Alodine vs. Anodize: Understanding the Key Differences and Applications
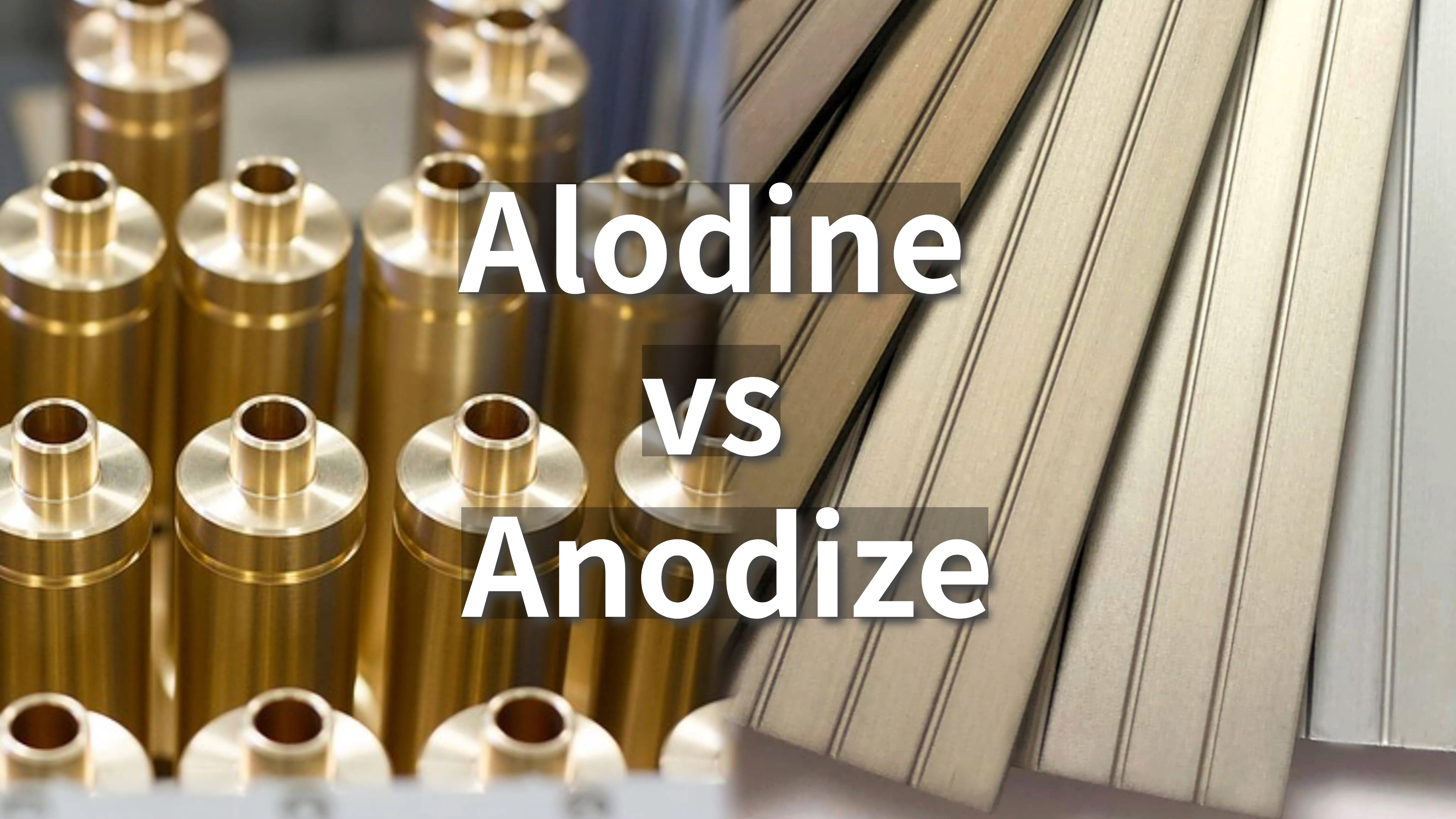
Discover the key differences between Alodine and anodize coatings. Find out which one offers superior protection and performance for metal parts.
