4130 vs 4140 Steel - Understanding the Differences
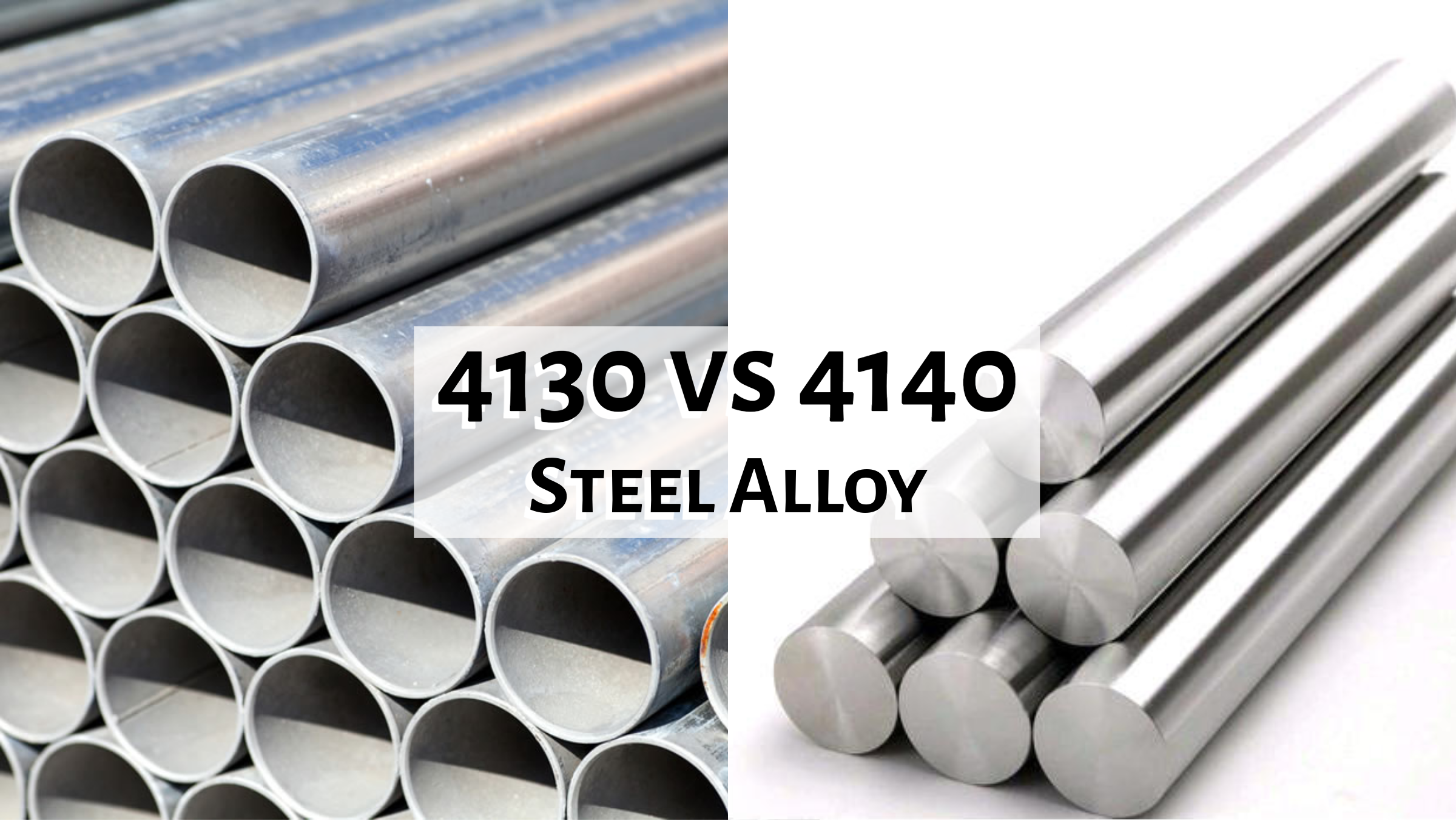
Discover the disparities between 4130 and 4140 steel alloys to learn their unique properties, applications, and performance in various industrial settings.
Introduction
To modify steel's properties for specific applications, various elements are added in small quantities. These elements, like carbon (C), chromium (Cr), and molybdenum (Mo), significantly influence the final characteristics of the steel:
Carbon (C): Increases strength and hardness but reduces ductility (bendability).
Chromium (Cr): Improves corrosion resistance and hardenability.
Molybdenum (Mo): Enhances high-temperature strength.
4130 and 4140 are two popular types of chromium-molybdenum (Chromoly) steel widely used in various industries. By understanding the distinctions between 4130 and 4140 steel, you can make informed decisions that contribute to a project's success.
