PEEK Plastic Material: All You Should Know
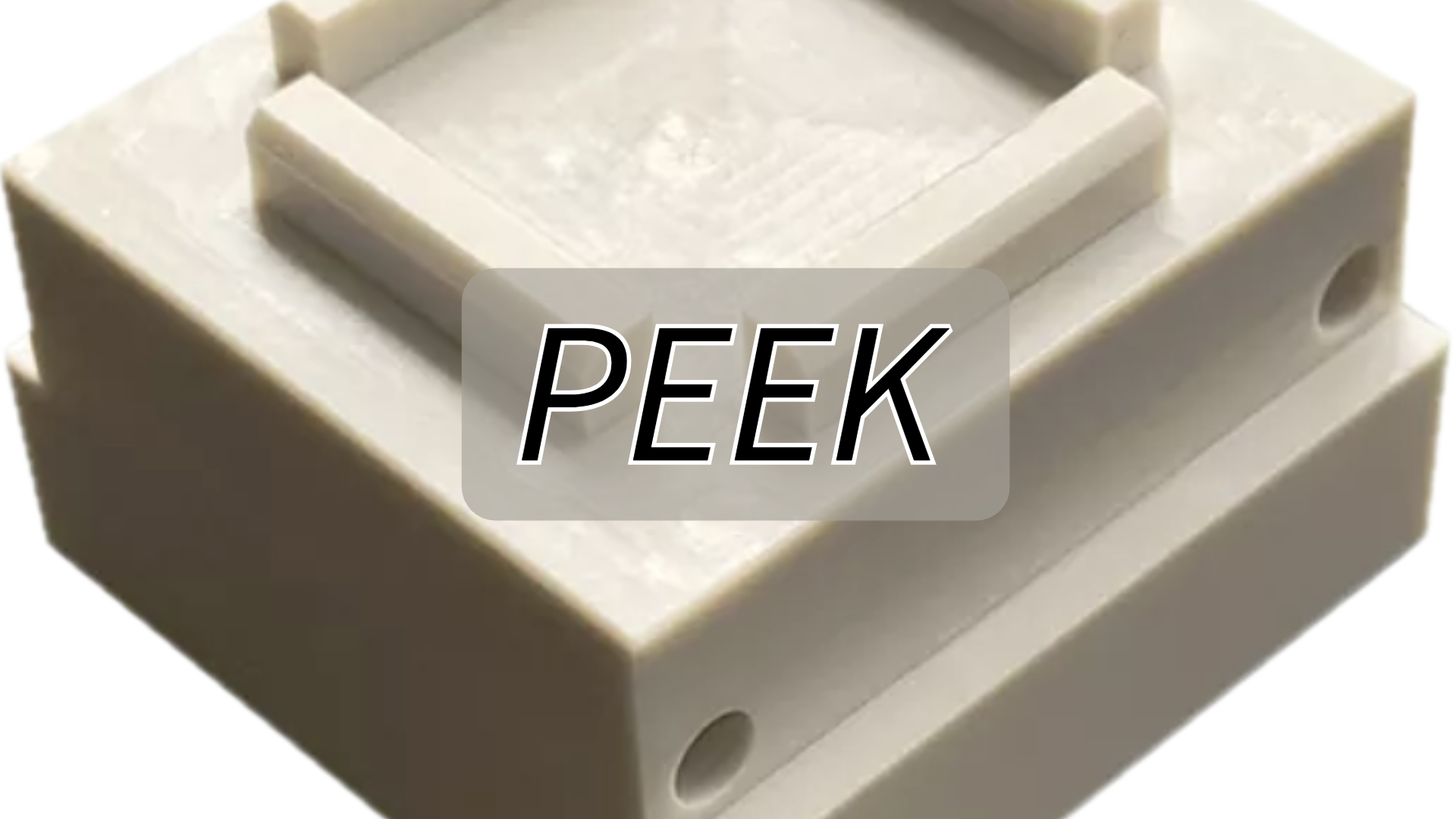
Decode PEEK plastic material from its properties, grades, and prices to its applications, and compare it with similar high-performance materials.
Introduction
Polyether Ether Ketone (PEEK) is a high-performance thermoplastic known for its remarkable strength, temperature resistance, and chemical stability.
Widely used in demanding applications like aerospace, medical devices, and automotive components, PEEK offers a unique blend of properties that make it ideal for environments where traditional materials fall short.
In this article, we’ll explore everything you need to know about PEEK, from its key properties and different grades to its processing options and the unique advantages it offers over other high-performance materials.
Whether you’re considering PEEK for an industrial application or simply want to learn more about this remarkable material, this guide will provide a comprehensive understanding of what makes PEEK one of the most sought-after thermoplastics in the market today.
Definition of PEEK
PEEK (Polyether Ether Ketone) is a high-performance thermoplastic polymer belonging to the polyaryletherketone (PAEK) family. It is known for its exceptional combination of properties that include high mechanical strength, excellent chemical resistance, and thermal stability, even at temperatures up to 260°C (500°F). PEEK’s unique attributes make it suitable for demanding applications in industries such as aerospace, automotive, medical, and oil and gas.
