Ultem, or Polyetherimide (PEI) Explained
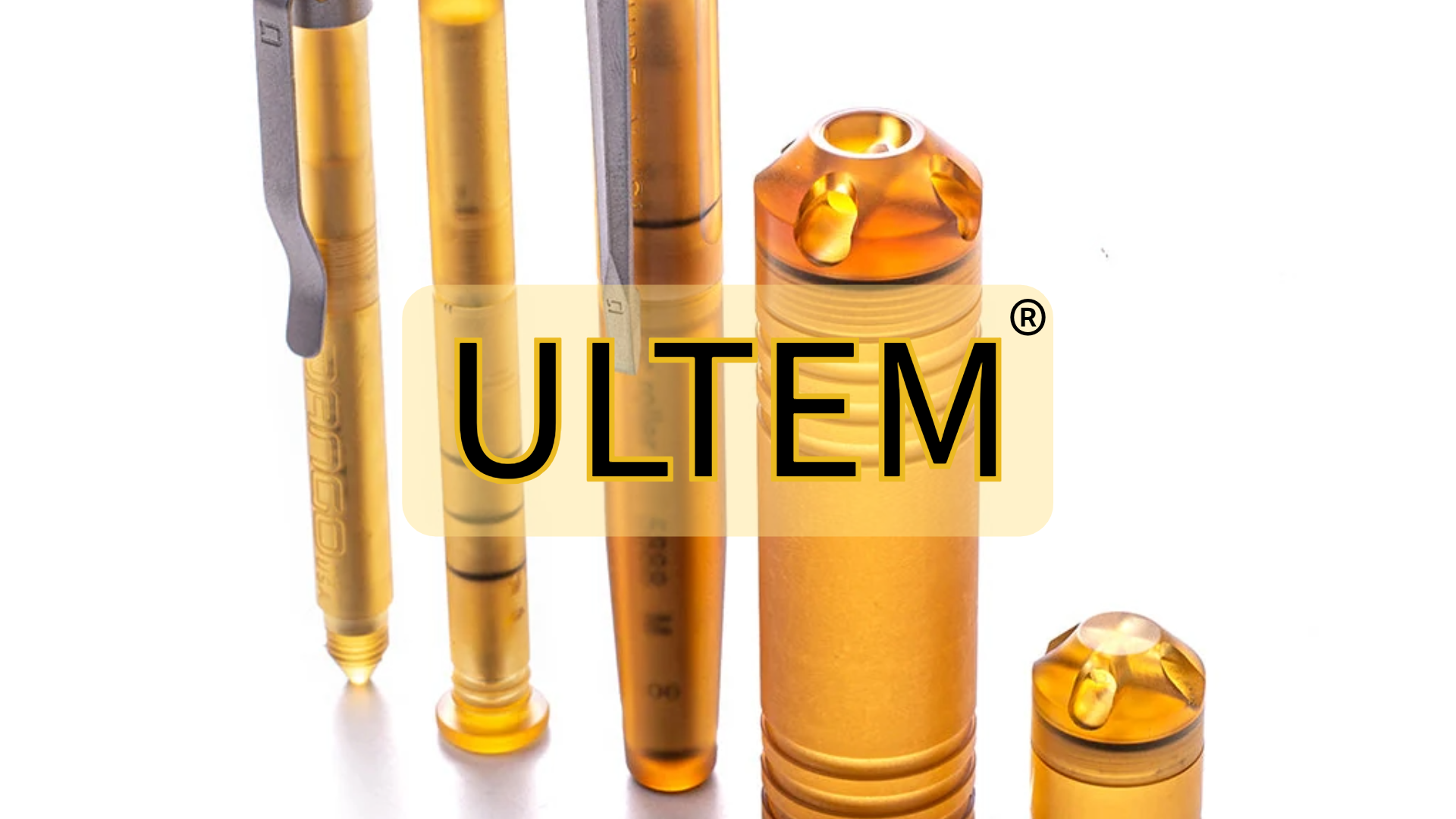
Clarify what is Ultem, its relation to PEI plastic, its types, properties, and uses. Also, the article will compare Ultem vs. PEEK.
Introduction
ULTEM, a high-performance thermoplastic known scientifically as polyetherimide (PEI), stands out for its exceptional mechanical strength, heat resistance, and chemical stability.
