Passivation of Stainless Steel: Enhancing Corrosion Resistance
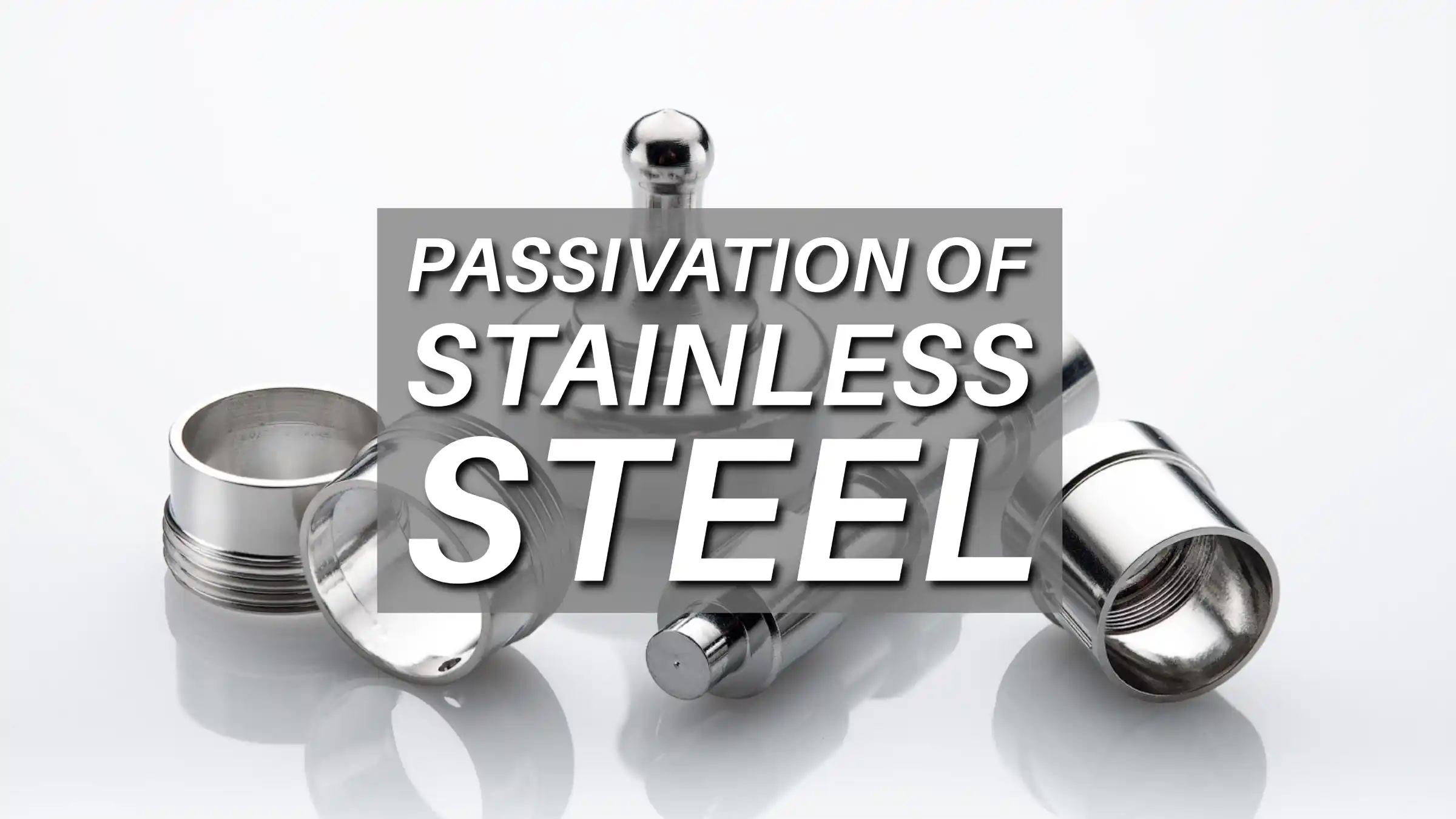
This article explores the process of passivation for stainless steel, explaining its importance in enhancing corrosion resistance.
Introduction
In this article, we delve into the critical process of passivation for stainless steel, elucidating its significance in bolstering corrosion resistance and ensuring the longevity of stainless steel components.
Scientific Principles Behind Passivation
Chemical Basis of Passivation
Passivation is fundamentally defined by the formation of a passive oxide layer on the surface of stainless steel. This process involves the interaction between the metal surface, oxygen, and other elements present in the environment.
