Mastering Precision: How CNC Precision Machining Works
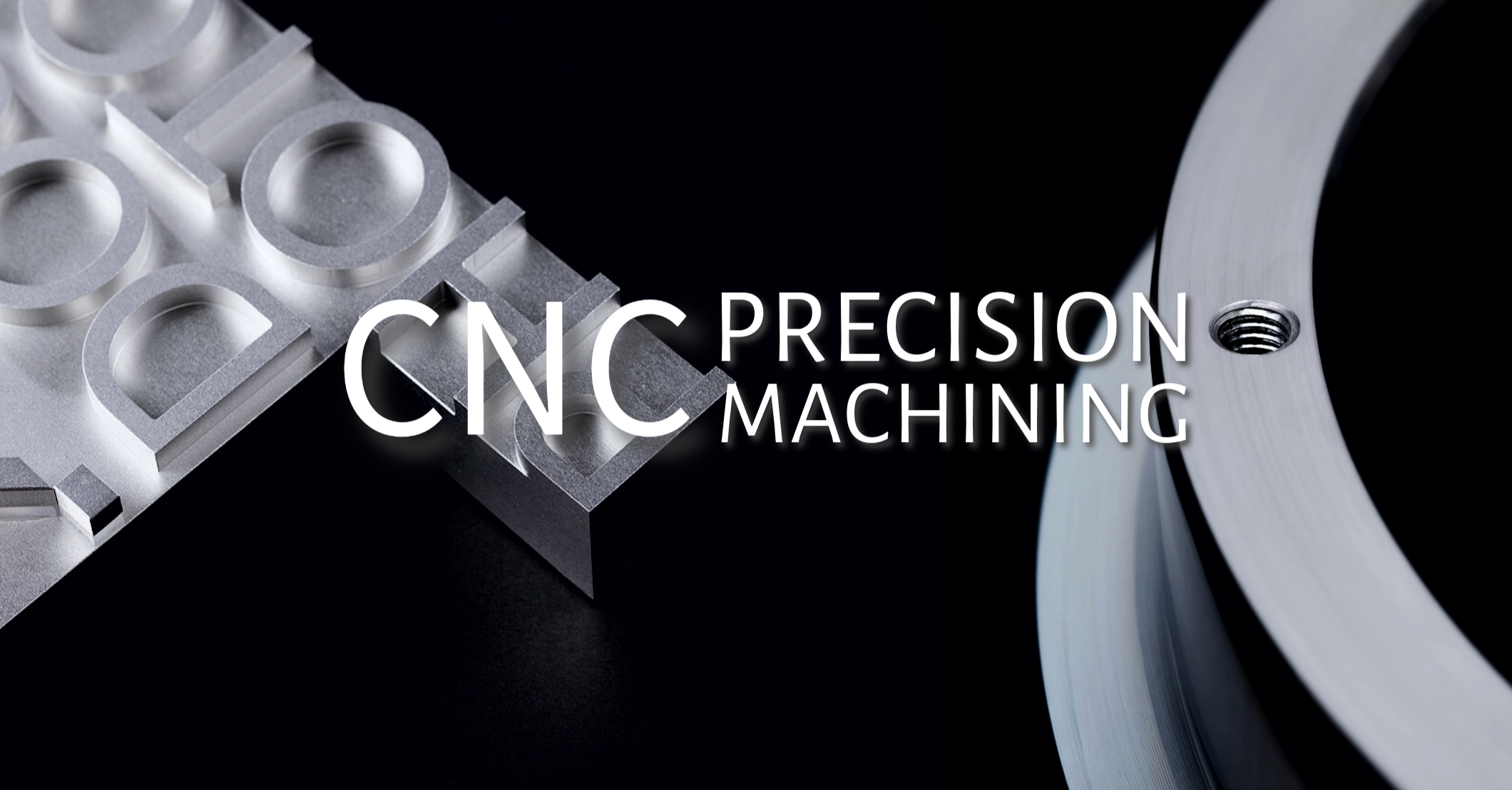
Delve into the intricacies of CNC precision machining, where computer-controlled precision meets raw materials to craft everything from intricate components to heavy-duty parts.
What is CNC Precision Machining?
CNC precision machining is a computer-controlled manufacturing process that focuses on the ability to consistently replicate specific attributes across a large production volume, ensuring that the dimensions and characteristics of multiple units closely match the targeted values. It is commonly used in industries requiring high levels of accuracy and consistency.
In CNC machining, precision is achieved through rigorous quality control processes, where machine shops and suppliers conduct inspections and measurements on a representative sample of produced parts to meet predefined quality standards and ensure that the components adhere to specified tolerances.
Tolerances and Quality Control
Tolerance Standards: ISO GPS and ASME Y14.5
Precise dimensional accuracy and tight tolerances are critical in CNC machining. Component function and assembly often rely on parts holding precise form and size within extremely narrow tolerance bands. As such, maintaining stringent tolerances is vital for quality control in CNC processes.

Industry and application standards offer tolerance guidelines, and compliance with these standards guarantees the interchangeability of manufactured components.
The ISO GPS (Geometrical Product Specification) system encompasses more than 100 standards, addressing dimensioning, tolerance specifications, gauging, inspection, and calibration, including but not limited to:
ISO 8015: Defines the fundamental concepts and rules of the GPS system.
ISO 1101: Contains geometrical symbol specifications and rules for drawing/part definition.
ISO 2768: Sets general geometric dimensioning and tolerancing standards. It has two parts - ISO 2768-1 for linear and angular dimensions without a stated tolerance, and ISO 2768-2 for toleranced geometrical features.
In contrast, ASME Y14.5 is a single standard focused only on drawings, requiring a separate document for verification.
Notably, the ISO GPS system involves higher costs due to multiple documents. The choice between these standards depends on factors like specific application needs, budget constraints, and training availability.
| Permissible deviations in mm | |||
Basic size range in mm | f | m | c | v |
0.5 up to 3 | ±0.05 | ±0.1 | ±0.2 | – |
over 3 up to 6 | ±0.05 | ±0.1 | ±0.3 | ±0.5 |
over 6 up to 30 | ±0.1 | ±0.2 | ±0.5 | ±1.0 |
over 30 up to 120 | ±0.15 | ±0.3 | ±0.8 | ±1.5 |
over 120 up to 400 | ±0.2 | ±0.5 | ±1.2 | ±2.5 |
over 400 up to 1000 | ±0.3 | ±0.8 | ±2.0 | ±4.0 |
over 1000 up to 2000 | ±0.5 | ±1.2 | ±3.0 | ±6.0 |
over 2000 up to 4000 | – | ±2.0 | ±4.0 | ±8.0 |
In Unionfab, we take pride in our commitment to precision and quality — we offer tolerances range from ±0.0002 ~ ±0.005 inches (0.005 ~ 0.127 mm).
We recognize that precision is not a one-size-fits-all concept, and by offering this range, we cater to the diverse needs of industries that rely on CNC precision machining to drive innovation and performance.
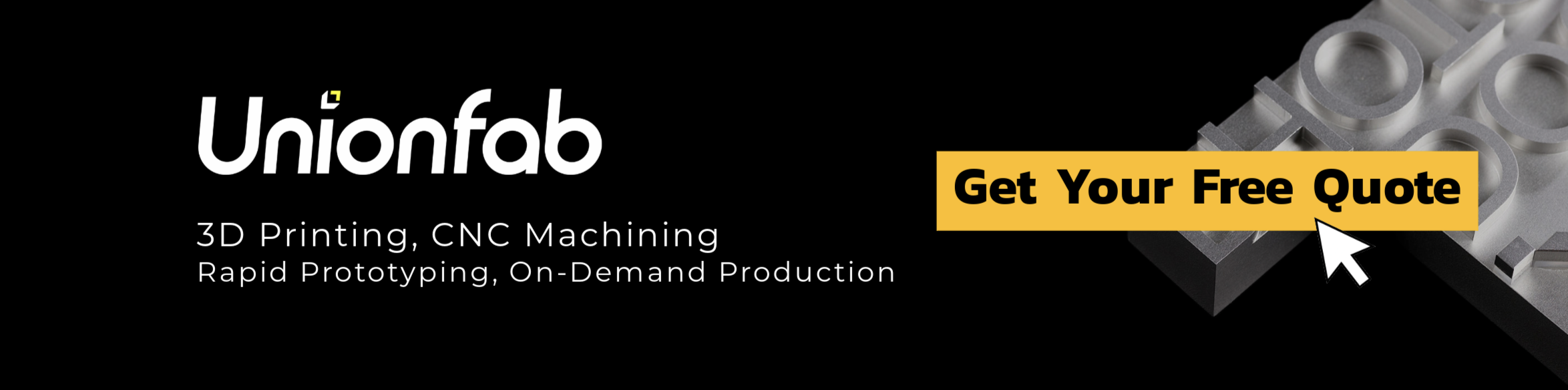
Maintaining stringent tolerances necessitates continuous quality control and corrective actions throughout all stages of CNC machining. Tight tolerance requirements demand meticulous process monitoring to catch any potential non-conformities.
How to Enhance the Precision in CNC Machining?
