4 Axis CNC: The Key to Complex Machining
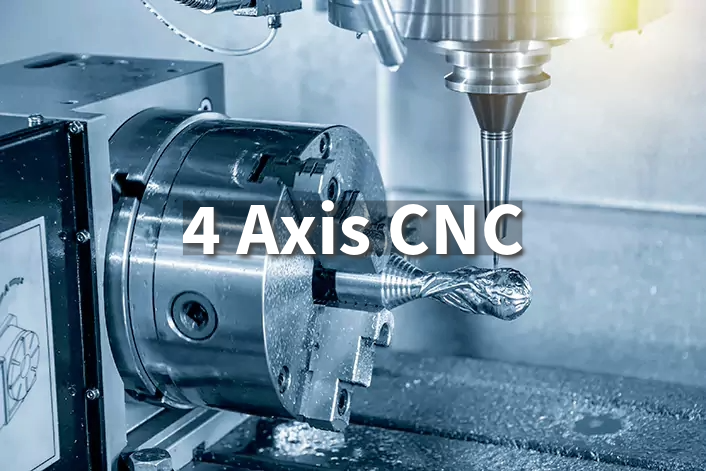
Uncover the key benefits of 4 axis CNC machining for more complex, efficient production processes.
Introduction
Computer Numerical Control (CNC) machining is a manufacturing process where pre-programmed computer software dictates the movement of factory tools and machinery. Rather than having a machining operation controlled manually by an operator, CNC utilizes automated toolpaths to precisely shape raw material like metal, plastic, wood, foam, and composites into finished parts.
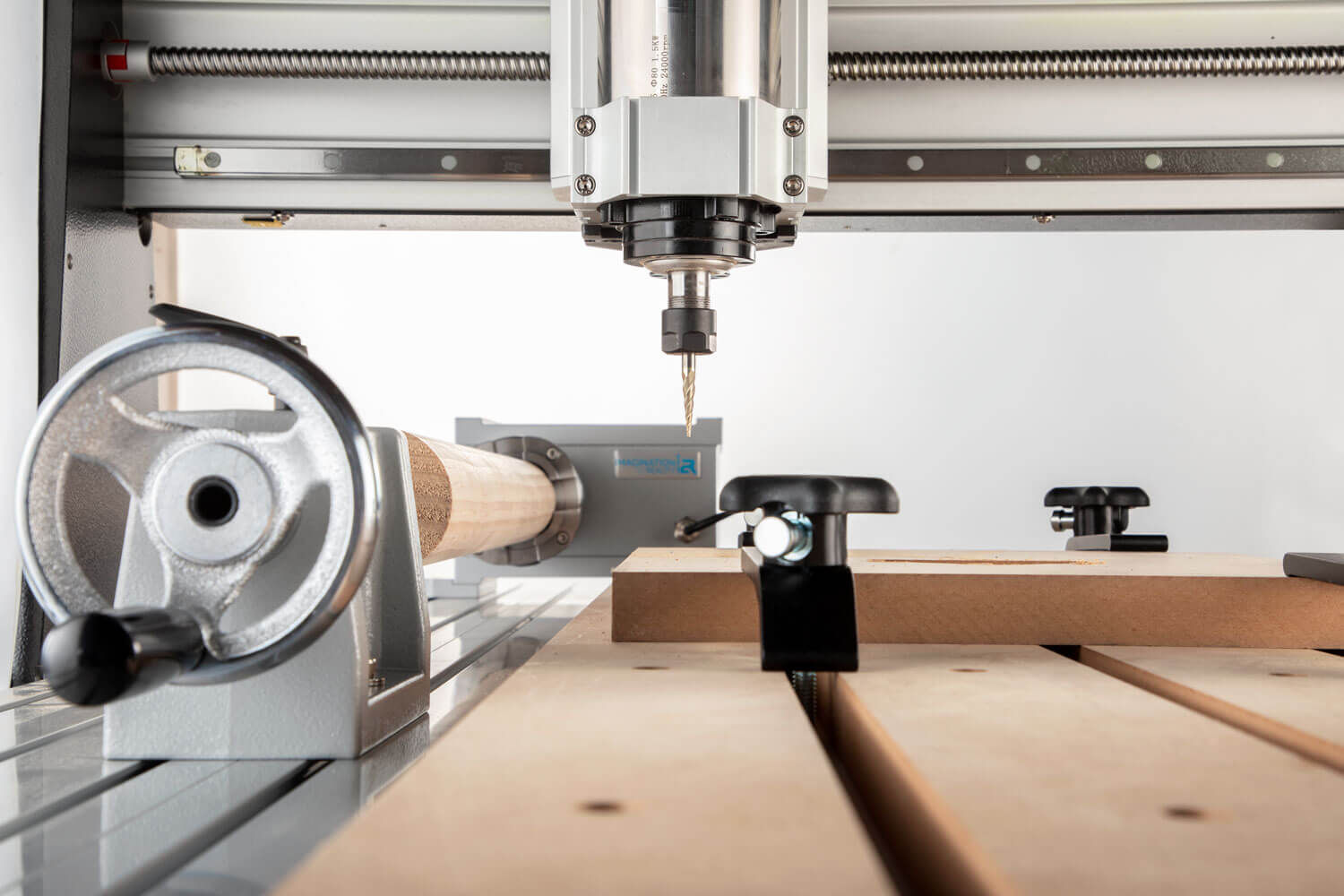
Source: bgprecision.com.au
Focus on 4 Axis CNC
While basic 3 axis CNC machines can handle many standard manufacturing tasks, more complex parts often require additional rotational axes of movement. This is where 4 axis CNC truly shines.
The addition of a 4th axis, usually in the form of a rotary table, allows a part to be machined in multiple orientations without having to manually re-clamp and re-position it. This greatly simplifies setups and improves precision for parts that have features milled at various angles.
Applications of 4 Axis CNC
Common products manufactured using 4 axis CNC include turbine blades, camera lenses, engine components, and orthopedic implants. The 4th axis provides the capability to machine complex contours or profiles on multiple sides and faces of a part without stopping the automatic cycle.
This increased flexibility makes 4 axis CNC well-suited for low volume, high precision applications across many industries. It allows for more complex part geometries to be produced efficiently through single set-up machining cycles.
What is a 4 Axis CNC Machine?
Definition of 4 axis CNC technology
A 4 axis CNC machine is a computer numerical control (CNC) system that can control four axes of movement simultaneously - the traditional three linear axes (X, Y, Z) plus one rotary axis.
How it differs from 3 axis machines
Compared to a traditional 3 axis machine, which can only move tooling in three directions, a 4 axis CNC adds a fourth rotational axis that allows the part to be tilted or turned. This extra axis of motion provides greater flexibility to machine complex geometric shapes.
How 4 Axis CNC Machines work
In a 4 axis machine, the primary three axes (X, Y, Z) control the linear movement of the tooling head in the horizontal plane and vertically. The fourth axis is typically a rotary table that the raw material or finished part is attached to. By rotating this table, the CNC can access all faces of the part without having to re-clamp it. Precise servo motors synchronize the movements of all four controlled axes, allowing for complex profiles to be milled or drilled on multiple sides in a single set-up.