The passive oxide layer serves as a protective barrier against corrosion agents, safeguarding the integrity of the material.
Role of Chromium in Passivation
Chromium, a vital component of stainless steel alloys, reacts with oxygen to form a protective chromium oxide layer on the metal's surface.
This layer, formed through exposure to oxygen in the atmosphere or aqueous environments, provides superior corrosion resistance.
It serves as a barrier, safeguarding the metal from degradation and enhancing its durability.
Formation of Passive Oxide Layer
Passivation fosters the development of a passive oxide layer characterized by several key attributes:
Density: The passive oxide layer is dense and tightly adherent to the surface of the stainless steel substrate. This dense structure effectively blocks the diffusion of corrosive agents, such as moisture and chloride ions, towards the underlying metal.
Chemical Stability: The chromium oxide layer demonstrates remarkable chemical stability, even in aggressive environments characterized by high acidity, salinity, or temperature fluctuations. This stability ensures long-term protection against corrosion.
Self-Repair Mechanisms: In the event of minor damage or disruption to the passive oxide layer, chromium within the stainless steel matrix exhibits self-healing properties. Chromium atoms migrate to the site of damage, facilitating the reformation of the protective oxide layer and preserving the material's corrosion resistance.
By fostering the growth of this passive oxide layer, passivation effectively fortifies stainless steel against corrosion, oxidation, and degradation, thereby extending its service life and enhancing its reliability in diverse industrial and commercial applications.
Steps in Passivation of Stainless Steel
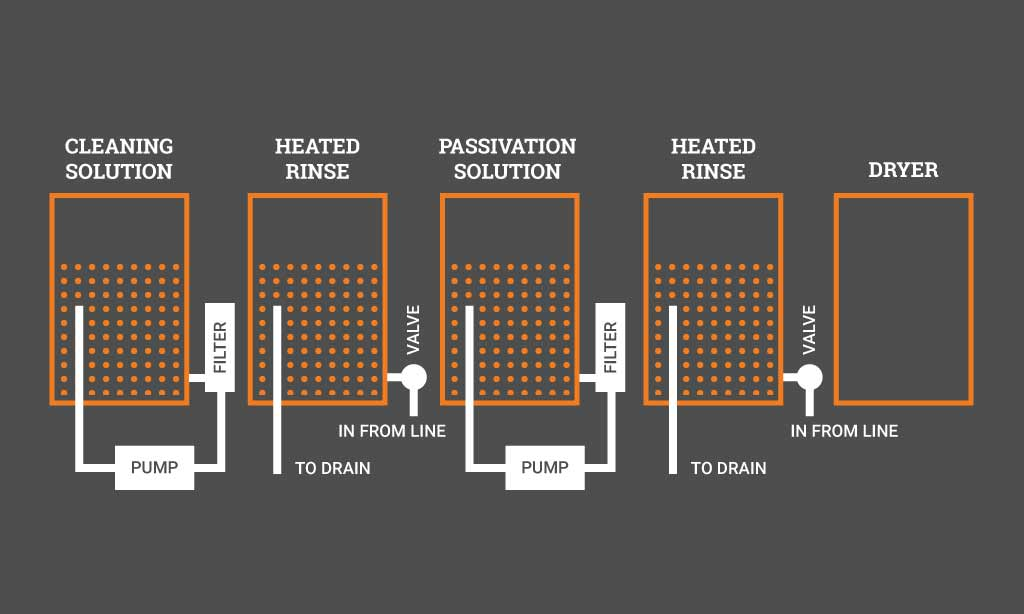
Source: tfgusa.com
Step 1. Pre-Cleaning Procedures
Surface contaminants, oils, and greases must be thoroughly removed before passivation.
This step ensures proper adhesion of the passive oxide layer to the stainless steel surface.
Step 2. Acidic Treatment Solutions
Stainless steel is treated with acidic solutions, typically containing nitric or citric acid.
These solutions initiate the passivation process by removing surface impurities and promoting the formation of the protective oxide layer.
Step 3. Neutralization
After the acidic treatment, residual acids on the surface must be neutralized to prevent any further chemical reactions.
Neutralization ensures that the passivation process is complete and that no active chemical agents remain on the stainless steel surface.
Step 4. Rinsing
Thorough rinsing is essential to remove any remaining chemical residues from the passivation process.
This step helps prevent contamination and ensures the integrity of the passive oxide layer.
Step 5. Drying
Complete drying of the stainless steel components is necessary to prevent water-induced corrosion or contamination.
Drying may involve air drying or the use of drying equipment to ensure that all moisture is removed from the surface.