Design for Ideal Tolerances: An Art of Trade-off
Tighter tolerances increase accuracy but also manufacturing complexity and costs. Features should be classified based on their functional importance - dimensions critical for assembly fits or alignments need fine tolerances while others can allow more variance to reduce costs without affecting function.
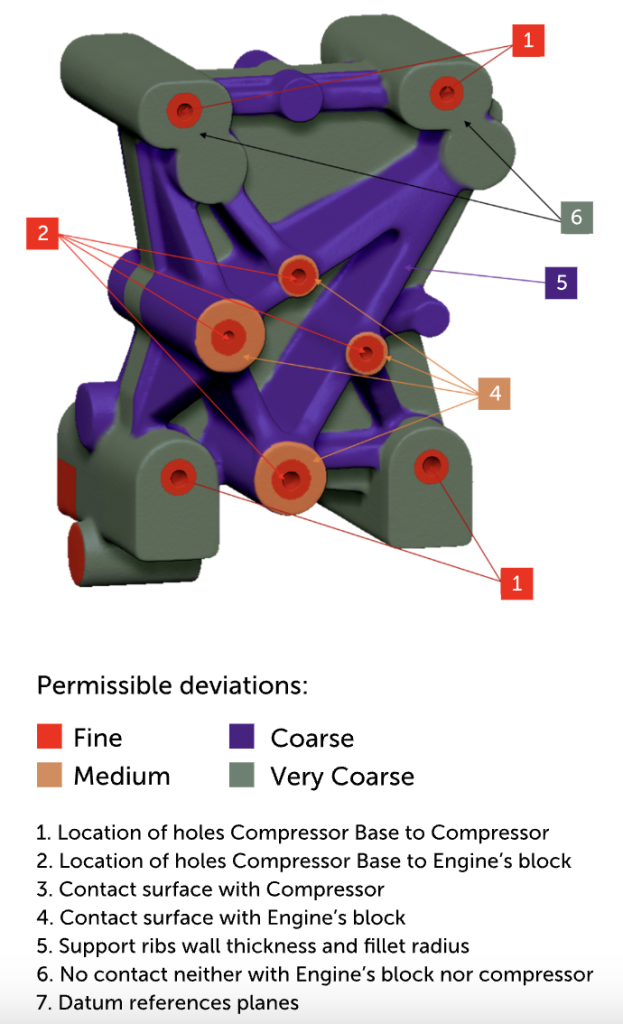
For example, ribs, fillets and other non-mating shapes can often accept less stringent tolerances compared to holes, slots or surfaces that directly interface.
Ensuring Measurement System Accuracy
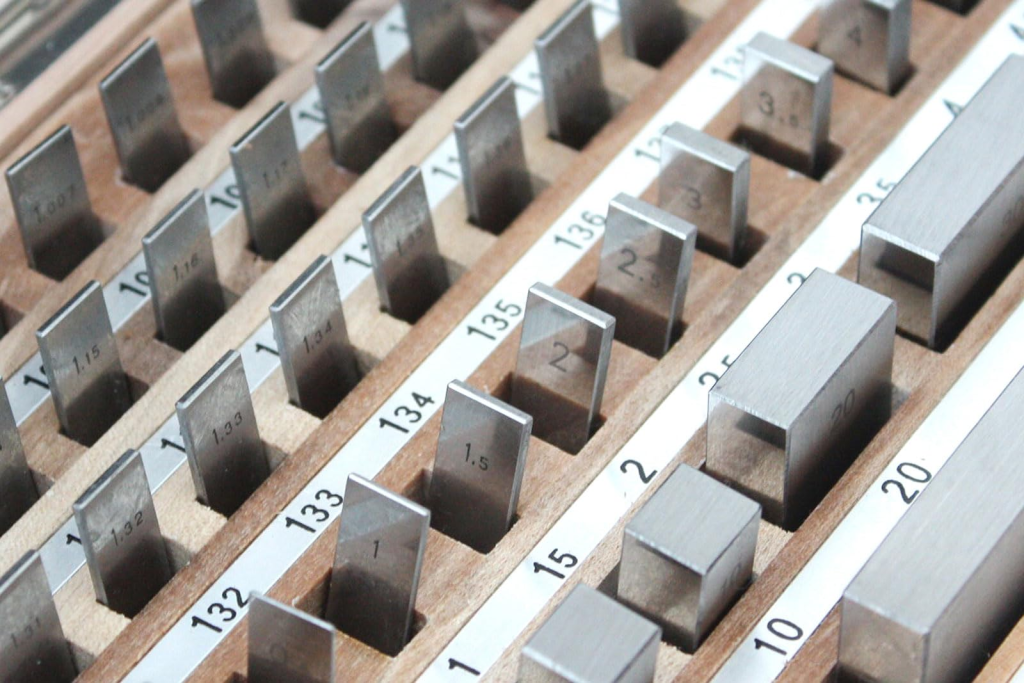
It's critical to validate the accuracy and precision of the measurement systems themselves through regular calibration and use of gauge blocks/pins. Comparing measurement system readings to known gauge values catches any measurement drift. This ensures issues stem from the process/parts rather than measurement inaccuracy.
Statistical Methods to Analyze Variation
Measurement System Analysis (MSA) and Gauge R&R (Repeatability and Reproducibility) apply statistics to separate multiple sources of variation - measurements, operators, equipment, environment. They clearly identify where the largest portion of non-conformance originates, focusing optimization efforts.
Quality Control at Programming Stage
Quality control begins at the programming stage. Tools such as simulation verify cuts will meet tolerances before actual production. On the shop floor, periodic part inspections identify early issues from set-up errors or machine drift.
Process Monitoring with Statistical Control Charts
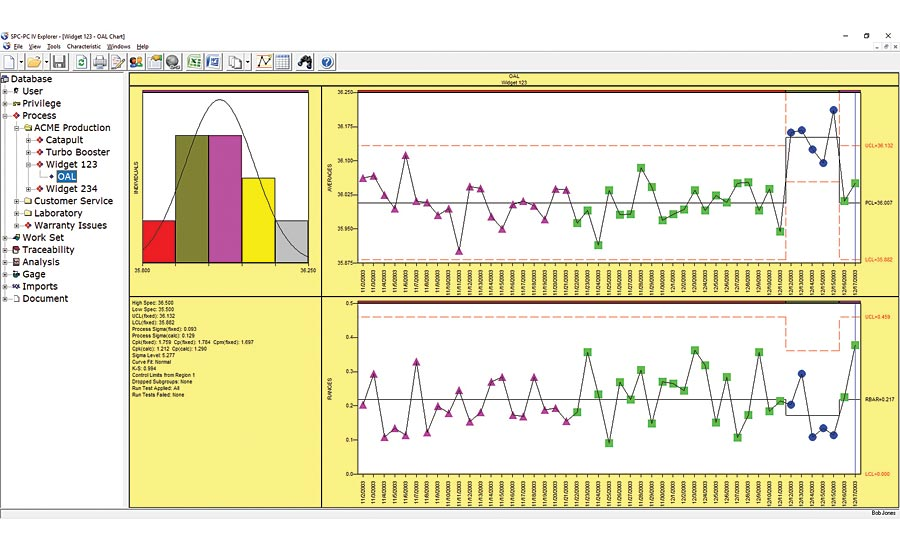
Statistical process control (SPC) charts track dimensions for outliers requiring troubleshooting. Precision instruments like coordinate measuring machines (CMMs) digitally scan sampled parts for variance. Non-compliant results trigger root cause analyses to isolate problems.
Common corrective actions include machine calibrations, cutter replacements, thermal condition adjustments, and fixture modifications. Operators record corrective details to prevent recurring errors. Keep process documented to ensure consistency across shifts.
Even during runs, quality checks like in-process gauging capture deviations so adjustments maintain precision.
Jigs and Fixtures
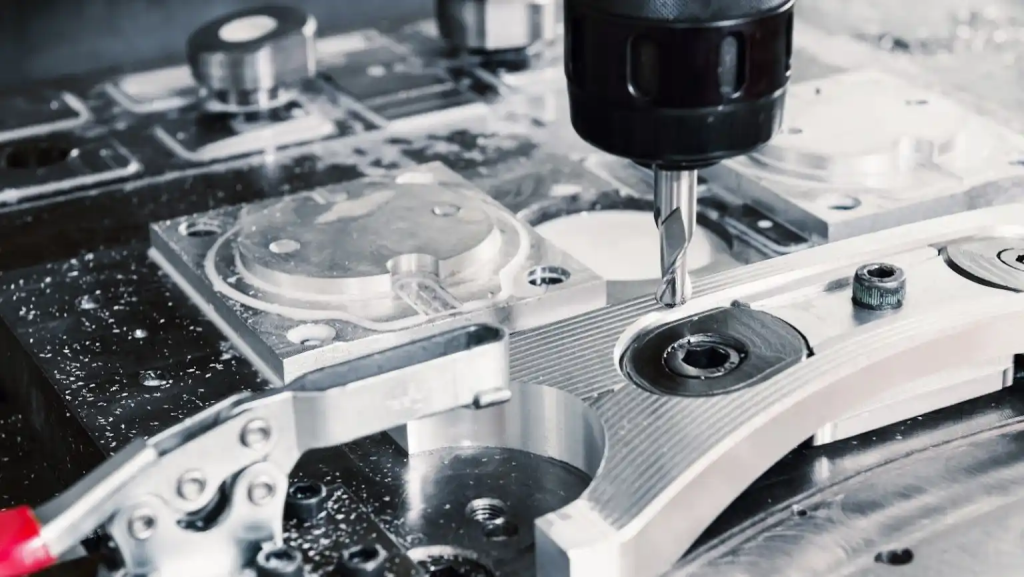
Dedicated jigs use dowels, locators and clamps to precisely locate parts for machining within tight tolerances. This ensures features are cut in the correct positional relationship.