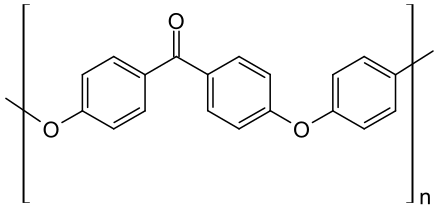
Source: wikipedia.org
PEEK Plastic Properties
Physical Property
Property | Description |
---|---|
Specific Gravity | 1.30 g/cm³ |
Water Absorption (24-hour Immersion) | 0.1% to 0.5% |
Dimensional Stability | Maintains shape and size under thermal and mechanical stress |
Electrical Property
Property | Description |
---|---|
Dielectric Strength | 17-25 kV/mm |
Dielectric Constant | 3.2-3.5 |
Volume Resistivity | 10^16 ohm-cm |
Mechanical Property
Property | Description |
---|---|
Tensile Strength | 90-100 MPa (13,000 to 14,500 psi) |
Tensile Modulus | 3.6-4.1 GPa |
Tensile Elongation | 20-40% |
Flexural Strength | 150-170 MPa |
Flexural Modulus | 3.7-4.0 GPa |
Compressive Strength | 110-120 MPa |
Hardness | Shore D 85 |
Izod Impact (Notched) | 5-15 kJ/m² |
Wear Resistance | Excellent, with a low coefficient of friction |
Thermal Property
Property | Description |
---|---|
Melting Point | 343°C (649°F) |
Glass Transition Temperature (Tg) | 143°C (289°F) |
Continuous Use Temperature | Up to 250°C (482°F) |
Thermal Conductivity | Moderate |
Thermal Expansion | Low coefficient |
Other Properties
Property | Description |
---|---|
Chemical Resistance | Resistant to strong acids, bases, and organic solvents |
Flame Retardance | Meets UL 94 V-0 Standards |
Biocompatibility | FDA-approved for medical implants |
Radiation Resistance | High resistance to gamma rays and X-rays |
Grades and Variants of PEEK and Their Comparison
Grades and Variants | Key Properties | Applications | Notes |
---|---|---|---|
Unfilled PEEK | Standard PEEK with balanced properties. | General industrial use, medical devices. | High purity, good for general-purpose use. |
Glass-filled PEEK | 30% glass fiber reinforcement, increased stiffness and dimensional stability. | Structural components, electronics. | Improved rigidity but slightly reduced impact resistance. |
Carbon-filled PEEK | 30% carbon fiber reinforcement, superior strength and wear resistance. | Bearings, bushings, aerospace parts. | Higher tensile strength and lower coefficient of friction. |
Medical-grade PEEK | Biocompatible, sterilization-resistant. | Implants, surgical instruments. | Certified for long-term human contact, FDA approved. |
Lubricated PEEK | Contains internal lubricants for enhanced wear performance. | Seals, gears, sliding components. | Reduces friction and improves wear resistance, especially for moving parts. |
Colorable PEEK | Customizable in various colors. | Consumer products, visible components. | Maintains PEEK properties while adding aesthetic flexibility. |
Conductive PEEK | Filled with conductive materials (e.g., carbon) to improve electrical conductivity. | Electronics, EMI shielding. | Balances electrical performance with mechanical integrity. |
Processing Options
PEEK (Polyether Ether Ketone) can be processed using various methods depending on the application requirements. Here’s an overview of the primary processing options:
1. Injection Molding
Process Overview: PEEK pellets are melted and injected into a mold cavity to produce complex shapes with high precision. It is the most common method for mass production of PEEK parts.
Advantages: Produces high-precision components with excellent surface finish and tight tolerances. Suitable for producing large volumes.
Applications: Automotive parts, medical components, and electronic housings.
2. Extrusion
Process Overview: PEEK is melted and forced through a die to create continuous profiles like rods, sheets, and films.
Advantages: Ideal for producing semi-finished products like bars and tubes that can be further machined.
Applications: Pipes, insulation coatings, and sheets for further machining.
3. Compression Molding
Process Overview: PEEK powder is placed into a heated mold and compressed under high pressure to form solid components.
Advantages: Suitable for producing thick-walled or large components that are difficult to produce using injection molding.
Applications: Structural components, heavy-duty industrial parts.
4. 3D Printing (Additive Manufacturing)
Process Overview: PEEK is printed using Fused Filament Fabrication (FFF) or Selective Laser Sintering (SLS). In FFF, a filament is extruded layer by layer; in SLS, powdered PEEK is sintered with a laser.
Advantages: Enables the production of complex geometries and customized parts with reduced material waste.
Applications: Prototyping, customized medical implants, aerospace components.
5. Machining
Process Overview: PEEK sheets, rods, or tubes produced via extrusion or compression molding are machined using CNC techniques to achieve high-precision parts.
Advantages: Allows for the creation of parts with extremely tight tolerances and complex designs.
Applications: Gears, bushings, medical devices.
Uionfab’s Service
Unionfab provides a wide range of manufacturing services, including 3D printing, CNC machining, Casting, and Injection Molding, catering to rapid prototyping and on-demand production.
With a diverse selection of materials, fast turnaround times, and cost-effective solutions, Unionfab ensures high-quality results for all your manufacturing needs.
If you're interested in manufacturing with PEEK plastics or other materials, feel free to contact us.
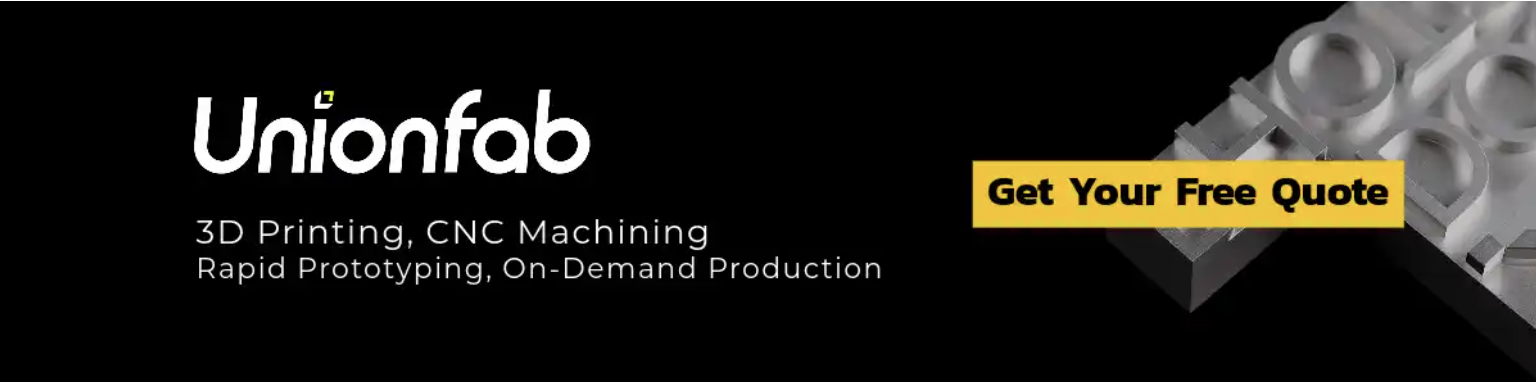
Challenges and Limitations
1. High Processing Temperatures
PEEK's need for high processing temperatures close to 400°C often leads to challenges in maintaining material integrity, which is a universal concern in industries using PEEK.
2. Cost Efficiency
The high cost of PEEK, both in terms of raw material and the required high-spec processing equipment, is a significant consideration for any project, making it a common issue in budgeting and material selection.
3. Machinability
Due to its toughness and high melting point, PEEK can be difficult to machine, making this a frequent challenge in manufacturing settings where precise component specifications are needed.
4. Moisture Absorption
While PEEK has good resistance to moisture, its slight absorption can impact applications requiring stringent dimensional and mechanical stability, making it a notable point in engineering applications.
5. Weld Line and Mold Shrinkage
These are typical issues in the injection molding of many polymers, including PEEK, especially in complex geometries or large molded parts.
6. Chemical Resistance
Although PEEK is resistant to many chemicals, its vulnerability to strong acids and halogens can be problematic in certain chemical processing environments.
7. Thermal Expansion
The mismatch in thermal expansion rates between PEEK and other materials can cause issues in mixed-material assemblies, especially where precise engineering tolerances are necessary.
8. Recycling and Sustainability
The difficulties in recycling PEEK stem from its high melting point and potential for degradation, posing environmental and economic challenges.