Step 6. Inspection
Finally, a visual inspection is conducted to ensure the formation of a uniform and intact passive oxide layer on the stainless steel surface.
Any defects or inconsistencies in the passivation process can be identified and addressed during this inspection.
Factors Influencing Passivation of Stainless Steel
Environmental Conditions
Temperature: Passivation reactions are temperature-sensitive, with higher temperatures generally accelerating the process. However, excessively high temperatures can lead to excessive oxide growth or undesirable reactions.
Humidity: Adequate humidity levels are necessary to facilitate the diffusion of reactants and promote uniform oxide layer formation. Low humidity may hinder the passivation process.
pH Levels: The acidity or alkalinity of the environment can influence the chemical reactions involved in passivation. Optimal pH conditions are essential for achieving the desired passive oxide layer.
Material Composition
Chromium Content: Higher chromium content in stainless steel alloys enhances the passivation process, as chromium is the primary element responsible for forming the protective oxide layer.
Alloying Elements: Other alloying elements present in the stainless steel matrix can influence the passivation process and the characteristics of the passive oxide layer.
Surface Finish: Surface finish affects the accessibility of reactants to the metal surface and the adherence of the passive oxide layer. A smooth surface finish promotes uniform passivation and better corrosion resistance.
Contaminants
Presence of Surface Contaminants: Surface contaminants such as oils, greases, or dirt must be thoroughly removed before passivation to ensure proper adhesion and integrity of the passive oxide layer.
Chemical Residues: Residual chemicals from manufacturing processes, such as cutting fluids or lubricants, can interfere with passivation and compromise the quality of the oxide layer.
Passivation Methodology
Choice of Passivation Solution: The selection of passivation solutions, such as nitric acid or citric acid-based formulations, depends on factors like material compatibility, environmental regulations, and desired surface characteristics.
Application Techniques: Proper application techniques, including immersion, spraying, or brushing, ensure uniform coverage and effective passivation of all surfaces.
Duration of Treatment: The duration of passivation treatment must be optimized to achieve the desired thickness and integrity of the passive oxide layer without excessive consumption of resources or time.
By considering these factors and implementing appropriate measures, manufacturers can optimize the passivation process to enhance the corrosion resistance and longevity of stainless steel components in various applications.
Benefits of Passivated Stainless Steel
Enhanced Corrosion Resistance
Formation of Protective Oxide Layer: Passivation facilitates the formation of a dense and adherent oxide layer on the surface of stainless steel, effectively shielding it from corrosion agents such as moisture, chemicals, and salts.
Resistance in Aggressive Environments: The passive oxide layer provides robust protection against corrosion even in harsh or corrosive environments, extending the service life of stainless steel components.
Increased Longevity of Components
Prolonged Service Life: Passivated stainless steel components exhibit greater durability and resistance to corrosion-induced degradation, resulting in extended service intervals and reduced maintenance requirements.
Reduced Risk of Failure: By mitigating corrosion-related damage, passivation helps prevent premature failure of stainless steel parts, enhancing reliability and operational efficiency.
Improved Surface Cleanliness
Hygienic Surface: Passivation removes surface contaminants and impurities, ensuring a clean and sanitary surface suitable for use in sensitive environments such as food processing, pharmaceuticals, and healthcare.
Prevention of Contamination: The smooth and inert surface produced by passivation minimizes the risk of microbial growth, product contamination, and cross-contamination, meeting stringent hygiene standards and regulatory requirements.
Aesthetic Improvements
Enhanced Visual Appeal: Passivation results in a smooth, uniform surface finish with a satin-like appearance, enhancing the aesthetic appeal of stainless steel products.
Consistent Finish: Passivation produces a uniform surface texture and coloration across stainless steel components, improving overall product aesthetics and visual consistency.
By leveraging the benefits of passivated stainless steel, manufacturers can produce high-quality components that offer superior corrosion resistance, longevity, cleanliness, and visual appeal, meeting the diverse needs of various industries and applications.
Applications of Passivated Stainless Steel
Passivated stainless steel serves a multitude of purposes across diverse industries, owing to its exceptional corrosion resistance and hygiene properties:
Industrial Applications
Chemical Processing: Passivated stainless steel components are utilized in chemical reactors, pipelines, and storage tanks where exposure to corrosive chemicals is prevalent. The enhanced corrosion resistance ensures longevity and safety in harsh chemical environments.
