Metal 3D Printing Guide: Basics, Costs & Companies
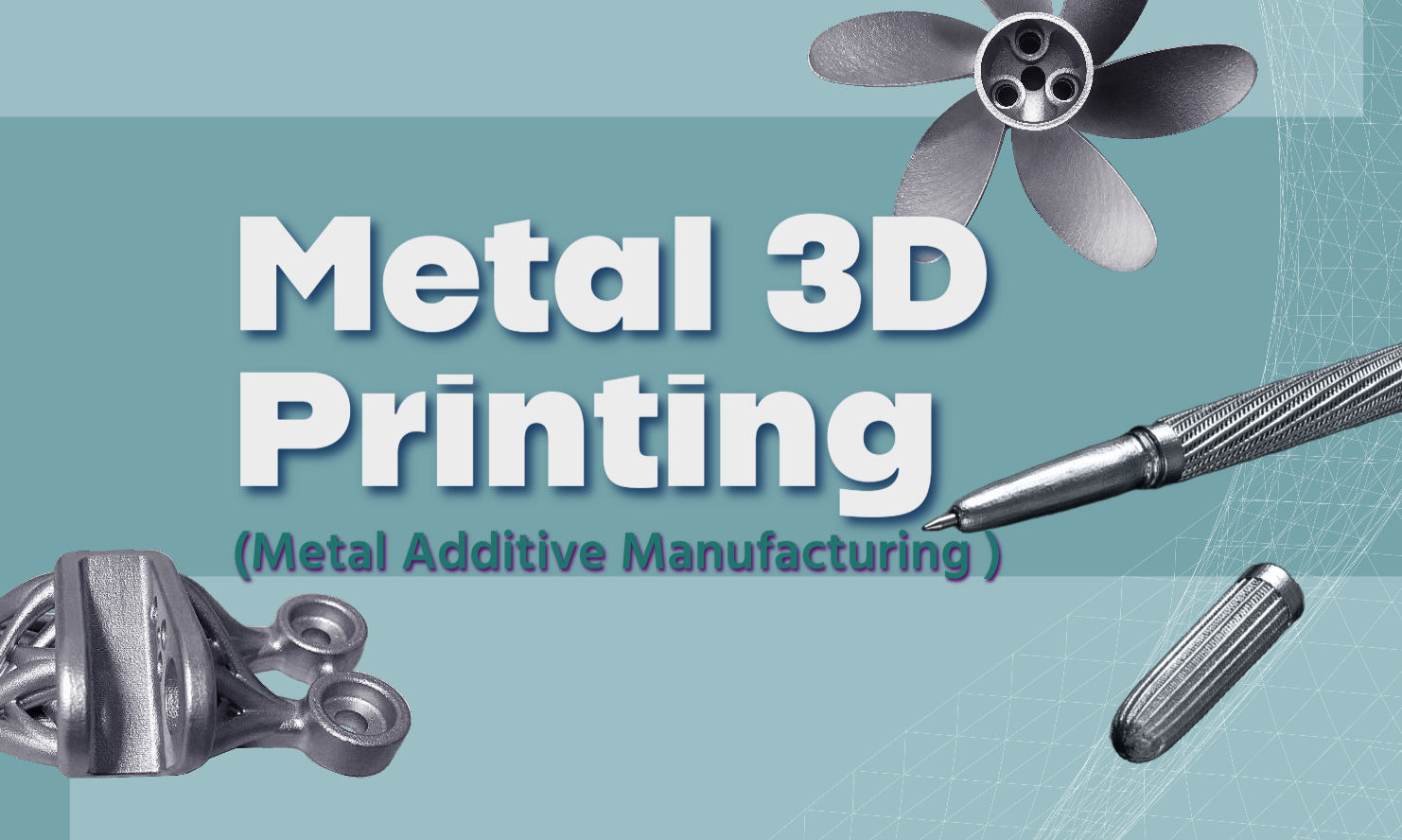
Learn metal 3D printing essentials: technologies, materials, costs, and applications as well as how to choose the right method and the most suitable service provider.
Introduction
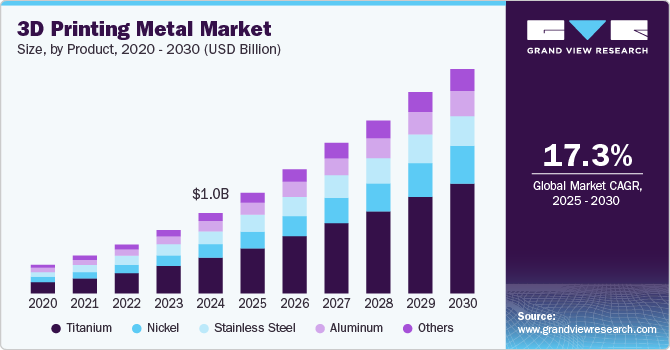
Source: Grand View Research
According to Grand View Research, the global 3D printing metal market is surging — valued at $1.0 billion in 2024 and projected to grow at 17.3% annually through 2030. This explosive growth stems from rapid innovations in printing technologies and the shift toward digital-first manufacturing.
But what exactly fuels this revolution? In this guide, we strip away the complexity:
How metal 3D printing works?
Key materials, costs, and real-world applications;
How it stacks up against CNC machining and casting;
Major players redefining the industry.
What is Metal 3D Printing?
Metal 3D printing, or metal additive manufacturing, creates high-strength, fully dense metal components layer by layer, directly from digital 3D models.
Unlike traditional manufacturing methods, this advanced technology enables complex geometries—including hollow structures, organic shapes, and intricate internal channels—that are impossible to machine or cast.
Watch the step-by-step video below to see how does metal 3d printing work.
