Guidelines for Orienting and Supporting 3D Models in Additive Manufacturing
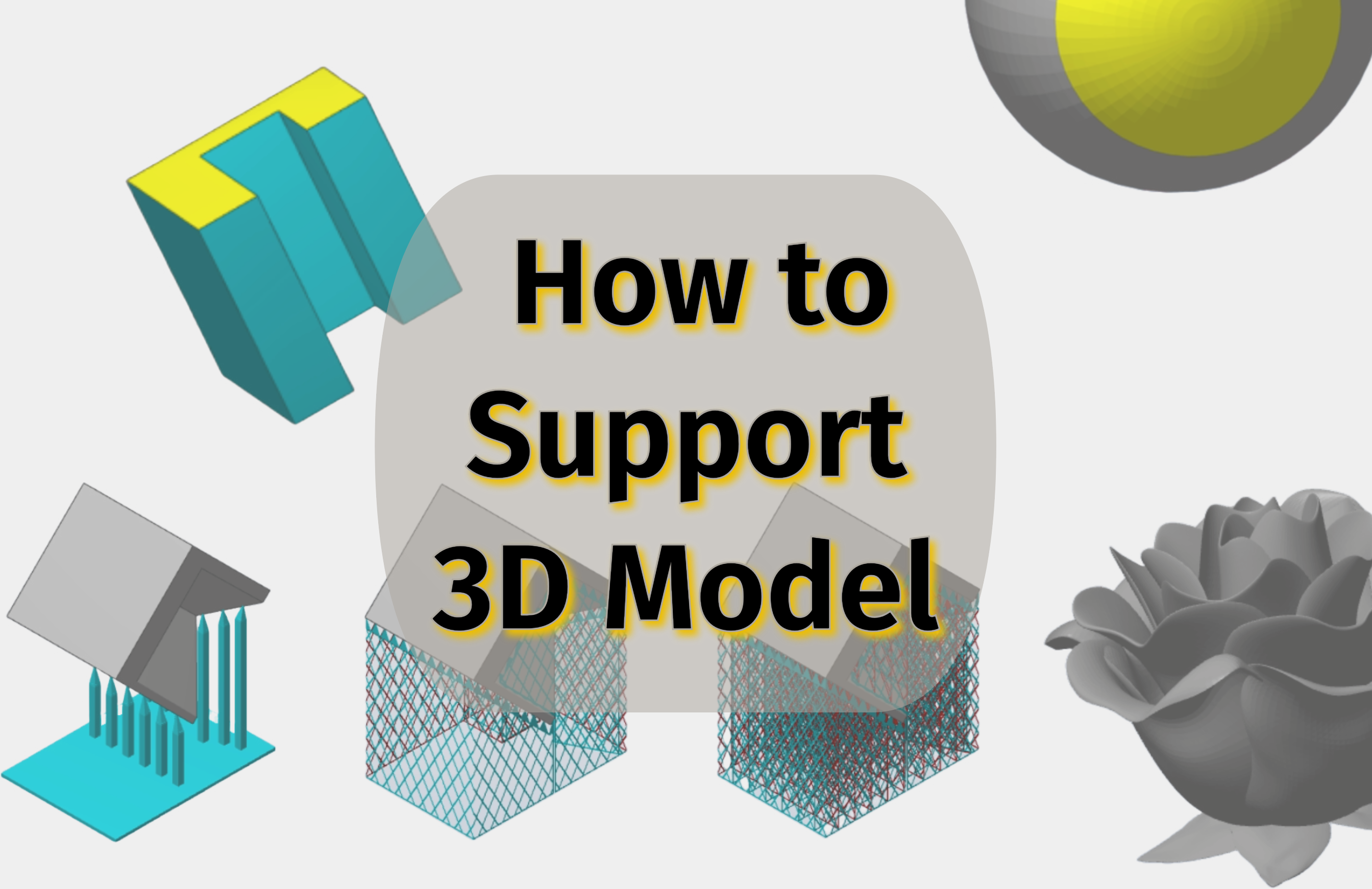
Guidelines and best practices to optimize orientation and supports for 3D model files, especially for intricate geometries.
Introduction
Proper orientation and supports for 3D model files is critical for successful additive manufacturing, especially when printing complex geometries.
This article will provide best practice guidelines and strategies for optimizing orientation and supports to enable more efficient and higher quality printing. The choices made regarding positioning of the part and creation of support structures have a major influence on factors such as print quality, material usage, print time, and post-processing work required.
Part Orientation Strategies
Alignment to Reduce Supports
Orienting the part so less material is suspended mid-air with no build plate adhesion allows more of the object to print directly without assistance.
Analyze orientations that maximize direct contact with the build platform. Minimizing these unsupported features through strategic part positioning reduces unnecessary support material usage.
