Titanium 3D Printing: A Complete Guide [+ Free Cost Calculator]
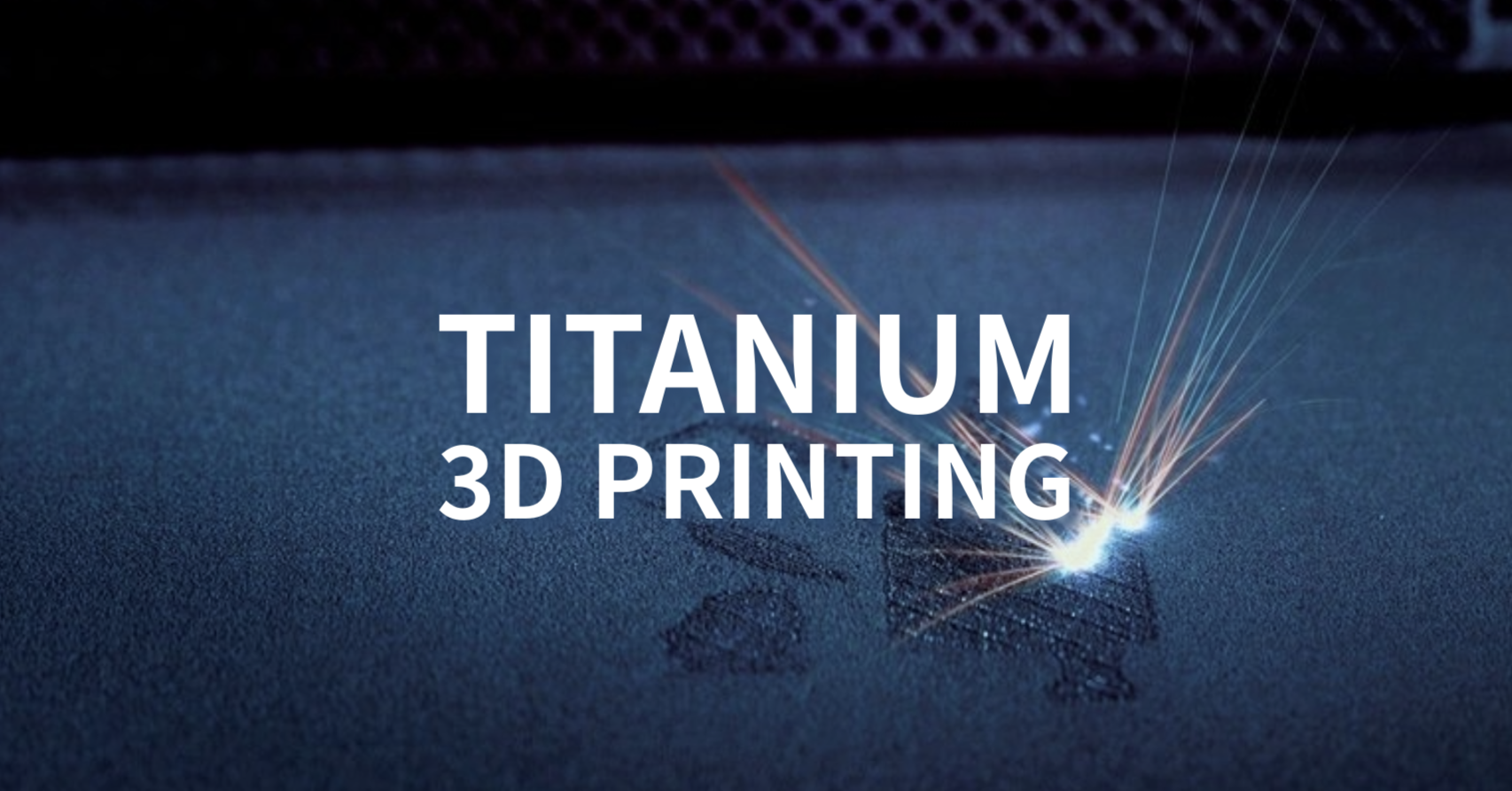
Discover everything about Titanium 3D Printing. Learn why Titanium is the go-to material for lightweight, high-strength parts. Get a tailored estimate with Unionfab’s free cost calculator!
Overview
Titanium has long been celebrated for its unique combination of lightness, strength, and biocompatibility, making it a go-to material for high-performance applications.
Unlike traditional machining methods, which often result in material waste and higher costs, titanium 3D printing offers a more efficient and cost-effective solution, making it a game-changer for industries at the cutting edge of innovation.
