3D Printing vs. CNC Machining
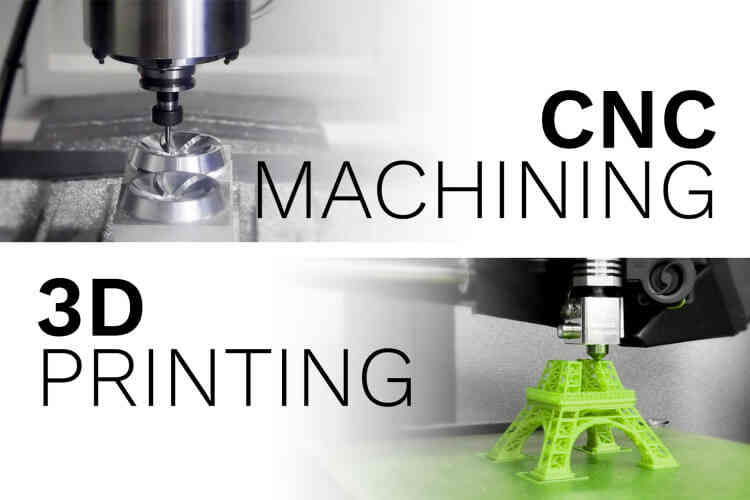
Discover the key differences between 3D Printing and CNC Machining. Learn about their processes, materials, benefits, and best use cases in manufacturing.
TL:DR: Head straight to the part “3D Printing vs. CNC Machining: How to Choose the Right Technology” to tell the differences.
Introduction
In manufacturing, both 3D Printing and CNC Machining are game-changers, revolutionizing the way products are designed, prototyped, and produced. However, choosing the right technology can be challenging without a clear understanding of their differences.
Explore the intricacies of 3D Printing and CNC Machining in this article. Whether aiming for complex designs, high precision, or cost efficiency, understanding these technologies will guide your manufacturing decisions.
3D Printing
Definition of 3D Printing
source: gifer.com
3D printing, also known as additive manufacturing, is a technology that creates three-dimensional objects by layering materials based on digital models. Unlike traditional subtractive manufacturing methods (such as cutting or drilling), 3D printing builds objects layer by layer from the bottom up, directly translating a computer-aided design (CAD) file into a physical item.
