Additive Manufacturing | A Beginner’s Guide
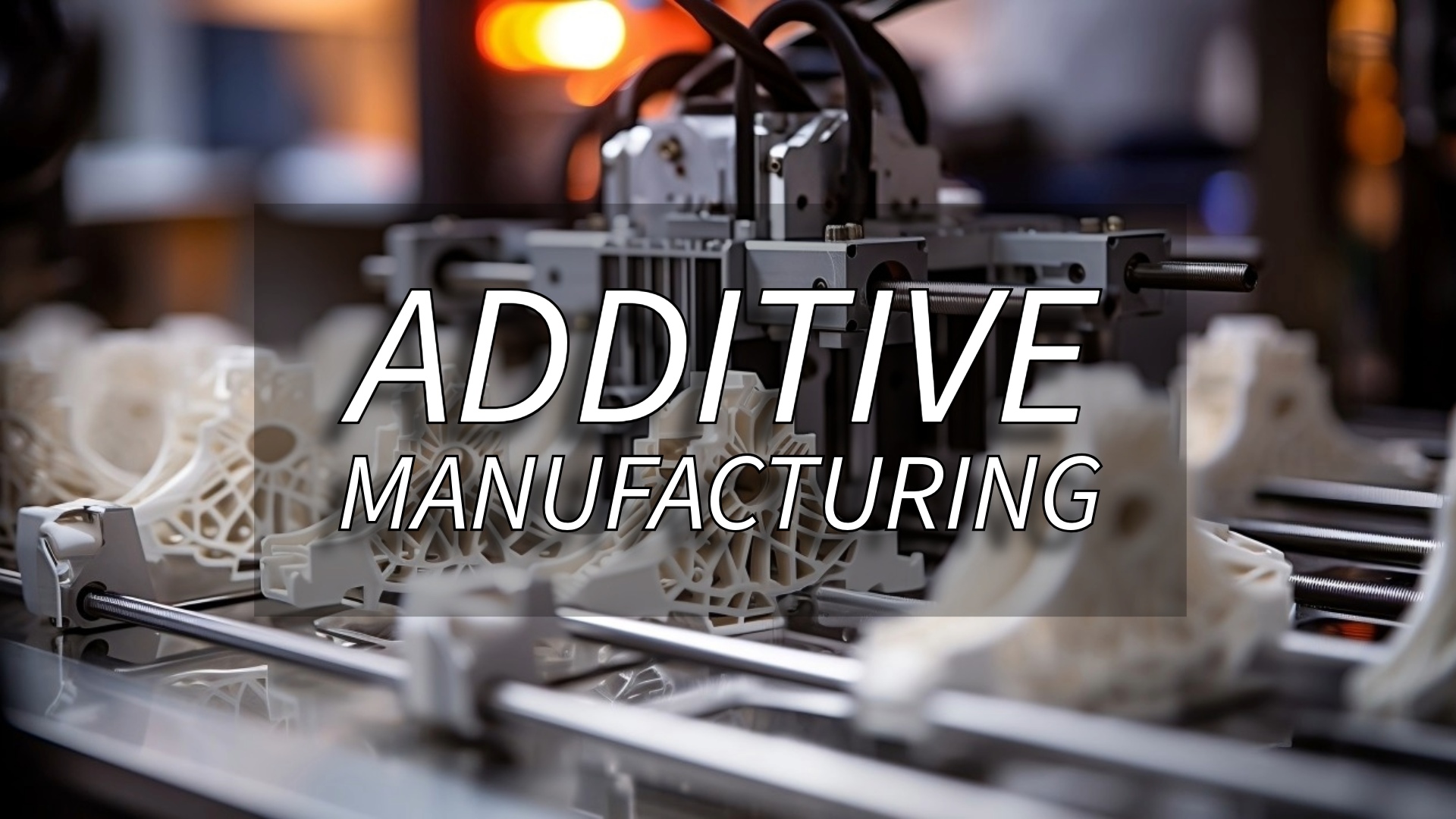
A beginner's complete guide to additive manufacturing from its definition, materials, processes, and applications.
Introduction
Additive manufacturing, or 3D printing, is a process that builds objects layer by layer from digital models. Unlike traditional methods that cut away material, additive manufacturing creates parts from the ground up, offering more design flexibility and efficiency.
Additive manufacturing is revolutionizing industries like aerospace, automotive, healthcare, and consumer products. Its ability to produce complex designs, minimize waste, and speed up prototyping makes it a vital technology for modern production.
This article will give you a clear understanding of additive manufacturing. We'll cover its definition, history, materials, processes, benefits, and challenges. Whether you're a business owner, engineer, or just curious about the future of manufacturing, this guide will provide the essential knowledge to explore and utilize additive manufacturing effectively.
What is Additive Manufacturing ?
Source: makeagif.com
Definition
Additive Manufacturing is the construction of a three-dimensional object from a CAD model or a digital 3D model.
Contrasting with traditional subtractive manufacturing, where material is removed from a solid block to shape an object, additive manufacturing involves depositing, joining, or solidifying material under computer control, typically adding material layer by layer (such as fusing plastics, liquids, or powder grains).
Feature
Layer-by-Layer Construction: The process involves building up an object layer by layer, which allows for the creation of complex geometries and intricate designs that would be difficult or impossible to achieve with traditional methods.
Digital Model: Additive manufacturing begins with a digital 3D model created using computer-aided design (CAD) software. This model is then sliced into thin layers, which guide the printer on where to deposit material.
Versatile Materials: A wide range of materials can be used in additive manufacturing, including plastics, metals, ceramics, composites, and even biological substances. Each material has unique properties that make it suitable for different applications.
Customization: Additive manufacturing enables the production of customized products tailored to specific requirements, making it ideal for prototyping, small batch production, and personalized items.