Types of Metal 3D Printing Technologies
Evolution of Metal 3D Printing Technologies
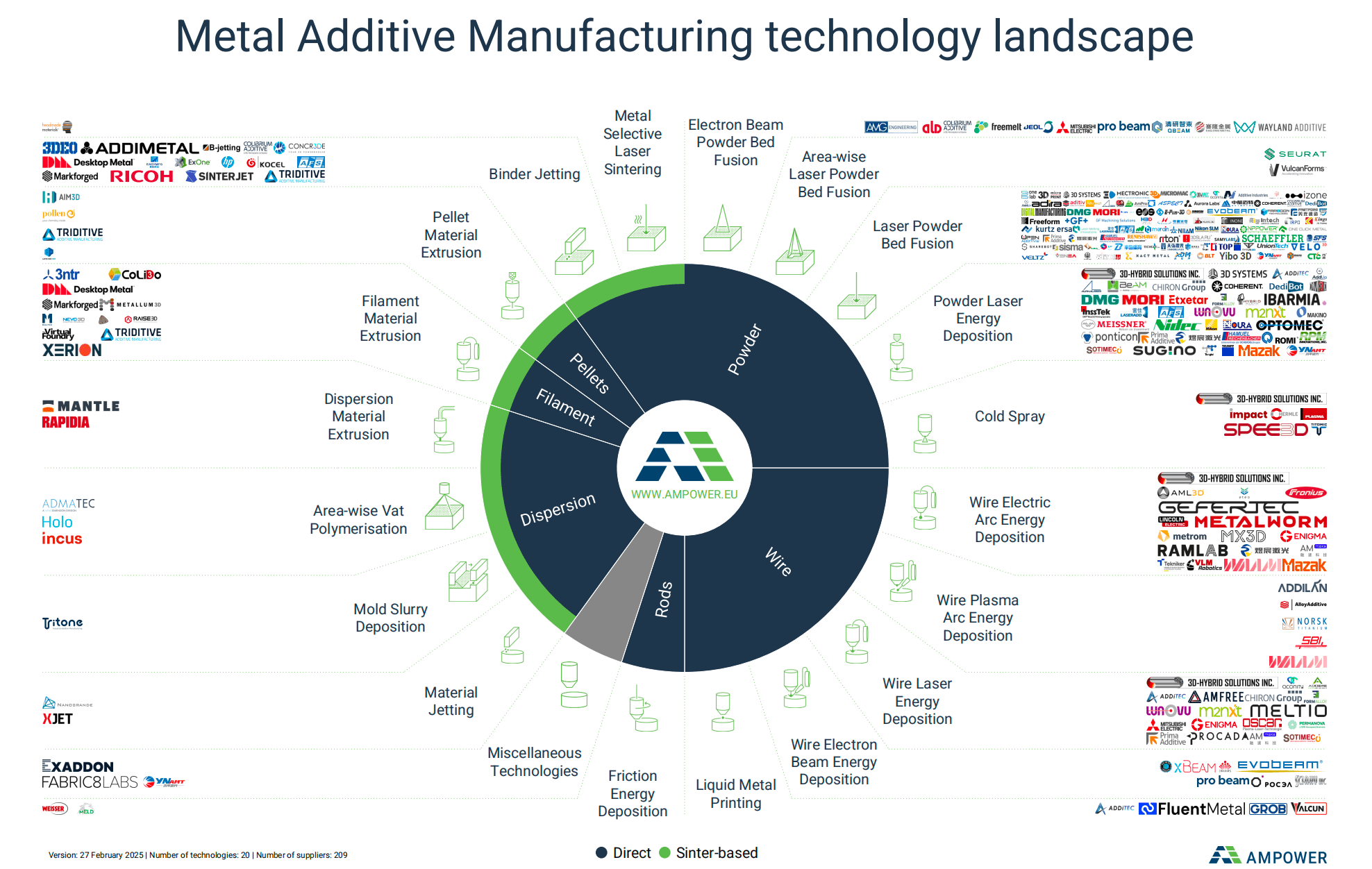
Source: AM Power
Attracted by the strong momentum in the development of metal AM industry, over the past two decades, numerous new technologies and manufacturers have sprung up.
According to AM Power’s latest research, there are essentially twenty different metal AM processes, distinguished by raw material (powder, wire, etc.), binding mechanism (melting, sintering, etc.), and energy source (laser, electron beam, arc, etc.). And as many as 209 3d printer suppliers have entered into the market.
