Powder Coating Thickness: A Comprehensive Guide
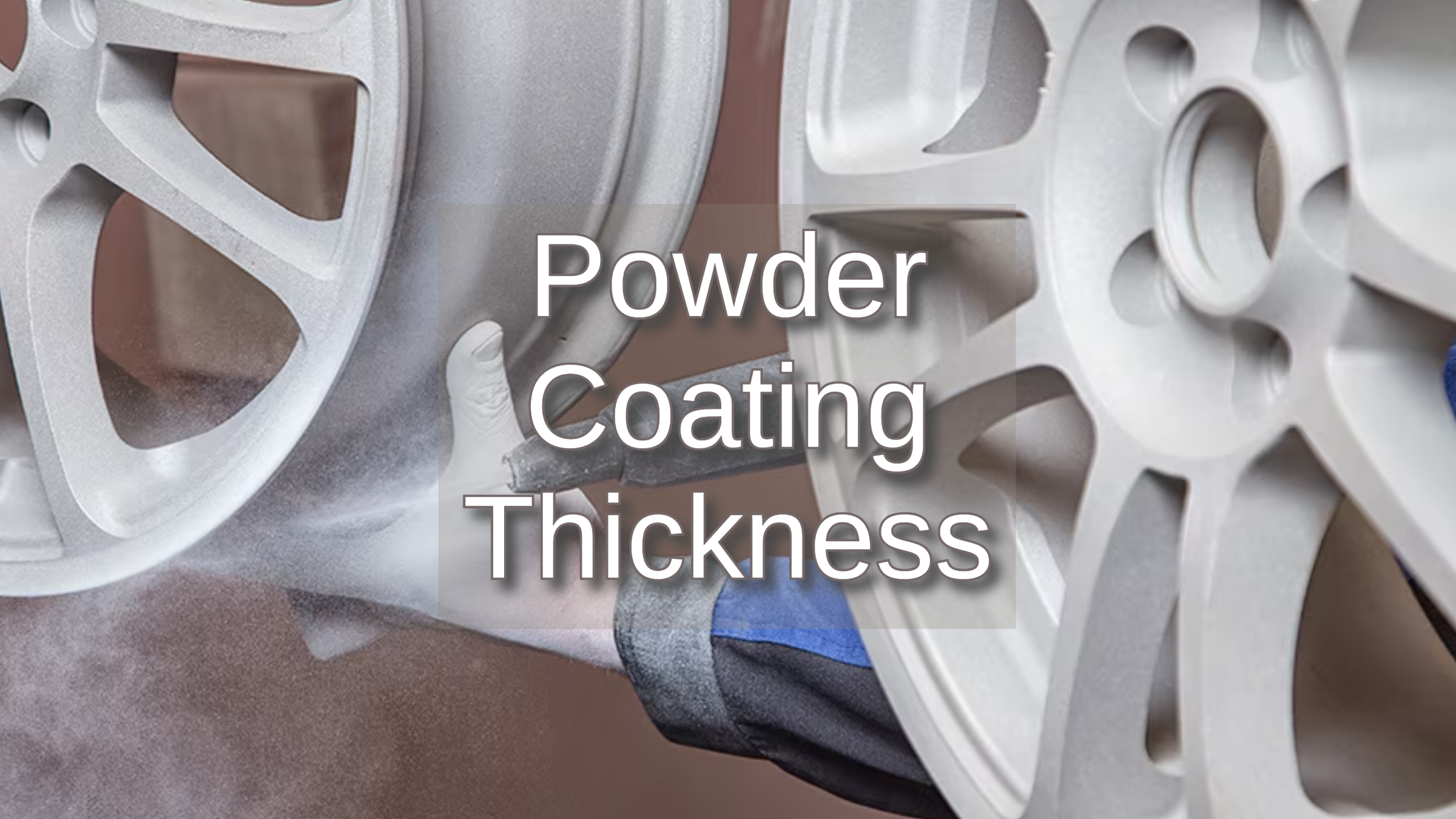
Uncover the secrets of a flawless finish. This guide explores powder coating thickness, covering its importance, measuring methods and standards.
Introduction
Powder coating is a common method for giving metal objects a durable, attractive finish. It is the fastest growing of all the finishing technologies. Instead of using liquid paint, it involves spraying electro-statically charged dry powder onto the surface.
The thickness of the coating is a key factor in the process, which plays a crucial role in the final quality and performance. In this guide, we will explore why coating thickness matters and how it impacts the finished product.