History of Additive Manufacturing
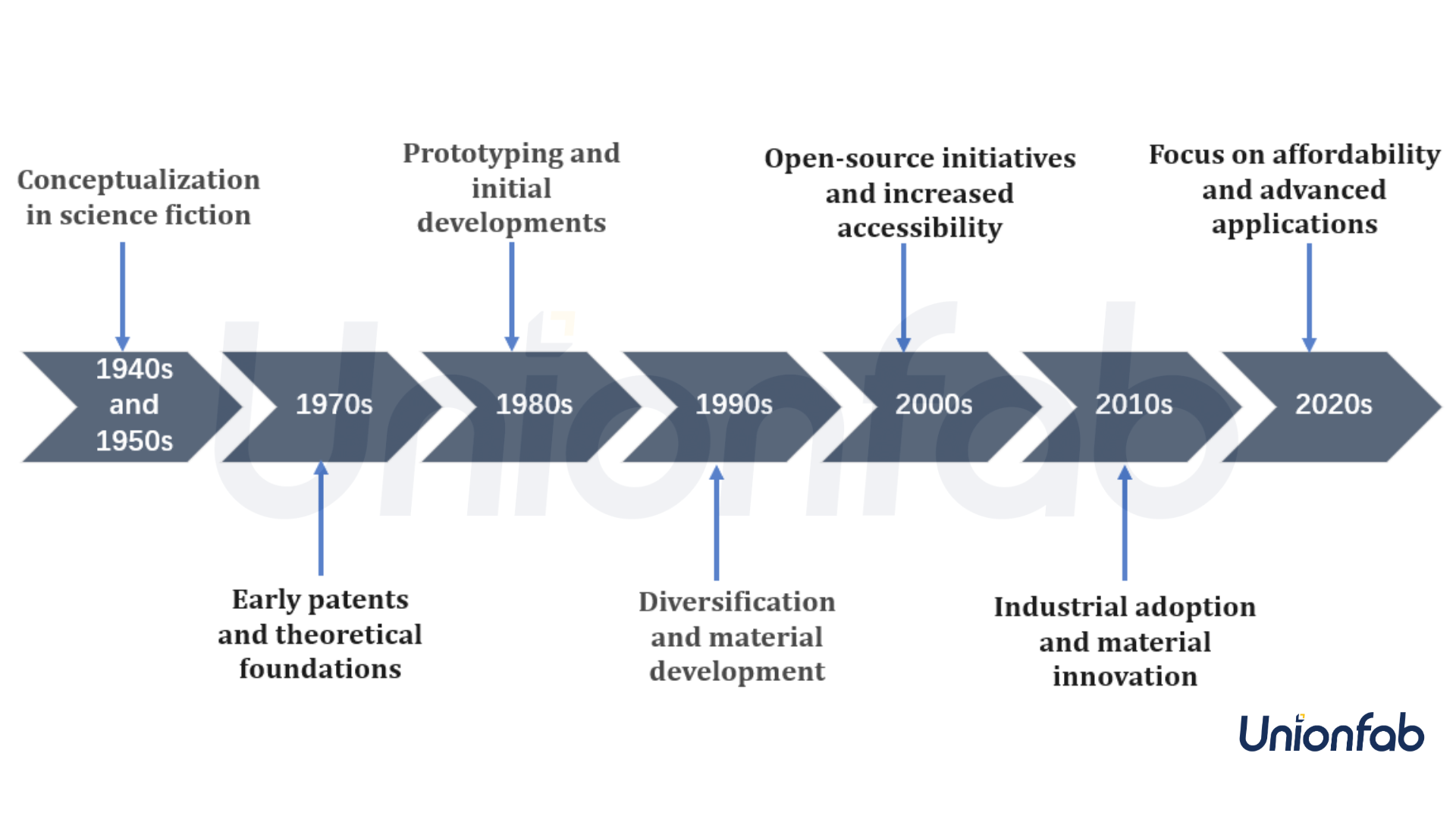
1940s and 1950s: Conceptualization in Science Fiction
The idea of additive manufacturing first appeared in science fiction.
1945: Murray Leinster described a device that "prints" objects using plastic in his short story "Things Pass By."
1950: Raymond F. Jones further explored this concept with a "molecular spray" in his story "Tools of the Trade."
1970s: Early Patents and Theoretical Foundations
1971: Johannes F. Gottwald patented the Liquid Metal Recorder, a device for creating metal patterns on a reusable surface, marking an early form of 3D printing.
1974: David E. H. Jones elaborated on 3D printing concepts in his New Scientist column, establishing theoretical foundations for the technology.
1980s: Prototyping and Initial Developments
The 1980s witnessed significant technological advancements:
1980: Hideo Kodama developed methods for 3D plastic models using UV light to harden photopolymer resin.
1984: Patents for stereolithography (SLA) processes were filed by multiple inventors, including Bill Masters and Alain Le Méhauté.
1986: Chuck Hull patented the first commercial 3D printing system using SLA and founded 3D Systems Corporation, releasing the SLA-1.
1988: S. Scott Crump developed fused deposition modeling (FDM), which Stratasys later commercialized.
1990s: Diversification and Material Development
Additive manufacturing diversified and saw the development of metal sintering and melting techniques like selective laser sintering (SLS) and direct metal laser sintering (DMLS).
The term "3D printing" gained traction, originally referring to powder bed processes developed at MIT.
The Fraunhofer Society developed the selective laser melting process, further advancing the technology (1995).
2000s: Open-Source and Accessibility
The early 2000s marked a shift towards accessibility and open-source projects:
2004: The RepRap project aimed to create self-replicating 3D printers.
2006: The Fab@Home project promoted open-source fabrication systems.
2009: Expiring patents led to a surge in affordable FDM printers, making the technology more accessible to the general public.
2010s: Industrial Adoption and Material Innovation
The 2010s saw significant industrial adoption and material innovation:
Metal additive manufacturing became viable for producing end-use parts, particularly in aviation.
