HDPE vs. ABS: Which Plastic is Right for You?
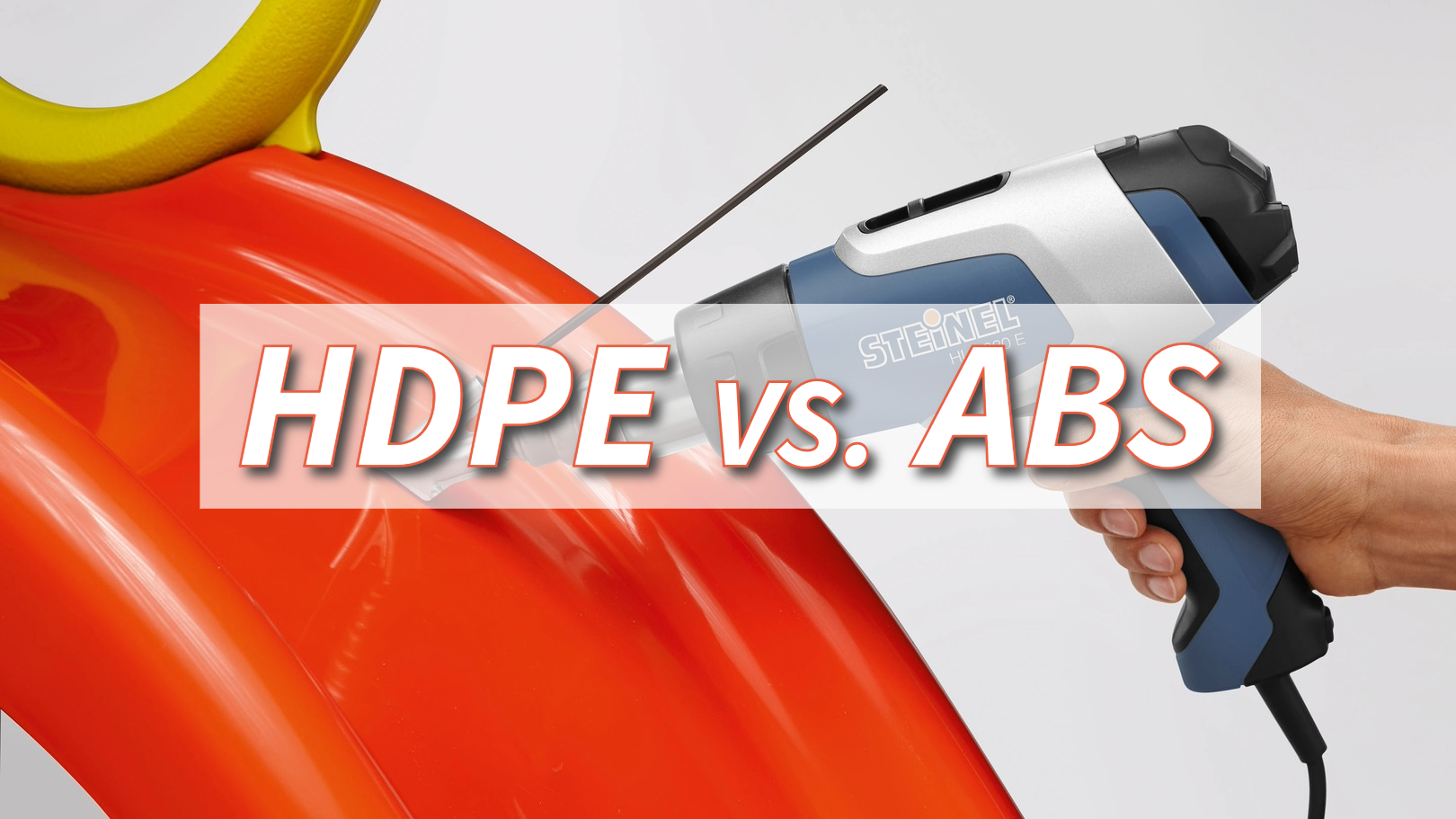
Comparing HDPE and ABS helps in selecting the right one for your specific needs, whether for durability, appearance, or cost.