Comparison Among 5 Different PEEK Brands
1. Victrex
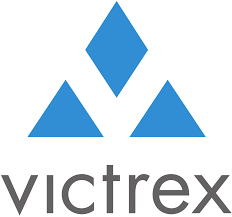
Properties: Offers a wide range of PEEK grades, including high-performance, medical grade, and food contact grades.
Applications: Widely used in aerospace, automotive, electronics, and healthcare.
Unique Offerings: Known for Victrex APTIV film, a high-performance thin film product.
Global Reach: One of the most recognized and widely available PEEK brands.
2. Solvay
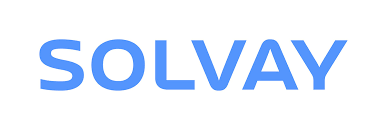
Properties: Provides PEEK under the KetaSpire and AvaSpire lines, with excellent mechanical and chemical resistance properties.
Applications: Suitable for healthcare, automotive, aerospace, and industrial applications.
Unique Offerings: AvaSpire is a blend of PEEK and PAEK, offering enhanced flexibility and colors.
Global Reach: Strong distribution network and regarded for innovative formulations.
3. Evonik
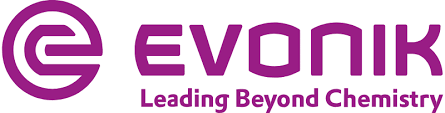
Properties: Their VESTAKEEP brand is known for its high purity, making it ideal for demanding applications.
Applications: Focuses on medical implants, automotive, and industrial machinery.
Unique Offerings: Offers a line of PEEK for 3D printing applications.
Global Reach: Well-established with a good track record in high-performance plastics.
4. Ensinger
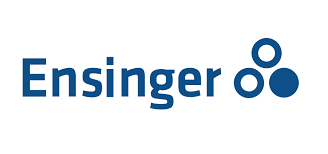
Properties: TECAPEEK is recognized for its high mechanical strength and resistance to high temperatures.
Applications: Used in industrial, medical, and food processing applications.
Unique Offerings: Available in various forms including stock shapes and custom cast parts.
Global Reach: Ensinger products are known for quality and versatility in processing.
5. Röchling
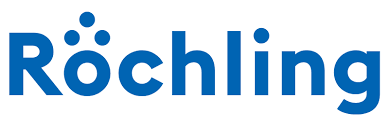
Properties: SustaPEEK offers good mechanical and thermal properties.
Applications: Ideal for mechanical engineering, medical technology, and the food industry.
Unique Offerings: Offers a broad range of sizes and shapes for diverse industrial needs.
Global Reach: Known for tailored solutions and specific industry focus.
Comparison of PEEK with Similar Materials
PEEK vs. Ultem
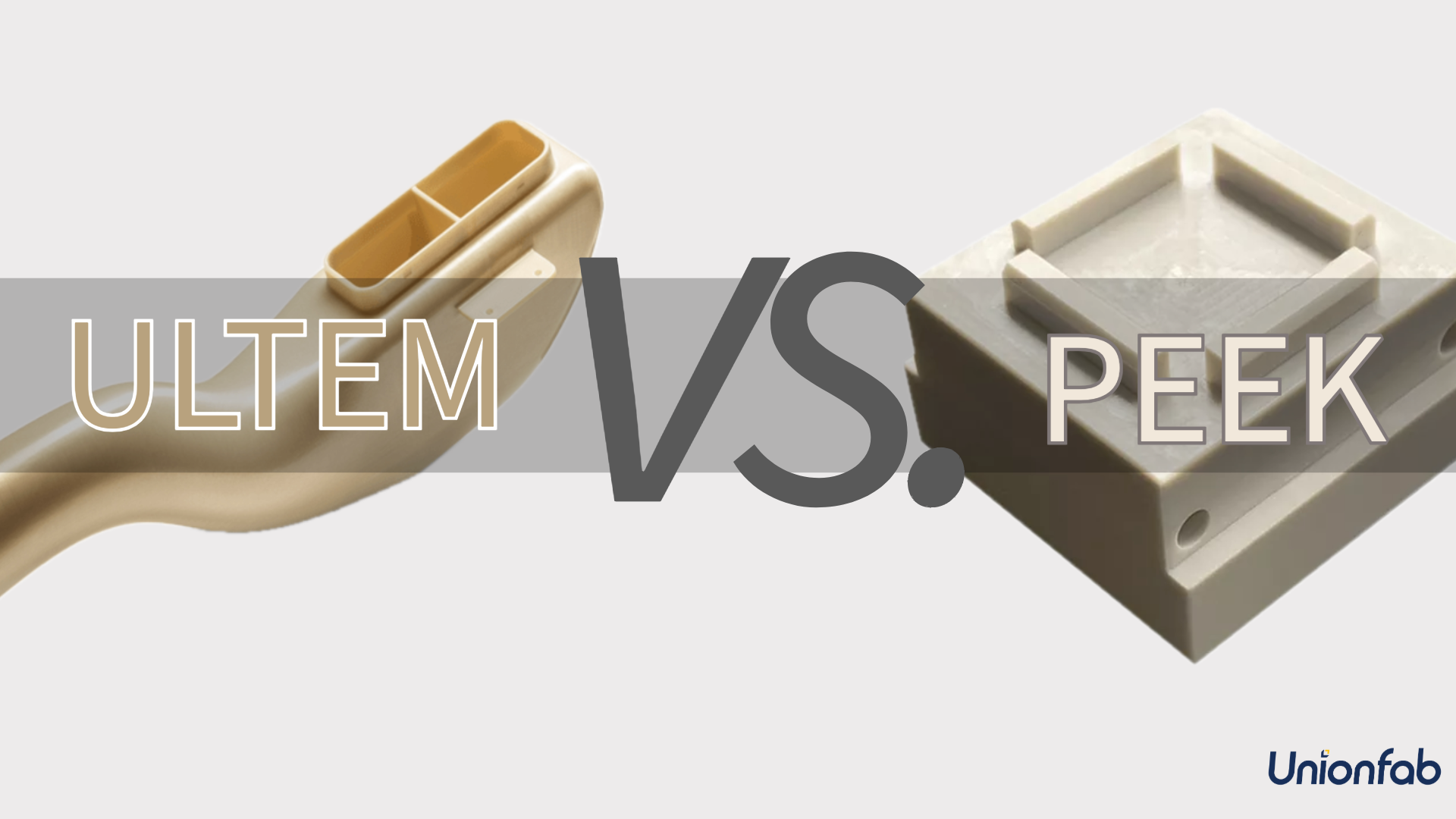
Thermal Stability
PEEK: Even higher heat resistance, with a continuous use temperature of up to 260°C.