Filabot introduced a system for recycling plastic into 3D printing filament (2012).
Multi-material 3D printing and advancements in electronic printing broadened the applications of additive manufacturing.
2020s: Affordability and Advanced Applications
The 2020s have focused on affordability and advanced applications:
2021: The world’s first fully 3D-printed prosthetic eye was fitted.
2024: The University of Maine revealed the world’s largest 3D printer, capable of producing objects up to 96 feet long. Researchers also used machine learning to enhance synthetic bone construction.
Additive Manufacturing Materials
Plastics:
The most widely used category, offering affordability, versatility, and a wide range of options like:
Acrylonitrile Butadiene Styrene (ABS): Strong, durable, and commonly used for functional prototypes and parts.
Polylactic Acid (PLA): Biodegradable, user-friendly, and ideal for rapid prototyping and low-stress applications.
Polycarbonate (PC): High strength, heat resistance, and clarity, making it suitable for demanding parts and functional models.
Nylon: Offers high strength, flexibility, and chemical resistance, used in various applications like gears and enclosures.
Metals:
Enabling the creation of high-strength and complex metal parts for diverse industries, including:
Titanium: Lightweight, biocompatible, and corrosion-resistant, ideal for aerospace, medical implants, and high-performance parts.
Stainless Steel: Offers excellent strength, corrosion resistance, and heat tolerance, widely used in industrial applications and functional parts.
Aluminum: Lightweight, strong, and good conductor of heat and electricity, suitable for aerospace components and lightweight structures.
Nickel Alloys: Offer high strength, heat resistance, and corrosion resistance, used in demanding applications like turbine blades and engine components.
Composites:
Combining the properties of different materials for unique characteristics, such as:
Carbon Fiber Reinforced Polymer (CFRP): High strength-to-weight ratio, stiffness, and dimensional stability, ideal for lightweight and high-performance parts.
Metal-Polymer Composites: Blending metal properties with the versatility of polymers for specific applications.
Ceramics:
Offering high heat resistance, wear resistance, and biocompatibility, suitable for:
Alumina: High hardness, wear resistance, and thermal conductivity, used for cutting tools, molds, and heat exchangers.
Zirconia: High strength, biocompatibility, and chemical resistance, ideal for medical implants and dental applications.
Sand:
Primarily used in binder jetting AM for creating molds and cores for metal casting applications.
Types of Additive Manufacturing Processes
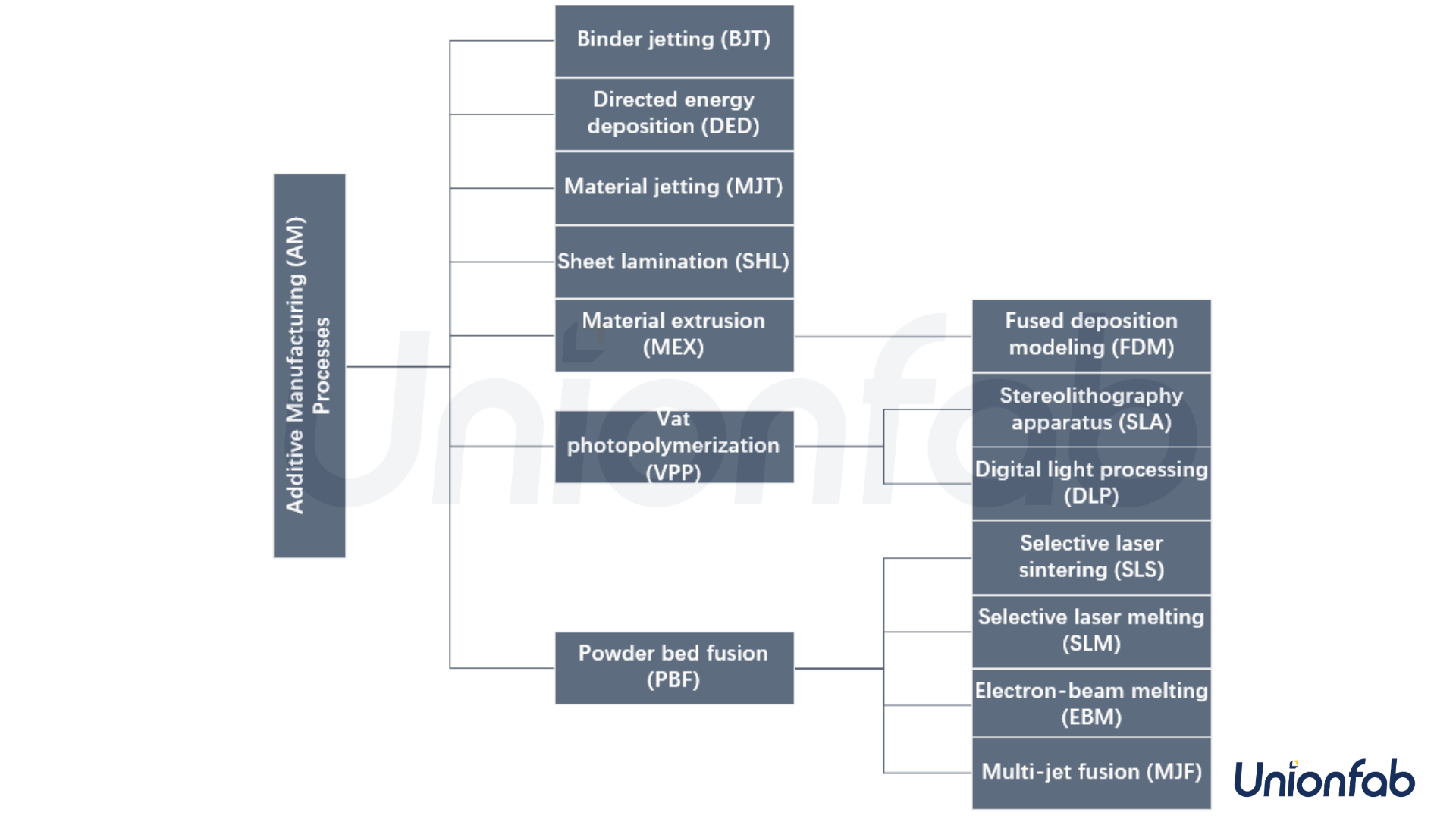
The table below provides a concise overview of various additive manufacturing processes, highlighting their methods, materials, and typical applications.