Common Types of 3D Printing Technologies
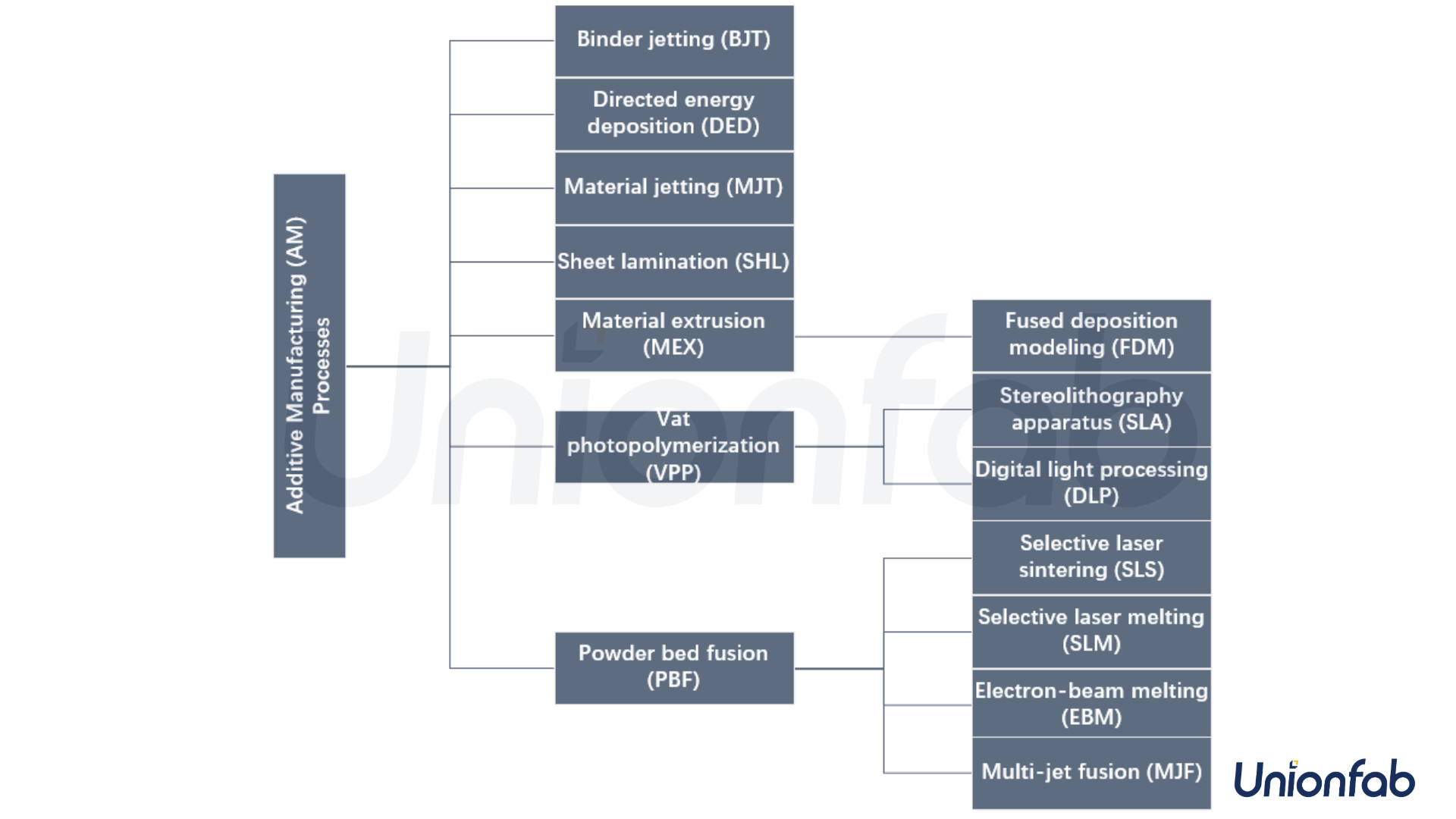
There are several types of 3D printing technologies, each suited for different applications:
Process Type | Process | Materials | Applications |
---|---|---|---|
Binder Jetting (BJT) | A liquid binder is selectively deposited onto a powder bed, bonding the particles layer by layer to create the object. | Various powders like metals, plastics, and sand. | Prototypes, sand casting molds, architectural models. |
Directed Energy Deposition (DED) | A focused energy source (laser or electron beam) melts metal wire or powder, depositing it layer by layer to create the object. | Primarily works with metals. | Large metal parts, repairs, functional components. |
Material Extrusion (Fused Deposition Modeling, FDM) | A heated nozzle extrudes a filament of molten plastic, depositing it layer by layer to build the object. | Primarily uses thermoplastics like ABS, PLA, and nylon. | Prototypes, functional parts, design models. |
Material Jetting (MJT) | Similar to an inkjet printer, this process jets droplets of material (photopolymer resin, wax) layer by layer to build the object. | Uses photopolymers, wax, and other specialized materials. | High-resolution prototypes, full-color models, dental applications. |