Introduction
HDPE is known for its toughness and flexibility, making it ideal for outdoor and industrial uses. ABS, on the other hand, is prized for its strength and smooth finish, often used in consumer products and detailed components.
Comparing these materials helps in selecting the right one for your specific needs, whether for durability, appearance, or cost.
What is HDPE?
HDPE is made from tightly packed chains of ethylene molecules, giving it a dense, tough structure. This composition makes it resistant to impacts, chemicals, and environmental stress.
Uses:
Pipes and Fittings: Ideal for water and gas systems.
Packaging: Commonly used for bottles, containers, and plastic bags.
Outdoor Products: Such as playground equipment and furniture.
Industrial Applications: Includes tanks, liners, and chemical containers due to its strength and resistance.
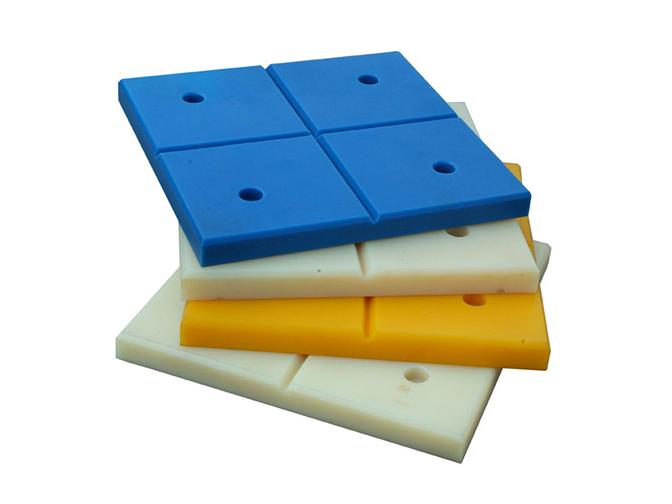
Source: hnokayplastic.com
What is ABS?
ABS is composed of three main components: acrylonitrile, butadiene, and styrene. Acrylonitrile improves its resistance to chemicals and heat, butadiene adds toughness, and styrene provides rigidity and ease of processing.
Uses:
Cars: Dashboards, door panels, steering wheels, and other inside parts.
Household Appliances:Toys, appliances, computer cases, and electronics.
Construction: Plumbing pipes, fittings, and parts that help hold things together.
Medical Devices: Instrument housings, equipment cases, and things that are used only once.
Others: Luggage, helmets, and sports gear.
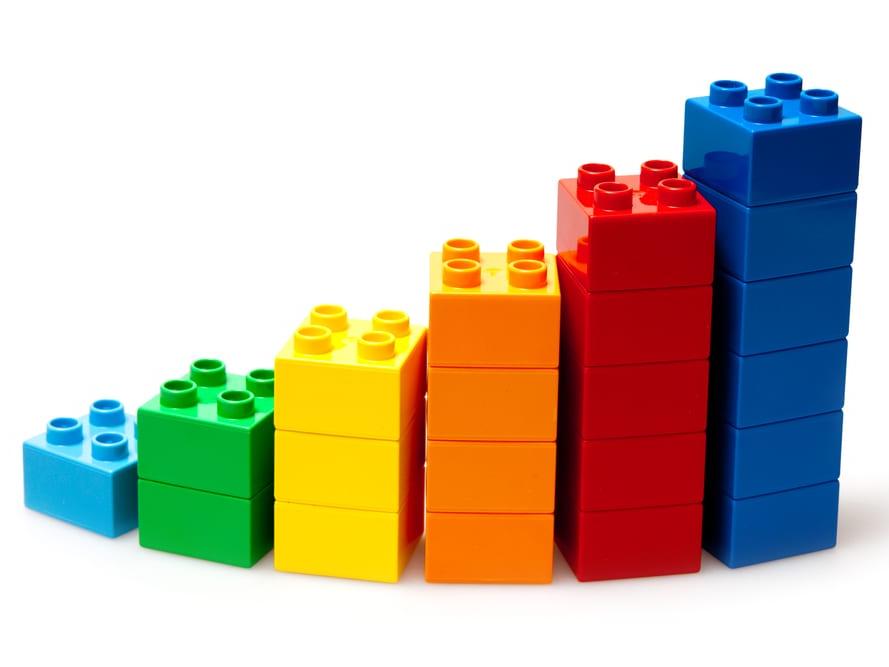
Source: phantomplastics.com
HDPE vs. ABS: Key Differences
Category | Subcategory | HDPE | ABS |
---|---|---|---|
Strength and Durability | Flexibility | More flexible; bends and stretches without breaking. | Harder; better impact resistance |
Rigidity | Less rigid; ideal for bending and stretching. | More rigid; maintains shape under pressure. | |
Mechanical Properties | Flexibility | Softer; bends easily. | Stiffer; holds shape well under stress. |
Durability | Good for low-stress items. | Stronger under pressure and weight. | |
