What is Deburring? Definition and Tools Explained
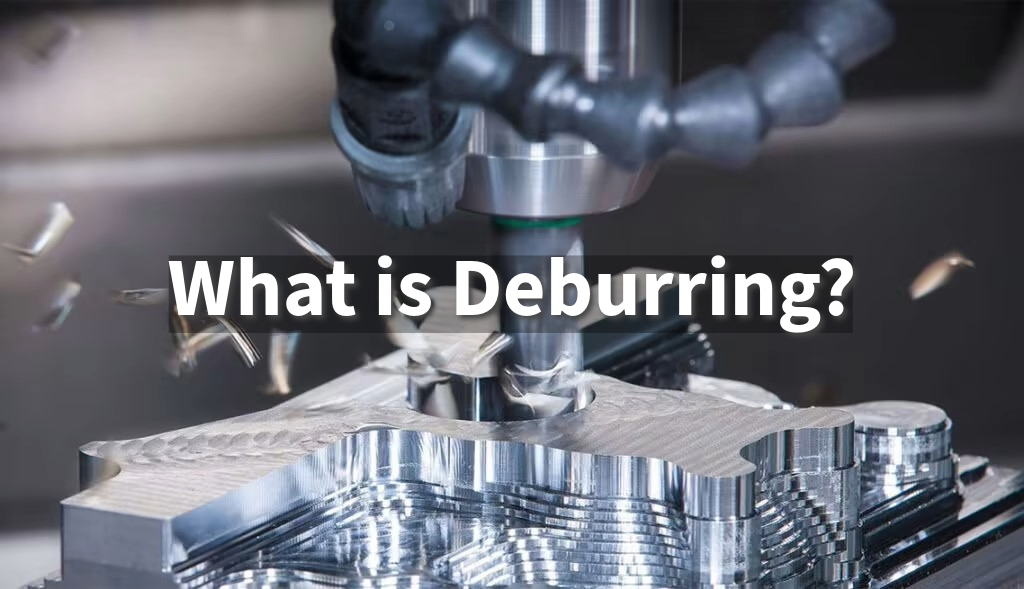
Discover the meaning of deburring, its role in enhancing product quality, and the essential tools and machines used.
Introduction
Has your metal projects ever had sharp edges that could cut you? Deburring is the process that removes those sharp edges to make projects safer. It is an important part of manufacturing metal parts.
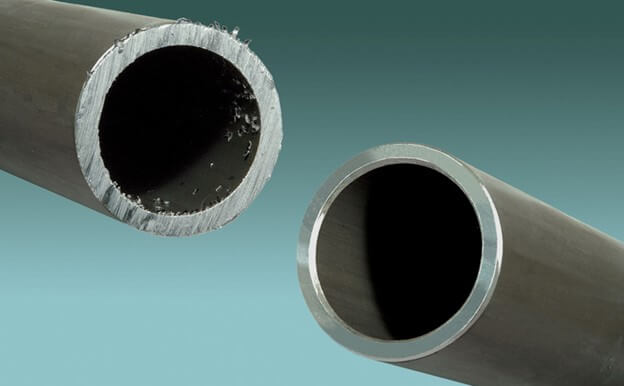
Brief Overview of Deburring
When metal is cut or machined, it leaves behind small burrs or raised edges of metal. Deburring is the process of removing these burrs to create a smooth surface. There are a few different deburring methods used in manufacturing:
Hand Deburring: Using small files, sandpaper or other hand tools to gently remove burrs.
Blast Deburring: Using an abrasive material like aluminum oxide or glass beads fired at high pressure to remove burrs.
Automatic Deburring: Using rotating abrasive bands or brushes on a machine to debur parts quickly.
Importance of Understanding Deburring
Deburring helps create precise, consistent metal parts. It ensures a smooth surface so parts fit together properly. It also makes parts safer to handle by removing sharp edges.
Understanding deburring is important for quality control in manufacturing. Properly deburred parts will work better and be less likely to cause cuts or other injuries.