ULTEM: High glass transition temperature (~217°C) but lower than PEEK.
Mechanical Strength
PEEK: Superior mechanical properties, especially in demanding environments.
ULTEM: High tensile strength and stiffness but generally lower than PEEK.
Chemical Resistance
PEEK: Outstanding chemical resistance, even in harsh environments including strong acids, bases, and solvents.
ULTEM: Good resistance to many chemicals, but vulnerable to strong acids and bases.
Cost
PEEK: Significantly more expensive, typically ranging from $500 to $1,000 per kg, depending on the grade.
ULTEM: Typically costs $100 to $250 per kg, depending on the grade.
Flame Retardancy
PEEK: Also flame retardant, but PEEK offers even higher levels of safety in extreme conditions.
ULTEM: Naturally flame retardant with low smoke and toxicity.
Dimensional Stability
PEEK: Exceptional dimensional stability even at very high temperatures and under heavy loads.
ULTEM: Excellent stability, but can be slightly less stable than PEEK under very high temperatures.
Applications
PEEK: Ideal for highly demanding environments like oil & gas, aerospace, and medical implants due to its superior properties.
ULTEM: Used in aerospace, automotive, electronics, and medical applications where high strength and moderate heat resistance are needed.
Processability
PEEK: More challenging to process due to its higher melting point and required processing temperatures.
ULTEM: Easier to process in 3D printing (FDM) and injection molding.
PEEK vs. PEKK
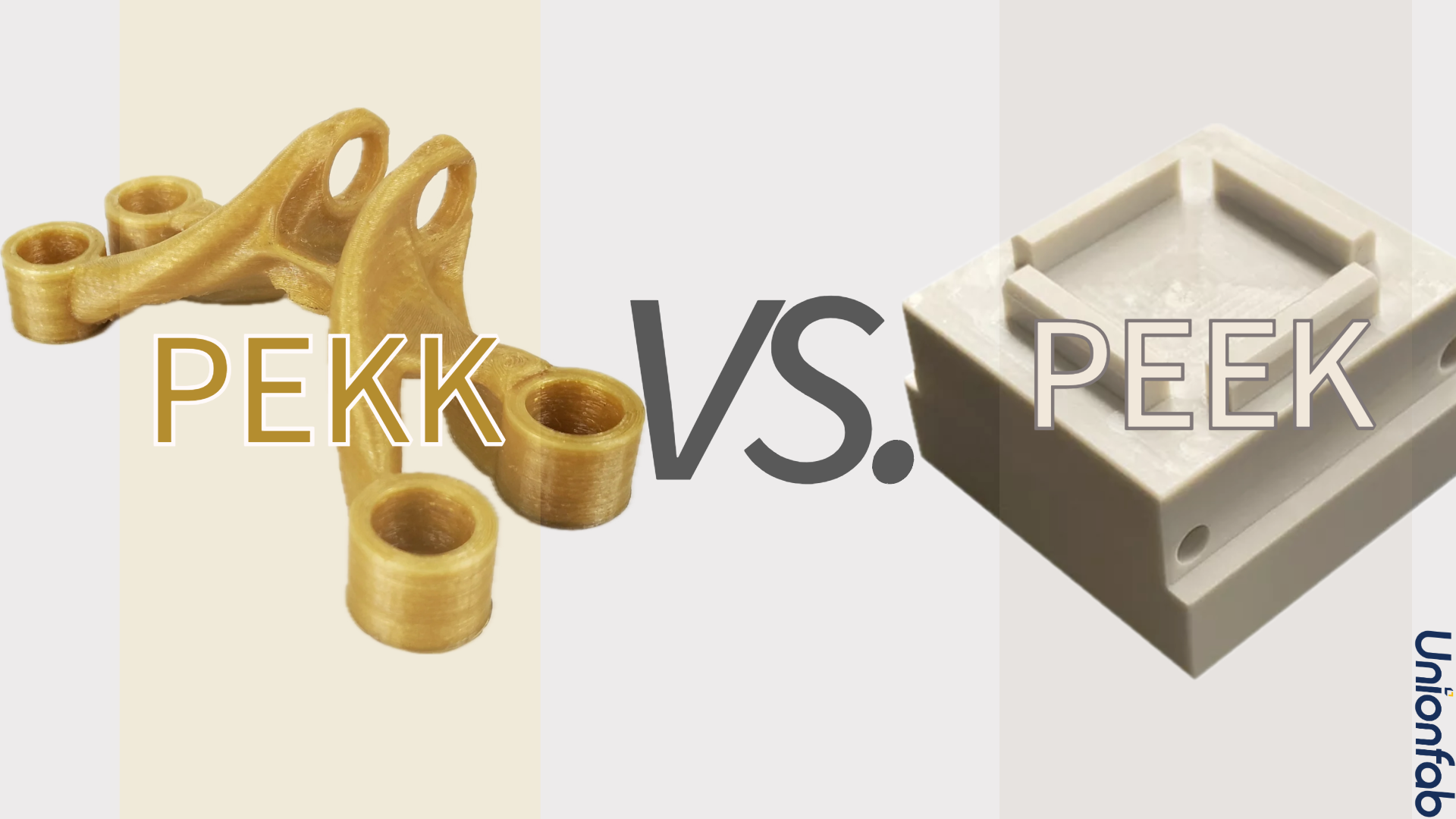
Thermal Stability
PEEK: Offers a high continuous use temperature up to 260°C.
PEKK: Similar to PEEK, PEKK can operate in high temperatures but has a slightly higher glass transition temperature, which can offer improved performance in certain high-temperature applications.
Mechanical Strength
PEEK: Known for its excellent tensile strength and stiffness, PEEK is suitable for demanding structural applications.
PEKK: Generally offers comparable or slightly superior mechanical properties, especially under specific conditions like elevated temperatures or dynamic stress environments.
Chemical Resistance
PEEK: Exhibits outstanding resistance to a wide range of chemicals, including strong acids, bases, and solvents.
PEKK: Provides chemical resistance similar to PEEK but with variations depending on the type of PEKK (as there are different types like PEKK-A, PEKK-C, and PEKK-T which have different ratios of terephthaloyl and isophthaloyl groups).
Flame Retardancy and Smoke Emission
PEEK: Flame retardant with low smoke and toxicity.
PEKK: Also flame retardant, and some grades of PEKK are specifically optimized to produce even lower smoke and gas emissions during combustion.
Dimensional Stability
PEEK: Provides excellent dimensional stability due to its semi-crystalline nature, which helps maintain properties over a wide range of temperatures and mechanical stresses.
PEKK: Offers slightly better dimensional stability in high-temperature applications due to its higher crystallinity, which can be an advantage in precision manufacturing sectors.
Processing and Manufacturability
PEEK: Can be processed using conventional methods like injection molding, extrusion, and machining. It requires high processing temperatures.
