Threaded Hole [ +Methods & Design Tips]
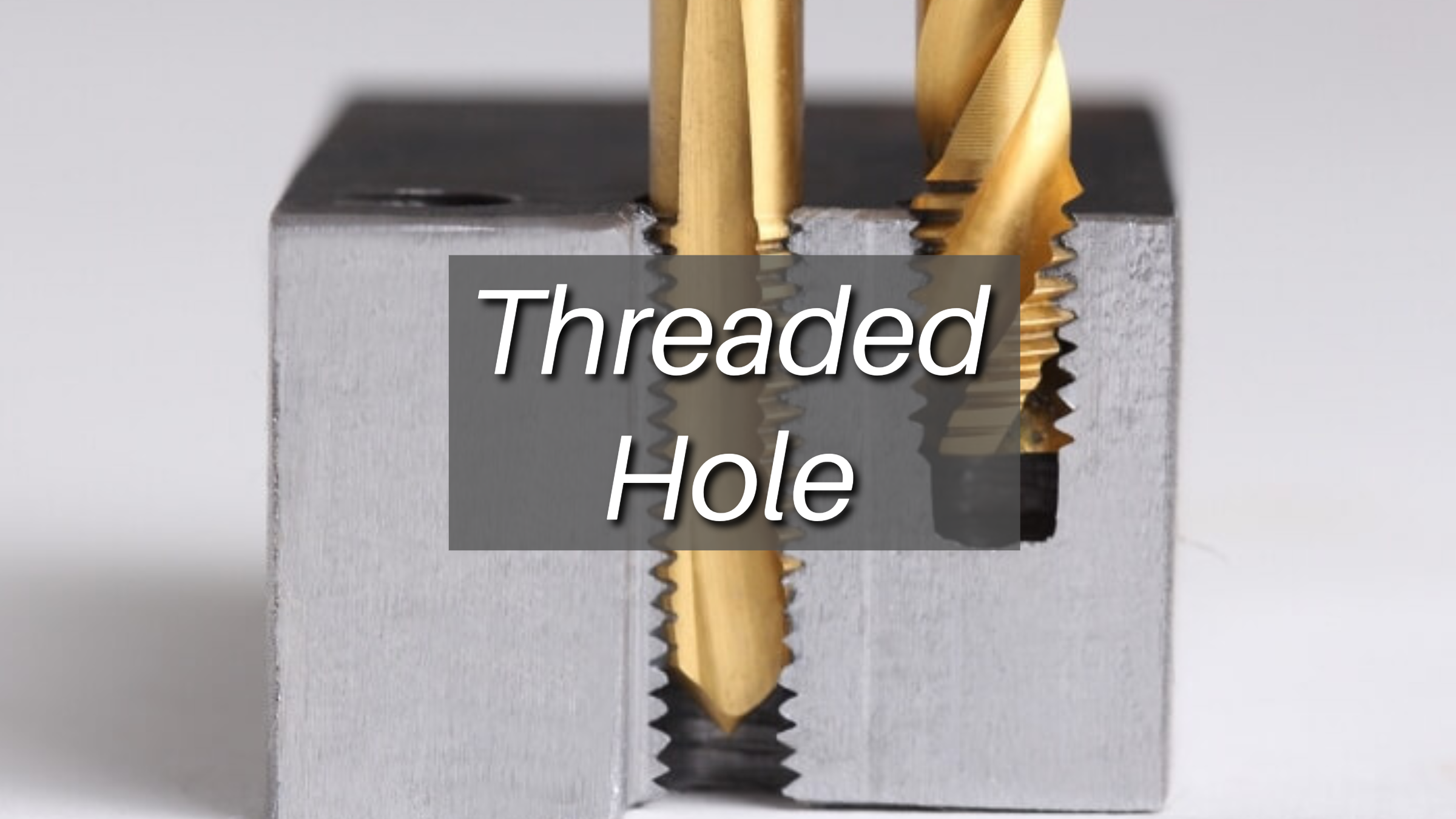
Discover everything about threaded holes—design standards, CNC manufacturing methods, pros and cons, and repair tips. Choose the right threading method to improve part performance and production efficiency with Unionfab.