4 Axis CNC Mill
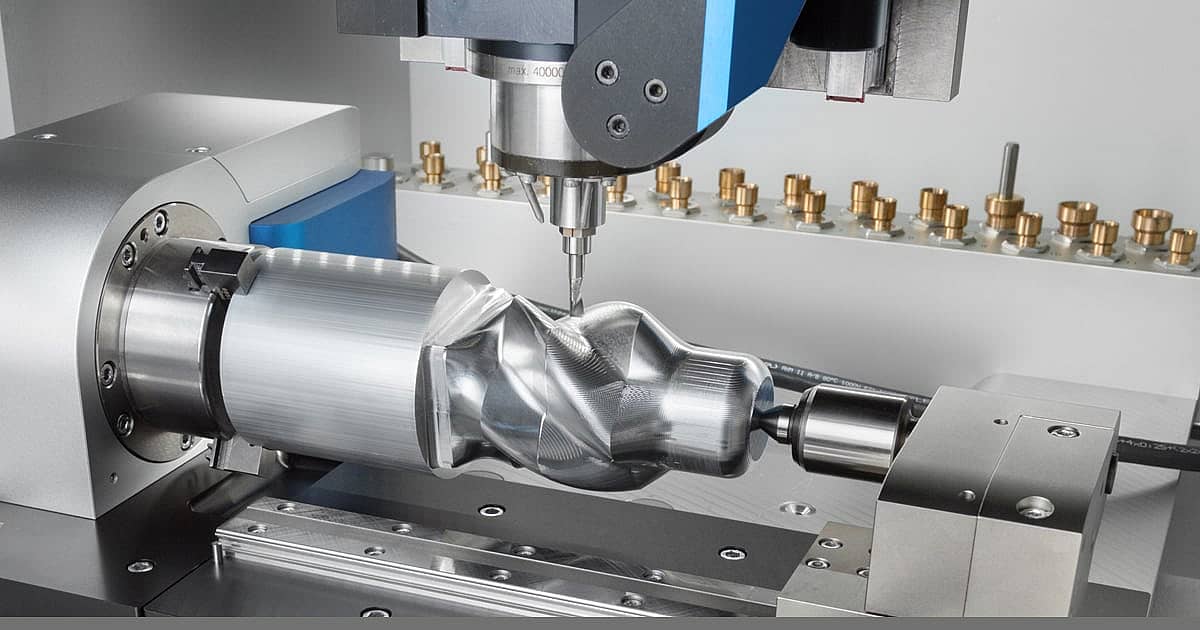
Source: datron.com
4 axis CNC mills play an important role in advanced manufacturing facilities. A CNC mill is a machining center that utilizes endmills and drilling tools to shape raw materials. Adding a fourth rotary axis takes its capabilities to a new level.
Role of 4 axis CNC mills
Equipped with a trunnion table or rotary platform as the fourth axis, 4 axis CNC mills can machine parts in any orientation without needing to re-clamp them. This allows complex profiles to be milled on multiple sides and faces of a workpiece in a single loading. The mill can accurately position and synchronize movement of the spindle and rotary unit for intricate multi-surface machining.
Projects they handle
Common applications include molds, dies, aerospace components and medical implants that have intricate 3D geometries requiting machining on several planes. Impellers, turbine blades and mechanical seals also benefit from 4 axis mills. Non-conventional parts with sculpted or contoured sides like propellers and prosthetics can be machined efficiently. The rotational axis expands what designs can be brought directly from CAD models to physical production.
4 Axis CNC Router
Definition and applications of 4 axis CNC routers
A 4 axis CNC router functions much like a 4 axis mill but is optimized for working with non-metallic materials like wood, plastics, composites and foams. The additional rotational axis allows complex 3D profiles to be cut on multiple sides of a workpiece. Common projects include signs, architectural models, prototyping parts, electronics housings and point-of-purchase displays.
Routers vs. mills for different machining needs
CNC mills are better suited for heavy-duty machining of metals where rigidity and tool loads are critical. Their closed construction contains metalworking fluids and chips.
Routers work ideally for multi-axis cutting of less dense materials. Their open-frame design provides good access and chip/shaving removal. Compared to mills, routers cut at higher speeds and feeds for productivity.
Both play an important role - 4 axis routers economically produce intricate short-run plastic/wood products while 4 axis mills precision-machine advanced metal components. The optimal choice depends on production volumes and material being cut or milled.
Advantages of 4 Axis CNC Machining
Precision in machining complex parts
The 4th rotary axis allows precise cutting or milling of intricate profiles on multiple surfaces without rehandling parts. Features such as twisted reliefs and asymmetrical contours can be machined to tight tolerances.
