CNC Machining: A Complete Guide
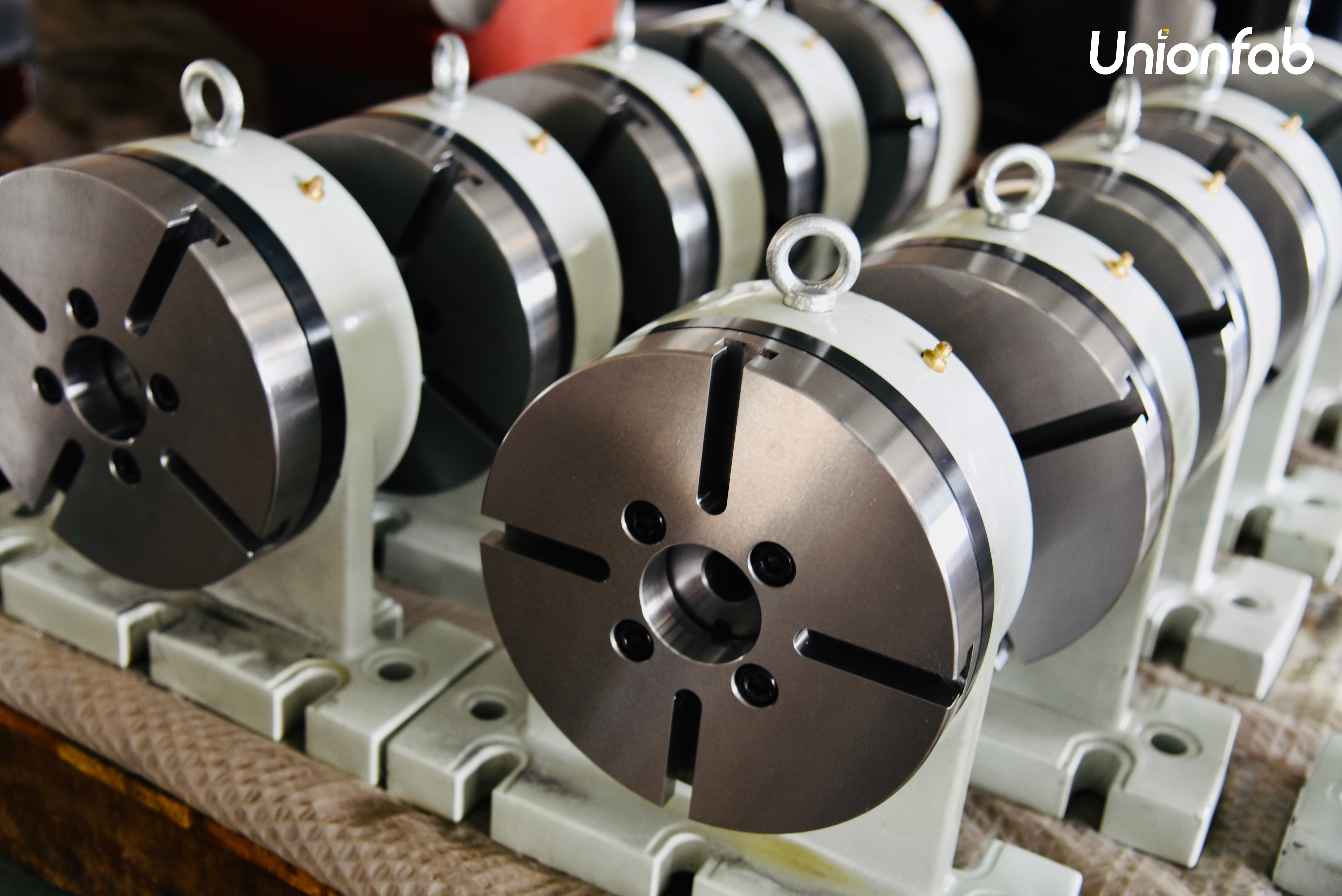
What is CNC Machining?
CNC machining is a manufacturing process that uses computer numerical control (CNC) to automate and control machine tools like milling machines, lathes, routers, grinders and lasers.
In contrast to additive manufacturing which builds up parts layer-by-layer or injection molding that involves deforming materials to achieve the desired form, CNC machining carves away material to form complex geometries.