Introduction
Metal finishing is a process that involves treating metal surfaces to improve their appearance, durability, and resistance to corrosion. It is crucial in various industries, from automotive and aerospace to electronics and architecture.
Two common metal finishing techniques are Alodine and Anodize. Both processes create protective layers on metal surfaces, but they differ in their methods, characteristics, and applications.
This article will explore the fundamentals of these coatings, highlighting their key differences and suitable applications.
Alodine Coating: A Chemical Conversion Coating
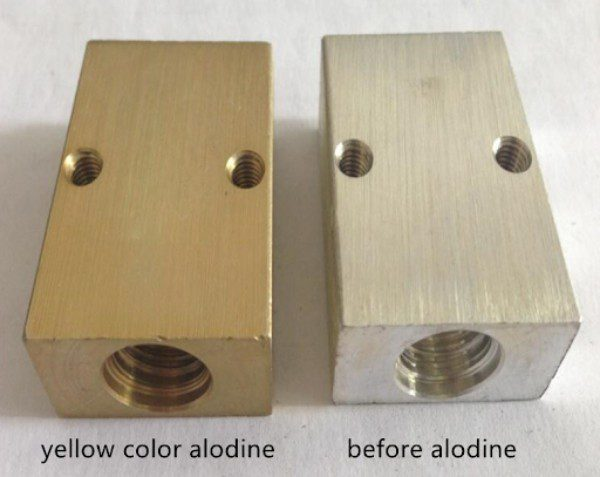
Alodine is a type of coating applied to metal surfaces to protect them from corrosion. Unlike paint, which simply covers the metal, alodine actually reacts with the metal to form a protective layer. This process is called chemical conversion.
Benefits of Alodine
Corrosion Resistance: Alodine provides excellent protection against rust and other forms of corrosion.
Paint Adhesion: Paint sticks better to metal surfaces that have been treated with Alodine, resulting in a longer-lasting finish.
Drawbacks of Alodine
Limited Thickness: The Alodine coating is very thin, which means it offers less protection than some other coatings.
Aesthetic Appeal: Alodine does not change the appearance of the metal significantly, and it may not have the same shiny or colorful look as other finishes.
Anodizing: An Electrochemical Process
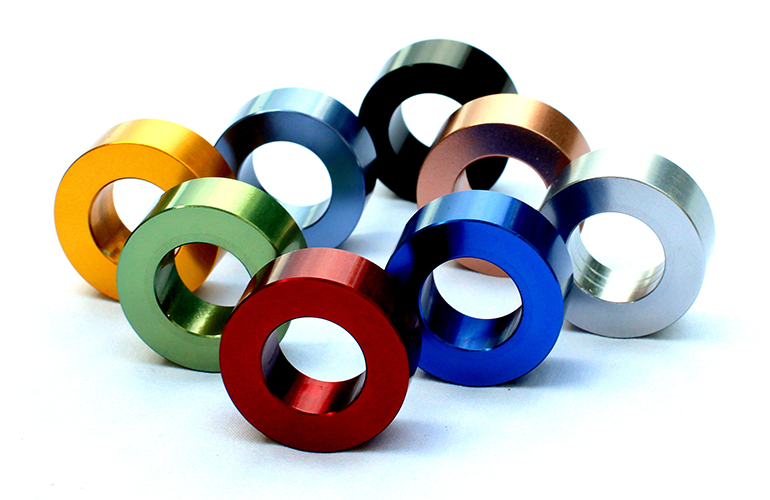
Anodizing is another method used to protect metal surfaces, primarily aluminum.
Unlike Alodine, anodizing involves an electrochemical process. This means that electricity is used to create a protective layer on the metal.
