CNC Grinding: A Complete Guide
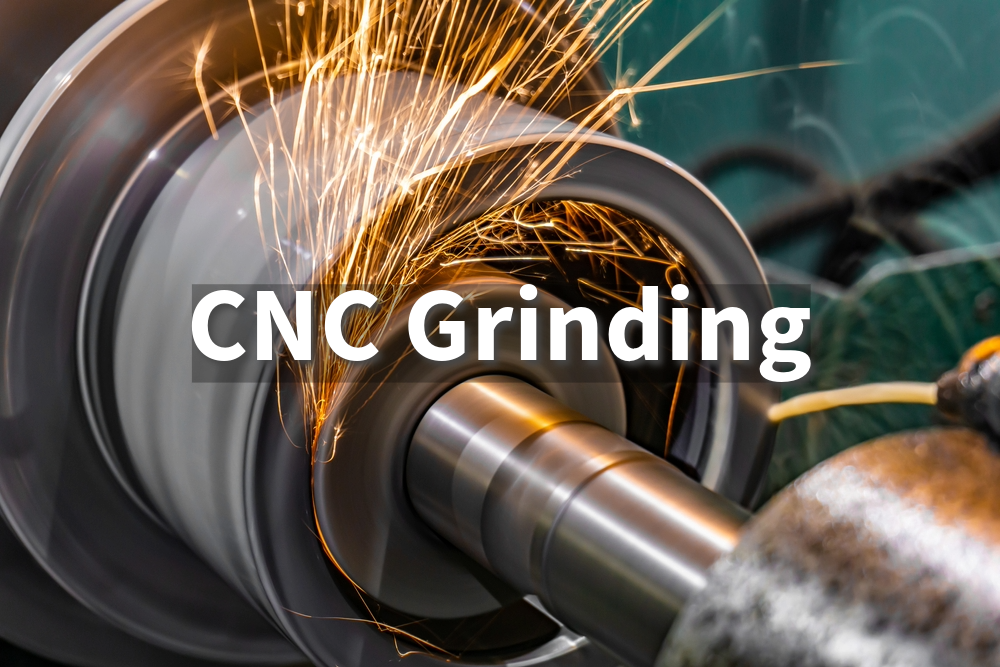
Explore how CNC grinding enhances precision, efficiency, and flexibility in manufacturing. Learn about the key advantages and applications of CNC grinders.
Introduction to CNC Grinding
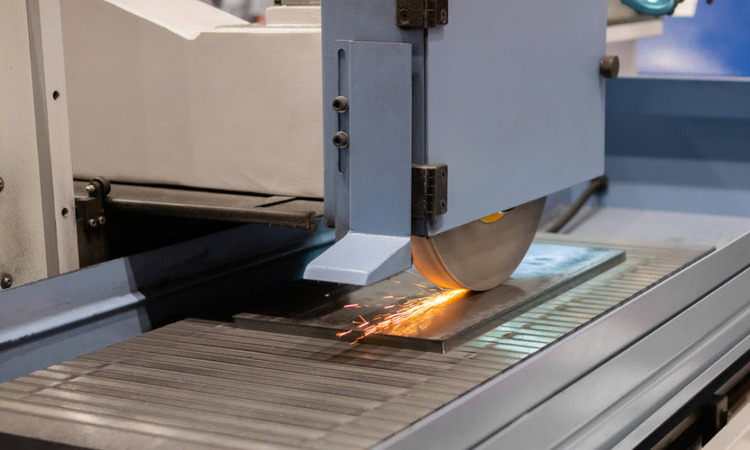
Source: at-machining.com
CNC grinding is a machining process that uses programmed abrasive wheels to shape and finish components. It can precisely process metals and non-metals to tight tolerances and smooth surfaces.
A CNC grinder removes small amounts of material from a workpiece. Its computerized control allows for repetitive, high-precision machining tasks. This makes it suitable for producing complex or high-precision parts across many industries.
What is CNC Grinding?
CNC grinding uses abrasive cutting wheels to remove small amounts of material from a workpiece with precision. Some key aspects of the CNC grinding process include:
A CNC grinding machine controls abrasive wheels or belts to precisely cut complex shapes and contours into metal or other workpiece materials. The wheel is programmed to follow a specific path controlled by computerized numerical codes.
Grinding wheels can be flat, cylindrical, belt-shaped or have a unique contour matching the desired workpiece shape. They rotate at high speeds and their sharp, abrasive grains do the cutting or grinding of the material.
