A Complete Guide to Bead Blasting
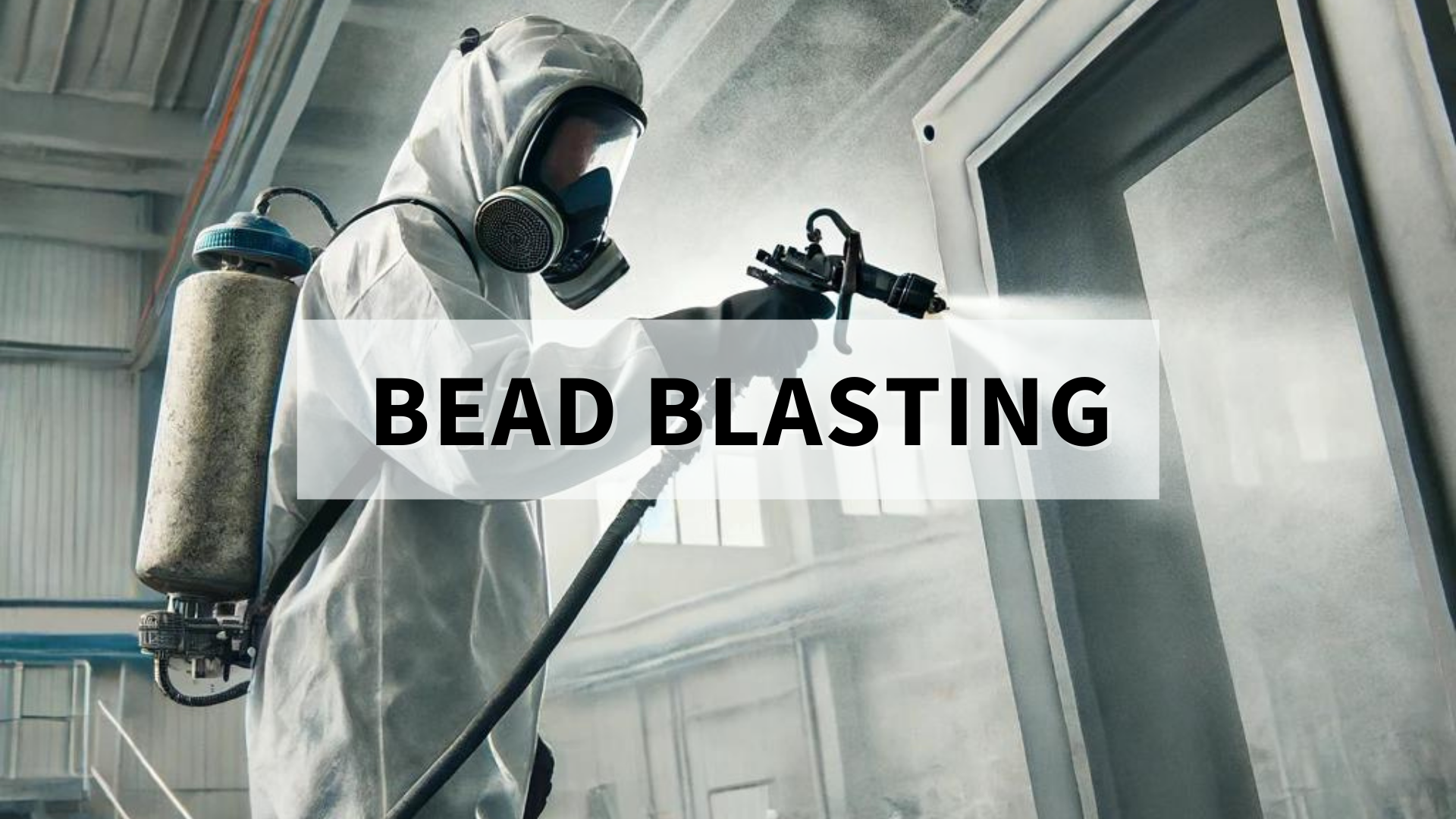
This article is a complete guide to bead blasting from its definition, media, equipment, pros & cons, and applications.
Introduction
Bead blasting is a versatile surface preparation technique widely used across various industries to achieve diverse surface finishes. This guide aims to provide a thorough understanding of bead blasting, from its fundamental principles to practical applications.
Therefore, whether you're a professional looking to refine your techniques or a novice seeking to learn more, this article will cover everything you need to know about bead blasting.
What is Bead Blasting?
