From Rough to Refined: Post-Processing Methods to Elevate metal Parts
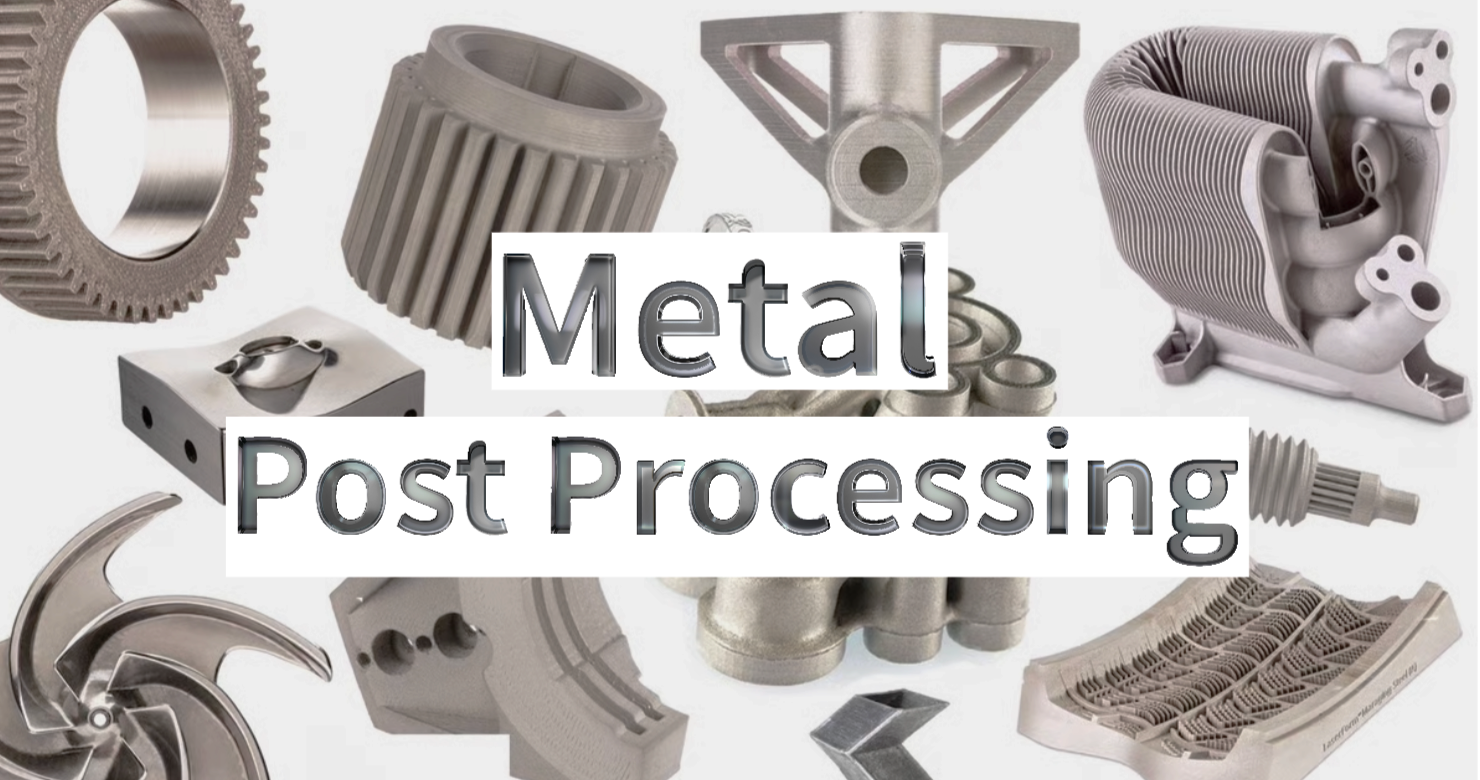
Explores an array of post-processing techniques that elevate the aesthetics and functionality of metal 3d printing parts with Unionfab.