4130 vs 4140: Composition
Composition of 4130 Steel
1. Alloying Elements:
4130 steel is a Chromoly steel, meaning its primary alloying elements are:
Chromium (Cr): Improves hardenability and corrosion resistance.
Molybdenum (Mo): Enhances high-temperature strength.
2. Chemical Makeup:
4130 steel is primarily composed of:
Iron (Fe): 97.03% - 98.22% (by weight) - The base metal.
Carbon (C): 0.28% - 0.33% - Provides strength and hardness, but to a lesser extent compared to 4140 steel.
Chromium (Cr): 0.8% - 1.1% - Enhances hardenability and corrosion resistance.
Molybdenum (Mo): 0.15% - 0.25% - Improves high-temperature strength.
Manganese (Mn): (Usually not listed but present) - Contributes to strength and hardenability.
Silicon (Si): (Usually not listed but present in small amounts) - Deoxidizer and aids in grain refinement.
Sulfur (S) and Phosphorus (P): (Present in very small amounts and undesirable) - Can negatively impact toughness and weldability if exceeding specified limits.
Composition of 4140 Steel
1. Alloying Elements:
Similar to 4130, 4140 steel is a Chromoly steel with the same key elements:
Chromium (Cr): Improves hardenability and corrosion resistance.
Molybdenum (Mo): Enhances high-temperature strength.
2. Chemical Composition:
The main difference between 4130 and 4140 lies in their carbon content:
Iron (Fe): 96.785% - 97.77% (by weight) - The base metal.
Carbon (C): 0.38% - 0.43% - Higher carbon content compared to 4130, leading to greater strength and hardness.
Chromium (Cr): 0.8% - 1.1% - Similar to 4130.
Molybdenum (Mo): 0.15% - 0.25% - Similar to 4130.
Manganese (Mn): (Usually not listed but present) - Contributes to strength and hardenability.
Silicon (Si): (Usually not listed but present in small amounts) - Deoxidizer and aids in grain refinement.
Sulfur (S) and Phosphorus (P): (Present in very small amounts and undesirable) - Can negatively impact toughness and weldability if exceeding specified limits.
The slight increase in carbon content (around 0.1%) in 4140 steel significantly impacts its mechanical properties compared to 4130 steel.
4130 vs 4140: Mechanical Properties
Strength Characteristics of 4130 Steel
1. Tensile Strength:
4130 steel exhibits moderate tensile strength, typically ranging from 560 MPa (81,000 psi) to 725 MPa (105,000 psi) depending on its heat treatment condition. Tensile strength represents the maximum stress a material can withstand before pulling apart.
2. Yield Strength:
The yield strength of 4130 steel is around 460 MPa (67,000 psi). Yield strength indicates the stress level at which the material begins to deform plastically (permanently).
3. Impact Resistance:
4130 steel offers good impact resistance, making it suitable for applications that experience shock loads. This toughness allows the material to absorb energy without fracturing.
Strength Characteristics of 4140 Steel
1. Tensile Strength:
4140 steel boasts a higher tensile strength compared to 4130. It typically ranges from 655 MPa (95,000 psi) to 979 MPa (142,000 psi) depending on the heat treatment. This higher carbon content translates to a stronger and harder material.
2. Yield Strength:
The yield strength of 4140 steel is also higher than 4130, typically around 415 MPa (60,000 psi). This indicates a greater resistance to permanent deformation under stress.
3. Impact Resistance:
While 4140 steel offers decent impact resistance, it's generally slightly lower than 4130 due to its higher carbon content. This trade-off means it may be less suitable for applications requiring exceptional shock absorption.
Key takeaway: 4130 steel provides a good balance of strength and toughness, while 4140 prioritizes higher strength at the expense of some impact resistance.
4130 vs 4140: Heat Treatment and Hardenability
Both 4130 and 4140 steels can be heat treated to achieve desired mechanical properties. Heat treatment involves controlled heating, holding, and cooling to modify the microstructure of the steel, influencing its strength, hardness, and ductility.
Heat Treatment Process for 4130 Steel
1. Annealing:
Purpose: Softens the steel for easier machining or shaping.
Process: Heat the steel to a specific temperature (typically around 815°C - 870°C or 1500°F - 1600°F) for a certain time, then slowly cool it in the furnace. This allows the microstructure to become uniform and relieves internal stresses.
2. Quenching and Tempering:
Purpose: Increases the steel's hardness and strength.
Process:
Austenitizing: Heat the steel to a higher temperature (around 845°C - 870°C or 1550°F - 1600°F) than for annealing. This transforms the microstructure into a single-phase structure called austenite.