PEKK: Often considered to be more versatile in processing, especially in additive manufacturing (3D printing). PEKK can crystallize more rapidly, allowing better dimensional stability during printing.
Cost and Availability
PEEK: Widely available and extensively used, but it is expensive.
PEKK: Typically even more costly than PEEK due to its specialized production process and slightly less widespread use.
Applications
PEEK: Commonly used in aerospace, automotive, medical implants, and electronics for its robust performance.
PEKK: Finding increasing use in aerospace and automotive applications, particularly in high-performance parts that benefit from its high thermal stability and excellent mechanical properties. It's also growing in popularity in additive manufacturing applications.
PEEK vs. PPSU
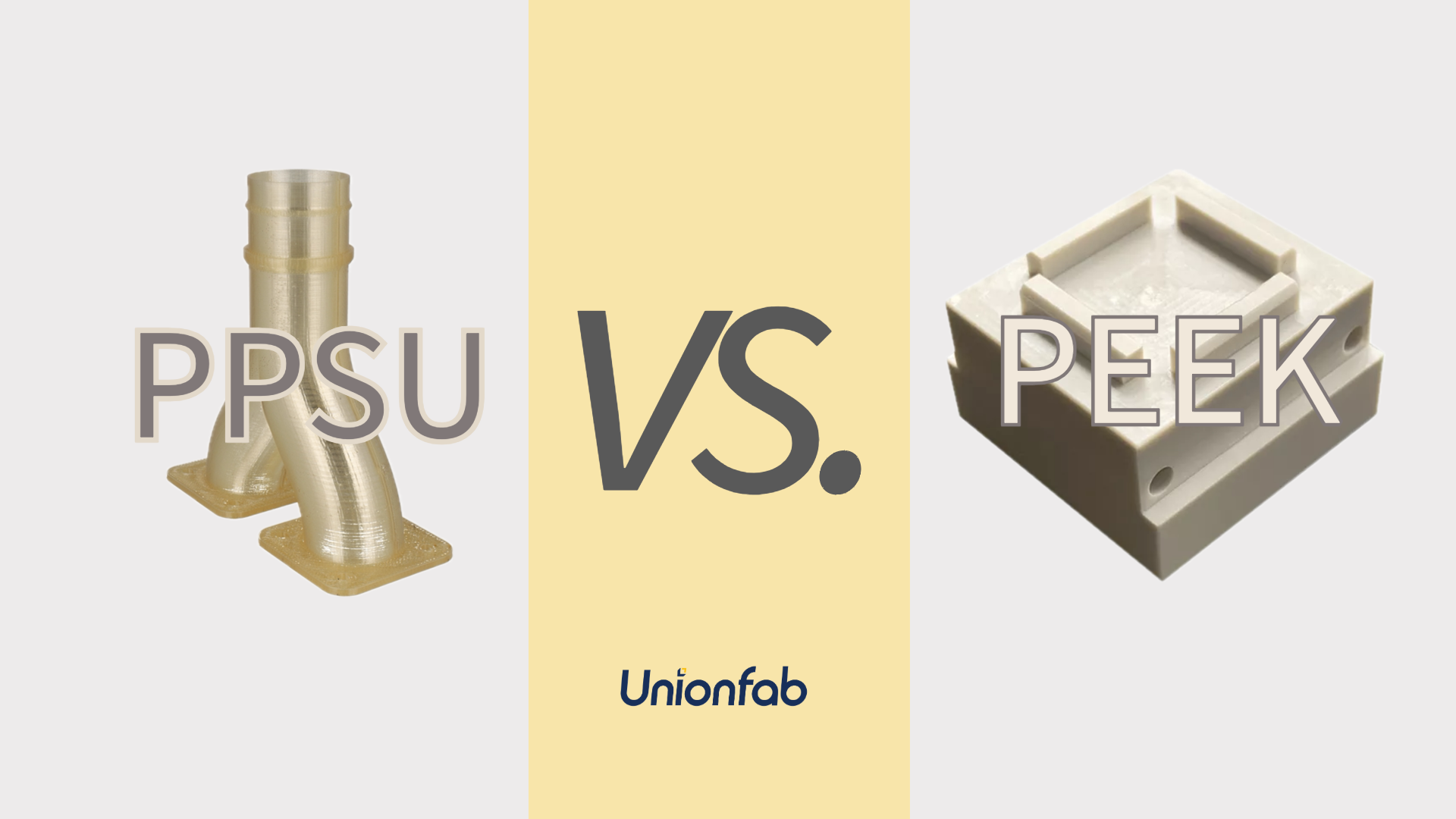
Thermal Stability
PEEK: Has a continuous service temperature of up to 260°C and exhibits excellent thermal stability, making it suitable for high-temperature applications.
PPSU: Features a lower continuous use temperature, typically around 180°C. It has good thermal stability but doesn't match the high-temperature capabilities of PEEK.
Mechanical Strength
PEEK: Offers superior mechanical strength, stiffness, and durability. It is well-suited for structural applications where high load-bearing capacity is essential.
PPSU: While strong and tough, PPSU generally has lower mechanical strength compared to PEEK. However, it excels in impact strength and toughness, even at elevated temperatures.
Chemical Resistance
PEEK: Provides outstanding chemical resistance across a broad range of chemicals including hydrocarbons, acids, and solvents.
PPSU: Also offers excellent chemical resistance, particularly to alkalis and complex hydrocarbons, but may be more susceptible to some solvents than PEEK.
Flame Retardancy and Smoke Emission
PEEK: Is inherently flame retardant with low smoke and toxic gas emissions upon combustion.
PPSU: Also flame retardant and emits low levels of smoke and toxic gases. It is frequently used in applications requiring stringent fire safety standards.
Dimensional Stability
PEEK: Exhibits exceptional dimensional stability due to its semi-crystalline nature, maintaining properties over a wide temperature range and under mechanical stress.
PPSU: Although slightly less dimensionally stable than PEEK at high temperatures, PPSU maintains excellent stability and is known for its high resistance to creep.
Biocompatibility
PEEK: Highly biocompatible and often used in medical implant applications. It is resistant to sterilization methods like autoclaving.
PPSU: Extremely biocompatible and suitable for medical applications, including those requiring repeated sterilization. It resists common hospital cleaners and disinfectants well.
Processing and Manufacturability
PEEK: Can be challenging to process due to its high melting point; typically requires specialized equipment for molding and extrusion.
PPSU: Easier to process than PEEK, with a lower melting temperature. It can be more readily molded and extruded, making it suitable for complex shapes and thin-walled components.
Cost and Availability
PEEK: Tends to be very expensive, reflecting its superior performance properties and processing challenges.
PPSU: Generally less costly than PEEK, making it a more economical choice for applications that can trade off some mechanical and thermal performance for cost savings.