What is post-processing in the context of metal 3D printing
Post-processing in the context of metal 3D printing refers to a series of additional steps and treatments that are applied to a metal part after it has been produced through an additive manufacturing (AM) process.
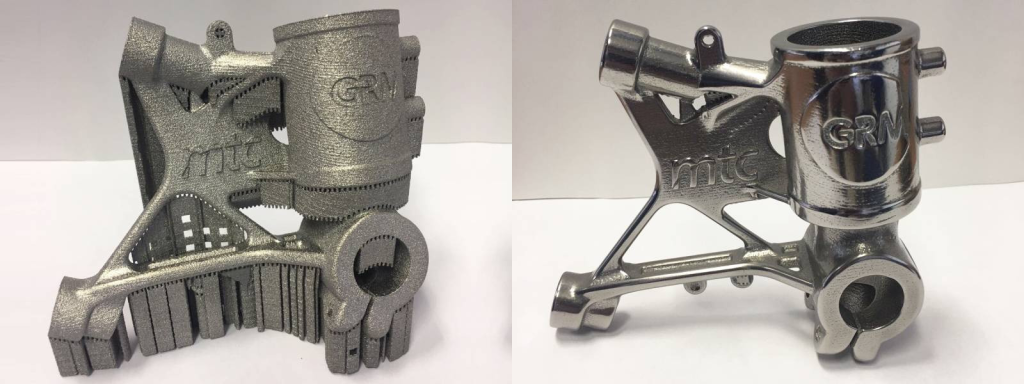
While the initial AM process creates the basic shape of the part by layering and fusing metal materials, post-processing aims to refine and enhance the part's properties, surface finish, and overall quality.
Post-processing methods are utilized to address specific challenges and optimize the part for its intended application. In the realm of metal 3D printing, post-processing can encompass a variety of techniques.
Why Do 3D Printed Metal Parts Needs Post-processing
Post-processing is an essential stage that bridges the gap between the raw 3D printed part and the final, fully functional, and refined product. It allows manufacturers to overcome challenges associated with AM.
Post-processing of 3D printed parts can improve visual attractiveness, tailor material characteristics, attain precise dimensional tolerances, and ensure compliance with industry or application standards.
Surface Improvement
Metal 3D printed parts often have a rough and textured surface due to the layer-by-layer deposition process. Post-processing techniques like polishing, sandblasting, or electropolishing can achieve smoother surfaces, eliminating roughness and enhancing aesthetics.
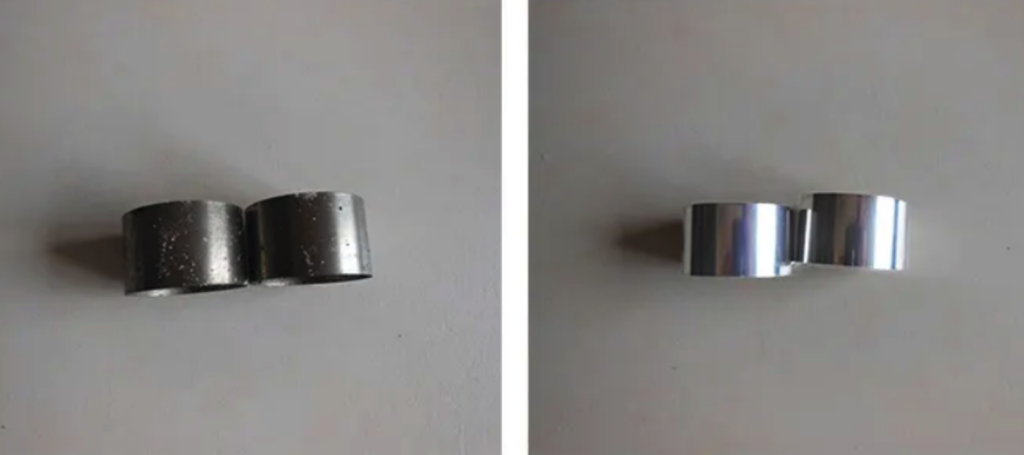
Roughness Reduction: Metal 3D printing processes often result in a layered surface texture that can affect aesthetics and functionality.