Oil and Gas Industry: Passivated stainless steel plays a crucial role in oil rigs, refineries, and pipelines, where exposure to corrosive substances such as saltwater, acids, and hydrocarbons is common. It ensures the integrity of equipment and infrastructure in challenging offshore and onshore environments.
Automotive Sector: Passivated stainless steel parts are utilized in automotive exhaust systems, fuel tanks, and engine components, where resistance to corrosion from exhaust gases, road salts, and environmental factors is essential for durability and performance.
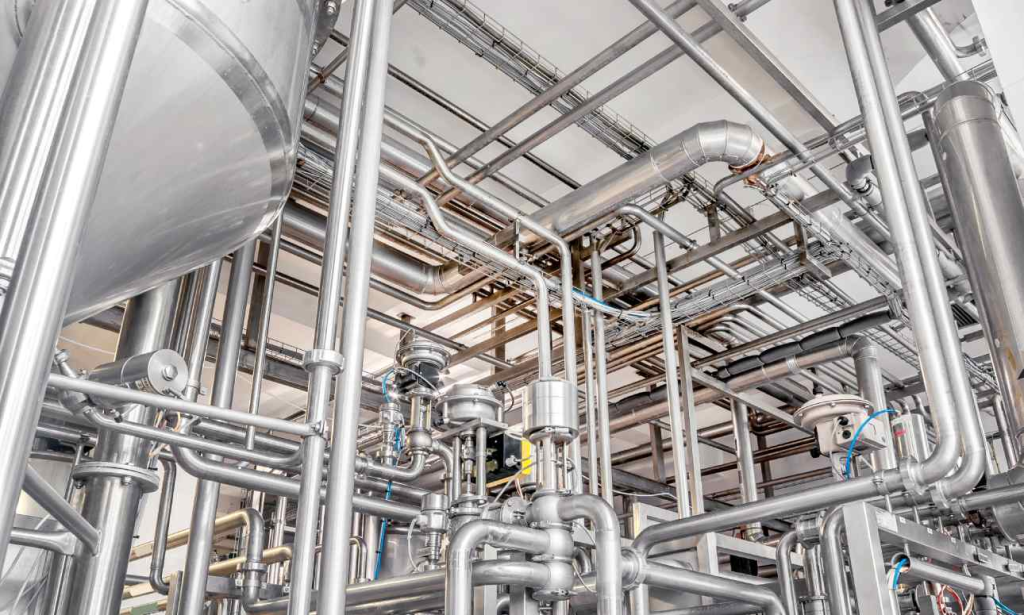
Source: diversey.com
Medical Equipment
Surgical Instruments: Passivated stainless steel is indispensable for surgical instruments and implants due to its biocompatibility, corrosion resistance, and sterilizability. It ensures the reliability and safety of critical medical devices used in surgical procedures.
Implants: Stainless steel implants, such as bone plates, screws, and orthopedic devices, undergo passivation to enhance biocompatibility and resistance to bodily fluids, ensuring successful integration and long-term stability within the human body.
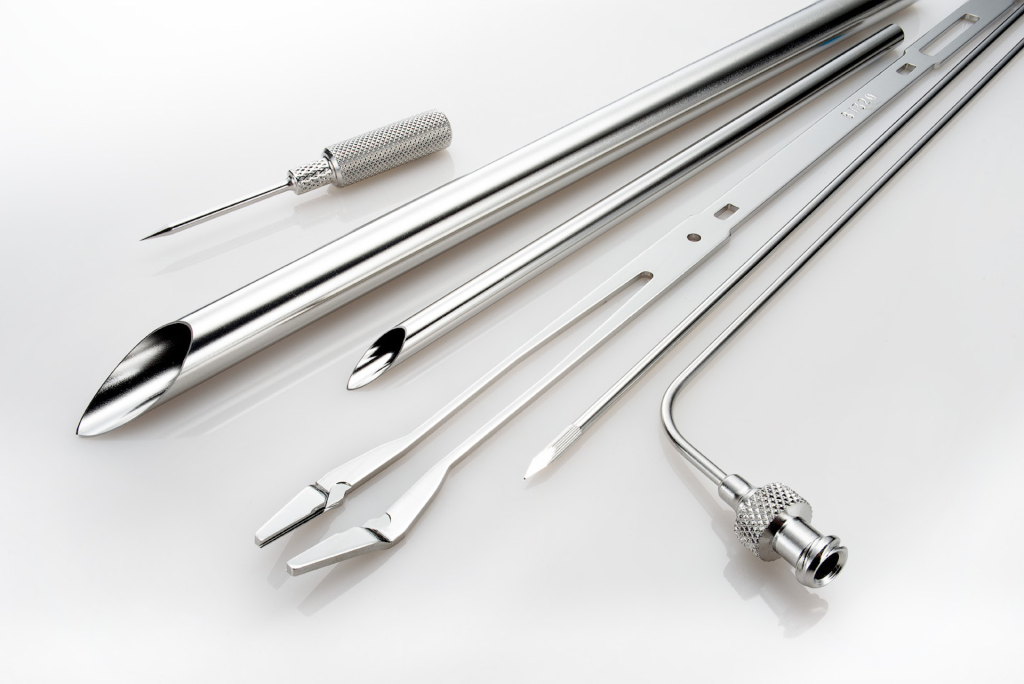
Source: neelectropolishing.com
Food Processing Equipment
Passivated stainless steel is widely employed in food processing equipment, such as tanks, vats, conveyors, and mixers, where cleanliness, hygiene, and resistance to corrosion and contamination are paramount.
