Black Phosphate Coating: Process and Benefits
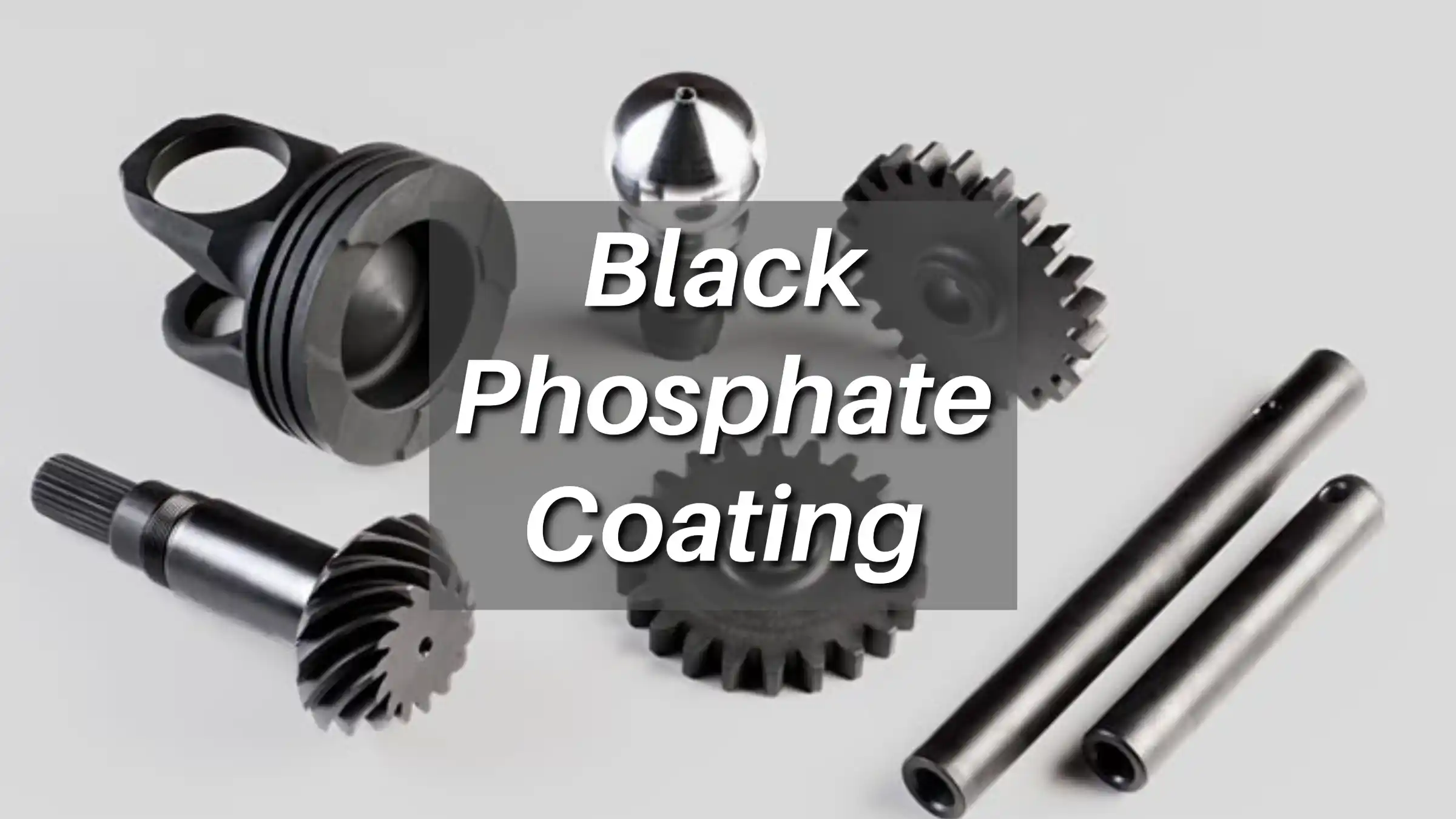
This article explores the intricacies of black phosphate coating, covering its methods, advantages, and diverse applications.