Aesthetic Improvement: Post-processing steps like electroplating, dyeing, painting, and laser engraving can enhance the aesthetic appeal of 3D printed items.
Contact Performance: Smooth surfaces reduce friction and wear, enhancing the performance of moving or sliding components.
Mechanical Property Refinement
Certain post-processing techniques, like heat treatment or shot peening, can improve the mechanical properties of metal 3D printed parts, such as hardness, toughness, and fatigue resistance.
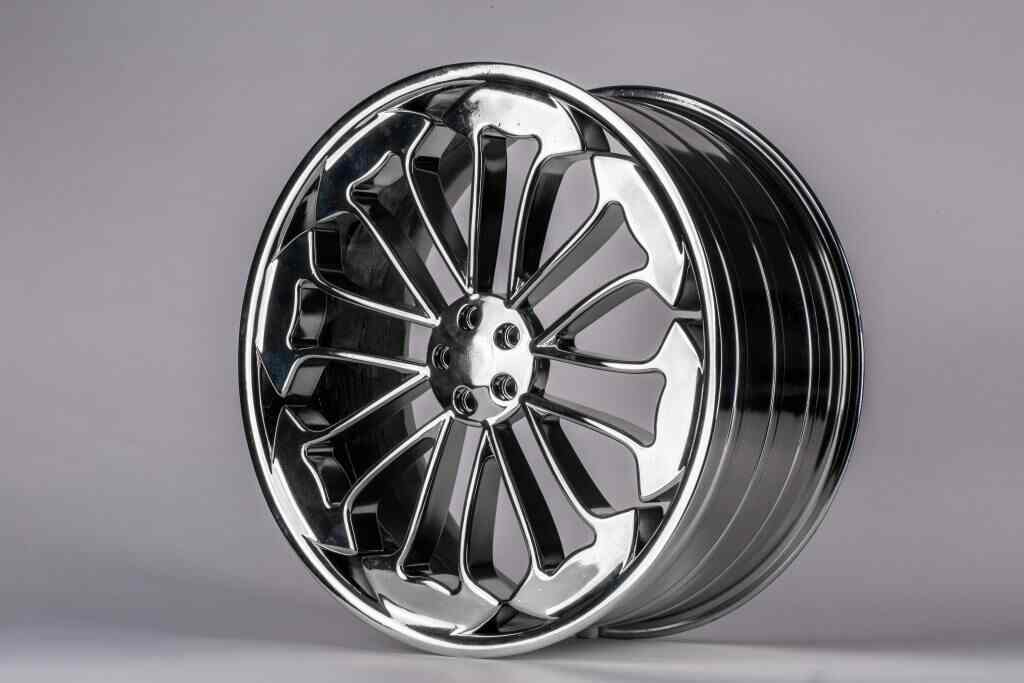
Stress Relief: Post-processing methods like heat treatment reduce residual stresses, minimizing the risk of part distortion or failure.
Toughness and Durability: Techniques like shot peening increase material strength and fatigue resistance, extending part lifespan.
Material Consistency: Homogenizing the microstructure through post-processing ensures consistent mechanical properties across the part.
Corrosion Protection: Metal 3D printed parts may be susceptible to corrosion due to exposed surfaces and potential microstructural variations. Coatings, platings, or chemical treatments applied during post-processing can enhance corrosion resistance.
Porosity Reduction: Some metal AM processes can result in parts with microscopic pores or voids. Post-processing methods, such as heat treatment, help reduce porosity, enhancing the mechanical properties and structural integrity of the parts.