It ensures the integrity and safety of food products and complies with stringent regulatory standards.
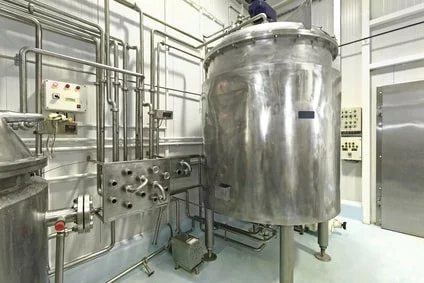
Source: mpofcinci.com
Marine and Aerospace Uses
Marine Applications: Passivated stainless steel components are crucial for marine vessels, offshore platforms, and marine equipment exposed to corrosive seawater, salt spray, and atmospheric conditions. It provides reliable corrosion protection, ensuring the structural integrity and longevity of maritime infrastructure.
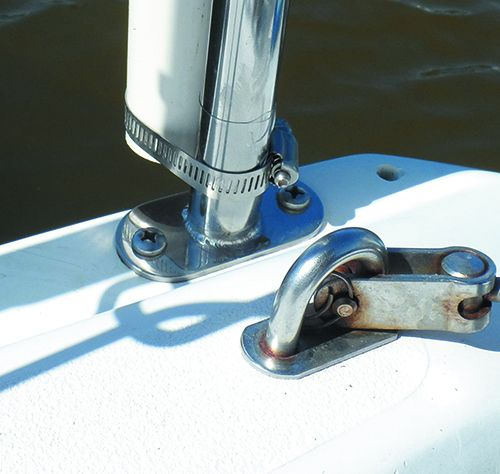
Source: practical-sailor.com
Aerospace Sector: Passivated stainless steel is utilized in aircraft components, fuel systems, and structural elements subjected to aggressive environments, including high altitude, humidity, and temperature fluctuations. It guarantees the reliability and performance of aerospace systems under challenging operating conditions.
In summary, passivated stainless steel finds extensive application in critical sectors such as industry, healthcare, food processing, marine, and aerospace, where durability, corrosion resistance, hygiene, and regulatory compliance are paramount considerations.
Conclusion
Passivation of stainless steel is a critical process for enhancing corrosion resistance and ensuring the longevity and reliability of stainless steel components.
By understanding the underlying principles, adhering to proper procedures, and considering key factors, manufacturers can produce high-quality stainless steel products with superior performance and durability.
Make High Quality Products at Unionfab
Unionfab is dedicated to providing high-quality manufacturing solutions for our customers.
We can provide various types of CNC machining and finishing services you may need, including passivation as mentioned in this article.
For further details, please feel free to reach out to us via our Contact Us page.
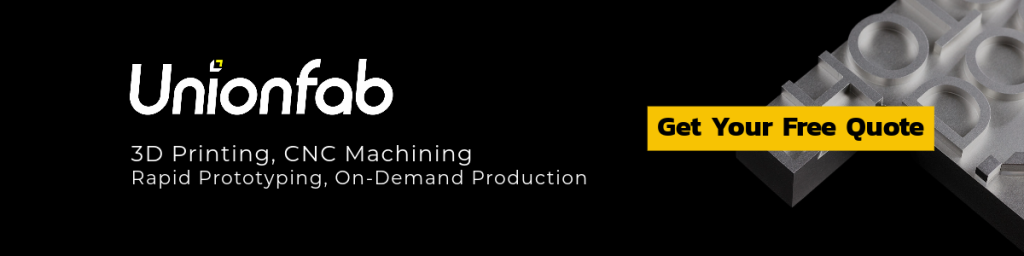