Automotive Injection Molding: Techniques and Solutions Explored
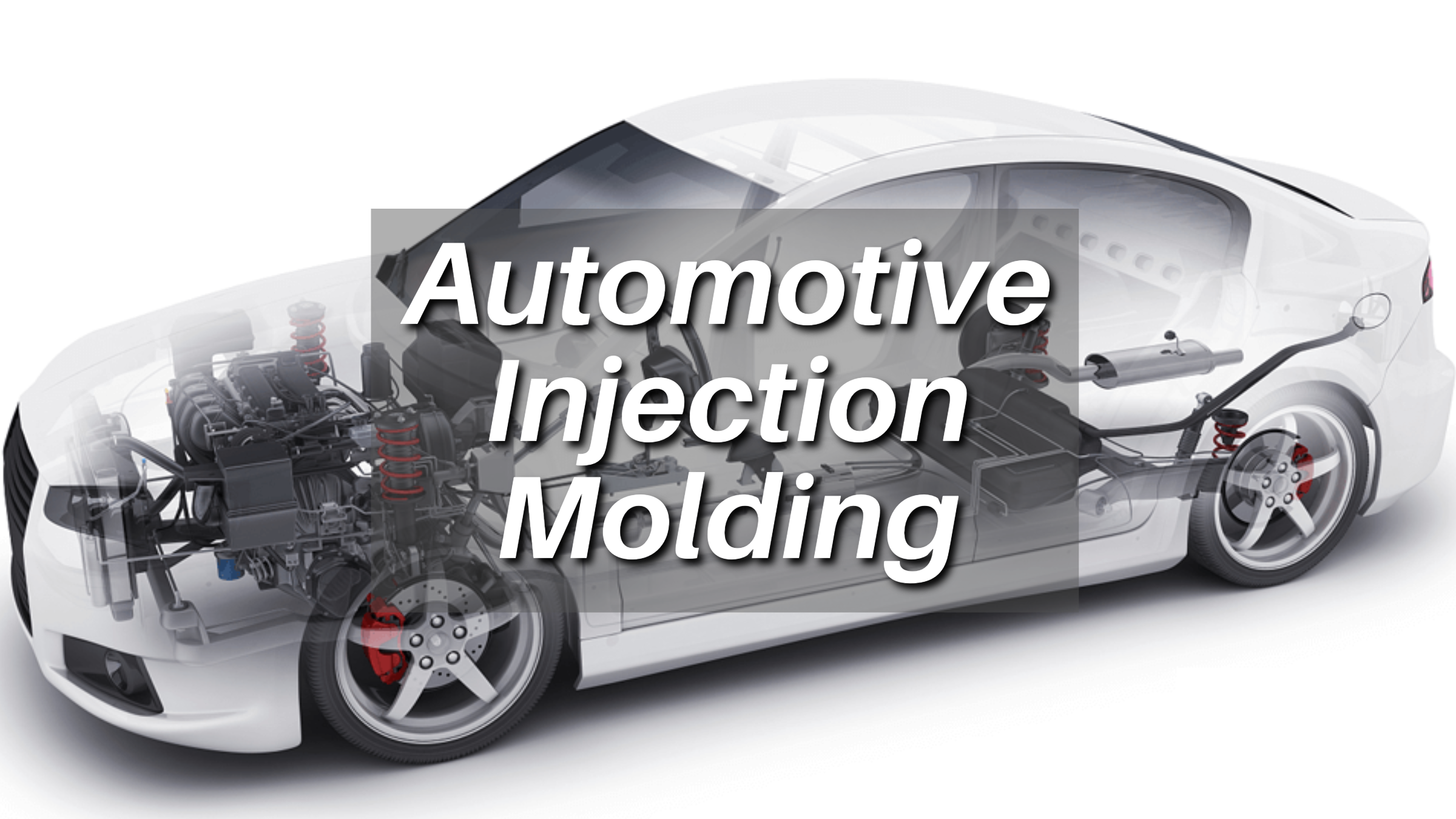
This article explores the manufacturing process of automotive injection molding as well as its advantages and applications in automobile manufacturing.