What is Deburring?
Definition of Deburring
Deburring is defined as the process of removing burrs from the edge or surface of a workpiece made of metal, wood, plastic or other material.
Burrs are small slivers or raised edges of material left behind when a workpiece is cut, sheared, machined or otherwise formed.
Why Deburring is Necessary
There are several important reasons why deburring is necessary in manufacturing:
Safety
Burrs can be very sharp and cause cuts or puncture wounds if handled. Deburring removes this safety hazard.
Fit and Function
Burrs prevent proper assembly of parts and impact how components fit together. They need to be removed for parts to fit as designed.
Finish and Appearance
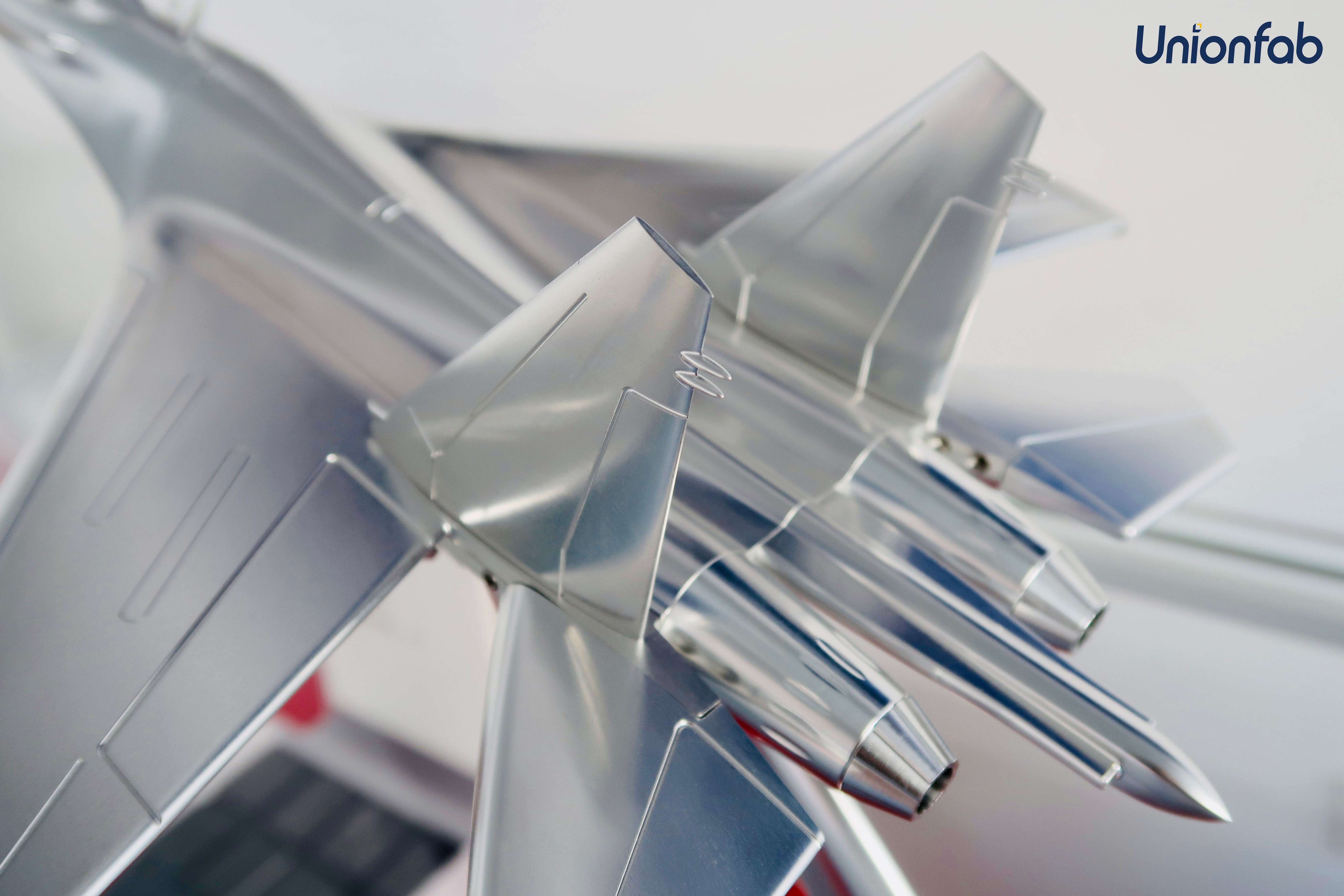
Source: Unionfab
Burrs leave an unfinished surface appearance that does not meet quality standards. Deburring creates a smooth surface.