Bead blasting is a surface preparation technique that uses a stream of small, abrasive beads propelled at high velocity by compressed air or centrifugal force to clean, smooth, or texturize a variety of materials.
Bead blasting is commonly used in industries like automotive, aerospace, and manufacturing to enhance appearance, remove contaminants, or alter surface properties. The type of bead media and blast parameters can be customized to achieve the desired finish, from a matte look to a polished shine.
Understanding the fundamentals of bead blasting and its versatile applications can help professionals make informed decisions about their surface preparation and finishing needs.
How Does Bead Blasting Work?
Bead Blasting Equipment
The bead blasting process relies on specialized equipment to effectively propel the abrasive media onto the target surface. The following table details the equipment used.
Bead Blasting Cabinet: An enclosed chamber that contains the blasting media and workpiece, protecting the operator. It is typically made of durable materials like steel or aluminum.
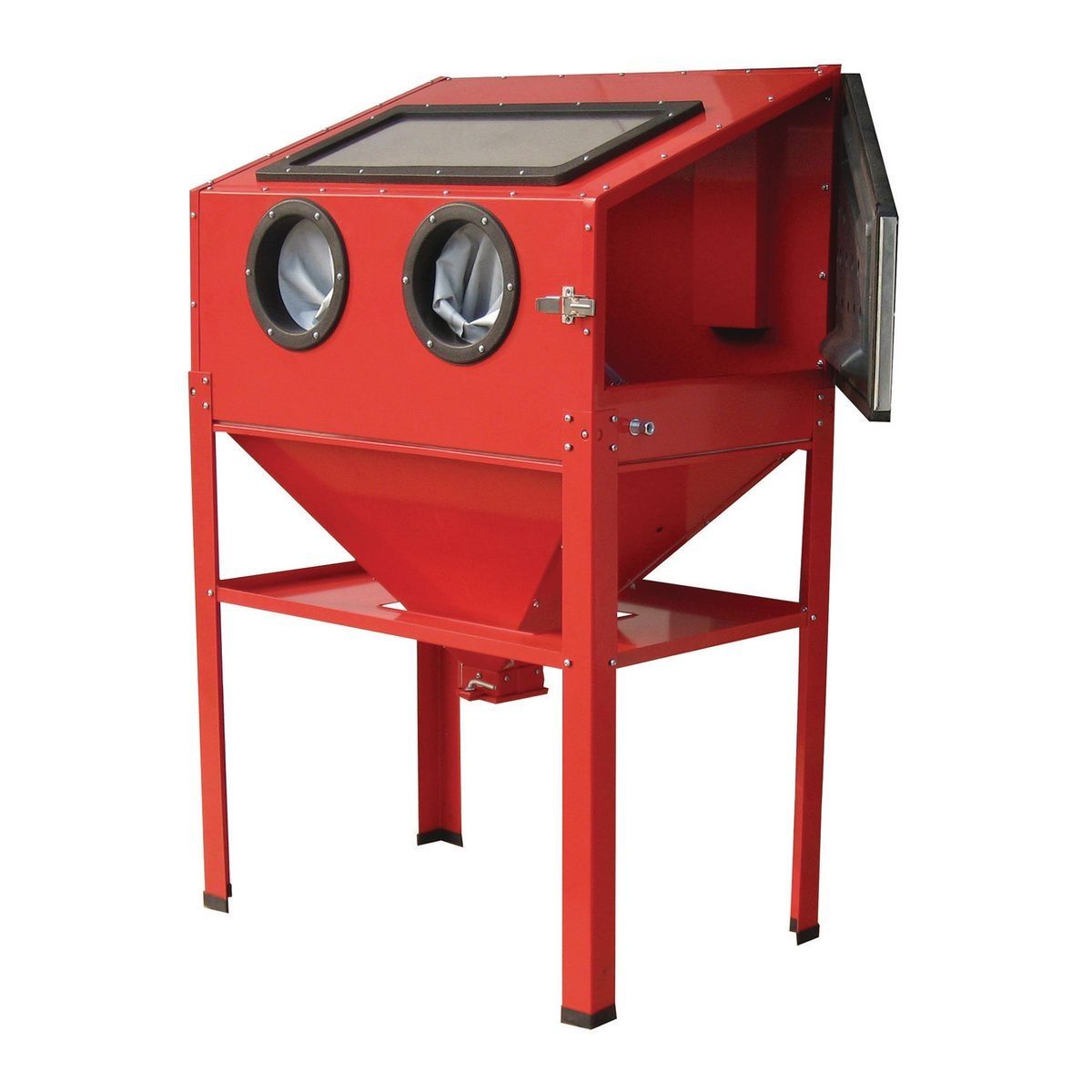
Air Compressor: It generates the high-pressure air flow to propel the bead media at the desired velocity.