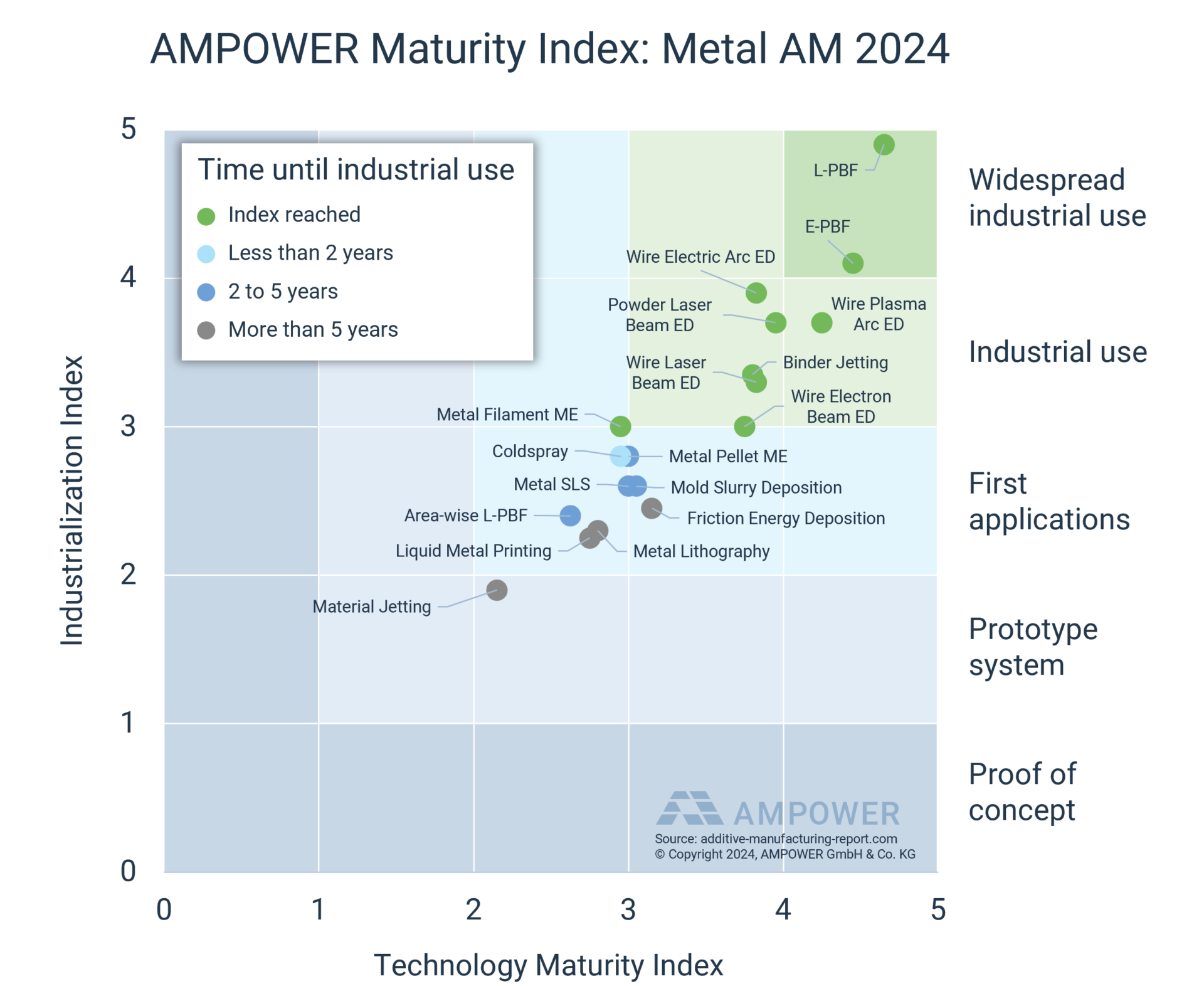
Source: AM Power
Despite 20 types of technologies on the market, not all of them are ready for widespread industrial use. According to the 2024 Metal AM Technology Maturity Index by AM Power,
Only L-PBF and E-PBF are widely used in industrial applications.
Seven other technologies — Wire Electric/Plasma Arc ED, Powder/Wire Laser Beam ED, Wire Electron Beam ED, Binder Jetting, and Metal Filament ME (Material Extrusion)—are suitable for industrial use but not yet widely adopted.
The rest may take 2 to 5 years, or even longer, to become industrially viable.
The nine metal 3D printing technologies suitable for industrial use will be our main focus. Based on different metal binding mechanisms, they can be grouped into four main categories: PBF, DED, BJ, and ME.
Next, we will introduce and compare these four categories.
PBF VS. DED VS. BJ VS. ME
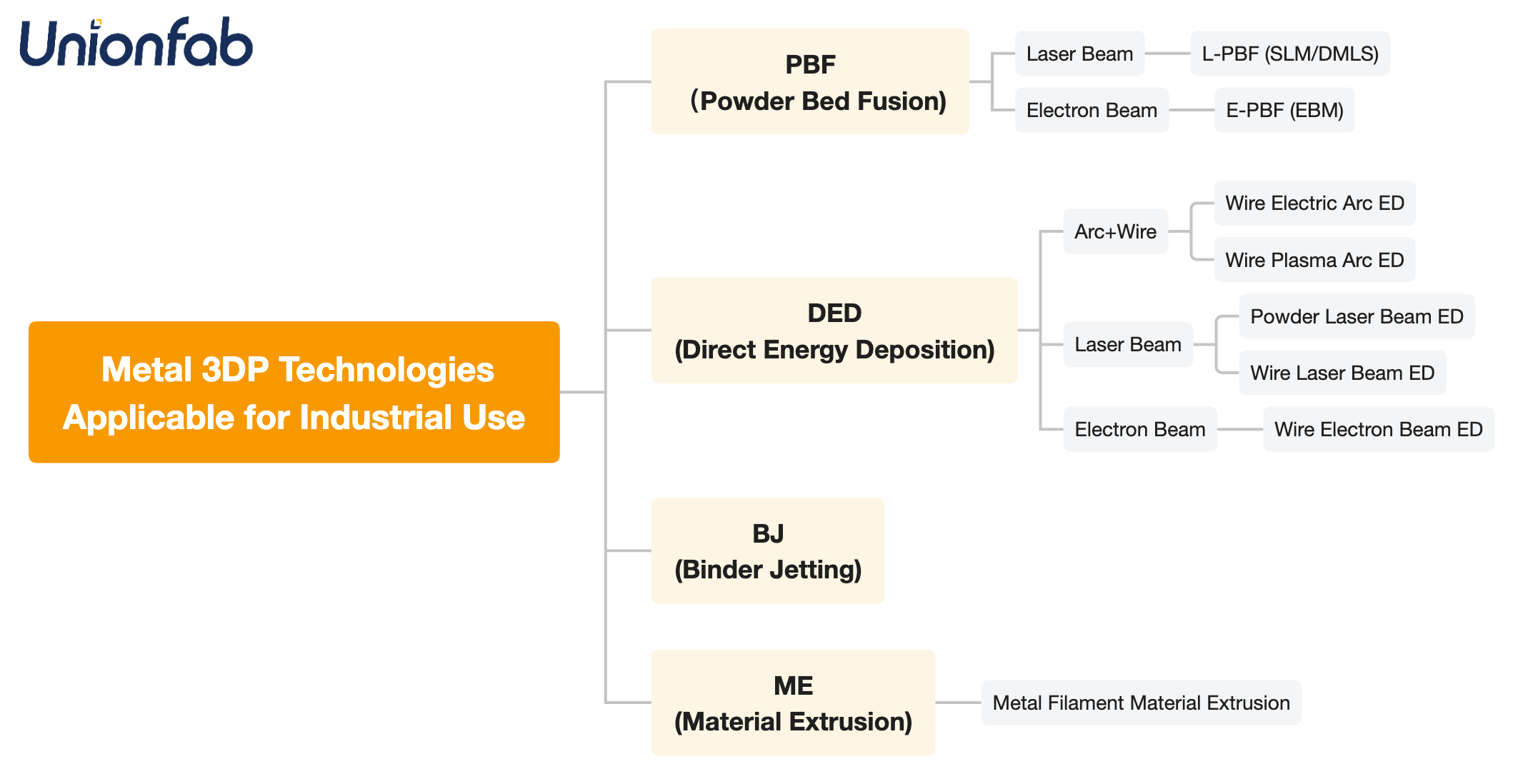
Here we have compared the four categories of metal 3d printing technologies to help you have a good understanding and choose the most suitable one based on your needs.