Introduction
Automotive injection molding is a pivotal process in modern vehicle manufacturing, offering unparalleled precision and efficiency in producing various components. This guide provides an overview of automotive injection molding, emphasizing its significance, materials, and key processes.
Understanding Injection Molding
Overview Of Automotive Injection Molding
Automotive injection molding encompasses a diverse range of components essential for vehicle construction, including:
- Interior Components: Dashboard panels, door handles, and trim pieces.
- Structural Elements: Engine covers, air intake manifolds, and battery housings.
This process is integral to achieving lightweight yet durable parts that meet the stringent requirements of the automotive sector.
Importance Of Injection Molding In Automotive Industry
Injection molding is crucial in the automotive industry for its ability to produce lightweight parts, enhancing fuel efficiency and vehicle performance.
It also enables rapid prototyping and mass production, reducing time-to-market and enhancing overall efficiency.
Moreover, its capability to achieve tight tolerances and intricate designs ensures that automotive parts meet stringent quality and safety standards, underscoring its significance in the automotive sector.
Materials Used in Automotive Injection Molding
A wide variety of polymers are employed in automotive injection molding to meet the diverse requirements of different components.Common materials include:
- Polypropylene (PP): Known for its lightweight nature and excellent chemical resistance, PP is commonly used in interior components and under-the-hood parts.
- Polyethylene (PE): PE offers high impact strength and flexibility, making it suitable for applications such as fuel tanks and reservoirs.
- Acrylonitrile Butadiene Styrene (ABS): ABS is valued for its toughness and heat resistance, making it ideal for exterior trim components and interior panels.
- Nylon: Nylon offers excellent strength and durability, often used in components requiring high mechanical performance, such as gears and bearings.
- Polycarbonate (PC): PC is prized for its optical clarity and impact resistance, making it suitable for applications such as headlamp lenses and instrument panels.
By carefully selecting materials based on their mechanical properties, chemical resistance, and aesthetic characteristics, automotive manufacturers can ensure that injection-molded parts meet the demanding requirements of vehicle design and performance.
Processes of Automotive Injection Molding
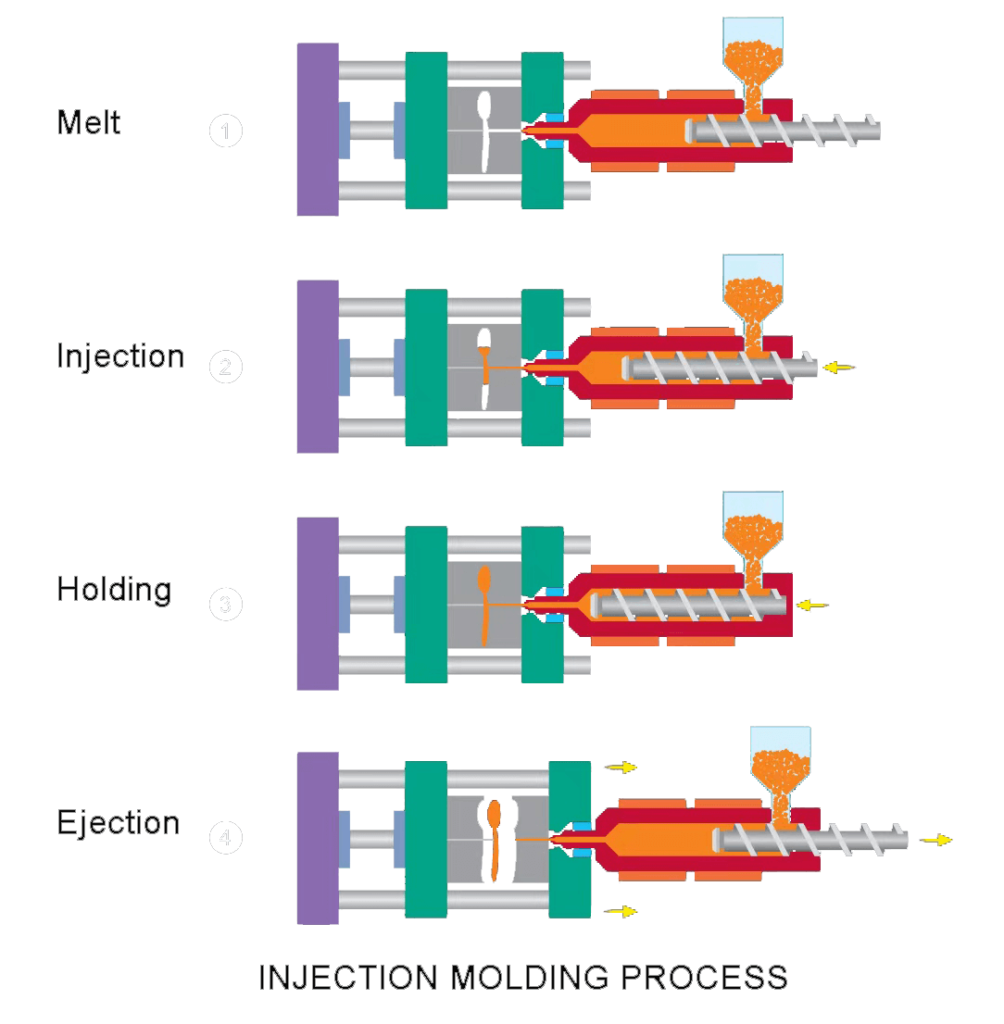
Source: plasticmoulds.net
Step 1. Material Selection
The process begins with careful selection of materials based on the desired properties and performance requirements of the finished part.
Factors such as strength, durability, chemical resistance, and aesthetic appearance are taken into consideration during material selection.
Step 2. Material Preparation
Selected materials are then prepared for injection molding by melting and homogenizing them to achieve uniformity and consistency.
This step involves feeding the raw material into a hopper, where it is heated and melted to the appropriate temperature for injection.
Step 3. Injection