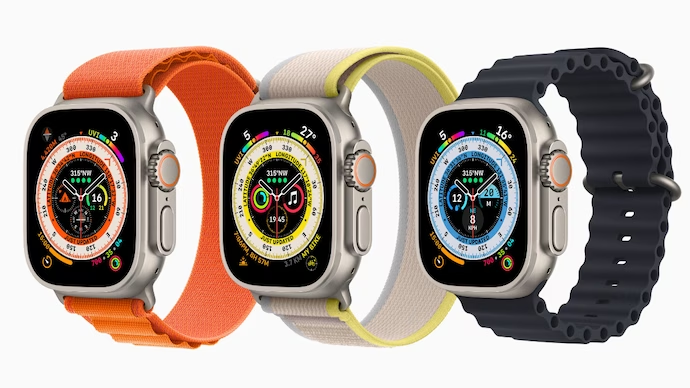
One of the most exciting developments in titanium 3D printing is its adoption by leading tech giants like Apple. The iPhone 15 Pro and Apple Watch Ultra both incorporate Grade 5 Titanium (Ti-6Al-4V)—the same high-strength alloy used in aviation and medical implants.
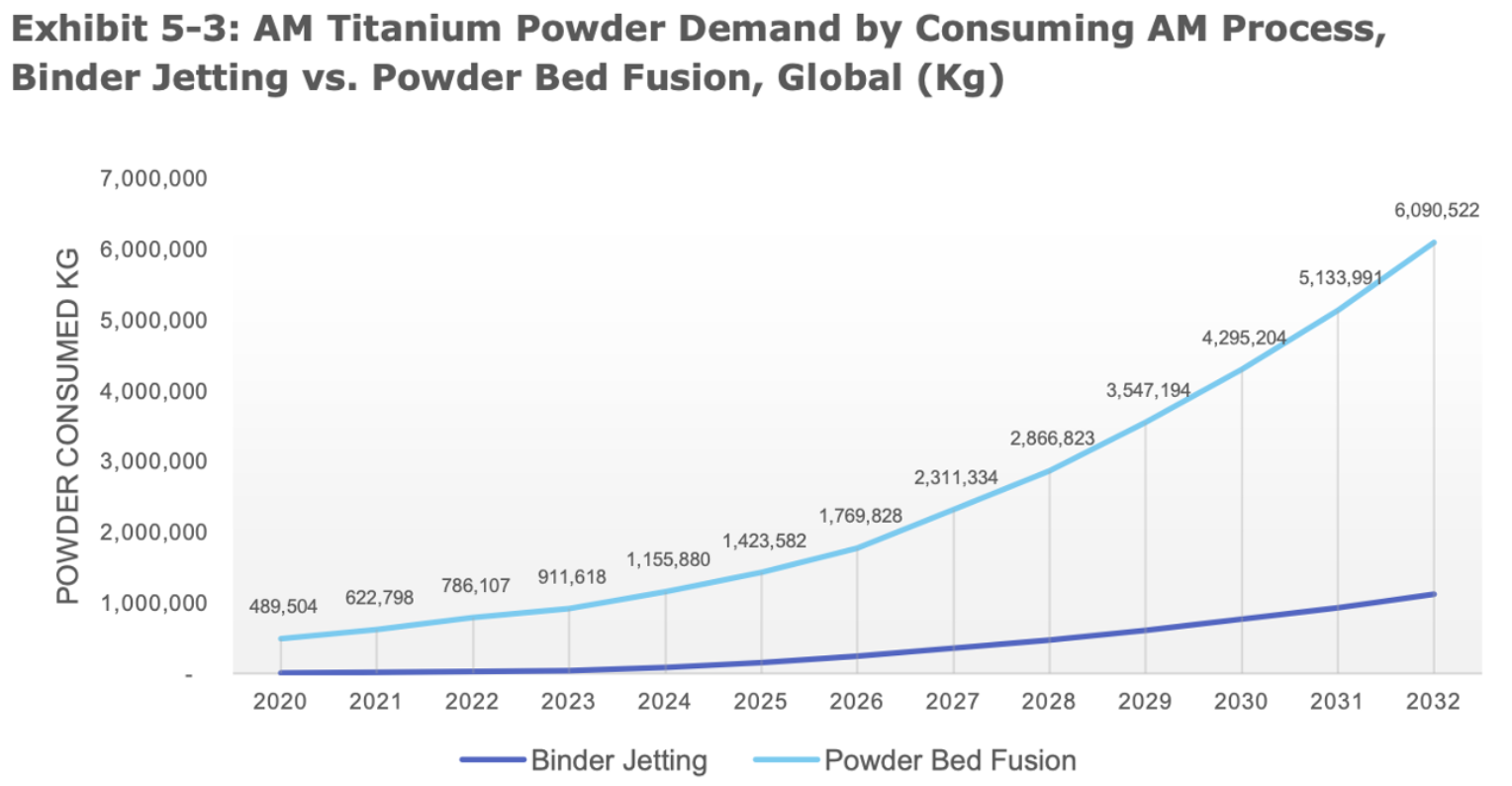
According to a report by Additive Manufacturing Research (AM Research), the titanium 3D printing market is projected to grow from $214 million in 2023 to a remarkable $1.4 billion by 2032. With 3D printing enabling more precise, cost-effective Titanium production, pushing the boundaries of design and performance.