Powder Bed Fusion (SLS, SLM, DMLS) | A laser or electron beam selectively melts powder particles (plastic or metal) to fuse them together layer by layer. | Works with a wide range of materials like plastics, metals (including titanium and stainless steel), and even some ceramics. | Complex metal parts, high-strength prototypes, end-use functional parts. |
Sheet Lamination (SHL) | Thin sheets of material (paper, metal) are bonded together layer by layer to create the object. | Uses various sheet materials like paper, plastic, and metal. | Rapid prototypes, composite structures. |
Vat Photopolymerization (SLA, DLP) | Uses a vat of liquid resin and a light source (laser in SLA, projector in DLP) to cure thin layers selectively, solidifying the desired object shape. | Primarily uses photopolymers (light-curable resins). | High-resolution prototypes, jewelry, dental models. |
Table 1 Introduction of Common Types of 3D Printing Technologies
3D Printing Process: Steps from Design to Printing
The 3D printing process involves several key steps:
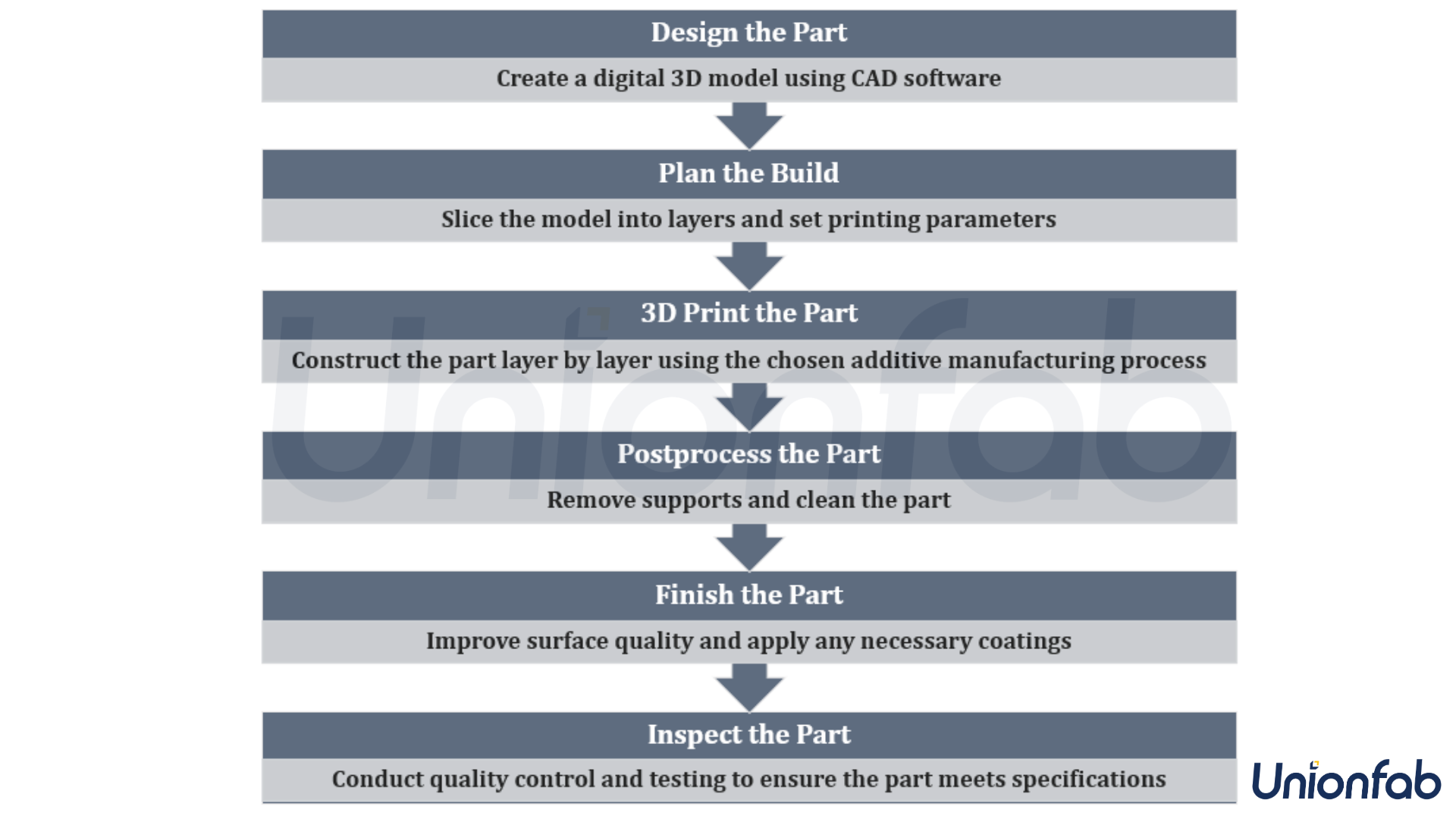
Design the Part
CAD Modeling: Create a digital 3D model using CAD software as the blueprint.
Optimization: Enhance the model for weight, strength, and complex geometries.