Once the material is prepared, it is injected into the mold cavity under high pressure using an injection molding machine.
The material fills the mold cavity, taking on its shape and configuration.
Step 4. Cooling
After injection, the molten material undergoes a cooling process to solidify within the mold cavity.
Controlled cooling ensures that the part achieves the desired shape and structural integrity.
Step 5. Ejection
Once the material has cooled and solidified, the finished part is ejected from the mold cavity using ejector pins or other mechanisms.
Careful ejection is essential to prevent damage to the part or the mold.
Step 6. Trimming and Finishing
After ejection, excess material, known as flash, is trimmed away from the part using precision cutting tools.
The part may also undergo additional finishing processes, such as surface polishing or painting, to achieve the desired appearance and functionality.
Step 7. Quality Control
Throughout the injection molding process, rigorous quality control measures are implemented to ensure that parts meet specified requirements.
This includes inspection of dimensions, surface finish, and mechanical properties to identify any defects or deviations from standards.
Step 8. Regrinding and Recycling
Scrap material generated during the injection molding process is collected and reprocessed through grinding into small pellets.
These pellets can then be reused in subsequent injection molding cycles, reducing waste and enhancing sustainability.
By meticulously executing each of these processes, automotive manufacturers can achieve consistent, high-quality production of injection-molded parts essential for vehicle construction and performance.
Quality Control in Automotive Injection Molding
Design Review
Before production begins, a thorough design review assesses the feasibility of the design for injection molding.
- Feasibility Analysis: Evaluating the design to ensure it can be manufactured efficiently with injection molding techniques.
- Optimization: Making necessary adjustments to the design to reduce potential manufacturing challenges and optimize manufacturability.
- Risk Reduction: Identifying and mitigating risks that could lead to defects, thus enhancing the overall quality of the final product.
Production Preparation
During production setup, meticulous attention ensures that equipment and processes are configured correctly.
- Material Selection: Choosing appropriate mold materials based on the specific requirements of the automotive part.
- Machine Configuration: Setting up injection molding machines with the correct parameters to ensure consistent production.
- Parameter Calibration: Calibrating temperature, pressure, and other critical parameters to minimize variability and ensure adherence to quality standards.
In-Process Control
Continuous monitoring of key parameters during injection molding is essential to maintaining process stability.
- Key Parameters: Tracking variables such as pressure, temperature, cycle time, and part weight.
- Real-Time Monitoring: Using sensors and software to monitor the process in real-time, allowing for immediate adjustments.
- Defect Prevention: Promptly identifying and addressing issues to prevent defects, ensuring that parts consistently meet specifications.