Much smaller amounts of material are removed in grinding compared to other machining like milling, turning or drilling. This allows achieving very fine details and close tolerance sizes in the workpiece.
CNC grinding can produce surfaces that are flat to within a few millionths of an inch. It is well-suited for very hard or brittle materials that are difficult to machine by other processes.
The key difference between CNC grinding and other CNC machining processes like milling or lathe operations is that grinding removes material using an abrasive cutting process rather than direct metal cutting. This allows achieving mirror-like surface finishes and tighter tolerances that are critical for precision applications.
How CNC Grinders Work
CNC grinding machines perform precision grinding through computer numerical control of an abrasive cutting wheel. An overview of the basic machine components include:
A rigid casting or frame provides a stable base for the grinding process. It houses the motor, slides and other moving parts.
The workhead fixture precisely holds and rotates the workpiece. It is connected to the Computer Numerical Control (CNC) system to be accurately positioned and aligned with the grinding wheel.
The grinding wheel head holds the abrasive grinding wheel and precisely positions it in relation to the workpiece using a servo motor and electronically controlled slides.
A CNC controller runs the grinding program, providing coordinated movement of the workpiece and wheel to perform the accurate and repeatable cuts defined in the program.
The main types of CNC grinding machines include:
Surface Grinders - Used to produce flat, angular and contour surfaces. The wheel sits in a vertical spindle above a horizontal worktable.
Cylindrical Grinders - Produce cylindrical/tubular components. The wheel is fitted on a horizontal spindle for rotary grinding against a revolving workpiece.
Centerless Grinders - Have no workpiece fixtures. Parts pass between two rotating grinding wheels.
Internal Grinders - Create precision bores or holes in the workpiece. The smaller grinding spindle fits inside the larger workpiece spindle.
This provides an overview of the key machine components and most common CNC grinder types used in manufacturing. The CNC control allows precision automation of the grinding process.
Key advantages of CNC grinding:
Precision and Accuracy in Surface Finishing
CNC grinding can achieve incredibly smooth surfaces with a median roughness of less than 1 micrometer. This is far better than alternative processes.
Close tolerances within a few millionths of an inch can be maintained due to the small material removal volume of grinding.
Complex contoured and multipart molds/casts can be finished to a very high degree of angularity, cylindricity and geometric tolerance.
Time and Cost Efficiency
Setup and processing times are greatly reduced through automated CNC programming of grinding paths.
