Is Nylon Heat Resistant? [+ Comparisons & Applications Explained]
![Is Nylon Heat Resistant? [+ Comparisons & Applications Explained]](https://ufc-dtc-cms.oss-accelerate.aliyuncs.com/blog/20240420/203945_92ee0qhe1.png)
Discover how heat-resistant nylon really is. Explore its thermal limits, compare it with other materials, and learn when to choose nylon for high-temperature applications.
Introduction
Whether you're designing automotive components that sit near hot engines or engineering industrial parts that must endure constant friction, understanding nylon’s heat resistance is crucial. Known for its versatility, nylon is widely used across industries—but how does it perform under heat?
This article takes a closer look at nylon’s thermal properties, including:
The key factors that affect its heat resistance
How different types of nylon behave under high temperatures
Comparisons with other common thermoplastics like ABS and PETG
Real-world applications where heat-resistant nylon excels
Whether you’re an engineer, product designer, or materials specialist, this guide will help you make informed decisions when selecting materials for heat-critical environments.
Understanding Nylon: Types, Properties & Industrial Relevance
Nylon is a member of the polyamide family—synthetic polymers celebrated for their toughness, flexibility, and resilience. This combination of properties makes nylon highly valuable across industries ranging from textiles and automotive to consumer goods and food packaging.
Among all its advantages, heat resistance is one of nylon’s standout traits.
But not all nylons are created equal. Different grades like Nylon 6, Nylon 66, Nylon 11, and Nylon 12 exhibit varying thermal and mechanical properties, influencing their suitability for specific applications.
Where Is Nylon Used?
Thanks to its strength and temperature endurance, nylon is widely used in:
Automotive under-the-hood parts
Electrical insulation
Industrial gears and bushings
Food-grade films and packaging
3D printing, especially in Selective Laser Sintering (SLS), for durable functional prototypes and low-volume production
Composition & Heat Resistance: What Makes Nylon Thermally Stable?
The heat resistance of nylon primarily stems from its molecular structure and semi-crystalline composition, which allows it to maintain integrity under elevated temperatures.
Key Thermal Properties
High Melting Point: Most common nylons melt around 220°C (428°F), much higher than many standard thermoplastics.
Semi-Crystalline Structure: The ordered regions within nylon’s molecular matrix increase rigidity, reducing deformation when exposed to heat.
Factors That Affect Nylon's Heat Resistance
While nylon's baseline thermal properties are impressive, several external factors can enhance or diminish its heat performance:
Factor | Effect on Heat Resistance | Example |
---|---|---|
Nylon Type | Alters melting point and HDT (Heat Deflection Temperature) | Nylon 66 > Nylon 6 in thermal endurance |
Additives | Reduce degradation at high temps | Heat stabilizers for long-term exposure |
Reinforcements | Improve stiffness and HDT | Glass fiber-filled Nylon 12 for structural parts |
Tip: When selecting nylon for high-temp environments, check both its HDT and whether it's reinforced or stabilized for thermal applications.
Nylon’s Mechanical Properties at Elevated Temperatures
While nylon’s heat resistance is impressive, thermal exposure does impact its mechanical behavior. The key is understanding how performance shifts with temperature changes:
Property | Effect of Heat | Explanation |
---|---|---|
Strength | Slight increase at moderate heat → Decreases with high heat | Molecular bonds become more flexible, then unstable |
Flexibility | Increases | Chain mobility rises, making nylon more pliable |
Durability | Decreases over time | Long-term heat weakens structure, increases brittleness |
Note: Nylon may feel stronger and more flexible in warm environments initially, but prolonged exposure can compromise performance, especially under load or stress.
Why Nylon Handles Heat So Well: The Science Behind Its Thermal Stability
Nylon’s reputation for excellent heat resistance stems from both its chemical bonding and semi-crystalline structure. These features work in tandem to maintain strength and shape under heat:
Strong Amide Bonds:
The robust molecular bonds in nylon chains require high energy to break, allowing the material to maintain integrity at elevated temperatures.Semi-Crystalline Morphology:
The crystalline zones in nylon add rigidity and reduce deformation—critical for components exposed to mechanical and thermal stress.High Melting Point:
With melting points typically around 220°C (428°F), nylon outperforms many other thermoplastics in thermal endurance.
In short, nylon's molecular backbone and structure are inherently designed to withstand the heat—making it a go-to material for demanding environments.
For more details about Nylon material, download our free Nylon Datasheet Bundle to compare top materials by property.
Key Factors That Influence Nylon's Heat Resistance
Although nylon is naturally heat-resistant, its real-world performance depends on various internal and external factors. Understanding these influences is essential for selecting the right grade for demanding environments.