Strong fixturing safely secures parts on the machine table/chucks to allow multifaceted surfaces and complex geometries to be cut without slippage affecting precision.
Post-Production Audits
Post-production audits confirm final parts as in-spec. A planned audit involves measuring a statistically significant sample of parts from a production run using CMMs or precision gaging equipment. All key dimensions and characteristics are re-verified.
Together, comprehensive quality protocols are needed to monitor all variables affecting precision and iteratively refine processes.
Equipment For CNC Precision Machining
CNC precision machining utilizes programmable automation to precisely cut and shape materials. Common CNC equipment includes lathes, milling machines, routers, laser cutters, electrical discharge machines (EDM), and plasma cutters.
CNC Lathe
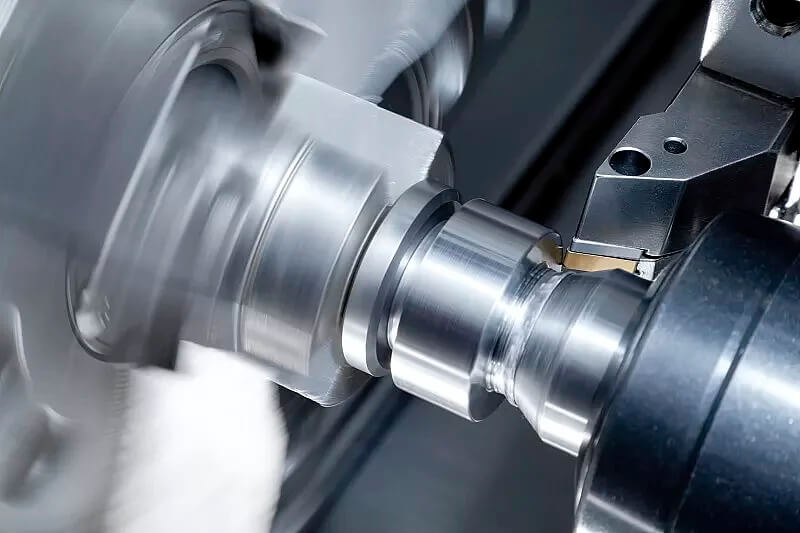
CNC lathes rotate the workpiece against a stationary cutting tool for operations like facing, turning, boring, threading, and grooving. The CNC system allows for precise control of spindle speed, feed rate, depth of cut, and other parameters. They are ideal for repetitive rounding, facing, and turning operations on axis-symmetric parts.
CNC Milling Machine
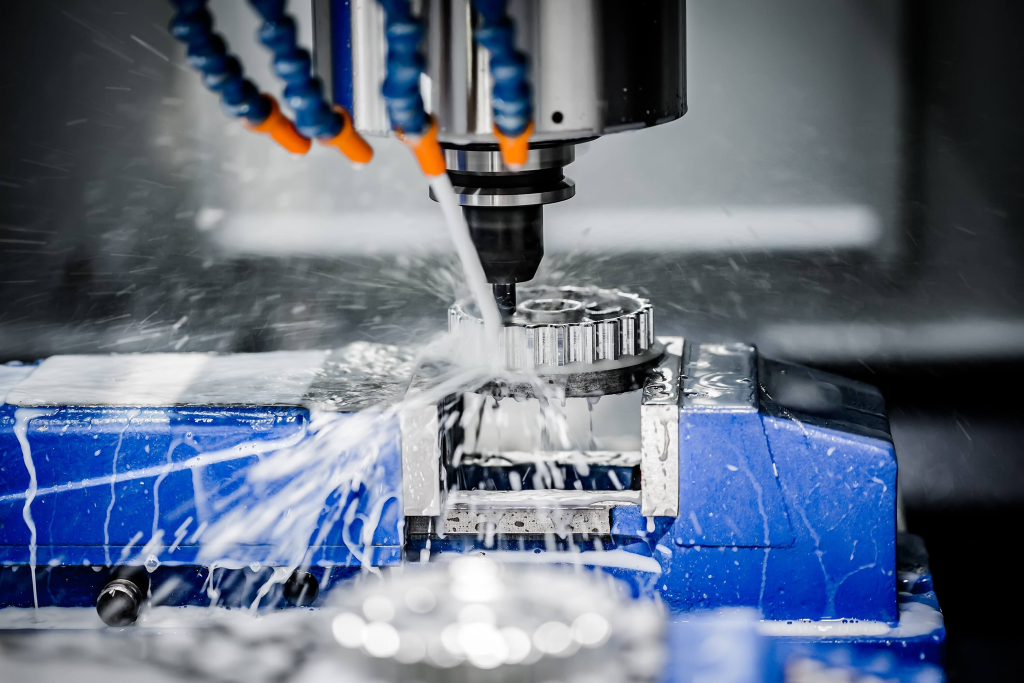
CNC milling use rotary cutters to remove material by advancing a workpiece through the spinning tool. The CNC controls feed rates, spindle speeds, tool paths, and depth per pass. It is versatile for complex geometries, slots, pockets, and surfacing operations.
CNC Router
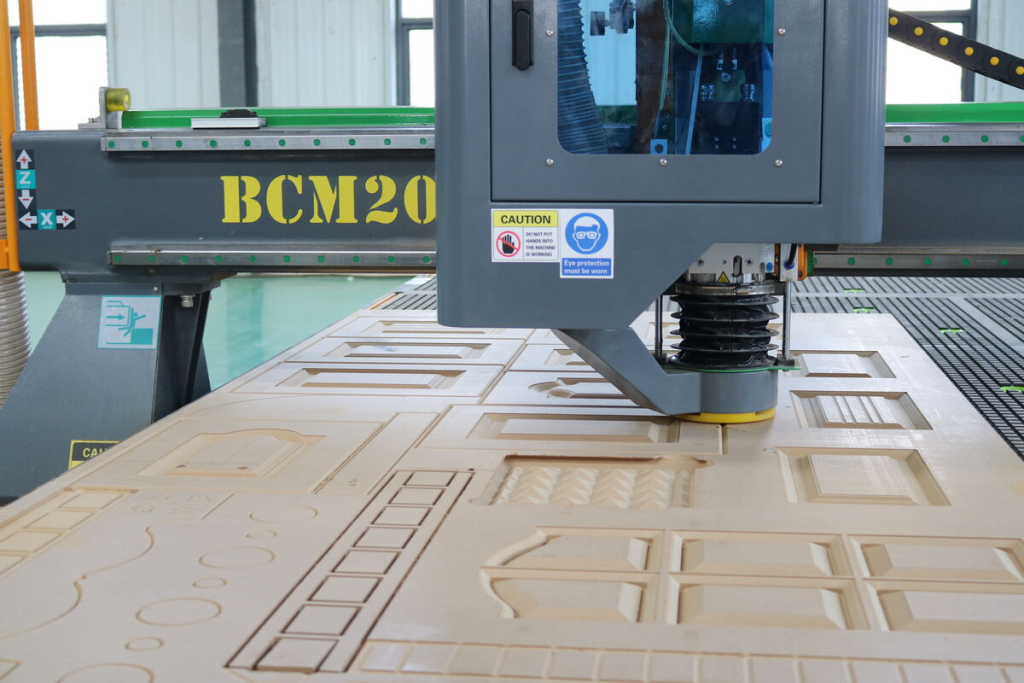
CNC routers function similarly to CNC milling machines but with a spinning router bit for cutting softer materials like wood, plastic, and aluminum. They excel at rapid prototyping, engraving, woodworking, sign making, and aerospace parts.