Introduction
Black phosphate coating, or manganese phosphate coating, is a chemical treatment applied to metal surfaces, most commonly steel.
This conversion process transforms the surface, enhancing its properties and offering several advantages.
Composition and Properties
Overview of Chemical Components
The primary component of black phosphate coating is manganese phosphate (Mn(PO4)2), though iron phosphate (FePO4) can also be present depending on the specific process.
To achieve the black color, additional elements are introduced into the treatment bath. These blackening agents typically include:
Antimony (Sb): This is the most common blackening agent, often added as antimony tartrate.
Nickel (Ni): Nickel salts can also contribute to the blackening process.
The base solution for the treatment usually consists of:
Phosphoric Acid (H3PO4): This reacts with the metal surface to form the phosphate layer.
Metal Oxides (ZnO, MnO2): These act as accelerators for the conversion process.
Other Additives: Depending on the desired properties, additional additives like fluorides can be used to improve wear resistance.
Physical and Chemical Properties
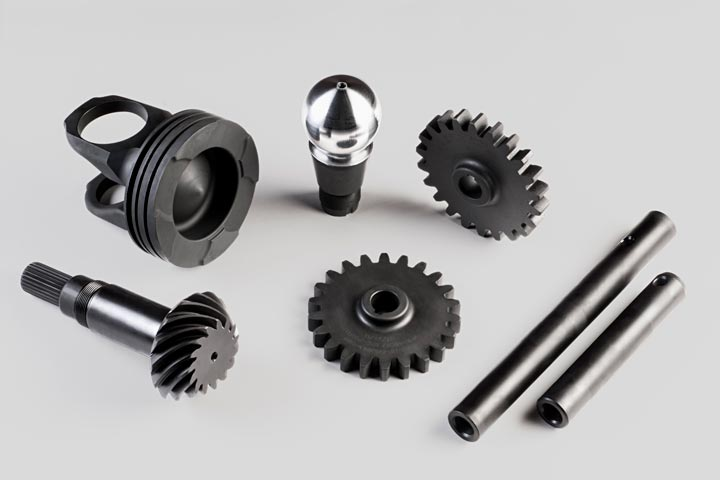
Source: difco.us.com
Color
Deep black, with a matte or slightly glossy finish.
Morphology
Microcrystalline structure with a slightly rough surface texture
Hardness
Relatively soft compared to other coatings, but offers good wear resistance due to its ability to trap lubricants.
Corrosion Resistance
The phosphate layer acts as a barrier, hindering the diffusion of corrosive agents towards the underlying metal.
Friction Reduction
The microporous structure traps lubricants, reducing friction between contacting surfaces.
Paint Adhesion
Offers a good foundation for paints and other coatings, promoting strong adhesion.
Chemical Resistance
Black phosphate coating offers moderate resistance to some chemicals but may not be suitable for highly acidic or alkaline environments.
Differences from Other Phosphate Coatings
There are several types of phosphate coatings, each with its own characteristics.
Feature | Black Phosphate | Zinc Phosphate | Iron Phosphate |
---|---|---|---|
Color | Dark black, matte | Grayish | Light gray to brown |
Primary Composition | Manganese phosphate (Mn3(PO4)2), potentially with iron phosphate (FePO4) | Zinc phosphate (Zn3(PO4)2) | Iron phosphate (FePO4) |
Additional Elements | Antimony (Sb) for color, Calcium (Ca) for uniformity (may include Zinc (Zn)) | None | None |
Key Properties | Superior lubrication | Good corrosion resistance good paintability | Good corrosion resistance as a base for further coatings |
Typical Applications | Engine components, firearms, fasteners, cutting tools | Automotive parts, appliance components, furniture | As a base for painting on steel |
Black Phosphate Coating Process
Pre-treatment and Surface Preparation
Degreasing
The metal surface is thoroughly cleaned to remove any oils, grease, dirt, or contaminants. This ensures a good foundation for the phosphate coating to adhere properly.
