in HSLA steels | Generally good |
Ductility | Good | High, especially in austenitic types |
Heat Resistance | Moderate | High |
Wear Resistance | Moderate to good | High, especially with hardened stainless steel |
Cost | Lower | Higher |
Magnetism | Typically magnetic | Non-magnetic (austenitic) or magnetic (ferritic/martensitic) depending on grade |
Common Uses | Structural applications, machinery, pipelines | Kitchenware, medical devices, chemical processing, architecture |
Examples | HSLA, Cr-Mo steels | 304, 316, 410, 430 stainless steel |
Limitations of Low Alloy Steel
Despite its many advantages, low alloy steel does have some limitations, including:
Limited Corrosion Resistance: Lower resistance compared to stainless steel, requiring coatings or maintenance in harsh environments.
Heat Treatment Sensitivity: Improper treatment can negatively affect its mechanical properties.
Higher Cost than Carbon Steel: More expensive due to added alloying elements, though cheaper than stainless steel.
Lower Ductility: Reduced formability, making it less suitable for applications needing significant shaping.
Fatigue and Wear: May not perform as well as high alloy steels in conditions of repeated stress or wear.
Conclusion
Low alloy steels are strong, tough, and moderately resistant to corrosion, making them useful in many industries. Engineers can choose the right type by understanding its different grades and properties.
However, it's important to weigh its benefits against its limitations and compare it with other options, like high alloy steel or stainless steel, when selecting materials for a project.
Cutting-Edge Steel Solutions from Unionfab
Unionfab transforms steel visions into realities through precision engineering. With expertise in CNC machining, casting and 3D printing, we deliver highly-engineered steel parts optimized for strength, durability and reliability.
Contact us to discuss your project's technical requirements or get an instant quote!