Lathe vs. Mill: Which is Better
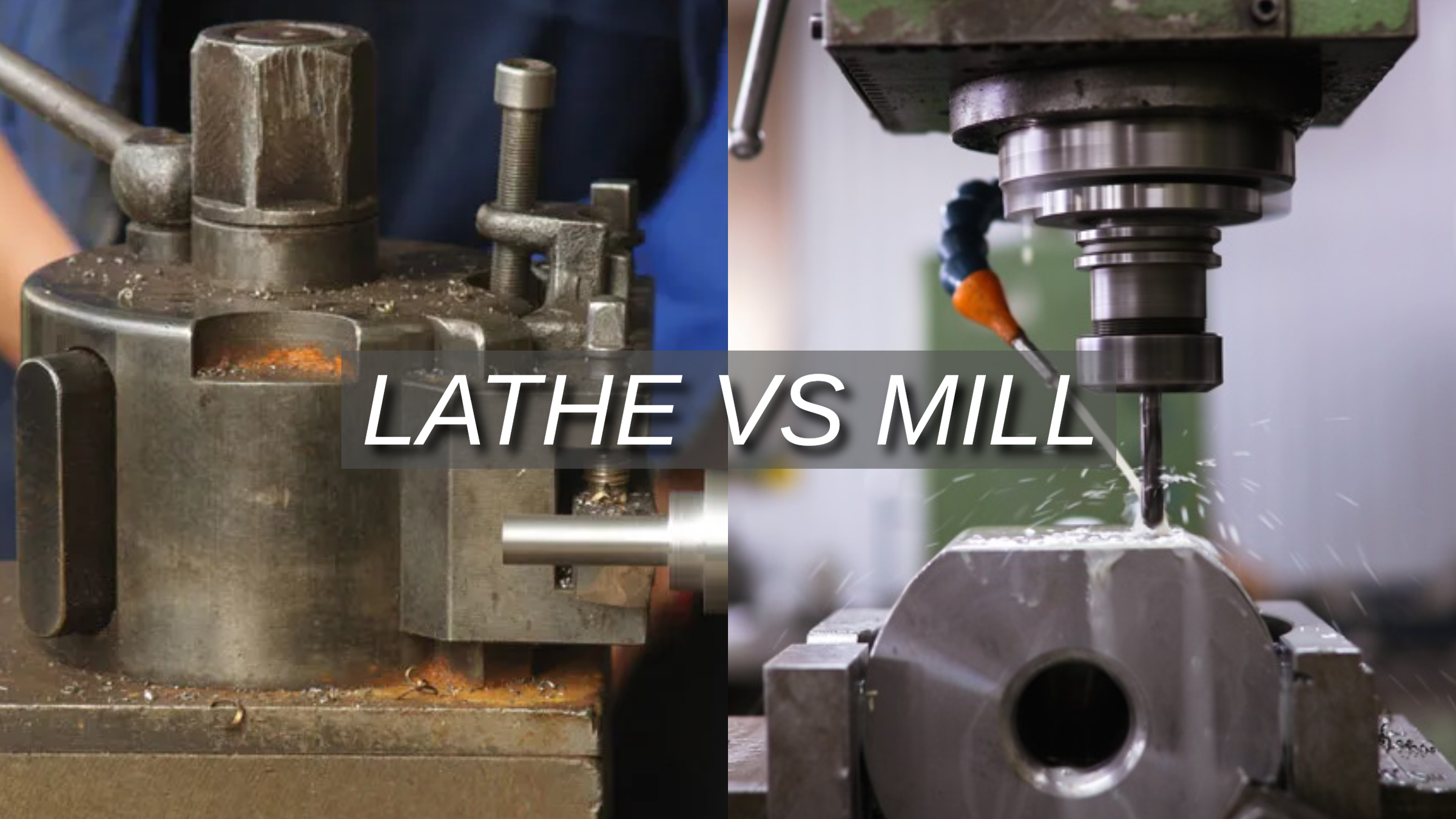
Understanding the differences between lathe and mill will help you choose the right CNC machine for your machining project.
Introduction
Lathes and mills are two fundamental machines used in machining, the process of creating parts by removing material from a solid workpiece. While both may seem similar at first glance, they have distinct functionalities and applications.