Multi-step manual processes can be combined into single setups to improve throughput.
less need for expensive mold refinishing leads to lower total manufacturing costs.
Versatility in Material Processing
A wide variety of materials like steel, ceramic, glass and composite can be ground due to its non-contact abrasive cutting.
Even very hard, heat-treated alloys and brittle materials are grindable.
Complex internal and external contours can be machined efficiently in a single clamping.
In summary, CNC grinding delivers precision finishing, automation advantages for high production, and flexibility in machining different material types - making it a very powerful precision manufacturing process.
Applications of CNC Grinding
Industries Using CNC Grinding
Automotive: engine components, turbochargers, pistons, wheels
Aerospace: jet engine parts, landing gear components, aircraft blades
Medical: implants, surgical instruments, prosthetics
Electronics: semiconductor wafers, printed circuit boards
Industrial machinery: molds, dies, machine tooling
Optics: lenses, prisms, mirrors
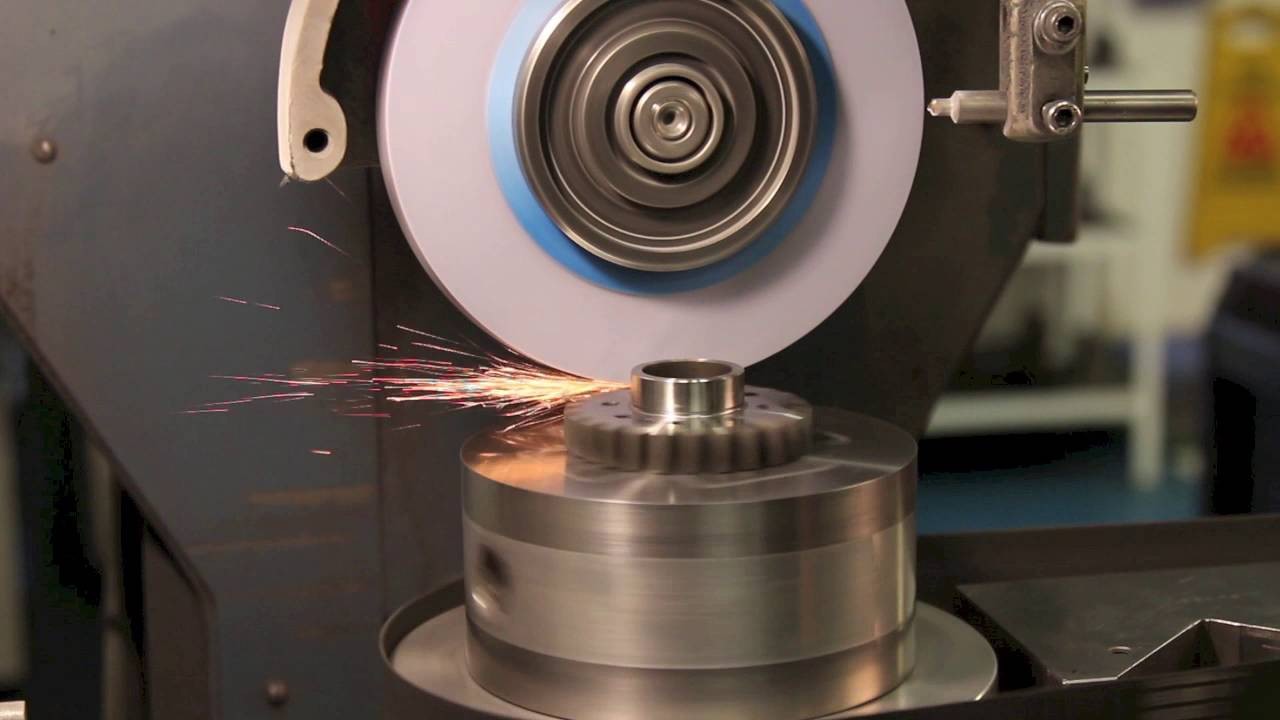
Source: at-machining.com
Typical Parts and Materials
High-strength alloys: stainless steel, titanium, Inconel
Brittle materials: ceramic inserts, carbides, optical glass
Small precision parts: gears, bearing races, threaded fasteners
Intricate molds and dies: for plastic parts injection molding
Complex profiles: contour grinding of turbine blades, camshafts
Large assemblies: centerless grinding of cylindrical rods up to 6m
CNC grinding excels at producing tiny yet critical features in demanding industries. Its combination of precision, versatility and automation makes it well-suited for a huge range of manufacturing applications across many sectors.
CNC Grinding vs. Conventional Grinding
CNC grinding utilizes computer numerical control to automate the grinding process compared to manual conventional grinding methods. The main advantages of CNC include:
Precision & Repeatability
CNC uses precise G-code programming to repetitively machining complex geometries with micron-level accuracy.
Programming Flexibility
Grinding programs can be easily modified for new part designs without tooling changes.
Increased Productivity
Automated CNC process grinds multiple identical parts faster than manual methods.
Improved Operator Safety
Machining is automated, reducing risks from manually moving heavy grinding wheels.
Limited Operator Dependence
CNC performance is highly repeatable regardless of operator experience level.
Conventional grinding relies on the manual control and skill of operators to select and move grinding wheels. It has less capability for intricate profiles, involves more setup time for tooling changes, and produces less consistent results.
In summary, CNC automation enhances precision, productivity and safety for mass-production grinding compared to non-computerised manual methods. It enables new opportunities for complex high-precision part machining.