Quenching: Rapidly cool the steel by submerging it in oil or water. This rapid cooling traps the high-temperature austenite phase within the steel, resulting in a harder but more brittle martensite structure.
Tempering: Reheat the quenched steel to a lower temperature (typically between 200°C - 650°C or 400°F - 1200°F) and hold it for a specific time, then air cool. This reduces brittleness and improves toughness while maintaining some of the increased hardness from quenching. The tempering temperature determines the final balance between strength, toughness, and ductility.
Heat Treatment Process for 4140 Steel
The heat treatment process for 4140 steel is very similar to 4130 steel due to their comparable compositions. Here's a breakdown:
1. Annealing:
The process and purpose are identical to 4130 steel.
2. Quenching and Tempering:
The process follows the same steps as 4130 steel: austenitizing, quenching, and tempering.
Important Note: Due to the slightly higher carbon content in 4140 steel, the austenitizing temperature might be slightly adjusted to achieve optimal results. It's crucial to consult heat treatment charts or consult a professional metallurgist for precise temperature specifications for your specific application.
4130 vs 4140: Applications and Industries
4130 steel excels in applications requiring a balance of strength, toughness, and weldability. 4140 steel prioritizes maximum strength for applications with high load-bearing demands.
Common Applications of 4130 Steel
4130 steel's good balance of strength, toughness, and weldability makes it a popular choice across various industries:
1. Aerospace:
Aircraft Fuselage Components: 4130 steel tubing is used for lightweight yet robust fuselage structures due to its strength-to-weight ratio.
Landing Gear: Its ability to withstand high stresses and impact loads makes it suitable for landing gear components.
Engine Mounts: The combination of strength and weldability allows for the fabrication of reliable engine mounts.
⠀2. Automotive:
Roll Cages: In race cars, 4130 steel roll cages offer superior protection in the event of a rollover.
Suspension Components: Control arms and other suspension parts benefit from 4130 steel's strength and ability to handle dynamic loads.
High-Performance Drivetrain Parts: Some high-performance axles and drive shafts utilize 4130 steel for its strength and fatigue resistance.
⠀3. Bicycle Frames:
High-End Mountain Bike Frames: 4130 steel offers a good balance of strength, weight, and ride quality for high-performance mountain bikes.
Custom Frames: Due to its weldability, it's a preferred material for custom bike frame builders.
Common Applications of 4140 Steel
4140 steel prioritizes high strength over toughness, making it ideal for applications demanding maximum load-bearing capacity:
1. Machinery Components:
Gears: The high strength of 4140 steel ensures gears can handle significant torque and resist wear.
Connecting Rods: In internal combustion engines, connecting rods experience high tensile and compressive forces, making 4140 steel a suitable choice.
Heavy Machinery Parts: Components in construction equipment, mining machinery, and other heavy-duty applications often utilize 4140 steel for its exceptional strength.
⠀2. Shafts and Axles:
Drive Shafts: The ability to transmit high torque makes 4140 steel a popular choice for drive shafts in various applications.
Axles: Axles in vehicles and heavy machinery rely on 4140 steel's strength to support weight and handle dynamic loads.
⠀3. Tooling and Dies:
Cold Work Tooling: For tools used in cold-working operations like stamping or punching, 4140 steel offers the necessary strength and wear resistance.
Certain Dies: While not ideal for all types of dies, 4140 steel can be used in specific die applications where high strength is crucial.
4130 vs 4140: Machinability and Weldability
Machinability of 4130 vs 4140
The key difference in machinability between 4130 and 4140 steel lies in their carbon content:
4130 Steel: With a lower carbon content (around 0.3%), 4130 steel is considered more machinable. It offers less resistance to cutting tools, resulting in cleaner cuts, longer tool life, and less chip formation. This makes it a preferred choice for complex machining operations.
4140 Steel: The higher carbon content (around 0.4%) in 4140 steel makes it less machinable compared to 4130. It can cause increased tool wear, require slower cutting speeds, and generate more chips during machining. However, it's still machinable with proper techniques and tooling selection.
Some additional factors to consider:
Heat Treatment: The hardness of the steel also affects machinability. Annealed steels of both types are easier to machine compared to their hardened counterparts.
Machining Techniques: Using appropriate cutting tools, coolants, and machining parameters can significantly improve the machinability of both steels.
Weldability of 4130 vs 4140
Welding Processes:
Both 4130 and 4140 steels are considered weldable, although 4130 offers some advantages:
Common Welding Processes: Both steels can be welded using various processes like Gas Tungsten Arc Welding (GTAW) or Shielded Metal Arc Welding (SMAW).