Process Type | Process | Materials | Applications |
---|---|---|---|
Binder Jetting (BJT) | A liquid binder is selectively deposited onto a powder bed, bonding the particles layer by layer to create the object. | Various powders like metals, plastics, and sand. | Prototypes, sand casting molds, architectural models. |
Directed Energy Deposition (DED) | A focused energy source (laser or electron beam) melts metal wire or powder, depositing it layer by layer to create the object. | Primarily works with metals. | Large metal parts, repairs, functional components. |
Material Extrusion (Fused Deposition Modeling, FDM) | A heated nozzle extrudes a filament of molten plastic, depositing it layer by layer to build the object. | Primarily uses thermoplastics like ABS, PLA, and nylon. | Prototypes, functional parts, design models. |
Material Jetting (MJT) | Similar to an inkjet printer, this process jets droplets of material (photopolymer resin, wax) layer by layer to build the object. | Uses photopolymers, wax, and other specialized materials. | High-resolution prototypes, full-color models, dental applications. |
Powder Bed Fusion (SLS, SLM, DMLS) | A laser or electron beam selectively melts powder particles (plastic or metal) to fuse them together layer by layer. | Works with a wide range of materials like plastics, metals (including titanium and stainless steel), and even some ceramics. | Complex metal parts, high-strength prototypes, end-use functional parts. |
Sheet Lamination (SHL) | Thin sheets of material (paper, metal) are bonded together layer by layer to create the object. | Uses various sheet materials like paper, plastic, and metal. | Rapid prototypes, composite structures. |
Vat Photopolymerization (SLA, DLP) | Uses a vat of liquid resin and a light source (laser in SLA, projector in DLP) to cure thin layers selectively, solidifying the desired object shape. | Primarily uses photopolymers (light-curable resins). | High-resolution prototypes, jewelry, dental models. |
How Additive Manufacturing Works ?
Additive manufacturing is a multi-step process that involves designing, planning, printing, and finishing a part. Here’s a detailed look at each stage:
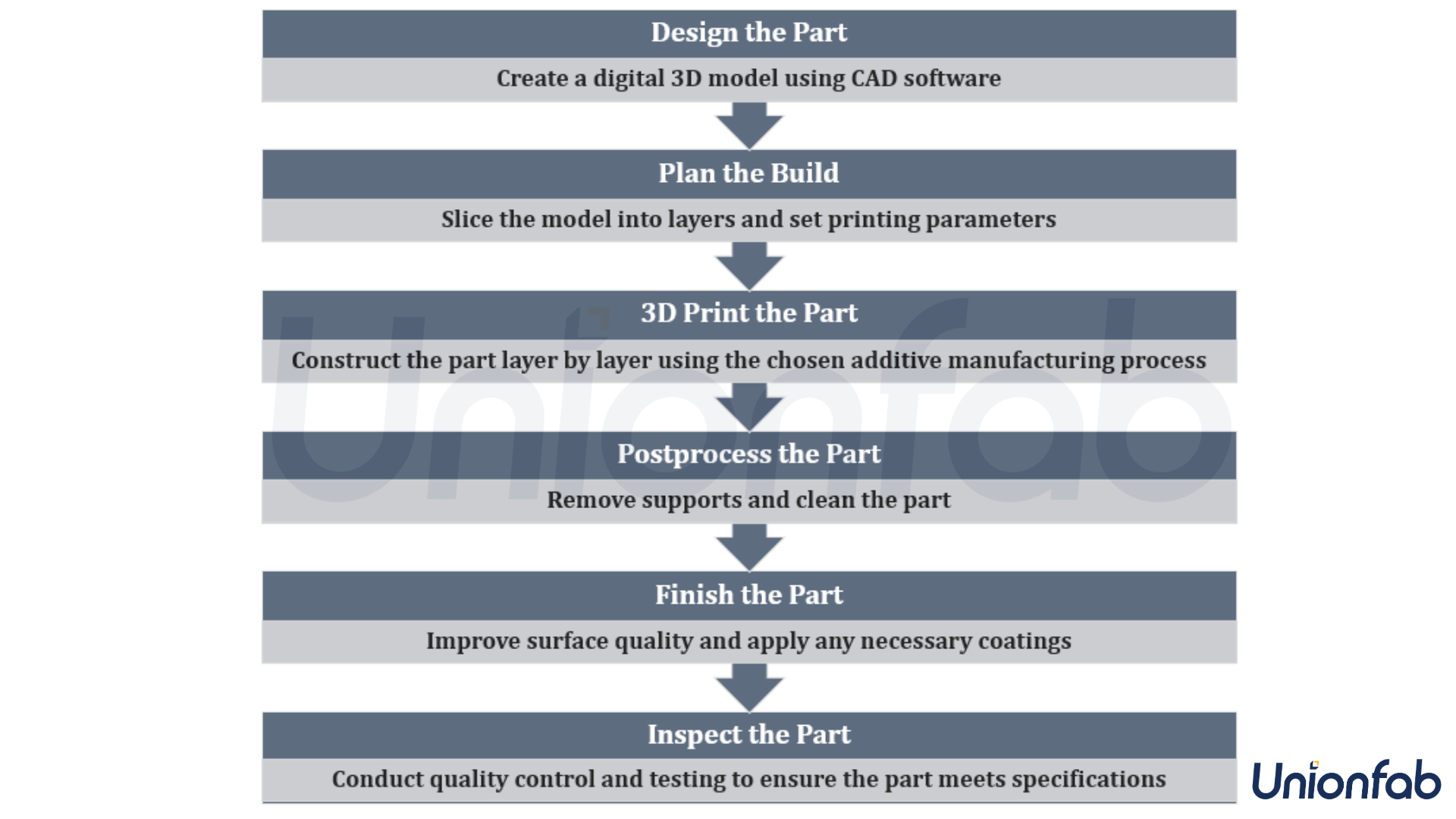
Design the Part
Computer-Aided Design (CAD): The process begins with creating a digital 3D model of the part using CAD software. This model serves as the blueprint for the entire manufacturing process.
