Exploring Binder Jetting: The Future of Metal 3D Printing
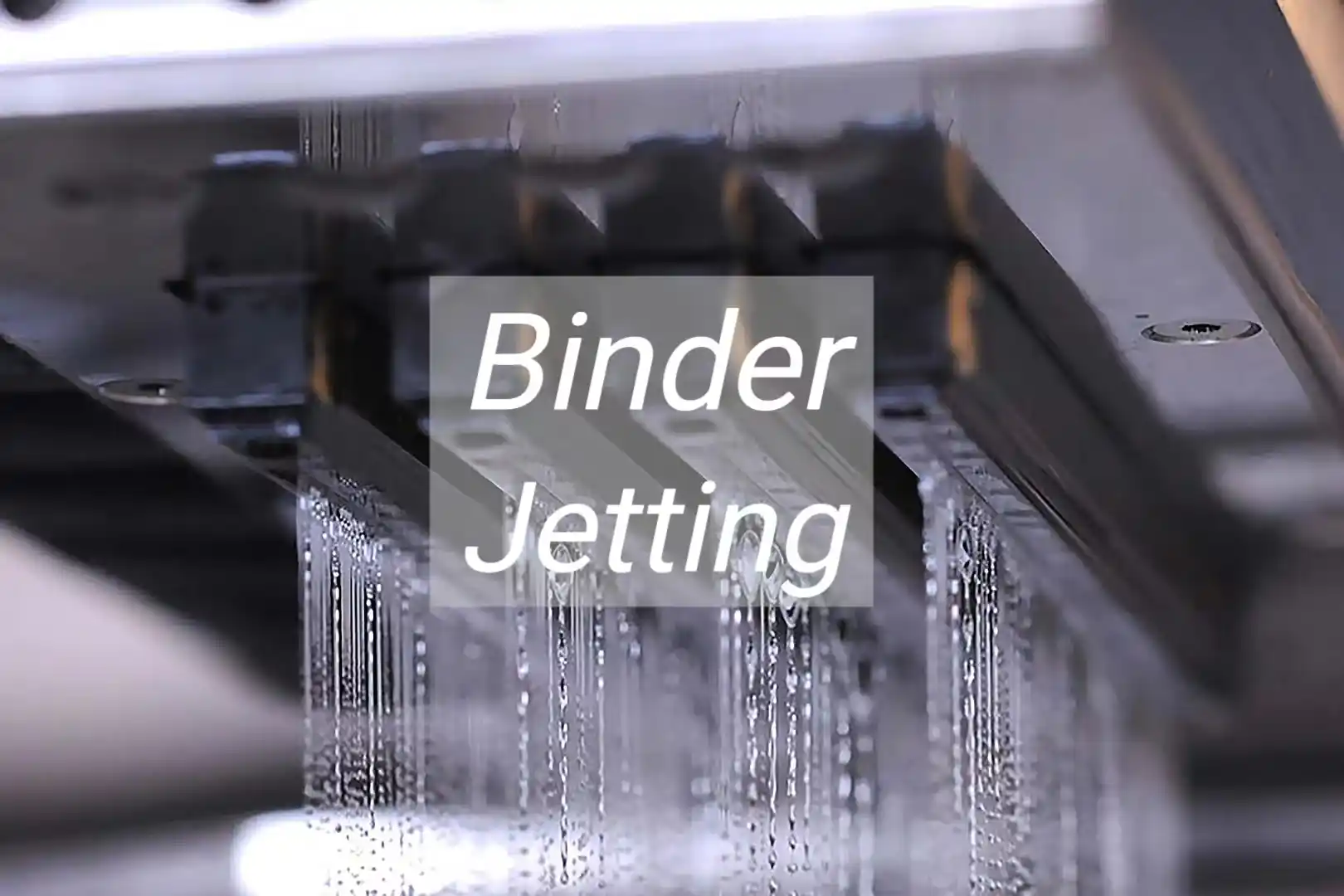
Binder jetting is a pivotal process in additive manufacturing, allowing for the creation of prototypes and functional parts using various materials such as metals and ceramics.
Introduction
Binder jetting transforms metal 3D printing with its innovative capabilities. This guide explores its applications, advantages, and the technology behind binder jetting 3D printers.
Whether you're in manufacturing, engineering, or simply curious about tech, this article offers a thorough insight into how binder jetting is revolutionizing additive manufacturing.