Customization and Adaptation
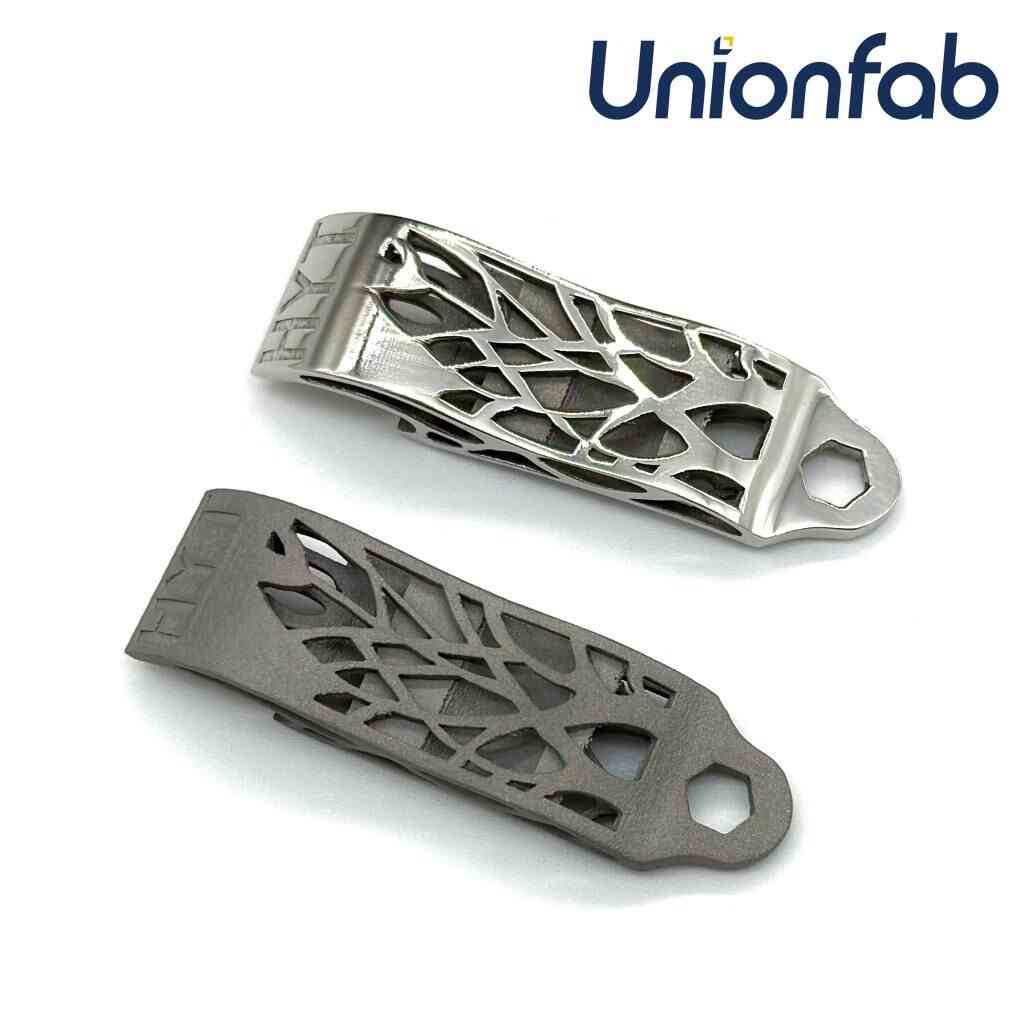
Industry Standards and Optimization: Post-processing can adapt metal 3D printed parts to specific applications, such as aerospace, medical, automotive, or industrial applications, by improving characteristics relevant to each industry.
Additional Features: Post-processing enables integration of features like threads, inserts, or mating surfaces that may be challenging to achieve through printing alone.
Microstructure Control: Some post-processing techniques, such as heat treatment or HIP, can modify the microstructure of the material, allowing for customization of material properties to meet specific performance requirements.
Multi-Material Integration: Certain post-processing methods, like machining or welding, can enable the integration of multiple materials or components, expanding the design possibilities and functionality of the part.