Comparison Aspect | PBF | DED | BJ | ME |
---|---|---|---|---|
Best For | High-precision complex parts (aerospace, medical) | Large-scale parts, repair & coating (airplanes) | Batch production of small parts (gears, filters) | Prototypes or simple tools |
How It Works | Laser/electron beam melts powder layer by layer | Melt metal powder/wire while spraying it | Binder jetting + sintering | Squeeze metal filament + sintering |
Types of Technologies | L-PBF (Laser) | Arc+Wire: | Binder Jetting | Metal Filament Material Extrusion |
Strength | ⭐️⭐️⭐️⭐️ | ⭐️⭐️⭐️ | ⭐️⭐️ | ⭐️ |
Accuracy & Finish | ⭐️⭐️⭐️⭐️ | ⭐️⭐️ | ⭐️⭐️⭐️ | ⭐️ |
Speed | ⭐️ | ⭐️⭐️⭐️⭐️ | ⭐️⭐️⭐️ | ⭐️ |
Size | Small/medium parts | Huge parts | Scalable bed size | Small/medium parts |
Post-Processing | Support removal, stress relief | Machining, surface refinement | Debinding, sintering (15-20% shrinkage) | Debinding, sintering (10-15% shrinkage) |
Cost | $$$ | $$ | $ | $ |
Safety & Environment | Inert gas, powder handling risks | Fume extraction, radiation shielding | Minimal hazards (cold process), but uses lots of energy | Safe, but uses lots of energy |
In summary, based on different key decision factors, you can prioritize a certain technology to meet your needs.
Precision > Cost → Choose PBF Best for: Medical implants, aerospace engine cores.
Size > Speed → Choose DED Best for: Large structural repairs (e.g., aircraft components).
Volume > Quality → Choose BJ Best for: Mass production of standardized small parts (gears, filters).
Cost > Performance → Choose ME Best for: Prototyping or temporary tooling with minimal strength requirements.
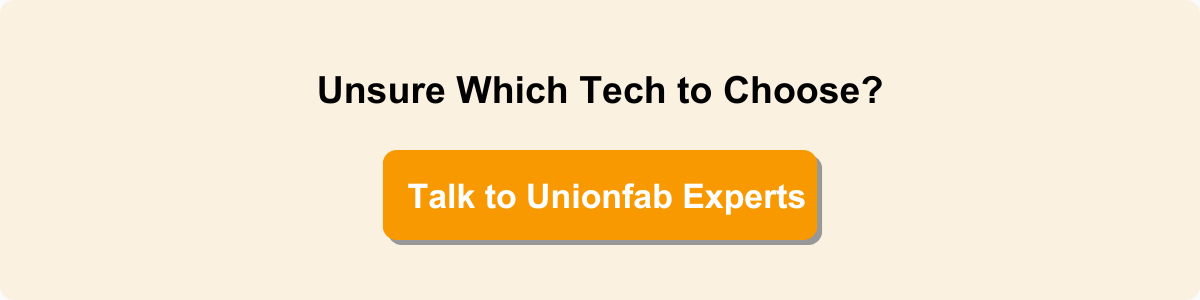
Metal 3D Printing Materials
Instead of prioritizing pure metals, metal alloys are more widely used in 3D printing due to their enhanced mechanical properties, tailored processability, and application-specific performance.
Figure shows common metal alloys used in 3D printing. In the table below, we compare their compatibility with different technologies, key properties, and applications.