The Anodizing Process
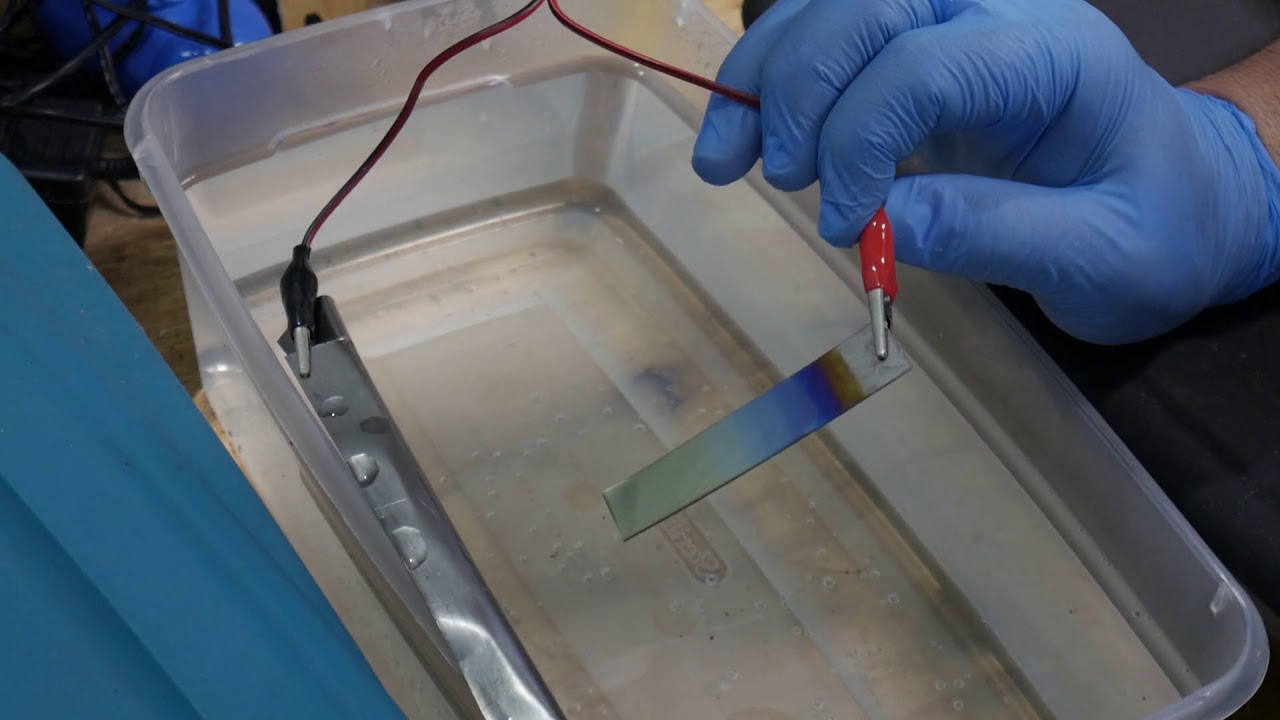
The metal part is placed in an electrolytic solution and given a positive electrical charge.
Oxygen from the solution reacts with the metal, creating a tough, corrosion-resistant oxide layer on the surface. This layer is thicker and more durable than the one formed by alodine.
Benefits of Anodizing
Durability: Anodized coatings are very hard and resistant to wear and tear.
Corrosion Resistance: Anodizing provides excellent protection against corrosion.
Color Options: Anodized coatings’ versatile color choices makes it a popular choice for decorative applications.
Drawbacks of Anodizing
Cost: Anodizing is generally more expensive than Alodine.
Hydrogen Embrittlement: In some cases, the anodizing process can cause hydrogen to become trapped in the metal, which can make it brittle. This is a concern in certain applications.
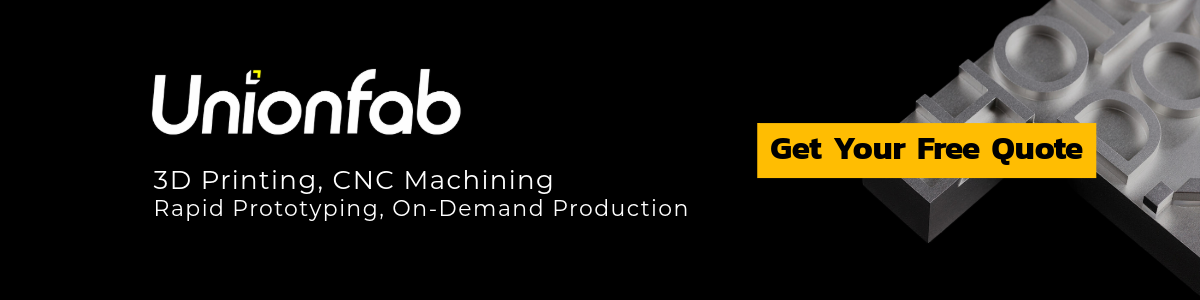
Industrial Applications: Alodine vs. Anodize
Alodine and anodizing, while both protective coatings for metals, are used in different industries based on their specific properties.