Final Inspection
Every automotive injection-molded part undergoes a comprehensive final inspection post-production.
- Dimensional Accuracy: Measuring parts to ensure they meet precise dimensional specifications.
- Surface Finish: Inspecting the surface quality to ensure it meets aesthetic and functional requirements.
- Structural Integrity: Performing functional tests to verify the part's strength and durability.
- Defect Identification: Conducting rigorous inspections to identify and eliminate defects, ensuring that only high-quality parts are shipped to customers.
By implementing robust quality control measures throughout the automotive injection molding process, manufacturers can uphold the highest standards, delivering reliable, defect-free parts that meet the rigorous demands of the automotive industry.
Advantages of Injection Molding Automotive Parts
Design Flexibility and Complexity
Injection molding enables the creation of intricate designs and complex geometries that are difficult to achieve with other methods.
This flexibility optimizes performance and aesthetics, fostering innovation in vehicle design and market differentiation.
Rapid Prototyping and Production
Automotive manufacturers can quickly prototype and produce parts with injection molding, reducing time-to-market.
Advanced CAD/CAM software and molding techniques streamline the process, enhancing efficiency in development cycles.
Consistency and Precision
Injection molding ensures exceptional consistency and precision in part production, maintaining uniformity in dimensions, surface finish, and mechanical properties across large production runs.
Strict quality control measures guarantee that each part meets exact specifications, ensuring reliable performance.
Cost-Effectiveness and Material Efficiency
Injection molding offers cost-effective manufacturing solutions by minimizing material waste, labor costs, and production time compared to traditional methods.
Precise material control and optimized part geometry maximize material efficiency, reducing overall production costs.
Integration of Multiple Components into Single Parts
Injection molding allows for the integration of multiple components into single parts, simplifying manufacturing processes and reducing assembly time and part count.
Consolidating functions into a single molded part improves efficiency, lowers costs, and enhances product reliability and performance.
Applications of Automotive Injection Molding
Lighting Components
Injection molding is commonly used to produce intricate lighting components, including:
- Headlamp Housings: These housings provide protection and support for headlamp assemblies, ensuring proper alignment and durability.
- Tail Lamp Bezels: Tail lamp bezels enhance the aesthetic appeal of vehicle rear-end designs while providing structural support for tail lamp assemblies.
- LED Light Guides: Injection-molded light guides are utilized in modern automotive lighting systems to distribute and diffuse light efficiently.
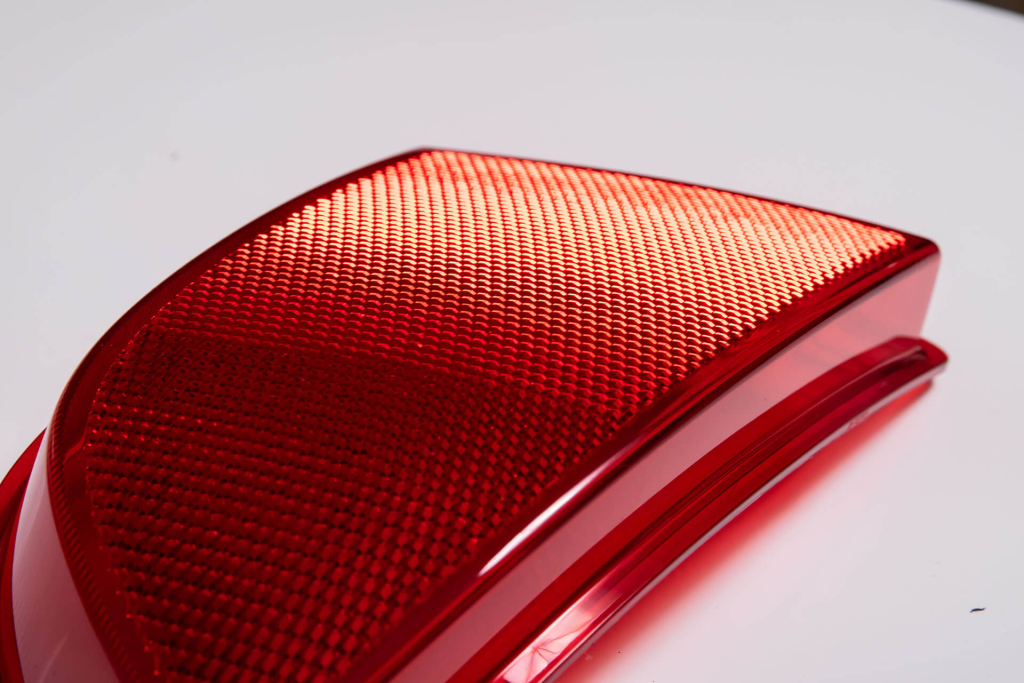
Source: global-plastics.com
Under-the-Hood Components
Under-the-hood components manufactured through injection molding include:
- Engine Covers: Engine covers protect the engine compartment from debris and contaminants while providing thermal insulation and noise reduction.