CNC Laser Cutter
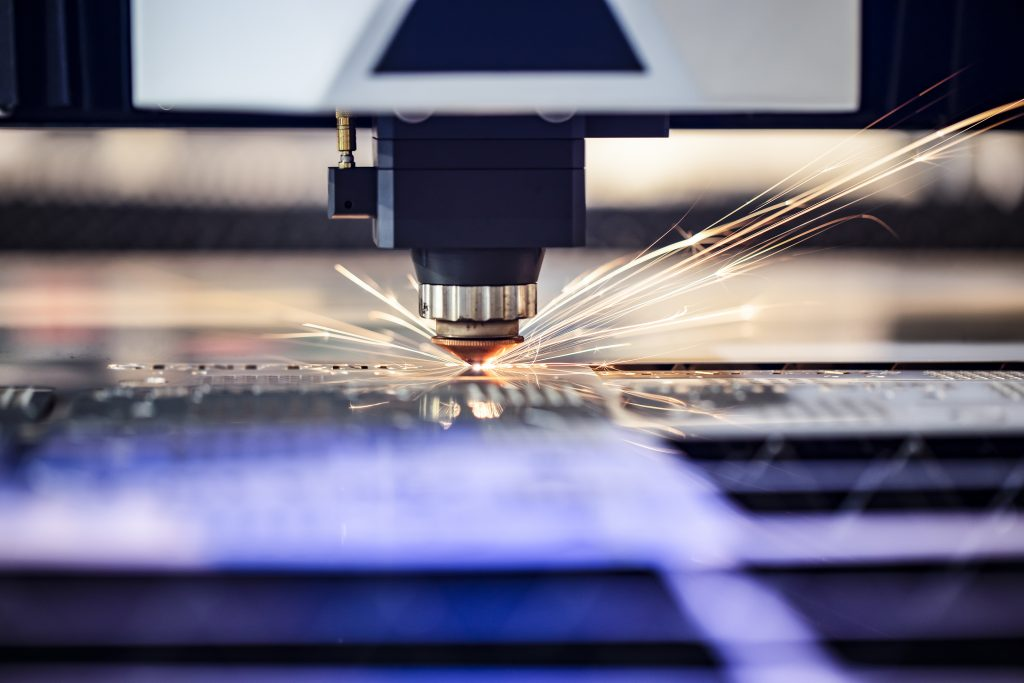
CNC laser cutters direct a high-power laser beam at the workpiece, melting, burning, or vaporizing the material. The focused laser light follows the programmed path to cut complex shapes with high accuracy and small kerf widths. Laser cutting is suitable for sheet metal, plastics, wood, and other materials.
CNC EDM Machine
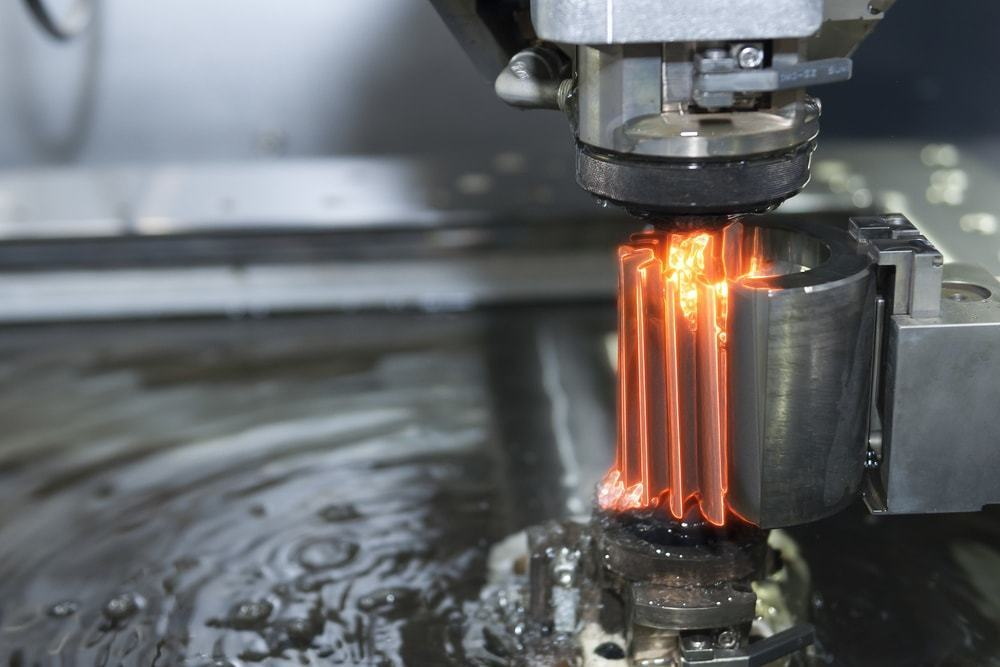
CNC electrical discharge machining (EDM) uses electrical discharges to erode conductive materials without mechanical forces. The CNC system guides fine voltage pulses between the workpiece and an electrode. EDM can produce intricate cavities, holes, and details in hard metals that may be difficult or impossible with other processes.
CNC Plasma Cutter
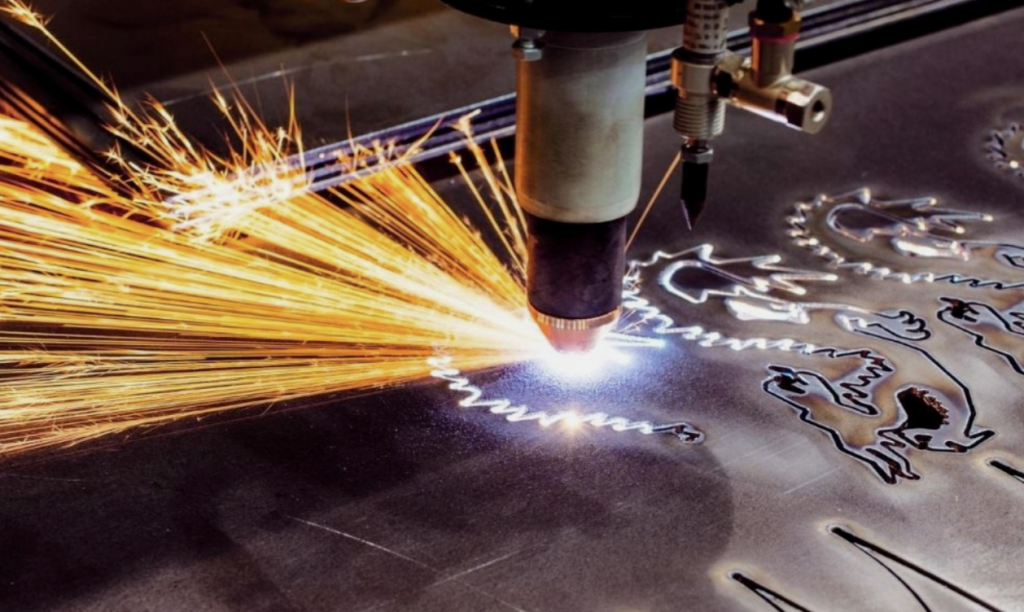
CNC plasma cutters pass an electrically conductive gas through an arc to melt and blow away material. The plasma jet follows the programmed path to cut sheets as thick as 1 inch. Plasma cutting is fast and has a high cut quality for thick steel, aluminum, and stainless steel.
3-Axis, 4-Axis, and 5-Axis CNC Machines
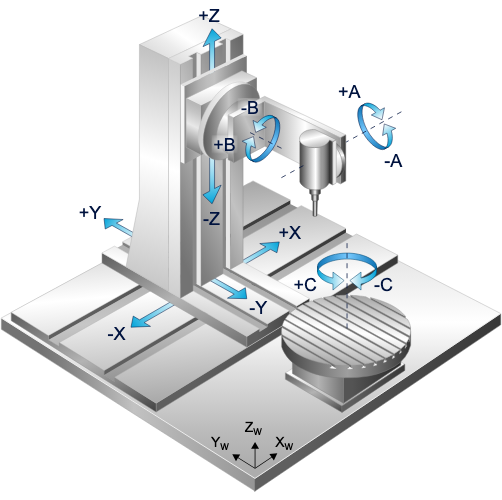
Advanced CNC machines offer 3-axis, 4-axis, 5-axis or even more control. 3-axis machines move the tool or workpiece linearly in the X, Y, and Z directions. 4-axis adds a rotary table for tilted and angled features. 5-axis machines provide full freedom of movement with tilting/rotation on two additional rotary axes, enabling the cutting tool to approach the workpiece from any direction. 5-axis CNC enables highly complex geometries in aerospace, medical, and automotive parts.
Multi-Tool CNC Machines
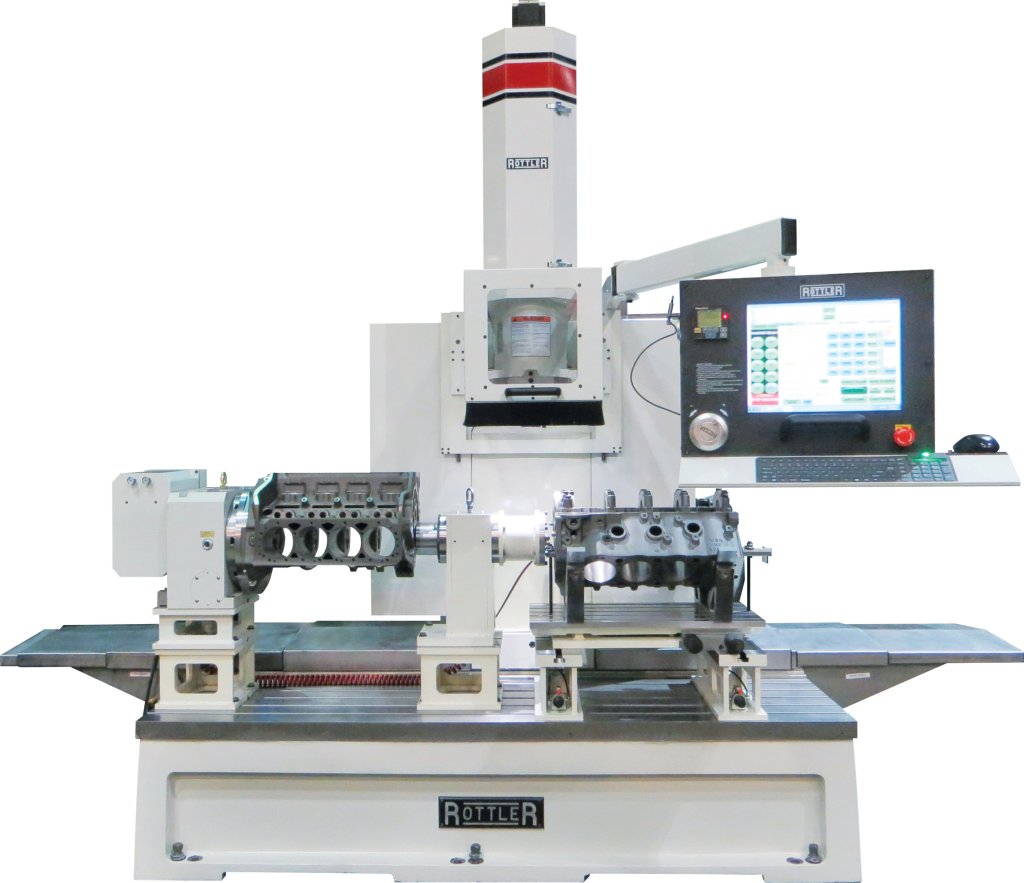
Multi-tool CNC machines utilize automatic tool changers to reduce operation time by allowing the machine to perform multiple operations without human intervention. The tool magazine stores multiple cutting tools, such as various diameter end mills and drills, which the machine can automatically swap into the spindle when needed. This allows completing different features of a part in one setup rather than changing tools manually between operations.