Plan the Build
Slicing: Slice the 3D model into thin layers with slicing software.
Parameter Setting: Adjust build parameters like layer thickness, speed, and supports for quality and speed balance.
3D Print the Part
Layer Construction: Construct the part layer by layer based on the sliced model using various additive manufacturing processes (e.g., FDM, SLA, SLS).
Material Deposition: Deposit, cure, or sinter material to form each layer until the part is complete.
Postprocess the Part
Support Removal: Remove support structures, either by breaking or dissolving them.
Cleaning: Clean the part to remove residual powder, resin, or debris.
Finish the Part
Surface Finishing: Improve surface quality through sanding, polishing, or coating.
Painting and Coating: Apply paint or coatings for aesthetics or protection.
Inspect the Part
Quality Control: Inspect the part visually, measure dimensions, and test functionality to ensure it meets specifications.
Testing: Perform stress, load, or other tests as needed to ensure performance.
Commonly Used Materials
3D printing can utilize a variety of materials, depending on the technology and application. Some of the most common materials include:
Type | Material | Properties | Common Uses |
---|---|---|---|
Plastics | PLA (Polylactic Acid) | Biodegradable, easy to print, low warping | Prototypes, consumer products, toys |
ABS (Acrylonitrile Butadiene Styrene) | Strong, durable, slightly flexible, heat resistant | Automotive parts, electronic housings, toys | |
PETG (Polyethylene Terephthalate Glycol) | Strong, impact-resistant, chemical resistant | Food containers, mechanical parts | |
Nylon | Strong, flexible, abrasion-resistant | Gears, bearings, mechanical parts | |
TPU (Thermoplastic Polyurethane) | Flexible, durable, impact-resistant | Wearable items, flexible prototypes | |
PEEK (Polyether Ether Ketone) | High strength, high temperature resistance, chemical resistant | Aerospace, medical implants, high-performance parts | |
Metals | Aluminum | Lightweight, corrosion-resistant, good strength-to-weight ratio | Automotive parts, aerospace components |
Stainless Steel | Strong, durable, corrosion-resistant | Medical devices, tools, industrial parts | |
Titanium | High strength-to-weight ratio, corrosion-resistant | Aerospace, medical implants, high-performance parts | |
Copper | Excellent electrical and thermal conductivity | Electrical components, heat exchangers | |
Ceramics | Zirconium Dioxide | High temperature resistance, wear-resistant | Dental implants, thermal insulation |
Silicon Carbide | High hardness, wear-resistant, high thermal conductivity | Cutting tools, aerospace components | |
Aluminum Oxide | High hardness, electrical insulation, wear-resistant | Electronic substrates, wear parts | |
Composites | CFRP (Carbon Fiber Reinforced Polymer) | High strength-to-weight ratio, stiff | Aerospace, automotive parts, sporting goods |
GFRP (Glass Fiber Reinforced Polymer) | Strong, lightweight, corrosion-resistant | Construction, automotive, marine applications |
Advantages of 3D Printing
High design freedom: 3D printing can create complex geometries that are difficult or impossible with traditional manufacturing.
Rapid prototyping: It allows for quick production of prototypes, accelerating the product development cycle.
Diverse material options: A wide range of materials can be used, catering to different requirements.
Cost-effective for small-batch production: Lower costs make it suitable for producing small quantities.
Reduced waste: Material is only used where needed, minimizing waste.
Disadvantages of 3D Printing
Slower production speed for mass production: It is less efficient for producing large quantities.
Material and strength limitations: Some materials lack the strength required for certain applications.
High costs, especially for metal printing: Metal 3D printing can be expensive.
Poor surface finish: Often requires post-processing to achieve a smooth surface.
Limited dimensional accuracy: Not suitable for high-precision parts.
Lower material strength: Generally not suitable for load-bearing components.
CNC Machining
Definition of CNC Machining
CNC (Computer Numerical Control) machining is a manufacturing process in which pre-programmed computer software dictates the movement of factory tools and machinery. This technology allows for the precise control of complex machinery, from grinders and lathes to mills and routers, transforming raw materials into finished products with high accuracy.