Lathe vs. Mill: Definition
Definition of a Lathe
A lathe is a machine tool used for shaping and cutting cylindrical workpieces. It works by rotating the workpiece against a stationary cutting tool, allowing for precise control over the shape and dimensions of the final product.
Various Types of Lathes
Type of Lathe | Description |
---|---|
Engine Lathe | Most common type, versatile for turning, facing, drilling, and threading. |
Speed Lathe | Designed for high-speed work with smaller diameters, commonly used in woodworking and jewelry making. |
Turret Lathe | Features a rotating tool holder for faster tool changes, ideal for mass production. |
CNC Lathe | Computer numerically controlled lathe, programmed to automate machining processes for complex parts. |
Definition of Mill
A mill is a machine tool used for shaping and creating features on a workpiece by feeding a multi-pointed cutting tool into a stationary piece. Mills offer great flexibility for machining flat surfaces, grooves, angles, pockets, and holes on a variety of shapes, not just cylindrical ones.
Different Types of Milling Machines
Type of Milling Machine | Description |
---|---|
Vertical Milling Machine (VMC) | Cutting tool moves vertically, allowing for drilling, boring, facing, and pocketing operations. |
Horizontal Milling Machine (HMC) | Spindle with cutting tool moves horizontally, suitable for large or long workpieces. |
CNC Milling Machine | Similar to VMC or HMC but controlled by a computer program for precise and automated machining. |
Jig Boring Machine | Specialized VMC with high precision for creating accurate holes and jigs. |
Lathe vs. Mill: Operational Principles & Machining Techniques
Lathe
The lathe operates on the principle of rotary machining. The workpiece spins continuously while a stationary cutting tool removes material to achieve the desired shape. Common techniques include:
- Turning: Reducing the diameter of a cylindrical workpiece.
- Facing: Creating a flat surface on the end of the workpiece.
- Drilling: Creating holes along the axis of rotation.
- Threading: Creating helical grooves for screws or fasteners.
Mill
The mill utilizes linear machining. The workpiece remains stationary, and a multi-tipped cutting tool fed by the machine removes material. Common techniques include:
- Milling: Creating flat surfaces, pockets, and slots with various milling cutters.
- Drilling and Boring: Creating holes of different sizes and depths.
- Facing: Similar to a lathe, creating a flat surface on a stationary workpiece.
- Slotting: Creating grooves or channels along the surface.
Lathe vs. Mill: Unique Features & Capabilities
Lathe excels at creating cylindrical shapes with smooth finishes and intricate details. It offers good concentricity (accuracy around the center) and can handle long, slender workpieces.
Mill provides greater versatility for machining various shapes, including flat surfaces, angles, pockets, and complex geometries. It allows for easy tool changes and machining multiple features at once.
Lathe vs. Mill: Precision, Speed & Efficiency
Precision: Both lathes and mills can achieve high precision with proper setup and tooling. However, CNC lathes often excel in creating parts with tight tolerances for diameters and round features.
Speed: Lathes can be very efficient for high-volume production of simple, symmetrical parts. Mills may require more setup time for complex geometries, impacting speed.
Efficiency: The efficiency of each machine depends on the specific job. Lathes excel at high-volume production of round parts, while mills offer more flexibility for intricate features on various shapes.
Lathe vs. Mill: Functions
Primary Function of Lathe
The primary function of a lathe is to remove material from a rotating workpiece to create cylindrical shapes or modify their diameter and length. It excels at machining features symmetrical about a central axis.
- Rotation: The workpiece spins on a central axis, allowing the cutting tool to interact with the entire circumference efficiently.
- Shaping: By moving the cutting tool across the rotating workpiece, the lathe can reduce the diameter (turning), create flat surfaces on the ends (facing), or cut grooves and threads.
- Dimensional Control: Precise control of the cutting tool path and rotation speed allows for accurate control over the final dimensions of the cylindrical workpiece.
Primary Function of Mill
Mill's primary function is to remove material from a stationary workpiece using a multi-pointed cutting tool to create flat surfaces, grooves, angles, pockets, holes, and complex contours on various workpiece shapes.
- Stationary Workpiece: The workpiece is firmly secured in place, enabling precise control of the cutting tool's movement.