Physical Properties | Texture and Finish | Smoother, waxy; lightweight and can float in water. | Heavier; glossy finish; prone to cracking in cold. |
Scratch Resistance | More prone to scratches. | Stays smooth longer but can crack under extreme cold. | |
Chemical Resistance | Resistance Level | Excellent; suitable for chemical containers and pipes. | Decent; less resistant to strong acids. |
Environmental Impact | Recyclability | Fully recyclable; commonly used in bottles and bags. | Recyclable but less eco-friendly. |
Cost | Price | Generally cheaper; popular for mass-produced items. | More expensive; used for high-strength applications. |
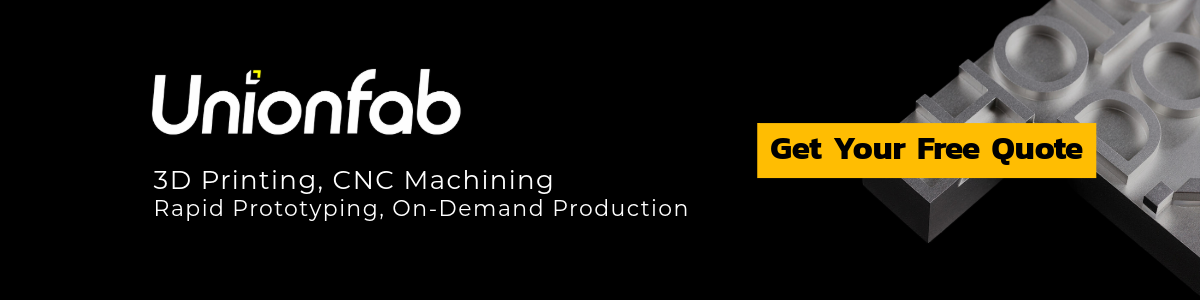
Strength and Durability
HDPE (High-Density Polyethylene) is more flexible and can handle being bent or stretched without breaking, which makes it ideal for outdoor use or tough environments.
ABS, on the other hand, is harder and more rigid, offering better impact resistance, meaning it can handle heavy shocks or hits without cracking.
Mechanical Properties
HDPE is softer but more flexible, meaning it can bend easily without breaking.
ABS is stiffer and more durable, making it stronger under pressure or weight. ABS is better for items that need to hold a solid shape, while HDPE is good for things that need to bend or move.
Physical Properties
HDPE is smoother, waxy, and can float in water due to its lightweight nature.
ABS is heavier and has a glossy finish. HDPE is more prone to scratches, while ABS stays smoother longer but may crack under extreme cold temperatures.
Chemical Resistance
HDPE has excellent resistance to chemicals, making it a good choice for chemical containers and pipes.
ABS has decent chemical resistance but is more vulnerable to strong acids and solvents.
Environmental Impact
HDPE is fully recyclable and is often used in products like plastic bottles and bags.
ABS is also recyclable but is less eco-friendly because of the chemicals used in its production.
Cost
HDPE is generally cheaper than ABS. HDPE’s low price makes it popular for mass-produced items like bottles or packaging.
By contrast, ABS tends to be used for products where higher strength and rigidity are needed, despite being more expensive.