Common Types of CNC Machining
Milling: Utilizes rotating cutting tools to remove material from a workpiece, capable of creating complex shapes and precise features.
source: gif.com
Turning: Involves rotating the workpiece while a stationary cutting tool removes material, typically used for cylindrical parts.
source: makeagif.com
Drilling: Uses a rotating drill bit to create round holes in the workpiece.
source: kinggroup.in
Grinding: Employs an abrasive wheel to remove material and achieve high surface quality and dimensional accuracy.
source: makeagif.com
Electrical Discharge Machining (EDM): Uses electrical discharges to erode material, ideal for hard metals and complex geometries.
source: www.wired.com
Plasma Cutting: Utilizes a high-velocity jet of ionized gas to cut through conductive materials.
source: makeagif.com
Laser Cutting: Employs a focused laser beam to melt, burn, or vaporize material, suitable for high-precision cuts in various materials.
source: www.k2metalfab.com
Waterjet Cutting: Uses a high-pressure stream of water, often mixed with an abrasive, to cut materials without generating heat.
source: tenor.com
CNC Machining Process: Steps from Design to Machining
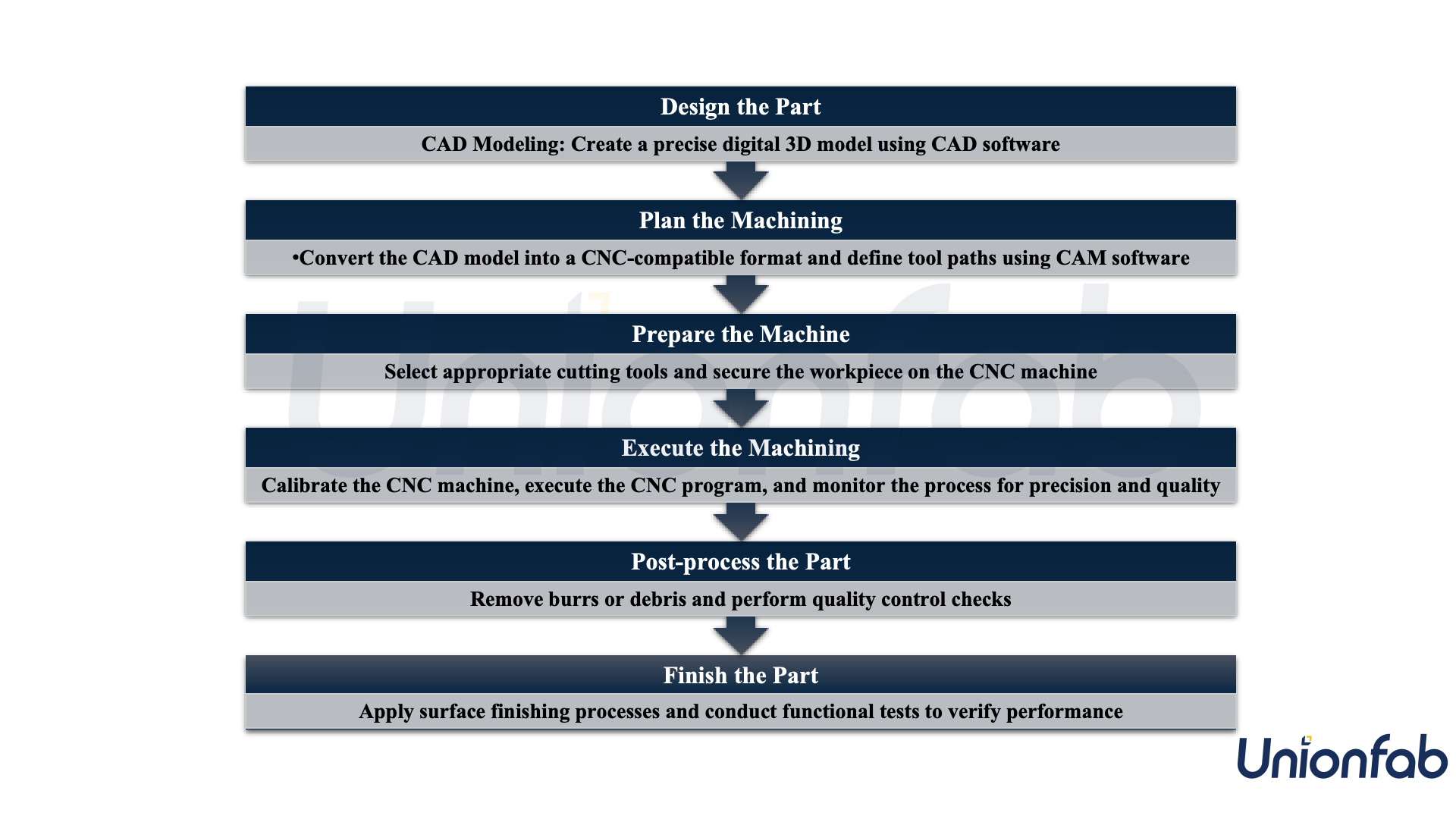
Design the Part
CAD Modeling: Create a precise digital 3D model using CAD software, which serves as the blueprint for machining.