What is a Threaded Hole?
A threaded hole is a drilled cavity that contains a spiral-shaped ridge—called a thread—along its inner surface. These threads are designed to match with external threads on screws, bolts, or studs, creating high-friction, high-strength connections. Threaded holes are everywhere: from smartphones and surgical tools to engines and aerospace assemblies.Key Features of Threaded Holes
Feature | Description |
---|---|
Hole Diameter | The drilled size before threading. Choosing the right drill size is critical for clean, durable threads. |
Thread Type | Common systems include Metric (M) and Imperial (UNC/UNF) threads. |
Thread Size | Denotes the major and minor diameters of the thread, e.g., M8, 1/4-20 UNC. |
Pitch | Distance between adjacent thread peaks. Finer pitches = better precision, coarser = faster assembly. |
Thread Depth | Threaded holes can be through holes (go all the way) or blind holes (have a bottom). |
How to Create a Threaded Hole
Creating a threaded hole is a multi-step process that can vary depending on the material, thread requirements, and production method. The most common techniques fall into two broad categories: cutting methods and forming/insertion methods.
1. Thread Tapping
Thread tapping is the most straightforward and widely used method. It involves drilling a pilot hole of the correct diameter, then using a tap—a hardened tool with cutting edges that match the desired thread profile—to cut threads into the hole. Taps come in different types: hand taps (taper, plug, and bottoming) for manual operations and machine taps for CNC operations. Proper lubrication is crucial to reduce friction and avoid tool breakage. Tapping is ideal for small- to medium-volume production and works with most machinable materials.
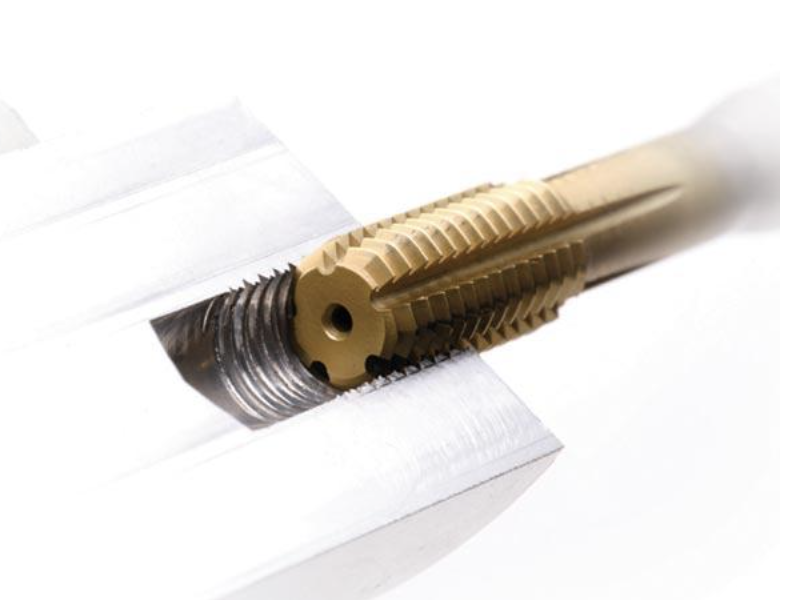
Source: canadianmetalworking.com
2. Thread Milling
Thread milling is a CNC process where a rotating multi-axis tool mills the thread profile directly into the workpiece. Unlike tapping, thread milling does not require reversing the spindle and can produce threads of various diameters with the same tool. It also allows for high precision, chip control, and better surface finish. Thread milling is especially suitable for large threads, blind holes, and applications where exact tolerances are required. It requires advanced CNC equipment and software, but offers flexibility and repeatability for high-value parts.