HDPE vs. ABS: Manufacturing Method
HDPE Manufacturing Methods
3D Printing (Fused Deposition Modeling - FDM): This additive manufacturing process employs a heated nozzle to extrude plastic filament, layer by layer, creating custom HDPE objects.
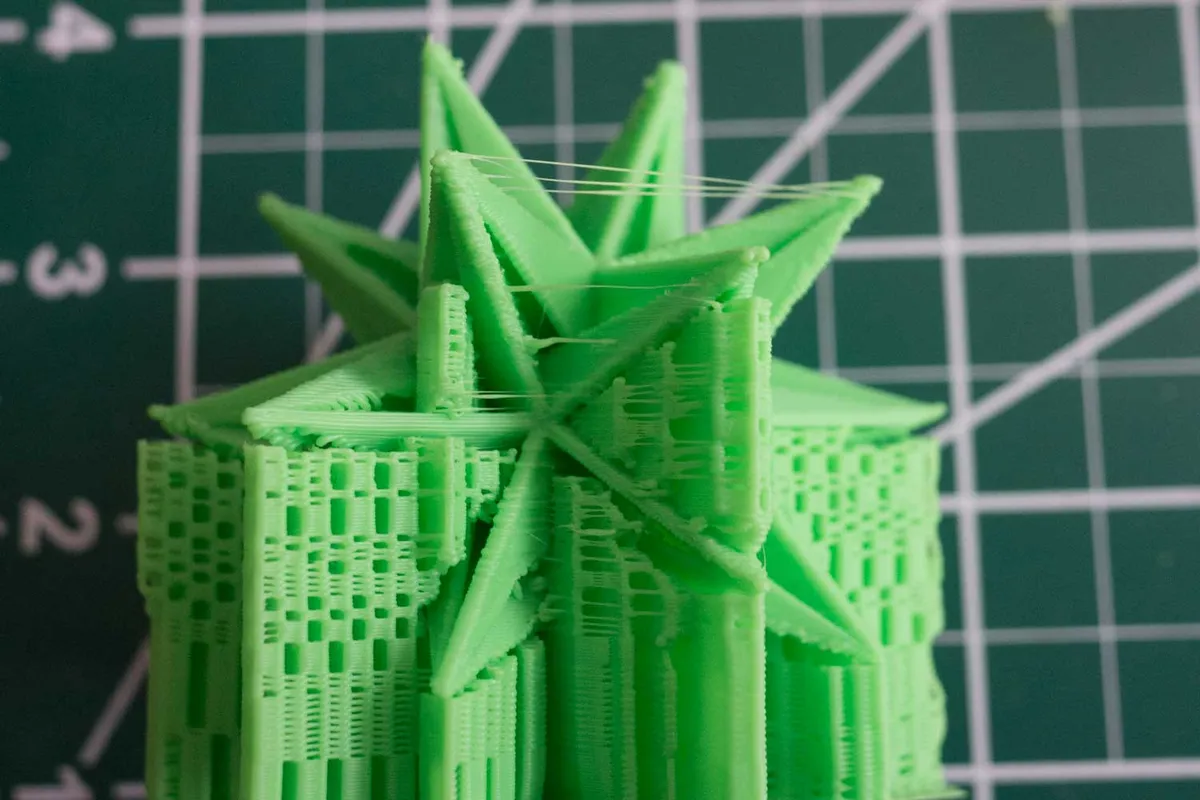
Source: tomsguide.com
CNC Machining: A subtractive manufacturing process involving computer-controlled tools to remove material from HDPE, resulting in precise, intricate shapes.
Blow Molding: In blow molding, HDPE is heated and melted into a tube of molten plastic. Air is then blown into the molten plastic, causing it to expand against the walls of a mold. Once cooled, the plastic takes the shape of the mold.
Injection Molding: In this method, HDPE pellets are melted and injected into a steel mold under high pressure. The mold is cooled, and once the plastic solidifies, the part is ejected. The process is repeated for mass production.
ABS Manufacturing Methods
Injection Molding: Similar to HDPE, ABS is also processed using injection molding. ABS pellets are melted, then injected into a mold under high pressure to form parts. Once cooled, the solid part is ejected. This process allows for the production of high-precision, complex shapes.