Alodine Applications
Alodine is commonly used in industries where corrosion resistance and paint adhesion are crucial. Some examples include:
Aerospace
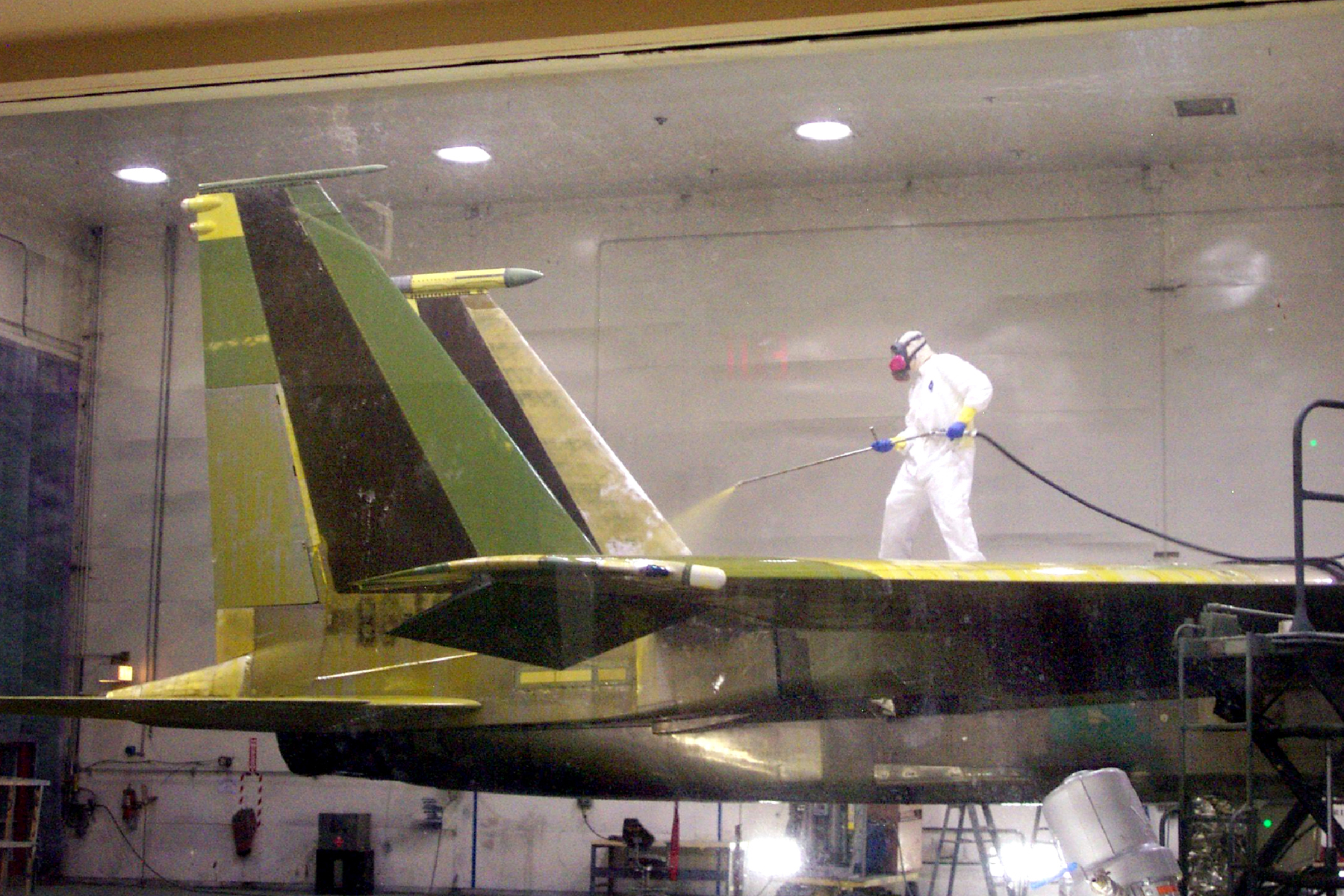
Aircraft parts require coatings that can withstand harsh environmental conditions and provide a strong base for paint.