Titanium for 3D Printing
Common Titanium Grades in 3D Printing
Material Grade | Composition | Key Features | Typical Applications |
---|---|---|---|
Ti6Al4V (Ti64, Grade 5) | 6% Aluminum, 4% Vanadium, 90% Titanium | High strength, corrosion-resistant, excellent fatigue resistance | Aerospace, medical implants, high-performance automotive parts |
Equivalent to Ti6Al4V | Equivalent to Ti6Al4V | Aerospace, medical, industrial applications | |
Ti6Al4V ELI (Grade 23) | Extra-low interstitial version of Ti64 | Superior biocompatibility, improved fracture toughness | Medical implants, dental prosthetics, surgical tools |
Commercially Pure Titanium (Grade 1-4) | 99%+ Titanium, small amounts of oxygen, iron, carbon | Increased ductility, corrosion resistance, lower strength than Ti64 | Chemical processing, marine applications, biomedical implants |
*TC4 is the same material as Ti6Al4V but follows Chinese GB/T standards.
Among the different grades of Titanium, Ti6Al4V (also known as TC4 in China) is the most commonly used in 3D printing. This alloy, made up of 6% aluminum and 4% vanadium, offers a superior balance of strength, weight, and corrosion resistance.
Properties of Titanium for 3D Printing
Titanium is a top-tier metal in additive manufacturing due to its exceptional strength-to-weight ratio, corrosion resistance, and biocompatibility.
Lightweight & High Strength-to-Weight Ratio
Compared to stainless steel, Titanium is significantly lighter and just as corrosion-resistant, better for weight-sensitive applications. Against aluminum, it offers greater strength and higher temperature resistance, though at a higher cost.
Corrosion Resistance
Titanium naturally forms a protective oxide layer, making it highly resistant to corrosion in harsh environments, including marine, aerospace, and medical applications.
Biocompatibility
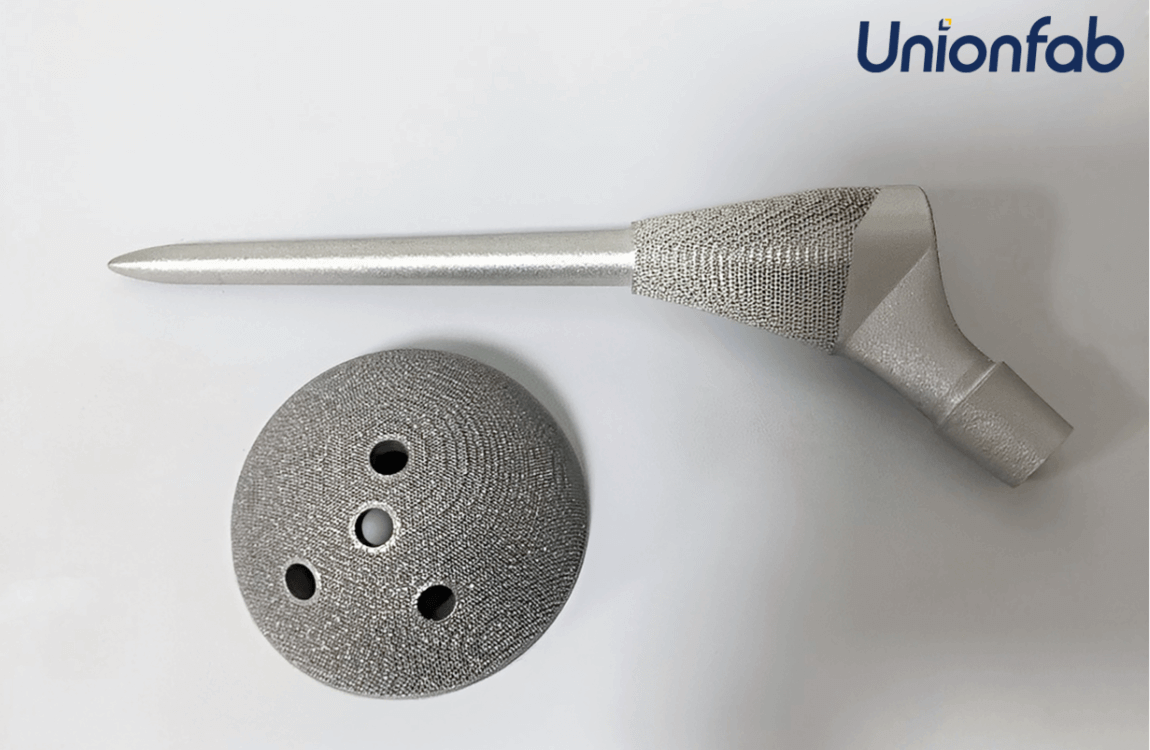
Source: Unionfab
As a non-toxic, non-allergenic metal, Titanium is widely used in medical implants, prosthetics, and surgical tools due to its excellent bone integration and long-term stability.