Category | Common Alloys | PBF | DED | BJ | ME | Key Properties | Typical Applications |
---|---|---|---|---|---|---|---|
Titanium Alloys | Ti-6Al-4V, Ti-6Al-4V ELI | ⭐️⭐️⭐️⭐️ | ⭐️⭐️⭐️ | ⭐️⭐️ | ⭐️ | High strength-to-weight ratio, biocompatible | Aerospace, medical implants |
Aluminum Alloys | AlSi10Mg, | ⭐️⭐️⭐️⭐️ | ⭐️⭐️ | ⭐️ | ⭐️ | Lightweight, thermal conductivity | Automotive, heat exchangers |
Stainless Steels | ⭐️⭐️⭐️⭐️ | ⭐️⭐️⭐️ | ⭐️⭐️⭐️ | ⭐️⭐️ | Corrosion resistance, moderate strength | Industrial tooling, marine parts | |
Tool Steels | H13, | ⭐️⭐️⭐️ | ⭐️⭐️⭐️⭐️ | ⭐️⭐️ | ⭐️ | Wear resistance, high hardness | Molds, dies, cutting tools |
Nickel-Based Superalloys | Inconel 718, Inconel 625 | ⭐️⭐️⭐️⭐️ | ⭐️⭐️⭐️⭐️ | ⭐️ | ❌ | High-temperature resistance | Turbine blades, aerospace engines |
Cobalt-Chrome Alloys | CoCrMo (ASTM F75), | ⭐️⭐️⭐️⭐️ | ⭐️⭐️⭐️ | ⭐️ | ⭐️ | High wear resistance, biocompatible | Dental implants, orthopedic devices |
Copper Alloys | CuCrZr, | ⭐️⭐️ | ⭐️⭐️⭐️ | ⭐️⭐️ | ⭐️⭐️ | Thermal/electrical conductivity | Heat sinks, electrical components |
From the table, PBF works best with metal materials, followed by DED, BJ, and ME. Among PBF methods, L-PBF, or SLM 3D Printing is the most widely used metal 3D printing technology today. To learn more about SLM 3D Printing, check our earlier article: Guide to SLM 3D Printing/Metal LPBF.
What’s more, aluminum alloys and stainless steel are cheaper than other metals and work well for most needs, making them the most popular choices in metal 3D printing.
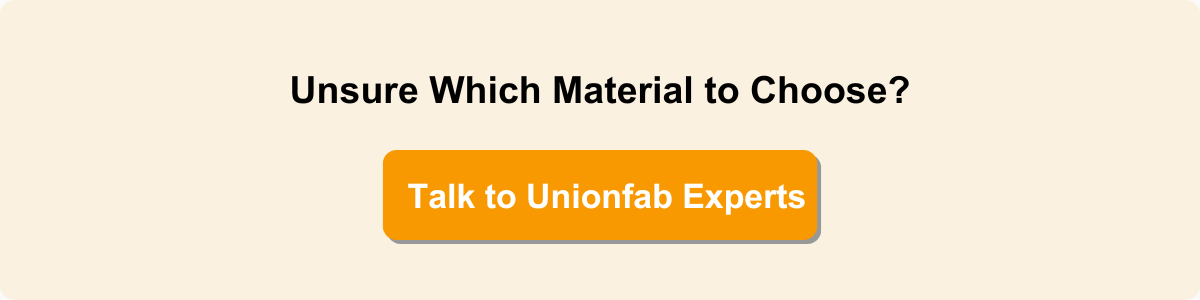
Metal 3D Printing vs. CNC vs. Casting
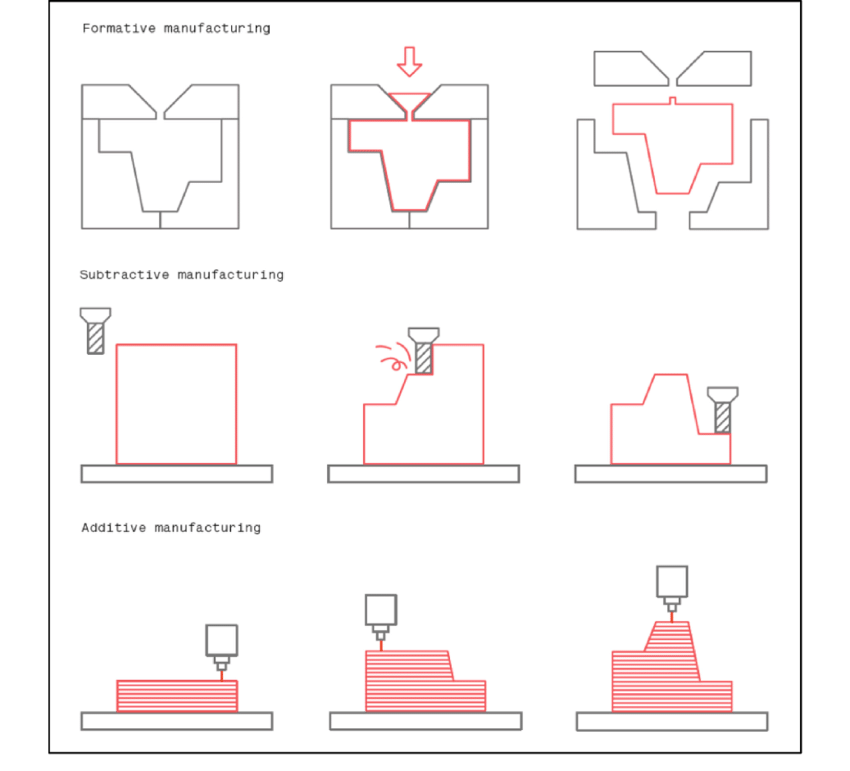
For manufacturing metal parts, besides metal 3D printing, there are traditional methods like CNC machining and casting. Metal 3D printing belongs to additive manufacturing; CNC subtractive manufacturing; Casting formative manufacturing.
The table below compares these three methods to help you understand their differences.