Automotive
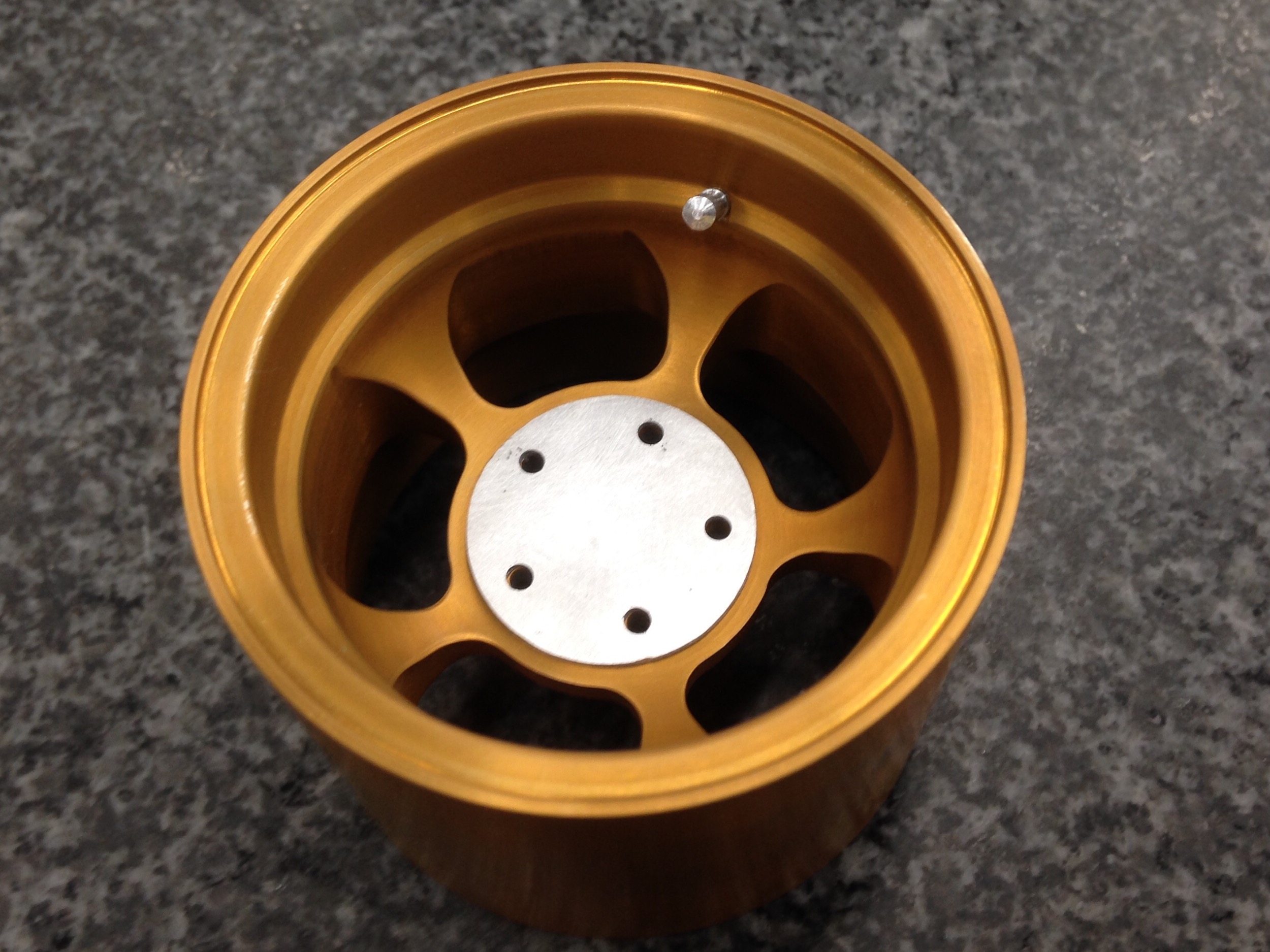
Car parts, especially those exposed to the environment, benefit from Alodine's corrosion protection.
