The Power of Direct Metal Laser Melting (DMLS) in 3D Printing

Discover how Direct Metal Laser Melting (DMLS) is revolutionizing metal manufacturing. This article explores the mechanics, benefits, applications, and future of DMLS 3D printing technology.
Introduction
3D printing, or additive manufacturing, has evolved significantly from its origins in rapid prototyping to a transformative technology across industries. Direct Metal Laser Melting (DMLS) is a standout method for metal manufacturing, enabling the production of complex, precise, and customized parts.
This article explores DMLS's fundamentals, benefits, applications, and future prospects in 3D printing.
What is DMLS
Direct Metal Laser Melting (DMLS), also known as Direct Metal Laser Sintering, is an advanced additive manufacturing technique specifically designed for creating high-quality metal parts.
The process involves using a high-powered laser to selectively melt and fuse layers of fine metal powder, building parts layer by layer directly from a digital model.
Comparison with Other Metal 3D Printing Techniques
Technique | Laser System | Binding Method | Environment | Part Properties |
---|---|---|---|---|
Direct Metal Laser Melting (DMLS) | Laser melting | Full melting | Open atmosphere | High strength, durable |
Selective Laser Sintering (SLS) | Laser sintering | Partial sintering | Open atmosphere | Moderate strength |
Electron Beam Melting (EBM) | Electron beam melting | Full melting | Vacuum | High strength, durable |
Binder Jetting | No laser | Binder + sintering | Open atmosphere | Varies by post-process |
Direct Metal Laser Melting (DMLS): Fully melts metal powder with a laser in an open atmosphere, producing strong, durable parts. It ensures precise geometries and mechanical properties directly from metal powder, contrasting with methods that may achieve lower density or strength due to partial melting.
Selective Laser Sintering (SLS): Partially fuses metal powder with a laser in an open atmosphere, resulting in moderately strong parts. Unlike DMLS, it doesn't fully melt the powder, affecting mechanical properties and surface finish, suitable for applications prioritizing cost-efficiency over maximum strength.
Electron Beam Melting (EBM): Fully melts metal powder with an electron beam in a vacuum, creating high-strength, dense parts. This method avoids oxidation, offering precise control over material properties and suitability for critical applications where purity is essential, contrasting with methods needing open atmospheres.
Binder Jetting: Uses binder and sintering in an open atmosphere to create parts. It offers material versatility and cost-effective production but generally results in lower mechanical strength and density compared to laser-based techniques like DMLS and SLS, necessitating additional post-processing for desired properties.
How DMLS Works
DMLS Machine Components
A DMLS machine consists of several key components:
Laser System: Provides a high-powered laser beam to melt the metal powder.
Build Platform: The surface on which the part is built, which moves down incrementally as each new layer is added.
Recoater: Spreads a thin layer of metal powder over the build platform.
Powder Bed: The metal powder reservoir used in the process.
Control System: Manages the laser movement, powder deposition, and other machine operations.
Step-by-Step Printing Process
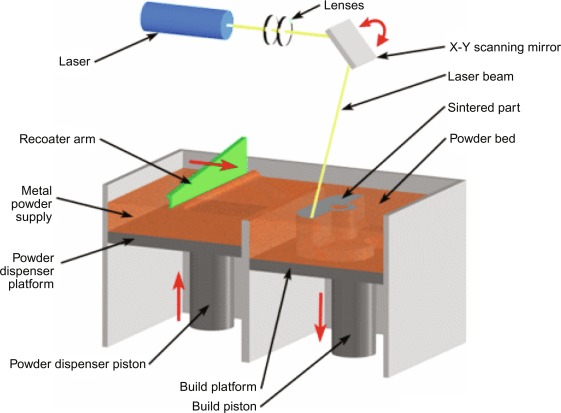
Source: sciencedirect.com
Step1. Design and Slice: The 3D model is sliced into thin layers using specialized software.
Step2. Powder Deposition: A layer of metal powder is spread over the build platform.
Step3. Laser Melting: The laser selectively melts the powder according to the first layer of the digital model.
Step4. Layer Construction: The build platform lowers, and a new layer of powder is spread. The laser melts this new layer according to the next slice of the model.
Step5. Repetition: This process repeats layer by layer until the entire part is constructed.
Step6. Part Removal: The completed part is removed from the powder bed.
Step7. Post-Processing: The part may undergo additional treatments such as heat treatment, machining, or surface finishing to achieve the desired properties.
Metals Used in DMLS
DMLS can work with a variety of metal powders, including:
Titanium Alloys: Known for their high strength-to-weight ratio and corrosion resistance, often used in aerospace and medical applications.