Multi-tool capabilities are especially advantageous for large production runs where uptime is critical. Common multi-tool CNC machines include machining centers with milling, drilling, boring, and tapping capabilities. Overall, multi-tool CNC improves cycle times and productivity for complex components requiring frequent tool changes.
Materials For CNC Precision Machining
CNC precision machining can process a wide range of materials, including metals, plastics, composites, and ceramics.
The machinability and cutting characteristics of each material govern appropriate feeds, speeds, tools, and strategies. Harder materials often necessitate slower speeds, smaller depths of cut, and rigid machine tools. Advanced techniques like high speed machining and hard turning can expand the capabilities for challenging materials.
Metal
Common metals machined with CNC equipment include aluminum, steel, stainless steel, brass, and titanium. Each material has distinct properties that make it suitable for certain applications and challenging to machine in different ways.
Aluminum
Aluminum is lightweight, corrosion resistant, thermally conductive, and easy to machine. The 6xxx series of aluminum alloys contain magnesium and silicon for strength at lighter weights than steel.
It is commonly used in aerospace components, architectural features, automotive parts, and consumer products.
Material Options: Aluminum 6061, 6063, 6082, 7075, 2024, 5052, A380, etc.
Steel
Steel offers high strength and hardness for structural and mechanical parts, though it requires rigid machines and high power to cut.
Material Options: 1214L, 1215, 1045, 4140, SCM440, 40CrMo, etc.
Stainless Steel
Stainless steel boasts exceptional durability and resistance to corrosion, making it indispensable for components in industries like medical devices, food processing, and architectural applications.
However, its hardness can pose challenges during machining, necessitating specialized tooling and expertise.
Material Options: SUS303, SUS304, SS316, SS304, SS416, SS316L, 17-4PH, etc.
Brass
Brass and bronze possess appealing aesthetics, low friction, and antimicrobial properties for valves, fittings, and decorative items.
Material Options: 260, C360, H59, H60, H62, H63, H65, H68, H70, Bronze, Copper, etc.
Titanium
Titanium has an unmatched strength-to-weight ratio but is difficult to cut and requires special tooling. Titanium alloys like Ti-6Al-4V have good biocompatibility.
Material Options: Titanium Grade F1-F5.
Plastics
Material Options: POM/Nylon/PC/PMMA/PVC/PU/Acrylic/ABS/PTFE/PEEK, etc. Some commonest choices are:
POM (Polyoxymethylene)
POM is a low-friction, high-strength plastic used in CNC precision machining for mechanical parts, gears, home appliances and automotive applications.
PC (Polycarbonate)
Polycarbonate is known for its optical clarity, impact resistance, and heat tolerance. It’s often used in optical lenses, automotive components, and safety equipment.
PMMA (Polymethyl Methacrylate)
PMMA, or acrylic, offers exceptional transparency and UV resistance, making it an ideal choice for signage, displays, and optical components.
ABS (Acrylonitrile Butadiene Styrene)
ABS is a versatile thermoplastic with good impact resistance, making it suitable for consumer goods and prototyping.
CAD/CAM and Programming
CAD Software
Computer-Aided Design (CAD) software such as SolidWorks, Creo, and Inventor are used to create digital 3D models and drawings of parts. CAD plays a vital role in precision machining as it allows:
Designing components with precision tolerances directly modeled into the part geometry
Performing interference checks and simulating assemblies
Generating engineering drawings and specifications
Facilitating sharing of designs between teams and suppliers
CAM Software
Computer-Aided Manufacturing (CAM) software such as Mastercam, Edgecam, and SolidWorks CAM translates digital CAD designs into automatable CNC toolpaths. The CAM programmer:
Defines machining operations, tools, speeds, feeds
Simulates the toolpaths to validate precision and detect errors
Generates G-code machining programs optimized for the CNC machine
G-code and M-code
G-code is the numerical programming language interpreted by CNC machines. It contains pre-programmed sets of instructions using Letter addressing and Numerical values to command:
Rapid linear and circular tool motions (G00, G01, G02, G03)
Spindle and coolant controls (M03, M08)
Tapping and threading cycles (G32)
M-codes provide additional functions like tool changes, coordinate system shifts and optional stop controls.
Surface Finishing in CNC precision machining
Surface finishing in CNC precision machining is the final touch that elevates a component from raw functionality to a polished, high-performance product.
Anodizing
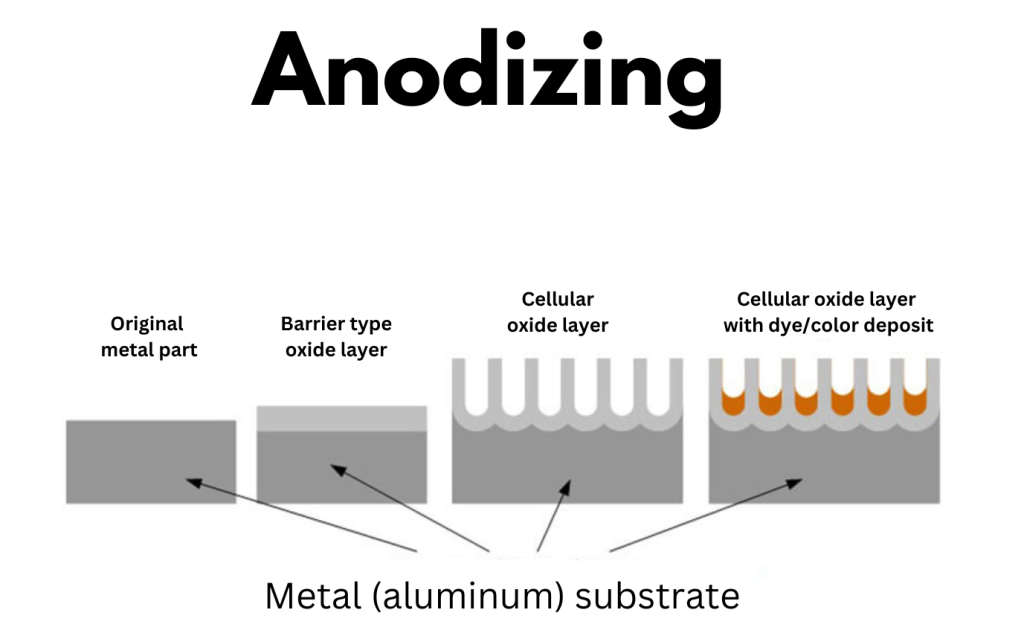
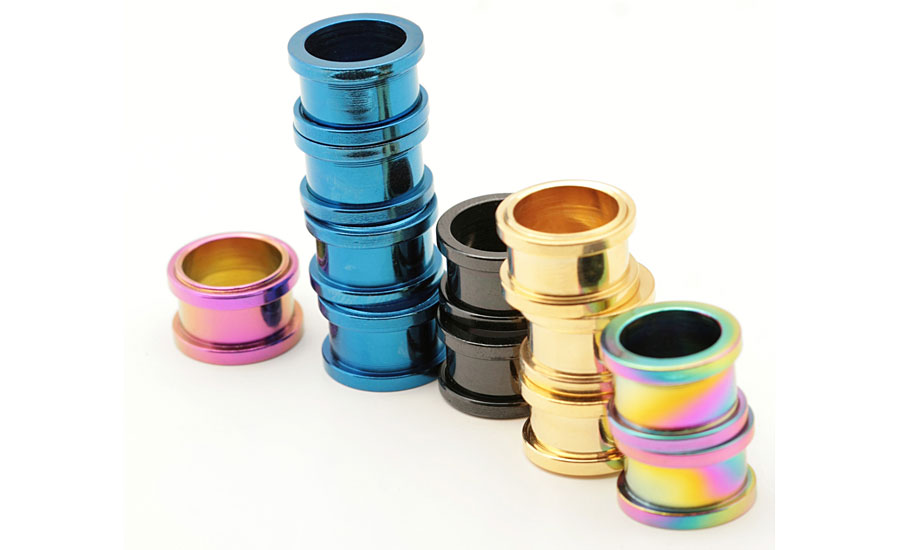
Anodizing forms a protective oxide layer on metals like aluminum, enhancing corrosion resistance and providing a decorative finish.
