Polypropylene vs. Nylon: Which One to Choose?
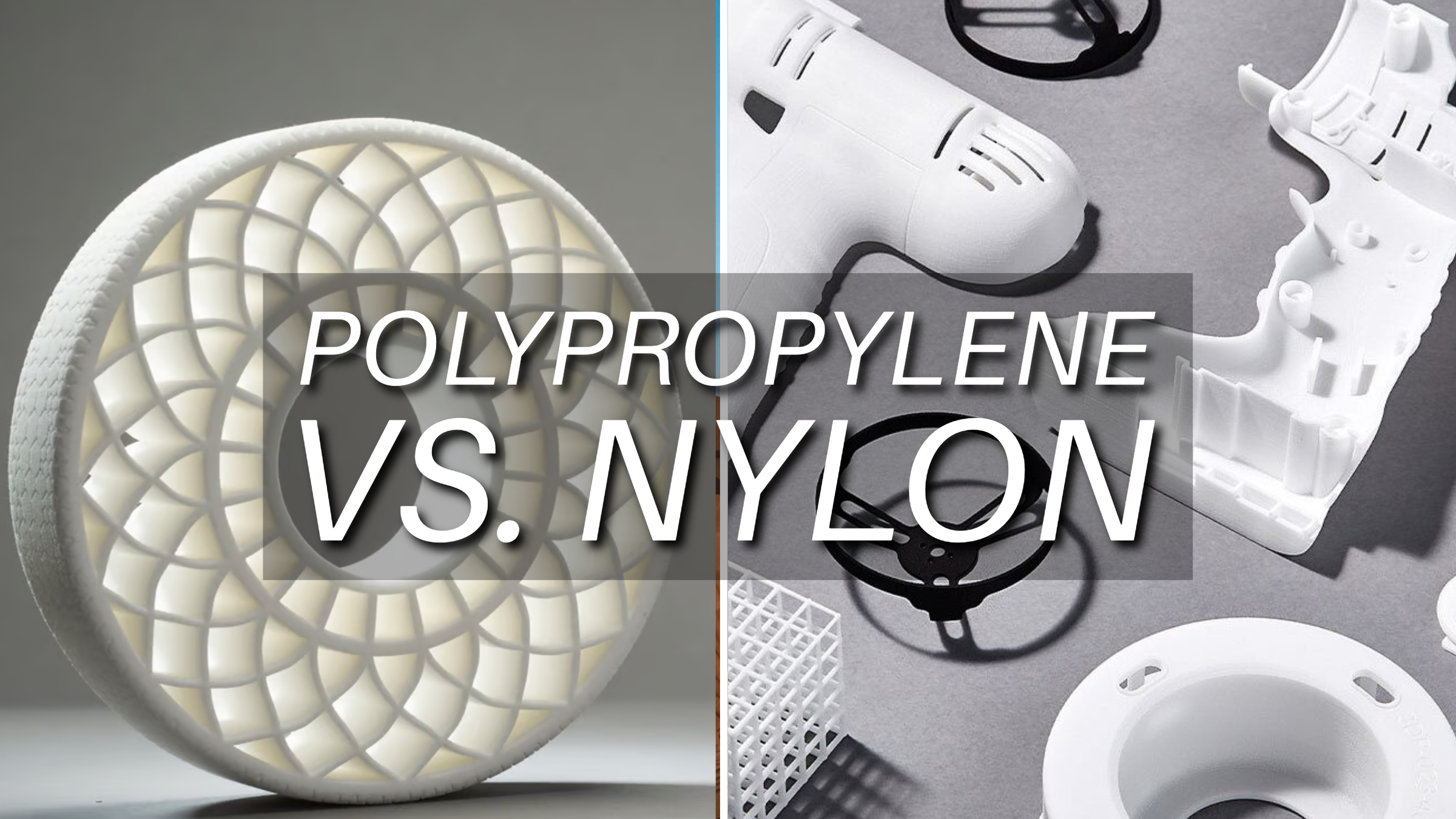
This article examines Polypropylene vs. Nylon, comparing their qualities, applications, and benefits in many sectors.
Introduction
Polypropylene (PP) and nylon are both commonly used synthetic polymers with advantageous properties for many industries.
Despite both being classified as plastics, they have distinct characteristics that make them better suited for different applications.
Comparing polypropylene and nylon goes beyond just understanding their individual properties. It allows us to make informed decisions about material selection based on specific needs.