Aluminum Alloys: Lightweight and good thermal conductivity, ideal for automotive and aerospace parts.
Stainless Steel: Offers excellent mechanical properties and corrosion resistance, widely used in various industries.
Inconel: A nickel-chromium-based superalloy known for its high temperature and corrosion resistance, used in aerospace and energy sectors.
Cobalt-Chrome: High wear resistance and biocompatibility, suitable for medical implants and dental prosthetics.
Benefits of DMLS
Precision and Accuracy: DMLS offers exceptional precision, melting and fusing metal powder layer by layer according to a digital model. This results in parts with fine details and tight tolerances, ideal for high-precision applications.
Design Flexibility: DMLS can create complex geometries unattainable with traditional methods. Designers can include intricate internal structures, lattice designs, and complex shapes without conventional machining constraints, optimizing parts for performance, weight, and functionality.
Material Efficiency: DMLS uses only the necessary amount of metal powder with minimal waste. Unused powder can be recycled, reducing material costs and environmental impact. This efficiency is particularly beneficial with expensive or scarce materials.
Strength and Durability: DMLS parts are strong and durable, with mechanical properties comparable to those made with traditional manufacturing methods, making them suitable for critical applications across various industries.
Challenges
Technical Challenges: DMLS requires precise control of parameters like laser power and scanning speed. Deviations can impact quality and consistency. Managing thermal stresses is also crucial to prevent warping and cracking.
Cost Considerations: DMLS can be costly, especially for small production runs or prototyping. Initial equipment investment and operating costs are significant, which can be a barrier despite long-term material efficiency benefits.
Quality Control and Post-Processing: Ensuring consistent quality requires rigorous control. Post-processing steps such as heat treatment, machining, and surface finishing are often necessary, increasing production time and cost.
Industry Applications
Aerospace
In aerospace, DMLS produces lightweight components like turbine blades and structural elements with high strength and complex geometries. This technology helps in meeting stringent aerospace standards while reducing costs and lead times.
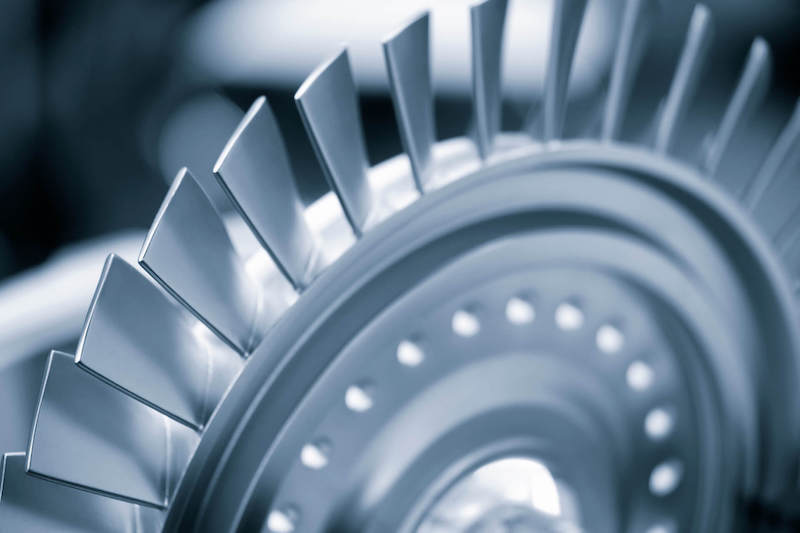
Source: rapidmfgco.com
Automotive
Automakers use DMLS for custom engine parts and lightweight structural components. It enhances vehicle performance and efficiency by optimizing part design and material properties, supporting rapid prototyping and production flexibility.