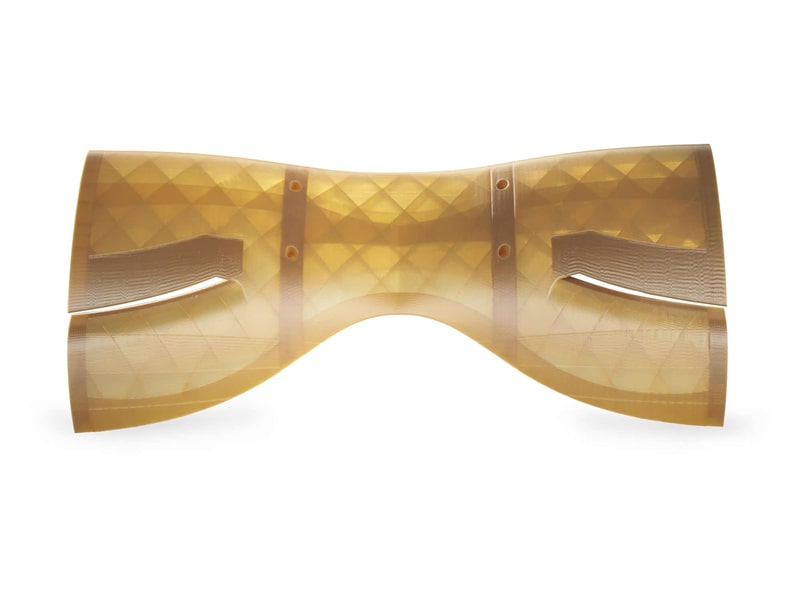
Source: uncrate.com
Developed originally for demanding industrial applications, ULTEM has gained widespread use across industries. Its versatility extends to various forms, including 3D printing filaments, making it a go-to material for both engineers and designers.
The article will clarify what is Ultem, its relation to PEI plastic, its types, properties, and uses. Also, the comparison between Ultem and PEEK will be covered.
Is Ultem the Same as Polyetherimide (PEI) ?
No, Ultem is not exactly the same as Polyetherimide (PEI).
Generally speaking, Ultem" is widely used to describe this material in industries like aerospace, automotive, and electronics, especially when referring to specialized applications like 3D printing and high-temperature environments. However, they are not the same.
Polyetherimide (PEI) is the generic name of Ultem. It is an amorphous, amber-to-transparent thermoplastic with characteristics similar to the related plastic PEEK.
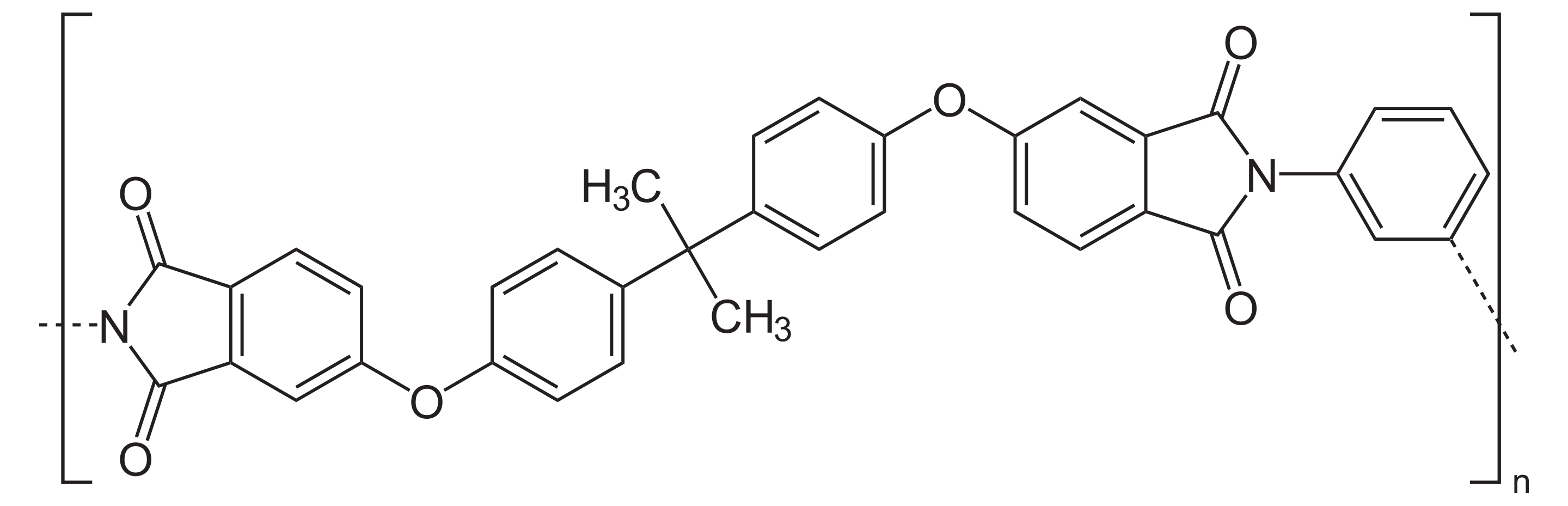
Source: wikipedia.org
“Ultem” is a brand name for a specific type of PEI developed by General Electric Plastics Division (now SABIC) . It refers to high-performance thermoplastic resins known for their excellent mechanical strength, heat resistance, and chemical stability.