Bead Blasting
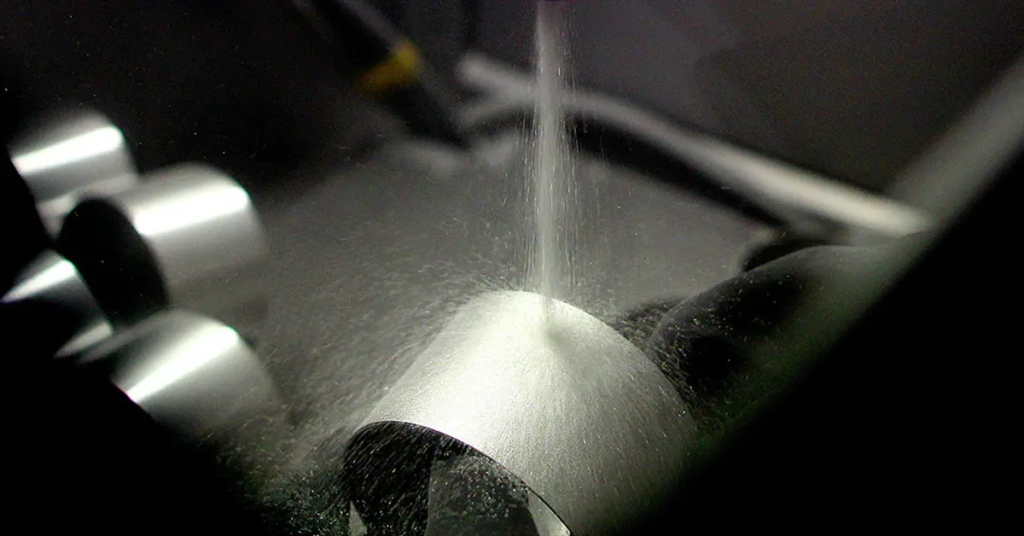
Bead blasting imparts a uniform matte finish to surfaces and can remove imperfections or contaminants.
Silk Screening
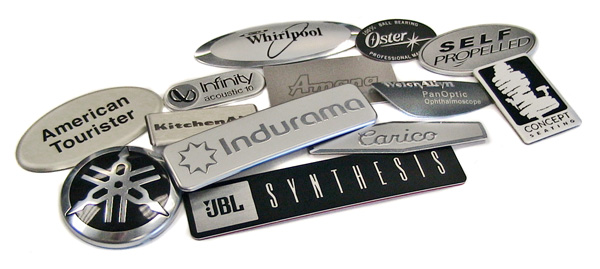
Silk screening involves printing graphics or labels directly onto the part’s surface, adding branding or informational elements.
PVD Plating (Physical Vapor Deposition)
PVD plating deposits thin, durable coatings with enhanced wear resistance, corrosion protection, and unique colors.
Plating (Zinc, Nickel, Chrome, Titanium)
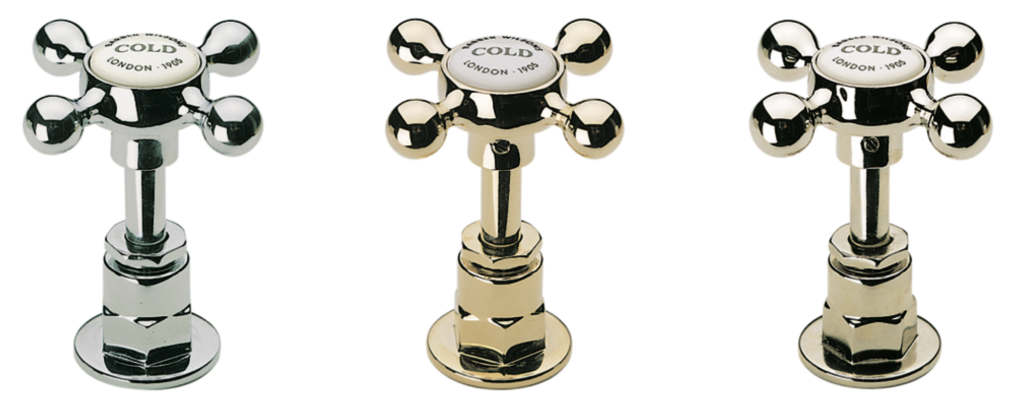
Metal plating enhances corrosion resistance and provides a decorative finish.
Brushing
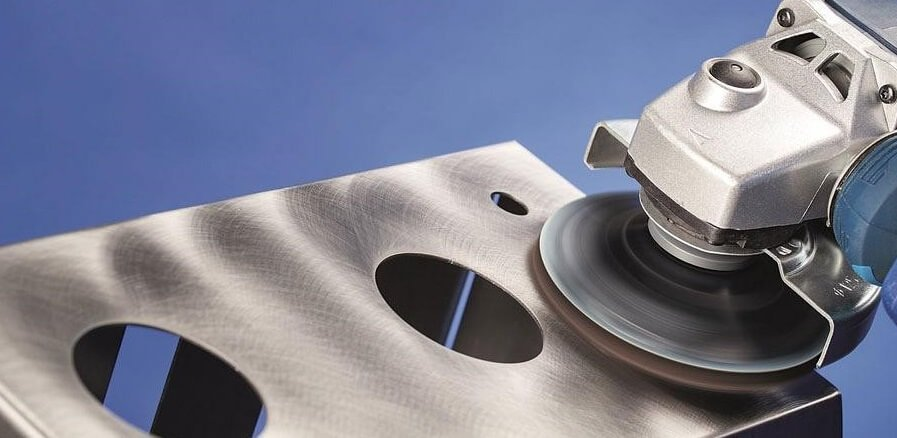
Brushing creates a fine-textured, directional finish on metal surfaces, often used for aesthetic appeal.
Painting
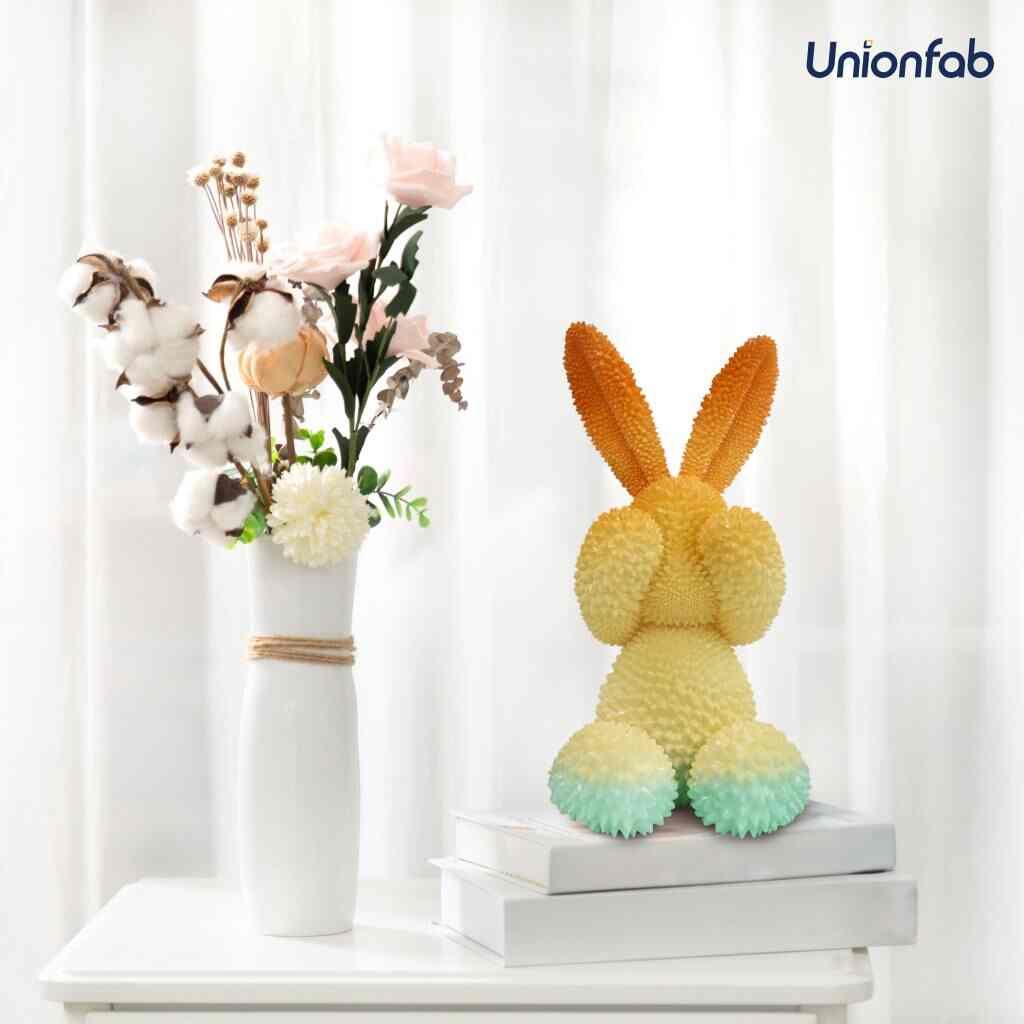
Painting adds color, protection, and aesthetics to parts, making it ideal for consumer products and industrial components.