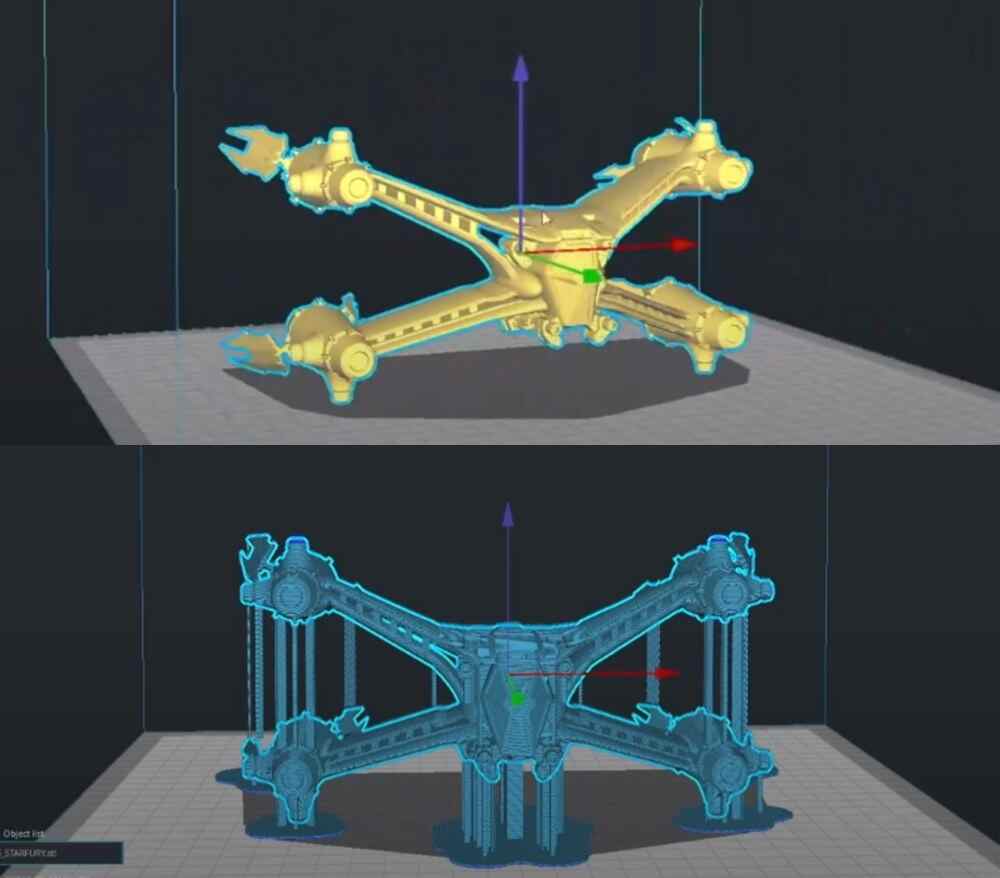
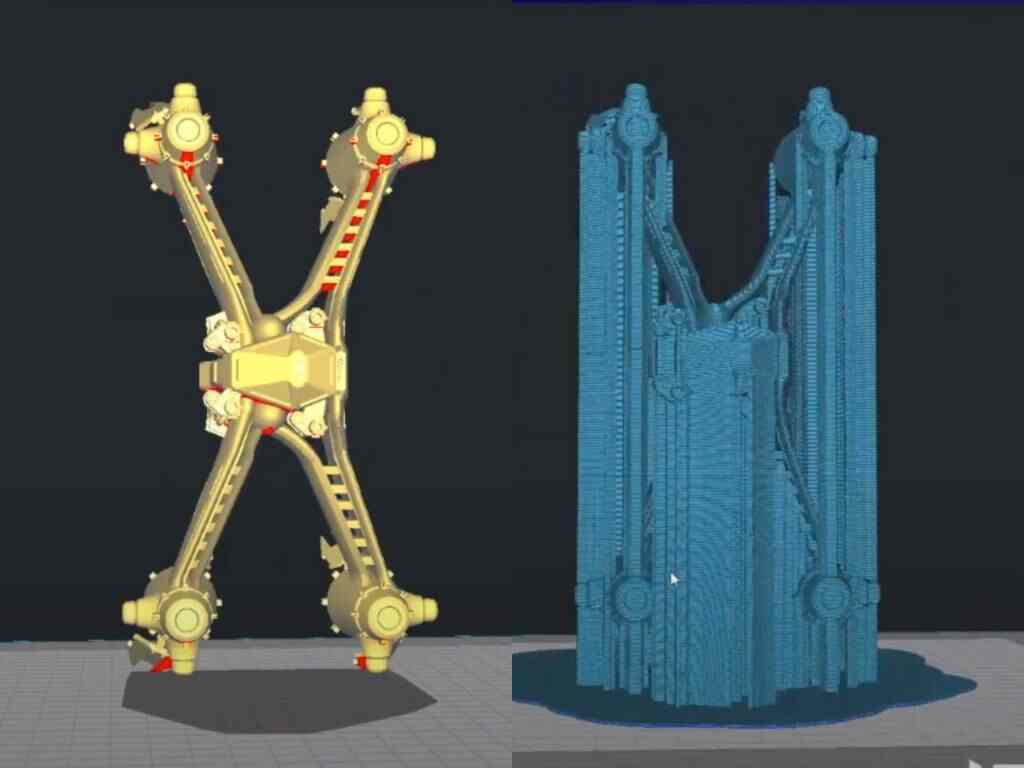
Consider Functional Loads
For functional parts, factor in the forces and loads the part will undergo when orienting the geometry. Optimize strength by aligning continuous print layers along the main load direction.
Optimize Surface Finish Needs
Consider aesthetic and finish requirements when orienting a part. Proper orientation can minimize or accentuate layer lines, creating a smooth, uniform appearance. Surfaces with critical tolerances may print better facing upward rather than sideways.
Some orientations will leave more visible marks after support removal. Place any remnants strategically in less visible areas if possible.
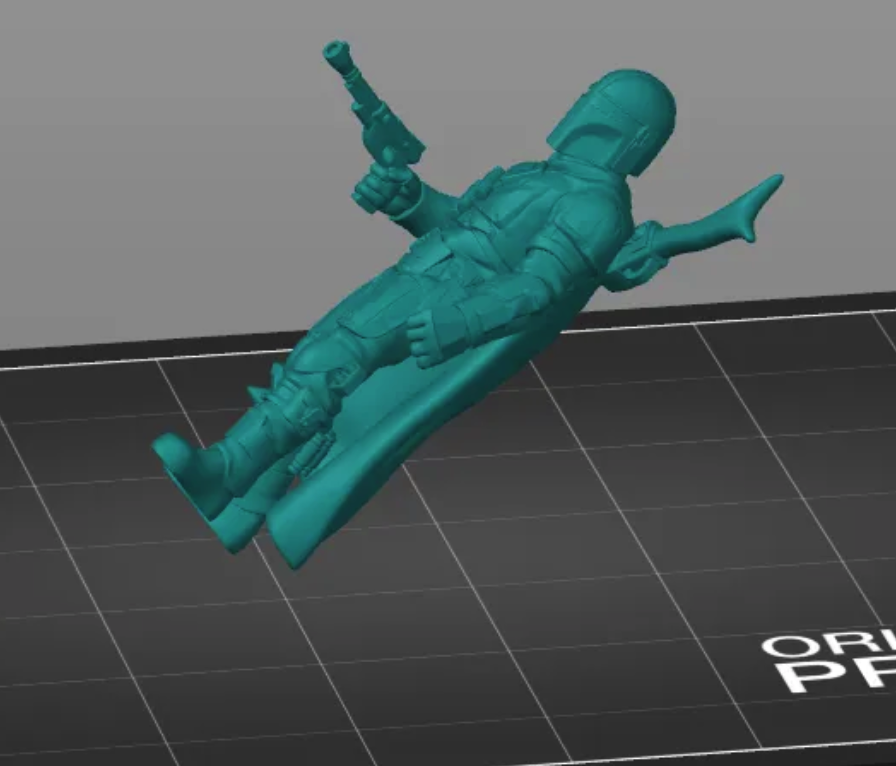
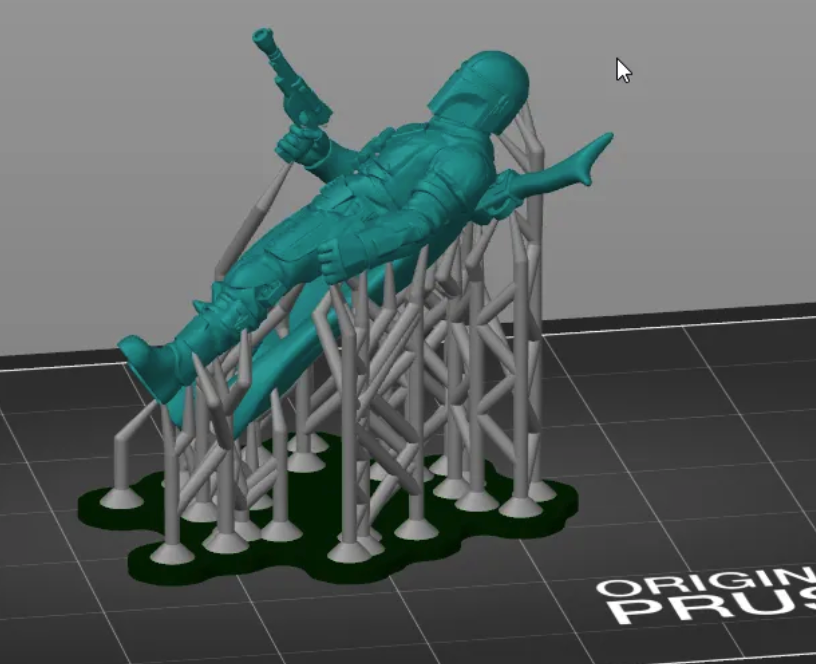
Identifying Areas Requiring Supports