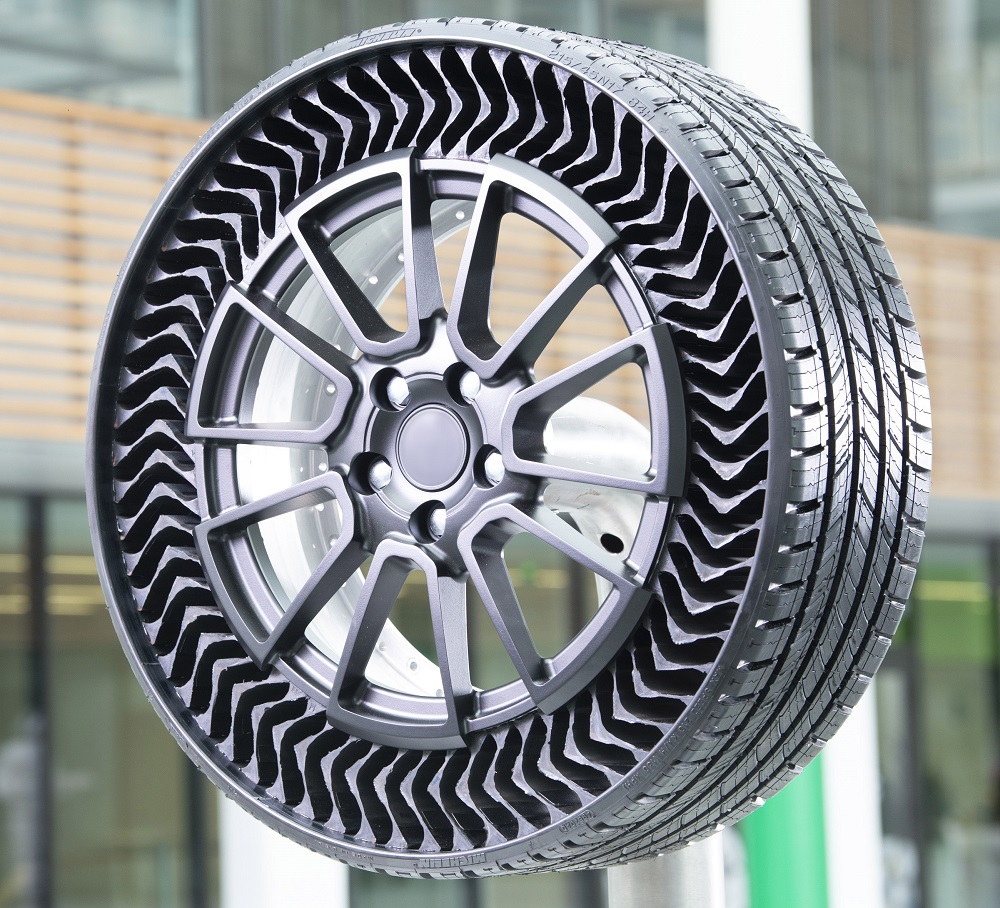
Source: 3dprintingindustry.com
Medical
DMLS enables the fabrication of patient-specific implants and prosthetics from biocompatible materials like titanium alloys. It ensures precise fitting and enhances biomechanical performance, revolutionizing medical treatments and reducing risks associated with traditional manufacturing methods.
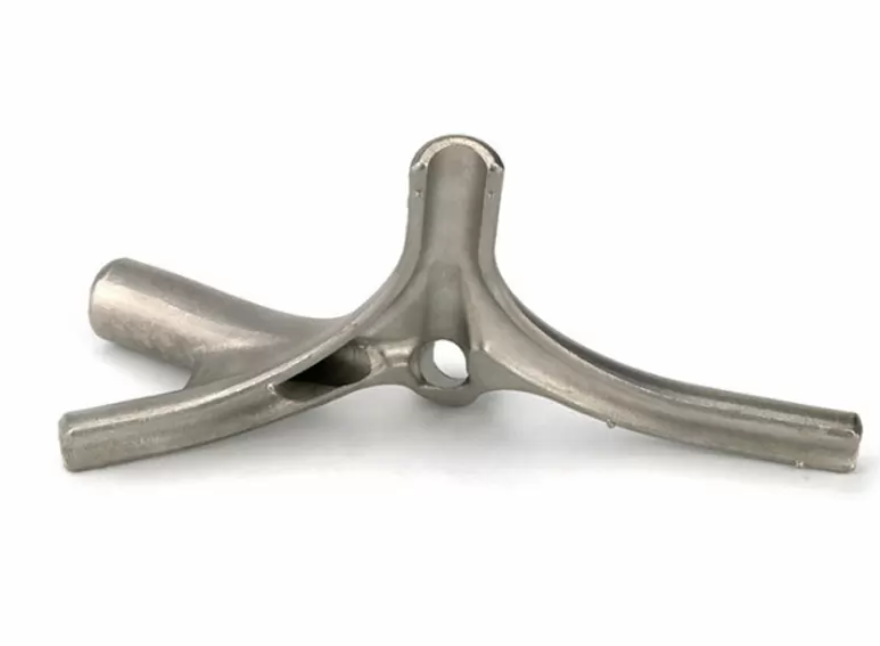
Source: be-cu.com
Tooling
In tooling, DMLS produces durable tools with superior mechanical properties such as high hardness and wear resistance. It supports industries with complex part requirements, improving productivity and reducing maintenance costs.