Many companies use the original Ultem resin from SABIC and optimize it for specific manufacturing methods. For example, Stratasys adapted it to Ultem™ 9085 for FDM (Fused Deposition Modeling) 3D printing. Ultem™ 9085 offers enhanced flame retardancy, a high strength-to-weight ratio, and meets aerospace and automotive standards for low smoke and toxicity.
Therefore, in one word, all Ultem is PEI, but not all PEI is ULTEM. And Ultem, as the most popular and well-known brand of PEI, can be generally used to describe Polyetherimide (PEI) due to its market dominance and widespread recognition.
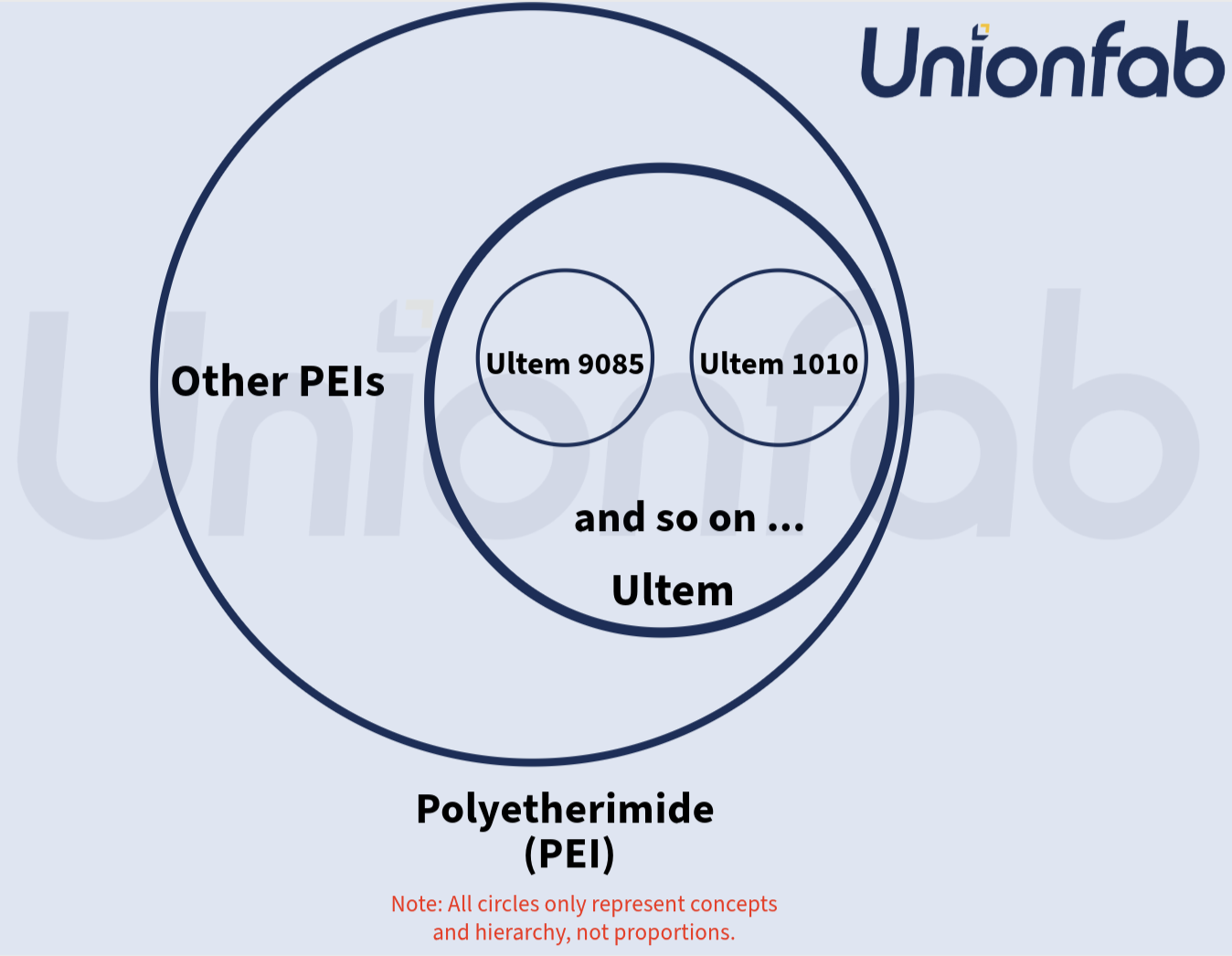
Grades and Properties of Ultem
After understanding what ULTEM is, let’s first take a look at a concise table summarizing its key properties. The table highlights Ultem’s core characteristics in areas such as thermal stability, mechanical strength, and chemical resistance, helping to explain why it is widely used in demanding industrial applications.
Property | Description |
---|---|
Color | Black; Natural amber; Brown |
Thermal Stability | High glass transition temperature (~217°C). |
Mechanical Strength | Strong tensile strength and stiffness. |
Flame Retardancy | Excellent flame resistance with low smoke and toxicity. |
Chemical Resistance | Resists many harsh chemicals and hydrolysis. |
Electrical Insulation | Great dielectric strength and stability across frequencies. |
Dimensional Stability | Maintains shape and size under stress and temperature changes. |
Applications | Used in aerospace, automotive, medical devices, and 3D printing. |