Overview of the CNC Machining Process
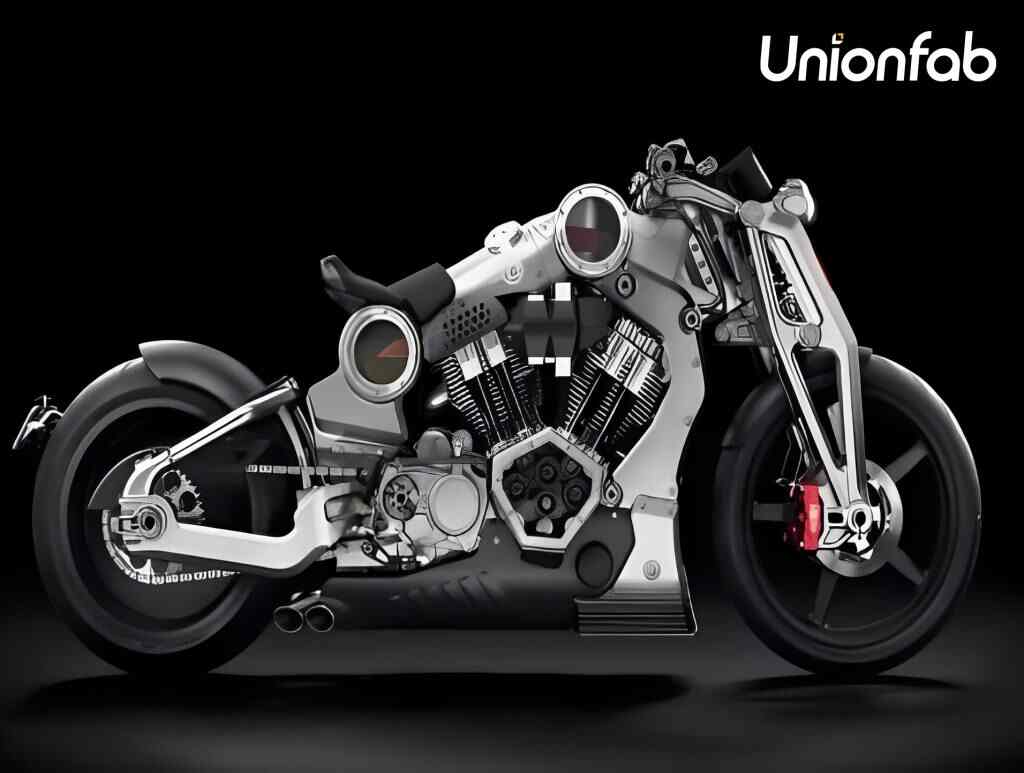
CNC machining involves several key steps to take a design from concept to finished part:
Step 1: Creating a CAD model
The first step is to create a 3D model of the part geometry using CAD (computer-aided design) software. The CAD file precisely defines the part's shapes, dimensions, and tolerances.
Popular CAD programs used for CNC machining include SolidWorks, Autodesk Inventor, and Solid Edge.
Step 2: Converting to G-code
Next, CAM (computer-aided manufacturing) software is used to analyze the CAD model and generate toolpaths. The toolpaths are then converted to G-code, the language that CNC machines understand.
Step 3: Setting up the CNC machine
Before machining, the necessary cutting tools, workholding fixtures, and material stock are set up on the CNC machine. The G-code program is loaded and relevant parameters are adjusted in the machine's control interface.
Step 4: Machining the part
During machining, the CNC machine follows the programmed instructions to automatically cut away material and create the desired part geometry.
Step 5: Inspecting and refining
Once machining is complete, the part is inspected to ensure dimensional accuracy, surface finish, and overall quality meets specifications.
Post-processing like deburring, polishing, and coating may also be applied to achieve the final part finish.
Fundamentals of CNC Machining
Explanation of Computer Numerical Control (CNC)
Computer Numerical Control (CNC) is the automated control technology central to CNC machining. It enables precise programmed control of machining tools like mills, lathes and routers.
CNC works by converting CAD design data into a language that machine tools can interpret and execute. This is done through a program of coded alphanumeric instructions known as G-code.