High-Temperature Resistance
Titanium retains its mechanical properties at elevated temperatures, making it ideal for jet engines, rocket components, and industrial applications where extreme heat is a factor.
Why is Titanium Ideal for 3D Printing?
Titanium is an excellent material for 3D printing, not just because of its physical properties, but also because traditional machining methods struggle with it.
In conventional manufacturing, Titanium is notoriously difficult to machine due to its hardness and tendency to wear down cutting tools quickly. It also has an extremely high Buy-to-Fly Ratio—a term used in aerospace to describe material waste. When machining a Titanium part from a solid billet, up to 90% of the raw material is lost as chips. This inefficiency drives up costs, making Titanium components expensive and time-consuming to produce.
Enter 3D printing, which solves these challenges in three key ways:
Material Efficiency – Additive manufacturing builds parts layer by layer, meaning only the necessary material is used. This drastically reduces waste and lowers costs.
Complex Geometries – 3D printing enables topology optimization, where software designs organic, lightweight structures that wouldn’t be possible with traditional machining. This is crucial in aerospace and medical applications.
No Tool Wear – Since Titanium 3D printing doesn’t involve cutting tools, manufacturers avoid costly tool replacements and downtime.
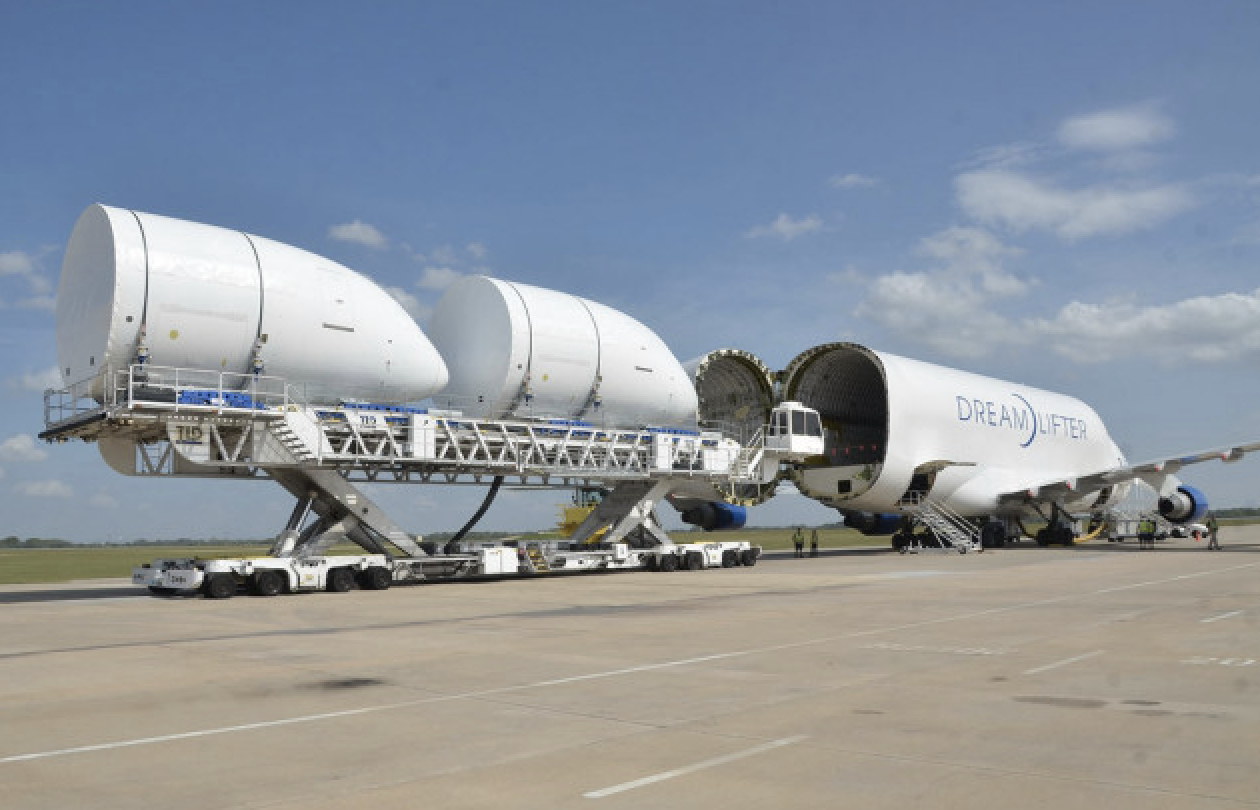
A perfect example is Boeing's collaboration with Norsk Titanium to incorporate 3D-printed titanium parts in the 787 Dreamliner. By replacing traditionally manufactured components with additively manufactured structural titanium parts, Boeing anticipates saving $2 million to $3 million per aircraft, thereby enhancing the 787's profitability.