Durability
Over time, burrs could compromise the strength and durability of connecting parts due to added stress or premature wear. Deburring helps parts last.
Precision
Burrs can interfere with tight tolerances and precise measurements needed for parts to perform as specified. Deburring ensures dimensional accuracy.
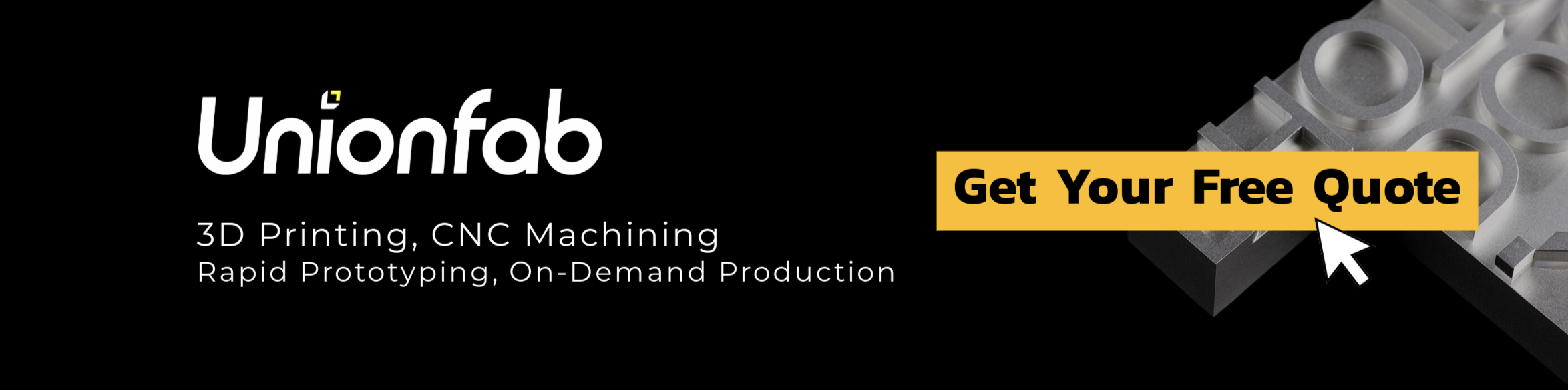
Deburring Process
Steps Involved
The basic steps in deburring parts are:
Inspect for burrs - Examine edges and surfaces under good lighting to find all burrs.
Prepare part - Secure part in deburring fixture or use protective gloves for handling.
Select deburring method - Choose technique based on part material, required surface finish, and other factors.
Deburr edges - Systematically deburr all edges using chosen technique in straight, overlapping strokes.
Inspect finish - Use a magnifying glass to ensure all burrs are completely removed.
Finish part - Clean and handle part according to quality control standards.
Types of Deburring Techniques
Manual deburring uses hand tools like files, sandpaper or burr removal attachments for drills. It's best for small volume work and complex shapes.
Mechanical deburring employs tumbling barrels, vibratory machines or rotating wire brushes to remove burrs automatically. Good for high production volumes.
Thermal deburring heats parts to make burrs brittle prior to removal using compressed air jets. Works well for metals like aluminum.
Electrochemical deburring (ECD) dissolves metal using electric current and chemical baths for burr removal. Good for parts with tight clearances.