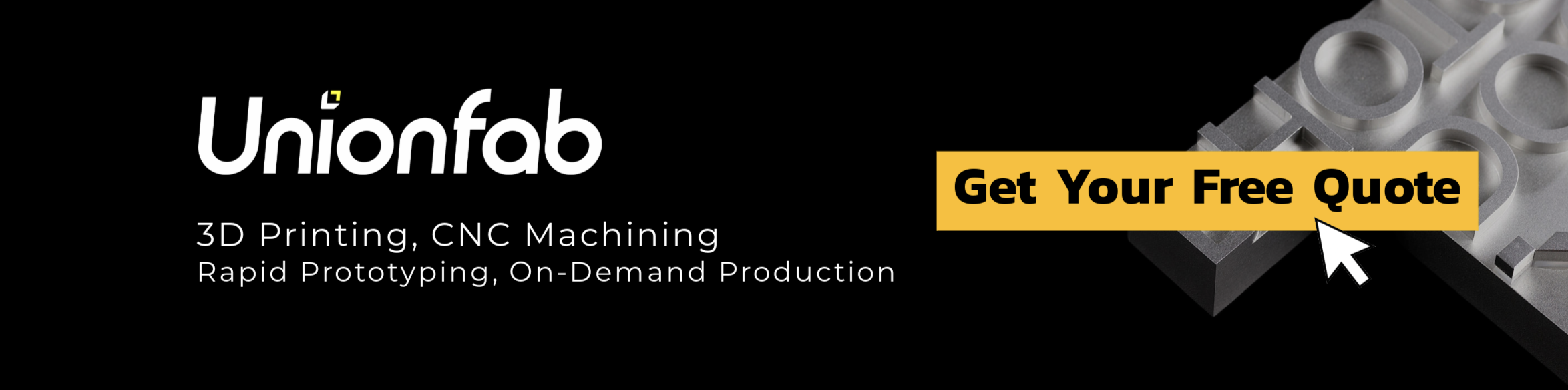
Post-Processing Requirements for Specific Metal AM Processes
Metal additive manufacturing processes offer exciting possibilities. However, ensuring the optimal quality and functionality of the printed components often requires meticulous post-processing. Let’s explore the tailored approaches for each technique:
Powder Bed Fusion (PBF): Selective Laser Melting (SLM) / Electron Beam Melting (EBM)
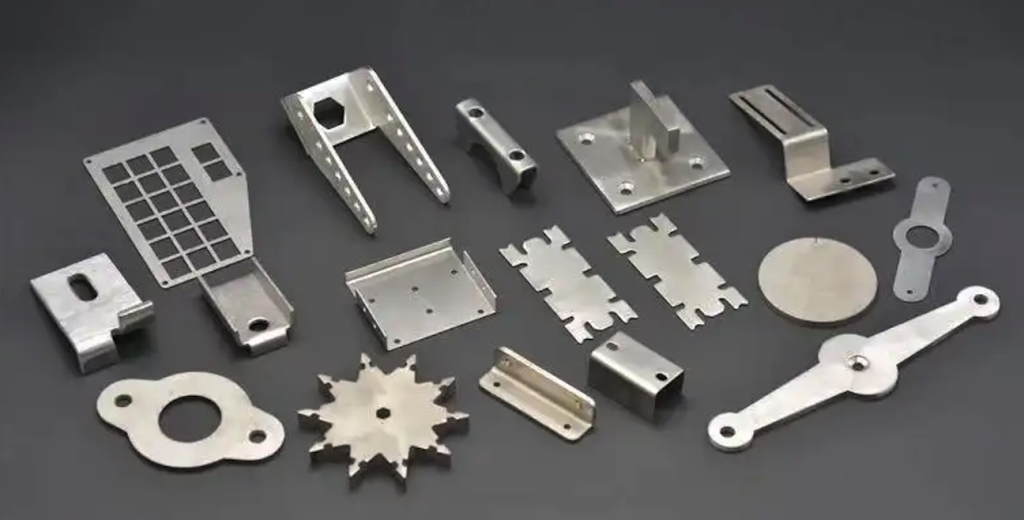
Heat Treatment: Employed to alleviate residual stresses and bolster part stability and mechanical properties.
Hot Isostatic Pressing (HIP): Decreases porosity, augmenting material density, mechanical strength, and fatigue resistance.