Methods like solvent degreasing or alkaline cleaning are commonly used.
Rinsing
The cleaned metal is rinsed with clean water to remove any residual cleaning chemicals.
Pickling (Optional)
In some cases, pickling with a mild acid solution may be used to remove oxides or scale from the metal surface.
This step improves the reactivity of the metal with the phosphating solution.
Activation (Optional)
Activation with a weak acid solution can further enhance the bonding between the metal and the phosphate coating.
This step is not always necessary but can be used for specific types of metals or to improve coating performance.
Phosphating Bath and Immersion Process
Bath Preparation
A phosphating bath is prepared with a specific solution containing various chemicals. The primary components typically include:
Metal Phosphates: These can be manganese phosphate or a combination of manganese and iron phosphate, depending on the desired properties.
Acids: Phosphoric acid is a common component, helping to create the phosphate layer.
Additives: Antimony compounds (like antimony tartrate) are added for the black color. Additionally, calcium compounds might be incorporated to regulate the solution's pH and promote uniform coating formation.
Temperature Control
The phosphating bath is maintained at a specific temperature range, usually between 140°F and 190°F (60°C and 88°C).
This temperature control is crucial for a consistent and successful phosphating reaction.
Immersion
The cleaned and (potentially) activated metal component is completely submerged in the phosphating bath for a predetermined time.
During this immersion, a chemical reaction occurs between the metal surface and the bath solution, leading to the formation of the phosphate layer.
Post-treatment Procedures
Rinsing: After immersion, the phosphated component is thoroughly rinsed with clean water to remove any residual phosphating solution.
Neutralization: The rinsed component may be dipped in a weak alkaline solution to neutralize any remaining acidity from the phosphating process.
Drying: The component is dried using warm air or a similar method to prevent flash rusting.