What is Binder Jetting?
Definition and basic principles
Binder jetting is an additive manufacturing process where a binding agent is selectively deposited onto layers of powder material, such as metals or ceramics.
This process builds parts layer by layer based on a digital 3D model, using unbound powder as a temporary support.
Historical development and evolution
Binder jetting emerged in the 1990s to create prototypes and has since evolved into a viable technology for producing functional parts. Early systems had limited resolution and material options, and they were primarily used for rapid prototyping.
Over time, advancements in printer technology, materials, and binder formulations have expanded the capabilities of it.
Key differentiators from other 3D printing technologies
Key Aspect | Binder Jetting | Other 3D Printing Technologies |
---|---|---|
Speed | Fast | Slower (e.g., SLS, DMLS) |
Cost | Cost-effective | Higher initial cost |
Design Freedom | Complex geometries | Limited geometric flexibility |
Material Versatility | Metals, ceramics, composites | Limited range of materials |
Post-Processing | Required (e.g., sintering) | Minimal post-processing |
Binder jetting stands out as a versatile additive manufacturing process due to its speed, cost-effectiveness, design flexibility, and material options, surpassing other 3D printing technologies. Its evolution from rapid prototyping to functional part production underscores its increasing significance in modern manufacturing across diverse industries.
Types of Binder Jetting Materials
Metal Powders
Manufacturers widely use metal powders in binder jetting to create functional metal parts. Common metals include:
Steel: Used for industrial parts, tooling, and prototypes due to its strength and durability.
Titanium: Known for its high strength-to-weight ratio, corrosion resistance, and biocompatibility, suitable for aerospace, medical, and automotive applications.
Aluminum: Lightweight and corrosion-resistant, used in aerospace, automotive, and consumer goods.
Other metals such as cobalt-chrome, nickel alloys, and precious metals like gold and silver are also compatible with it, offering versatility in material selection for various applications.
Ceramic Powders
Manufacturers use ceramic powders in binder jetting to create parts with excellent heat resistance, electrical insulation, and chemical stability. Examples include:
Silicon Carbide: Known for its hardness and thermal conductivity, used in high-temperature applications.
Alumina: Offers excellent mechanical strength and electrical insulation, suitable for electronic components and wear-resistant parts.
Ceramic materials are valuable in industries such as electronics, aerospace, and medical where thermal and electrical properties are critical.
Composite Materials
Composite materials combine different materials to achieve specific properties like strength, flexibility, or electrical conductivity. Examples include:
Metal Matrix Composites: Combine metals with ceramic reinforcements for enhanced strength and wear resistance.
Polymer Matrix Composites: Include fibers like carbon or glass embedded in a polymer matrix for lightweight, strong parts.
These materials expand the applications of binder jetting into fields requiring tailored material properties, such as automotive, sports equipment, and aerospace.
Overview of Binder Types
Binders in binder jetting play a crucial role in adhering powder particles together during printing. They can be categorized into organic and inorganic types:
Organic Binders: Typically polymers or wax-based materials that provide good binding properties at lower temperatures. They are often used for their ease of removal during post-processing stages like debinding.
Inorganic Binders: Include materials like ceramics or metals that offer higher strength and stability at elevated temperatures. Inorganic binders are essential for applications requiring high-temperature resistance and durability.
The choice of binder depends on the specific material being printed and the desired properties of the final part. Manufacturers often optimize binder formulations to achieve the best balance of adhesion, strength, and processability for their applications.
In summary, binder jetting offers a versatile platform for producing parts from a range of materials including metals, ceramics, and composites, supported by different binder types to meet diverse industrial needs for functional and prototype production.
Metal Binder Jetting: Advancing the Technology
Definition and concept of metal binder jetting
Metal binder jetting is an advanced additive manufacturing technique where metal powder is selectively deposited and bound together layer by layer using a liquid binding agent. The process follows a similar principle to traditional binder jetting but focuses specifically on metal materials.
This method enables the production of complex metal parts with intricate geometries that may be difficult or impossible to achieve through traditional manufacturing methods.
How it enhances traditional binder jetting processes
Metal binder jetting represents an evolution from its predecessor, offering several enhancements:
Material Strength and Properties: Metal binder jetting allows for the production of parts with superior mechanical properties compared to plastic or ceramic binder jetting. Metals such as stainless steel, titanium, and aluminum can be used, offering high strength, corrosion resistance, and thermal properties.