Plan the Machining
Computer-Aided Manufacturing (CAM): Convert the CAD model into a CNC-compatible format using CAM software.
Tool Path Generation: Define tool paths, cutting sequences, and machine parameters to optimize the machining process.
Prepare the Machine
Select Tools: Choose appropriate cutting tools based on material and design requirements.
Setup: Secure the workpiece on the CNC machine and load the required tools.
Execute the Machining
Initial Setup: Calibrate the CNC machine and verify tool positions.
Machining: Execute the CNC program, which guides the cutting tools to remove material and shape the part according to the design.
Monitoring: Continuously monitor the process to ensure precision and quality.
Post-process the Part
Deburring and Cleaning: Remove any burrs or debris from the machined part.
Inspection: Perform quality control checks, including visual inspection and precise measurements to ensure the part meets specifications.
Finish the Part
Surface Finishing: Apply finishing processes such as polishing, coating, or painting to achieve the desired surface quality.
Final Testing: Conduct any necessary functional tests to verify performance.
Commonly Used Materials
CNC machining can work with a wide range of materials, making it versatile for different applications:
Types | Materials | Properties | Common Uses |
---|---|---|---|
Metals | Aluminum | Lightweight, corrosion-resistant, easy to machine | Automotive, aerospace, consumer electronics |
Stainless Steel | Strong, corrosion-resistant, durable | Medical devices, food processing equipment, marine applications | |
Carbon Steel | High strength and hardness | Industrial machinery, automotive parts, construction | |
Titanium | High strength-to-weight ratio, corrosion-resistant | Aerospace, medical implants, high-performance applications | |
Brass | Excellent machinability, corrosion resistance, electrical conductivity | Plumbing, electrical components, musical instruments | |
Copper | High electrical and thermal conductivity | Electrical components, heat exchangers, plumbing | |
Tool Steel | Hard, heat-resistant | Making tools, dies, molds | |
Plastics | ABS | Strong, tough, impact-resistant | Automotive parts, consumer products, toys |
Polycarbonate | High impact resistance, optical clarity | Protective gear, eyewear, electronic enclosures | |
Nylon | Strong, wear-resistant, low friction | Gears, bearings, industrial components | |
POM (Polyoxymethylene/Acetal/Delrin) | High stiffness, low friction, excellent dimensional stability | Precision parts, gears, bearings | |
PTFE (Polytetrafluoroethylene/Teflon) | Excellent chemical resistance, low friction | Gaskets, seals, non-stick coatings | |
PVC (Polyvinyl Chloride) | Good chemical resistance, rigidity | Pipes, fittings, enclosures | |
HDPE (High-Density Polyethylene) | Strong, lightweight, resistant to impact and chemicals | Containers, pipes, cutting boards | |
Wood | Hardwood (e.g., Oak, Maple) | Durable, strong | Furniture, cabinetry, flooring |
Softwood (e.g., Pine, Cedar) | Easier to machine | Construction, furniture, decorative items | |
Plywood | Engineered wood made from thin layers of wood veneer | Construction, furniture, paneling | |
Composites | CFRP (Carbon Fiber Reinforced Polymer) | High strength-to-weight ratio, stiffness | Aerospace, automotive, sports equipment |
GFRP (Glass Fiber Reinforced Polymer) | Strong, lightweight, corrosion-resistant | Construction, automotive, marine applications |
Advantages of CNC Machining
Good Surface Finish: CNC machining produces parts with excellent surface quality, often requiring minimal post-processing.