Aspect | Metal 3D Printing | CNC Machining | Casting |
---|---|---|---|
Complexity | Excels at intricate, organic designs; no tooling limitations. | Limited by tool access; complex internal features require extra setups. | Mold-dependent; hollows/undercuts need cores. |
Speed | Slow per-part speed, but no tooling delays. Ideal for prototypes. | Fast for small/medium batches; slower for highly complex parts. | Slow mold creation, but fastest per-part at scale (high volume). |
Material Usage | Additive process: minimal waste | Subtractive: high waste (up to 90% for complex parts). | Moderate waste (gating systems), but recyclable. |
Material Choice | Limited metals (e.g., Ti, Al, steel alloys). | Broad metals, plastics, composites. | Wide metals (e.g., cast iron, bronze, Zn alloys). |
Surface Finish | Rough surfaces; requires post-processing (machining/polishing). | Smooth finishes (Ra 0.8–3.2 µm); ready-to-use. | Moderate (Ra 3.2–12.5 µm); secondary machining often needed. |
Costs | High per-part cost; optimal for <100 units. | Moderate per-part cost; economical for 100–10k units. | Low per-part at scale (>1k units); high mold/tooling upfront. |
If you prioritize cost, you can follow the general rule of thumb below to choose the most cost-efficient manufacturing method.
<100 units: 3D printing (flexibility, low setup).
100–1,000 units: CNC (balance of speed and cost).
>1,000 units: Casting (mass-production efficiency).
If you want to learn more about how much does metal 3d printing cost, check out our previous article Guide to Metal 3D Printing Cost. Or, click our online free metal 3d printing cost calculator below to get a metal 3d printing instant quote.
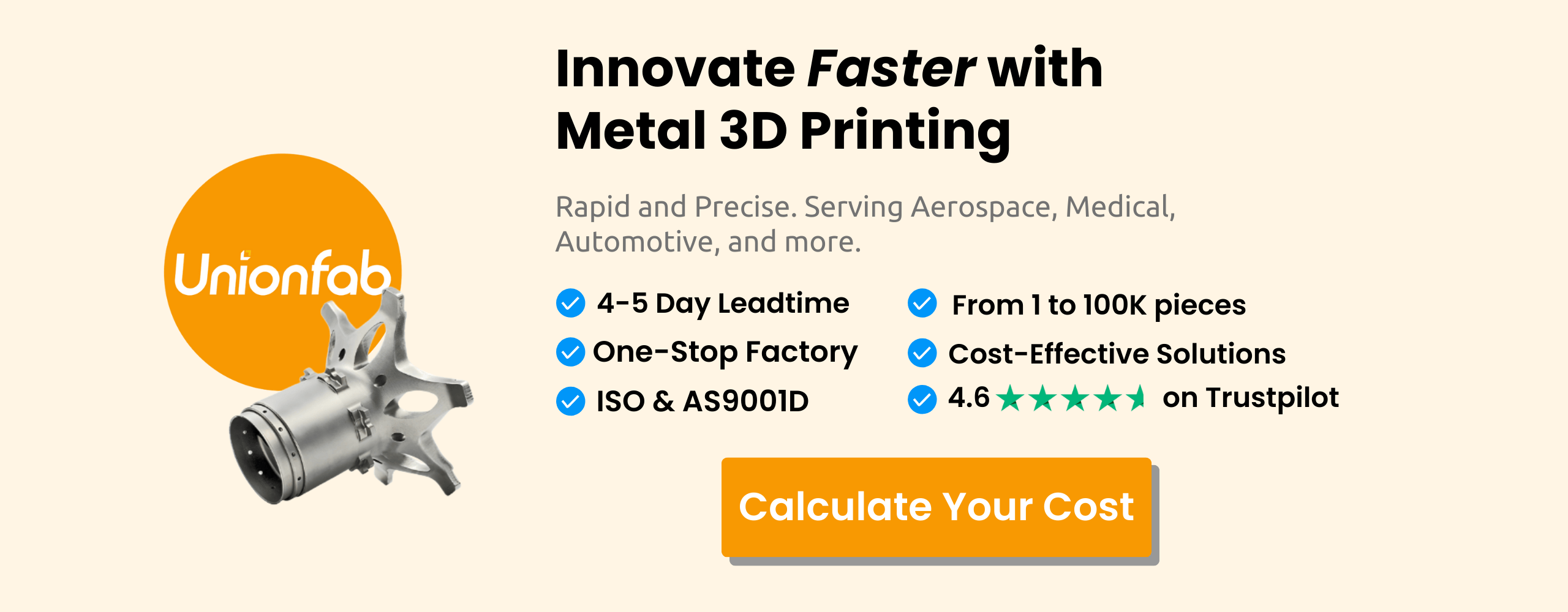
Service Providers Comparison
When choosing a metal 3D printing service provider, it's important to compare key factors like material options, build volume, cost etc. In this section, we will compare major service providers to help you make an informed decision.