In additive manufacturing, support structures provide critical scaffolding to overhanging geometries that cannot print successfully on their own. Strategic placement of supports is enabled through established guidelines.
The “45° Rule”
This guideline states that angled overhangs exceeding approximately 45 degrees from vertical will likely need support material for structural integrity as they print.
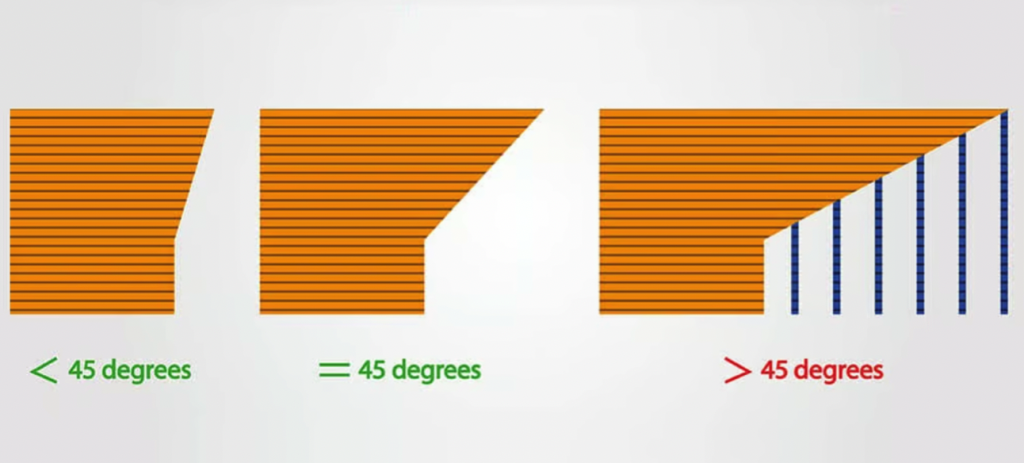
At shallow angles under 45 degrees, the overhanging material can typically bridge itself and print successfully without collapsing or deforming due to gravity.
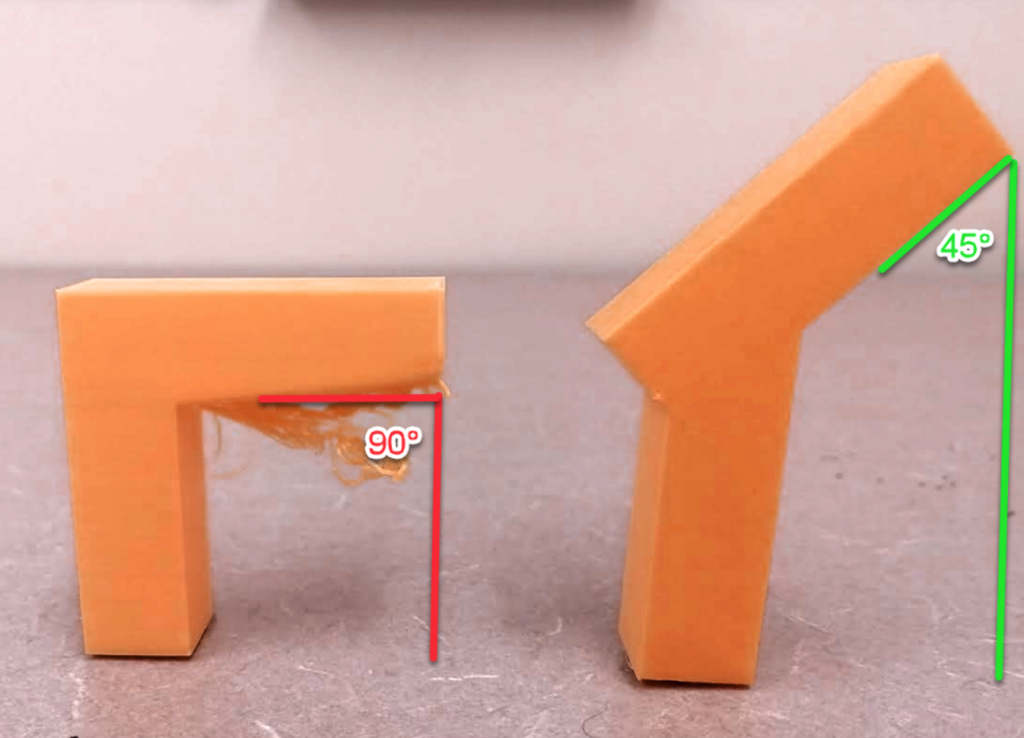
However, as the overhang angle surpasses 45 degrees, the prone material becomes increasingly unstable and unsupported. This increases the likelihood of print defects like warping or drooping without supports.