The Ultem family of resins includes a variety of grades designed for different applications. Here, we will present the properties of the most well-known and commonly-used 4 types: Ultem™ 1000, Ultem™ 9085, Ultem™ 1010, Ultem™ 2200.
Property | ULTEM™ 1000 | ULTEM™ 9085 | ULTEM™ 1010 | ULTEM™ 2200 |
---|---|---|---|---|
Glass Transition Temperature (°C) | 217°C | 186°C | 216°C | 217°C |
*Tensile Strength (MPa) | 110 MPa | 90 MPa | 100 MPa | 170 MPa |
* Flexural Modulus (GPa) | 3.3 GPa | 2.15 GPa | 3.2 GPa | 5.5 GPa |
Flame Retardancy | Standard | Aerospace-grade | Food/medical grade | Glass-filled |
Advantage | Good all-around performance | Excellent (low) flame, smoke, and toxicity (FST) properties | Sterilizable and biocompatible | High stiffness and dimensional stability |
Chemical Resistance | Good resistance to most chemicals | Resistant to hydrolysis and harsh chemicals | Resistant to sterilization chemicals | Improved chemical resistance due to glass fiber |
Electrical Insulation | Excellent dielectric strength | Good insulation over a wide frequency range | Stable electrical properties | High dielectric strength |
Dimensional Stability | Stable even under thermal stress | Good dimensional stability in challenging environments | Retains stability in varying temperatures | Enhanced stability with low thermal expansion |
Applications | General-purpose, electrical components | Aerospace, transportation | Food processing, medical devices, industrial applications | High-strength components, automotive |
Properties of Ultem™ 1000, Ultem™ 9085, Ultem™ 1010, Ultem™ 2200
*Note: The two values can vary depending on testing conditions, material orientation, and processing methods.