Extrusion: ABS can also be processed through extrusion. ABS pellets are heated and forced through a die to form continuous profiles, which are then cooled and cut into desired lengths. This method is used for creating long, continuous parts.
3D Printing (Fused Deposition Modeling - FDM): ABS is a popular material for 3D printing using the FDM technique. ABS filament is heated and extruded through a nozzle to create objects layer by layer based on a digital model. Once the material cools, it solidifies into the final shape.
Thermoforming: In thermoforming, ABS sheets are heated until they become pliable and then pressed into a mold to form specific shapes. Once cooled, the sheet solidifies and retains the shape of the mold.
HDPE vs. ABS: Which Material Should You Choose?
When to Choose HDPE
Flexibility and Lightweight
HDPE is more flexible than ABS, which means it can bend or stretch without breaking. It’s also very light, making it a great choice for products that need to be easy to carry or move.
Examples include plastic bottles, containers, and pipes.
Chemical Resistance
HDPE has excellent resistance to chemicals, so it’s often used for products like chemical containers, fuel tanks, and piping systems.
If the product will be exposed to chemicals, HDPE is a better choice because it won’t break down easily.
Outdoor Use
HDPE is also UV-resistant and can handle being outdoors for a long time without getting damaged by sunlight.
This makes it a good material for outdoor furniture, playground equipment, and other items that need to withstand weather conditions.
Cost
HDPE is usually cheaper than ABS, so if cost is a major factor, HDPE might be the better option.
It’s often used for large-scale production where keeping costs low is important.
Durability in Low-Stress Situations
HDPE is tough but not as rigid as ABS. It’s great for products that don’t need to bear a lot of weight or withstand heavy impacts.
Things like plastic bags, bottles, and low-stress containers are common uses for HDPE.
When to Choose ABS
Strength and Rigidity
ABS is much stronger and more rigid than HDPE. It can handle high-impact situations without cracking, which makes it perfect for products that need to be tough and durable.
This includes things like car parts, protective gear, and electronics casings.
Better Finish
ABS has a smooth, glossy finish, making it ideal for products where appearance is important.
Toys like LEGO bricks and other high-quality plastic products often use ABS because it holds its shape well and looks polished.
Complex Shapes and Precision
ABS is easier to mold into detailed and complex shapes, which makes it useful for products that require precision.
Things like keyboards, remote controls, and car dashboards are often made of ABS because of its ability to hold intricate designs.
Indoor Use
While ABS is strong, it doesn’t do as well outdoors as HDPE because it can degrade when exposed to UV rays from the sun.
For products that will mostly be used indoors, like appliances, toys, and electronics, ABS is an excellent choice.
Higher Cost for Durability
ABS tends to be more expensive than HDPE, but it’s worth the price if you need a material that can handle high impacts and stress without breaking.
If you’re making something that requires a strong, rigid material, ABS is worth the investment.
Alternative Materials for HDPE and ABS
HDPE Alternatives:
LDPE (Low-Density Polyethylene): More flexible, used for plastic bags.
PP (Polypropylene): More rigid, used for food containers and automotive parts.
PVC (Polyvinyl Chloride): Used for pipes and window frames.
PET (Polyethylene Terephthalate): Strong, used in beverage bottles.
ABS Alternatives:
Polycarbonate (PC): Tough, used in eyewear and bulletproof glass.
PLA (Polylactic Acid): Biodegradable, used for 3D printing and cutlery.
Nylon (Polyamide): Used in gears and bearings.
POM (Polyoxymethylene): Used in precision parts like gears.
Conclusion
HDPE and ABS are both strong plastics, but they have different qualities. HDPE is a bendy, strong plastic that resists chemicals well, making it great for outdoor use. ABS is a stiff, strong plastic that can handle heavy shocks, making it good for detailed, strong things.
When choosing a material, it's important to consider your specific needs, such as strength, flexibility, appearance, and cost.
Unionfab: Your Trusted Partner in Plastic Manufacturing
Unsure which is best for your project? Our experts can assist you in making an informed decision.
Explore our extensive material choices, or contact us today for personalized guidance!