What is Polypropylene
Definition of Polypropylene
Polypropylene is a polyolefin, a type of polymer formed by the chain-like linkage of repeating propylene monomers (C3H6).
Chemical Composition of Polypropylene
Polypropylene is a hydrocarbon, meaning its backbone is made entirely of carbon and hydrogen atoms. The chemical formula for polypropylene can be represented as (C3H6)n, where "n" signifies the vast number of repeating propylene units.
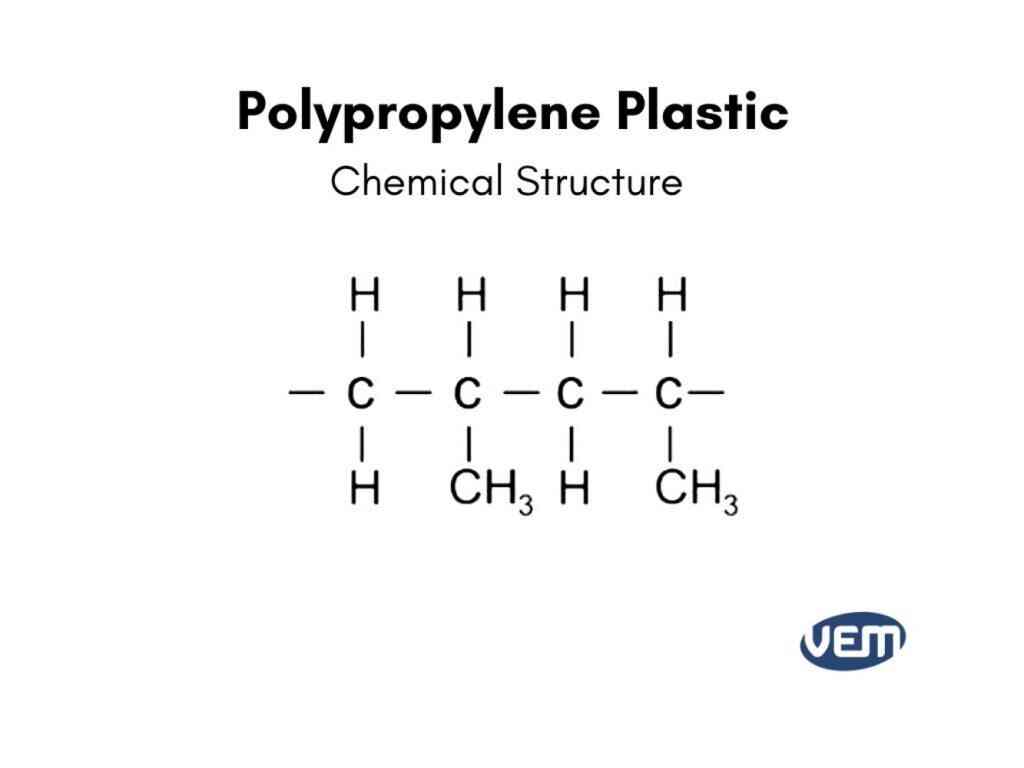
Source: vem-tooling.com
Physical properties of Polypropylene
Polypropylene (PP) has a partially crystalline structure. It is a mix of ordered and disordered regions. This unique structure contributes to its interesting properties.
- Strength: Polypropylene offers good tensile strength and rigidity, making it suitable for load-bearing applications.
- Flexibility: Compared to other thermoplastics like polyethylene, PP is slightly less flexible but still exhibits some degree of bendability.
- Density: Polypropylene is a low-density material, lighter than water and most other common plastics. This makes it ideal for applications where weight reduction is crucial.
- Heat Resistance: PP boasts good heat resistance, with a melting point around 160°C (320°F). This allows it to withstand moderate temperatures without deformation.
- Chemical Resistance: Polypropylene is resistant to most chemicals and solvents at room temperature, making it suitable for storing various products.
Industry Applications of Polypropylene
Polypropylene's versatility is reflected in its diverse applications across numerous industries.
- Automotive: Parts like bumpers, dashboards, and interior panels utilize PP due to its lightweight nature, good strength, and heat resistance.
- Packaging: Food containers, bottles, and caps often rely on PP for its chemical resistance, moisture barrier properties, and cost-effectiveness.