- Air Intake Manifolds: Injection-molded air intake manifolds control the flow of air into the engine cylinders, optimizing performance and fuel efficiency.
- Battery Housings: Battery housings securely encase automotive batteries, protecting them from external damage and ensuring safe operation.
- Reservoirs and Tanks: Injection-molded reservoirs and tanks store fluids such as coolant, windshield washer fluid, and hydraulic fluids, contributing to the proper functioning of vehicle systems
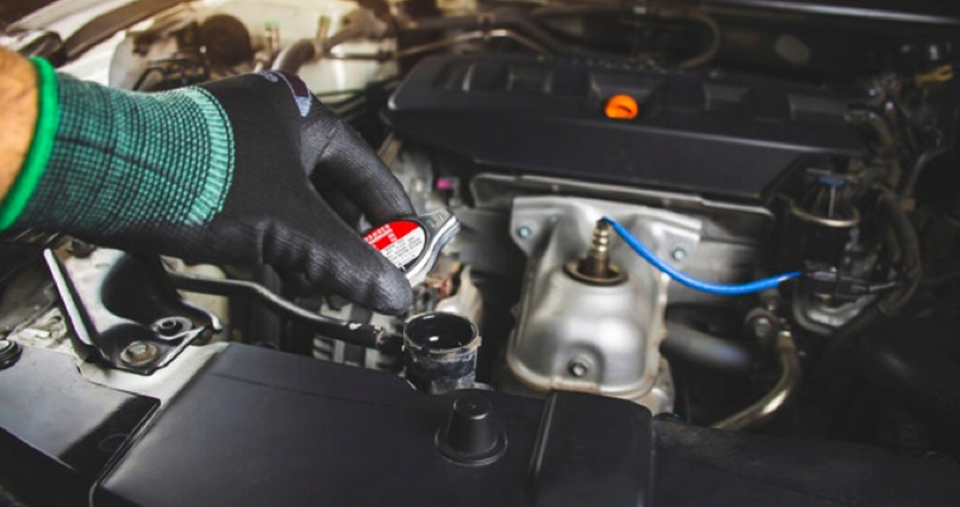
Source: ideastampi.com
Functional and Structural Components
Functional and structural components produced through injection molding include:
- Fasteners and Clips: Injection-molded fasteners and clips are used for securing various automotive components, offering reliable attachment and ease of installation.
- HVAC Components: Heating, ventilation, and air conditioning (HVAC) components such as vents, ducts, and control knobs are commonly manufactured through injection molding.
- Gaskets and Seals: Injection-molded gaskets and seals ensure leak-proof connections and prevent fluid or gas leakage in critical automotive systems.
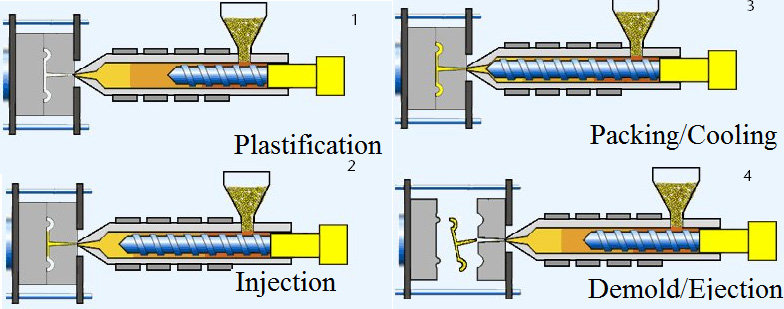
Source: splasticinjectionmould.com
Safety Components
Safety-critical components manufactured through injection molding include:
- Airbag Housings: Injection-molded airbag housings provide structural support and protection for airbag modules, ensuring reliable deployment and occupant safety in the event of a collision.