Applications
Aerospace
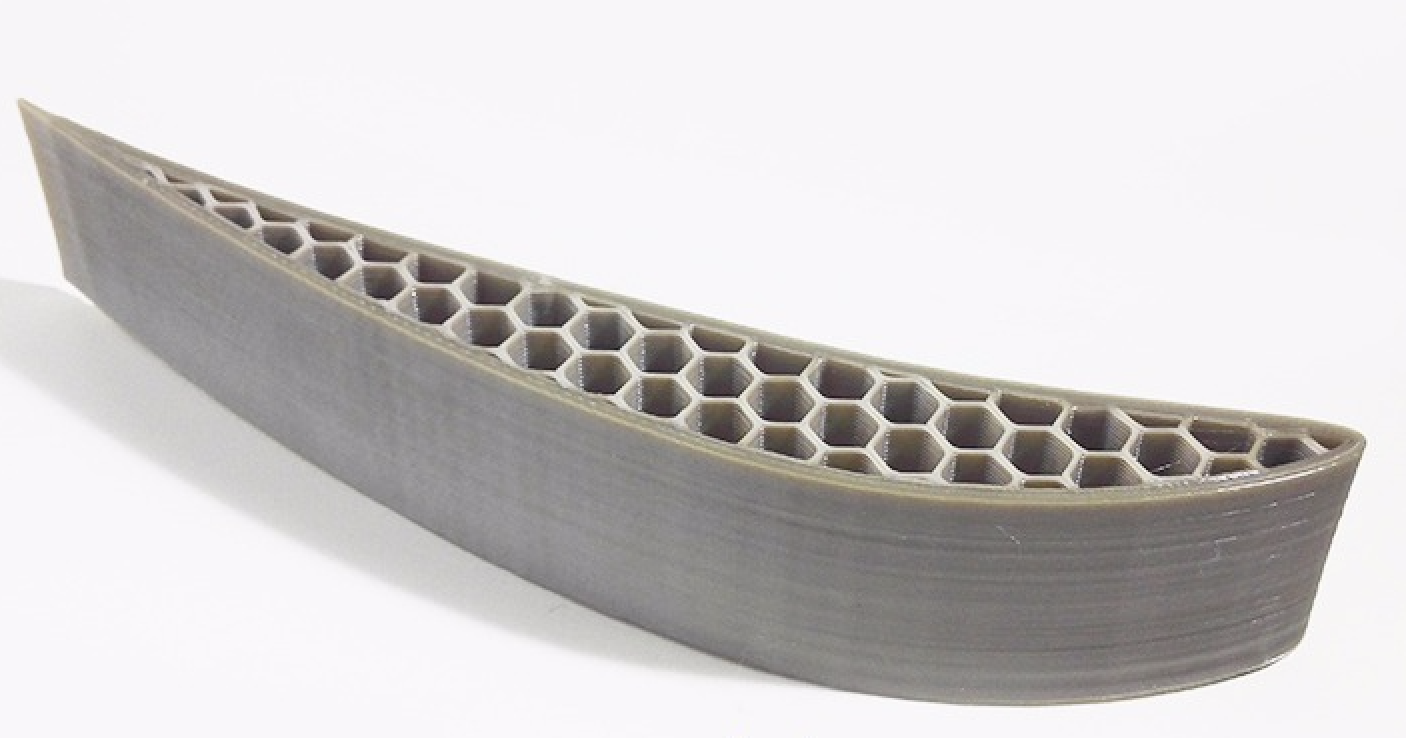
Source: roboze.com
Components: PEEK is used for components that need to withstand extreme conditions such as high temperatures and mechanical stress. Examples include seals, bushings, bearings, and compressor parts.
Weight Reduction: Its lightweight nature allows for weight savings in aircraft, contributing to fuel efficiency and overall performance enhancements.
Automotive
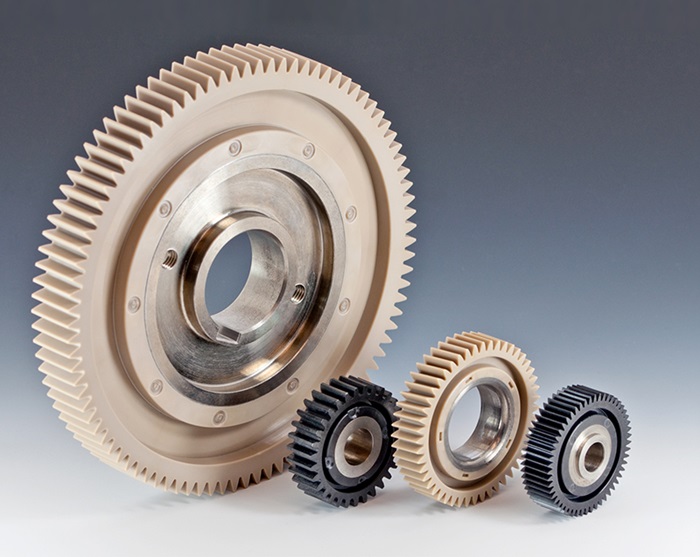
Source: peekchina.com
Under the Hood Components: Due to its heat resistance, PEEK is ideal for parts near the engine such as connectors, pumps, and seals.
Electrical Components: Its excellent insulating properties make it suitable for electrical connectors, sensors, and actuators.
Medical Devices
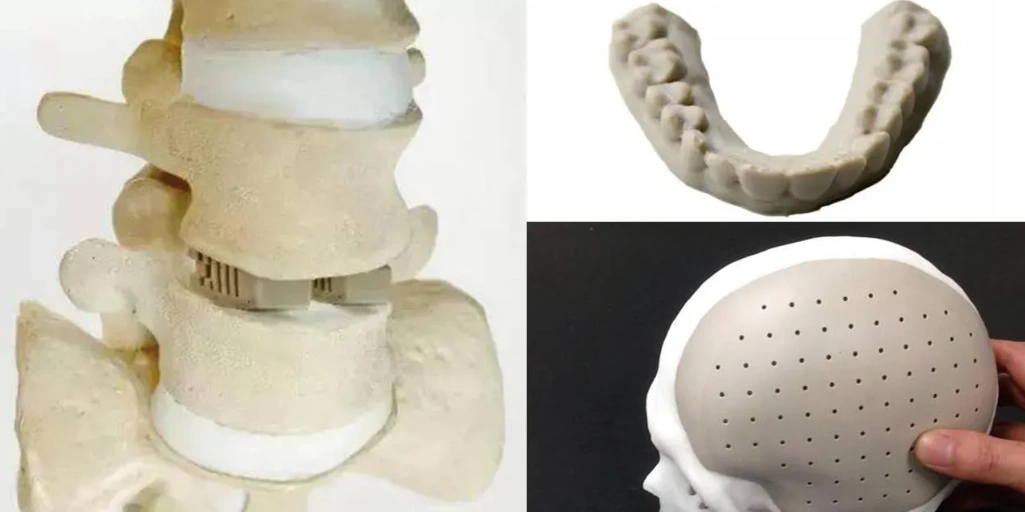
Source: superbmaterials.com
Implants: PEEK is widely used for medical implants such as spinal fusion devices and hip replacements because of its biocompatibility and similar stiffness to bone.