Anodizing Applications
Anodizing is preferred in industries that demand durability, corrosion resistance, and often, aesthetic appeal. Common applications include:
Architecture
Building components, such as window frames and exterior panels, are often anodized due to its durability and resistance to weather.
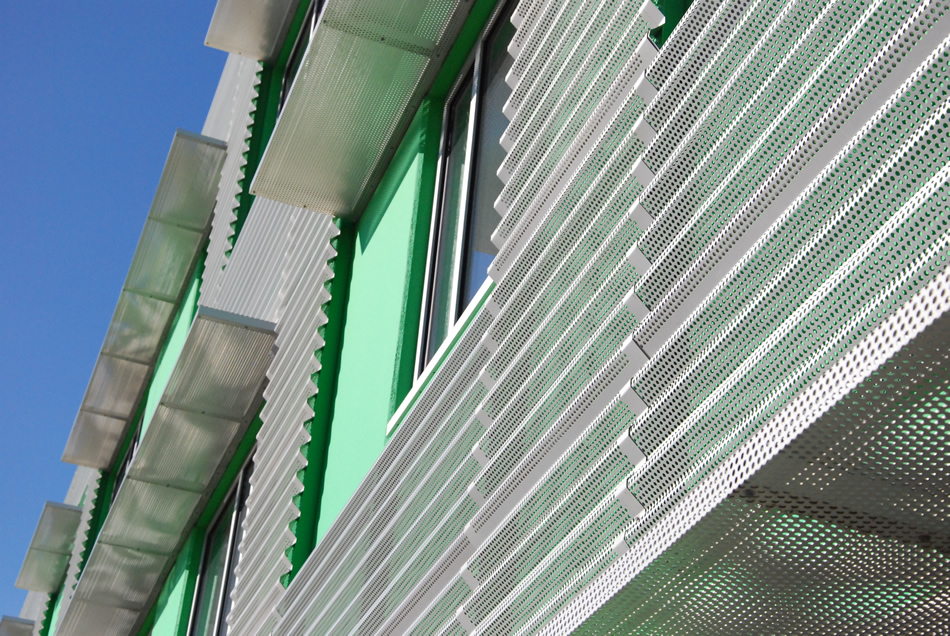
Automotive
Anodizing is widely used in the automotive industry to improve the durability, appearance, and corrosion resistance of metal components, especially aluminum.