Importance of Powder Coating Thickness
Powder coating thickness is vital for the overall quality and performance of the finished product:
Factor | Impact of Powder Coating Thickness |
---|---|
Durability | Thicker = More durable, Thinner = Less durable |
Appearance | Thicker = Orange peel texture, Thinner = Smoother finish |
Adhesion | Proper thickness = Optimal adhesion, Too thin/thick = Poor adhesion |
Material Efficiency | Right thickness = Material efficiency, Too much/less = Wasteful |
Standard/Typical Powder Coating Thickness
Powder coating thickness isn’t a one-size-fits-all situation. Finding the ideal thickness involves balancing performance with practicality.
Standard Units
Mils (thousandths of an inch): Often used in the US and Canada.
Microns (thousandths of a millimeter): Used in Europe and elsewhere.
Typical Thickness Guidelines
Application | Thickness (Mils) | Thickness (Microns) | Notes |
---|---|---|---|
General | 2.0 – 5.0 | 50 – 125 | Standard protective coatings |
Quick Removal | 1.0 – 1.5 | 25 – 37.5 | Easy to remove without residue |
Architectural | 2.4 – 3.2 | 60 – 80 | Qualicoat and AAMA 2605 standards |
Industrial | 4.0 – 10.0 | 100 – 250 | Varies by environment and protection needs |
General Powder Coating Thickness
The majority of powder coatings have a thickness ranging from 2.0 to 5.0 mils (50 to 125 microns). This provides a balanced combination of durability and aesthetics suitable for general use applications.
Some specialized coatings may have a reduced thickness down to 1.0 mils where easy removal property is required.
In some heavy industrial applications involving severe abrasion, chemical exposure, or other extreme operating conditions, much thicker powder coatings of 5.0 mils or greater may be applied.
Standards for Powder Coating Thickness
Qualicoat Specifications
Qualicoat sets thickness requirements for powder coatings on aluminum used in architectural applications.
Depending on the class of coating, the minimum thickness usually ranges from 60 to 80 microns (approximately 2.4 to 3.2 mils).
AAMA 2605
The American Architectural Manufacturers Association (AAMA) specifies performance requirements for high-performance organic coatings, including powder coatings.
AAMA 2605 requires a minimum thickness of 50 microns (2 mils) for certain architectural applications, with higher thicknesses for more demanding environments.
BS EN 12206-1
This British Standard specifies the thickness and quality requirements for coatings on aluminum and aluminum alloys, including powder coatings.
Minimum thickness values typically range from 60 to 80 microns, depending on the environment and application.
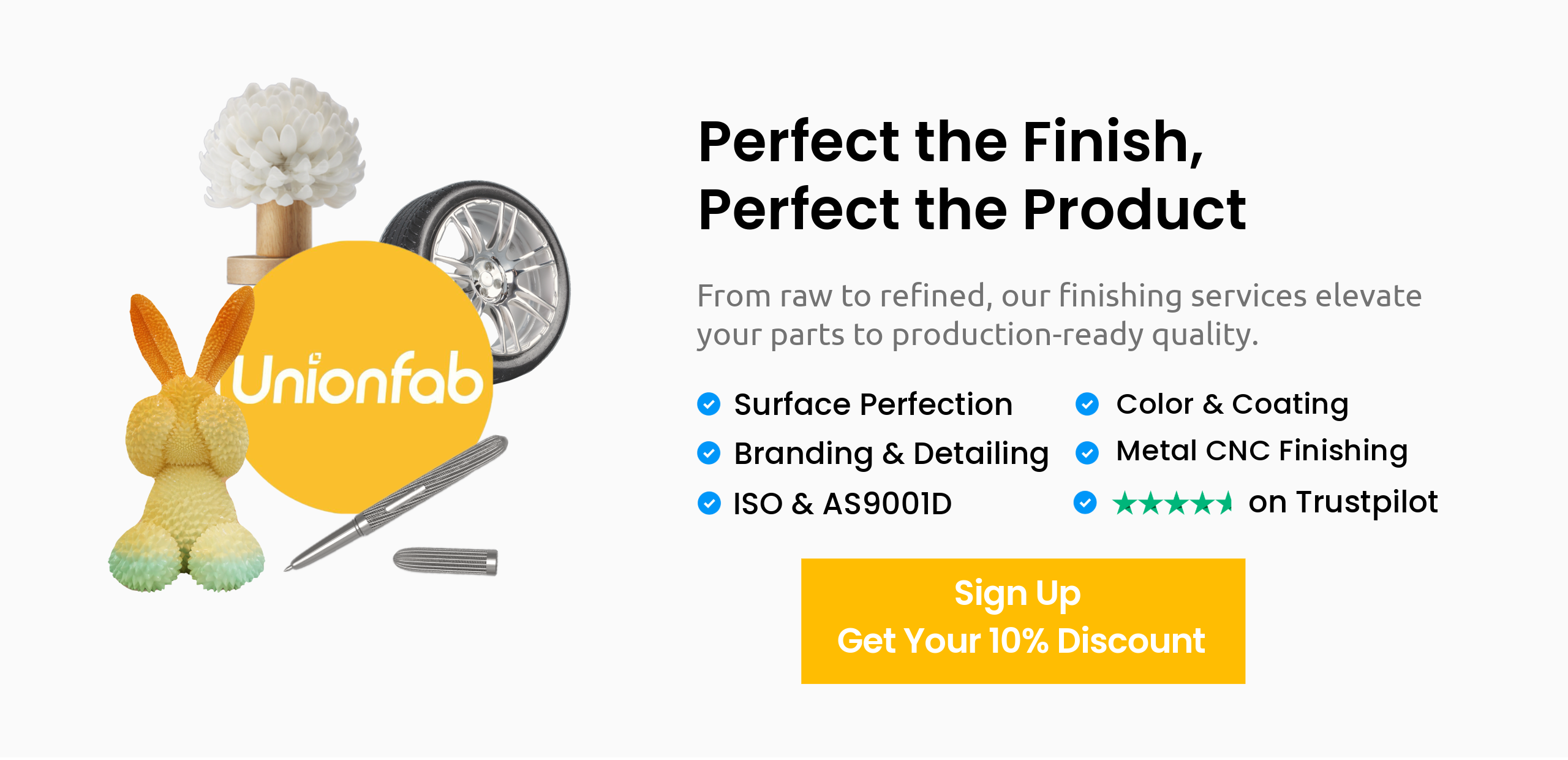
At Unionfab, we provide expert powder coating services tailored to meet your project’s specific needs. Simply contact our team to discuss your project requirements and receive a personalized quote.