Powder Coating
Powder coating offers a durable and attractive finish through the application of electrostatically charged powder particles.
Passivation
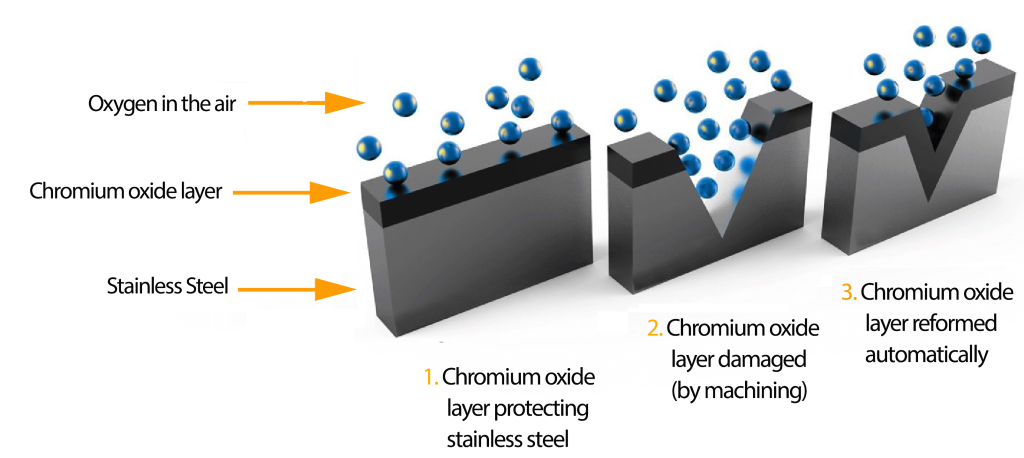
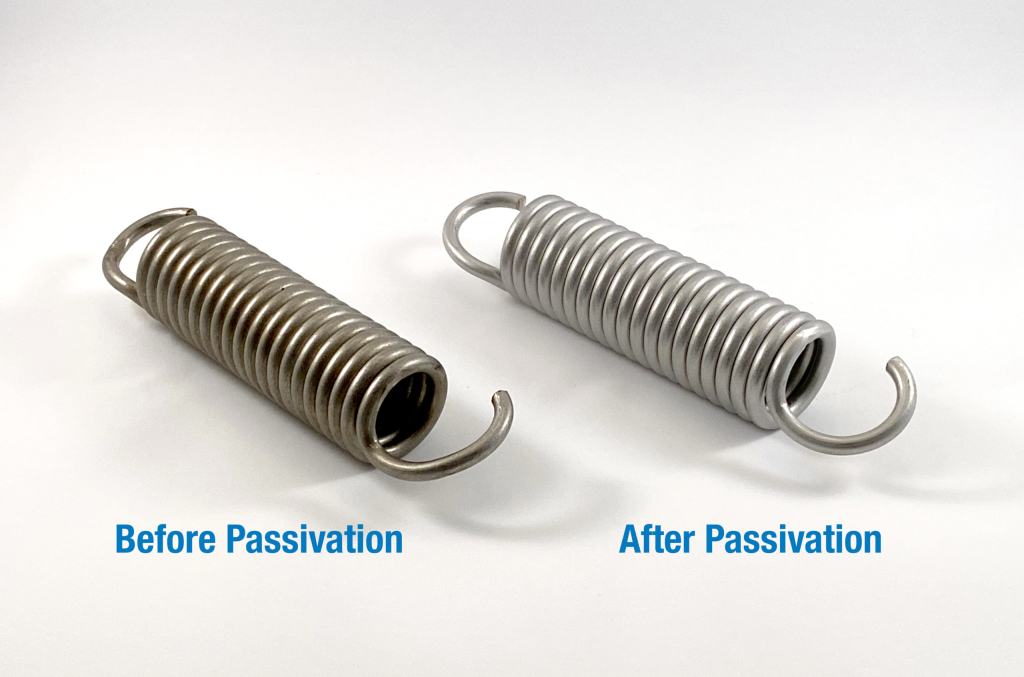
Passivation is a chemical process that is used to make the surface of a metal less reactive and more resistant to oxidation and corrosion
Electrophoresis
Electrophoresis creates a protective and decorative coating by immersing the part in an electrically charged paint solution.
Advanced Technologies For CNC Precision Machining
Automation
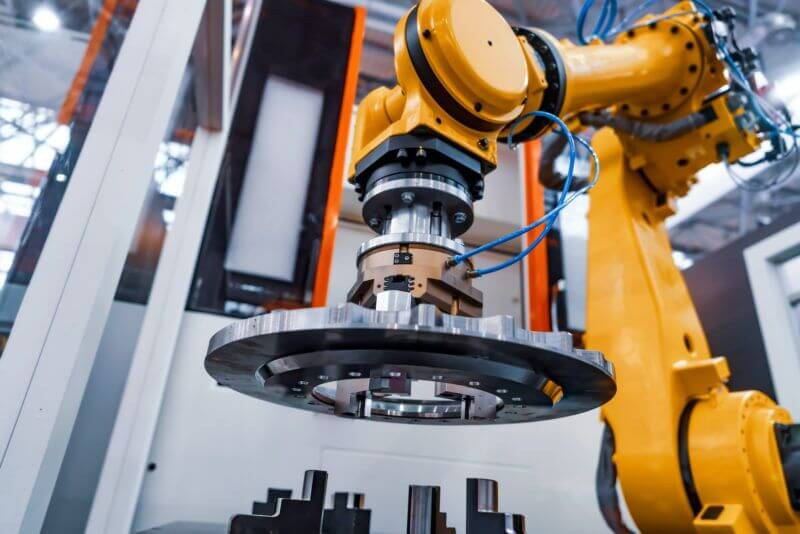
The integration of automation technologies, including robotics and machine tending systems, has streamlined the production process, reducing human intervention and increasing efficiency.
Additive Manufacturing
The fusion of CNC machining with additive manufacturing techniques enables the creation of complex parts with reduced material waste. This hybrid approach combines the precision of CNC machining with the design freedom of 3D printing.
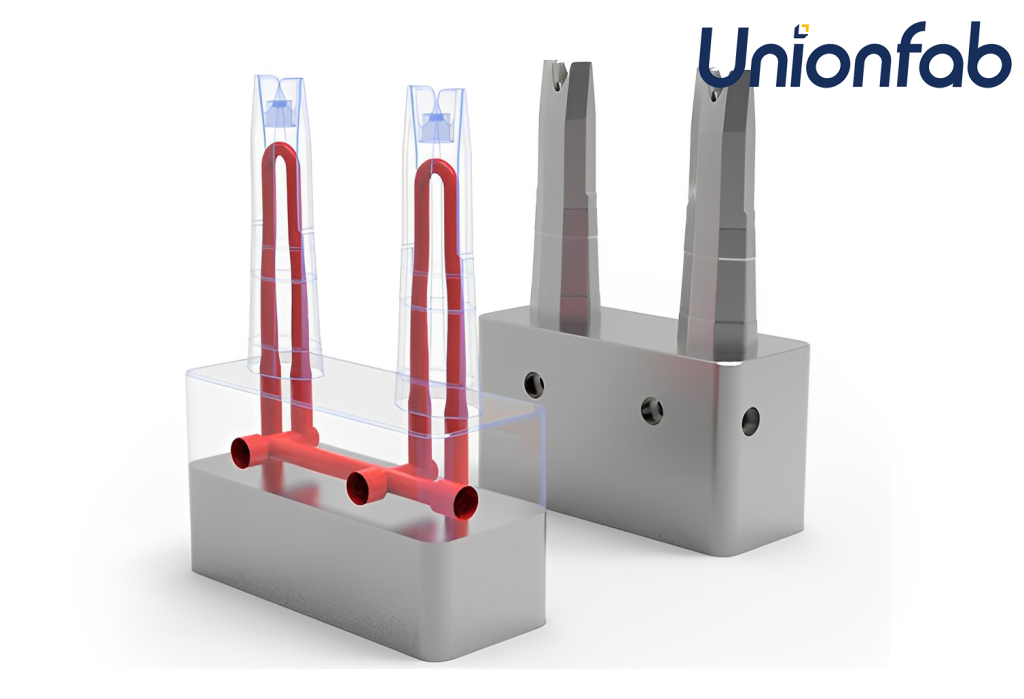
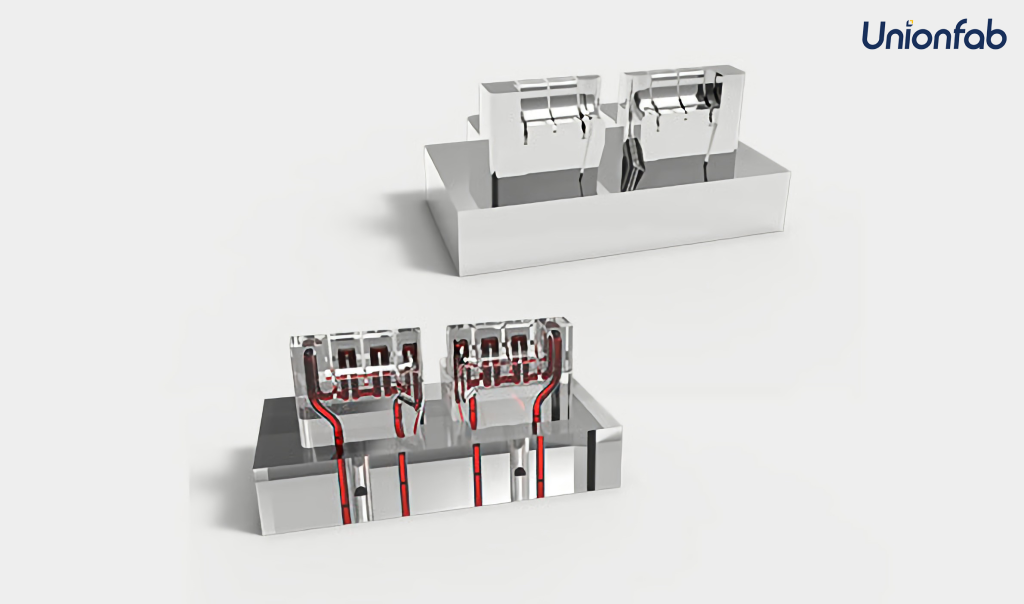
Besides, additive manufacturing creates strong customizable fixtures on-demand with conformal cooling channels to precisely locate parts for CNC operations.