Role of CAD and CAM
CAD (Computer-Aided Design) software creates the 3D model containing the part geometry, dimensions and tolerances. CAM (Computer-Aided Manufacturing) software then converts this model into machining instructions (G-code) to physically cut the part on the CNC machine.
There are several software packages that combine CAD and CAM functionality into one integrated system:
Autodesk Fusion 360 - Provides both CAD modeling and CAM programming in one platform. Widely used for CNC machining applications.
SolidWorks CAM - Seamlessly integrates CAM and simulation directly within the SolidWorks CAD environment.
Mastercam - Offers 2D and 3D CAD tools in addition to extensive CAM capabilities for programming CNC mills, lathes, routers, lasers and more.
FreeCAD - An open source, free CAD/CAM package with integrated tools for design and machining operations.
Overview of G-code programming
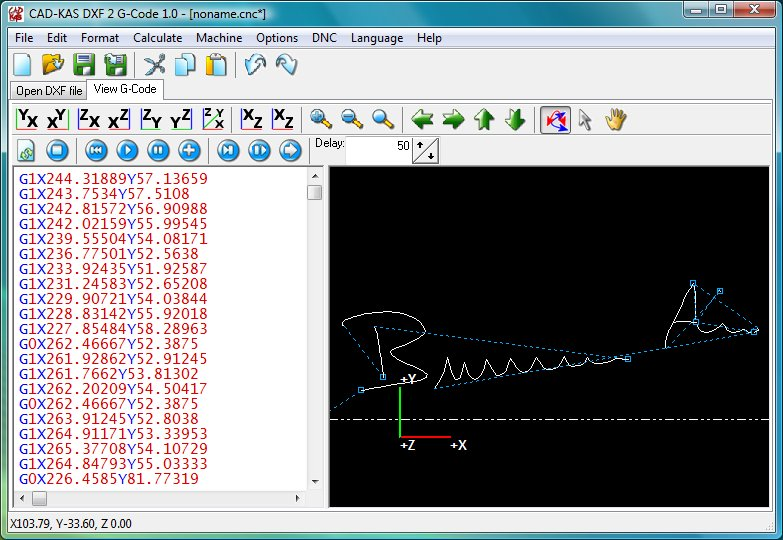
G-code is the numerical control programming language understood by CNC machines. A G-code program specifies basic functions like:
Controlling axes motions and feed rates
Turning cutting tools and spindles on/off
Setting cutting speeds and depths
Applying coolant
Types of CNC Machines
CNC Milling Machines
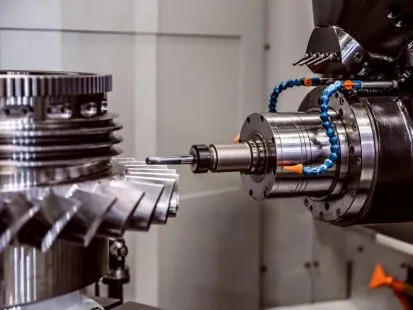
CNC milling machines use rotating cutters to remove material from a still workpiece to make parts with complex shapes and features.
CNC Turning Machines
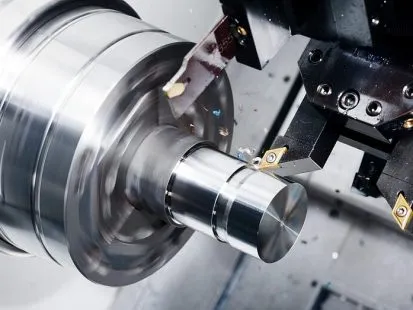
CNC lathes hold the spinning workpiece against a fixed cutting tool to cut cylindrical and round symmetrical parts.
Comparison to Milling:
In turning, the workpiece rotates, and the cutting tool moves along the length of the workpiece to remove material. While in milling, the cutting tool rotates, and the workpiece remains stationary.
Turning is ideal for efficiently machining external and internal cylindrical, cone-shaped, and recessed features. Milling allows more flexibility in making complex block-like geometries.