Titanium 3D Printing Technologies
Key Titanium 3D Printing Technologies
Technology | How It Works | Titanium Compatibility | Advantages |
---|---|---|---|
Selective Laser Melting (SLM) / Direct Metal Laser Sintering (DMLS) | Uses a high-powered laser to melt and fuse fine titanium powder layer by layer | Ideal for Ti6Al4V, CP Titanium | High precision, excellent mechanical properties, widely used |
Electron Beam Melting (EBM) | Uses an electron beam in a vacuum to melt titanium powder | Works well with Ti6Al4V, Grade 23 (ELI) | Faster printing speeds, reduced residual stresses, ideal for large parts |
Direct Energy Deposition (DED) | A high-power laser or electron beam melts titanium wire or powder as it is deposited | Suitable for Titanium wire and powder-based materials | Great for repairs and large-scale components |
Deposits a binding agent onto layers of titanium powder, which is later sintered | Works with Titanium-based powders | Lower-cost process | |
Cold Spray | Accelerates titanium powder particles at supersonic speeds onto a surface to build up layers | titanium powder particles | Best for coatings, repairs, and component reinforcement |
Looking to harness the power of SLM or Metal Binder Jetting technologies?
At Unionfab, we specialize in creating high-quality titanium parts with cutting-edge 3D printing methods. Get in touch now to learn how our technology can benefit your business!
[View Real Customer Feedback on Trustpilot]
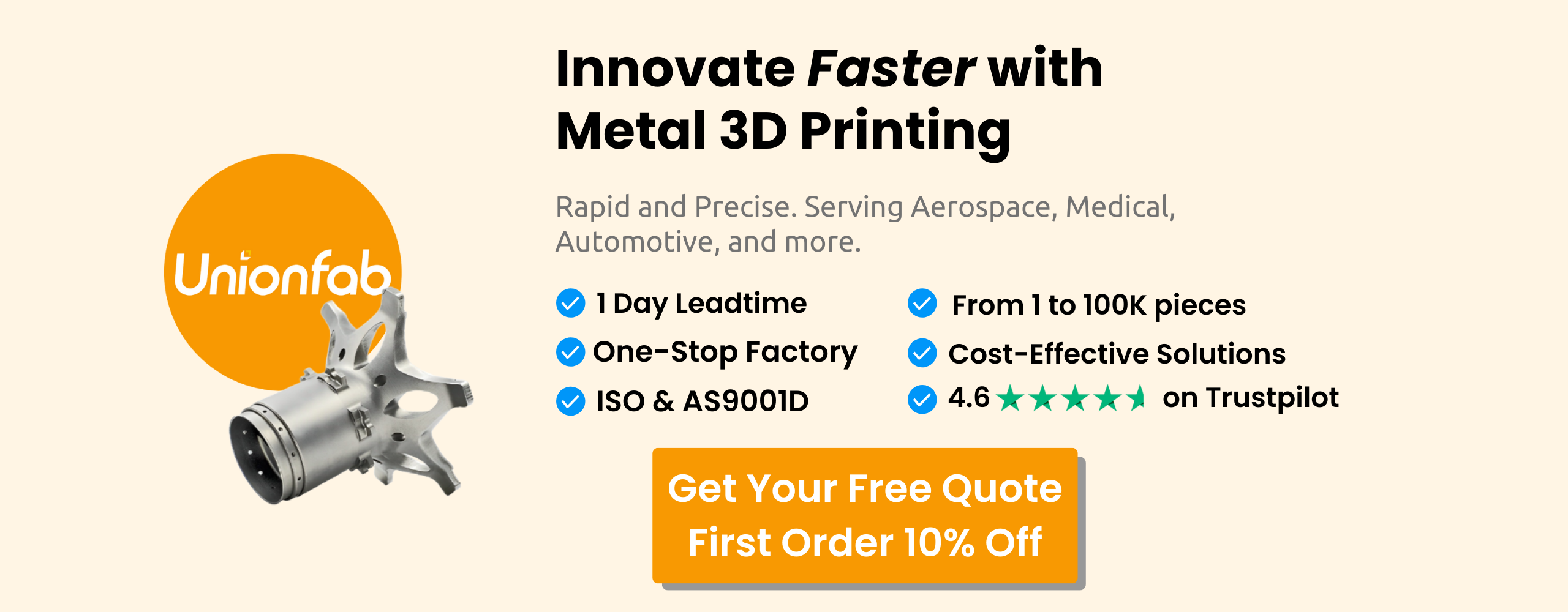
3D Printers Compatible with Titanium
Below is a comparison of some notable 3D printers capable of processing titanium:
3D Printer Model | Manufacturer | Printing Technology | Build Volume | Approximate Price | Notable Features |
---|---|---|---|---|---|
Markforged | Atomic Diffusion Additive Manufacturing (ADAM) | 300 x 220 x 180 mm | $99,500 – $200,000 | Lower operational costs. | |
EOS GmbH | Direct Metal Laser Sintering (DMLS) | 250 x 250 x 325 mm | $700,000 – $1,000,000 | High precision for aerospace and healthcare. | |
HP | Binder Jetting | 430 x 320 x 200 mm | ~$400,000 | High productivity for mass production. | |
SLM Solutions | Selective Laser Melting (SLM) | 500 x 280 x 365 mm | ~€,500,000 | Quad-laser system for increased productivity. | |
Renishaw | Laser Powder Bed Fusion (LPBF) | 250 x 250 x 350 mm | ~€250,000 | Quad-laser system for increased productivity. | |
SLM Solutions | Selective Laser Melting (SLM) | 280 x 280 x 365 mm | ~$250,000 | Dual-laser system for complex geometries. |
How Much Does 3D Printed Titanium Cost?