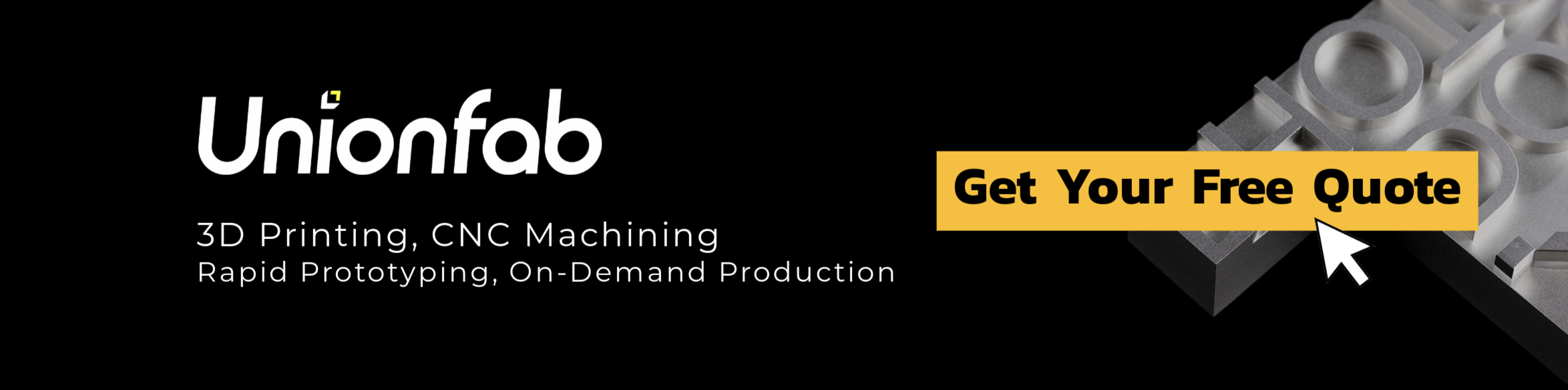
Ultem VS. PEEK
Thermal Stability
ULTEM: High glass transition temperature (~217°C) but lower than PEEK.
PEEK: Even higher heat resistance, with a continuous use temperature up to 260°C.
Mechanical Strength
ULTEM: High tensile strength and stiffness but generally lower than PEEK.
PEEK: Superior mechanical properties, especially in demanding environments.
Chemical Resistance
ULTEM: Good resistance to many chemicals, but vulnerable to strong acids and bases.
PEEK: Outstanding chemical resistance, even in harsh environments including strong acids, bases, and solvents.
Cost
ULTEM: Typically costs $100 to $250 per kg, depending on the grade.
PEEK: Significantly more expensive, typically ranging from $500 to $1,000 per kg, depending on the grade.
Flame Retardancy
ULTEM: Naturally flame retardant with low smoke and toxicity.
PEEK: Also flame retardant, but PEEK offers even higher levels of safety in extreme conditions.
Dimensional Stability
ULTEM: Excellent stability, but can be slightly less stable than PEEK under very high temperatures.
PEEK: Exceptional dimensional stability even at very high temperatures and under heavy loads.
Applications
ULTEM: Used in aerospace, automotive, electronics, and medical applications where high strength and moderate heat resistance are needed.
PEEK: Ideal for highly demanding environments like oil & gas, aerospace, and medical implants due to its superior properties.
Processability
ULTEM: Easier to process in 3D printing (FDM) and injection molding.
PEEK: More challenging to process due to its higher melting point and required processing temperatures.
Applications of Ultem
Ultem in Aerospace: ULTEM is widely used for aircraft interior components, ducting, and connectors due to its excellent flame retardancy, low smoke, and low toxicity properties.
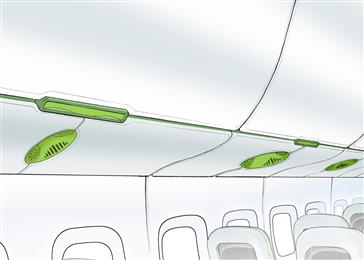
Source: pressreleasefinder.com
Ultem in Automotive: ULTEM’s high strength and heat resistance make it ideal for lightweight yet durable automotive parts, such as lighting housings, sensors, and electronic component enclosures.