CNC Routers
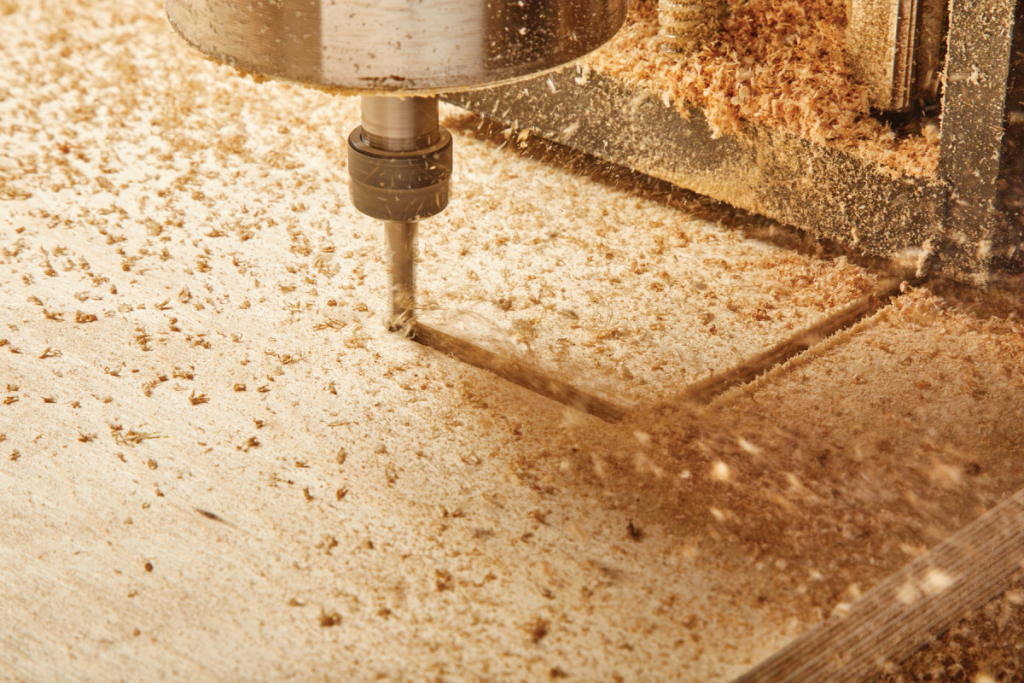
CNC routers use a spinning router bit to cut shapes, slots and edges into flat sheet materials like wood, plastic, and light metals.
Applications: Commonly used for sign making, engraving, carpentry, machining furniture parts, and similar work on flat stock materials.
3-Axis, 4-Axis, 5-Axis and More
Multi-Axis CNC Milling Machines
3-Axis Milling: Traditional 3-axis milling machines move along the X, Y, and Z axes. They are well-suited for producing simple shapes and flat surfaces.
4-Axis Milling: Adding a fourth rotational axis (often referred to as the A-axis) enables the machine to tilt the workpiece or the cutting tool. This configuration is particularly useful for creating inclined surfaces, tapered features, and complex contours.
5-Axis Milling: The addition of a fifth axis (often referred to as the B-axis or rotary axis) introduces even greater flexibility. This enables the machine to rotate the workpiece or the cutting tool around multiple angles, allowing for the machining of intricate, multi-sided parts without repositioning the workpiece. 5-axis machines are especially valuable for producing aerospace components, molds, and complex sculptures.
Multi-Axis CNC Turning Machines
3-Axis Turning: Traditional 3-axis turning machines move along the longitudinal (X), axial (Z), and sometimes cross-slide (Y) axes. They are suitable for creating cylindrical shapes, threads, and simple contours.
4-Axis Turning: The addition of a fourth axis, often a rotating turret (C-axis), enhances the machine's capabilities. This axis allows for indexing the workpiece, enabling the machining of features at various angles. 4-axis turning is commonly used for producing complex geometries and features such as holes on non-linear surfaces.
Multi-Turret Turning: Some advanced turning machines feature multiple turrets, each with its own set of tools. This configuration allows for simultaneous machining of multiple features and reduces cycle times.