- Seatbelt Components: Injection-molded seatbelt components, including buckles, anchors, and retractors, play a crucial role in securing occupants and mitigating injury during vehicle collisions.
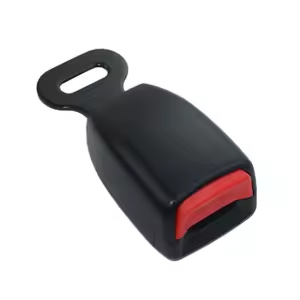
Source: s.alicdn.com
Electrical and Electronic Components
Injection molding is widely used to produce electrical and electronic components, including:
- Connector Housings: Injection-molded connector housings provide secure connections for electrical wiring and components, ensuring reliable signal transmission and electrical integrity.
- Sensor Housings: Housings for automotive sensors, such as temperature sensors, pressure sensors, and proximity sensors, are manufactured through injection molding to protect sensitive electronics from environmental factors.
- Control Modules: Injection-molded control modules house electronic control units (ECUs) and other electronic components, facilitating the operation and control of various vehicle systems.
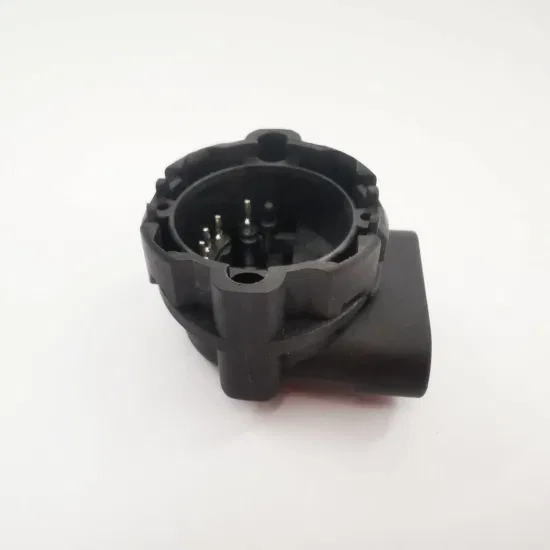
Source: golden-light.en.made-in-china.com
These applications highlight the vital role of automotive injection molding in producing high-quality, reliable, and cost-effective components.
Its versatility and efficiency drive innovation in the automotive industry, contributing to safer and more advanced vehicles.
Conclusion
Automotive injection molding stands as a cornerstone in modern automobile manufacturing, offering unparalleled versatility, precision, and efficiency in producing a wide range of components.
With its ability to meet the stringent requirements of the automotive industry, injection molding continues to drive innovation and excellence in vehicle design and production.
Unionfab: Meet Your Diverse Manufacturing Needs
Unionfab provides comprehensive manufacturing solutions for diverse industries, including automotive injection molding.
Additionally, we offer a wide range of essential services, such as 3D Printing and CNC machining, to meet various needs.
For more information, feel free to contact us through our Contact Us page.
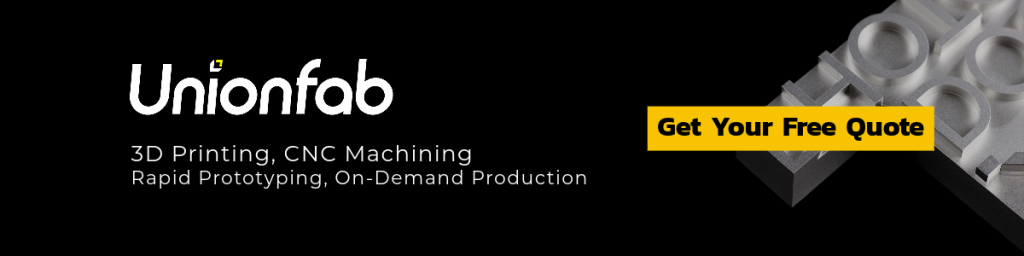