Bead Blaster Gloves: Protective equipment worn by the operator to safeguard their hands during the blasting process.
Bead Blaster Gun: A specialized nozzle or gun used to direct and control the flow of the bead media onto the target surface.
Bead Blasting Media
Except for the equipment, the type of bead media is also a vital parameter to influence the final look of the finish. Therefore, here is a table telling the differences between the common media.
Type | Material | Hardness | Surface Finish | Cost | Advantages | Drawbacks | Ideal Applications |
---|---|---|---|---|---|---|---|
Glass Beads ![]() | Soda-lime glass | 5-6 Mohs | Uniform, matte | Low | Rounded, less aggressive | Prone to shattering, limited abrasion | Cleaning, deburring, peening |
Ceramic Beads ![]() | Aluminum oxide | 8-9 Mohs | Smooth, matte | Moderate | Sharper, more aggressive | Higher cost, potential for media breakdown | Polishing, deburring, etching |
Plastic Beads | Acrylic or nylon | 2-3 Mohs | Uniform, low-impact | Moderate | Rounded, non-abrasive | Limited cleaning and deburringcapabilities | Delicate parts, precision cleaning |
Steel Shot ![]() | Carbon steel | 7-8 Mohs | Smooth, glossy | Moderate to High | Rounded, peening action | Can cause surface contamination, higher media cost | Peening, deburring, surface hardening |
Aluminum Oxide ![]() | Fused aluminum oxide | 9 Mohs | Rough, aggressive | High | Sharp, angular | Potential for media breakdown, high dust generation | Heavy-duty cleaning, etching, profiling |
Silicon Carbide ![]() | Silicon and carbon | 9-10 Mohs | Aggressive, angular | High | Extremely sharp, high cutting ability | Potential for media breakdown, high dust generation | Aggressive cleaning, surface texturing |
Step-by-Step Video Demonstration
To further illustrate the bead blasting process, we've included a step-by-step video demonstration that presents the technique in action.
Pros and Cons of Bead Blasting
The common Pros and Cons of Bead Blasting are presented below:
Pros:
Produces uniform, consistent finish
Effectively removes contaminants and burrs
Enhances material hardness and fatigue life
Allows precise control of blast parameters
Generally cost-effective
Cons:
Generates significant dust and debris
Highly abrasive media can damage delicate surfaces
Media breakdown over time requires replacement
More labor-intensive than some methods
Requires proper containment and safety measures
Tips for Best Operations and Practices
Safety First - Gear Up
Respirator: Use a NIOSH-approved respirator to protect against dust.
Helmet: Wear a fully enclosed helmet with an air supply to protect your head, neck, and shoulders.
Gloves: Use thick, cut-resistant gloves to protect your hands and forearms.
Eye Protection: Wear safety glasses or a visor under your helmet for extra eye protection.
Earplugs: Use earplugs or noise-canceling headphones to protect your ears.
Blast Suit: Wear a blast suit or heavy clothing to keep abrasives off your skin.
Prepare the Environment
Ventilation: Ensure proper ventilation to remove dust particles, using exhaust fans or blasting respirators.
Pre-Blasting Clean Up: Remove flammable materials and clutter from the blasting area to minimize fire and tripping hazards.
Signage: Mark the blasting area with clear, visible signs indicating restricted access and required PPE.
Proper Lighting: Ensure good lighting in the blasting area, using adjustable lights for hard-to-see spots.
Monitor Workpiece Temperature: Allow workpieces to cool if they get too hot to touch.
Equipment Setup and Maintenance
Pre-Operation Inspection: Regularly check hoses, couplings, the blasting unit, and the air compressor for wear, leaks, or damage.
Safety Features: Ensure the deadman trigger and pressure relief valve work correctly.
Calibration: Maintain air pressure and media flow as per the manufacturer's guidelines.
Scheduled Maintenance: Perform regular maintenance and replace worn parts as per the equipment manual.
Blasting Technique
Distance and Angle: Keep a consistent distance and angle between the nozzle and the workpiece for even blasting.