Surface Polishing and Grinding: Enhances surface finish by mitigating layering effects, resulting in improved aesthetics and contact performance.
Machining: Enables precise dimensions and intricate features, especially crucial for tougher metals.
Coating and Plating: Elevates corrosion resistance while providing an added protective layer.
Binder Jetting (BJT)
Sintering: Furnace sintering fuses metal particles, enhancing material strength.
Infiltration: Introducing a secondary material, like polymer or metal, into the porous part improves mechanical properties and porosity reduction.
Surface Coating: Applied to enhance corrosion resistance and add an aesthetic finish.
Metal Filament Extrusion
Sintering: Paralleling binder jetting, sintering fuses metal particles, contributing to material strength.
Machining: Vital for achieving precision dimensions and intricate details.
Surface Smoothing and Coating: Employed similarly to other methods to heighten both visual appeal and functional attributes.
Directed Energy Deposition (DED)
Machining: Used to achieve precise dimensions and surface finish, particularly advantageous for large-scale parts.
Heat Treatment: Alleviates stresses and refines material properties, enhancing overall structural integrity.
Surface Finishing: Techniques such as shot peening or grinding enhance surface quality, reducing roughness.
Incorporating these specialized post-processing methods tailored to each metal additive manufacturing technique ensures that your parts achieve superior quality, functionality, and compliance with industry standards.
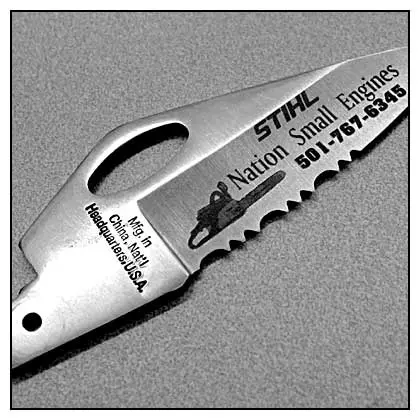
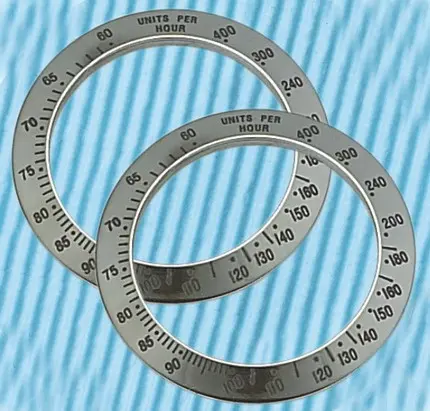
Unionfab’s Tailored Expertise: Elevating Your Metal AM Parts to Excellence
As a leading metal 3D printing service provider, Unionfab leverages extensive post-processing capabilities to deliver parts that meet your expectations. Our experienced engineers will recommend the ideal post-processing methods tailored to your specific metal AM technology, material, and quality goals.
Unionfab’s comprehensive post-processing services include stress relieving, surface finishing, coatings, heat treatment, machining, and more. By utilizing Unionfab’s post-processing expertise, you can fully realize the potential of metal additive manufacturing and achieve excellence for your printed metal components.