Laser deburring directs high intensity light to vaporize metal burrs. Best for burrs in hard-to-reach places.
Proper deburring ensures precision and safety in manufactured parts. Understanding the process is valuable for quality inspection as well.
Deburring Tools
Manual Deburring Tools
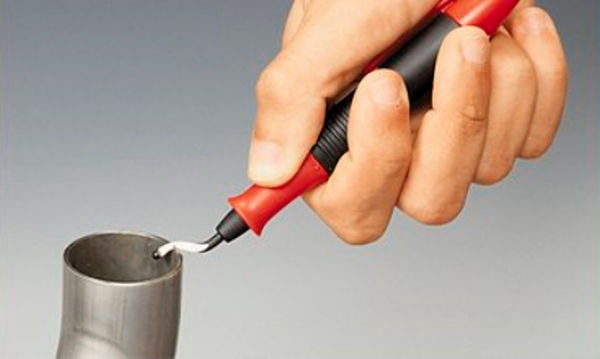
Hand Files - Files come in different shapes, cuts and sizes for various surfaces like flat, round, triangular. Coarse-cut files remove more material while fine-cut creates smooth finishes. It's important to file in one direction only.
Deburring Blades - Rotary blades attach to drills for filed edges in tight spaces. Straight deburring blades are held manually for flat, contoured surfaces.
Abrasive Tools- Sandpaper, emery cloths and stones are used wet or dry. Finer grits create smoother surfaces. Rolled strips are handy for cylindrical parts.
Automated Deburring Tools
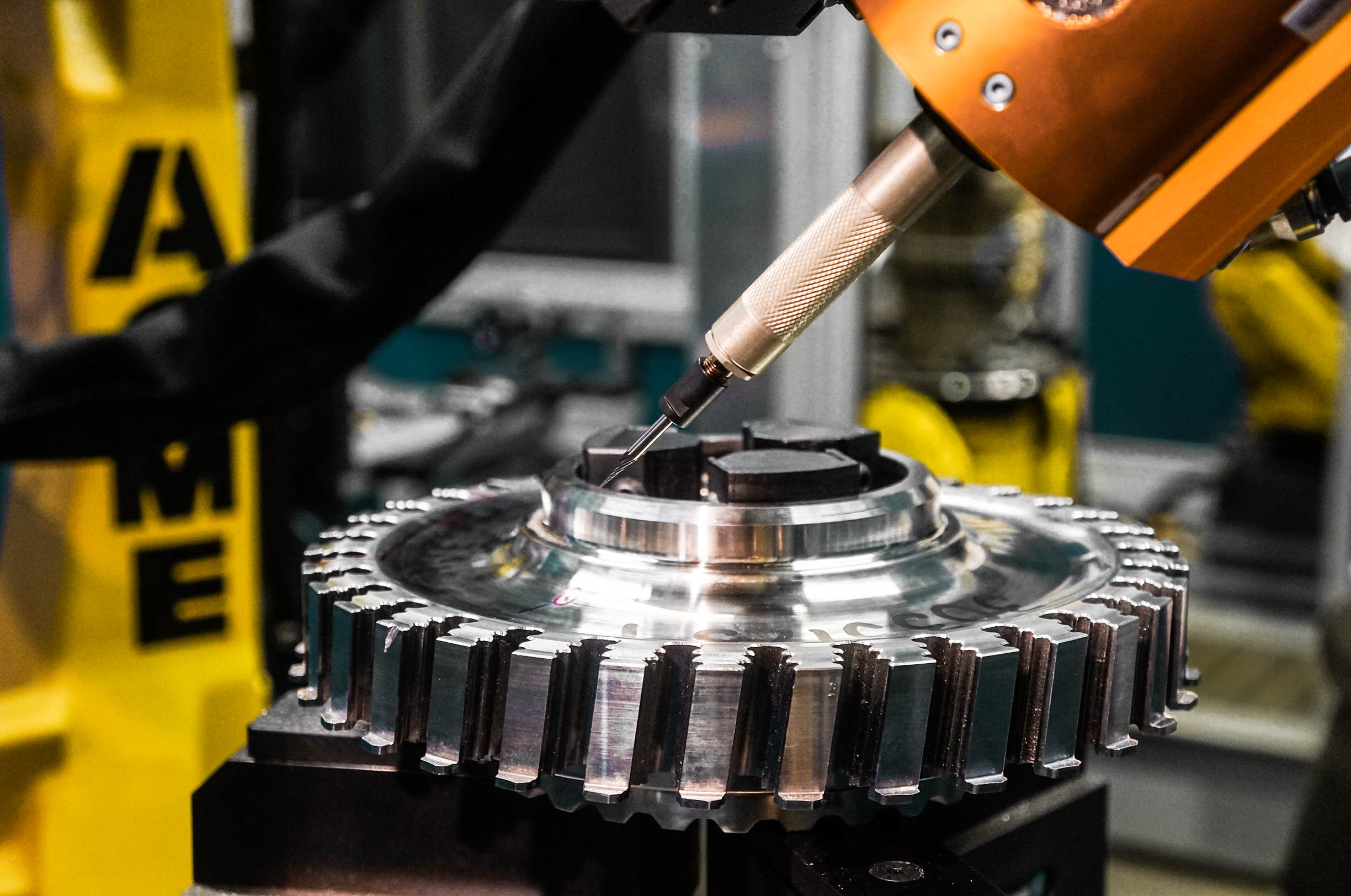
Rotary Tools - Dremel and die grinder type rotary tools use abrasive bits or stones. Low speeds are best for deburring. Always use safety goggles and avoid touching spinning parts.