Therefore, the general rule serves as a useful cutoff test when assessing a model’s geometry. Overhangs up to around 45 degrees may print without issues, while greater angles should be evaluated for support requirements based on the specific overhang length and model material properties.
The “YHT Principle”
This principle utilizes the angled shapes of the letters Y, H, and T as handy visual proxies to demonstrate varying support needs.
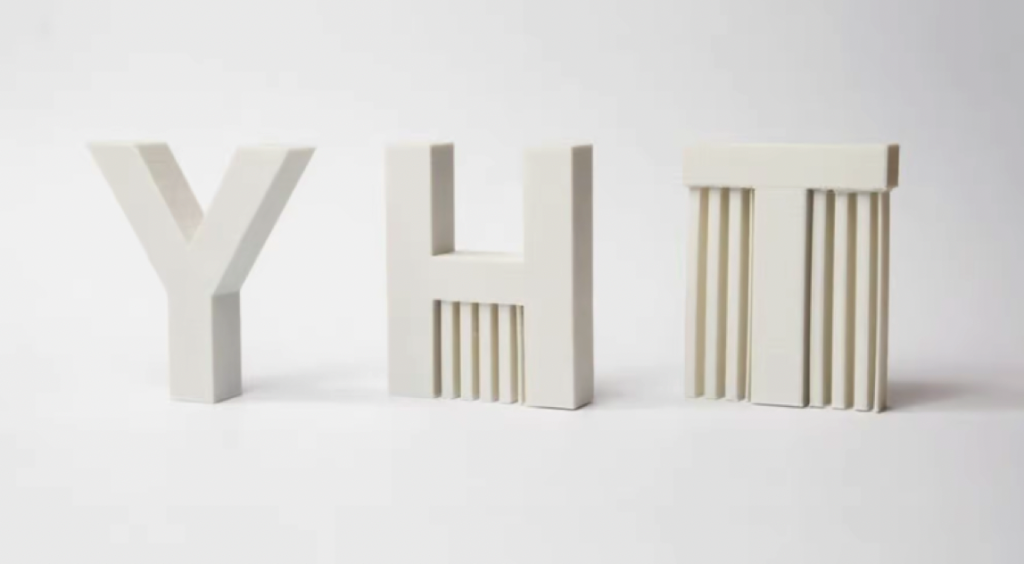
The Y’s angled arms at 45 degrees represent overhangs that may potentially print successfully without supports, depending on length.
The H illustrates a bridging scenario - if the vertical elements are close (within 5mm), the bridge may print without supports. Wider spacing would likely require bridging support.
The T shape exemplifies a situation where supports would be required, as its 90 degree overhangs have no underlying structure.
By visualizing these letter shapes and angles, the principle provides a simple framework for assessing support requirements based on angles and bridges.
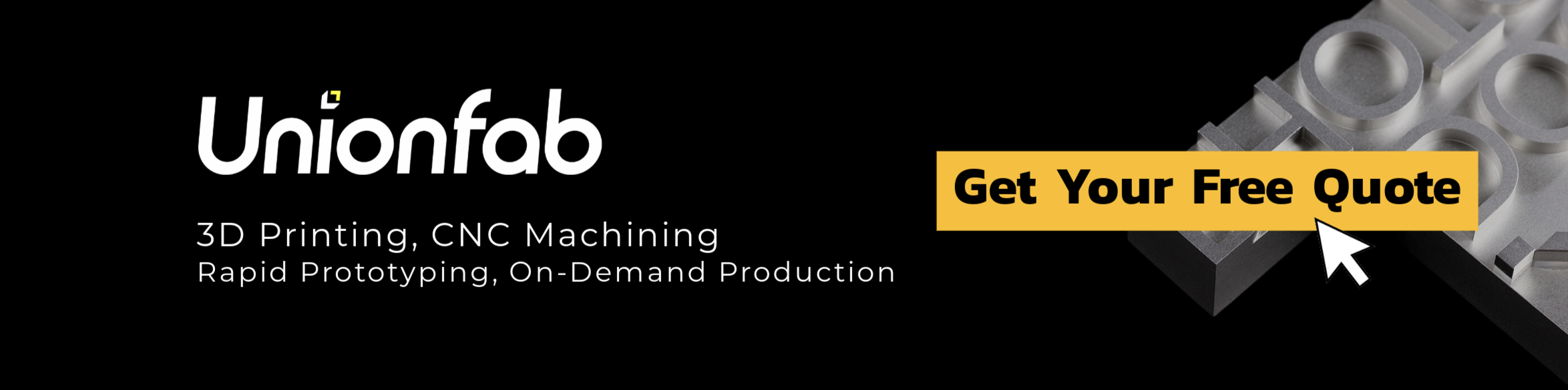
Tree Supports vs. Fence Supports
When it comes to support structures in 3D printing, two prevalent types—tree supports and fence supports—offer distinct attributes that cater to specific requirements.