Precision and Detail: Advances in printhead technology and binder formulations enhance the precision and resolution of metal binder jetting. This enables the production of fine details and complex geometries with high accuracy.
Application Diversity: Metal binder jetting expands the range of applications into industries requiring robust metal parts, such as aerospace, automotive, medical implants, and industrial tooling. It facilitates rapid prototyping as well as the production of end-use parts.
Examples of materials and applications
Stainless steel, titanium, and aluminum are pivotal in various industries. Stainless steel excels in applications needing robustness and corrosion resistance, such as brackets and surgical tools. Titanium stands out in aerospace for its lightweight properties and biocompatibility in medical implants. Aluminum is favored in the automotive and aerospace sectors for its strength-to-weight ratio in structural components.
These materials—stainless steel, titanium, and aluminum—are essential across industries. They enable lightweight, durable components in aerospace, enhance automotive performance, facilitate customized medical implants, and support precise industrial tooling applications.
The Process of Binder Jetting
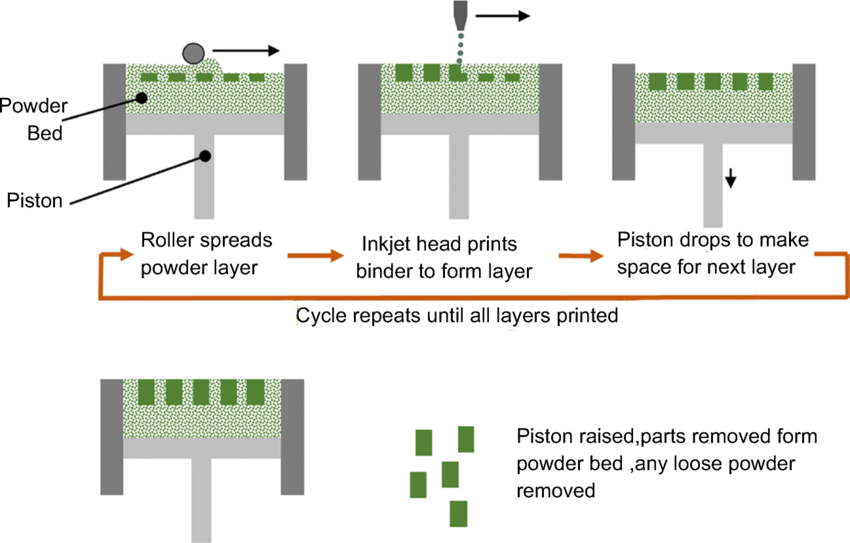
Source: researchgate.net
Layer-by-layer deposition
Preparation: The process begins with a digital 3D model of the part that needs to be produced. This model is sliced into thin cross-sectional layers, typically ranging from 20 to 100 microns in thickness, depending on the specific technology and material used.
Powder Bed Preparation: A thin layer of powder material (metal, ceramic, or composite) is evenly spread across the build platform using a recoating mechanism.
Binder Deposition: A print head or inkjet nozzle selectively deposits a liquid binding agent onto the powder bed according to the pattern dictated by the digital model. This binding agent binds the powder particles together at the specific locations corresponding to the cross-section of the part being produced.
Layer Compaction: After each layer is selectively bound, the build platform typically moves down by one layer thickness, and the process repeats. The new layer of powder is spread over the previous one, and the binder is deposited again, adhering to the previous layer and building up the part incrementally.
Support Structure: Unbound powder acts as a support structure for overhanging features and complex geometries. This support allows for the construction of intricate designs without additional support structures often required in other manufacturing methods.
Role of the binder material
The binder material plays a critical role in the binder jetting process:
Adhesion: The binder serves to adhere powder particles together to form a cohesive layer that solidifies into a part after post-processing.
Control: It controls the bonding strength between particles and influences the mechanical properties of the final part.
Flexibility: Different binders can be used to adjust properties like viscosity, drying time, and thermal stability, optimizing the process for specific materials and applications.
The choice of binder material depends on factors such as the type of powder material being used, desired mechanical properties of the final part, and compatibility with post-processing steps.
Post-processing techniques
After the binder jetting process is complete, the printed parts undergo post-processing steps to achieve the desired mechanical properties and surface finish:
Curing: Involves drying the binder and solidifying the part by exposing it to heat or ultraviolet light. Curing increases the strength of the binder and prepares the part for subsequent processing steps.