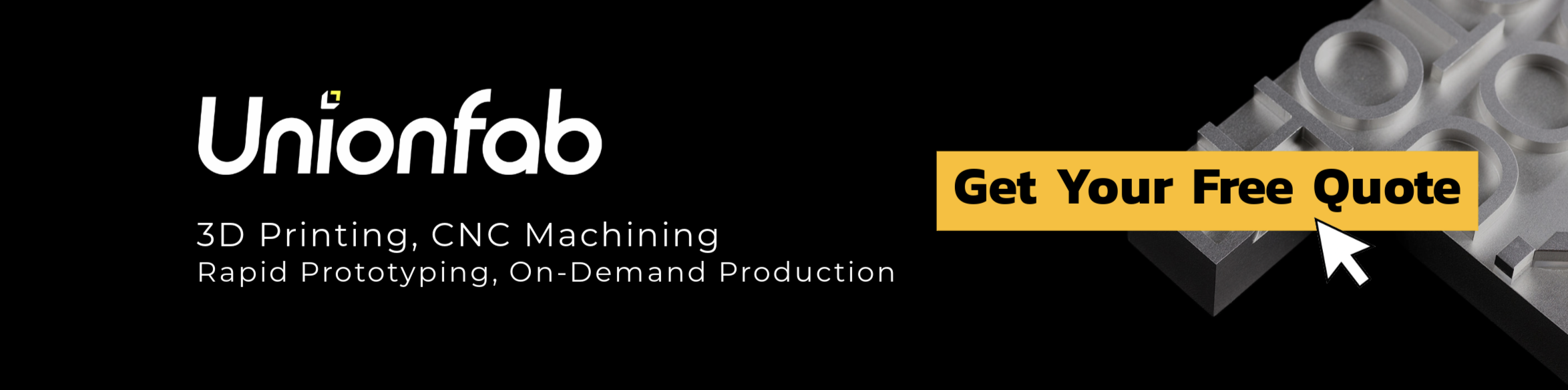
Multi-Axis CNC Routers
3-Axis Routing: Traditional 3-axis routers move along the X, Y, and Z axes. They excel at cutting flat surfaces, contours, and simple 3D shapes.
4-Axis Routing: Adding a fourth rotational axis (often referred to as the A-axis) enables the router to tilt the spindle or the workpiece. This configuration is valuable for carving intricate designs on curved surfaces and producing complex 3D carvings.
5-Axis Routing: Incorporating a fifth axis (often referred to as the B-axis or rotary axis) introduces even more versatility. This axis allows for the rotation of the spindle or workpiece to achieve complex angles, enabling the creation of intricate and sculptural designs from multiple directions.
CNC Machining: Advantages and Challenges
Advantages of CNC Machining
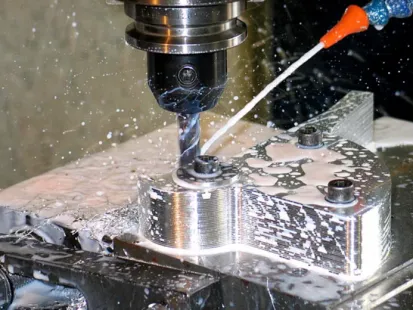
Precision and Tight Tolerances: Achieve +/- 0.001″ to 0.005″ tolerances for precise outcomes.
Continuous Operation: Machines run non-stop, meeting demands even 24/7.
Customization and One-Off Production: Craft custom, legacy parts effectively.
Steady Supply for High Demand: Ideal for industries needing consistent high-volume production.
Material Versatility: Over 50 materials, including metals and plastics, can be machined.
Excellent Physical Properties: CNC parts inherit superior bulk material qualities.
Challenges of CNC Machining
Complex Geometry Costs: Intricate shapes can raise machining costs due to tool access limitations.
Startup Investment: High initial costs for skilled personnel and setup, but advantageous for larger runs.
Wire EDM Limitations: Slower, more expensive, and restricted to electrically conductive materials.
CNC Machining vs. 3D Printing
Process
CNC machining is a subtractive manufacturing process. Material is removed from a solid block to create the desired shape.
3D printing is an additive manufacturing process where material is layered to build the final object.
Accuracy and Tolerances
CNC machining offers high precision and tight tolerances, making it suitable for applications where dimensional accuracy is critical.
While improving, 3D printing may not achieve the same precision and tolerances as CNC machining.
Materials
CNC machining works with a wide range of materials, including metals, plastics, and composites. Material properties remain consistent with the bulk material.