Factors Affecting Powder Coating Thickness
Powder Coating Method
Electrostatic Spraying
The most common method, where powder is applied using an electrostatic gun.
Factors like air pressure, flow rate, and gun voltage significantly impact the amount of powder deposited. Higher air pressure or flow rate can lead to thicker coatings, while lower settings result in thinner layers.
Operator technique can influence thickness uniformity. Maintaining a consistent distance and spray pattern is crucial to avoid areas with excessively thick or thin coatings.
Fluidized Bed Coating
The thickness is influenced by the immersion time, temperature, and viscosity of the powder in the bed.
Powder Size and Powder Type
Powder coatings consist of pigment and resin particles that are finely ground into a blended powder mixture. Their properties will affect the thickness of a powder coating.
Particle Size: Smaller particle sizes tend to produce a smoother and thinner coating, while larger particles often result in a thicker and more textured coating.
Powder Composition: Powders with good flow characteristics can create smooth, even coatings at the desired thickness. However, powders with higher melting points may require adjustments in application settings to avoid an overly thick coating.
Substrate Material
Thermal Conductivity: Materials like aluminum, which dissipate heat quickly, may lead to thinner coatings. Conversely, steel, with lower thermal conductivity, might retain heat longer, potentially resulting in thicker coatings.
Surface Texture: Rough or porous surfaces may require more powder to achieve a uniform coating, increasing thickness.
Measuring Powder Coating Thickness
Dry film thickness (DFT) gauges are commonly used to check cured powder coatings. They can measure the thickness without harming the coating.
DFT instruments ues different techniques to measure. Here are the most common methods:
1. Magnetic Induction
This method is used to measure the thickness of non-magnetic coatings (e.g., paint, powder coatings) on ferromagnetic substrates (e.g., steel, iron).
How It Works: A probe generates a magnetic field that changes based on the distance from the substrate, which is influenced by the thickness of the coating. The instrument then converts this change into a DFT reading.
Instruments: Handheld magnetic thickness gauges like the Elcometer 456 or Fischer Feritscope.
2. Eddy Current
This method is used for measuring the thickness of non-conductive coatings (e.g., powder coatings, anodizing) on non-ferrous metal substrates (e.g., aluminum, brass).
How It Works: A coil in the probe generates an alternating magnetic field, inducing eddy currents in the conductive substrate. The strength of these currents varies with the distance from the coil, allowing for measurement of the coating thickness.
Instruments: Eddy current thickness gauges like the PosiTector 6000 or Elcometer 456 with eddy current probes.