Media Flow and Pressure: Gradually increase pressure and media flow to the minimum needed for the desired result.
Safe Working Distance: Maintain a recommended safe distance from the work surface for better control and safety.
Nozzle Control: Never point the nozzle at yourself or others; always direct the abrasive stream at the work surface.
Whip Checks: Use whip checks on hose connections to prevent injuries from accidental disconnections.
Post-Blasting Clean Up
HEPA Vacuum: Use HEPA-filtered vacuums to clean up fine dust particles in the blasting area.
Avoid Compressed Air: Do not use compressed air for cleaning, as it can stir up hazardous dust.
Blasting Media Disposal: Dispose of used blasting media according to local regulations and the media's Safety Data Sheet (SDS).
Ergonomic Considerations
Cabinet Position: Set the blasting cabinet at a comfortable height to reduce back strain.
Anti-Fatigue Mats: Use anti-fatigue mats if you need to stand for long periods.
Applications of Bead Blasting
Bead blasting, a versatile surface treatment process, finds applications across various industries due to its ability to clean, finish, and enhance materials without causing significant surface damage. Below are specific examples of bead blasting applications in different fields:
Automotive Industry
Surface Preparation: Cleans and prepares surfaces for painting or coating, ensuring better adhesion and a smooth finish.
Restoration: Removes rust, old paint, and grime from classic car parts without damaging the underlying material.
Engine Component Cleaning: Cleans engine parts like cylinder heads and intake manifolds, removing carbon deposits and contaminants.
Aerospace Industry
Component Maintenance: Cleans turbine blades, engine components, and landing gear, removing corrosion and contaminants while maintaining tolerances.
Surface Finishing: Achieves desired finishes (matte, textured) for aesthetic, adhesion, and aerodynamic improvements.
Medical Industry
Instrument Sterilization: Removes impurities from medical instruments, implants, and devices, meeting hygiene standards.
Surface Texturing: Creates rough surfaces on implants to enhance bone adhesion and tissue integration.
Manufacturing Industry
Tool and Die Cleaning: Removes residue, scale, and oxidation from molds and dies, extending lifespan and ensuring product quality.
Surface Finishing: Provides a consistent finish on machined parts, thus reducing the need for further polishing.
Electronics Industry
PCB Cleaning: Cleans printed circuit boards, removing solder residues and contaminants without damaging circuits.
Component Preparation: Prepares electronic component surfaces for better adhesion of coatings or bonding materials.
Art and Design
Surface Texturing: Creates unique textures and finishes on metal, glass, and ceramic artworks.
Restoration: Restores antiques and sculptures by removing dirt, corrosion, and old finishes without damage.
Construction and Architecture
Concrete Surface Preparation: Prepares concrete for coating or sealing, ensuring better adhesion and application.
Stone and Tile Cleaning: Cleans and restores natural stone and tiles, removing stains and weathering effects without altering appearance.
Comparison with Sand, Shot & Grit Blasting
Aspect | Bead Blasting | Sandblasting | Shot Blasting | Grit Blasting |
---|---|---|---|---|
Media | glass/ceramic beads, steel shot | sand (silica or alternative) | steel shot, grit, cut wire | aluminum oxide, silicon carbide, garnet |
Material Suitability | metals, plastics, glass, ceramics | metals, concrete, stone | metals, durable materials | metals, concrete, stone |
Aggressiveness | moderate | high | high | very high |
Cost | moderate | low | high | moderate to high |
Precision | high | low to moderate | moderate to high | moderate to high |
Advantages | surface-friendly smooth finish | heavy-duty cleaning efficiency | hard material effectiveness and surface strengthening | aggressive cleaning and prep efficiency |
Drawbacks | less effective on very tough contaminants | high dust and silica risk | high equipment and media costs and wear risk | high dust risk, extensive PPE and safety requirements |
Applications | cleaning, surface prep, texturing | paint/rust removal, surface prep | surface prep, cleaning, peening | paint/rust removal, surface prep |
Choosing the Right Bead Blasting Equipment
Factors to consider
When selecting bead blasting equipment, it’s crucial to consider several factors to ensure you choose the right machine for your specific needs. Here are the key points to keep in mind:
Project Size
Small: Benchtop bead blaster for detailed work.
Large: Full-sized blast cabinet or industrial-grade machine for bigger tasks.Budget
Entry-Level: Affordable models for occasional use.