Tree Supports: Branching Out for Versatility
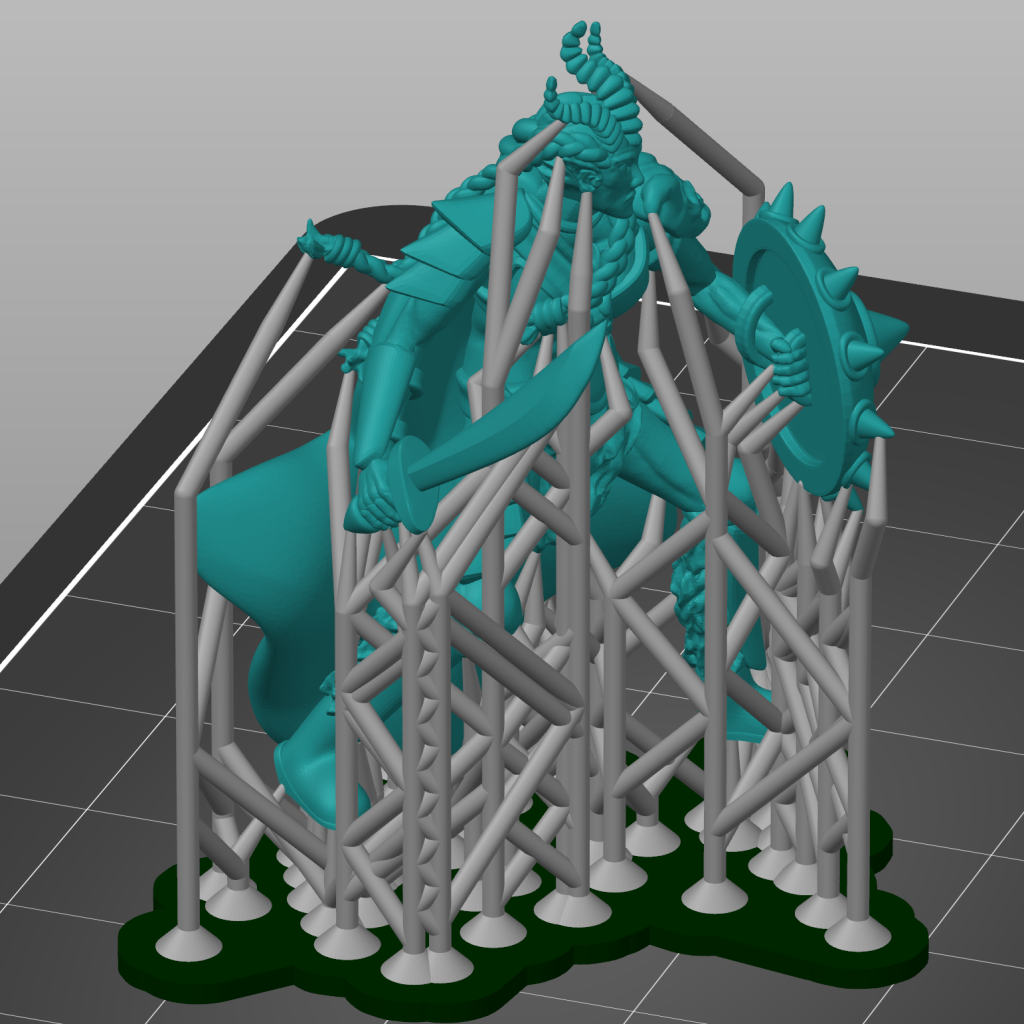
Tree supports, as their name implies, exhibit a branching structure that extends to offer support over distances.
Applications: These supports excel in scenarios where complex and irregular geometries demand support that can span considerable gaps.
Design Speed: Tree supports are notable for their swiftness in design implementation, making them well-suited for iterative design processes.
Versatility: Their inherent branching structure lends them versatility, allowing them to adapt to various geometries with ease.
Fence Supports: Building Walls of Durability
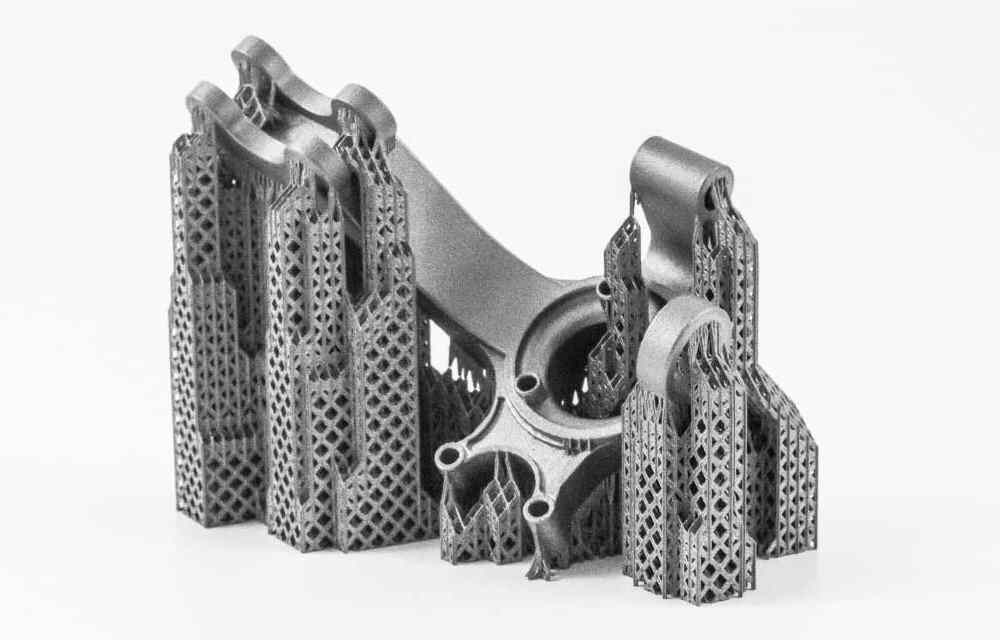
Fence supports, resembling walls, are erected perpendicular to a part's surface, creating a lattice-like structure.
Applications: Fence supports excel in situations where durability, stability, and ease of removal are essential, particularly for cosmetic parts or high-volume production.
Durability: The wall-like structure of fence supports ensures robustness, contributing to print stability during the additive manufacturing process.
Ease of Removal: Fence supports offer a streamlined removal process, reducing post-processing efforts and minimizing the risk of damaging the part.