- Textiles: Non-woven fabrics and carpets sometimes incorporate PP fibers for their strength, durability, and stain resistance.
- Medical Devices: Syringes, vials, and other medical equipment benefit from PP's sterility, chemical resistance, and biocompatibility.
- Consumer Goods: Appliance parts, toys, furniture, and storage containers often use PP due to its affordability, durability, and lightweight properties.
What is Nylon
Definition of Nylon
Nylons belong to a group of polymers called polyamides. These are formed when diamine and dicarboxylic acid molecules react, creating long chains with repeating amide linkages (-CO-NH-).
Chemical Composition of Nylon
Different combinations of diamines and dicarboxylic acids create various types of nylon, each with slightly different properties. For example, Nylon 66, the most common type, uses hexamethylene diamine and adipic acid.
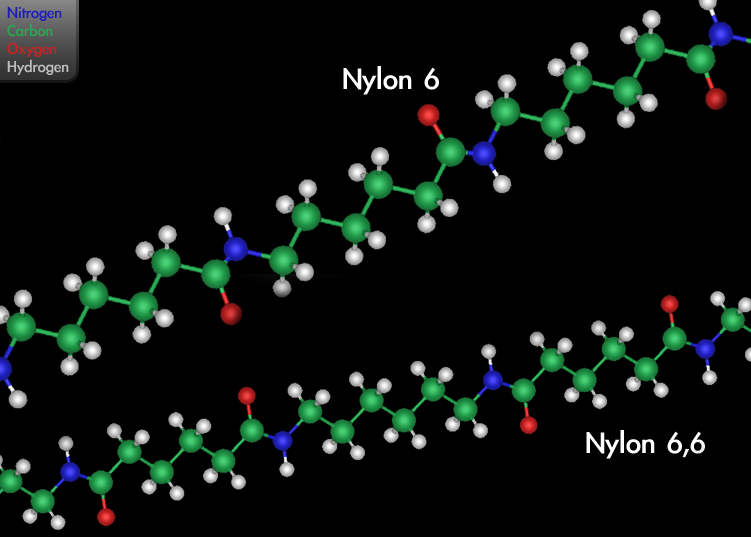
Source: wikimedia.org
Physical properties of Nylon
Durability
Nylon is known for its exceptional durability. The strong amide bonds give it high tensile strength, meaning it can resist significant pulling forces without breaking. This makes it ideal for applications requiring long-lasting performance.
Elasticity
While not as stretchy as rubber, nylon exhibits good elasticity, allowing it to recover its shape after being stretched. This property makes it perfect for fabrics that need to retain their form but also offer some give.
Abrasion Resistance
Nylon excels in resisting wear and tear. This makes it a top choice for carpets, ropes, and clothing exposed to friction.
Heat Resistance
Nylons have good heat resistance, typically able to withstand temperatures around 150°C (300°F) before melting. This allows them to be used in applications involving moderate heat.
Low Friction
Nylon exhibits a low coefficient of friction, meaning surfaces made of nylon slide smoothly against each other. This makes it suitable for gears, bearings, and other components requiring smooth movement.
Industry Applications of Nylon
Nylon's diverse properties have led to its widespread use across various sectors.
- Engineering: Gears, bearings, tubing, and other high-performance parts often utilize nylon due to its strength, wear resistance, and low friction.
- Textiles: Clothing, carpets, sportswear, and hosiery heavily rely on nylon for its durability, elasticity, and wrinkle resistance.
- Household Products: Toothbrush bristles, zipper closures, and various household goods benefit from nylon's strength, flexibility, and abrasion resistance.
- Sports and Recreation: Fishing lines, tents, and sports equipment leverage nylon's strength, lightweight nature, and weather resistance.
- Medical Applications: Sutures, surgical mesh, and other medical devices utilize nylon's strength, biocompatibility, and sterility.
Polypropylene vs. Nylon: Pros and Cons
Polypropylene (PP) and nylon are two common and versatile plastic materials, but they each have distinct strengths and weaknesses. Selecting the right one depends on the specific application's needs.