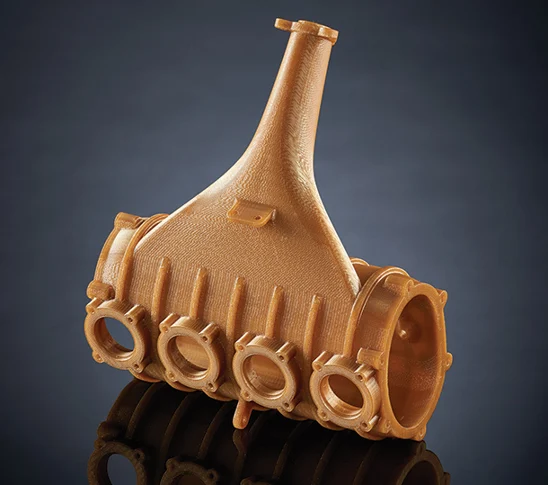
Source: stratasys.com
Ultem in Electronics and Electrical: ULTEM’s superior electrical insulation and thermal stability make it suitable for printed circuit boards, connectors, and components used in high-temperature environments.
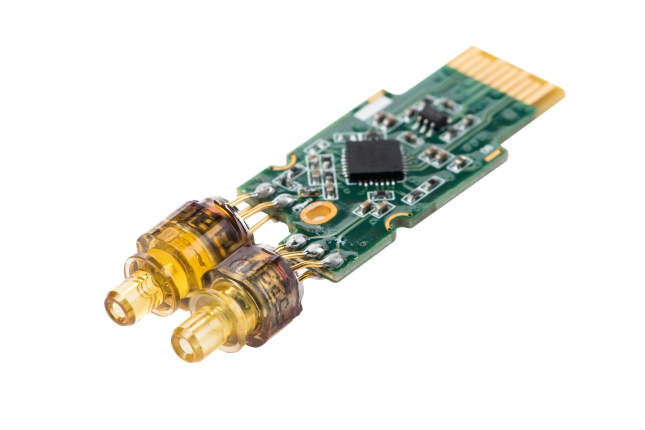
Source: sabic.com
Ultem in Medical Devices: ULTEM’s biocompatibility and sterilizability make it ideal for surgical instruments, medical device components, and diagnostic equipment.
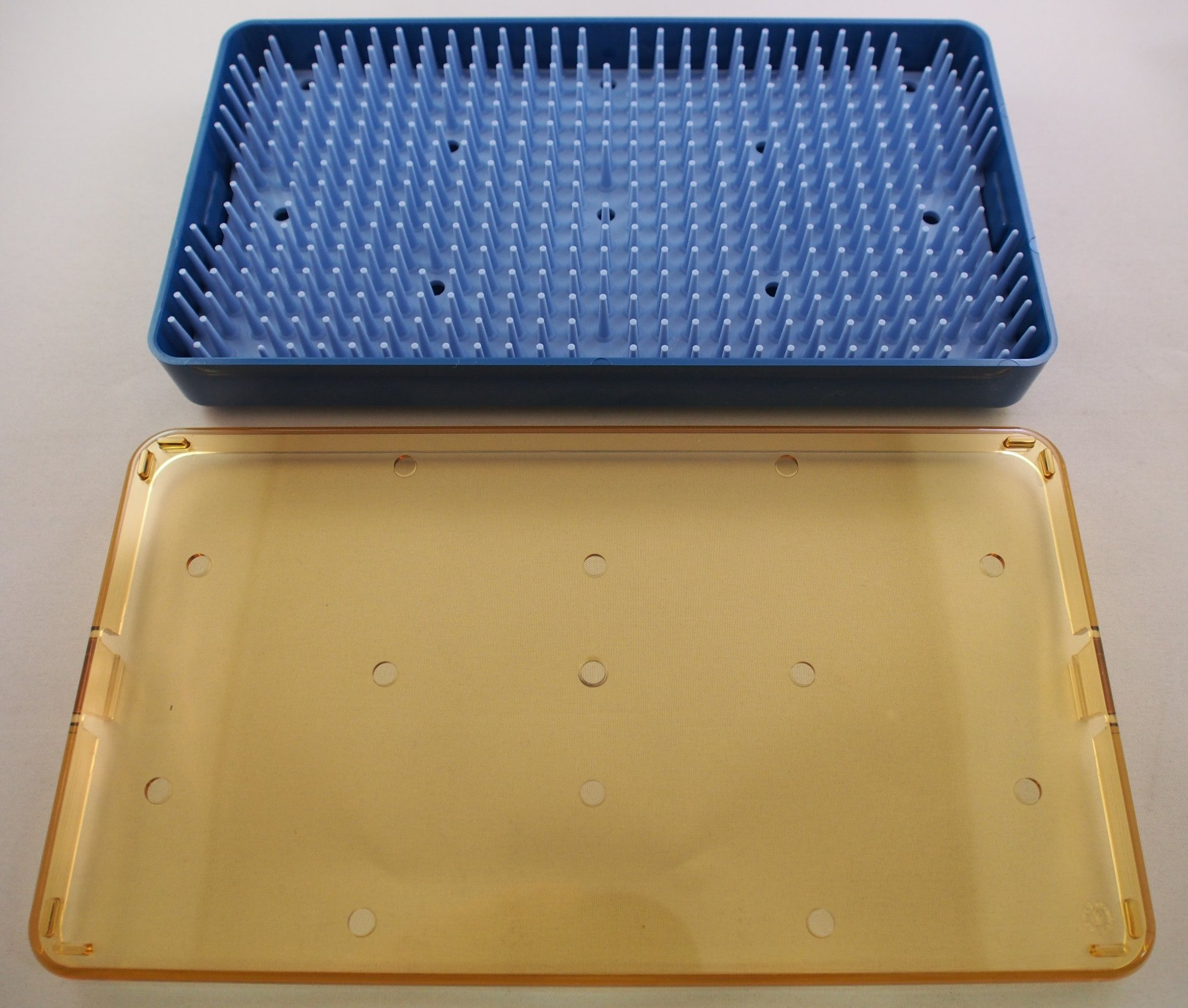
Source: strongvisiontech.com