Duration of Heat Exposure
Not all heat is equal—how long nylon is exposed to elevated temperatures can drastically affect its performance:
Continuous Use Temperature:
This is the maximum temperature at which nylon can operate reliably over time. For example, Nylon 66 typically maintains performance between 120–150°C under continuous load. Beyond this range, mechanical and structural degradation can occur.Short-Term Peaks:
Nylon can handle temperatures above its continuous use limit for short durations (e.g., during brief heating cycles), but frequent exposure can accumulate damage.
Tip: When in doubt, check both continuous use temperature and HDT (Heat Deflection Temperature) in material datasheets.
Additives & Reinforcements
Nylon formulations can be modified to withstand even higher temperatures:
Enhancer | Effect | Example Application |
---|---|---|
Heat Stabilizers | Reduce polymer chain degradation at high temps | Electrical insulators, engine parts |
Glass Fibers | Increase stiffness, load-bearing strength, and thermal stability | Gear wheels, structural brackets |
Mineral Fillers | Improve dimensional stability under heat | Automotive connectors |
Environmental & Processing Influences
Beyond additives and base polymer type, external conditions and processing methods also impact heat resistance:
Environmental Exposure:
UV radiation and moisture can accelerate degradation at high temperatures.
Chemical interactions (e.g., with oils, fuels) may reduce thermal performance.
Processing Conditions:
Improper cooling or uneven crystallinity during molding can lower heat tolerance.
Optimized processing (e.g., slow cooling for higher crystallinity) can enhance final thermal stability.
Summary Table: What Affects Nylon’s Heat Resistance?
Factor | Impact | Remarks |
---|---|---|
Heat Duration | Affects performance lifespan | Nylon 66: 120–150°C continuous |
Additives & Fillers | Boost stiffness & thermal endurance | Glass-filled nylons offer higher HDT |
UV / Moisture / Chemicals | Can accelerate heat-related degradation | Especially in outdoor or exposed uses |
Processing Conditions | Influence crystallinity and performance | Proper cooling improves structure |
Real-World Applications of Nylon in High-Temperature Environments
Nylon’s thermal durability, dimensional stability, and resistance to wear make it a top choice for components exposed to sustained or cyclical heat. Here’s a breakdown by industry:
Automotive Industry
Nylon is widely used in under-the-hood components, where temperature fluctuations and mechanical stress are the norm.
Component | Typical Nylon Type | Temperature Resistance |
---|---|---|
Engine Fan Shrouds | Glass-Filled Nylon 66 | Up to 150°C continuous |
Intake Manifolds | Heat-Stabilized Nylon 66 | 140–160°C |
Valve Covers, Clips | Nylon 6 + Additives | 120–140°C |
Why it works: Nylon maintains dimensional accuracy and wear resistance, even with engine heat and vibrations.
Electrical & Electronics
Nylon's combination of dielectric properties and heat resistance makes it suitable for:
Wire and Cable Insulation: Nylon 12 and Nylon 11 are often used for flexible, heat-tolerant coatings.
Electrical Connectors: High-temperature Nylon 66 resists soldering heat and deformation.
Pro Tip: Choose halogen-free, flame-retardant nylon for safety-critical connectors in electronics.
Food & Consumer Products
In applications involving contact with heat, food, or both, nylon offers a compliant and reliable solution:
Use Case | Material Type | Notes |
---|---|---|
Food Conveyor Belts | Nylon 11 (FDA-compliant) | Withstands 100–120°C, high wear |
Bearings in Mixers | Nylon 6 with lubricants | Self-lubricating and thermally stable |
Ironing Board Covers | Heat-Resistant Nylon 6 | Resists melting and warping under hot irons |
Plumbing & Mechanical Components
Nylon’s chemical resistance + moderate thermal performance makes it ideal for:
Washers, Gaskets (Hot Water Use): Nylon 66 or Nylon 6/12 blends
Small Gears & Bearings: Glass-fiber Nylon 12 for enhanced strength and heat deflection
Final Tip: Match Material to Application
Not all nylons are equal—glass-filled, heat-stabilized, or lubricated variations can drastically improve performance. Always consider:
Temperature exposure (continuous & peak)
Mechanical load
Moisture or chemical exposure
Looking to source high-heat nylon parts? Request a quote from Unionfab now.
How Does Nylon Compare with Other High-Temperature Materials?
While nylon doesn’t match metals or specialized thermosets in extreme heat tolerance, its balance of mechanical performance, weight, and cost makes it a compelling material for many mid-temperature engineering applications.
Let’s see how nylon stacks up:
Comparison Table: Nylon vs. Other Materials
Material | Heat Resistance | Advantages | Limitations |
---|---|---|---|
Metals | Very High ( >500°C) | Excellent strength, rigidity | Heavy, expensive, corrosion-prone |
Nylon | Good (120–150°C) | Lightweight, versatile, cost-effective | Lower temp resistance vs. metals |
Other Thermoplastics | Low (60–100°C) | Inexpensive, easy to mold | Poor heat tolerance, deforms easily |
Thermosets | High (150–250°C) | Excellent heat resistance | Brittle, non-recyclable |
Example: MJF-printed PA12 parts offer excellent mechanical durability and handle temperatures above 120°C, making them ideal for end-use parts in demanding environments.