3. Ultrasonic Pulse-Echo
Suitable for measuring the thickness of coatings on non-metallic substrates (e.g., wood, plastic) and multi-layer coatings.
How It Works: The instrument emits an ultrasonic pulse that travels through the coating and reflects back from the substrate. The time it takes for the echo to return is used to calculate the coating thickness.
Instruments: Ultrasonic thickness gauges like the PosiTector 200 or Elcometer 500.
How to Achieve Ideal Powder Coating Thickness
Powder coating thickness isn't a one-size-fits-all situation. Finding the ideal thickness involves balancing performance with practicality.
1. Surface Preparation
Cleaning: Remove contaminants like oils, grease, and dirt. This can be done through methods like degreasing, sandblasting, or chemical cleaning.
Pretreatment: Apply a suitable pretreatment, such as phosphating or chromating, to enhance adhesion and corrosion resistance.
2. Choosing the Right Powder
Powder Selection: Choose a powder formulated for the specific application and environment. Consider factors like the substrate, required thickness, and desired finish.
Particle Size: Opt for powders with consistent particle size distribution to ensure uniform application.
3. Optimizing Application Settings
Gun Settings: Adjust the electrostatic voltage and powder flow rate according to the manufacturer’s recommendations and the specific part geometry.
Spray Distance: Maintain an appropriate distance between the spray gun and the part, typically 6 to 12 inches, to ensure even coverage.
Part Positioning: Ensure parts are positioned correctly in the spray booth to allow for even coating and minimize shadowing or uneven buildup.
4. Controlled Environment
Control the temperature and humidity in the spray booth to avoid issues like powder clumping or poor adhesion.
5. Proper Curing Process
Set the curing oven to the correct temperature as specified by the powder manufacturer, typically between 350°F and 400°F (177°C to 204°C).
6. Thickness Testing
Regularly measure the Dry Film Thickness (DFT) using appropriate instruments to ensure it falls within the desired range.
Conclusion
Achieving optimal powder coating thickness is crucial for ensuring the durability, appearance, and performance of coated products.
Regular testing and adjustments further ensure that the coating thickness remains consistent and effective, contributing to the overall quality and success of the final product.
Why Choose Unionfab for Powder Coating?
One-Stop Manufacturing: In addition to coating, we offer end-to-end manufacturing solutions, including 3D printing, CNC machining, Casting, and post-processing.
Custom Solutions: From color selection to thickness optimization, we work with you to achieve your vision.
Precision & Quality: Our experts use advanced techniques to ensure every coating meets the highest standards.
Contact us now to get started!
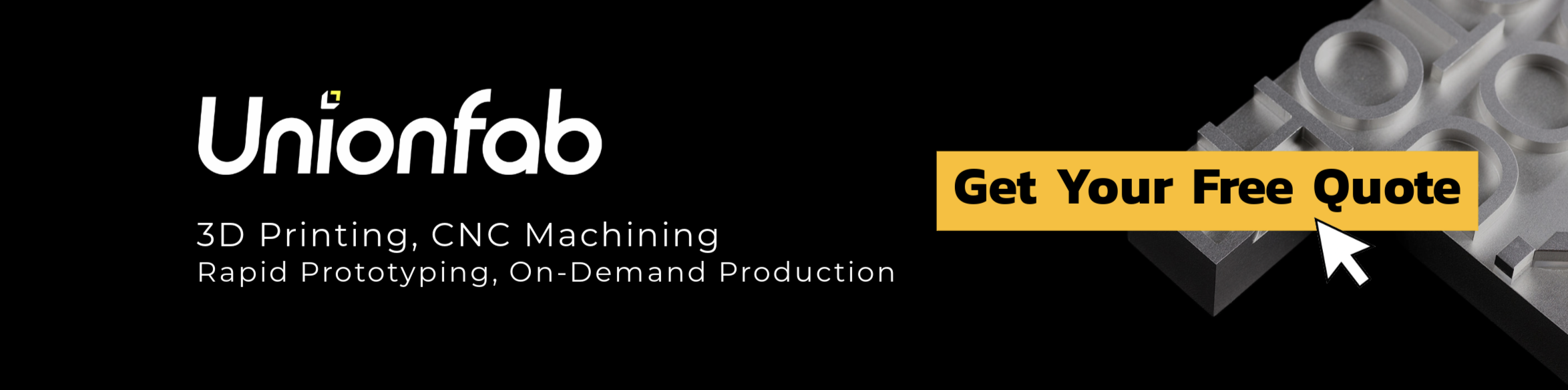