Optimization: Designers can optimize the model for weight, strength, and other properties. They can also incorporate complex geometries that are difficult or impossible to achieve with traditional manufacturing methods.
Plan the Build
Slicing the Model: Slicing software slices the 3D model into thin layers. Each layer represents a cross-section of the final part.
Setting Parameters: The software sets parameters for the build, such as layer thickness, printing speed, and support structures. These parameters can be adjusted to balance quality and production speed.
3D Print the Part
Layer-by-Layer Construction: The 3D printer constructs the part layer by layer according to the sliced model. Depending on the chosen additive manufacturing process (e.g., FDM, SLA, SLS), different materials and techniques are used to build the part.
Material Deposition: The printer deposits, cures, or sinters material to form each layer. The process continues until the entire part is completed.
Postprocess the Part
Removing Supports: If support structures were used during printing, they are removed. This can involve breaking away support material or dissolving it in a solution.
Cleaning: The part is cleaned to remove any residual powder, resin, or debris from the printing process.
Finish the Part
Surface Finishing: The part may undergo additional finishing processes to improve its surface quality. This can include sanding, polishing, or applying a coating.
Painting and Coating: Parts can be painted or coated for aesthetic purposes or to provide additional protection.
Inspect the Part
Quality Control: The final part is inspected to ensure it meets the required specifications and quality standards. This can involve visual inspection, dimensional measurement, and functional testing.
Testing: Depending on the application, parts may undergo stress tests, load tests, or other forms of evaluation to ensure they perform as expected.
Advantages of Additive Manufacturing
Additive manufacturing offers numerous benefits that make it a transformative technology in various industries. Here are some of the key advantages:
Speed and Efficiency in Production
Rapid Prototyping: Additive manufacturing significantly reduces the time needed to create prototypes. Designers can quickly iterate and refine their designs, speeding up the product development cycle.
Shorter Production Times: Parts can be produced faster compared to traditional manufacturing methods, especially for complex designs and small batches.
Ability to Create Complex Geometries
Intricate Designs: Additive manufacturing allows for the creation of complex and intricate geometries that are difficult or impossible to achieve with traditional methods. This includes internal structures, lattice designs, and overhangs.
Customization: Each part can be uniquely tailored to meet specific requirements without the need for additional tooling or modifications to the manufacturing process.
Flexibility in Using Different Materials
Wide Range of Materials: Additive manufacturing supports a diverse array of materials, including plastics, metals, ceramics, and composites. This flexibility enables the production of parts with varying properties and functionalities.
Material Combinations: Multi-material printing capabilities allow for the creation of parts with different materials in a single build, enhancing their functionality and performance.
Cost-Effectiveness
Reduced Tooling Costs: Traditional manufacturing often requires expensive molds and tooling for each design iteration. Additive manufacturing eliminates the need for these tools, reducing overall costs.
Economic Small Batches: For low-volume production runs and custom parts, additive manufacturing is more cost-effective than traditional methods, which are optimized for mass production.
Environmental Benefits (Less Waste)
Material Efficiency: Additive manufacturing builds parts layer by layer, using only the necessary amount of material. This results in significantly less waste compared to subtractive manufacturing, where excess material is cut away.
Sustainable Practices: The reduced material waste and potential for recycling unused materials contribute to more sustainable manufacturing practices.
Challenges and Limitations
While additive manufacturing offers numerous advantages, it also comes with its own set of challenges and limitations. Understanding these can help in effectively leveraging the technology and mitigating potential drawbacks.
High Initial Cost of Machines
Expensive Equipment: The cost of high-quality 3D printers, especially those capable of printing with metals and advanced materials, can be prohibitively high. This initial investment can be a barrier for small businesses and individual users.
Maintenance and Operating Costs: Beyond the initial purchase, maintenance and operation of 3D printers can also be costly, requiring skilled technicians and regular upkeep.
Time-Consuming for Large-Scale Productions
Slow Build Rates: Although additive manufacturing is efficient for small batches and prototyping, the process can be time-consuming for large-scale production runs. Building parts layer by layer is inherently slower than traditional mass-production techniques.
Extended Production Cycles: For large parts or high-volume production, the build time can be significantly longer, making it less suitable for applications requiring rapid turnaround.
Need for Post-Processing
Additional Steps Required: Many 3D printed parts require post-processing to achieve the desired surface finish, mechanical properties, or aesthetic quality. This can include removing support structures, sanding, polishing, or heat treatment.
Increased Labor and Costs: Post-processing adds extra steps to the manufacturing workflow, increasing labor requirements and overall production costs.
Ensuring Quality and Minimizing Defects in the Final Products
Quality Control Challenges: Ensuring consistent quality across all parts can be challenging due to variations in material properties, printer performance, and process parameters.
Defects and Inconsistencies: Additive manufacturing can sometimes produce parts with defects such as porosity, layer adhesion issues, or surface roughness. Ensuring that these defects are minimized requires rigorous testing and quality control measures.
Comparison with Conventional Manufacturing
Pros and Cons of Additive vs. Subtractive Manufacturing
Additive Manufacturing (AM):
Pros:
Design Flexibility: Capable of producing complex geometries and intricate designs that are difficult or impossible with subtractive methods.