- Multi-Axis Machining: The mill's cutting tool can move along multiple axes (X, Y, and Z) relative to the workpiece, providing great flexibility for machining different features.
- Feature Creation: Mills can create a wide range of features like flat surfaces through face milling, slots and grooves using peripheral milling, cavities and pockets with end milling, and long narrow slots with slot milling.
Lathe vs. Milling Machine: Pros & Cons
Lathe
Pros
- Excellent for Cylindrical Work: Creates smooth, precise cylindrical shapes with intricate details. Ideal for high-volume production of round parts like shafts, bearings, and bushings.
- High Concentricity: Due to the rotating workpiece, lathes excel at creating perfectly centered features like holes and grooves.
- Fast for Repetitive Tasks: Well-suited for repetitive turning operations on cylindrical stock, leading to efficient production.
- Relatively Simple Setup: Compared to mills, lathes often require less complex setup for basic operations like turning and facing.
Cons
- Limited Shape Capability: Primarily focused on cylindrical shapes and features symmetrical about a central axis. Not ideal for creating flat surfaces, complex angles, or intricate features on non-cylindrical workpieces.
- Larger Footprint: Lathes, especially those designed for larger workpieces, can take up significant floor space in a workshop.
Milling Machine
Pros
- Versatile Machining: Capable of machining a wider range of shapes, including flat surfaces, grooves, angles, pockets, holes, and complex contours on various workpiece geometries.
- Flexible Feature Creation: Offers greater freedom for creating intricate features like slots, pockets, and complex shapes compared to lathes.
- Drilling and Boring: Can efficiently drill and enlarge existing holes, making it a multifunctional machine.
Cons
- More Complex Setup: Milling complex shapes often requires multiple setups and tool changes, impacting production speed compared to lathes for simple cylindrical work.
- Lower Efficiency for Cylindrical Work: While mills can create cylindrical shapes, lathes generally offer higher efficiency for high-volume production of such parts.
- Learning Curve: Operating a mill effectively may require a steeper learning curve compared to basic lathe operations due to its multi-axis control.
Lathe vs. Mill: What to Consider When Choosing
Factor | Lathe | Milling Machine |
---|---|---|
Versatility | Limited to cylindrical shapes | Wide range of shapes (flat surfaces, grooves, angles, pockets, holes) |
Project Requirements | Precise cylindrical shapes with intricate details | Flat surfaces, complex geometries, various features |
Cost-Effectiveness | Generally more affordable (especially for basic models) | Higher initial cost due to complexity |
Scalability | Suitable for high-volume production of cylindrical parts | More versatile for diverse shapes and materials in the long run |
Conclusion
Both lathes and milling machines are powerful tools for shaping metal, but their strengths lie in different areas.
If your projects revolve around high-precision, cylindrical parts, a lathe offers efficiency and affordability. For projects demanding intricate features, flat surfaces, and work with diverse materials, a mill's versatility is unmatched.
Achieve Perfect CNC Machining at Unionfab
At Unionfab, we offer a full spectrum of CNC machining services, from CNC turning and milling to routing. Our multi-axis expertise allows us to craft custom solutions for your unique needs.
No matter your application, we ensure your project is produced accurately, efficiently, and at a competitive price.
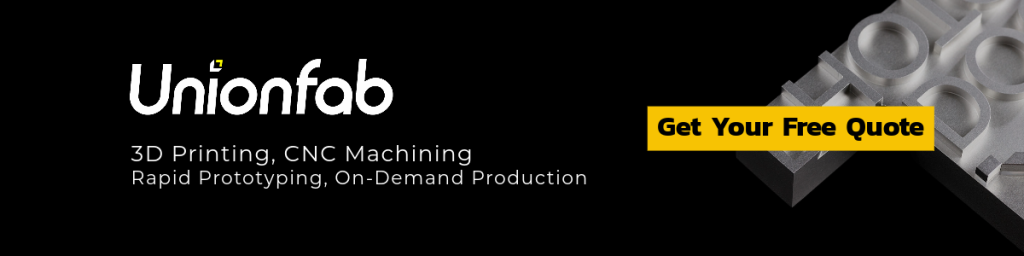