Titanium 3D printing is a premium technology, and its cost reflects that. The process is expensive due to several key factors:
Why Is It So Expensive?
Material Costs
Titanium powder, the feedstock for these processes, can cost several hundred dollars per kilogram, making it one of the pricier metal 3D printing materials.
High-End Equipment
The printers themselves, using DMLS or EBM, cost hundreds of thousands of dollars. Plus, they require controlled environments and precise energy sources, adding to operational costs.
Post-Processing Needs
Printing is just the start. Heat treatment, machining, and surface finishing are often required to achieve the desired mechanical properties and tolerances. These further increase the cost.
Considering titanium 3D printing for your project?
Unionfab’s free cost calculator helps you estimate the price of your titanium 3D print based on material, design, and quantity. Get a quick, tailored quote to see if titanium fits your budget!
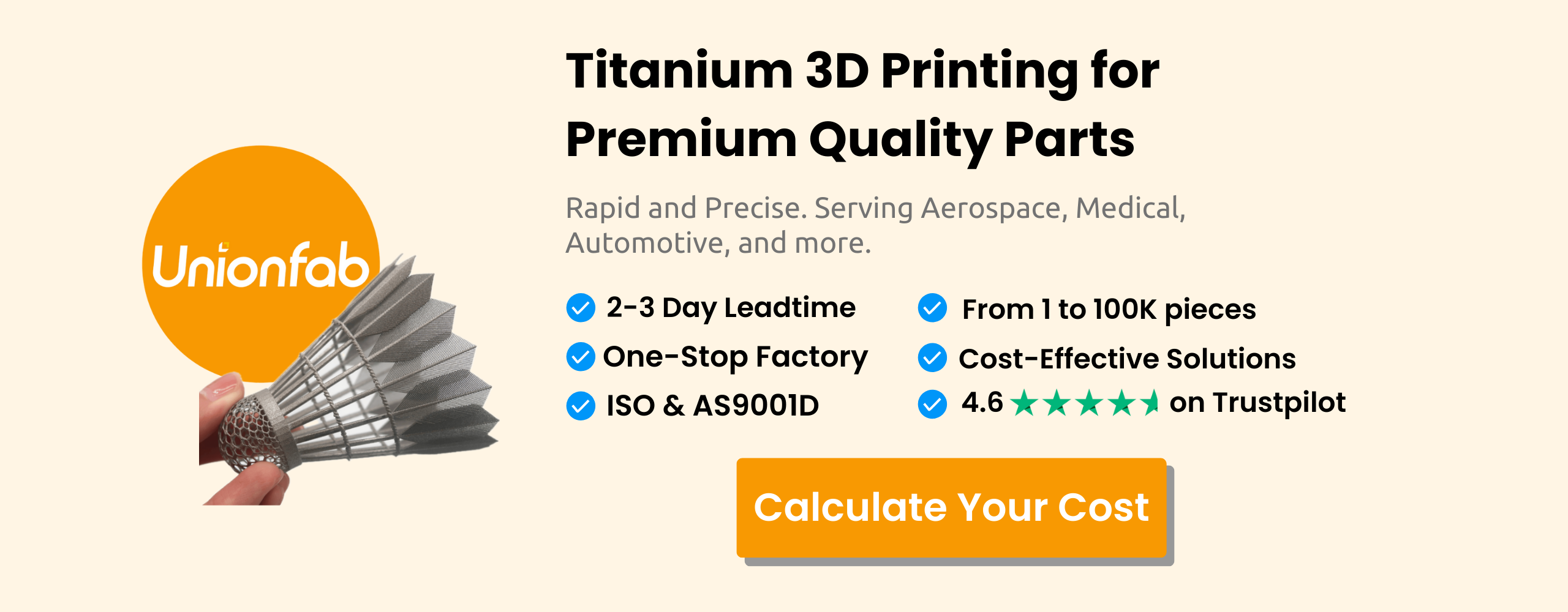
When Is Titanium 3D Printing the Best Choice?