Customization: Easily allows for the customization of each part without the need for additional tooling.
Material Efficiency: Builds parts layer by layer, using only the necessary material, resulting in less waste.
Rapid Prototyping: Speeds up the design and prototyping phase, allowing for quick iterations and adjustments.
Cons:
Slower Production Rates: Generally slower than subtractive manufacturing for large-scale production runs.
High Initial Costs: Advanced 3D printers, especially those capable of printing metals, can be expensive.
Post-Processing Requirements: Often requires additional steps such as sanding, polishing, or heat treatment to achieve desired finishes and properties.
Subtractive Manufacturing (SM):
Pros:
Speed and Efficiency for Large Volumes: Capable of quickly producing large quantities of parts, making it ideal for mass production.
High Precision and Surface Finish: Can achieve very high levels of precision and surface quality with appropriate tooling and techniques.
Established Processes: Long history and well-established processes and standards.
Cons:
Material Waste: Involves cutting away material from a larger block, leading to more waste.
Complex Geometry Limitations: Limited in its ability to create complex internal geometries and intricate designs.
Tooling Costs: Requires expensive molds, dies, and tools, particularly for low-volume or customized parts.
Situations Where Traditional Manufacturing is Still Preferable
High-Volume Production: For producing large quantities of identical parts, traditional manufacturing methods such as injection molding, stamping, and CNC machining are more efficient and cost-effective.
High Precision and Surface Finish: When the highest levels of precision and surface finish are required, traditional manufacturing techniques often provide superior results.
Material Constraints: For certain materials that are challenging to process with additive manufacturing, traditional methods may still be the best option.
Tool and Mold Production: When creating tools, dies, and molds for mass production, traditional subtractive techniques are typically used due to their precision and durability.
Potential for Hybrid Manufacturing Models
Combining Strengths: Hybrid manufacturing models combine the strengths of both additive and subtractive methods. For example, a part could be 3D printed to achieve complex internal geometries and then finished with CNC machining to achieve high precision and surface quality.
Enhanced Efficiency: By integrating both approaches, manufacturers can optimize production for both cost and performance, producing complex parts more efficiently than using either method alone.
Innovative Applications: Hybrid models enable the development of innovative applications and designs that leverage the unique advantages of both additive and subtractive processes.
Applications of Additive Manufacturing
Additive manufacturing has found applications across a wide range of industries due to its versatility, ability to create complex geometries, and capacity for customization. Here are some key areas where additive manufacturing is making a significant impact:
Aerospace
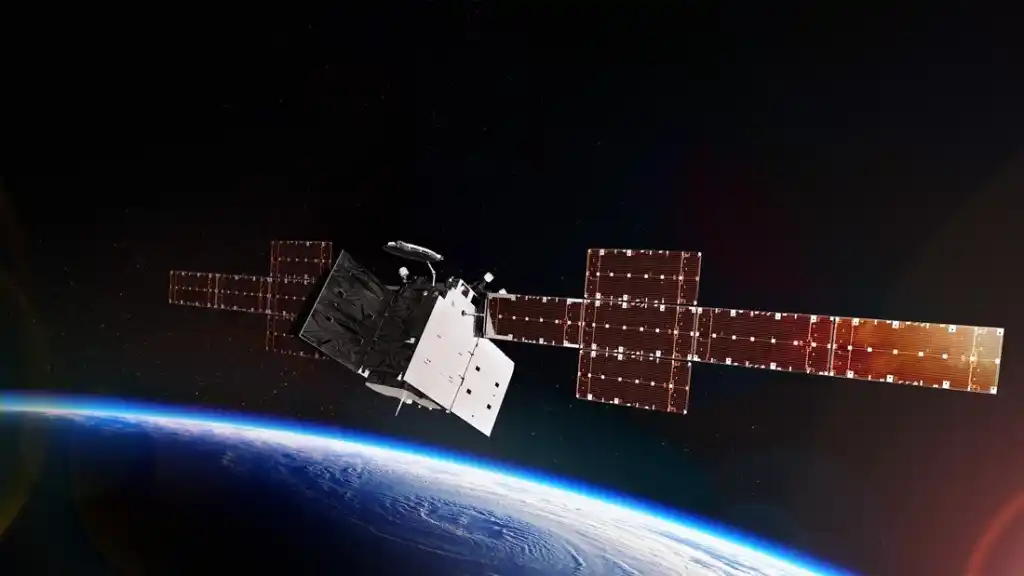
Source: boeing.mediaroom.com
Lightweight Components: Additive manufacturing allows for the production of lightweight components with complex geometries, reducing overall weight and improving fuel efficiency.
Rapid Prototyping: Aerospace companies use 3D printing to quickly create prototypes for testing and development, accelerating the design process.
Custom Parts: The ability to produce custom and low-volume parts on demand helps reduce inventory costs and lead times.
Automotive Industry
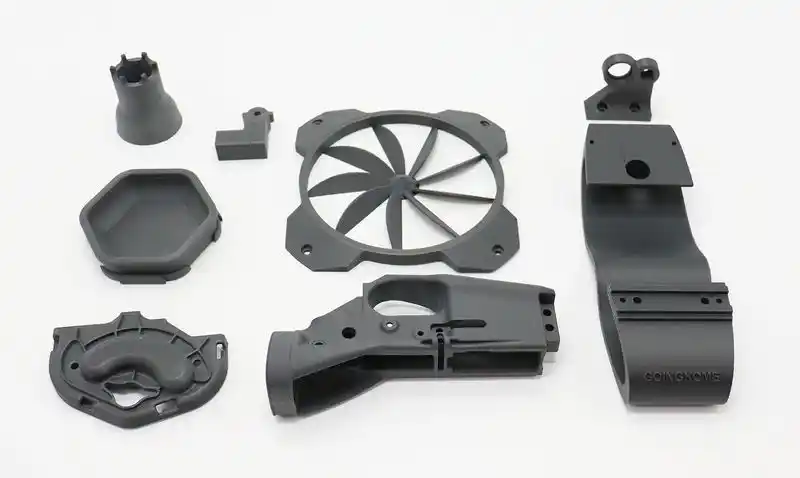
Source: top3dshop.com
Prototyping and Design: Additive manufacturing is used extensively for prototyping, allowing designers to quickly iterate and test new designs.