Choosing the Right CNC Grinder
Here are some key points to consider when choosing a CNC grinder:
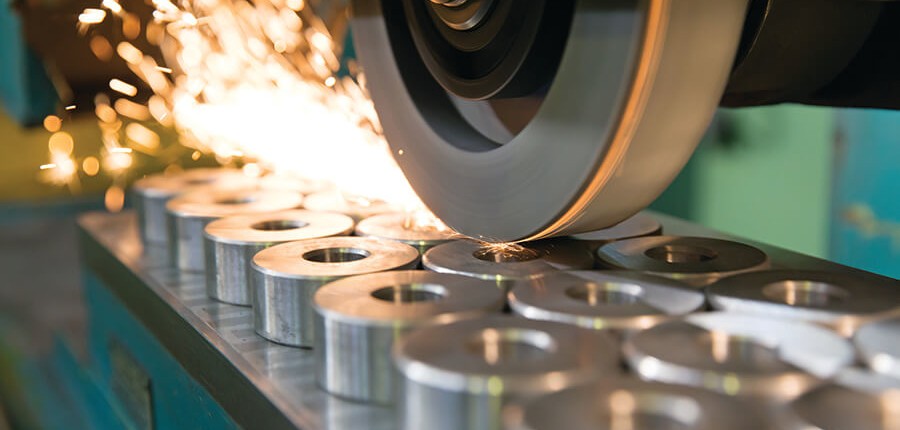
Source: cncjurczak.pl
Machine Size & Power
Maximum workpiece dimensions, wheel size and weight capacity
Accuracy & Repeatability
Positioning accuracy in microns, throughput, spindle control
Controls & Software
CNC controller type, programming format/language compatibility
Automation Features
Automatic loading/unloading, wheel dressers, collision avoidance
Spindle & Wheel Options
Types, speeds, wheel balancing, dressing capabilities
Maintenance Access
Ease of accessing components for cleaning and replacement
To maximize performance:
Follow manufacturer scheduled maintenance of wheels, slides, gears
Regularly vacuum and wipe grinding areas to remove swarf/debris
Accurately dress wheels to maintain sharp cutting surfaces
Ensure rigid clamping of workpieces to avoid positional shifts
Use proper coolant systems to flush away grinding heat
Train operators on safe operating procedures
Choosing a grinder with features aligned to your needs and budget, along with preventative maintenance, will ensure optimal precision, life and safety.
Conclusion
In conclusion, CNC grindng has become a invaluable precision machining process for manufacturing industries worldwide due to its unparalleled capacity for high-accuracy part finishing and complex profiling.
As margins are compressed and customer demands for quality and delivery escalate, efficient and repeatable grinding automation is essential.
Going forward, further advancement in CNC grinding technology will continue enabling new applications and production volumes. Developments include more powerful and compact grinding centers with higher axis speeds, improved resolution and thermal stability.
New automation systems will integrate loading/unloading robots, in-process gauging and artificial intelligence for self-optimizing processes. Advanced abrasive materials, dressers and bonded wheel technologies are enhancing material removal rates and component lifetimes.
Explore Precision Manufacturing Solutions with Unionfab
At Unionfab, we are committed to helping businesses achieve the highest level of precision in their manufacturing processes.
While CNC grinding is a critical part of many industries, Unionfab focuses on other cutting-edge manufacturing technologies to bring your designs to life with accuracy and efficiency, our expert team at Unionfab is here to consult with you on the best manufacturing techniques for your specific project.
Contact us today to learn more about how Unionfab can support your business with innovative, high-quality manufacturing solutions that fit your unique needs.
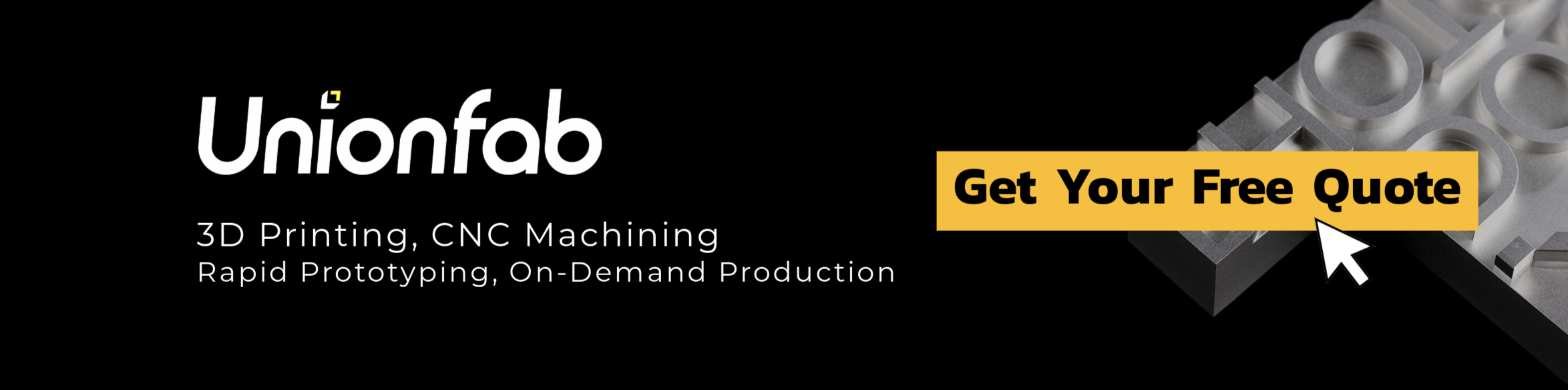