Feature | Polypropylene (PP) | Nylon |
---|---|---|
Cost | More affordable | Generally more expensive |
Weight | Lightweight | Can be heavier |
Chemical Resistance | Excellent | Good |
Moisture Barrier | Good | Can absorb moisture |
Strength & Rigidity | Good | Excellent |
Brittleness | Can become brittle at low temperatures | More flexible at low temperatures |
Heat Resistance | Lower heat deflection temperature | Higher heat deflection temperature |
Flexibility | Less flexible | More elastic |
UV Resistance | Susceptible to UV degradation (requires additives for outdoor use) | More UV resistant |
Abrasion Resistance | Good | Excellent |
Friction | Higher friction | Lower friction |
Polypropylene vs. Nylon: Applications
Polypropylene (PP) and nylon are both widely used plastics, but their strengths make them ideal for different applications.
Application Area | Polypropylene (PP) Excels Because | Nylon Outperforms Because |
---|---|---|
Cost-Conscious Applications | More affordable | - |
Lightweight Advantage (e.g., Automotive) | Lower weight for improved fuel efficiency | - |
Chemical Resistance (e.g., Containers) | Excellent resistance to chemicals | - |
Moisture Barrier (e.g., Packaging) | Good moisture barrier properties | - |
Durability (e.g., Carpets, Ropes) | - | Exceptional durability and abrasion resistance |
Elasticity (e.g., Sportswear) | - | Good elasticity for stretch and recovery |
Heat Resistance (e.g., Gears) | - | Higher heat tolerance |
Friction Reduction (e.g., Bearings) | - | Lower friction coefficient for smooth movement |
Industries Benefiting Most | Packaging, Automotive, Medical, Textiles | Textiles, Engineering, Sports & Recreation, Household Products |
Polypropylene vs. Nylon: Environmental Considerations
When choosing between polypropylene (PP) and nylon, environmental impact becomes an important factor.
Polypropylene (PP):
- Production Concerns: PP production requires a significant amount of energy and emits greenhouse gases. Additionally, some catalysts used in the process can be harmful to the environment.
- Durability and Disposal: While PP is durable, it's often used in disposable products like single-use plastics. This contributes to landfill waste and potential plastic pollution.
- Recycling Potential: PP is considered highly recyclable. However, the recycling infrastructure for PP varies depending on location.
Nylon:
- Energy-Intensive Production: Nylon production is even more energy-intensive than PP, leading to a larger carbon footprint.
- Slower Biodegradation: Unlike some plastics, nylon doesn't readily biodegrade, posing a longer-term environmental concern if it ends up in landfills.
- Mixed Recycling Stream: Nylon recycling can be complex as different nylon types require separate processing. Additionally, nylon often blends with other materials, making separation for recycling more challenging.
Sustainability Aspects:
- Reduce and Reuse: Regardless of the material, reducing plastic consumption and reusing products whenever possible is the most sustainable approach.
- Recycled Content: Look for products made with recycled PP or nylon content whenever available. This reduces reliance on virgin materials and promotes a more circular economy.
- Biodegradable Alternatives: In some cases, biodegradable alternatives might be a more sustainable option, especially for single-use applications.
Conclusion
While both polypropylene (PP) and nylon are versatile plastics, their distinct properties make them ideal for different applications.
Polypropylene (PP) offers affordability, lighter weight, excellent chemical resistance, and a good moisture barrier. Nylon excels in superior durability, elasticity, higher heat resistance, and lower friction. Consider carefully when choosing your material.
Unionfab: Your Partner for Diverse Material Needs
Unionfab offers a comprehensive selection of materials, including but not limited to Nylon 12 Carbon-filled, SLS Nylon 11 (White) and Nylon 66.
At Unionfab find the perfect material for your project, from cost-effective plastics to high-performance metals and resins.
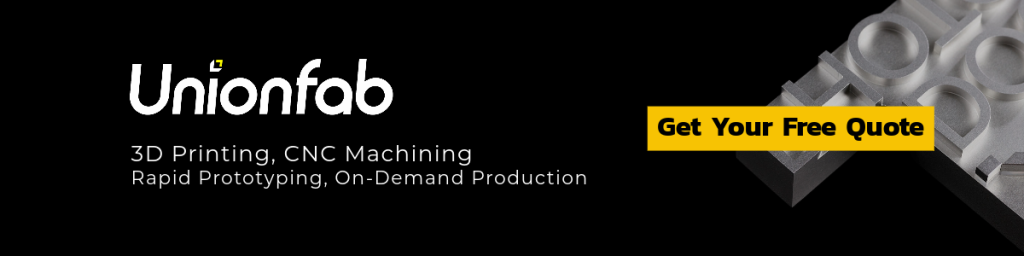