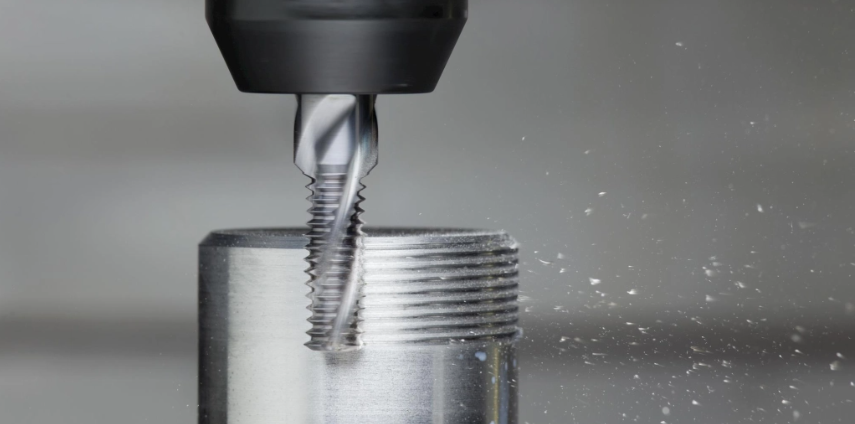
Source: tamachinery.com
3. Thread Rolling
Thread rolling is a non-cutting process that forms threads by plastically deforming the material using hardened dies. Since the material is displaced rather than removed, the resulting threads are denser and stronger, with excellent fatigue and wear resistance. This method is limited to ductile materials like aluminum, brass, and certain steels. Thread rolling is extremely efficient for high-volume production and produces high-strength threads with minimal material loss. However, it is not suitable for hard or brittle materials.
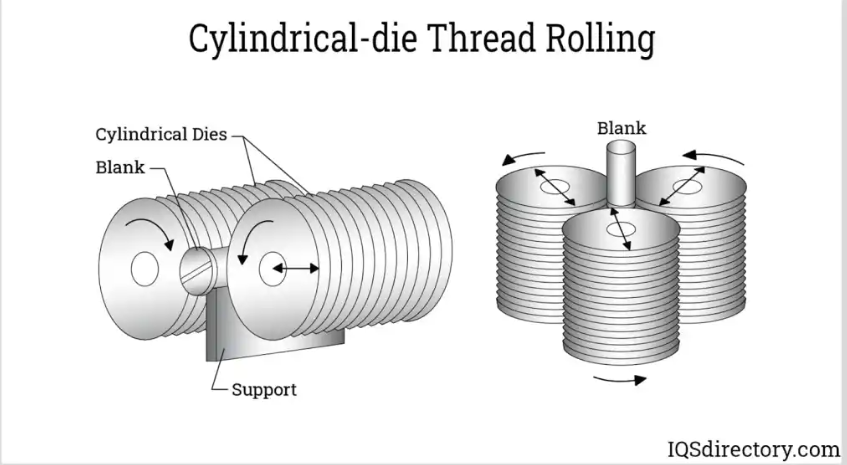
Source: iqsdirectory.com
4. Thread Cutting on a Lathe
For external threads or certain internal threads, a CNC or manual lathe can be used to cut threads using single-point tools. This is common in custom or one-off parts, especially when non-standard thread profiles are required. Though slower than tapping or rolling, it offers full control over thread geometry and finish.
5. Threaded Inserts for Soft or Damaged Materials
Threaded inserts are metal sleeves with internal threads that are installed into a pre-drilled hole. They are used when the base material is too soft (e.g., plastics, composites, aluminum) or when the original thread is damaged. There are multiple types:
Welded Inserts: Welded into place for high-load applications.
Weldable Threaded Insert
Source: wixroyd.comPress-Fit Inserts: Installed by pressing into an undersized hole to generate retention through friction.
Press-Fit Threaded Inserts
Source: dbroberts.comHelicoil (Wire) Inserts: Coiled wire inserts that restore damaged threads or reinforce soft materials.
Key-Locking Inserts: Feature locking keys for high-vibration environments.Inserts offer repairability, reusability, and enhanced load capacity, especially in materials prone to thread wear or failure.