Tree Supports vs. Fence supports: Pros and Cons
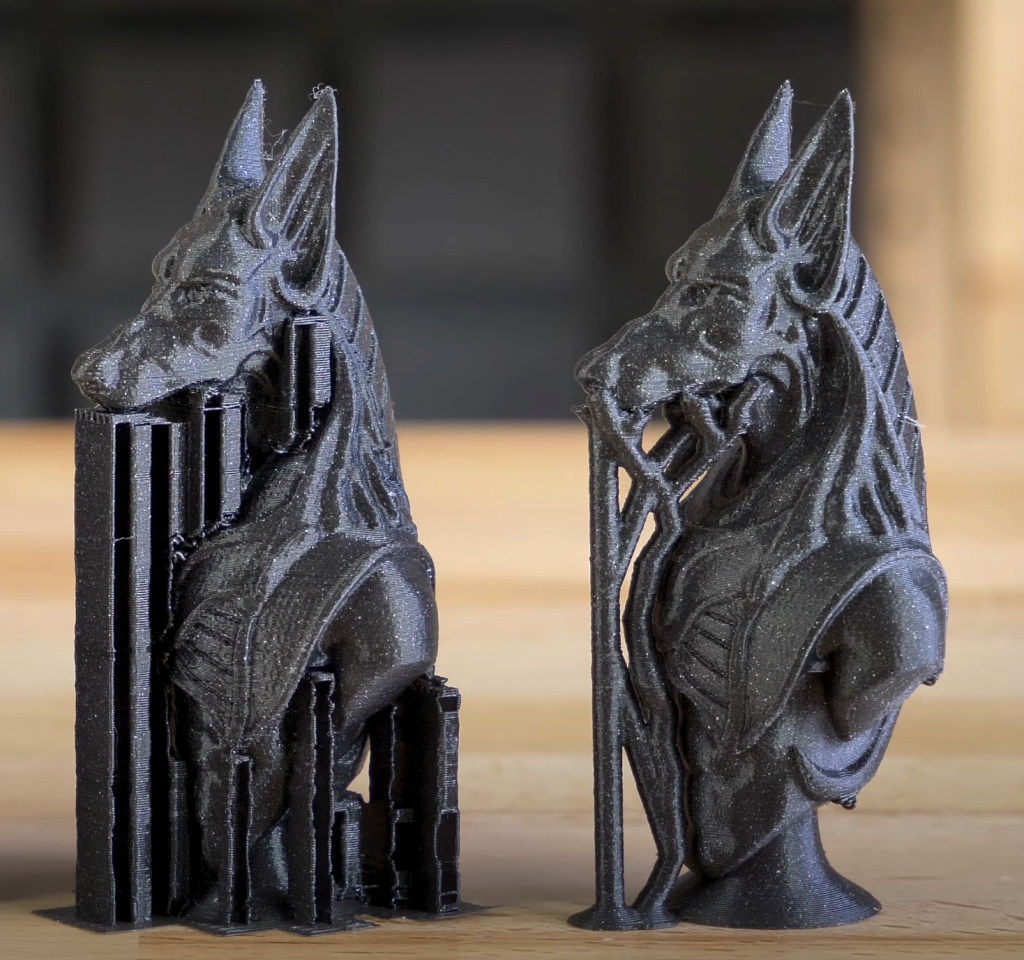
Tree Supports Pros
Versatile design suited for various geometries.
Quick design integration for complex shapes.
Efficient material usage enhances cost-effectiveness.
Tree Supports Cons
Can leave more visible support marks on the finished part.
May require more material due to branching structure.
Fence Supports Pros
Durability ensures stable printing, particularly in high-volume production.
Streamlined removal process minimizes post-processing challenges.
Ideal for parts where aesthetics and durability are paramount.
Fence Supports Cons
Less suitable for intricate designs requiring extended overhangs.
Design complexity may limit their versatility.
Elevated material cost compared to other support types.
Selecting the Right Support
The choice between tree supports and fence supports depends on the specific demands of the print, encompassing geometry, aesthetics, ease of removal, and intended application.
Preview support strategies in slicer software and pick approaches that require less material and will be simplest to detach after printing based on model geometry.
Utilizing Soluble or Breakaway Supports
In cases where intricate and complex geometries make manual support removal difficult or risk damaging the print, soluble or breakaway support materials offer a solution.
Soluble PVA or HIPS supports can eliminate manual removal when the model material is compatible. Support structures print encapsulated within the model and dissolve away in water or solvents. No marks remain.
When model properties prohibit soluble supports, breakaway supports have weak connecting points designed to snap off easily after printing. Minimal residue remains for cleanup.
Software Tools and Capabilities
Auto Orientation and Support Generation
Programs like Polydevs, PrusaSlicer, and Ultimaker Cura provide auto orientation and support generation features. These use algorithms to strategically position parts and place supports minimizing material use.
Polydevs is a powerful tool that provides the features for viewing, editing, repairing, and analyzing the model. You can adjust the model to an optimal orientation by setting these parameters, which will facilitate later support operations:
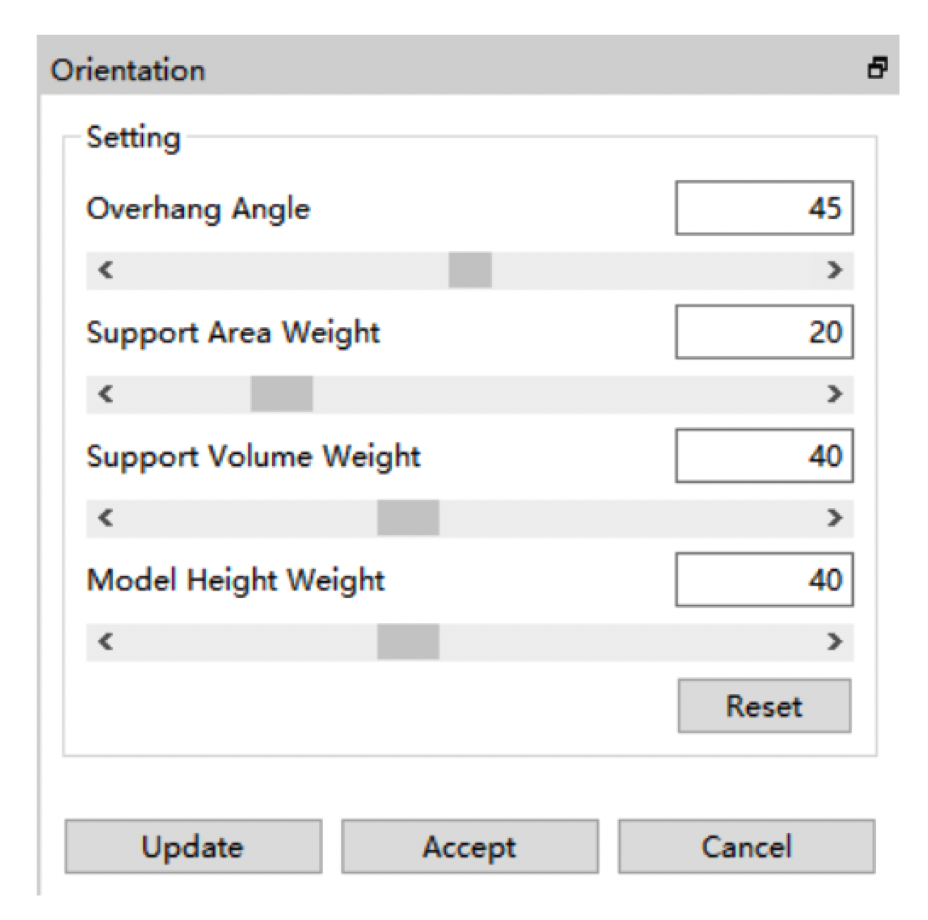
Polydevs Orientation Setting
Surface quality - Keeps overhang angel at 45% to keep visible details for critical surface
Support area - The greater the weight, the smaller the support area.