4130 Steel: Generally considered to have better weldability due to its lower carbon content. It experiences less weld hardening and reduces the risk of cracking around the weld zone.
4140 Steel: While weldable, 4140 steel requires stricter procedures to minimize weld cracking. Preheating and post-weld heat treatment might be necessary depending on the specific application and weld thickness.
Precautions and Challenges:
Here are some key points to remember when welding both steels:
Preheating: Preheating the steel before welding helps reduce the risk of cracking, especially for 4140 steel.
Interpass Temperature Control: Maintaining proper temperature between weld passes is crucial to avoid excessive heat buildup and potential cracking.
Post-Weld Heat Treatment: Depending on the application and thickness, post-weld heat treatment might be necessary to relieve residual stresses and improve weld toughness, particularly for 4140 steel.
Filler Metal Selection: Choosing the appropriate filler metal that matches the base metal composition is essential for optimal weld strength and performance.
Conclusion: 4130 steel offers superior machinability and weldability compared to 4140 steel. However, with proper techniques and precautions, both steels can be successfully machined and welded for various applications.
4130 vs 4140: Cost Considerations
Price Comparison Between 4130 and 4140 Steel
While the exact cost can vary depending on factors like quantity, supplier, and market fluctuations, generally:
4130 steel is slightly less expensive than 4140 steel.
The price difference is typically within 5%.
Factors Influencing Cost Differentials
The slight cost difference between 4130 and 4140 steel can be attributed to a few factors:
Raw Material Cost: The higher carbon content in 4140 steel might lead to a marginally higher cost for the raw alloying elements.
Manufacturing Processes: While both steels undergo similar processing, 4140 steel might require slightly more precise control during heat treatment due to its higher carbon content, potentially impacting cost.
It's important to note that the cost difference is often negligible compared to other factors like material selection's impact on performance and overall project success.
Future Prospects in Steel Alloy Technology
Steel alloy development is constantly evolving. Here are some potential future trends:
Development of High-Strength, Low-Alloy (HSLA) Steels: These steels aim to achieve high strength while maintaining good toughness and weldability, potentially offering alternatives to traditional Chromoly steels like 4130 and 4140.
Advanced Microalloying: Adding small quantities of specific elements can significantly enhance steel properties, leading to lighter and stronger materials for various applications.
Additive Manufacturing with Steel Alloys: The use of 3D printing technologies to create complex shapes with steel alloys might revolutionize manufacturing in the future.
Conclusion
Recap of Key Differences Between 4130 and 4140 Steel:
Feature | 4130 Steel | 4140 Steel |
---|---|---|
Carbon Content | Lower (0.28% - 0.33%) | Higher (0.38% - 0.43%) |
Strength | Moderate | Higher |
Toughness | Good | Slightly Lower |
Machinability | More machinable | Less machinable |
Weldability | Better | Good (requires stricter procedures) |
Cost | Slightly less expensive | Slightly more expensive |
Choosing between 4130 and 4140 steel depends on your project's specific needs:
Prioritize Strength: If maximum strength is crucial, 4140 steel is the better option for applications like gears, shafts, or heavy machinery components.
Balance Strength and Other Properties: When a good balance of strength, toughness, machinability, and weldability is required, 4130 steel is a more versatile choice. It's suitable for applications like aircraft structures, suspension components, or bicycle frames.
Cost Considerations: While the cost difference is minimal, if budget is a significant concern and your application can function well with 4130 steel's properties, it might be the more economical option.
By understanding the key differences between 4130 and 4140 steel, you can make informed decisions to select the most suitable material for your project needs.
Experience the Difference with Unionfab
With Unionfab's extensive material selection and expert support, you can unlock a universe of possibilities in 3D printing and on-demand manufacturing.
Contact us today to explore how we can transform your designs into reality.
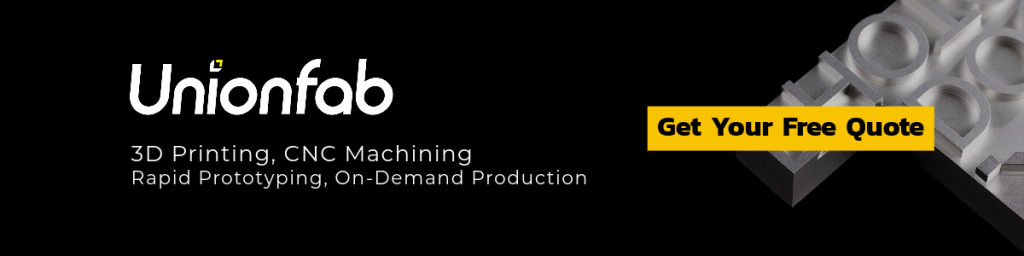