Surgical Instruments: Its resistance to sterilization processes makes it ideal for reusable medical tools and devices.
Electronics
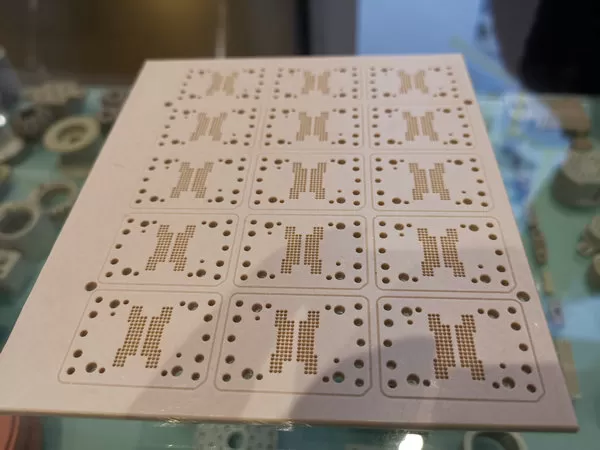
Source: peekchina.com
Insulators: PEEK's electrical insulation properties are utilized for connectors and other components in electronic devices.
Semiconductor Manufacturing: It is used in components that must endure high temperatures and aggressive chemicals during manufacturing processes.
Oil and Gas
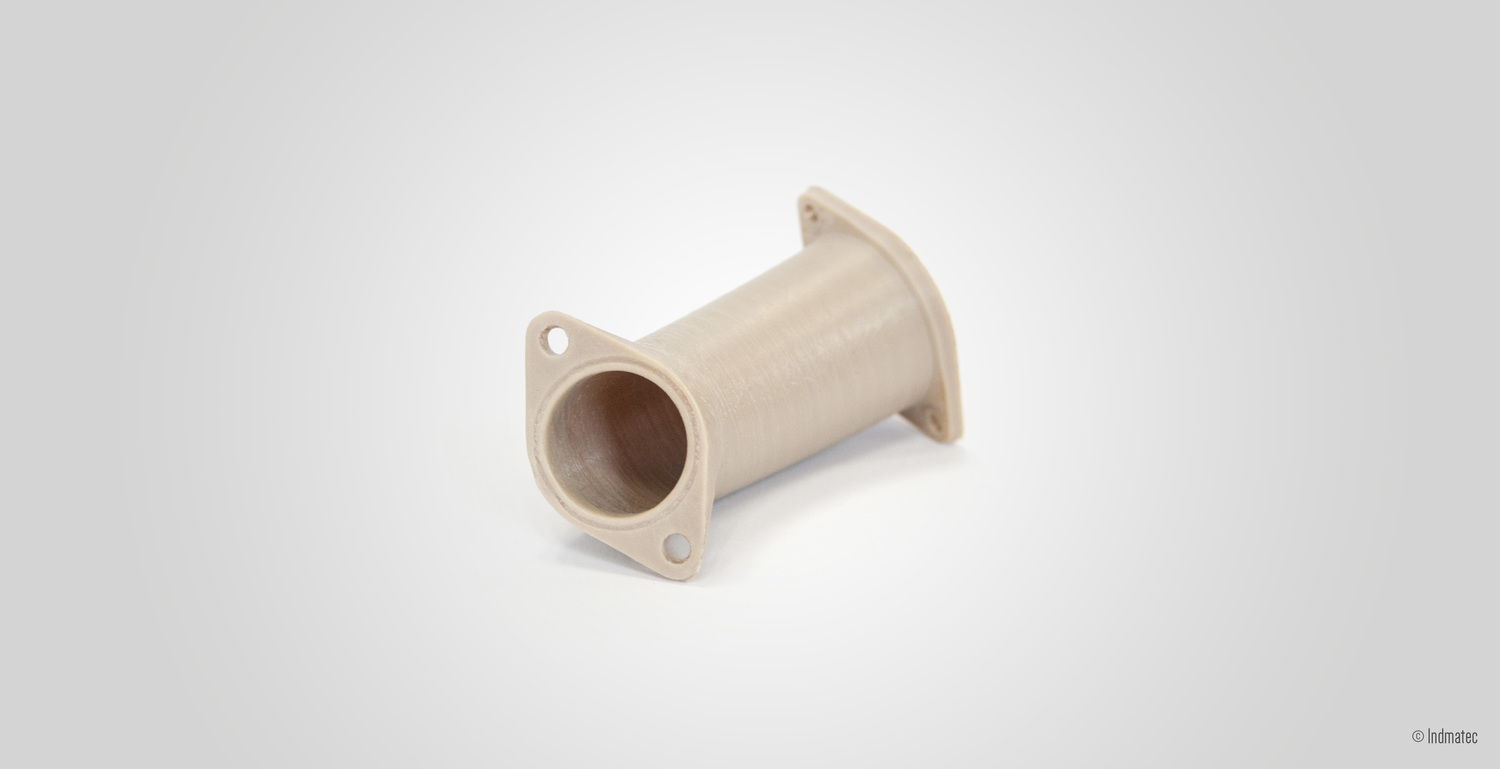
Source: 3printr.com
Seals and Gaskets: PEEK is used in seals, gaskets, and back-up rings that need to resist extreme pressures and corrosive environments found in oil and gas extraction and processing.
Compressor Valves: Its durability and resistance to wear make it suitable for high-performance parts like compressor valves.