End-Use Parts: Custom and performance parts, such as intake manifolds and brackets, can be produced with 3D printing, offering enhanced performance and reduced weight.
Tooling and Fixtures: The production of custom tools, jigs, and fixtures can be done more efficiently with additive manufacturing.
Medical Field
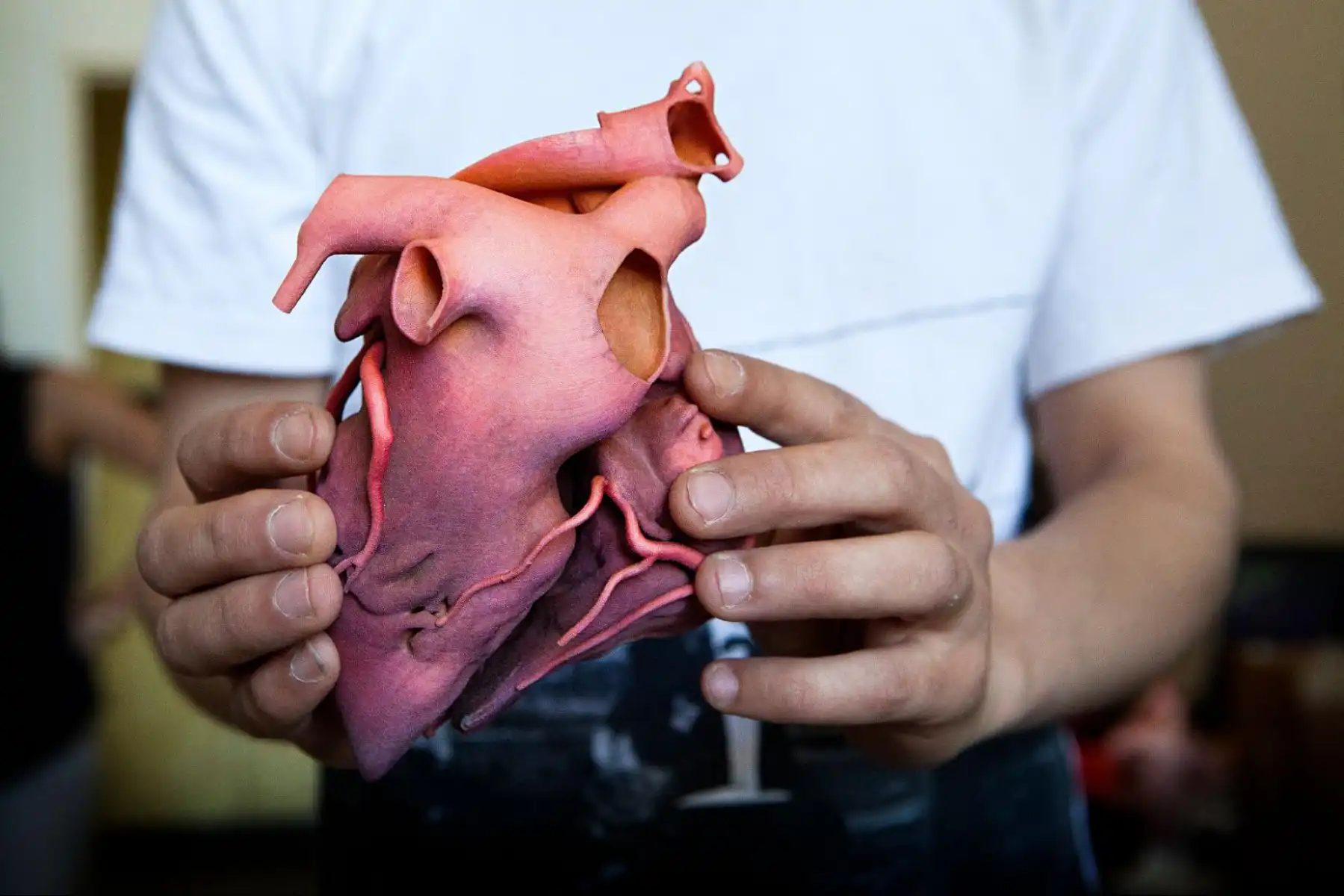
Source:spatial.com
Custom Implants and Prosthetics: Additive manufacturing enables the production of custom implants and prosthetics tailored to individual patients, improving fit and comfort.
Surgical Guides and Models: Surgeons use 3D-printed models and guides to plan and execute complex surgeries with higher precision.
Bioprinting: Research is ongoing into bioprinting tissues and organs, with the potential to revolutionize transplant medicine.