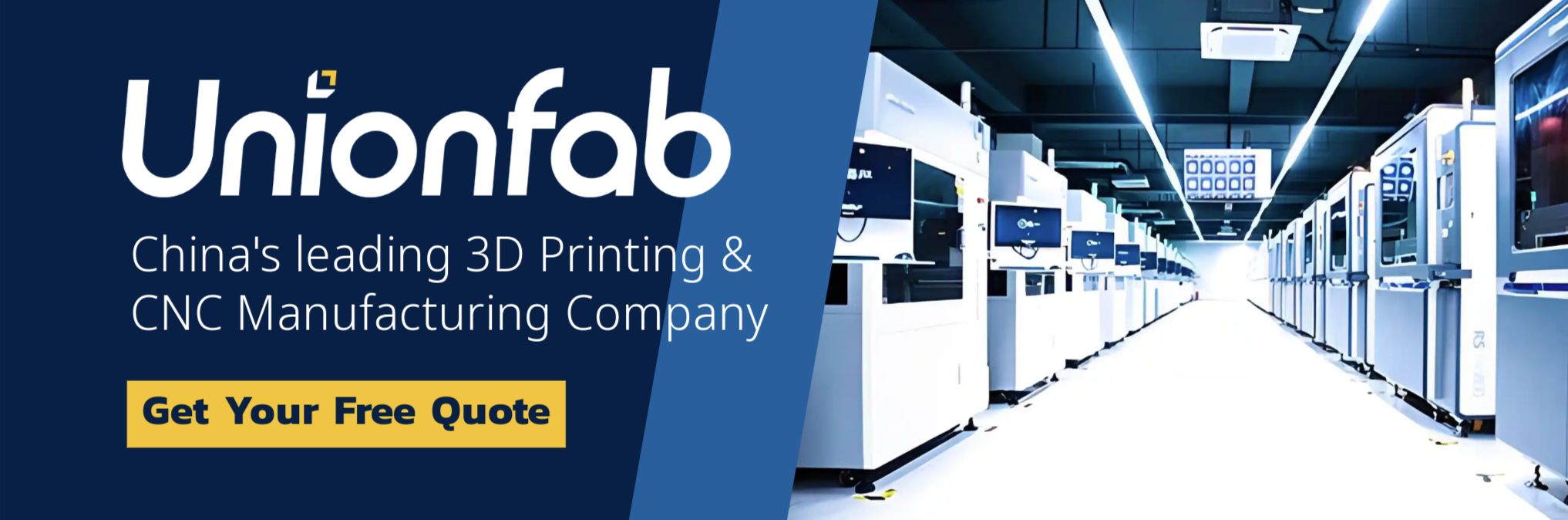
Metal AM Post-Processing — FAQs
Q1: What are the common post-processing techniques used to improve the surface finish of metal 3D printed parts?
A1: Common post-processing techniques for enhancing surface finish include polishing, grinding, sanding, shot peening, chemical treatments, and coatings. These methods smooth out layer lines, reduce roughness, and create a refined appearance on metal 3D printed parts.
Q2: Can you provide examples of real-world applications where post-processing significantly improved the quality of metal 3D printed parts?
A2: In aerospace, post-processing transformed 3D printed turbine blades by removing surface imperfections, enhancing aerodynamics, and improving overall performance. Additionally, medical implants have seen improved biocompatibility and reduced risk of bacterial growth through post-processing techniques that enhance surface smoothness.
Q3: What are the steps involved in post-processing a metal 3D printed part?
A3: Post-processing steps can vary but typically involve:
Removal of Supports: Detaching any temporary supports used during printing.
Surface Smoothing: Employing techniques like grinding, polishing, or sanding to enhance surface finish.
Heat Treatment: Applying heat to relieve stresses, improve mechanical properties, and enhance material integrity.
Coating or Plating: Adding protective or decorative layers to the surface.
Inspection and Quality Control: Conducting checks to ensure part dimensions, tolerances, and surface quality meet specifications.
Q4: Are there any limitations or drawbacks associated with certain post-processing techniques for metal 3D printed parts?
A4: Yes, some post-processing methods can alter dimensional accuracy or introduce thermal stress, potentially affecting the final part. Overly aggressive machining, for instance, might compromise intricate features. Additionally, some techniques may add time and cost to the production process.
Q5: Does post-processing affect the cost and time required for metal 3D printing projects?
A5: Yes, post-processing can impact both cost and time. More complex post-processing methods, such as extensive polishing or heat treatment, can add to production time and increase costs. However, these investments often lead to improved part quality and performance.
Q6: How do emerging technologies, such as AI and automation, impact the future of post-processing for metal 3D printed parts?
A6: Emerging technologies, including AI and automation, are poised to revolutionize the landscape of post-processing for metal 3D printed parts. Currently, post-processing leans heavily on human effort and expertise, which can be time-consuming and potentially introduce variations. However, the integration of AI-driven algorithms and automation holds the potential to significantly optimize and streamline these processes.