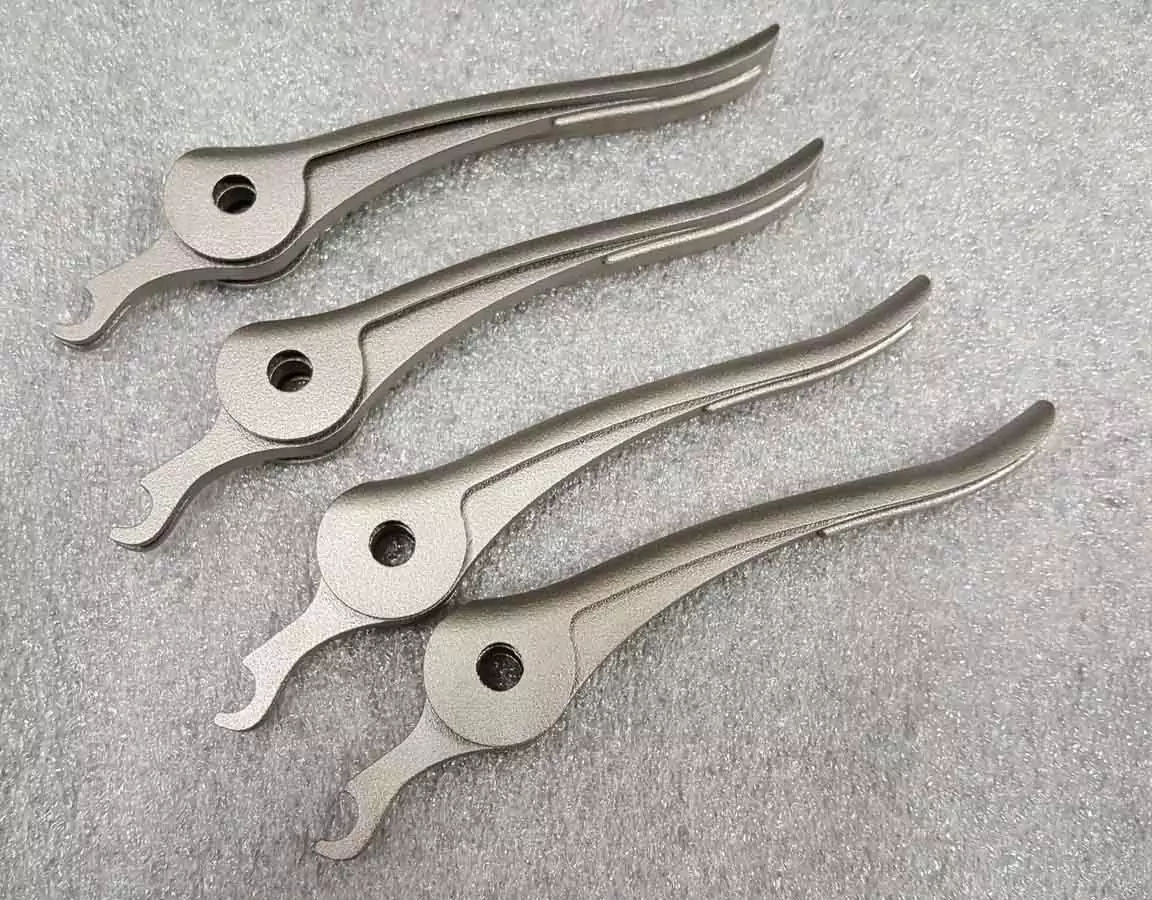
Source: sculpteo.com
Case Studies
GE Aviation: Fuel Nozzles for Jet Engines
GE Aviation has successfully implemented DMLS to produce fuel nozzles for its LEAP jet engines. Traditional manufacturing methods require the assembly of 20 separate parts, but with DMLS, the nozzle can be printed as a single piece. This not only reduces manufacturing time and cost but also improves the durability and performance of the nozzle.
GE Aviation reports that the DMLS-produced nozzles are five times more durable than those made with traditional methods.
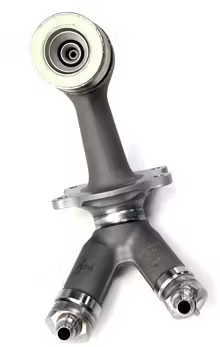
Source: laserfocusworld.com
Siemens: Gas Turbine Blades
Siemens has utilized DMLS to manufacture gas turbine blades, achieving significant performance improvements. The DMLS process allows for intricate cooling channel designs that enhance the blades' efficiency and durability under high temperatures.