Industrial Machinery
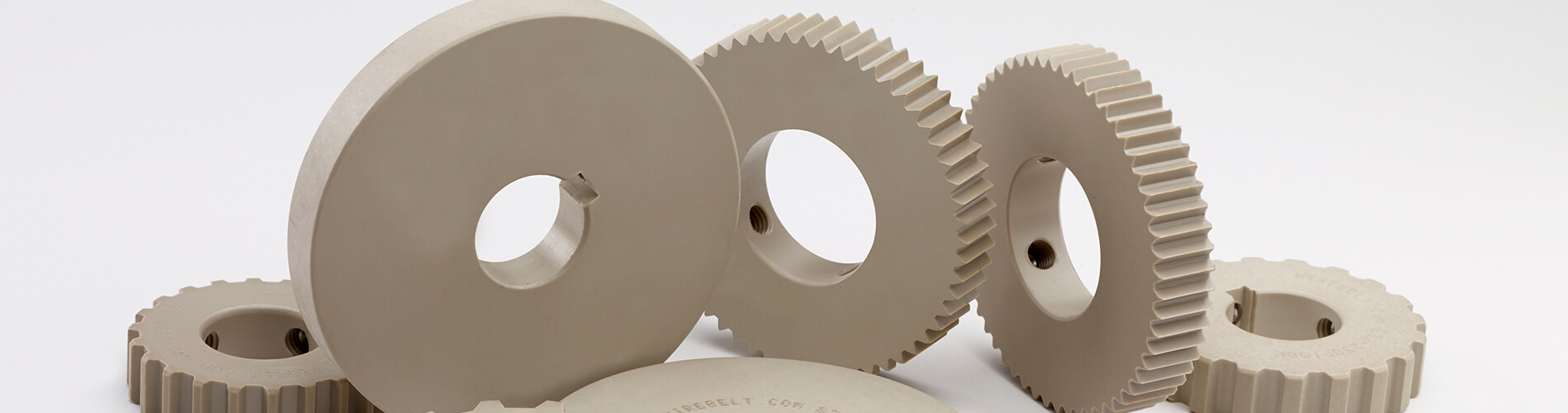
Source: wirebelt.co.uk
Gears and Bearings: PEEK is employed in various industrial machinery applications where high strength, low friction, and resistance to chemicals are required.
Pump and Valve Components: Due to its excellent mechanical properties and stability, PEEK is used in components that encounter harsh operating conditions.
Food Processing
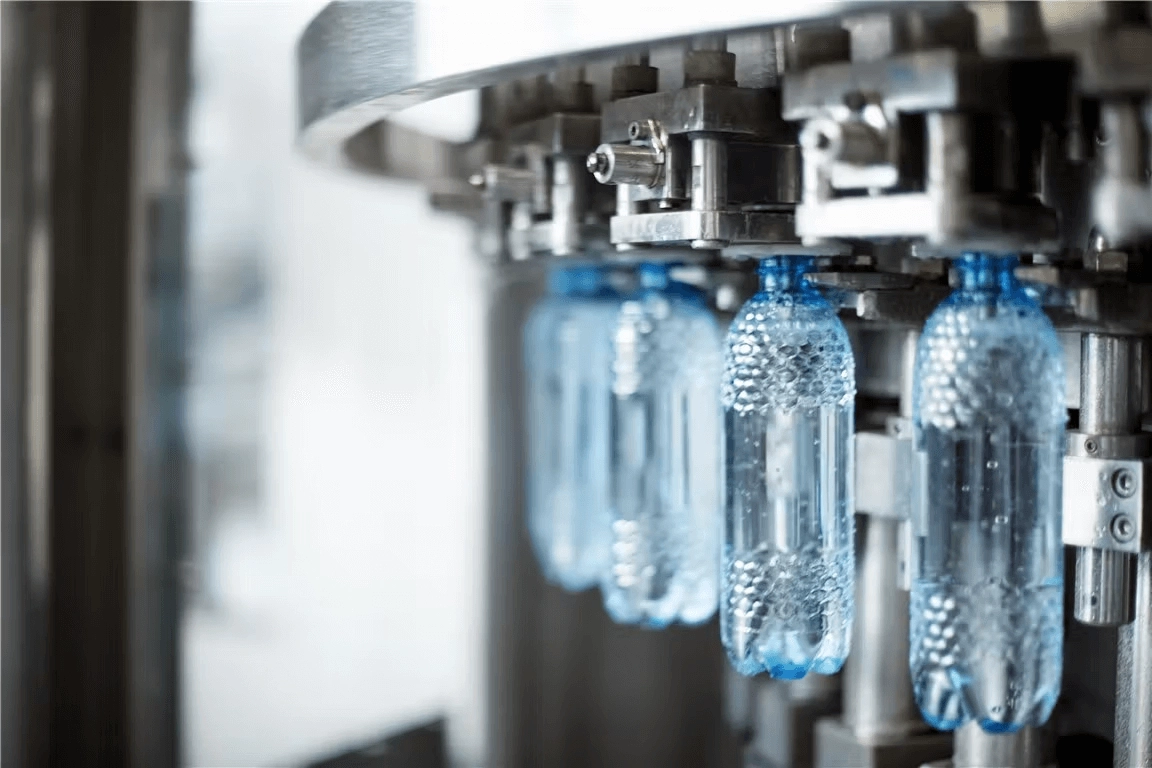
Source: junhuapeek.com
Equipment Components: PEEK's ability to withstand high temperatures and aggressive cleaning agents makes it suitable for food processing equipment components that require frequent sterilization.
Conclusion
PEEK (Polyether ether ketone) is a premier high-performance thermoplastic, valued across various industries for its exceptional mechanical strength, thermal stability, and chemical resistance.
Despite its higher cost, PEEK's durability justifies its selection, especially in critical applications where failure is not an option, from aerospace to medical devices. The strategic use of PEEK can lead to long-term savings by reducing maintenance and replacement needs.
As technology evolves, we anticipate broader applications and improved accessibility of PEEK, reinforcing its status as a cornerstone material in high-performance engineering.
FAQs
Why is PEEK plastic so expensive?
PEEK plastic is expensive due to several factors:
High Manufacturing Costs: The production process for PEEK involves high-temperature processing conditions and sophisticated equipment that contribute to higher manufacturing costs.
Raw Material Prices: The monomers used to synthesize PEEK are costly.
Performance Advantages: Its exceptional properties such as high-temperature resistance, chemical stability, and mechanical strength justify a premium, especially for applications where less durable materials would fail quickly.
Is PEEK plastic strong?
Yes, PEEK plastic is exceptionally strong. It is known for its:
High Mechanical Strength: PEEK exhibits excellent tensile and flexural strength.
High Impact Resistance: It can withstand significant impact before deforming or breaking, making it ideal for demanding engineering applications.
Durability: PEEK maintains its mechanical properties even under sustained stress and after repeated thermal cycling.
Is PEEK plastic safe to use?
PEEK is generally very safe to use and is often chosen for applications requiring stringent safety standards:
Biocompatibility: It is commonly used in the medical field for surgical implants due to its excellent biocompatibility.
Chemical Resistance: PEEK does not react with most chemicals, making it safe for use in harsh chemical environments, including handling food and medical applications where contamination must be avoided.
Low Toxicity: It does not emit harmful gases under normal use conditions, though precautions are necessary during processing to handle it at high temperatures.
What is PEEK plastic’s temperature range?
PEEK plastic can operate effectively within a broad temperature range:
Continuous Use: Typically, PEEK can handle continuous service temperatures up to 260°C (500°F).
Short-term Exposure: It can also withstand higher temperatures for short periods without significant degradation of its properties.