Specialized Deburring Tools- There are tools designed for specific deburring tasks like inside tight spaces or complex geometries. These get burrs out of hard to reach places.
Choosing the Right Tool
Consider the part material, size of burrs, required smoothness and needed precision. Manual tools work well for small custom jobs while automated tools are best for high volume production.
Using the correct deburring tool makes the job safer and gives excellent results.
Deburring Machines
Introduction to Deburring Machines
Deburring machines automatically remove burrs from large volumes of parts. This high-speed process is essential for mass production industries.
Types of Deburring Machines
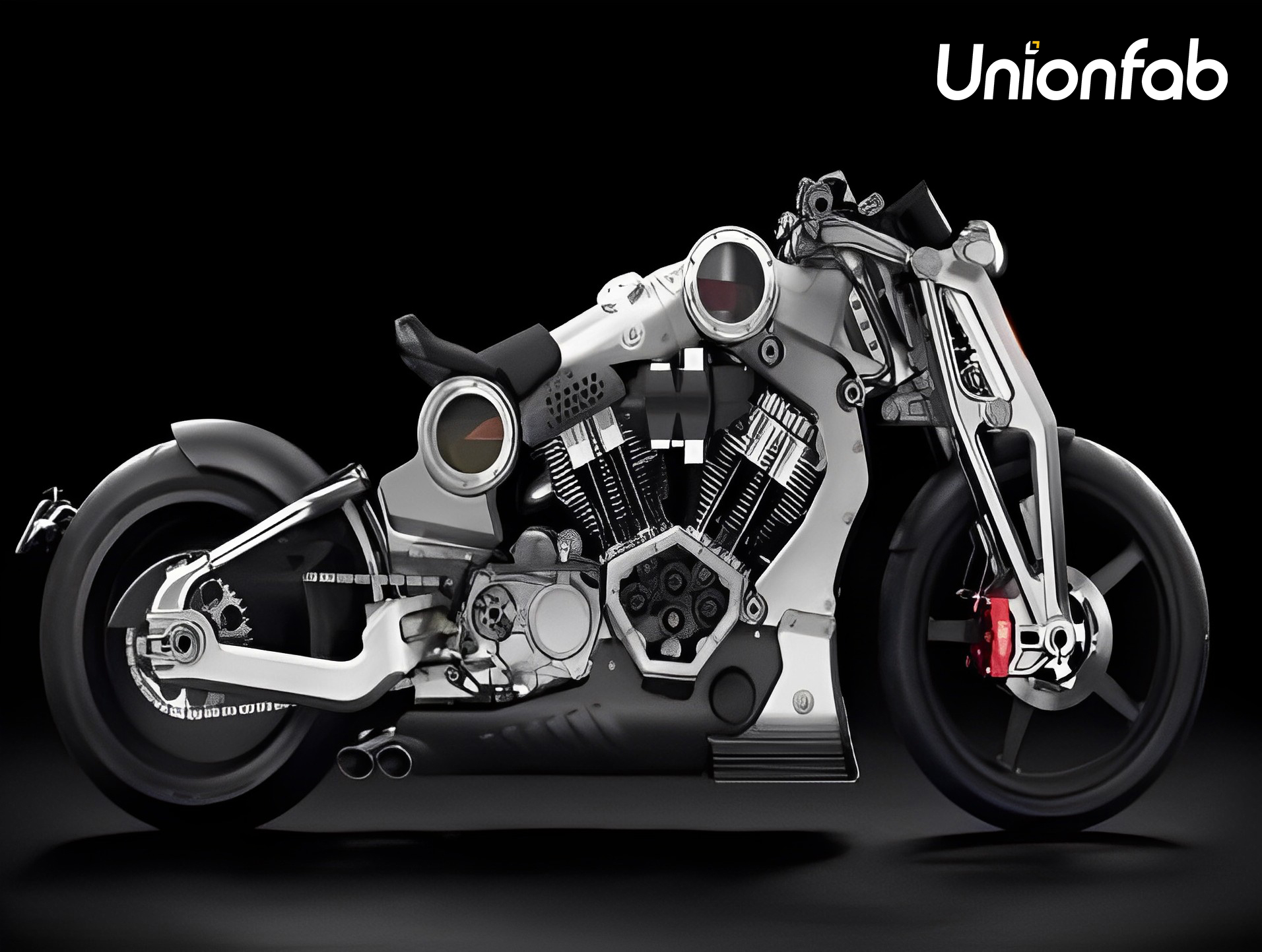
Source: Unionfab
Tumbling Machines - Barrel or vibratory tumbling machines roll or agitate parts with abrasive media to debur efficiently in batches. Effective for larger, simply shaped parts.