Support volume - The greater the weight, the smaller the support volume.
Model Height - Adjust the Z height of the model. The greater the weight, the lower the model, and the more conducive to achieving support.
Polydevs offer three types of supports to be automatically generated based on the needs of support strength:
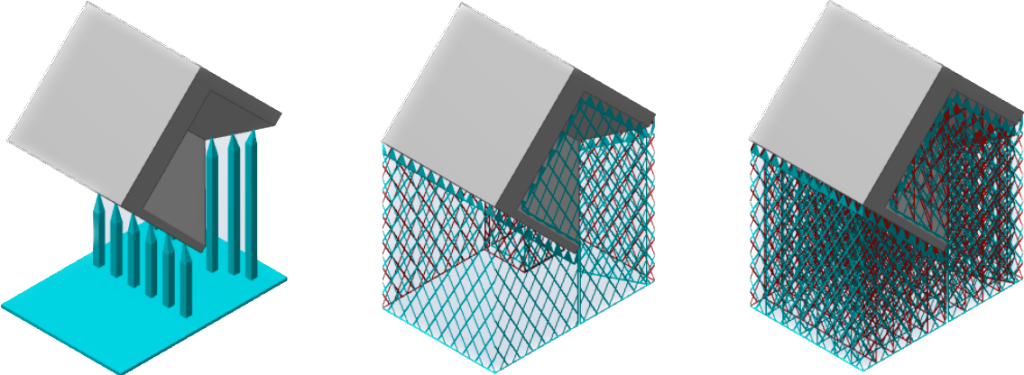
Customizing Supports
While auto-generation is beneficial, further customization is often needed for optimal orientation and support per model. Tools enable manually adjusting position, support types, density and other settings.
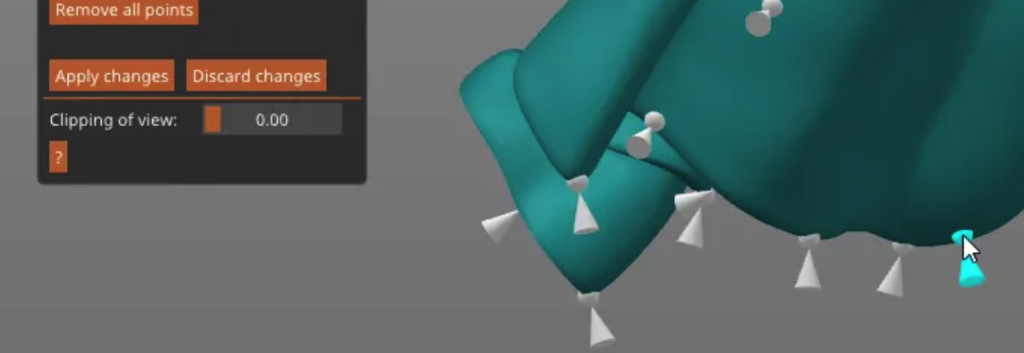
Comparing Options
Software can compare factors like material use, print time, and cost for different orientations and support settings. This facilitates choosing the most efficient options.
For example, Ultimaker Cura 3.0 introduce new features that reduce print time and material consumption. The “Recommended” mode arrives with pre-configured settings that aim to save print time, material usage, and material costs.
Key Takeaways
As we conclude our exploration of optimizing part orientation and support structures in 3D printing, let’s recap the essential insights garnered from this discussion.
Striving for Print Excellence
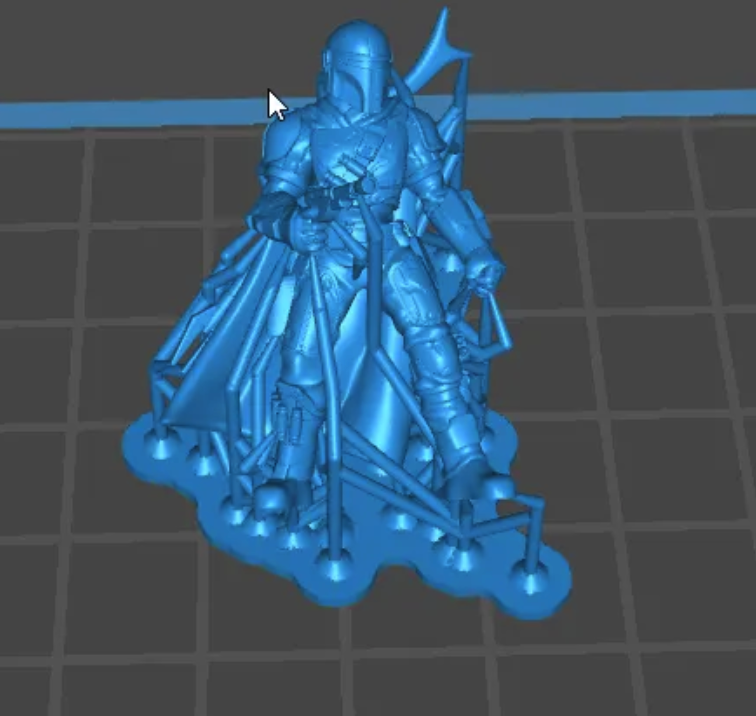
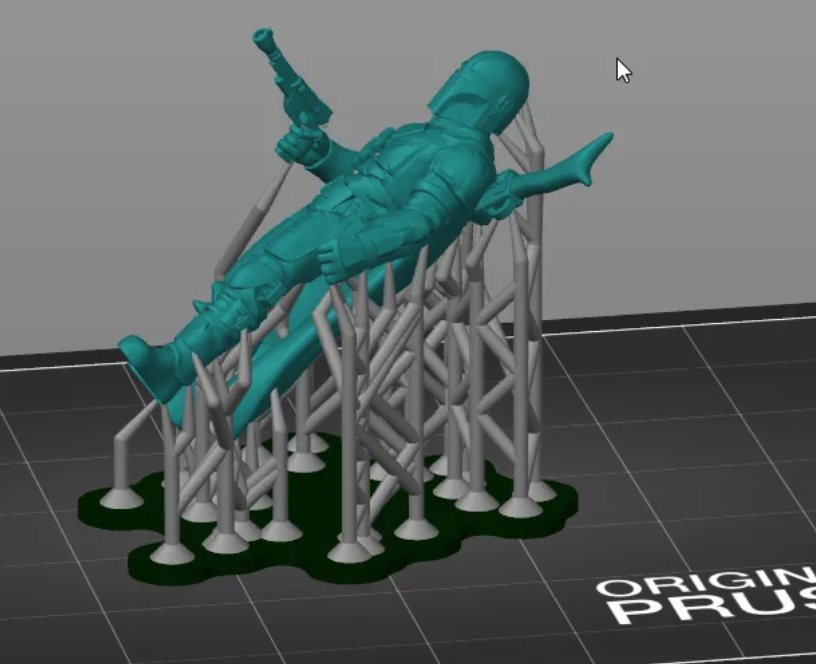
Part orientation and support structure design are critical factors that profoundly influence the success of 3D printing projects.