Quality Control Measures
Visual Inspection: The coating's appearance, uniformity, and color are visually inspected for any defects or inconsistencies.
Thickness Measurement: The thickness of the phosphate layer is measured using non-destructive techniques like magnetic gauges or eddy current meters.
Weight Gain Test: The weight gain of the metal part after coating is compared to a standard to verify the amount of phosphate deposited.
Adhesion Testing: Adhesion between the coating and the metal substrate is evaluated using methods like scratch tests or tape tests.
Corrosion Resistance Testing: The coated parts may be subjected to salt spray or other corrosion resistance tests to assess their effectiveness in protecting the underlying metal.
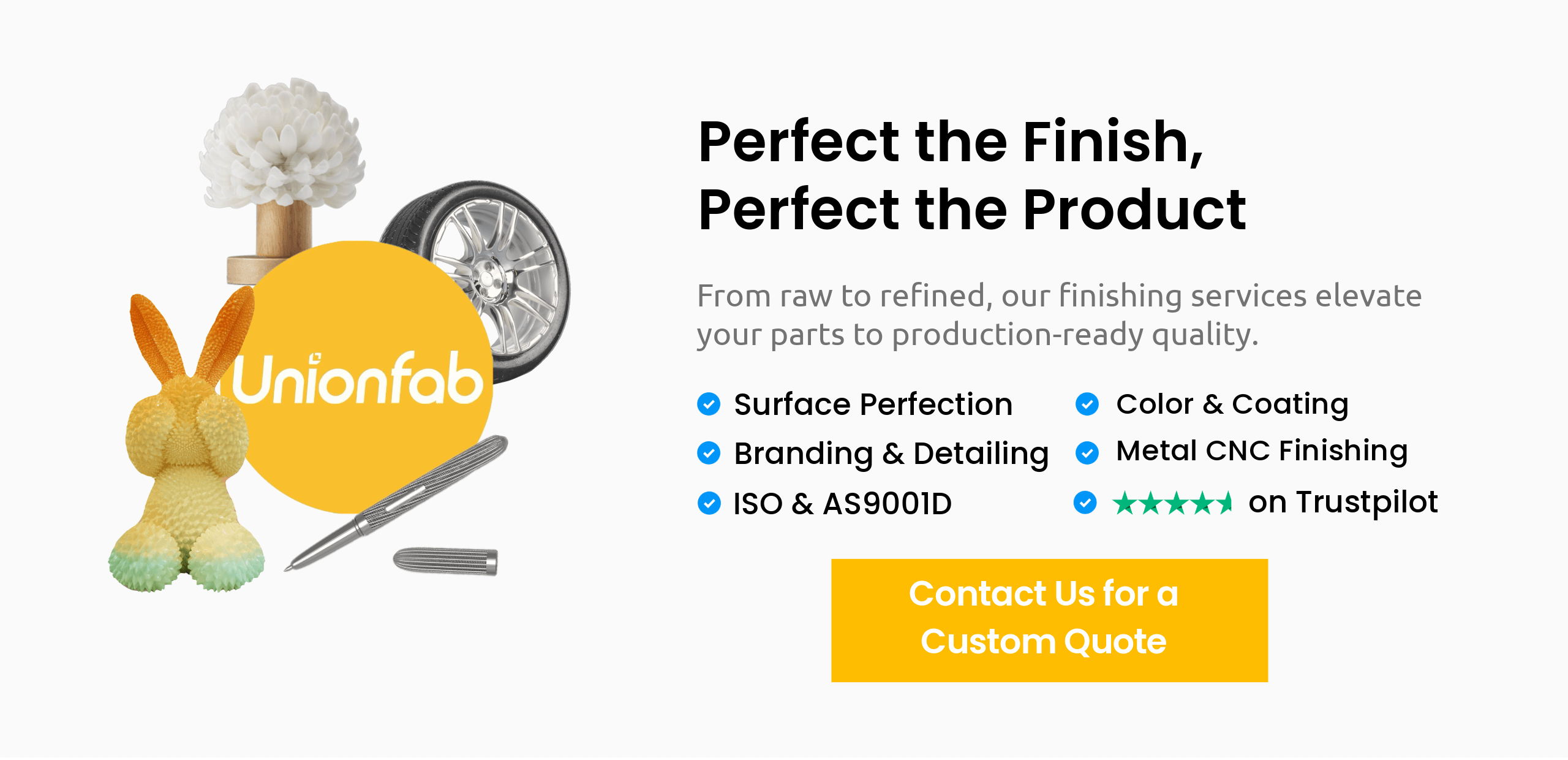
Benefits of Black Phosphate Coating
Corrosion Resistance Enhancement
Barrier Protection
The primary phosphate layer acts as a physical barrier, hindering the penetration of corrosive elements like moisture, oxygen, and salts.
This significantly reduces the risk of rust and other forms of corrosion, especially in mildly acidic or alkaline environments.
Improved Durability
By protecting the underlying metal, black phosphate coating extends the lifespan of components and reduces the need for frequent replacements.
Improved Lubricity and Wear Resistance
The microscopic texture of the black phosphate coating, with its peaks and valleys, acts as a reservoir for lubricants. This trapped lubricant reduces friction between contacting surfaces, leading to several advantages.
Reduced Wear
By minimizing friction, black phosphate coating helps to slow down wear and tear on moving parts. This extends the lifespan of components and reduces maintenance requirements.
Smoother Operation
The reduced friction translates to smoother operation of machinery and components, potentially improving efficiency and performance.
Aesthetic Improvements
Black phosphate coating boasts a distinctive dark, matte black finish. This aesthetic appeal can be desirable for certain applications, especially in situations where exposed metal components are visible.