Consumer Products
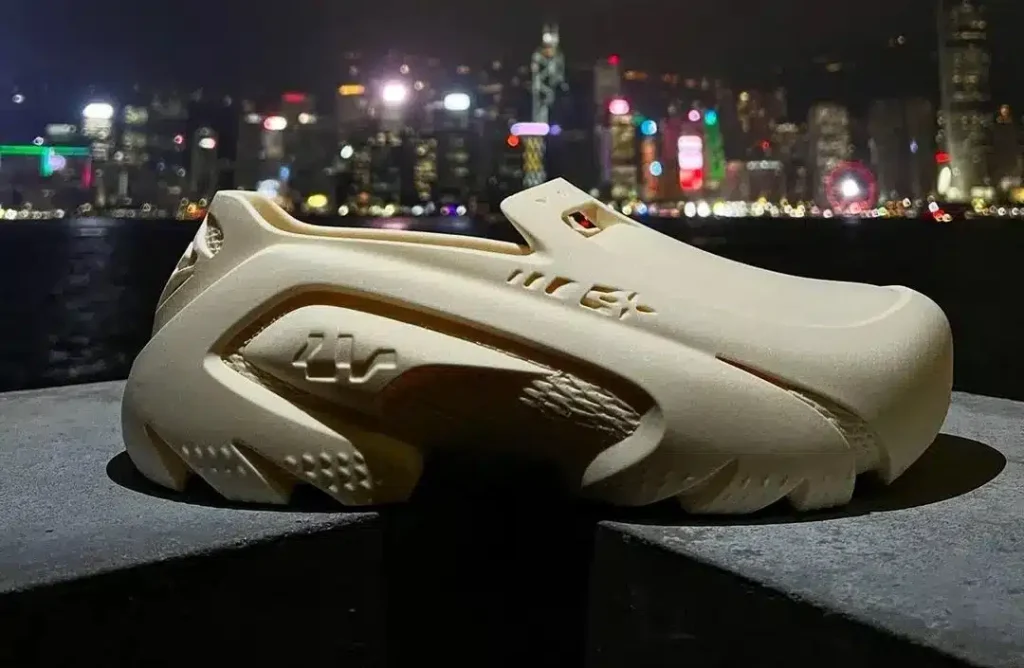
Source: voxelmatters.com
Personalized Items: Additive manufacturing allows for the creation of personalized consumer products, such as customized jewelry, eyewear, and phone cases.
Fashion and Footwear: Designers are using 3D printing to create innovative fashion items and custom-fit footwear, enhancing comfort and style.
Household Items: Consumers can print household items and replacement parts on demand, reducing the need for large inventories.
Emerging Areas
Construction: 3D printing in construction, also known as additive construction, is used to build structures and houses. This method offers reduced construction times and material waste.
Food Production: Experimental use of additive manufacturing in food production includes printing complex food structures and customized nutrition.
Education and Research: Additive manufacturing is widely used in educational institutions and research labs for creating models, prototypes, and conducting experiments.
Achieve Precision AM Deals with Unionfab
Unionfab excels in providing comprehensive AM services, highlighted by four key strengths: experience, certification, shipping, and cost.
Experience: With 100 3d printers and 20+ years' experience in 3D printing.
Certification: Meeting the rigorous ISO 9001 quality management standards.
Shipping: Air shipments in 3-5 days via DHL Express and FedEx.
Cost: 70% cheaper than European and American competitors.
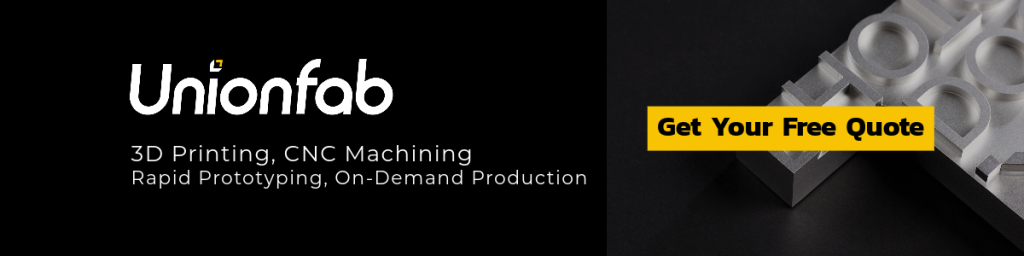
Conclusion
Additive manufacturing, or 3D printing, is transforming design and production with its flexibility, efficiency, and customization capabilities. It enables rapid prototyping, complex geometries, and sustainable practices across industries like aerospace, automotive, medical, consumer products, and more.
As this technology evolves, staying informed about the latest developments and advancements in additive manufacturing is crucial. We encourage businesses and individuals to explore the opportunities that additive manufacturing offers.
By integrating this technology into your workflows, you can drive innovation, reduce costs, and achieve greater efficiency. The future of manufacturing is here, and those who embrace additive manufacturing will be at the forefront of this exciting revolution.
FAQs
Is Additive Manufacturing the same as 3D Printing?
Not exactly, additive manufacturing and 3D printing are often used interchangeably. Both terms refer to the process of creating three-dimensional objects by adding material layer by layer based on digital models.
However, "additive manufacturing" is a broader term encompassing various technologies and methods beyond just 3D printing.
How is Additive Manufacturing different from Traditional Manufacturing?
Additive manufacturing builds objects layer by layer, using only the necessary material, which allows for complex geometries and customization.
In contrast, traditional manufacturing often involves subtractive processes, where material is removed from a larger block (e.g., machining), or formative processes, where material is shaped using molds and dies (e.g., casting).
Traditional methods are typically more efficient for large-scale production but generate more waste and are less flexible for complex designs and small batches.
Will Additive Manufacturing Replace Conventional Manufacturing?
While additive manufacturing offers many advantages, it is unlikely to completely replace conventional manufacturing. Instead, it complements traditional methods, particularly for low-volume, high-complexity, or customized parts.
Hybrid manufacturing models, which combine both additive and subtractive techniques, are becoming increasingly common, leveraging the strengths of both approaches to optimize production.
Example of Additive Manufacturing
One example of additive manufacturing is the production of custom medical implants. Using 3D printing, medical professionals can create implants tailored to a patient's specific anatomy, improving fit and function.
This process involves scanning the patient's body, designing the implant using CAD software, and printing it using biocompatible materials, such as titanium or specialized polymers.
Ready to Go Deeper ?
Read SLA vs SLS vs SLM: Choose the Right 3D Printing Technique – Unionfab to discover the differences between 3D printing techniques and find the perfect one for your needs.
Dive into the details of popular 3D printing materials with PLA vs. ABS vs. PETG: A Comprehensive Comparison (unionfab.com) and see how they stack up against each other.