3D printing offers a growing selection of materials, including plastics, metals, ceramics, and even biomaterials, although its range remains more constrained compared to CNC machining. Material properties may vary from traditional counterparts.
Strength and Durability
CNC machined parts exhibit excellent mechanical properties, often with higher strength and durability compared to 3D printed parts.
Surface Finish
CNC machining produces smooth surface finishes, making it suitable for parts with aesthetic requirements.
Surface finish of 3D printed parts is generally rougher, requiring post-processing for smoother finishes.
Complexity
3D printing excels at creating intricate, complex geometries that may be challenging or impossible to achieve with CNC machining.
Multi-axis CNC (4-axis or 5-axis) gets closer to 3D printing in terms of the complexity of geometries it can machine, but accessibility for interior features is still limited.
Production Volume
CNC is ideal for low to high production volumes. Well-suited for industries requiring large quantities of identical parts.
3D printing is suited for prototyping, customization, and small production runs.
Industry Applications
CNC machined parts are suitable for a wide variety of industries, including automotive, aerospace, electronics, industrial, robotics, construction, and agriculture.
CNC Machining for Industries
Aerospace Industry: CNC machining plays a vital role in manufacturing aircraft, satellites, and other aerospace vehicles, including engine parts and fuselage components.
Automotive Manufacturing: CNC machining is utilized for producing automotive parts, frames, body panels, and more.
Medical Field: CNC machining is involved in manufacturing medical equipment like scaffolds and artificial joints.
Industrial Sector: CNC machining contributes to the production of diverse industrial parts such as machine tools and industrial robots.
Metal Products: CNC machining is essential in creating metal products like cutting tools and molds.
Publishing Industry: CNC processing is employed in producing printing templates, such as printing boards.
Transportation: CNC processing is used to manufacture transportation equipment like trains and ships.
CNC Machining Applications
Rapid Tooling
Using CNC machining to cut a wide variety of fully dense materials, such as aluminum 5052 and stainless steel, ensures that the resulting fixtures or molds will be strong and durable.
Rapid Prototyping
We offer a range of affordable metal alloys (like Aluminum 6061) and plastics (like acetal and ABS). By leveraging the expertise of our skilled machinists, we can ensure the precise and accurate manufacturing of prototypes.
End-Use Production
The combination of performance-enhancing finishes, precision tolerances as low as +/- 0.001”, and a wide range of certifiable material options makes CNC machining an exceptional technology for producing end-use parts.
CNC Materials
CNC machining can process almost any machinable material from metals and plastics to composites and exotics.
At Unionfab, our CNC services encompass an extensive array of materials, each tailored to specific needs. We provide custom CNC quotes for a diverse range of options, including:
Metals
Aluminum alloys
Steel (powdered, stainless)
Titanium
Exotic alloys (maraging steel)
Plastics
Engineering thermoplastics (PEEK, nylon)
Common plastics (ABS, PLA)
Synthetic materials
Glass filled nylon
Carbon filled nylon
Custom Online CNC Machining Services
Get instant quotes for prototypes and production parts using our online CNC service. We are ISO 9001:2015, ISO 13485, and AS9100D certified.
Our CNC Machining Services
Rapid prototyping
Low volume batch production
High volume manufacturing
Quick turnaround times
Competitive pricing
Engineering design support
Why Choose Us?
Instant online quotes from CAD models
Vetted network of qualified CNC suppliers
ISO certified quality management system
Precision machining in plastics and metals
Streamlined ordering and fast delivery
We help bring products to market quickly through on-demand CNC services tailored to your application requirements.