Cost-Effectiveness
Relatively Simple Process
Compared to some other metal finishing processes, black phosphate coating is a relatively cost-effective option.
The process itself is simpler and requires less specialized equipment compared to techniques like electroplating or anodizing.
Durability and Long-Term Savings
The black phosphate coating's ability to enhance corrosion resistance, reduce wear, and provide a good foundation for paint can lead to long-term savings.
By extending the lifespan of components and reducing the need for frequent replacements or repainting, black phosphate coating offers a good return on investment.
Black Phosphate vs. Black Oxide: Comparison
Definition and Characteristics of Black Oxide
Definition
Black oxide, also known as magnetite conversion coating, is a thin layer of iron oxide (Fe3O4) formed on the surface of steel through a chemical reaction.
Characteristics
Appearance: Black oxide has a slightly less intense black color compared to black phosphate, with a more matte or slightly glossy finish depending on the process.
Corrosion Resistance: Black oxide offers moderate corrosion resistance, particularly effective in dry environments. However, its protection can diminish in humid or wet conditions.
Lubricity: Black oxide offers minimal lubrication properties. The smooth surface doesn't trap lubricants as effectively as black phosphate.
Wear Resistance: Black oxide has a moderate level of wear resistance due to the hardness of the iron oxide layer.
Key Differences in Chemical Composition
Black Phosphate
The primary component is manganese phosphate (Mn3(PO4)2), with the potential inclusion of iron phosphate (FePO4) and additional elements like antimony (Sb) for color and calcium (Ca) for uniformity.
Black Oxide
The primary component is magnetite (Fe3O4), an iron oxide compound formed by the conversion of the metal surface itself.
Differences in Application Processes
Stage | Black Phosphate | Black Oxide |
---|---|---|
Pre-Treatment | Degreasing, rinsing, pickling (optional), activation (optional) | Degreasing, rinsing |
Bath | Heated phosphating bath with manganese phosphates, antimony compounds, and acids | Hot alkaline solution |
Immersion Time | Longer immersion time (typically minutes) | Shorter immersion time (typically seconds) |
Post-Treatment | Rinsing, neutralization (optional), drying | Rinsing, drying |
Performance in Various Environments
Dry Environments: Both black phosphate and black oxide offer adequate protection.
Humid or Wet Environments: Black phosphate provides superior performance due to its better barrier properties against moisture and corrosion.
High-Wear Applications: Black phosphate's microscopic texture offers some lubrication benefits, making it a better choice for parts experiencing sliding contact.
Cost Comparison
Factor | Black Phosphate | Black Oxide |
---|---|---|
Chemicals | More expensive (manganese phosphate, antimony compounds, additives) | Less expensive (hot alkaline solution) |
Process Complexity | More complex (multi-step process) | Simpler process |
Labor | More labor required | Less labor required |
Upfront Cost | Slightly higher | More economical |
Bulk Processing | Cost savings possible | More significant cost reduction possible |
Long-Term Cost | Potential for savings due to extended component lifespan and reduced repainting | May require more frequent replacements and repainting |
Performance Requirements | Justifies higher upfront cost for superior corrosion resistance, wear reduction, and paint adhesion | Lower upfront cost suitable for dry environments with minimal corrosion risk |
Applications of Black Phosphate Coating
Automotive Industry
Engine Components
Black phosphate coating is frequently used on engine components like valve springs, tappets, and pushrods.
It protects these parts from wear and corrosion caused by high temperatures, friction, and exposure to engine oil.
Drivetrain Components
Gears, transmission parts, and other drivetrain components benefit from black phosphate's ability to reduce friction and enhance wear resistance, extending their lifespan and smooth operation.
Fasteners
Black phosphate coating is applied to fasteners like bolts, nuts, and screws to improve corrosion resistance and prevent them from seizing or galling during assembly and disassembly.
Aerospace Components
Landing Gear
Landing gear components experience significant wear and tear during landing and taxiing.