Ultem in 3D Printing: ULTEM, especially grades like ULTEM™ 9085, is widely used in FDM 3D printing for functional prototypes, tools, and customized parts that require high strength and heat resistance.
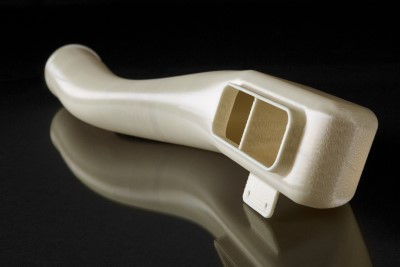
Source: stratasys.com
Ultem in Food Processing: Certain grades like ULTEM™ 1010 are suitable for food-contact applications due to their compliance with food safety standards and ability to withstand high-temperature sterilization.
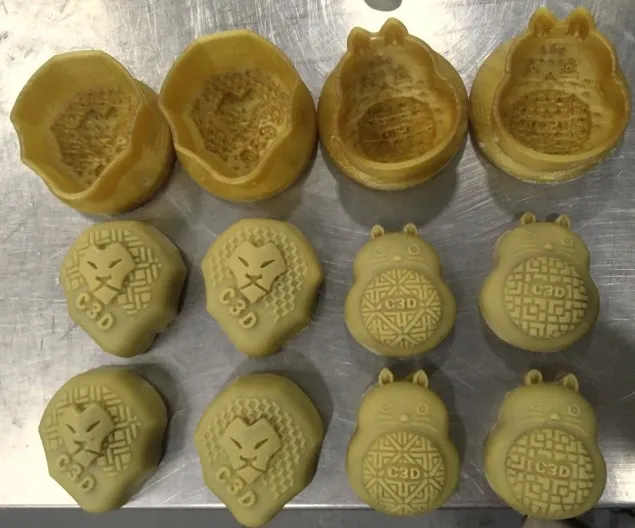
Source: creatz3d.com.sg
Ultem EDC (Everyday Carry): ULTEM is used in EDC products like knife handles, pens, and small tools. Its lightweight, durable, and visually appealing characteristics make it a popular choice for EDC enthusiasts.