6. 3D Printing with Threaded Features
In additive manufacturing, threads can be integrated into the printed part or created post-process. Fine-pitch threads are usually tapped after printing for better accuracy, while larger threads may be printed directly. Unionfab also offers post-print threading as part of our hybrid manufacturing services.
7. Additional Considerations and Tips
Select the correct pilot hole size based on thread size and material. Pilot hole charts are widely available for both metric and imperial systems.
When tapping blind holes, ensure proper chip removal and consider using spiral flute taps designed for such applications.
For high-precision or safety-critical parts, CNC methods like thread milling or thread rolling are recommended due to their repeatability and surface finish.
Thread gaging (e.g., GO/NO-GO gauges) is essential for quality control in production.
Consider material-specific behavior: hard materials may require coated taps or slower feed rates, while soft materials may deform easily and benefit from thread inserts.Selecting the right method depends on your design goals, material characteristics, production volume, and budget. Unionfab offers expert consultation and advanced CNC technology to ensure your threaded features meet industry standards with optimal performance and cost-efficiency.
Pros and Cons of Threaded Hole Creation Methods
Method | Pros | Cons |
---|---|---|
Thread Tapping | Simple, low-cost, compatible with many materials, good for small batches | Risk of tool breakage in hard materials; chip removal can be difficult in blind holes |
Thread Milling | High precision, flexible tool use, good chip control, ideal for CNC | Requires CNC equipment and programming; less cost-effective for low-volume jobs |
Thread Rolling | Produces strong, fatigue-resistant threads; no chips; high efficiency | Only suitable for ductile materials; not suitable for blind holes or brittle materials |
Lathe Cutting | Full control over thread geometry; suitable for custom profiles | Slower and less efficient for large volumes; requires skilled operators |
Threaded Inserts | Enhances strength in soft materials; easy to repair damaged holes | Added cost; may require specialized installation tools |
3D Printing + Post Processing | Allows integration in complex parts; flexible for prototyping | Printed threads often need machining to meet tolerance and strength requirements |
Tapped Hole vs Threaded Hole: What’s the Difference?
Category | Threaded Hole | Tapped Hole |
---|---|---|
Definition | Any hole with internal threads, regardless of method | Threaded hole created specifically by a tapping tool |
Process | Can be tapped, milled, rolled, or insert-based | Made by drilling + tapping only |
Strength | Depends on method; rolled is strongest | May slightly weaken material due to cutting |
Cost | Varies with method | Cost-effective and simple |
Common Problems and How to Fix Them
1. Stripped Threads
Caused by overtightening, corrosion, or using wrong fasteners. Fix: Re-tap or use threaded inserts (e.g., Heli-Coils)
2. Seized Threads
Result of corrosion or excessive thread locker. Fix: Heat application or solvent-based release agents
3. Broken Bolts
Occur under stress or improper torque. Fix: Use bolt extractors or drill out and re-tapTip: Unionfab offers re-threading and insert solutions for damaged holes.
Threaded Hole Applications by Industry
Manufacturing
Automotive: Engine components, body panels, chassis elements, and countless other parts rely on threaded holes for assembly and attachment.
Machinery: From industrial equipment to machine tools, threaded holes secure gears, bearings, shafts, and various components for smooth operation and power transmission.
Electronics: Circuit boards, heat sinks, and enclosures utilize threaded holes to mount electronic components and ensure proper heat dissipation.
Furniture: Knock-down furniture relies heavily on threaded inserts, screws, and bolts for easy assembly, disassembly, and structural integrity.
Construction
Buildings: Structural beams, columns, and other framing elements are often secured using large bolts and threaded connections for immense load-bearing capacity.
Bridges: Threaded connections play a vital role in assembling bridge components, ensuring the structural integrity of these critical infrastructure elements.
Plumbing and HVAC Systems: Pipes, valves, and fittings heavily rely on threaded connections to create leak-proof assemblies for water, gas, and air circulation systems.
Aerospace
Aircraft Assembly: Threaded holes of various sizes and high strength are crucial for securely fastening critical aircraft components, demanding exceptional reliability and safety standards.