Given its high costs, it’s important to evaluate if titanium 3D printing is the right fit for your needs. Below, we explore the ideal use cases for titanium 3D printing:
✅ Biocompatibility Is Essential
Titanium’s superior biocompatibility and corrosion resistance make it indispensable for custom medical implants.
3D printing enables precise, patient-specific designs that ensure optimal fit and performance in orthopedic and dental applications.
✅ High-Temperature Resistance Is Necessary
Titanium’s exceptional heat resistance makes it ideal for parts exposed to high temperatures, like turbine blades and rocket components.
3D printing further enhances its potential, enabling optimized geometries and cooling channels that boost efficiency and durability.
✅ Extreme Lightweighting Is a Goal
With its unparalleled strength-to-weight ratio, titanium is a game-changer in aerospace.
3D printing allows for the creation of intricate, lightweight structures that reduce fuel consumption and improve overall performance—something traditional methods can’t easily match.
✅ Premium, Sleek Consumer Products
Titanium's luxurious appearance and robustness make it perfect for high-end electronics and accessories. Its modern aesthetic is increasingly showcased in wearables and luxury devices, including the iPhone 15 Pro and Apple Watch Ultra.
Additionally, titanium's lightweight and strong properties are making it the material of choice for 3D printed bicycles. Some enthusiasts believe this innovative material could surpass carbon fiber in both performance and design. Join the hosts and discover the cutting-edge world of 3D-printed titanium in cycling with this exciting episode:
When to Consider Other Metals?
🚫 Budget Is a Concern
Titanium powder is expensive, and the printing process requires specialized equipment and post-processing. If cost efficiency is a priority, aluminum or stainless steel may provide sufficient performance at a lower price.
🚫 Extreme Lightweighting Is Not Required
If your application does not demand the highest strength-to-weight ratio, traditionally manufactured steel or titanium alloy castings might be a more economical and scalable choice.
Challenges of 3D Printing with Titanium
While 3D printing with titanium offers incredible advantages, it also comes with several challenges that need careful consideration:
Titanium Supply Chain & Pricing
Titanium powder is notoriously expensive, and its supply can be volatile. Fluctuating prices, limited suppliers, and complex procurement processes add to the financial burden.
For businesses, managing titanium’s supply chain and sourcing quality powder at a competitive price can be a significant challenge, especially for high-volume production.
Furthermore, high upfront and ongoing costs for specialized EBM/SLM machines and post-processing steps make titanium 3D printing impractical for smaller businesses.
Safe Handling
Titanium powder is highly flammable, making safety a major concern during 3D printing. To prevent fire hazards, printing must take place in an inert gas environment (such as argon or nitrogen).
This adds complexity, as specialized equipment is needed to maintain an oxygen-free atmosphere and meet strict safety protocols.
Case Study: Unionfab's 3D-Printed Titanium Alloy Badminton Shuttlecock
Using SLM 3D printing, Unionfab designed a titanium alloy badminton shuttlecock weighing only 10 grams—a feat made possible through advanced material properties and intricate design. Key features of the shuttlecock include:
Hexahedral Honeycomb Structure: The shuttlecock’s ball head features a hexahedral honeycomb structure, optimizing strength while maintaining an ultra-lightweight profile.
Precise Measurements:
Feather gap: 0.25mm
Single piece width: 0.45mm
Thickness: 0.17mm
Ball head wall thickness: 0.15mm
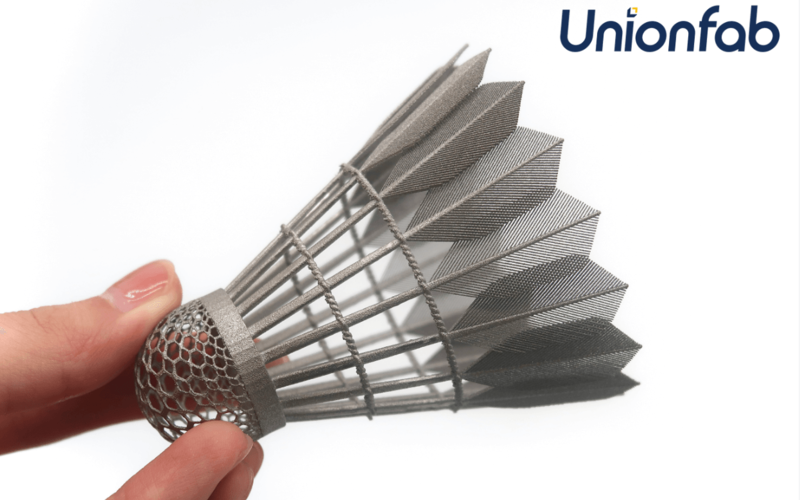
Post-Processing & Finishing of Titanium Parts
Raw 3D-printed titanium parts often come with a rough surface and require finishing to enhance appearance, durability, and performance.