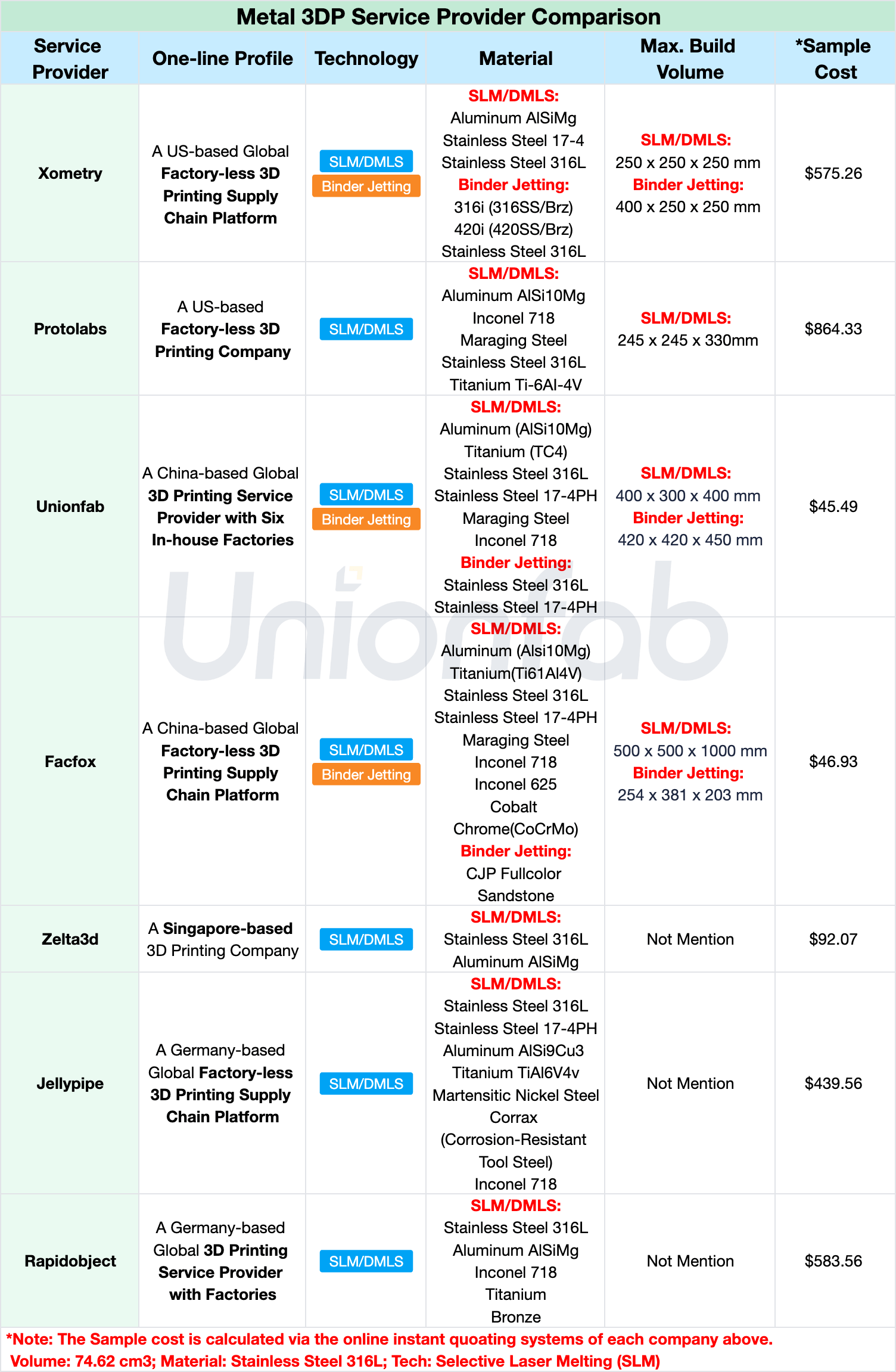
In summary,
Xometry, Unionfab, and Facfox offer both SLM/DMLS and Binder Jetting Technologies.
Xometry, Unionfab, and Facfox provide relatively rich metal materials.
Facfox has the largest build volume for SLM/DMLS: 500 x 500 x 1000 mm.
Unionfab has the largest build volume for Binder Jetting: 420 x 420 x 450 mm.
Xometry, Facfox, Protolabs and Jellypipe are factory-less supply chain platforms, while Unionfab and Rapidobject have self-owned factories.
Below is the score of some companies above on Trustpilot. You can click the score to see feedback from real customers.
Unionfab’s 3D Printing Service
With 20+ years of expertise, 1,000+ industrial 3D printers, and 6 cutting-edge factories, Unionfab, certified with ISO 9001, ISO 13485, and AS 9001D, is committed to delivering high-quality, cost-effective 3D printing services.
The followings are the details of our SLM printing service.
SLM/DMLS | Binder Jetting | |
---|---|---|
Equipment | BLT; SLM; EOS; EXONE | HP S100 |
Materials | Aluminum (Alsi10Mg) |
|
Max Part Size | 400 x 300 x 400mm | 420 x 420 x 450mm |
Layer Thickness | 0.035 mm | 0.035 mm |
Tolerance | ±0.2 mm | ±0.2 mm |
Min. Wall Thickness | 0.5 mm | 0.5 mm |
*Min. Reference Unit Price of Materials | Aluminum (Alsi10Mg): $0.6/g | Aluminum (Alsi10Mg) $0.6/g |
Pass Rate | 99.5% | 99.5% |
Lead Time | As fast as 4-5 days | As fast as 4-5 days |
On-time Delivery Rate | 98% | 98% |
Certification | ISO 9001, ISO 13485, and AS 9001D | ISO 9001, ISO 13485, and AS 9001D |
*The actual unit price is subject to real-time inquiry.
If you haven’t used Unionfab’s 3d printing service yet, sign up to get a 10% discount on your first order!
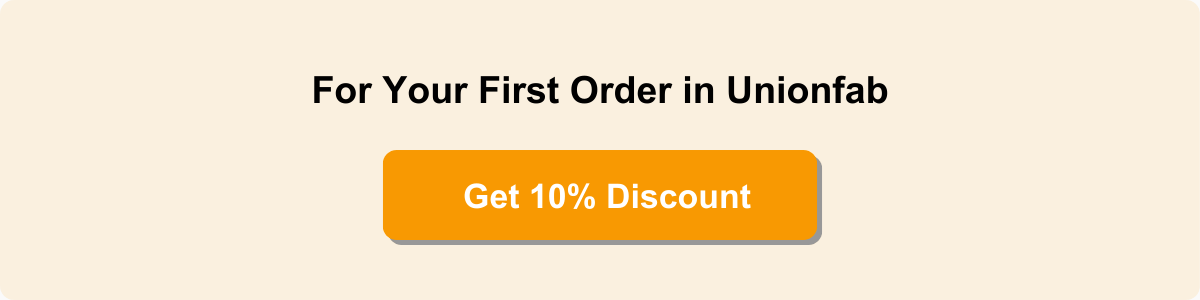
Post Processing
We not only provide high-precision printing but also a range of post-processing options below, including sandblasting, electroplating, and polishing etc., to improve surface quality, durability, and aesthetics of the prints, ensuring the perfect fit for various applications.