Engine Construction: Internal engine components like pistons, cylinders, and crankcases utilize threaded holes for precise assembly and high-pressure operation.
Spacecraft Assembly: Similar to aircraft, threaded connections are essential for assembling spacecraft structures and ensuring they withstand the extreme conditions of space.
Consumer Goods
Appliances: From washing machines to refrigerators, threaded holes secure various internal components and enable the attachment of external parts like knobs and handles.
Electronics: Threaded holes on the casing of electronics allow for the secure attachment of covers, batteries, and other user-serviceable components.
Toys: Threaded connections are often used in complex toys to enable assembly, adjustability, and durability for playtime.
Medical Devices
Prosthetic Limbs: Threaded connections are used to attach prosthetic limbs to patients, requiring biocompatible materials and precise tolerances.
Surgical Instruments: Many surgical instruments utilize threaded connections for secure assembly and functionality during delicate procedures.
Medical Implants: Certain types of medical implants, like bone screws, rely on threads for secure placement and functionality within the body.
Best Practices & Maintenance Tips
Use fasteners with matching thread specs. Apply proper torque to avoid stripping. Use lubricants for smoother installation. Choose corrosion-resistant threads in harsh environments. Inspect connections during routine maintenance.
Need Threaded Holes in Your Part? Trust Unionfab CNC Experts
At Unionfab, we combine state-of-the-art CNC turning and milling with deep technical expertise to deliver precision threaded holes for any material, tolerance, or application. Tapping, Milling, and Thread Rolling supported. Fast lead times for prototypes or full production. Expert DFM feedback to improve part reliability. Upload your CAD file now for instant quote or Book a call with our machining experts
Conclusion
Threaded holes may be small, but they play an outsized role in mechanical design, manufacturing, and assembly. From reliable structural fastenings to intricate assemblies in medical and aerospace fields, understanding their design, creation, and maintenance is vital.
Unionfab is here to help you make the right threads for the right job—with CNC precision, speed, and service that scales with your needs.
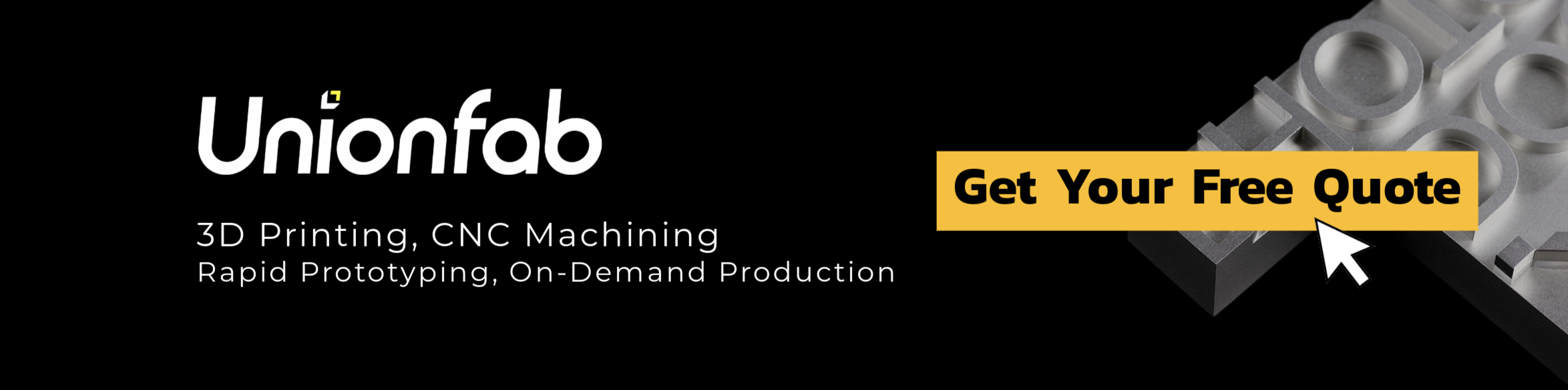