Vibratory Deburring Machines - Targeted vibration empowers various industries to debur precisely and quickly. They come in different scales for parts ranging from small to large.
Laser Deburring Machines - High-tech lasers vaporize even microscopic burrs on small intricate parts for electronics, aviation and more. Very fast and accurate.
CNC Deburring Machines - Integrating deburring modules into CNC machining centers lets sensitive burr removal be automated for unmanned operation. Precision and speed.
Selecting the Right Machine
Consider the part's material type, size, production number and complexity. A machine's capabilities, speed and cost-benefit allows choosing the optimal solution for consistent, quality deburring in high volumes.
For most manufacturers, automating with machines improves process control and output.
Applications of Deburring — Industry-Specific Applications
Aerospace
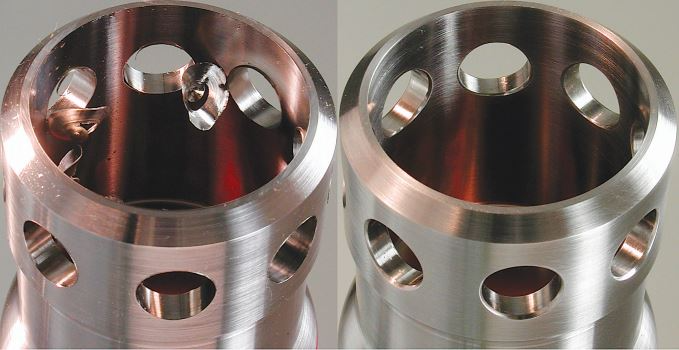
Deburring the metal joints in aircraft engines is critical. Burr-free parts ensure smooth airflow and prevent catastrophic failures at high speeds and temperatures.