High Precision: The process can achieve very tight tolerances, making it ideal for high-precision components.
Suitable for Mass Production: CNC machines can produce large quantities of parts with consistent quality.
Wide Range of Applications: Applicable to numerous industries, including aerospace, automotive, and medical.
Fast Processing Speed: Particularly for metal parts, CNC machining offers high processing speeds, increasing efficiency.
Disadvantages of CNC Machining
Limitations on Complex Shapes: While CNC machines can produce intricate parts, they have limitations in creating extremely complex geometries compared to 3D printing.
Material Waste: Subtractive manufacturing processes like CNC machining generate more material waste compared to additive manufacturing.
High Initial Equipment Cost: The upfront cost of CNC machines and associated tooling can be high, making it a significant investment for manufacturers.
3D Printing vs. CNC Machining: Additive vs. Subtractive
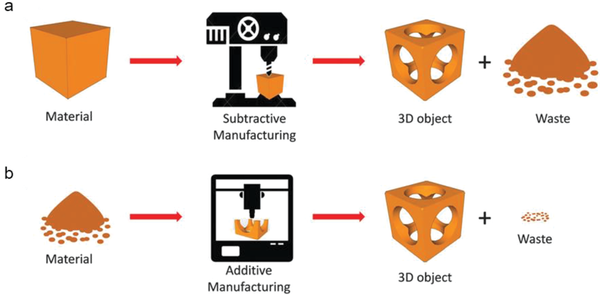
source: www.researchgate.net
The most fundamental difference between 3D printing and CNC machining is that 3DP falls under additive manufacturing, while CNC is a type of subtractive manufacturing. The table below details their differences from 3 aspects.
Aspect | Additive Manufacturing | Subtractive Manufacturing (CNC Machining) |
---|---|---|
Process | Builds parts layer by layer from the ground up using materials like plastics, metals, or ceramics. | Removes material from a solid block to create the desired shape using cutting tools. |
Material Utilization | Minimal waste, as material is added only where needed. | Generates more waste due to the removal of material from a larger block. |
Environmental Impact | Typically produces less material waste and can use environmentally friendly materials. | Generates more material waste but can recycle chips; energy-intensive for high precision and complex parts. |
3D Printing vs. CNC Machining: How to Choose the Right Technology
When deciding between 3D printing and CNC machining, several factors need to be considered to ensure the best fit for your manufacturing needs. The tables below can do you a favor.
Design & Flexibility
Aspect | 3D Printing | CNC Machining |
---|---|---|
Design Flexibility | Excels at complex, | Capable of complex shapes but with some limitations; Customization is more costly and time-consuming. |
Performance
Aspect | 3D Printing | CNC Machining |
---|---|---|
Accuracy and Tolerance | Lower accuracy | High precision |
Surface Quality | Requires post-processing for smooth finish. | Excellent surface quality, minimal post-processing. |
Material Utilization | Minimal waste, some support structure waste. | Generates more waste due to subtractive process. |
Efficiency
Aspect | 3D Printing | CNC Machining |
---|---|---|
Material Waste | Minimal, as material is added only where needed | Significant, as material is removed from a larger block |
Production Volume | Cost-effective for low to medium volumes (1-500 parts) | Cost-effective for high volumes (500+ parts) |
Lead Time | Short (1-3 days), ideal for rapid prototyping | Longer (1-2 weeks) due to setup and tooling requirements |
Cost
Aspect | 3D Printing | CNC Machining |
---|---|---|
Material Cost | PLA, ABS (plastics): | Aluminum: $5 to $25/kg |
Nylon, PETG: $40 to $80/kg | Stainless Steel: $10 to $50/kg | |
Resin (SLA): $100 to $200/liter | Titanium: $30 to $100/kg | |
Metal powders (SLS, DMLS): | Plastics (e.g., ABS, Nylon): | |
Machine Cost | Desktop FDM printers: | Entry-level CNC mills: |
Industrial FDM printers: | Professional CNC mills: | |
SLA printers: $2,000 to $200,000 | CNC lathes: | |
SLS/DMLS printers: |
|
Note: Costs vary widely based on machine models, materials, and production volumes. Provided ranges are general estimates.