Sintering: For metal parts, sintering is a crucial step where the part is heated to a temperature below its melting point. This causes the metal particles to fuse together, eliminating porosity and increasing density and strength. Sintering also enhances the mechanical properties of the part, making it suitable for functional applications.
Infiltration: In some cases, especially for porous materials like ceramics, infiltration is used to impregnate the part with a secondary material (often a resin or metal) to further improve mechanical properties, density, and surface finish.
Support Removal: Any remaining unbound powder that acts as a support structure is removed using methods such as brushing, blowing, or vacuuming. This step ensures that the final part maintains its intended shape and integrity.
Finishing: Finally, parts may undergo finishing processes such as machining, polishing, or coating to achieve specific surface textures, tolerances, or aesthetic requirements.
In conclusion, binder jetting creates complex parts by depositing layers of powder bound with liquid agents. Post-processing steps like curing, sintering, and infiltration enhance part strength and precision, making it ideal for diverse industrial applications.
Advantages and Challenges of Binder Jetting
Advantages of Binder Jetting
Speed and Efficiency
Binder jetting produces complex parts faster than traditional manufacturing methods due to its layer-by-layer deposition process. It reduces lead times and allows for rapid iteration in product development.
Cost-effectiveness
Compared to traditional manufacturing techniques, binder jetting can be more cost-effective for producing low to medium volumes of parts. It eliminates the need for expensive tooling and reduces material waste.
Design Flexibility
Binder jetting allows for the production of highly complex geometries and intricate designs that conventional methods cannot easily achieve. Designers have greater freedom to create innovative shapes and internal structures optimized for performance.
Ability to Produce Complex Geometries and Lightweight Structures
The layer-by-layer approach of binder jetting allows for the creation of lightweight structures with optimized internal geometries, reducing overall weight without compromising strength. This capability is beneficial in industries like aerospace and automotive, where weight reduction is critical for fuel efficiency and performance.
Comparison with Other Metal 3D Printing Technologies (SLS, DMLS, etc.)
Binder jetting can be more cost-effective and faster than selective laser sintering (SLS) or direct metal laser sintering (DMLS) for certain applications.It offers comparable or superior surface finish and resolution, making it suitable for a wide range of industrial applications.
Challenges and Limitations
Mechanical Properties of Printed Parts
Parts produced through binder jetting may exhibit lower mechanical properties compared to parts made through traditional manufacturing methods or other 3D printing technologies. This can restrict their use in applications requiring high tensile strength, fatigue resistance, or durability.
Material Limitations and Availability
The range of materials available for binder jetting may be limited compared to other manufacturing methods. Specialized materials with specific properties (e.g., high temperature resistance, biocompatibility) may be harder to find or more expensive.
Post-processing Requirements
Parts produced by binder jetting often require extensive post-processing steps such as curing, sintering, or infiltration to achieve desired mechanical properties and surface finish. These additional steps can increase production time and cost, offsetting some of the initial cost advantages of binder jetting.
Comparison of Final Product Quality with Traditional Manufacturing Methods:
Achieving the same level of surface finish, dimensional accuracy, and mechanical properties as traditional manufacturing methods can be challenging. Critical applications may require parts with properties that can only be reliably achieved through conventional manufacturing techniques.
In summary, binder jetting offers speed, cost-effectiveness, and design flexibility for complex structures, yet faces challenges with mechanical properties, material availability, post-processing, and achieving traditional manufacturing quality.
Applications of Binder Jetting
Industrial Manufacturing
Binder Jetting is widely used for rapid prototyping, enabling quick testing and refinement of designs. It also produces custom tools, jigs, and fixtures efficiently, and can manufacture end-use parts with complex geometries, making it valuable for small production runs.
Automotive and Aerospace Industries
In the automotive and aerospace sectors, Binder Jetting creates lightweight, intricate parts like turbine blades and fuel nozzles, enhancing performance and fuel efficiency. It is also used for prototyping, producing custom parts, and manufacturing on-demand spare parts, reducing downtime and inventory costs.