IoT and Data Analytics
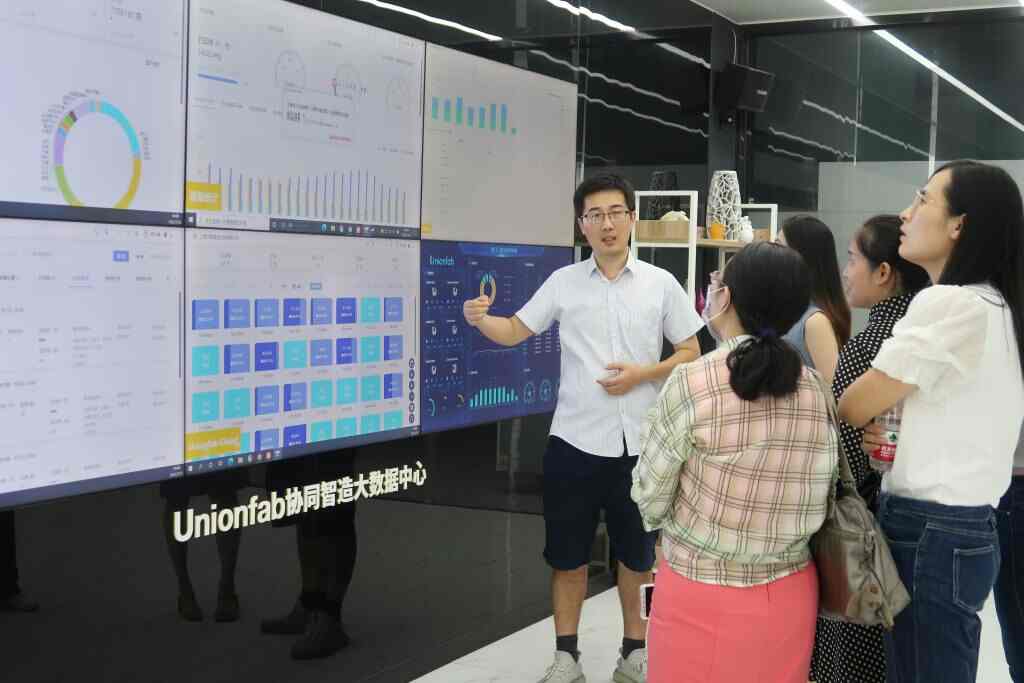
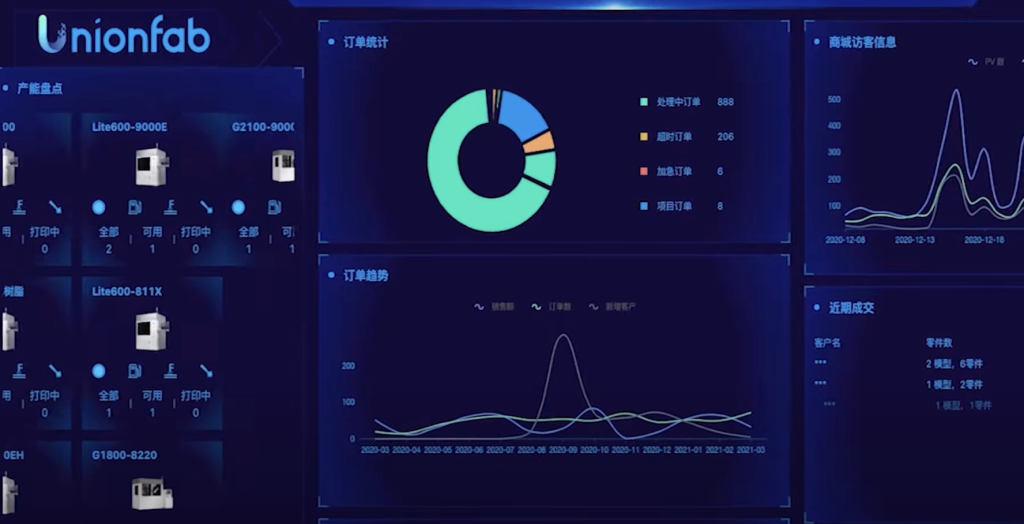
The Internet of Things (IoT) and data analytics offer real-time monitoring and data-driven insights, allowing for predictive maintenance, process optimization, and quality control.
Transparency Through Our Platform

You can closely monitor and manage every stage of your orders through our order management platform.
Challenges and Limitations
While offering immense precision and consistency, CNC machining faces challenges. Rigid setup and process control are required to minimize vibrations and deflection that can cause tolerance errors. Machinists must compensate for potential tool wear, chip evacuation issues, and complex fixturing needs. Parts with deep cavities or complex internal geometries can be difficult to machine and inspect.
Conclusion
In summary, achieving high precision CNC machining requires a systematic approach encompassing engineering best practices at each stage. Proper material selection, toolpath programming, fixtures, and adherence to industry standards facilitate holding tight tolerances from design to production. Complementary technologies aid prototyping, tooling and automation.
Together, applying these principles enables manufacturers to meet the stringent tolerance demands of markets requiring safety and performance, and advances the capabilities of CNC precision machining.
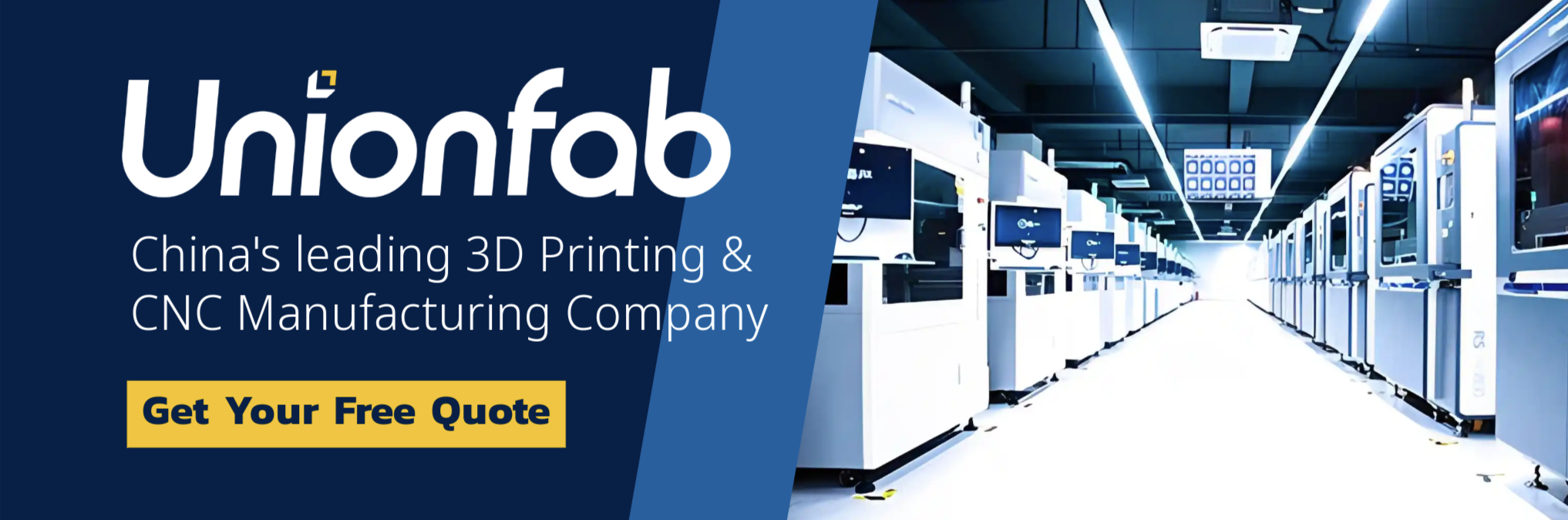