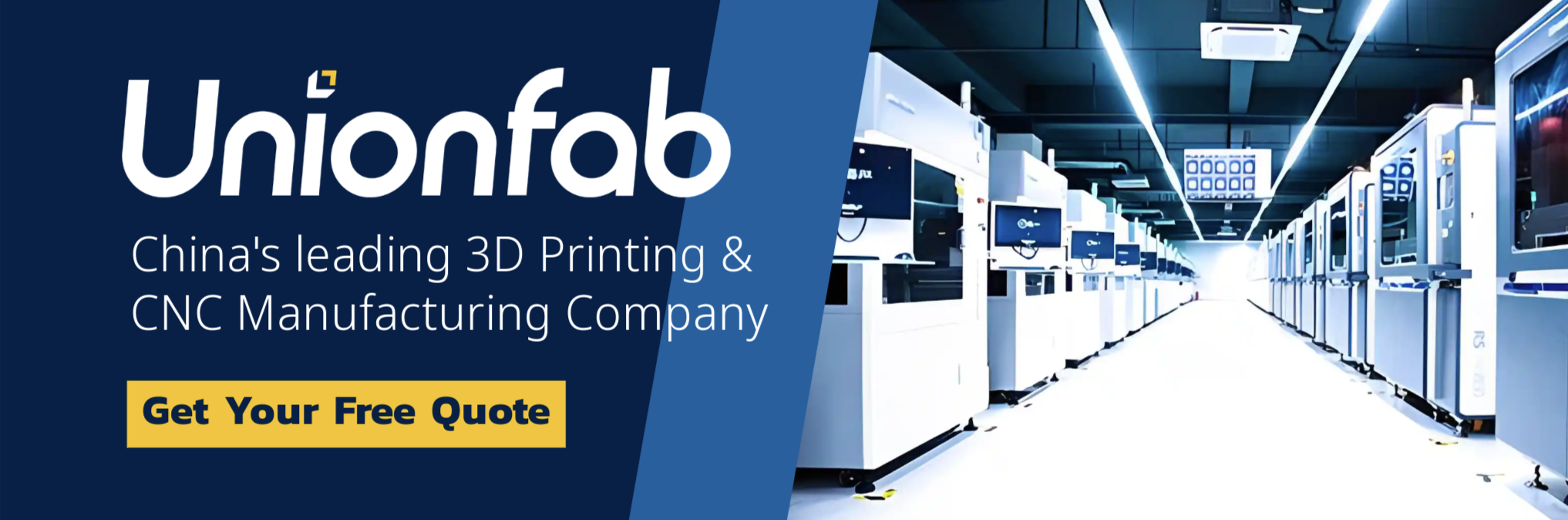
FAQs
What is the turnaround time for CNC machining?
The turnaround time for CNC machined parts largely depends on factors such as the unit number, size, and complexity. In some cases, manufacturers can deliver CNC machined parts within a day. With shipping and delivery, deadlines can be met within a week.
What are some common plastic materials used for CNC machining?
Here are some examples:
ABS - High strength, impact resistant engineering plastic. Durable with dimensional stability.
Acrylic - Optically clear plastic with high wear resistance.
Garolite (G10, G11) - Fiberglass reinforced plastic noted for strength and low moisture absorption.
Nylon - Strong, rigid engineering plastic with thermal stability.
PEEK - Temperature resistant high-performance plastic substitute for metals.
Polypropylene - Chemically inert plastic with excellent electrical properties.
PTFE (Teflon) - Chemically inert plastic stable at extreme temperatures.
PVC - Highly chemical resistant plastic often used for insulation.
ULTEM - High heat thermoplastic with excellent dielectric strength.
What types of CNC machining finishes are provided by Unionfab?
As-Machined - This is the standard finish with a surface finish of 125 Ra or better. Fastest option, sharp edges may remain. Additional finishing options can be specified when obtaining a quote.
Bead Blasting - Gives a smooth, matte surface appearance.
Tumbling - Removes burrs and sharp edges, eliminates machine marks.
Anodizing (Type II, Type III) - Corrosion resistant, can be dyed different colors.
Titanium Anodize - Enhances fatigue strength and wear resistance.
PTFE Impregnated Hard Anodize - Self-lubricating, dry contact surface. Extends product lifespan.
Chem Film - Corrosion protection with conductivity. Adds minimal thickness.
Passivation - Enhances corrosion resistance of steels. Extremely thin layer.
Powder Coating - Wear and corrosion resistant colored finish.
Electropolishing - Smooths surface and increases brightness. Material removal range is approximately 0.0001” - 0.0025”
Electroless Nickel - Uniform nickel coating resists corrosion and wear.
Silver Plating - Excellent conductivity and solderability but tarnishes.
Gold Plating - Corrosion and tarnish resistant with good solderability.
Zinc Plating - Evenly coats irregular surfaces preventing corrosion.