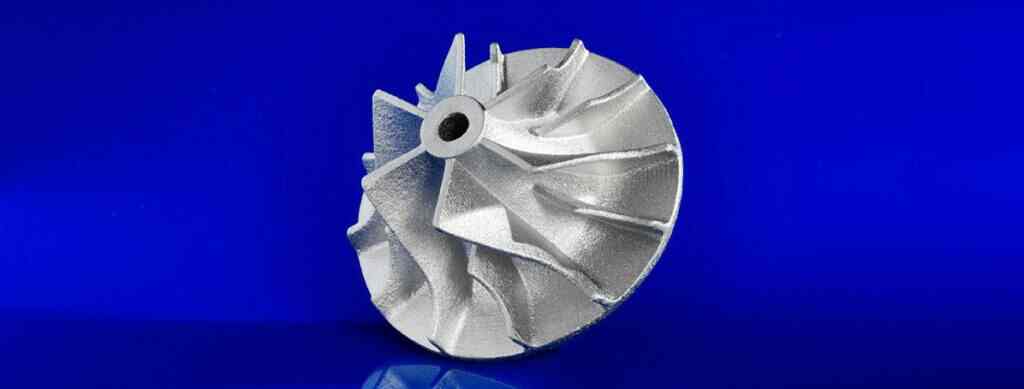
Source: ifam.fraunhofer.de
Medical and Dental Applications
Binder Jetting produces custom implants, prosthetics, and dental devices tailored to individual patients. It also creates precise surgical tools and guides, and detailed anatomical models for surgical planning and education, improving outcomes and accuracy in medical procedures.
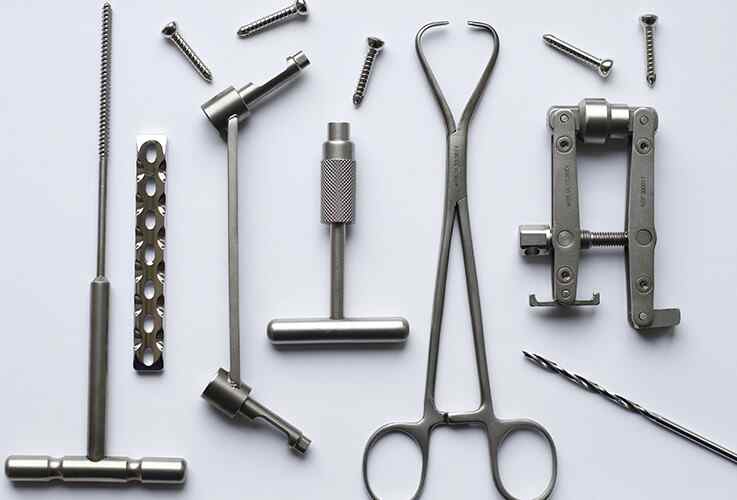
Source: microcare.com
Custom and Complex Part Production
This technology excels in producing parts with complex geometries that are difficult to achieve with traditional methods. It supports low-volume production and multi-material printing, allowing for rapid design iterations and the creation of parts with varied properties, such as combining different metals or integrating ceramic elements.
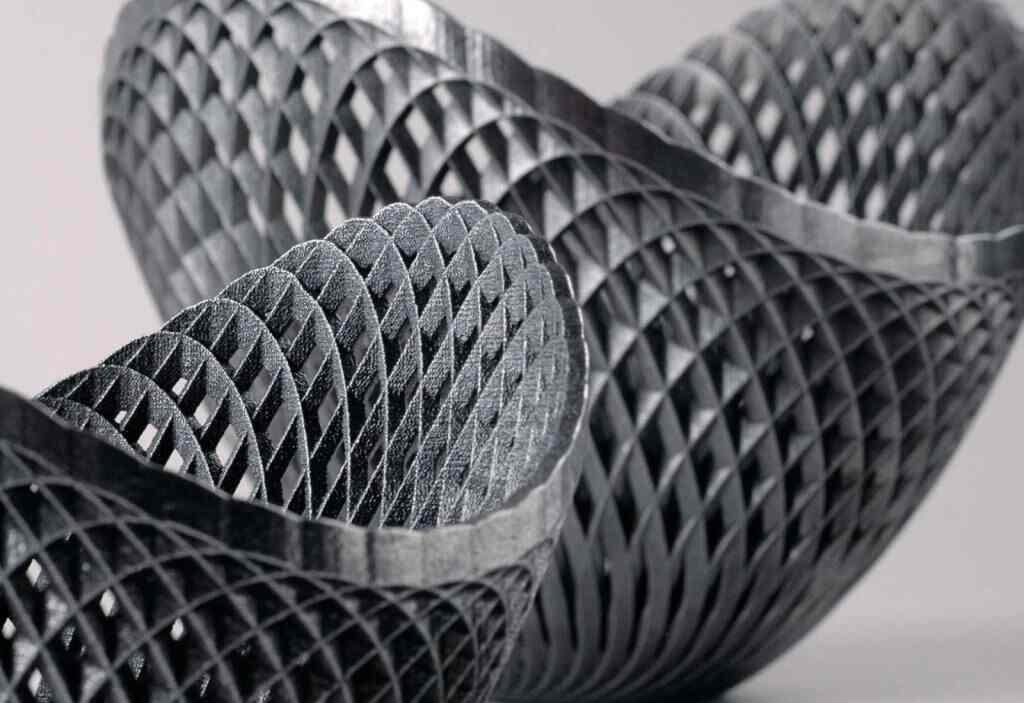
Source: hubs.com
Future Trends in Binder Jetting
Advancements in Technology
Future Binder Jetting technology aims to rival traditional manufacturing methods by improving resolution and speed. Enhanced material handling systems will broaden material options, while integrating with CNC machining and advanced post-processing techniques will optimize part properties and surface finishes.