Versatility in material handling and geometries
A wide range of materials from plastics to metals can be handled efficiently. Intricate blade designs, freeform shapes, and sculpted components beyond the capabilities of manual machining can now be produced.
Increased productivity and reduced manual labor
Complex multipoint surfaces are achieved through single setup automated cycles rather than separate manual operations. Cycle times are decreased as parts need not be re-verified, unclamped and repositioned multiple times. Labor costs are minimized while throughput is boosted.
In summary, 4 axis CNC technology enables manufacturing of high-value complex parts with perfected surfaces, tighter tolerances and less human involvement. Greater geometry freedom and reduced setups accelerate production. As designs advance, 4 axis control allows precision machining needs to be met cost-effectively for specialized short-run and prototype applications.
Applications of 4 Axis CNC Machines
Industries where 4 axis CNC is most beneficial:
Aerospace - aircraft parts, turbine blades
Medical - implants, surgical tools, dental models
Die/mold making - dies for injection molding, casting
Automotive - engine/transmission components
Consumer goods - electronics housings, small appliances
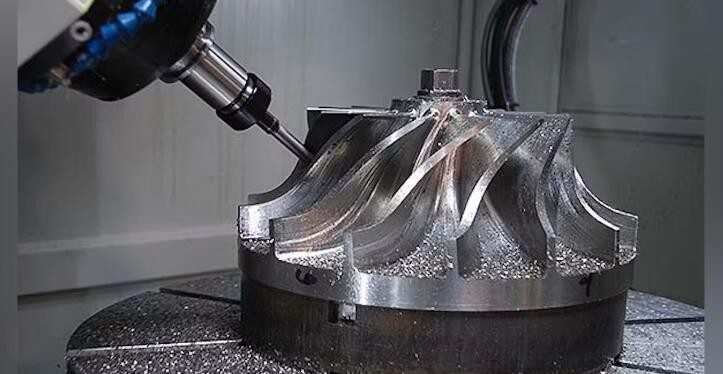
Source: worthyhardware.com
Examples of products made with 4 axis CNC machines:
Prosthetic sockets and joints with complex curvature
Propellers and impellers for marine applications
Camera, telescope and microscope lenses
Plastic parts with ergonomic or contoured shapes
Molds and dies for complex flashing/trim parts
Orthotics with customized anatomical fits
Turbine components like nozzles for aerospace engines
4 axis CNC is especially useful for industries that manufacture high-precision parts in low volumes with demanding geometries. Its precision and programming efficiency make it well-suited for prototyping. As designs become more intricate, 4 axis control opens up new possibilities for engineering complex functional components across many manufacturing sectors.
Conclusion
To summarize, 4 axis CNC technology provides unmatched flexibility and precision for machining parts with intricate 3D geometry. The additional rotational axis allows complex contours to be produced on multiple faces of a workpiece within a single automated cycle. This greatly simplifies setups while improving dimensional accuracy and surface finishes.
By adopting 4 axis CNC, manufacturers gain the capability to engineer completely new product designs limited only by their imagination rather than machining constraints.
Intricate impellers, sculpted housings, and anatomically customized implants can be precision-machined efficiently in low volumes. Diverse industries from aerospace to medical are leveraging 4 axis control to manufacture next-generation components.
Unionfab: Your Guide to Understanding 4 Axis CNC
Need help navigating the world of CNC technology or other advanced manufacturing solutions? Reach out to Unionfab for expert advice and support.
With six self-owned factories and a decade of experience, we're equipped to support your needs, from CNC machining to advanced manufacturing solutions.
Our experts can evaluate your application, recommend the best technical approach, and ensure you leverage the full capabilities of 4 or 5 axis systems.
Don't hesitate to contact us to discuss your specific project challenges. Our team of manufacturing specialists is ready to help you maximize the performance of your CNC processes through every step of the design-to-production workflow.