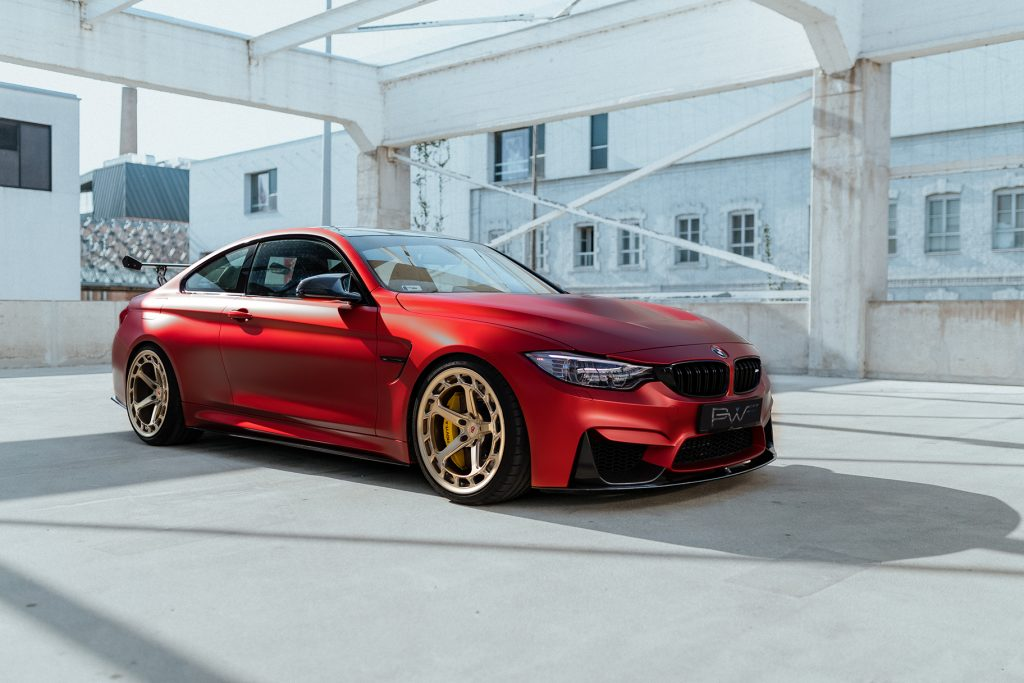
When wrapping a car with a vinyl wrap, an anodized surface provides a smooth, durable base that enhances adhesion. The protective anodized layer helps prevent damage to the metal underneath when wraps are applied and removed.
Electronics
Anodized aluminum is used in electronics because of its electrical insulating properties and ability to withstand heat.
Key Differences: Alodine vs. Anodize
Process Comparison
Alodine: This process involves immersing the metal in a chemical solution. A chemical reaction occurs, creating a thin protective layer on the metal's surface.
Anodizing: This process uses electricity to create a thicker, harder protective layer on the metal. The metal is placed in an electrolytic solution and connected to an electrical current.
Appearance and Texture
Alodine: Typically results in a clear or slightly yellowish coating. The texture is smooth to the touch.
Anodizing: Can produce a variety of finishes, from clear to colored. The texture is often harder and more durable than Alodine.
Performance Comparison
Feature | Alodine | Anodize |
---|---|---|
Corrosion Resistance | Good | Excellent |
Wear Resistance | Moderate | High |
Abrasion Resistance | Moderate | High |
Choosing the Right Coating: Alodine or Anodize?
Selecting the appropriate coating for a metal part is crucial for its performance and lifespan. To make an informed decision between Alodine and Anodize, consider the following factors:
Factors to Consider
Corrosion Resistance: If the metal part will be exposed to harsh environments, anodizing offers superior protection due to its thicker and harder coating.
Durability: For applications involving frequent wear and tear, anodizing's durability is preferred. Alodine is suitable for less demanding conditions.
Appearance: Anodizing provides a wider range of color options and finishes, making it a better choice for aesthetic purposes. Alodine typically results in a clear or slightly yellowish coating.
Cost: Alodine is generally more cost-effective than anodizing.
Paint Adhesion: If the part will be painted, Alodine is often preferred as it provides a better base for paint to adhere to.
Selecting the Right Coating
Based on the specific requirements of the metal part, you can choose between alodine and anodize:
Choose Alodine if:
Corrosion resistance is needed but not the highest level.
The part will be painted.
Cost is a primary concern.
Choose Anodizing if:
Maximum corrosion resistance and durability are required.
A variety of colors and finishes are desired.
The part will be exposed to significant wear and tear.
Conclusion
Alodine is a cost-effective option that excels in providing good corrosion resistance and a strong base for paint adhesion.
Anodizing offers superior durability, corrosion resistance, and a wider range of colors and finishes.
Ultimately, the best choice depends on the specific requirements of your project. Consider factors like corrosion resistance, durability, appearance, and cost to make an informed decision.
Trust Unionfab for High-Quality Finishing Solutions
Whether you need surface finishing, metal treatment, material coating or custom coloring - Unionfab has the expertise to elevate your products.
We offer a comprehensive range of finishing processes, from anodizing and plating and polishing, to painting, laser marking and more. Contact our team today to discuss your finishing needs and request a free quote.