Expansion into New Materials
Binder Jetting technology expands across sectors like aerospace and automotive, emphasizing advanced metals for high-performance needs. It also explores ceramics, composites, and bio-compatible materials for specialized components, advancing healthcare technologies.
Market Growth and Industry Impact
The Binder Jetting market shows strong growth potential, particularly in consumer goods and healthcare sectors. Its ability to minimize waste and facilitate customized production promises cost efficiencies, potentially disrupting traditional supply chains.
By enabling localized production, Binder Jetting could significantly reduce lead times, reshaping logistics and distribution models.
As demand increases, there's a growing demand for skilled Binder Jetting operators, prompting advancements in education and training to foster industry expansion and innovation.
Conclusion
Binder jetting is a game-changer in additive manufacturing, especially for metals and ceramics. With ongoing advancements, it offers faster, cost-effective production and unmatched design flexibility.
By embracing these innovations, manufacturers can revolutionize their industries, meeting diverse needs and fostering innovation.
Unionfab: Fulfilling Your Diverse Manufacturing Requirements
Unionfab provides comprehensive manufacturing solutions across various industries. Our range of services, such as 3D printing and CNC machining, addresses a wide array of needs.
For more information, feel free to contact us through our Contact Us page.
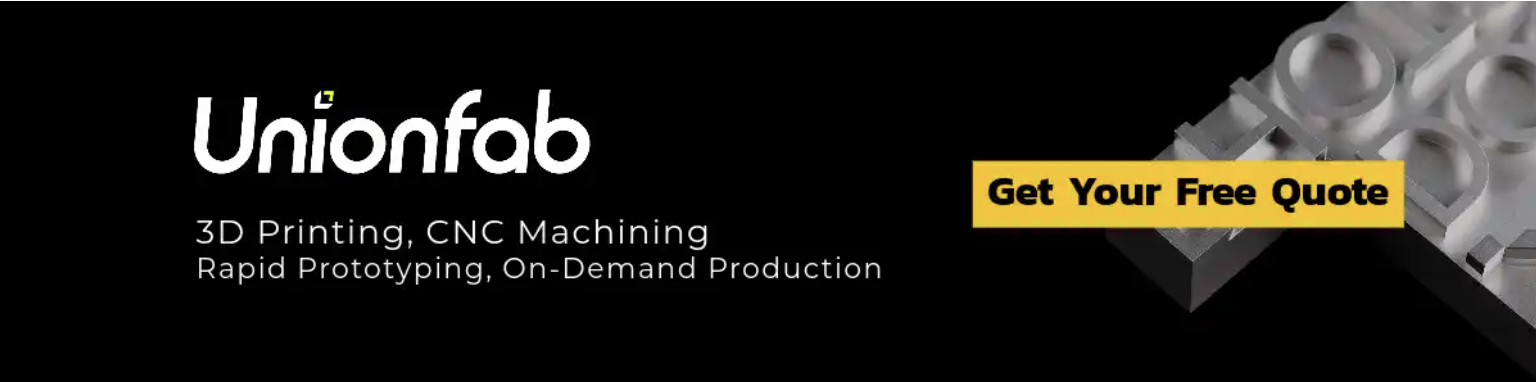