![]() | ![]() | ![]() | ![]() | ![]() |
---|---|---|---|---|
![]() | ![]() | ![]() | ![]() | ![]() |
![]() | ![]() | ![]() | ![]() | ![]() |
Case Displays of Metal 3D Prints by Unionfab
Here are some 3d-printed parts in different metals made by Unionfab.
![]() | ![]() | ![]() |
---|---|---|
![]() | ![]() | ![]() |
Virtual Factory Tour
Explore Unionfab's production process, equipment, and quality control in our VR factory tour. Click the GIF below to start your virtual visit now!
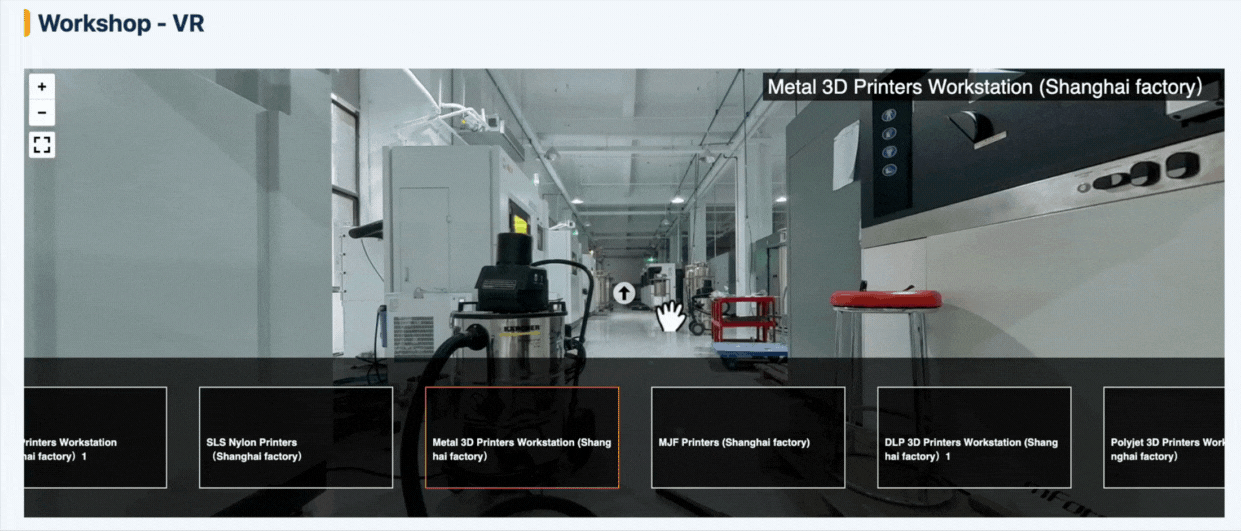
Future Trends and Developments in Metal 3D Printing
New materials - More metal alloy powders will become available for 3D printing, including superalloys, refractory metals and rare earth materials. New metal composites will also emerge.
Multi-material printing - The ability to print different metal and non-metal materials within the same part will enable production of components with tailored properties and functional gradients.
Printed electronics - Integration of conductive materials within 3D printed metal structures will create opportunities for customized electronic components.
Industry adoption curves - Widespread adoption of metal AM for end-use production across industries like aerospace, automotive and medical is likely to accelerate as technology improves and costs decrease.
As these capabilities are realized, metal 3D printing will increasingly move from prototyping to production applications. Overall, the future of metal AM remains extremely promising.
FAQs
Can Inconel be 3D printed?
Yes, Inconel can be 3D printed using Powder Bed Fusion (PBF) or Directed Energy Deposition (DED). Inconel 625 and 718 are commonly used due to their high-temperature resistance and corrosion resistance.
What metals cannot be 3D printed?
Some metals are difficult or impossible to 3D print due to high reflectivity, oxidation, or brittleness. Examples include:
Pure Copper & Gold (high reflectivity affects laser absorption)
Magnesium & Beryllium (high flammability)
Cast Iron (brittle and prone to cracking)
How long does it take to 3D print metal?
It depends on the part size, complexity, and printing method. Typically:
Small parts: A few hours
Medium parts: 10–20 hours
Large parts: Several days
Is 3D printed metal stronger than forged?
No, forged metal is generally stronger due to its grain structure and work-hardening process. However, 3D printed metal can be comparable in strength if optimized with heat treatments and post-processing.
What are the downsides of metal 3D printing?
High cost (machines, materials, and post-processing)
Slow production speed (compared to CNC and casting)
Limited material options
Porosity & defects (can affect mechanical properties)
What is the largest metal 3D printing company?
The leader depends on market segment and technology focus. For example, if you refer to the largest metal 3D printing service provider in China, Unionfab is the leader.
What is the strongest type of metal 3D printing?
Laser Powder Bed Fusion (L-PBF) produces some of the strongest metal parts due to its high density and fine microstructure. Titanium, Inconel, and Maraging Steel are among the strongest 3D printed metals.
Do you need a special 3D printer to print metal?
Yes, metal 3D printing requires industrial-grade machines that use lasers, electron beams, or binders to fuse metal powder or wire.
Is metal 3D printing cheaper than CNC?
It depends.
For complex, low-volume parts → 3D printing is cheaper (less material waste, no tooling).
For simple, high-volume parts → CNC is cheaper (faster, lower cost per part).
Is metal 3D printing the future?
Yes, metal 3D printing is growing, especially for aerospace, medical, and automotive industries. However, it won’t fully replace traditional methods but will complement them for complex and high-performance parts.