Professional: Higher-end, durable machines for regular, professional use.Space Availability
Compact Spaces: Compact or benchtop models for limited space.
Large Workspaces: Larger cabinets for more room and powerful equipment.Ease of Use
User-friendly controls and easy maintenance features, especially important for beginners.Dust Collection
Effective dust collection systems to maintain a clean and safe working environment.Durability
High-quality materials that can withstand regular use and abrasive media.
Recommendations for Top Bead Blasting Machines
Brand | Description |
---|---|
Offers a range of blast cabinets and portable blast machines known for their durability and performance. | |
Provides affordable and reliable benchtop and cabinet blasters suitable for hobbyists and small workshops. | |
Highly regarded for their durability and efficiency, suitable for both small and large projects. | |
Offers a variety of blast cabinets, from entry-level to professional-grade, with excellent customer support. | |
Provides a range of affordable blast cabinets, ideal for small to medium-sized projects. |
Choosing a Bead Blasting Service
When selecting a bead blasting service, it's important to evaluate several key factors to ensure you receive high-quality and reliable results. Here are the main points to consider:
Factors to Consider
Experience: Choose a provider with extensive industry experience for reliable and high-quality results.
Equipment Capabilities: Ensure the provider uses modern, well-maintained equipment suitable for your project requirements.
Safety Measures: Verify that the provider follows strict safety protocols and uses proper PPE and dust collection systems to protect both their workers and your project.
Certifications: Look for relevant certifications like ISO 9001, indicating commitment to quality and industry standards.
Unionfab' s Service
Unionfab excels in providing comprehensive finishing services, highlighted by four key strengths: experience, certification, shipping, and cost.
Experience: One of China's first industrial-grade 3D printer manufacturers; with 20+ years' experience in 3D printing.
Certification: Meeting the rigorous ISO 9001 quality management standards.
Shipping: Air shipments in 3-5 days via DHL Express and FedEx.
Cost: 70% cheaper than European and American competitors.
FAQs
Is glass bead blasting safe?
Yes, glass bead blasting is generally considered safer than other blasting techniques like sandblasting due to the media used. Here's why glass bead blasting is considered safer:
Media: Glass beads are non-toxic and don't contain free silica. Silica, a major health concern in sandblasting, can lead to lung diseases like silicosis.
Gentler Abrasive: Glass beads are less abrasive than sand. Therefore, they are suitable for delicate surfaces where sandblasting would cause damage.
Reduced Dust: Glass beads tend to generate less dust compared to sand, lowering the overall airborne particles you need to be concerned about.
How long does bead blasting take?
The time it takes to bead blast something mainly depends on the size of the surface and the desired finish. Here's a general guideline:
Small objects (think jewelry or small car parts): A few minutes to ten minutes.
Medium-sized surfaces (think motorcycle wheels or furniture panels): Fifteen minutes to an hour.
Large surfaces (think car bodies or bridge beams): Several hours or even a full day.
Can you bead blast aluminum?
Yes, bead blasting can be used on aluminum surfaces. Aluminum parts that require a dull finish are typically bead blasted. Compared to sandblasting, which can be too aggressive for aluminum, bead blasting offers a gentler touch. Specifically, glass beads won't gouge or damage the aluminum surface as much as sand particles.
What is the difference between bead blasting and sandblasting?
Both bead blasting and sandblasting are techniques for cleaning and shaping surfaces, but they differ in their media (the abrasive material used) and their overall effect. Here's a breakdown of the key differences:
Feature | Bead Blasting | Sandblasting |
---|---|---|
Media | Glass or ceramic beads | Silica sand |
Impact | Gentler | More aggressive |
Applications | Cleaning, deburring, polishing | Heavy-duty cleaning, rust removal, shaping metal |
Results | Smooth, polished finish, matte/satin texture | Roughened surface, clean metal |
Safety | Generally safer (non-toxic media) | Requires stricter precautions (silica dust hazard) |
Conclusion
Bead blasting is a versatile technique used across industries for various surface finishes. Understanding the equipment, media types, best practices, and safety precautions is essential for effective and safe bead blasting.
By following safety protocols and industry standards, businesses can harness bead blasting to improve the appearance, performance, and longevity of their products. Whether you tackle the task yourself with proper equipment or choose a reliable service provider like Unionfab, being well-informed ensures optimal performance and quality.
Leveraging the expertise in this guide can help unlock the full potential of bead blasting to improve your projects' efficiency and aesthetic appeal.