Support structures provide stability for overhangs, complex geometries, and delicate features, enhancing print quality.
For enhanced surface quality, position the part at a 45° angle (see the images above). This choice may extend printing time and cost, yet it promises to elevate the overall print quality.
Guiding Principles for Success
The “45° rule” serves as a foundational guideline, indicating that overhangs exceeding 45 degrees from vertical generally require support.
The “YHT principle” offers a visual framework to determine support necessity based on the overhang angles of Y, H, and T shapes.
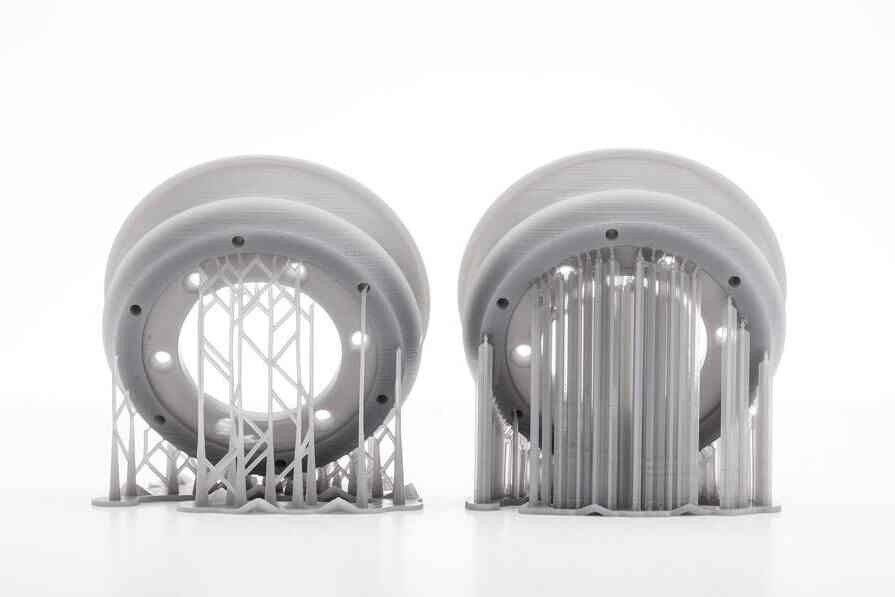
Embracing Excellence with Unionfab
In your journey to harness the full potential of additive manufacturing, consider partnering with Unionfab.
With our profound expertise, Unionfab not only offers cutting-edge 3D printing technology but also extends their guidance to optimize part orientation and support structures.
We invite you to experience the Unionfab difference firsthand. Embrace the challenge, innovate with intention, and let your creations bear the hallmark of Unionfab’s dedication to excellence.
Get an instant quote and start your printing journey with Unionfab!
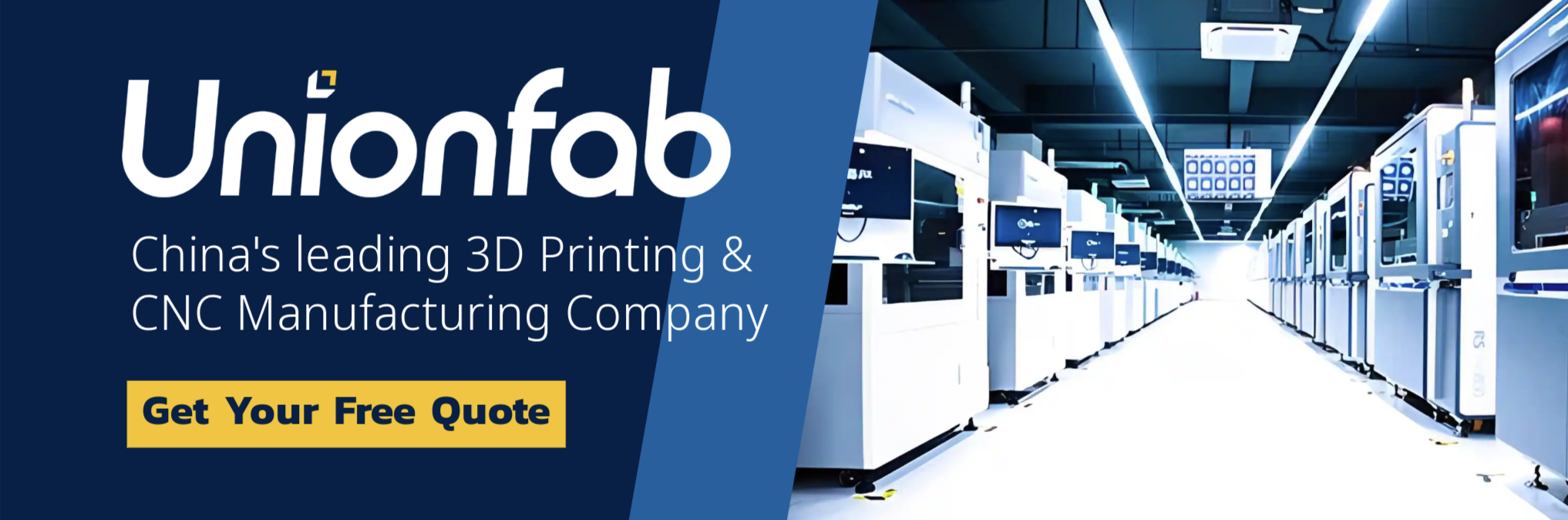