Automoti
Sharp burrs on brake assemblies could damage seals or hoses. Deburring brake parts maintains optimum braking performance for safety.
Electronics
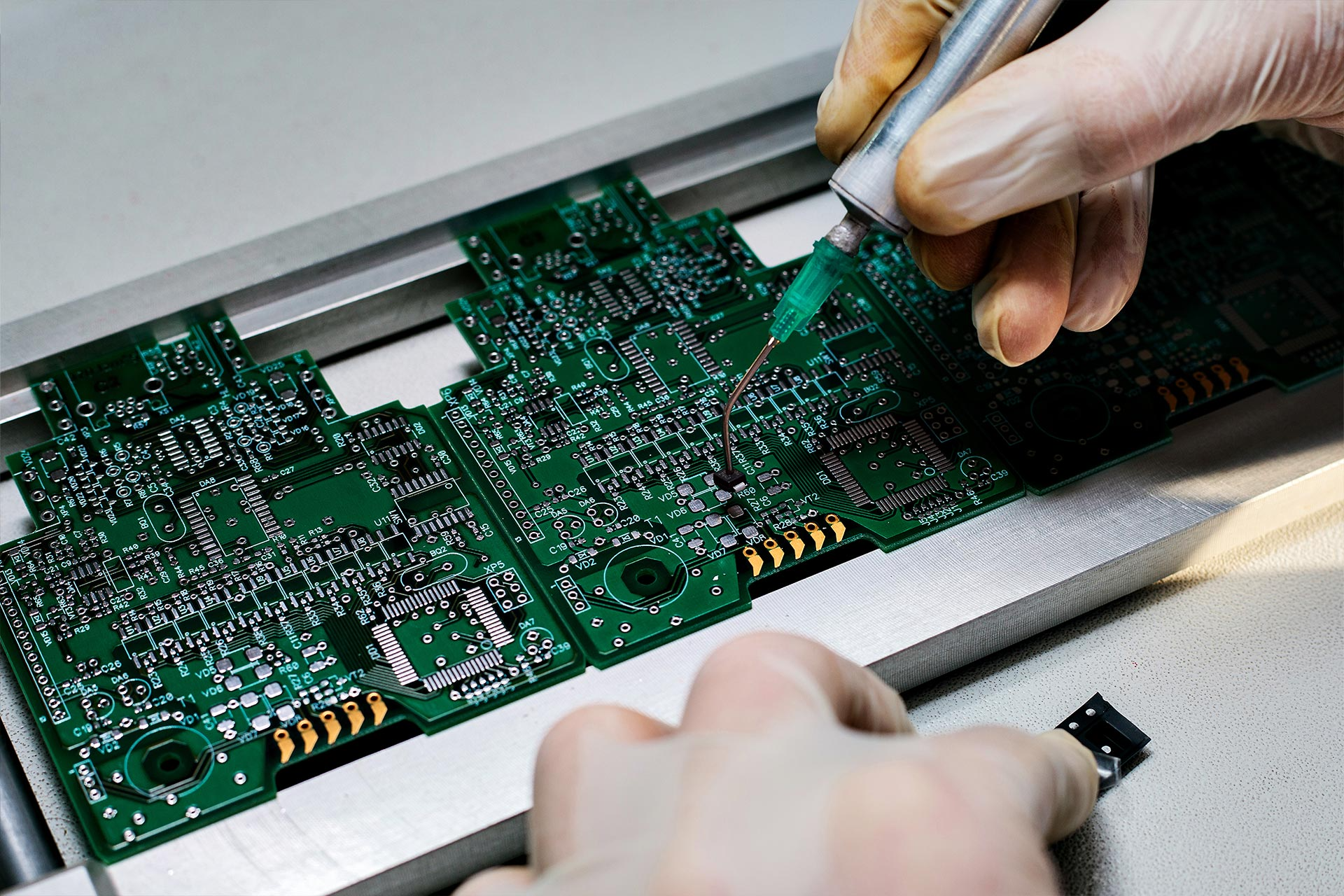
Even microscopic burrs must be removed from circuit boards to avoid short-circuits between closely packed components. This protects against defects.