Siemens has reported a reduction in production time from months to weeks, and the ability to rapidly iterate on design improvements has resulted in more efficient and reliable turbine operation.
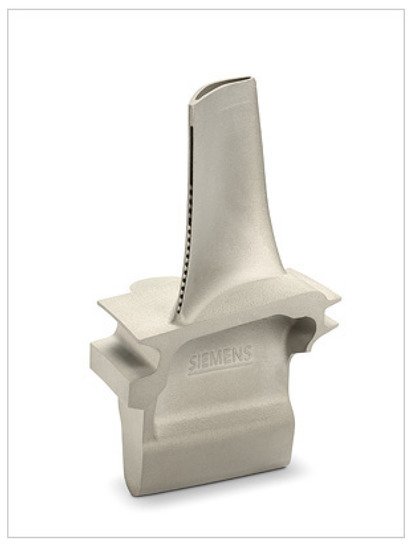
Source: encyclopedia.pub
Future of DMLS
Innovations and advancements
Innovations in DMLS are driven by advancements in multi-laser systems, led by companies such as EOS, which are enhancing production speeds and scalability for large-scale manufacturing. Concurrently, ongoing research into alloys like aluminum-scandium and high-entropy alloys aims to boost mechanical properties, expanding DMLS capabilities to handle increasingly complex applications.
Impact on manufacturing
The impact on manufacturing is profound with DMLS. It enables decentralized, on-demand production, effectively reducing inventory requirements, logistical costs, and vulnerabilities to global supply chain disruptions. Additionally, DMLS supports mass customization by accommodating diverse industry needs for intricate, personalized designs without incurring substantial cost escalations.
Predictions for future adoption
In the future, DMLS is poised for broader adoption across aerospace, medical, energy, defense, and consumer goods sectors, driven by cost-effectiveness and scalability. Integration with AI, machine learning, and IoT will optimize processes, ensuring high-quality outputs and fostering innovation. Enhanced regulatory frameworks will bolster reliability and safety, boosting industry confidence and adoption rates.
Conclusion
Direct Metal Laser Melting (DMLS) is transforming metal manufacturing with its precise laser technology, enabling the creation of complex, durable parts across industries like aerospace, automotive, and medical.
As DMLS advances with new alloys and multi-laser systems, its potential for innovation and efficiency in additive manufacturing continues to expand.
Advancing Innovation: Unionfab's DMLS Technology
Unionfab specializes in Direct Metal Laser Melting (DMLS), optimizing production across aerospace, automotive, and medical industries. Our cutting-edge DMLS technology ensures precise, high-quality metal parts.
Contact us to explore Unionfab's DMLS solutions for advanced additive manufacturing.
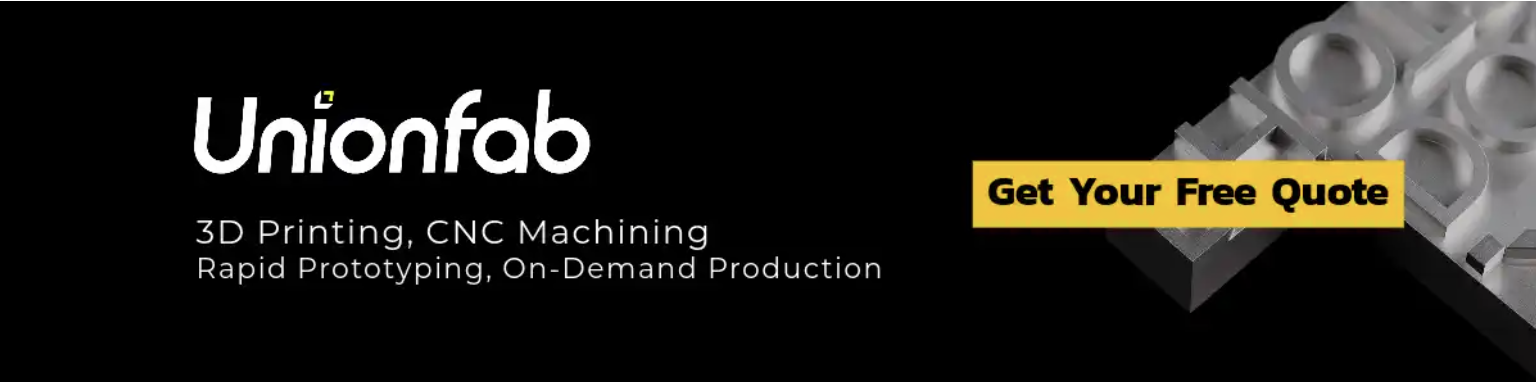