At Unionfab, we offer advanced finishing solutions to enhance both the appearance and durability of the parts.
Zinc Plating ![]() | Tin Plating ![]() | Nickel Plating ![]() | Chrome Plating ![]() | Painting ![]() |
---|---|---|---|---|
Powder Coating ![]() | Sandblasting ![]() | Shot Peening ![]() | Polishing ![]() | Texture Finishing (VDI, SPI, MOLD Texture) ![]() |
Anodizing ![]() | Blueing ![]() | Brushing ![]() | Heat Treatment ![]() | Laser Engraving ![]() |
Need help with finishing your titanium parts for the best performance and appearance? Contact Unionfab for expert post-processing solutions tailored to your needs!
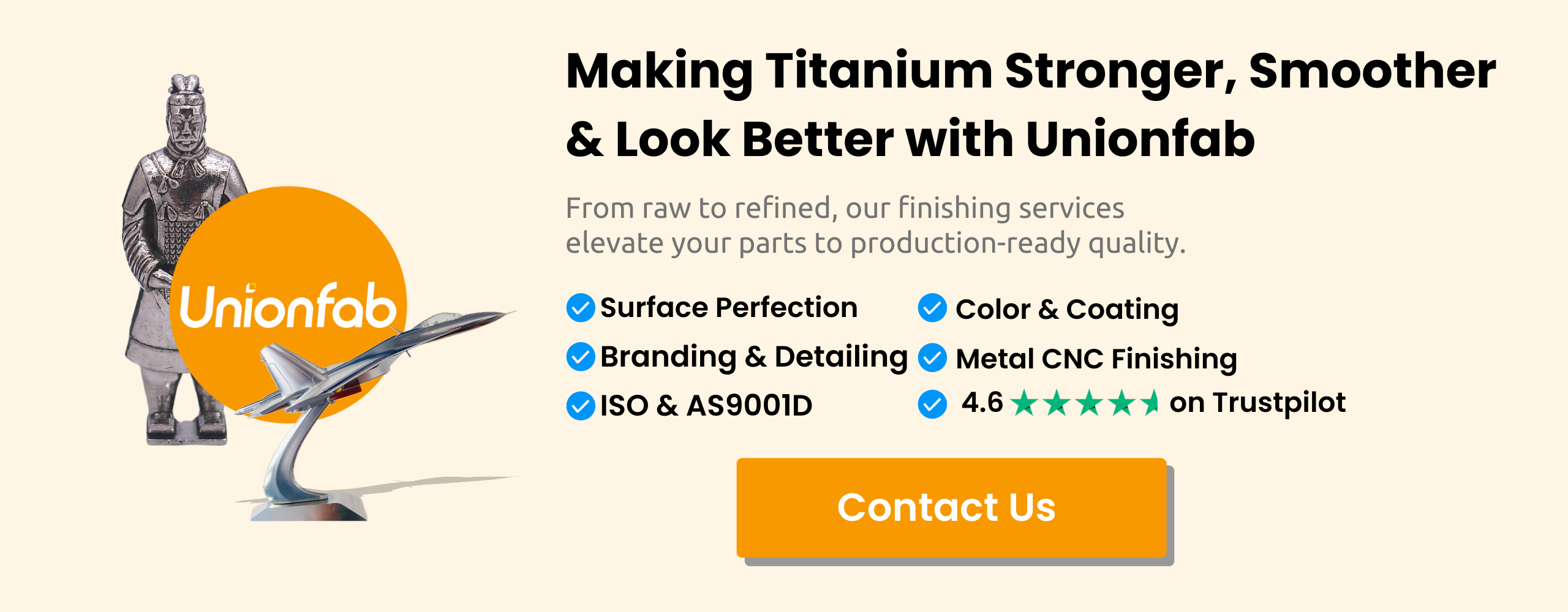
Unionfab: Expertise in Metal 3D Printing Technologies
Unionfab provides professional 3D printing services for electronics and other precision manufacturing industries. With extensive experience operating industrial-grade metal additive manufacturing equipment.
Capabilities for Low Volume Metal Parts Production
Our small-batch metal 3D printing services excel at producing low volumes of complex metal parts on demand.
From Design to Completion
Unionfab handles files from all major 3D model systems and delivers finished, post-processed parts. We provide affordable, expedited metal additive services to help product development teams capitalize on the untapped potential of metal 3D printing.