Why Nylon Often Wins in Mid-Temp Use Cases
Heat Resistance: Stronger than most thermoplastics, and suitable for prolonged use around 120–150°C.
Lightweight Alternative to Metals: Offers structural strength at a fraction of the weight—ideal for mobility- and energy-sensitive applications.
Cost-Effective: Far more affordable than machined metals or high-grade thermosets, especially in low-volume or on-demand production.
Selecting the Right Nylon for High-Temperature Applications
Choosing the right type of nylon isn’t just about heat resistance—it’s about matching thermal, mechanical, and environmental demands to the correct material formulation. Here’s a step-by-step guide to ensure optimal performance:
Step 1: Understand the Thermal Requirements
Start by defining the operating environment:
Continuous Use Temperature:
What’s the maximum temperature the part must withstand over time? Nylon 66, for example, is often suitable up to 150°C.Peak Exposure:
Will there be occasional thermal spikes? Can the nylon tolerate short-term stress without deformation?
Tip: If your application involves cyclic heat loads (e.g., engine startup/shutdown), choose heat-stabilized nylon grades.
Step 2: Consult Technical Data Sheets
Material datasheets offer critical insights into thermal limits and other specifications. Key metrics to evaluate:
Heat Deflection Temperature (HDT): Indicates how well the nylon holds shape under load at high temperatures.
Melting Point: Common nylons melt between 215–265°C, depending on type and formulation.
Step 3: Consider Additional Performance Needs
Beyond heat, think long-term functionality:
Mechanical Strength: Will the part endure heavy loads or impact?
Chemical Exposure: Is it used in oily, acidic, or solvent-rich environments?
Wear Resistance: Is friction a concern (e.g., sliding parts or gears)?
Solution: For applications involving all three, glass-filled Nylon 66 or PA12 with lubricants may offer the best blend of performance.
Step 4: Factor in Environmental Conditions
Conditions like UV light, humidity, and chemical exposure can accelerate degradation—even at moderate temperatures. For outdoor or harsh environments, consider UV-stabilized, moisture-resistant nylon blends.
Conclusion
Nylon’s heat resistance, combined with its light weight and versatility, makes it one of the most capable thermoplastics for demanding environments. But the key to success lies in choosing the right grade—backed by application data and expert insight.
Discover Broad Nylon Selection at Unionfab
Unionfab provides a variety of nylon products, such as SLS Nylon 11, SLS Nylon 12 white, and glass-filled Nylon 12 off-white. These materials are suitable for designs requiring rigidity, allowing you to choose the best solution for each step. It is worth noting that our SLS Nylon 12 demonstrates excellent heat resistance.
Whether you opt for 3D printing or traditional manufacturing techniques like CNC machining or vacuum casting, Unionfab seamlessly integrates your chosen material into the production process.
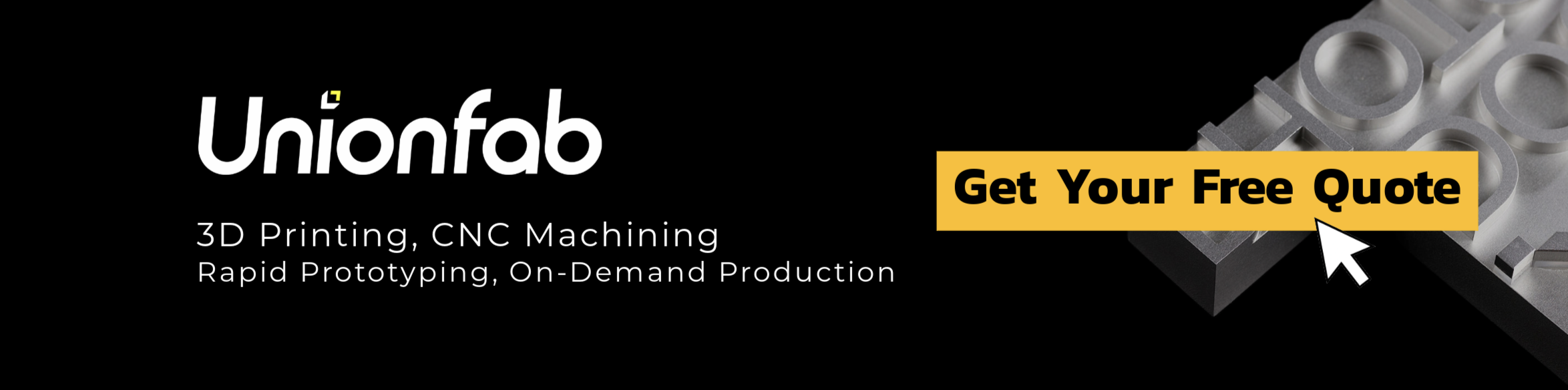