Applications
Aspect | 3D Printing | CNC Machining |
---|---|---|
Application Range | Prototyping, small-batch, customized products. | Mass production, |
Maintenance & Labor
Aspect | 3D Printing | CNC Machining |
---|---|---|
Maintenance | Lower ongoing maintenance costs | Higher maintenance costs due to complex machinery |
Labor Costs | Generally lower due to more automation | Higher due to the need for skilled operators |
Durability
Aspect | 3D Printing | CNC Machining |
---|---|---|
Average Lifetime | Desktop printers: 3-5 years | Entry-level CNC machines: |
Industrial printers: 5-10 years | Professional CNC machines: |
Energy
Aspect | 3D Printing | CNC Machining |
---|---|---|
Energy Consumption | Generally lower, especially for smaller machines | Higher due to the power needed for cutting and operation of larger machines |
Scalability
Aspect | 3D Printing | CNC Machining |
---|---|---|
Scalability | Easier for small to medium quantities | More efficient for large quantities |
Examples
Example Part | 3D Printing Cost | CNC Machining Cost |
---|---|---|
Example Part (100g) | Simple Plastic Part: $2 to $10 | Simple Aluminum Part: |
Example Part (500g) | Complex Plastic Prototype: $25 to $150 | Complex Stainless Steel Part: $200 to $500 |
Example Part (1kg) | Large Metal Part: $30 to $100 | Large Plastic Part: |
FAQs
Is CNC Machining Better Than 3D Printing?
It depends on the application. CNC machining is ideal for high-precision, high-strength parts and mass production due to its accuracy and surface finish. It's suitable for a wide range of materials, including metals and plastics. Conversely, 3D printing excels at creating complex designs and prototypes quickly with minimal waste, making it perfect for small-batch production and customization.
Will 3D Printing Make CNC Machining Obsolete?
No, 3D printing won't make CNC machining obsolete. While 3D printing is great for complex geometries and rapid prototyping, CNC machining is essential for high-precision, high-strength parts and large-scale production. Both technologies complement each other in manufacturing.
Is 3D Printing Cheaper Than CNC Machining?
3D printing can be cheaper for small batches and complex, customized parts due to less material use and minimal setup. However, CNC machining is often more cost-effective for large-scale production because of faster production speeds and material versatility.
What Are Some Advantages of 3D Printing Over CNC?
Design Flexibility: Produces complex geometries and intricate designs.
Material Efficiency: Minimal waste, adding material only where needed.
Rapid Prototyping: Quick production of prototypes for faster design iterations.
Customization: Ideal for unique, customized items and small batches.
What to Choose Between 3D Printing and CNC Machining?
Choose based on your needs:
3D Printing: Best for complex designs, rapid prototyping, small-batch production, and customized items.
CNC Machining: Best for high-precision parts, mass production, and applications requiring high strength and durability.
How to Integrate 3D Printing with CNC Machining?
Combine both technologies for their strengths:
Hybrid Manufacturing: Use 3D printing for complex shapes and CNC machining for precision finishing.
Prototyping to Production: 3D print prototypes and use CNC machining for final production.
Tooling and Fixtures: 3D print custom fixtures and jigs for CNC setups.
What Are the Alternatives to 3D Printing and CNC Machining?
Injection Molding: For mass production of plastic parts with high repeatability.
Casting: Produces metal parts in large quantities with complex shapes.
Laser Cutting: Cuts and engraves materials like metal, plastic, and wood with high precision.
Waterjet Cutting: Uses high-pressure water to cut various materials, including metals, glass, and stone.
Manual Machining: Traditional methods using manual tools for small-scale or highly customized work.