Medical
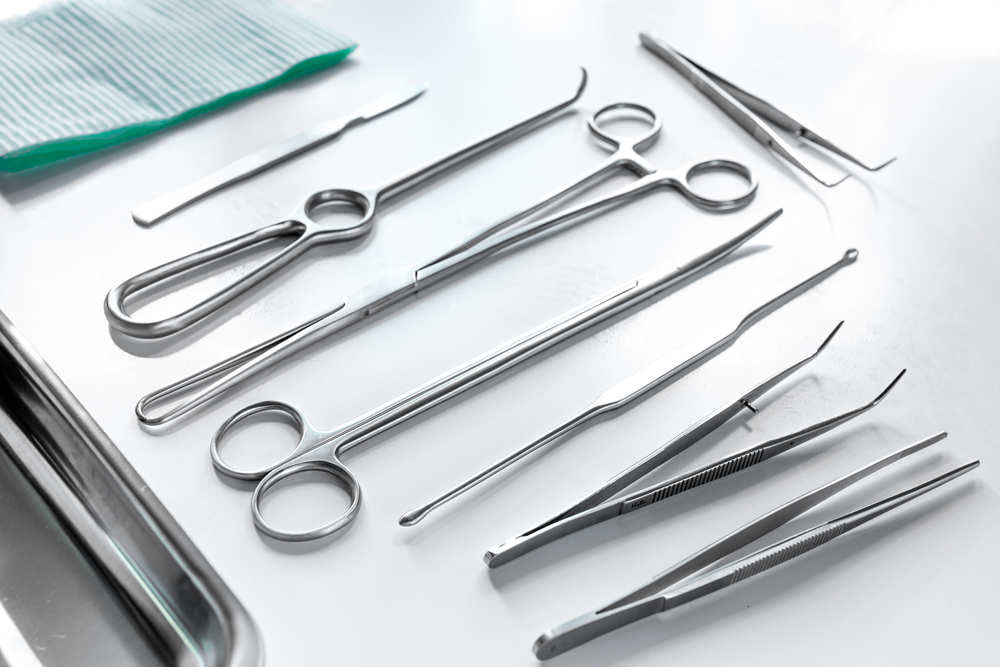
Surgical tools and implants require flawless surfaces to prevent patient wounds. Thorough deburring is essential for medical device functionality and patient well-being.
Appliances
Home appliances contain spun metal components that need burr removal. Deburring blender blades, for example, helps prevent jams and ensures safe,consistent performance.
Across industries, deburring delivers crisp edges that uphold products' integrity, safety, reliability and user experience.
Conclusion
In conclusion, deburring ensures metal, plastic and other machined parts are burr-free through either manual or mechanical methods. Proper deburring has far-reaching quality, safety and financial advantages. It improves dimensional accuracy and assembly efficiency while preventing injuries from sharp edges.
Meet Our Metal Experts at Unionfab
At Unionfab, we don't just machine metal – we engineer excellence. Our metal manufacturing capabilities combine CNC technology with precision finishing techniques to transform your most concepts into reality.
Our Metal Mastery Includes:
5-axis precision machining
Tolerances as tight as ±0.005 mm
Materials: Aluminum, Stainless Steel, Titanium, Exotic Alloys
Precision Metal Finishing: Electropolishing, Bead blasting, Anodizing, Powder coating, Laser etching and marking, …
Get a quote to select your preferred finishing, or contact Unionfab today to discuss your specific metal manufacturing needs. Our experienced team guarantees quality work within your timeline and budget. Let us enhance the look and durability of your products.