Black phosphate coating provides a layer of protection against corrosion and wear, ensuring smooth operation and extended service life.
Aircraft Hardware
Black phosphate coating is used on various aircraft hardware components, such as brackets, hinges, and control linkages, to enhance corrosion resistance and improve wear performance.
Industrial Machinery
Machine Tools
Black phosphate coating is used on certain machine tool components like slides, ways, and gears.
It reduces friction, enhances wear resistance, and offers a good base for lubricants, leading to smoother operation and extended tool life.
Textile Machinery
Black phosphate coating finds application in textile machinery components like needles and gears.
It improves wear resistance and reduces friction, ensuring smooth operation and reducing downtime for maintenance.
Food Processing Equipment
Black phosphate coating can be used on specific food processing equipment components due to its ability to resist corrosion from food acids and moisture.
Additionally, the smooth surface can minimize food residue build-up, promoting hygiene.
Consumer Goods
Firearms
Black phosphate coating is a popular choice for firearms due to its combination of corrosion resistance, wear resistance, and a sleek black finish.
It protects against sweat, moisture, and minor scratches, while also enhancing the firearm's aesthetics.
Hardware
Black phosphate coating can be found on some hardware items like bolts, screws, and nuts.
It offers a visually appealing finish and some level of corrosion resistance for applications requiring a balance of aesthetics and functionality.
Musical Instruments
Black phosphate coating is sometimes used on certain musical instrument parts like screws, bridges, and tuners.
It provides a visually appealing dark finish and can offer some protection against corrosion from sweat or moisture.
Conclusion
Black phosphate coating is a versatile and valuable metal finishing technique. Its ability to enhance corrosion resistance, improve lubrication, and provide a sleek black finish makes it a desirable choice for various applications.
From protecting critical components in the automotive and aerospace industries to extending the lifespan of machinery and enhancing the aesthetics of consumer goods, black phosphate coating offers a compelling combination of functionality and visual appeal.
Achieve Better Manufacturing at Unionfab
Unionfab offers a comprehensive solution for achieving better manufacturing. Our 3D printing capabilities accelerate your design and prototyping phase while finishing services make your products perfect.
Partner with Unionfab and bring your innovative ideas to life!
Looking for Expert Finishing Services?
Unionfab is a leading 3D printing and manufacturing company providing a wide range of value-added services, including anodizing, heat treatment, polishing, and more. We are your one-stop partner, guiding your projects from prototyping to finishing with the utmost precision and quality.
With 20+ years of experience, we ensure your designs are manufactured to perfection.
From surface perfection like polishing and sandblasting to specialized metal finishes, our services are tailored to meet your needs. Contact Us today to discuss your project and explore our value-added services!
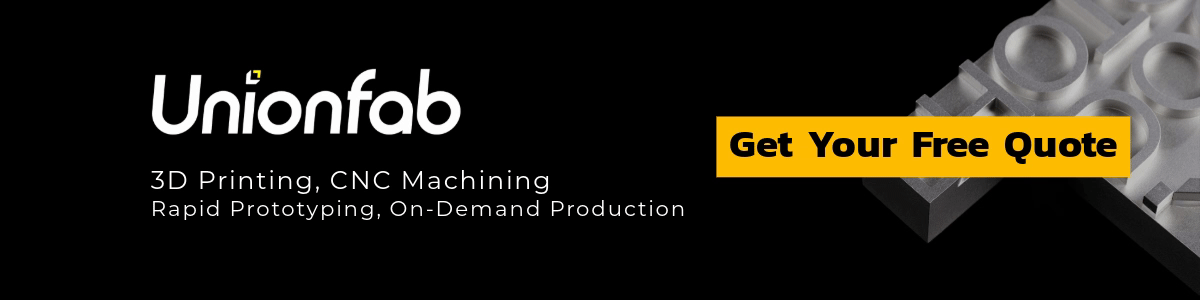