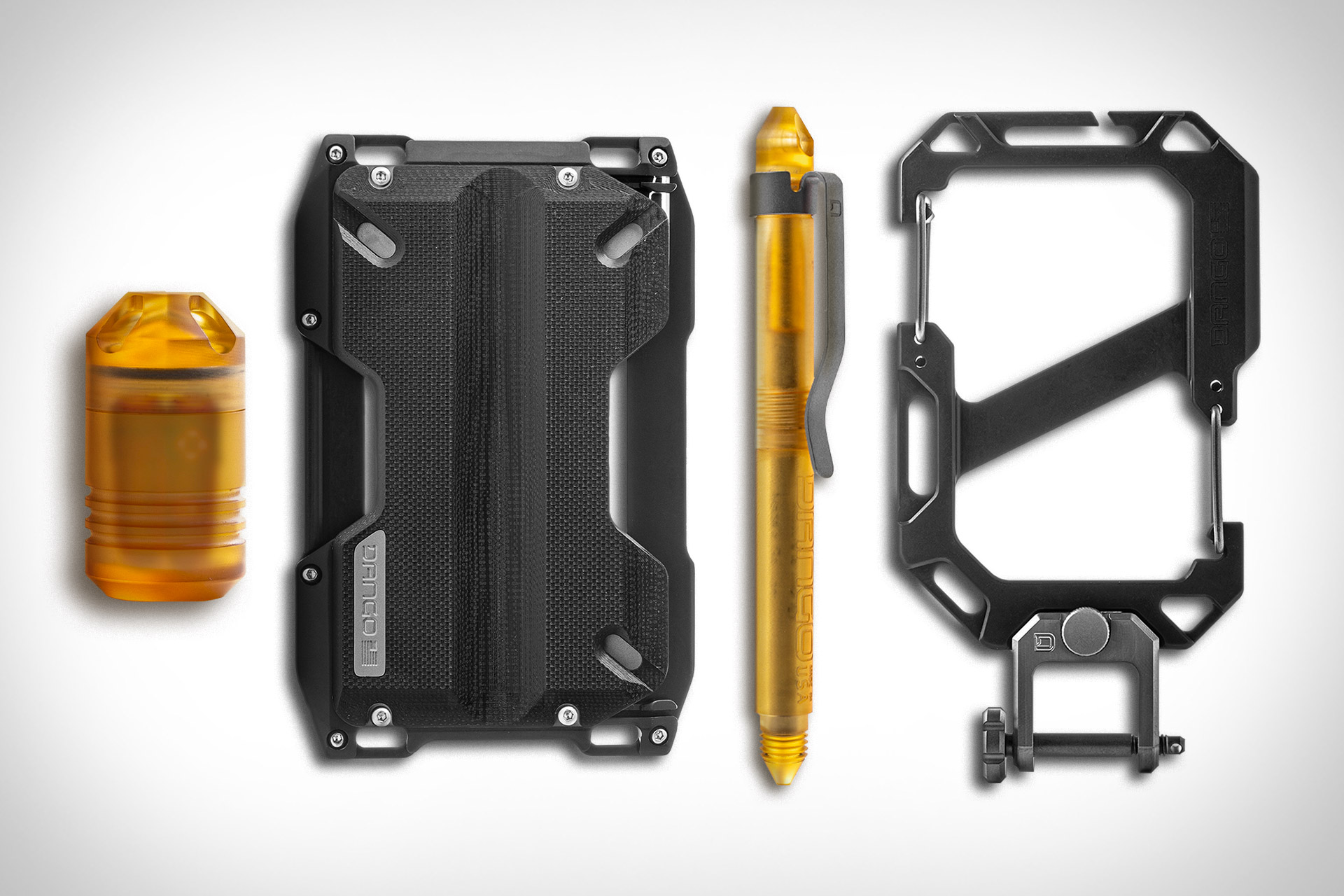
Source: uncrate.com
Conclusion
In summary, Ultem, or polyetherimide (PEI), is a high-performance thermoplastic known for its mechanical strength, heat resistance, and chemical stability.
Its versatility spans from aerospace components to medical devices and 3D printing, offering reliable performance in various demanding applications.
On the other hand, PEEK delivers unmatched mechanical and thermal performance, making it the go-to choice for critical components in oil & gas, medical, and automotive sectors.
At Unionfab, we offer both Stratasys ULTEM™ 9085 for FDM 3d printing and PEEK plastic material for CNC machining.
Whether you need superior heat resistance or exceptional chemical stability, our expert team is ready to help you choose the best material for your needs.